Technical Specifications Prompt Natural Cement The
Total Page:16
File Type:pdf, Size:1020Kb
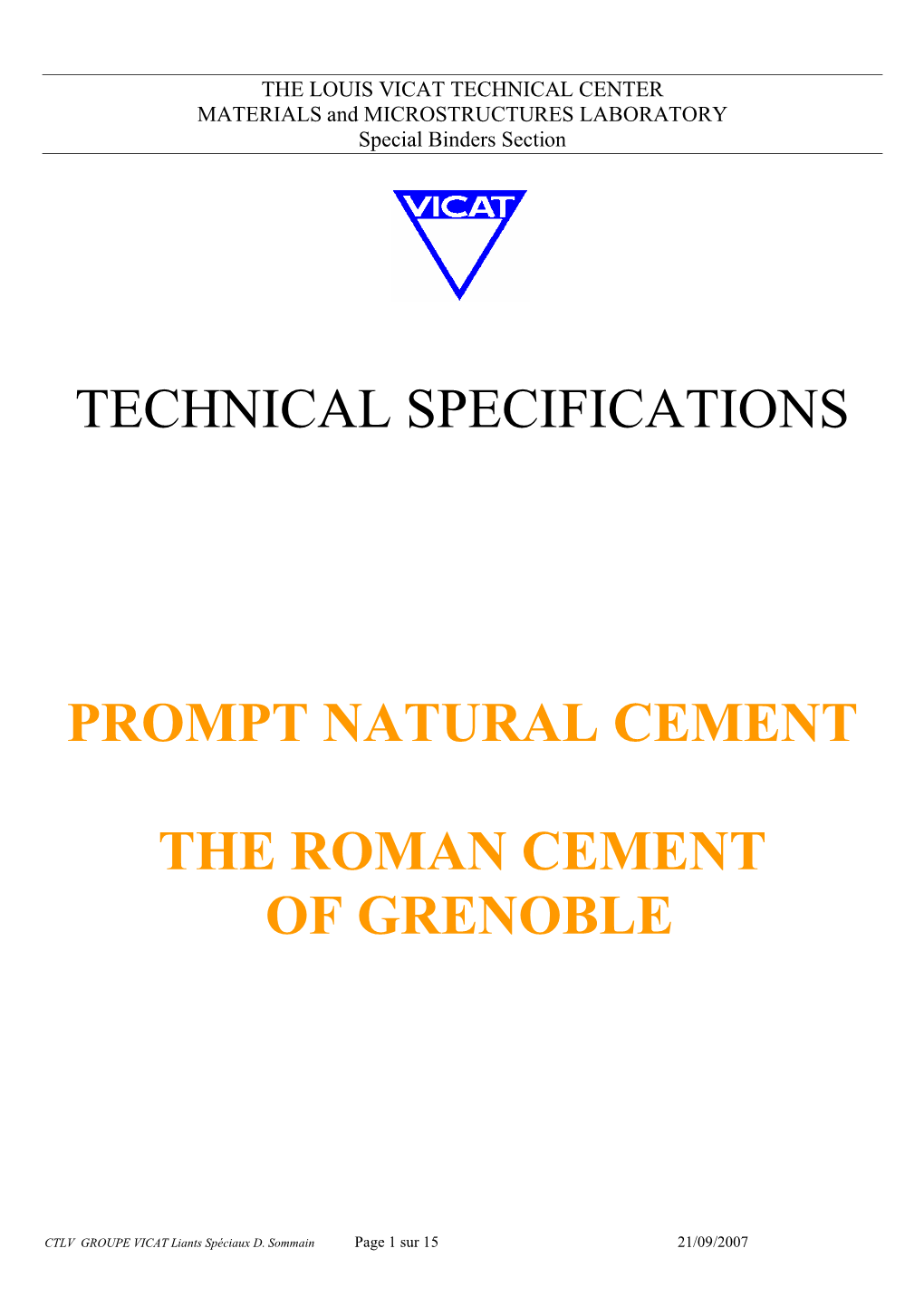
Load more
Recommended publications
-
Archaeology South-East ASE
Archaeology South-East ASE LAND AT CRAYLANDS LANE/LONDON ROAD LITTLE SWANSCOMBE, KENT (Centred at NGR 559786 174912) HISTORIC BUILDING RECORD (HISTORIC ENGLAND LEVEL 1 & 3) Commissioned by Swanscombe Developments LLP LAND AT CRAYLANDS LANE/LONDON ROAD, LITTLE SWANSCOMBE, KENT HISTORIC BUILDINGS RECORD (HISTORIC ENGLAND LEVEL 3) NGR: 559786 174912 Commissioned by Swanscombe Developments LLP Site Code: CLI 16 Project No. 160242 Report No. 2016180 OASIS ID: archaeol6-251290 Assistant Prepared by: Hannah Green BA, MA Archaeologist Reviewed and Amy Williamson BA Project Manager approved by: Date of Issue: May 2016 Revision: 2 Archaeology South-East Units 1 & 2 2 Chapel Place Portslade East Sussex BN41 1DR Archaeology South-East Land At Craylands Lane / London Road, Little Swanscombe, Kent Historic Buildings Record SUMMARY In April 2016 Archaeology South-East (a division of the Centre for Applied Archaeology, UCL) carried out a programme of historic building recording of the buildings and tramway tunnels adjacent to Craylands Lane and London Road, Little Swanscombe, Kent, DA10 0LP, prior to the proposed redevelopment of the site for residential use. This recording exercise forms a detailed survey of the extant tramway tunnels at Historic England Level 3 (English Heritage 2006a). The wider site was subject to a Level 1 record, for contextual purposes. A desk-based assessment has previously been produced for the site by Archaeology South-East (ASE 2005). The site was established as a quarry in the early 20th century, forming part of the Swanscombe Works. The Swanscombe Works was one of the largest cement producers throughout the 20th century, and at its closure in 1990 was the oldest cement producer in the world. -
View Annual Report
BUILDING FOR GROWTH 2017 ANNUAL REPORT LAFARGEHOLCIM LAFARGEHOLCIM IS THE LEADING GLOBAL CONSTRUCTION MATERIALS AND SOLUTIONS COMPANY. FROM SMALL LOCAL PROJECTS TO THE BIGGEST, MOST TECHNICALLY CHALLENGING INFRASTRUCTURE ENDEAVORS, WE SUPPORT BUILDERS AROUND THE WORLD. TOWARD INTEGRATED REPORTING SUSTAINABILITY REPORT 7KLVLVRXUȴUVWVWHSRQRXUMRXUQH\WRGHOLYHUDQ integrated annual report. By applying the principles of integrated reporting, we aim to present a more holistic YLHZRIKRZZHFUHDWHYDOXHLQERWKȴQDQFLDODQGQRQ ȴQDQFLDOWHUPV2YHUWKHFRPLQJ\HDUVZHKRSHWKLV report will be an increasingly effective tool for all stakeholders to understand how LafargeHolcim contributes to our world. The Sustainability Report complements this report. FIND OUT MORE ABOUT It presents more detail on our sustainability achievements WHAT WE DO ONLINE as well as progress against our sustainability strategy, www.lafargeholcim.com The 2030 Plan. It will be published in April 2018. LAFARGEHOLCIM 1 ANNUAL REPORT 2017 KEY GROUP FIGURES FINANCIAL HIGHLIGHTS SALES CONTENTS Group at a glance 2 6.1 4.7 Chairman’s statement 4 RECURRING EBITDA GROWTH NET SALES GROWTH % % Chief Executive’s statement 6 2016: 8.7 2016: –1.7 Our Leadership 10 Around our business 12 Tailored solutions 14 5,990 209.5 Customer focus 16 RECURRING EBITDA SALES OF CEMENT Recycled materials 18 CHF M MILLION TONNES Unlocking value 20 2016: 5,950 2016: 233.2 Marketplace 22 Strategy 2022 24 By the numbers 26 1,685 278.7 Business review: FREE CASH FLOW SALES OF AGGREGATES > Asia Pacific 28 CHF M MILLION TONNES 2016: 1,660 2016: 282.7 > Europe 30 > Latin America 32 > Middle East Africa 34 5.8 50.6 > North America 36 Innovation 38 RETURN ON INVESTED CAPITAL SALES OF READY-MIX CONCRETE % MILLION M3 Our people 42 2016: 5.2 2016: 55.0 Health & Safety 44 Risk management 46 Notes: Recurring EBITDA replaces the former Operating EBITDA Adjusted. -
