(12) Patent Application Publication (10) Pub. No.: US 2010/0099806 A1 Houze Et Al
Total Page:16
File Type:pdf, Size:1020Kb
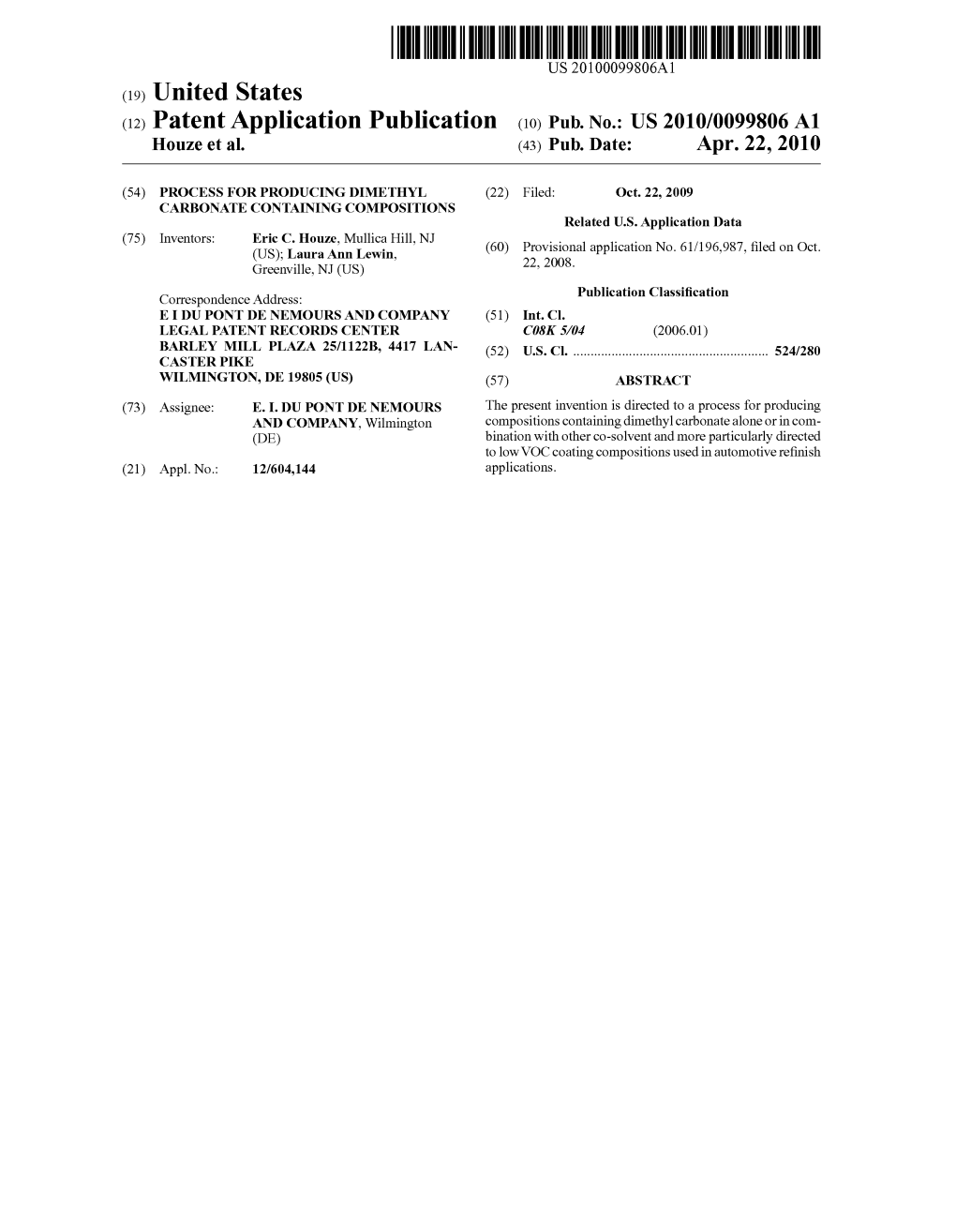
Load more
Recommended publications
-
2010CTS-Proceedings-Wacenske
Understanding Volatile Organic Compound (VOC) Regulations in the Roofing Industry DWAYNE WACENSKE Firestone Building Products 250 West 96th Steeet, Indianapolis, IN 46260 Phone: 3178163856 • Email: [email protected] Proceedings of the RCI 25th International Convention Wachenske 243 ABSTRACT There have been many changes in the regulations governing materials used in the roofing industry in recent years. The regulations set maximum allowable amounts of volatile organic compounds (VOC) that products may contain. Complicating matters is that these rules and regulations are being enacted at the state level and sometimes on the local level, making it very difficult for the roofing community to understand their obligations and responsibilities. This paper will try to clarify these rules and regulations as well as the implementation of them. A discussion on the products available to meet these requirements will also be included. SPEAKER Dwayne Wacenske is the TPO product manager for Firestone Building Products. Wacenske has more than 20 years of experience in the plastics industry and 10 years in the roofing industry. Wacenske holds a bachelor of science degree in chemistry from the University of Akron. Wachenske 244 Proceedings of the RCI 25th International Convention Understanding Volatile Organic Compound (VOC) Regulations in the Roofing Industry INTRODUCTION these rules and regulations as well as ozone. Groundlevel ozone is an air There have been many changes in the implementation of them. A dis pollutant that is harmful to breathe, the regulations governing materials cussion on the strategies employed to damages crops, trees and other vege used in the lowslope commercial meet these requirements also is tation, and is the main ingredient of roofing industry in recent years. -
Tert-Butyl Acetate: VOC-Exempt Solvent for Coatings Outline
Tert-Butyl Acetate: VOC-Exempt Solvent for Coatings Outline • Solvent Use in Coatings • Solvent Regulations • Tert-Butyl Acetate as a VOC replacement – TBAC properties – Formulating compliant products with TBAC • Lacquers • Urethanes • Epoxies • Alkyds • Conclusions | www.lyondellbasell.com | 2 Solvent Uses in Coatings and Adhesives • Resin Synthesis – Acrylics, alkyds • Formulation – Resin solubilization – Pigment grinding • Surface Preparation – Parts degreasing • Application – Viscosity reduction – Surface wetting – Flow and leveling – Hardness development and curing • Cleanup – Spray gun cleanup | www.lyondellbasell.com | 3 Solvent Regulations Multiply… • International Regulations – Montreal protocol on ozone depleting substances (ODS) • National Regulations – Control of Volatile Organic Compounds (VOCs) – Control of Hazardous Air Pollutants (HAPs) • State and local regulations • Grass roots initiatives | www.lyondellbasell.com | 4 Grass Roots: Green Building Initiatives • EPA lacks jurisdiction to regulate indoor air quality • Health and environmental concerns: – Indoor air quality (VOCs, HAPs, ozone, PM, mold, pollen, etc… ) – Materials safety (lead, asbestos, phthalates) – Efficient use of resources (energy and materials) – Environmental impact of products (global warming, pollution, ozone depletion) • Leading to new product certification requirements: – Leadership in Energy and Environmental Design (LEED rating) – Green Seal product standards: • Commercial Adhesives (GS-36) • Paints and Coatings (GS-11) • Stains and Finishes (GS-47) -
