Nov. 2, 1965 R
Total Page:16
File Type:pdf, Size:1020Kb
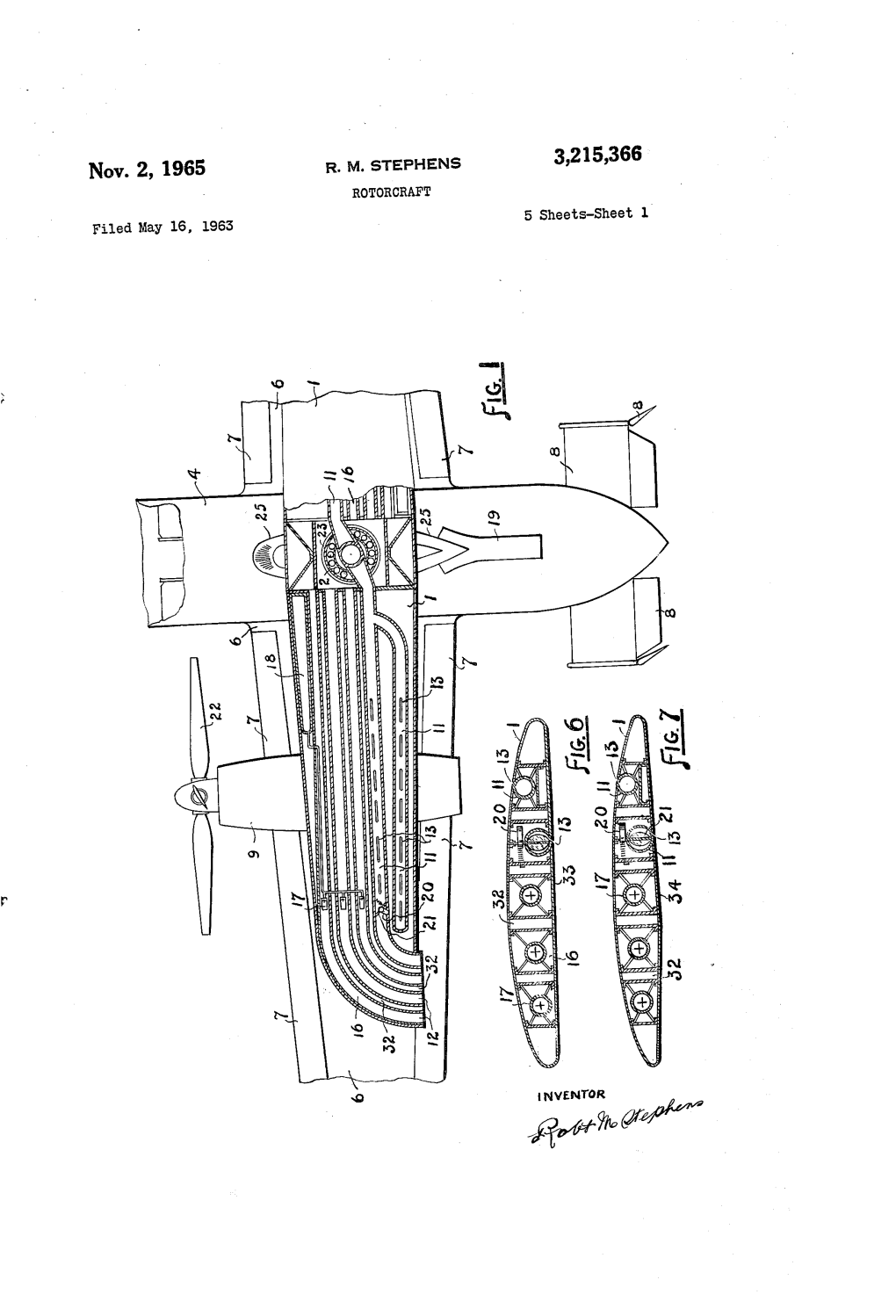
Load more
Recommended publications
-
Assessment of Navy Heavy-Lift Aircraft Options
THE ARTS This PDF document was made available from www.rand.org as a public CHILD POLICY service of the RAND Corporation. CIVIL JUSTICE EDUCATION Jump down to document ENERGY AND ENVIRONMENT 6 HEALTH AND HEALTH CARE INTERNATIONAL AFFAIRS The RAND Corporation is a nonprofit research NATIONAL SECURITY POPULATION AND AGING organization providing objective analysis and effective PUBLIC SAFETY solutions that address the challenges facing the public SCIENCE AND TECHNOLOGY and private sectors around the world. SUBSTANCE ABUSE TERRORISM AND HOMELAND SECURITY TRANSPORTATION AND INFRASTRUCTURE Support RAND WORKFORCE AND WORKPLACE Purchase this document Browse Books & Publications Make a charitable contribution For More Information Visit RAND at www.rand.org Explore RAND National Defense Research Institute View document details Limited Electronic Distribution Rights This document and trademark(s) contained herein are protected by law as indicated in a notice appearing later in this work. This electronic representation of RAND intellectual property is provided for non- commercial use only. Permission is required from RAND to reproduce, or reuse in another form, any of our research documents for commercial use. This product is part of the RAND Corporation documented briefing series. RAND documented briefings are based on research briefed to a client, sponsor, or targeted au- dience and provide additional information on a specific topic. Although documented briefings have been peer reviewed, they are not expected to be comprehensive and may present preliminary findings. Assessment of Navy Heavy-Lift Aircraft Options John Gordon IV, Peter A. Wilson, Jon Grossman, Dan Deamon, Mark Edwards, Darryl Lenhardt, Dan Norton, William Sollfrey Prepared for the United States Navy Approved for public release; unlimited distribution The research described in this report was prepared for the United States Navy. -
National Advisory Committee for Aeronautics
NATIONAL ADVISORY COMMITTEE FOR AERONAUTICS TECHNICAL NOTE 2154 AN ANALYSIS OF TIlE AUTOROTATIVE PERFORMANCE OF A BELICOPTER POWERED BY ROTOR-TIP JET UN[TS By Alfred Gessow Langley Aeronautical Laboratory Langley Air Force Base, Va. Washington July 1950 NATIONAL ADVISORY COMMITTEE FOR AERONAUTICS TECHNICAL NOTE 2l AN ANALYSIS OF THE AUTOROTATIVE PERFORMANCE OF A HELICOPTER POWERED BY ROTOR-TIP JET UNITS By Alfred Gessow SUMMARY The autorotative performance of an assumed helicopter was studied to determine the effect of inoperative jet units located at the rotor- blade tip on the helicopter rate of descent. For a representative ram- jet design, the effect of the jet drag is to increase the minimum rate of descent of the helicopter from about l,OO feet per minute to 3,700 feet per minute when the rotor is operating at a tip speed of approximately 600 feet per second. The effect is less if the rotor operates at lower tip speeds, but the rotor kinetic energy and the stall margin available for the landing maneuver are then reduced. Power-off rates of descent of pulse-jet helicopters would be expected to be less than those of ram- jet.helicopters because pulse jets of current design appear to have greater ratios of net power-on thrust to power-off, drag than currently designed rain jets. Iii order to obtain greater accuracy in studies of autorotative per- forimance, calculations in'volving high power-off rates of descent should include the weight-supporting effect of the fuselage parasite-drag force and the fact that the rotor thrust does not equal the weight of the helicopter. -