Press Release
PRESS RELEASE Vicat owns 100% of Vicat Sagar in India Paris La Défense, 15 July 2014: The Vicat group (NYSE Euronext Paris: FR0000031775 – VCT) has purchased Sagar Cements’ stake in the Vicat Sagar Cement company, subject to customary conditions precedents. After this transaction, Vicat will own 100% of Vicat Sagar Cement. This company operates a plant located in North Karnataka and has production capacity of 3 million tonnes per year. It features the latest in cement-making technology, its own power plant and access to the rail network. Together with the share purchase, the two groups will untie all their ownership links. With Bharathi Cement and Vicat Sagar Cement, the Vicat group's Indian operations boast two particularly modern and high-performance cement facilities representing total capacity of 8 million tonnes. This transaction enables Vicat to strengthen its position in a market that shows very strong potential. VICAT INVESTOR In 2013, the Group generated sales of €155 million in India, up +12.7% at constant CONTACTS: scope and exchange rates. In the first quarter of 2014, sales in India were up STÉPHANE BISSEUIL +27.2% at constant scope and exchange rates. TEL: +33 (0)1 58 86 86 13 [email protected] ABOUT VICAT VICAT PRESS CONTACTS: The Vicat Group has almost 7,700 employees working in three core divisions, Cement, Concrete & Aggregates and Other Products & Services, which generated consolidated FRANCOIS LESAGE sales of €2,286 million in 2013. TEL: +33 (0)1 58 86 86 26 The Group operates in 11 countries: France, Switzerland, Italy, the United States, francois.lesage@tbwa- corporate.com Turkey, Egypt, Senegal, Mali, Mauritania, Kazakhstan and India. -
How Limestone, Rocks, and Volcanic Ash Built the Modern World
26/11/2017 The Rock Solid History of Concrete ALEXANDERVANLOON/WIKIMEDIA The Rock Solid History of Concrete By Jonathan Schifman Oct 12, 2017 1.5k HOW LIMESTONE, ROCKS, AND VOLCANIC ASH BUILT THE MODERN WORLD. The story of concrete is so ancient that we don't even know when and where it begins. It is a story of discovery, experimentation, and mystery. Emperors and kings became legends for erecting great concrete structures, some of which are still a mystery to engineers today. Many of history's most skilled architects found inspiration in slabs of the gray building material. Common bricklayers advanced the technology, and a con man played a crucial role in the development of concrete recipes. Today, the world is literally filled with concrete, from roads and sidewalks to bridges and dams. The word itself has become a synonym for something that is real and tangible. Press http://www.popularmechanics.com/technology/infrastructure/a28502/rock-solid-history-of-concrete/ 1/22 26/11/2017 The Rock Solid History of Concrete your handprints into the sidewalk and sign your name to history. This is the story of concrete. The First Cement—and Maybe Concrete? Let's get this out of the way right here: cement and concrete are not the same thing. Cement, a mixture of powdered limestone and clay, is an ingredient in concrete along with water, sand, and gravel. Concrete's invention was made possible by the development of cement, and to trace the history of cement, we must trace the use of its components. ADVERTISEMENT - CONTINUE READING BELOW The earliest known use of limestone in a structure has been dated back about 12,000 years. -