Toxicity Assessment of Dimethyl Carbonate Following 28 Days Repeated Inhalation Exposure
Vol: 36(2), Article ID: e2021012, 9 pages https://doi.org/10.5620/eaht.2021012 eISSN: 2671-9525 Original Article Toxicity assessment of dimethyl carbonate following 28 days repeated inhalation exposure Dongseok Seo 1 ,* 1 Toxicological Study Department, Occupational Safety and Health Research Institute, KOSHA, Korea *Correspondence: [email protected] Received: April 21, 2021 Accepted: June 10, 2021 Abstract Dimethyl carbonate (DMC) has been used as a reagent in methylation reactions, can be used as paints, coatings, and adhesives, and is a chemical that is being used increasing, which poses a health hazard to workers who handle it. So, the toxic reactions of F344 rats with inhalation exposure to 600, 1600, and 5000 ppm concentrations for 6 hours, 5 days a week, 4 weeks was evaluated. During the exposure period, general signs were observed, body weight and food consumption were measured, and hematologic and blood biochemical tests, organ weight measurements, necropsy, and histopathological examination were performed after the end of exposure. During the exposure period, dimethyl carbonate was exposed to an average of 599.26±31.40, 1614.64±80.79 and 5106.83±297.13 ppm in the chambers of the T1, T2 and T3 test groups, respectively. During the test period, general signs, weight change, food consumption, organ weight measurement, necropsy, and histopathological examination did not show any effects related to exposure to the test substance. However, as a result of blood and blood biochemical tests, an increase in AST, ALP, APTT, and PT levels was observed. From these results, it is judged that liver is the target organ when repeated inhalation exposure of dimethyl carbonate, the test substance, for 4 weeks, and the exposure-related effects of the test substance were observed at PT and ALP levels up to 600 ppm exposure concentration, but NOEC (No Observed Effect Concentration) was determined to be less than 600 ppm because it was not judged as an adverse effect. -
Safety Data Sheet
SAFETY DATA SHEET 1. Identification Product identifier ZERO VOC EXEMPT SOLVENT Other means of identification Product code 8020 Recommended use Industrial applications. Recommended restrictions Professional use only Manufacturer/Importer/Supplier/Distributor information Manufacturer Company name Ellis Paint Company Address 3150 E. Pico Blvd. Los Angeles, CA 90023-3683 United States Telephone Customer Service (800) 672-4900 Website www.ellispaint.com E-mail [email protected] Emergency phone number CHEMTREC (800) 424-9300 2. Hazard(s) identification Physical hazards Flammable liquids Category 2 Health hazards Serious eye damage/eye irritation Category 2A Specific target organ toxicity, single exposure Category 3 respiratory tract irritation Specific target organ toxicity, single exposure Category 3 narcotic effects Aspiration hazard Category 1 Environmental hazards Not classified. OSHA defined hazards Not classified. Label elements Signal word Danger Hazard statement Highly flammable liquid and vapor. May be fatal if swallowed and enters airways. Causes serious eye irritation. May cause respiratory irritation. May cause drowsiness or dizziness. Precautionary statement Prevention Keep away from heat/sparks/open flames/hot surfaces. - No smoking. Keep container tightly closed. Ground/bond container and receiving equipment. Use explosion-proof electrical/ventilating/lighting equipment. Use only non-sparking tools. Take precautionary measures against static discharge. Avoid breathing mist or vapor. Wash thoroughly after handling. Use only outdoors or in a well-ventilated area. Wear eye protection/face protection. Wear protective gloves/eye protection/face protection. Response If swallowed: Immediately call a poison center/doctor. If on skin (or hair): Take off immediately all contaminated clothing. Rinse skin with water/shower. If inhaled: Remove person to fresh air and keep comfortable for breathing. -