Over Thirty Years After the Wright Brothers
ver thirty years after the Wright Brothers absolutely right in terms of a so-called “pure” helicop- attained powered, heavier-than-air, fixed-wing ter. However, the quest for speed in rotary-wing flight Oflight in the United States, Germany astounded drove designers to consider another option: the com- the world in 1936 with demonstrations of the vertical pound helicopter. flight capabilities of the side-by-side rotor Focke Fw 61, The definition of a “compound helicopter” is open to which eclipsed all previous attempts at controlled verti- debate (see sidebar). Although many contend that aug- cal flight. However, even its overall performance was mented forward propulsion is all that is necessary to modest, particularly with regards to forward speed. Even place a helicopter in the “compound” category, others after Igor Sikorsky perfected the now-classic configura- insist that it need only possess some form of augment- tion of a large single main rotor and a smaller anti- ed lift, or that it must have both. Focusing on what torque tail rotor a few years later, speed was still limited could be called “propulsive compounds,” the following in comparison to that of the helicopter’s fixed-wing pages provide a broad overview of the different helicop- brethren. Although Sikorsky’s basic design withstood ters that have been flown over the years with some sort the test of time and became the dominant helicopter of auxiliary propulsion unit: one or more propellers or configuration worldwide (approximately 95% today), jet engines. This survey also gives a brief look at the all helicopters currently in service suffer from one pri- ways in which different manufacturers have chosen to mary limitation: the inability to achieve forward speeds approach the problem of increased forward speed while much greater than 200 kt (230 mph). -
E. E. W.M. PE Velocity Animproved Fight Control Method Is Utilized With
US00572.7754A United States Patent (19) 11 Patent Number: 5,727,754 Carter, Jr. 45) Date of Patent: Mar. 17, 1998 (54 GYROPLANE 4,928,907 5/1990 Zuck, 5,301,900 4/1994 Groen et al. ......................... 244,1725 75) Inventor: Jay W. Carter, Jr. Burkburnett, Tex. 5,462,409 10/1995 Frengley et al. ........................ 416/144 Primary Examiner-Galen L. Barefoot 73) Assignee: CarterCopters, L.L.C.. Wichita Falls, Attorney, Agent, or Fi Felsman, Bradley, Gunter & Tex. Dillon, LLP (21) Appl. No.: 521,690 57 ABSTRACT 22 Filed: Aug. 31, 1995 An improved gyroplane having an improved rotor blade (51) int. Clar. inchwith anper edgewise pound of stiffness aircraft gross(E) ofweight at least and 80,000 blade weightspounds (52) 244/8: 244/75 R; 24.4/17.11 of sufficient size to store a minimum of 100 foot pounds of 58) Field of Search .............................. 244/4 R., 6, 7 R. rotational kinetic energy per pound of gross weight of the 244/17.118 gyroplane while the rotor blade pitch is set to minimum lift during blade prerotation. Then a clutch driving the rotor is 56) References Cited disengaged and the rotor blade pitch is changed to a lift U.S. PATENT DOCUMENTS condition to enable the gyroplane to climb to an altitude of at least fifty feet. The speed and thrust of a propeller is D. 172,712 7/1954 Gebhard ................................. D2/335 increased to achieve an increasing a horizontal velocity to D. 178,598 8/1956 Fletcher. P22 maintain altitude, first with the rotor blade providing most of D. -