Annual Report 2019.Pdf
Annual report 2019 Cover photo: Reinforcement of JFK coastal road, Marseilles (France) INTERVIEW with Guy Sidos, Chairman and CEO 3 THREE ISSUES THAT STEER OUR CHOICES 4 Ecological and energy transition 5 Urban transformation 6 Digital transformation 7 VICAT IN NUMBERS 8 CONTENTS MAJOR ROLE IN LIVING TOGETHER 9 Meeting the needs of many different markets 10 Vicat throughout the world 12 Three strategic focuses for controlled development 14 Governance and shareholders 16 Fondation Louis Vicat 18 Innovation for living together 20 Our CSR commitments 22 A YEAR OF ADVANCES 27 France 28 Rest of Europe 32 Americas 34 West Africa 38 Mediterranean 40 Asia 42 FINANCIAL INDICATORS 46 Annual report 2019 VICAT IS A FRENCH COMPANY FOUNDED 167 YEARS AGO IN THE FOOTSTEPS OF LOUIS VICAT, WHO DEMYSTIFIED ARTIFICIAL CEMENT IN 1817. Today, working in 12 countries, the Group lays out a top-class offering of mineral and bio-based construction materials, along with services that meet the needs of construction trades. Wherever it has cement plants, aggregate quarries, concrete batching plants, and factories ARE WE WHO manufacturing finishing products for the building industry, Vicat strives to produce locally and in so doing develop employment and the local economy. For a number of years, under its commitment to ecological transition, the Group has been reducing the carbon footprint of all its businesses and putting the virtues of circular economy into practice. Still family-run, the Company cultivates a relationship of confidence with customers, partners, and employees on a daily basis. 2 Vicat Interview with… “Building and GUY SIDOS Chairman and CEO living together implies coming up with innovative, sustainable construction solutions” For the Vicat group, which is active represents 10% of the Group’s and replacing them with incinerable throughout the world, what were the production capacity. -
Portland Cement
International Conference on Transport, Civil, Architecture and Environment engineering (ICTCAEE'2012) December 26-27, 2012 Dubai (UAE) Portland Cement Alireza Baghchesaraei1 , Omid Reza Baghchesaraei2 kiln is fired by coal, the ash of the coal acts as a secondary raw Abstract— portland cement is the most common type of cement material. in general usage in many parts of the world, as it is a basic ingredient Portland cement was developed from cements (or correctly of concrete, mortar, stucco and most non-specialty grout. There are hydraulic limes) made in Britain in the early part of the different standards for classification of Portland cement. The two nineteenth century, and its name is derived from its similarity major standards are the ASTM C150 used primarily in the U.S. and to Portland stone, a type of building stone that was quarried on European EN-197. EN 197 cement types CEM I, II, III, IV, and V do the Isle of Portland in Dorset, England. Joseph Aspdin, a not correspond to the similarly-named cement types in ASTM C 150. Portland cement manufacture can cause environmental impacts at all British bricklayer, in 1824 was granted a patent for a process stages of the process. When cement is mixed with water a highly of making a cement which he called Portland cement. His alkaline solution (pH ~13) is produced by the dissolution of calcium, cement was an artificial hydraulic lime similar in properties to sodium and potassium hydroxides. the material known as "Roman Cement" (patented in 1796 by James Parker) and his process was similar to that patented in Keywords—New,Material,Portland Cement 1822 and used since 1811 by James Frost who called his cement "British Cement". -