Immunotoxicity and Allergic Potential Induced by Topical Application of Dimethyl Carbonate (DMC) in a Murine Model
HHS Public Access Author manuscript Author Manuscript Author ManuscriptJ Immunotoxicol Author Manuscript. Author Author Manuscript manuscript; available in PMC 2015 November 19. Published in final edited form as: J Immunotoxicol. 2013 ; 10(1): 59–66. doi:10.3109/1547691X.2012.691124. Immunotoxicity and allergic potential induced by topical application of dimethyl carbonate (DMC) in a murine model Stacey E. Anderson, Jennifer Franko, Katie L. Anderson, Albert E. Munson, Ewa Lukomska, and B. Jean Meade National Institute for Occupational Safety and Health (NIOSH), Morgantown, WV, USA Abstract Dimethyl carbonate (DMC) is an industrial chemical, used as a paint and adhesive solvent, with the potential for significant increases in production. Using select immune function assays, the purpose of these studies was to evaluate the immunotoxicity of DMC following dermal exposure using a murine model. Following a 28-day exposure, DMC produced a significant decrease in thymus weight at concentrations of 75% and greater. No effects on body weight, hematological parameters (erythrocytes, leukocytes, and their differentials), or immune cell phenotyping (B- cells, T-cells, and T-cell sub-sets) were identified. The IgM antibody response to sheep red blood cell (SRBC) was significantly reduced in the spleen but not the serum. DMC was not identified to be an irritant and evaluation of the sensitization potential, conducted using the local lymph node assay (LLNA) at concentrations ranging from 50–100%, did not identify increases in lymphocyte proliferation. These results demonstrate that dermal exposure to DMC induces immune suppression in a murine model and raise concern about potential human exposure and the need for occupational exposure regulations. -
Tbac™ Solvent: a New Tool for VOC-Compliant Adhesives and Sealants
TBAc™ Solvent: A New Tool for VOC-Compliant Adhesives and Sealants Outline • Solvent use in adhesives and sealants • Solvent regulations and Green Building initiatives • Tert-Butyl Acetate as a compliance tool – TBAC properties – Adhesive resin solubility – Sample reformulation • Conclusions | www.lyondellbasell.com | Solvent Use in Adhesives & Sealants • Resin Synthesis • Adhesive/Sealant Formulation • Surface Preparation – Parts degreasing – Hand wipe cleaning • Application – Viscosity reduction – Surface wetting and penetration – Green strength • Cleanup – Spray gun cleanup – Adhesive and sealant removers | www.lyondellbasell.com | Solvent Regulations Multiply… • International Regulations – Montreal protocol on ozone depleting substances (ODS) • National Regulations – Control of Volatile Organic Compounds (VOCs) – Control of Hazardous Air Pollutants (HAPs) • State and local regulations • Grass roots initiatives | www.lyondellbasell.com | Emerging Issues: Green Building and Indoor Air Quality • Health and environmental concerns: – Indoor air quality (VOCs, HAPs, ozone, PM ) – Materials safety (lead, asbestos, phthalates) – Efficient use of resources (energy and materials) – Environmental impact of products (global warming, persistence, ozone depletion) • Leading to new product certification requirements: – Leadership in Energy and Environmental Design (LEED rating) – Green Seal product standards: • Commercial Adhesives (GS-36) • Paints and Coatings (GS-11) • Stains and Finishes (GS-47) | www.lyondellbasell.com | Benefits of “Greener” -