(12) United States Patent (10) Patent No.: US 8,991,744 B1 Khan (45) Date of Patent: Mar
USOO899.174.4B1 (12) United States Patent (10) Patent No.: US 8,991,744 B1 Khan (45) Date of Patent: Mar. 31, 2015 (54) ROTOR-MAST-TILTINGAPPARATUS AND 4,099,671 A 7, 1978 Leibach METHOD FOR OPTIMIZED CROSSING OF 35856 A : 3. Wi NATURAL FREQUENCIES 5,850,6154. W-1 A 12/1998 OSderSO ea. 6,099.254. A * 8/2000 Blaas et al. ................... 416,114 (75) Inventor: Jehan Zeb Khan, Savoy, IL (US) 6,231,005 B1* 5/2001 Costes ....................... 244f1725 6,280,141 B1 8/2001 Rampal et al. (73) Assignee: Groen Brothers Aviation, Inc., Salt 6,352,220 B1 3/2002 Banks et al. Lake City, UT (US) 6,885,917 B2 4/2005 Osder et al. s 7,137,591 B2 11/2006 Carter et al. (*) Notice: Subject to any disclaimer, the term of this 16. R 1239 sign patent is extended or adjusted under 35 2004/0232280 A1* 11/2004 Carter et al. ............... 244f1725 U.S.C. 154(b) by 494 days. OTHER PUBLICATIONS (21) Appl. No.: 13/373,412 John Ballard etal. An Investigation of a Stoppable Helicopter Rotor (22) Filed: Nov. 14, 2011 with Circulation Control NASA, Aug. 1980. Related U.S. Application Data (Continued) (60) Provisional application No. 61/575,196, filed on Aug. hR". application No. 61/575,204, Primary Examiner — Joseph W. Sanderson • Y-s (74) Attorney, Agent, or Firm — Pate Baird, PLLC (51) Int. Cl. B64C 27/52 (2006.01) B64C 27/02 (2006.01) (57) ABSTRACT ;Sp 1% 3:08: A method and apparatus for optimized crossing of natural (52) U.S. -
Propulsion System Based on Compressed Air Due to Rotor Blade Rotation
International Journal of Smart Grid and Clean Energy Propulsion system based on compressed air due to rotor blade rotation Aiman Elmahmodia*, Nikola Davidovicb, Ramadan A. Al-Madanic a Aeronautical Eng., Faculty of engineering-University of Tripoli, Tripoli - Libya b EDePro Jet Propulsion Laboratory, Begrade, Serbia cEngineering Faculty, Al-Jabel Algharbi University, Tripoli – Libya Abstract The theoretical and experimental investigation of the potential of jet propulsion system to drive rotor of (VTOL) Vertical Takeoff and Landing aircraft has been presented. The analysis of tip jet propulsion system is based on compressed air due to rotor blade rotation. The system performances were compared in the case of the rotor with rocket, and pressure-jet engine. Rocket engine had practical application in middle of 20th century, while the present work tip jet pressure propulsion system is based on turbojet thermodynamic cycle. Comparison has been performed according to available and required power, and to flight duration. Performances of the present propulsion system were also analyzed with introduction of typical rotor geometry. Analysis shows possible application of such propulsion as unmanned or low-weight helicopters and Vertical Take-Off and Landing (VTOL) vehicles. Keywords: Helicopter rotor, tip jet, flying vehicle, unmanned helicopters, pressure jet. Nomenclature ma Air inlet mass flow rate (kg/sec) n number of rotor blades mf Fuel mass flow rate (kg/sec) M payload (Kg) me exit mass flow rate (kg/sec) f fuel – air mixture ratio cpa Specific heat (J/kg.K) P Power (w) Ta Ambient temperature (K) PROT Rotor useful power (w) Csp specific fuel consumption (kg/Nh) Pdrag drag power (w) γ Specific heat ratio F Thrust (N) πr pressure ratio of the rotor blade. -
Model Predictive Control (Mpc) Algorithm for Tip- Jet Reaction Drive