Concrete Story-Telling (By New-Territories)
Concrete Story-Telling (by New-Territories) 1 ) Concrete in general Concrete is a material used in building construction, consisting of a hard, chemically inert particulate substance, known as an aggregate (usually made from different types of sand and gravel), that is bonded together by cement and water. The Assyrians and Babylonians used clay as the bonding substance or cement*1. The Egyptians used lime and gypsum cement. In 1756, British engineer, John Smeaton made the first modern concrete (hydraulic cement) by adding pebbles as a coarse aggregate and mixing powered brick into the cement. In 1824, English inventor, Joseph Aspdin invented Portland Cement, which has remained the dominant cement used in concrete production. Joseph Aspdin created the first true artificial cement by burning ground limestone and clay together. The burning process changed the chemical properties of the materials and Joseph Aspdin created a stronger cement than what using plain crushed limestone would produce. *1 cement : the word “cement” traces to the Romans, “caementicium”= masonry made from crushed rock with burnt lime as bindern referred to as “cementum,” “cimentum,” “cäment” and cement. The other major part of concrete besides the cement is the aggregate. Aggregates include sand, crushed stone, gravel, slag, ashes, burned shale, and burned clay. Fine aggregate (fine refers to the size of aggregate) is used in making concrete slabs and smooth surfaces. Coarse aggregate is used for massive structures or sections of cement. Concrete that includes embedded metal (usually steel) is called reinforced concrete or ferroconcrete. Iron reinforced concrete was invented (1849) by Joseph Monier, who received a patent in 1867. -
I on the Historv Oi Portland After 1 150 Years
Christopher Hall De~artmentof Bulldlnq I On the Historv oi Portland after University of Manchester . Institute of Science and Technology Manchester. England M60 1QD 1 150 Years Cementitious building materials have a long history, and began to build the third Eddystone lighthouse off the the date 1824, traditionally taken as the origin of portland southwest coast of Britain (4),apparently a labor of Hercu- cement, is in fact only the date of a patent (I) granted to les in the absence of a good hydraulic cement. Smeaton, ap- Joseoh Asodin (1778-1855) of Leeds. Eneland. who mav preciating the need to obtain the best component materials not at that'time have made portland cemeit at all. ~oday; fur the lime-pozzolana cement he intended to use, exam- cement is the successor to a line of materials with a historv ined a number of mixtures, and found that the quality de- reaching hack to the ancient world; it has a chemistry o? pended on the limestone (5). He made the important dis- perhaps unsurpassed complexity amongst major inorganic covery that the best mortars were made from limes con- industrial materials and is still the subject of intense study. taining clay impurities. We recognize now that the alumi- At some ~ointin the second quarter of the 19th century, nosilicate clay minerals are closely related to those in the about 150 ago, the cement as we know it now was fir& pozzolana, with this essential difference: that they are produced. burned intimately with the lime in the calcining process. It The very simplest of the mineral cements are those based soon emerged that certain heavily clay-bearing limestones on gypsum, hydrated calcium sulfate. -