(12) Patent Application Publication (10) Pub. No.: US 2006/0128589 A1 Shriner (43) Pub
US 2006O128589A1 (19) United States (12) Patent Application Publication (10) Pub. No.: US 2006/0128589 A1 Shriner (43) Pub. Date: Jun. 15, 2006 (54) LOW VOC AIR INTAKE SYSTEM CLEANER Related U.S. Application Data (60) Provisional application No. 60/634,721, filed on Dec. (75) Inventor: Kenneth E. Shriner, Wichita, KS (US) 9, 2004. Publication Classification Correspondence Address: (51) Int. Cl. SHOOK, HARDY & BACON LLP CLID (7/00 (2006.01) INTELLECTUAL PROPERTY DEPARTMENT (52) U.S. Cl S10/407: 51O/499 2555 GRAND BLVD Oa - - - - - - - - - - - - - - - - - - - - - - - - - - - - - - - - - - - - - - - - - - - - - - - - s KANSAS CITY, MO 64108-2613 (US) (57) ABSTRACT Disclosed is a method and a Volatile Organic Compound (73) Assignee: BG Products, Inc., Wichita, KS (VOC) cleaning composition for cleaning the air intake system of a engine, the cleaning composition comprising, a pyrrolidinone, an alcohol, and a VOC solvent. The Volatile (21) Appl. No.: 11/298,254 Organic Compound (VOC) cleaning composition is used to clean contaminants from the plenum of an internal combus tion engine by spraying or otherwise introducing the com (22) Filed: Dec. 9, 2005 position into the plenum. US 2006/O128589 A1 Jun. 15, 2006 LOW VOC AIR INTAKE SYSTEM CLEANER 0009. This chemistry includes a combination of: (i) sol vents in which VOC compliance is required, and (ii) VOC CROSS-REFERENCE TO RELATED exempt solvents. The formulation meets specific viscosity APPLICATIONS and volatility requirements, and utilizes a synergistic inter action which occurs between a pyrrolidinone and an alcohol. 0001) This application claims the benefit of U.S. Provi Preferably a volatile alcohol. These agents have been shown sional Application No. -
Development of Azeotropic Blends to Replace TCE and Npb in Vapor Degreasing Operations
Development of Azeotropic Blends to Replace TCE and nPB in Vapor Degreasing Operations Darren L. Williams, Ph.D. Chemistry Department, Sam Houston State University, Huntsville, TX 77341 [email protected] (936)294-1529 December 21, 2016 Final Report Strategic Environmental Research and Development Program Weapons Systems and Platforms (WP-2522) US Army Corps of Engineers, Contract W912HG-14-C-0062 Dr. Robin Nissan, WP Program Manager [email protected] (571)372-6399 Table of Contents Table of Contents ............................................................................................................................ ii List of Tables ................................................................................................................................. iii List of Figures ................................................................................................................................ iv List of Acronyms ........................................................................................................................... vi Keywords ..................................................................................................................................... viii Acknowledgments.......................................................................................................................... ix Abstract ........................................................................................................................................... 1 Objectives ...................................................................................................................................... -