MODEL PREDICTIVE CONTROL (MPC) ALGORITHM FOR TIP- JET REACTION DRIVE SYSTEMS A Thesis Presented to The Academic Faculty by Brian Kestner In Partial Fulfillment of the Requirements for the Degree Doctor of Philosophy in the School of Aerospace Engineering Georgia Institute of Technology December 2009 MODEL PREDICTIVE CONTROL (MPC) ALGORITHM FOR TIP- JET REACTION DRIVE SYSTEMS Approved by: Prof. Dimitri N. Mavris, Advisor Dr. Jimmy Tai School of Aerospace Engineering School of Aerospace Engineering Georgia Institute of Technology Georgia Institute of Technology Dr. Tim Healy Mr. Randy Rosson Gas Turbine Combustion Engineering Gas Turbine Performance Methods General Electric Energy General Electric Energy Prof. Brian German School of Aerospace Engineering Georgia Institute of Technology Date Approved: November 13, 2009 ACKNOWLEDGEMENTS I would like to thank my advisor, Professor Dimitri Mavris, for giving me the opportunity to join the ASDL and pursue my PhD. In addition to providing me with this opportunity, his philosophy towards research was most inspiring. I would like to especially thank Dr. Jimmy Tai for all the support, advice, and help over the last five years. The formulation of this dissertation came out of our weekly meetings. I could not have completed this dissertation without his help. I would like to thank Dr. Tim Healy and Mr. Randy Rosson. The feedback and help provided was always most enlightening, even though it usually took me awhile to realize it. I would to thank Professor Brian German for always keeping an eye on me. To the love of my life, Gina Martell, thank you for being there through all the good and the bad. -
Helicopter Society (AHS) International STEM Committee: Free to Distribute with Attribution History of Rotorcraft
History and Overview of Rotating Wing Aircraft Photo by Paolo Rosa Produced by the American Helicopter Society (AHS) International STEM Committee: www.vtol.org/stem Free to distribute with attribution History of Rotorcraft • Definition of Rotorcraft – Any flying machine using rotating wings to provide lift, propulsion, and control that enable vertical flight and hover Rotating wings provide propulsion, Rotating wings provide lift, but negligible lift and control. propulsion, control at same time. History of Rotorcraft • Two key configurations developed in parallel – Autogiro • Close to helicopter, uses many of same mechanical feature • Cannot hover • Unpowered rotor – Helicopter • Powered rotor • Many configurations have been developed • Autogiros flew first! – Autogiro innovations enabled development of first helicopters Autogyro – How it Works Lift Unpowered Rotor that Spins Due to Wind Blowing Through Rotor Like a Wind Turbine Relative Wind No Need for Anti-Torque Since Not Driven Thrust By an Engine Fixed to the Fuselage Control Surfaces Autogyro – How it Works Kind of like parasailing, except rotor provides lift in addition to drag. Helicopter – How it Works • Powered Rotor • Equal and opposite torque applied to rotor acts on fuselage Tail Rotor Rotor Thrust Thrust Main Rotor Drive Shaft Tail Boom Cockpit Tail Rotor Engine, Fuel, Landing Skids Transmission, etc. Controls Helicopter – Need for Anti-Torque • Engine fixed on body – exerts torque on rotor shaft – Rotor shaft exerts equal and opposite torque on body • Many configurations -
The Evolution of the British Rotorcraft Industry 1842-2012