Useful Natural History? Pest Control in the Focus of the Economic Society of Bern
USEFUL NATURAL HISTORY? PEST CONTROL IN THE FOCUS OF THE ECONOMIC SOCIETY OF BERN Martin Stuber and Regula Wyss Many scientific disciplines in the eighteenth century were increasingly oriented towards the needs of practice. This new understanding of sci- ence was linked to a utilitarian concept of nature, economic ideas about raising productivity, and political ideas focused on increasing prosper- ity and promoting “common weal” [Glückseligkeit]. The economic and patriotic societies that arose throughout Europe primarily in the second half of the eighteenth century emerged from this fundamental process of transformation into modernity, of which they were simultaneously the driving force.1 The Economic Society of Bern [Oekonomische Gesellschaft Bern], founded in 1759, was one of the most important of these societies, not least because of its dual-language publication organ, which was read The present article was written at the Institute of History of the University of Bern, in the context of a research project entitled “Useful Science, Nature Appropriation and Politics. The Economic Society of Bern in the European Context, 1750–1850” (headed by André Holenstein and Christian Pfister). This project is funded by the Swiss National Science Foundation, the Albrecht von Haller Foundation of the Burgergemeinde Bern, and the University of Bern Research Foundation. Some of the material used here was first pre- sented in a lecture by Martin Stuber at the Göttinger Umwelthistorisches Kolloquium (13 April 2005, moderated by Bernd Herrmann). Other parts are based on a lecture held by the authors as part of the lecture cycle of the Historical Society of the Canton of Bern (30 October 2009). -
The Mineral Industry of Switzerland in 2014
2014 Minerals Yearbook SWITZERLAND U.S. Department of the Interior December 2017 U.S. Geological Survey THE MINERAL INDUSTRY OF SWITZERLAND By Sinan Hastorun Switzerland is a highly developed, landlocked, and $675.3 billion (CHF642.3 billion1) in 2014. The slightly higher mountainous country in Central Europe that borders the rate of growth was mainly owing to increased net exports and, European Union (EU) member states of Austria, France, to a lesser degree, increased domestic private consumption. Germany, and Italy as well as the Principality of Liechtenstein. The gross value added from manufacturing and construction Few mineral commodities were mined in the country although increased by 2.0% in 2014, compared with a revised increase more than 1,000 mineral deposits (in particular, iron ore of 1.0% in 2013. Within manufacturing and construction, and manganese ore) have been identified on Swiss territory. the value added from manufacturing increased by 2.4% Switzerland’s mineral output consisted almost exclusively of compared with an increase of 0.7% (revised) in 2013, and that industrial minerals for the construction sector, refined precious of construction increased by 2.1% compared with 2.0% in the metals, and refined mineral fuels. Industrial minerals that previous year. The mining and quarrying sector contracted were mined and used on a large scale by industry were clay, in 2014; its value decreased by 5.3% in 2014 compared with gypsum, lime, and rock salt. Hydraulic cement and sulfur (from an increase of 1.9% (revised) in 2013 (Federal Statistical petroleum refining) were also produced. Construction aggregates Office, 2015c, e, h, i; European Commission, 2015, p. -