Amend Rule 102 – Definition of Terms
BOARD MEETING DATE: May 2, 2014 AGENDA NO. 28 PROPOSAL: Amend Rule 102 – Definition of Terms SYNOPSIS: The proposed amendment exempts trans 1-chloro-3,3,3- trifluoropropene from the VOC definition of the rule. The U.S. EPA has already exempted the compound from the federal VOC definition because of its negligible photochemical reactivity level. COMMITTEE: Stationary Source, February 21, 2014, Reviewed RECOMMENDED ACTIONS: Adopt the attached resolution: 1. Certifying the Notice of Exemption for Proposed Amended Rule 102 - Definition of Terms; and 2. Amending Rule 102 – Definition of Terms. Barry R. Wallerstein, D.Env. Executive Officer EC:PF:NB:DD:RC __________________________________________________________________________________________________________________ Background The U.S. EPA delisted trans 1-chloro-3,3,3-trifluoropropene (also known as HFO- 1233zd) from the federal VOC definition because of its negligible contribution to the formation of tropospheric ozone. In October 2013, Honeywell, Inc. petitioned the SCAQMD to include HFO-1233zd as a VOC-exempt compound in Rule 102 – Definition of Terms. The proposed compound has good cleaning properties and is expected to be used as a compliant substitute solvent for HCFC-225 in vapor degreasing operations for precision cleaning of critical parts used in aerospace and military applications. HCFC-225 is classified as a Class II Ozone Depleting Substance under the Clean Air Act, and is being phased out by the end of 2014. HFO-1233zd may also be used as a blowing agent for closed cell insulating foams, aerosol cleaner for electronics cleaning, and as a refrigerant in chillers. However, SCAQMD staff is not aware of any transition for these uses, and does not anticipate a shift towards a more expensive option in the absence of any other regulatory drivers. -
(12) United States Patent (10) Patent No.: US 9.422,434 B2 Ledford Et Al
USOO9422434B2 (12) United States Patent (10) Patent No.: US 9.422,434 B2 Ledford et al. (45) Date of Patent: Aug. 23, 2016 (54) LOW VOC COATING REDUCERS 6,306,943 B1 * 10/2001 Henry ................ CO8G 18,0852 252,364 (71) Applicant: Pilgrg Service Co., Inc., Pearland, 7,438,9526,538,143 B1B2 10/20083/2003 ConnellyPinschmidt, et al.Jr. et al. (U ) 7,785,413 B2 8, 2010 Bortz 8,076,414 B2 12/2011 Power (72) Inventors: John S. Ledford, Pearland, TX (US); 8,329,634 B2 12/2012 Bortz Jason Olson, Pearland, TX (US); John 8,337,608 B2 12/2012 Bortz Kuca, Pearland, TX (US); Katia Baizan, 8,557,343 B2 10/2013 Bateman et al. Pearland, TX (US); Jean-Pierre Baizan, 8,961,680 B2 * 2/2015 Pasin ..................... CO9D106,311 7 OO1 Pearland, TX (US); Lynn Place, 2003/0207121 A1 11/2003 McGee Pearland, TX (US); Amber Livesay, 2006/0233.955 A1 10, 2006 Smith et al. Pearland, TX (US) 2007/0001492 A1 1/2007 Chang 2007, OO14926 A1 1/2007 Stricker et al. (73) Assignee: PACKAGING SERVICE CO, INC., 2008. O139437 A1* 6, 2008 Power .................... Cope's Pearland, TX (US) 2009/0000549 A1 1/2009 Wang et al. 2010.00998.06 A1* 4/2010 Houze .................. CO8K 5.0025 (*) Notice: Subject to any disclaimer, the term of this 524/28O patent is extended or adjusted under 35 2010/0240573 A1* 9/2010 Zysman ................... C1 58.: U.S.C. 154(b) by 0 days. 2010/0272883 A1 10, 2010 Wirz et al. 2010/02799.12 A1* 11, 2010 Bortz ....................