Journal of Aeronautical History Paper No. 2012/07 THE EVOLUTION OF THE BRITISH ROTORCRAFT INDUSTRY 1842-2012 Eur Ing David Gibbings C Eng., FRAeS Based on a paper originally presented to the European Rotorcraft Forum in Hamburg, September 2009. ABSTRACT This paper relates the way in which rotorcraft developed in Britain, leading to the growth of an effective design and manufacturing industry. The narrative is divided into five sections, each of which represents defining phases in UK based activity leading towards the development of the modern helicopter: 1. The Pre-Flight Period (1842-1903) This section covers British activity during the period when the objective was simply to demonstrate powered flight by any means, and where rotors might be considered to be a way of achieving this. 2. The Early Helicopter Period (1903-1926). Early attempts to build helicopters, including the work of Louise Brennan, which achieved limited success with a rotor driven by a propellers mounted on the blade tips. 3. The Pre-War Years (1926-1939) This section gives emphasis to development of the gyroplane and in particular the work of Juan de la Cierva, with his UK-based company to develop his 'Autogiro', from which the understanding of rotor dynamics and control was established, and which was to lead to the realisation of the helicopter by others. Although UK rotary wing development was driven by the gyroplane, the work carried out by the Weir Company, which was to lead to the first successful British helicopter is discussed. 4. The War Years. (1939-1945) Rotary wing activities in the UK were very limited during World War 2, restricted to the work carried out by Raoul Hafner with the Rotachute/ Rotabuggy programme and the use of autogiros for the calibration of radar. -
Design Solution and Structural Optimisation of Feathering Hinge Assembly of Teetering Rotor Head for Tip-Jet Helicopters
DESIGN SOLUTION AND STRUCTURAL OPTIMISATION OF FEATHERING HINGE ASSEMBLY OF TEETERING ROTOR HEAD FOR TIP-JET HELICOPTERS NENAD KOLAREVIĆ University of Belgrade, Faculty of Mechanical Engineering, Belgrade, [email protected] MILOŠ STANKOVIĆ University of Belgrade, Faculty of Mechanical Engineering, Belgrade, [email protected] NIKOLA DAVIDOVIĆ University of Belgrade, Faculty of Mechanical Engineering, Belgrade, [email protected] MARKO MILOŠ University of Belgrade, Faculty of Mechanical Engineering, Belgrade, [email protected] Abstract: If one compares the tip-jet helicopters to the conventional ones, one of the most important disadvantages are the much heavier blades, due to the massive inner channel for operating fluid transport through its structure. This increased blade mass causes a significantly larger centrifugal force that loads the construction of the rotor head, especially the feathering and teetering hinge. The case study of this paper is feathering hinge assembly of teetering rotor head for ultra- light tip-jet unmanned helicopter. The new design solution and structural optimization for such engineering problem is presented in this paper. The described construction solution is developed for a new project of unmanned helicopter Hussar based on the experience and knowledge achieved on the previous helicopters ATRO-X and Hornet. Keywords: tip-jet helicopter, feathering hinge, rotor head, structural optimization, design solution. 1. INTRODUCTION compared to the light aluminum or composite blades of the conventional helicopters. On the other hand, tip-jet The tip-jet helicopters are very rare and specific in design. helicopters require a larger diameter of the rotor disk and This concept is based on the propulsion force on the blade larger speed of rotation than the conventional helicopters. -
Advantageous Autorotation