CORPORATE SOCIAL RESPONSIBILITY INFORMATION 2018 Aggregate Mining in Saint-Jean-Le-Vieux in Ain, France
CORPORATE SOCIAL RESPONSIBILITY INFORMATION 2018 Aggregate mining in Saint-Jean-le-Vieux in Ain, France 2 VICAT Corporate Social Responsibility Information 2018 Corporate Social Responsibility Information 2018 1. MESSAGE FROM THE CHAIRMAN AND CEO 4 2. PRESENTATION OF THE GROUP 7 3. STATEMENT OF EXTRA-FINANCIAL PERFORMANCE - 2018 31 4. CROSS-REFERENCE TABLE OF ITEMS IN THE STATEMENT OF EXTRA-FINANCIAL PERFORMANCE REPORT 64 GLOSSARY 66 VICAT Corporate Social Responsibility Information 2018 3 MESSAGE FROM THE CHAIRMAN AND CEO There is simply no alternative to cement to meet the need for construction materials in the years to come. Guy SIDOS Invented by Louis Vicat 200 years ago, is cement still a material of the future? There is simply no alternative to cement to meet the need for Each generation has successfully adapted the company to construction materials in the years to come. Given the scale of the contingencies of the times and nurtured it with passion population growth, cement, that is locally produced, is simply the before passing it on to the next generation, ever respectful only material available in sufficient quantity and at a sufficiently of the admirable work of the Group’s equally passionate affordable price. employees, without whom this growth would not have been The manufacturing and usage of this material that has brought possible. quality housing to so many people and provided protection In a global environment where business cycles in different and comfort to users for two centuries is changing in line countries are not necessarily synchronized, our model brings with sustainable development policies and circular economy resilience through geographic diversification. -
Background Facts and Issues Concerning Cement and Cement Data
Background Facts and Issues Concerning Cement and Cement Data By Hendrik G. van Oss Open-File Report 2005-1152 U.S. Department of the Interior U.S. Geological Survey ii U.S. Department of the Interior Gale A. Norton, Secretary U.S. Geological Survey P. Patrick Leahy, Acting Director For product and ordering information: World Wide Web: http://www.usgs.gov/pubprod Telephone: 1-888-ASK-USGS For more information on the USGS—the Federal source for science about the Earth, its natural and living resources, natural hazards, and the environment: World Wide Web: http://www.usgs.gov Telephone: 1-888-ASK-USGS Any use of trade, product, or firm names is for descriptive purposes only and does not imply endorsement by the U.S. Government. Although this report is in the public domain, permission must be secured from the individual copyright owners to reproduce any copyrighted material contained within this report. iii Preface This report is divided into two main parts. Part 1 first serves as a general overview or primer on hydraulic (chiefly portland) cement and, to some degree, concrete. Part 2 describes the monthly and annual U.S. Geological Survey (USGS) cement industry canvasses in general terms of their coverage and some of the issues regarding the collection and interpretation of the data therein. The report provides background detail that has not been possible to include in the USGS annual and monthly reports on cement. These periodic publications, however, should be referred to for detailed current data on U.S. production and sales of cement. It is anticipated that the contents of this report may be updated and/or supplemented from time to time.