The DARPA Heliplane aimed to Advantageous double helicopter performance in a VTOL platform without the complexity of a helicopter transmission or anti-torque system. Autorotation (All images via Skyworks Global) Skyworks Global plans to commercialize affordable autorotating aircraft in regions without aviation infrastructure and looks to revive DARPA Heliplane technology for speed, range and vertical takeoff. By Frank Colucci hile sustained autorotative flight found a lasting market in recreational gyroplanes, the technology Whas broader potential. Skyworks Global last year re- branded the Groen Aeronautics line of gyrocraft and plans to What’s in a Name? commercialize the technology for more users — this summer with the SparrowHawk III kit gyroplane, then with the larger Autogiro: the original term, trademarked and licensed by Juan de la Cierva, for an aircraft using an Hawk 5 gyroplane built offshore, and potentially with big, tip-jet- autorotating rotor for lift plus one or more propellers driven gyrodynes that can take off and land vertically and hover. for thrust. “What we’re going to solve is two-thirds of the world’s aviation autogyro: the general term for an autorotating requirements,” stated Skyworks’ executive committee director, aircraft, particularly one that was not a licensed retired US Air Force Brig. Gen. John Michel. “No one has paid Cierva Autogiro. The FAA recognizes the name attention to the two-thirds of the world with no infrastructure, “gyroplane” instead. no educated workforce — gyrocraft are built for that.” Skyworks AutoGyro: a German company that produces over Global’s “simple, elegant solution” of a freewheeling rotor with 300 gyroplanes annually. collective pitch control is protected by patents to make gyrocraft Gyrocopter: this term was trademarked by Igor safer and more flexible. -
Gluhareff Pressure Jet Engine: Past, Present and Future
Gluhareff Pressure Jet Engine: Past, Present and Future Ronald Barrett* The University of Kansas, Lawrence, Kansas 66045 and Irina Gluhareff† Gluhareff Helicopters LLC, Valencia, CA 91355 This paper is an historical overview of one of the more unrecognized technologists and classes of jet engines the technical community has known. Although not featured in any classic text of yesteryear or today, the engine was first reduced to practice more than 50 years ago. The engine as a whole and enabling components have been covered in several patents, flown thousands of times and boasts a total production run in the thousands. The paper outlines the history of the engine's inventor, Mr. Eugene M. Gluhareff, starting from his education at Rensselaer Polyetchnic Institute, moving through Sikorsky Aircraft Corporation and finally ending up in private business. The basic physics of the engine is also explained along with its similarities to other athodyds and several profound differences. The paper outlines the current state of pressure jet engines of this family and describes new improvements which continue to add performance to this dark horse of the jet engine family. Nomenclature f = fuel-to-air ratio Po = stagnation pressure of flow ma = mass flow rate of air Poa = stagnation pressure of airflow mf = mass flow rate of fuel Pof = stagnation pressure of fuel ηi = inlet total pressure conversion efficiency I. The Inventor: Eugene M. Gluhareff A. The Formative Years: Russia, Emigration, Rensselayer, United Aircraft Corporation UGENE M. Gluhareff was born in St. Petersburg, Russia in 1916 to a family of landed technologists and E educators. After emigrating to the United States with his family via Finland in the early 1920's, he enrolled in Rensselaer Polytechnic Institute in Troy, New York where he earned a Bachelor's Degree in Aeronautical Engineering in 1942.