Fundamentals of Roof Lnspections by William M
Total Page:16
File Type:pdf, Size:1020Kb
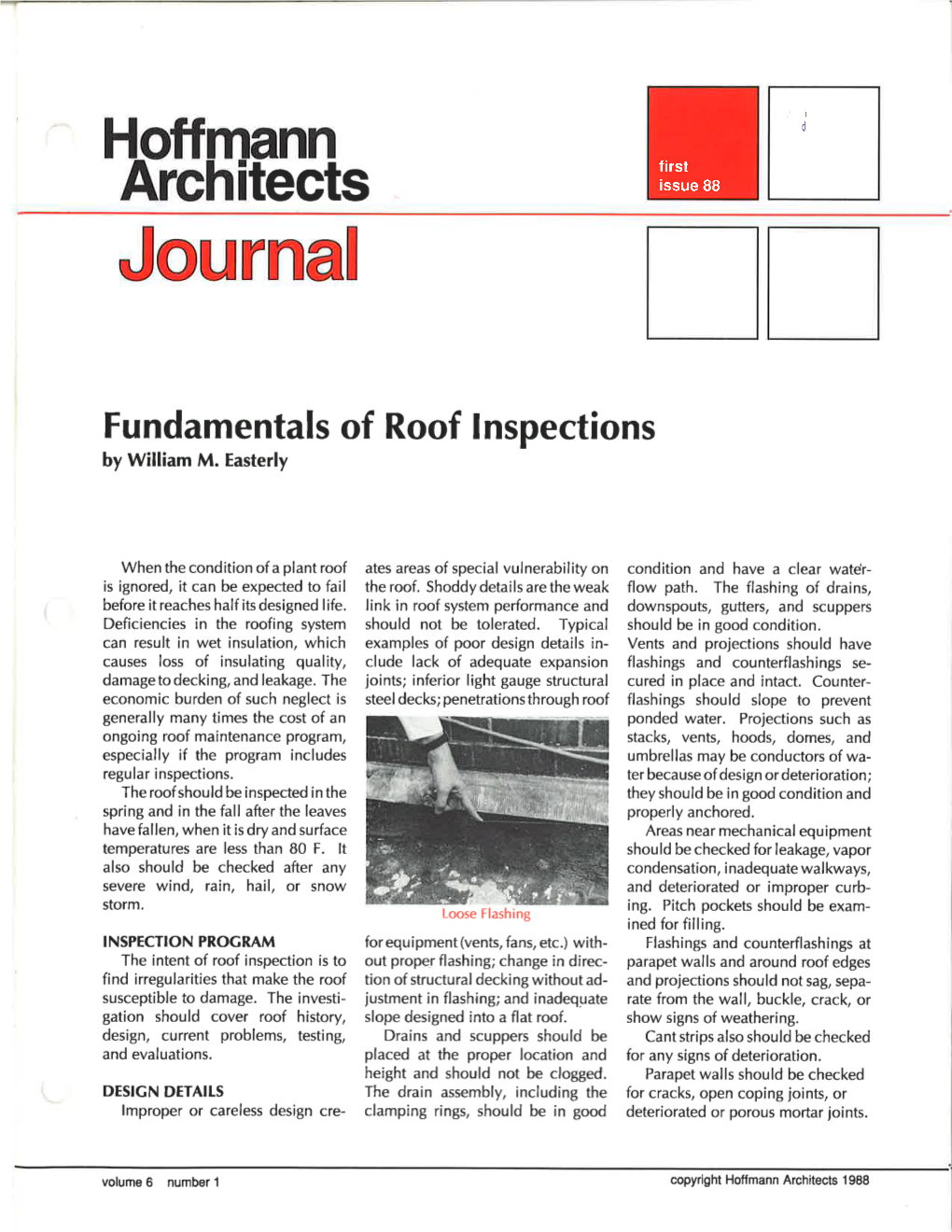
Load more
Recommended publications
-
The Building Envelope: Energy Efficiency and Economics
ISSUE 4/2009 V O L U M E 2 6 N U M B E R 4 Journal of architectural technology published by Hoffmann Architects, Inc., specialists in the rehabilitation of building exteriors. The Building Envelope: Energy Efficiency and Economics Richard P. Kadlubowski, AIA and Dean W. Yates, AIA According to the U.S. Environmen- As these structures age, we are tal Protection Agency (EPA), the con- faced with a choice: rehabilitate and struction and operation of buildings is upgrade the inefficient buildings, or responsible for nearly half of America’s replace them. greenhouse gas emissions. In com- With landmark and historic struc- parison, all forms of transportation tures, the importance of preserving combined—including airplanes, trucks, the existing building is clear. But what buses, and cars—account for just a about buildings that are neither ef- quarter of total emissions. Because so ficient nor architecturally significant? much of the country’s building stock Replacing an old building with a new was constructed when fuel was cheap one uses energy. That energy takes and plentiful, little regard was paid to many, many years to recover through designing energy-saving enclosures. improved performance—if at all. A better approach, then, is to improve the energy profile of the buildings we already have. To cut back on energy consumption, federal, state, and local authorities have adopted increasingly rigorous standards for building performance. These regulations, along with tax incentives for improved energy man- agement, have led to an upsurge in energy efficiency retrofits for existing structures. Before investing in major capital improvements to heating and cooling systems, however, consider making simple, less costly upgrades to the building enclosure. -
Thin-Stone Veneers Offer Unique Design and Performance Demands
Journal of architectural technology published by Hoffmann Architects, specialists in exterior rehabilitation Third Issue 1997 Volume 15 Number 3 Thin-Stone Veneers Offer Unique Design and Performance Demands relatively new product known as rein- Theodore F. Babbitt, AIA forced stone veneer is also available. Made of very thin stone veneers N ew stone-cutting technologies laminated with epoxy to a reinforcing have allowed for ever-thinner stone expanded-steel mesh, these reinforced veneers to be used as a curtain-wall stone panels come in 5/16" and 3/16" component on high-rise and other thicknesses and offer the strength of buildings, a radical departure from the stone veneers twice their thickness. traditional use of dimension stone as This new technology was developed in a load-bearing element or a heavy- Turin, Italy and to date has been used in weight, non-load bearing facade. But Europe and New York City. while these veneers offer an excellent design opportunity at a cost lower An Intrinsic Danger than dimension stone, relatively little While the engineering principles and data is available on their long-term physical properties of dimension stone performance. And problems are are well understood and tested by starting to crop up after just two time, thin-stone veneers offer a new decades of use. Owners, architects, realm of design, engineering, fabrica- and builders should be forewarned tion, transport, and installation when choosing thin-stone veneers: demands. Testing prior to installation precise detailing is essential to may show no problems, but under prevent displacement, cracking, real-world conditions, veneers may spalling, water intrusion, and, ulti- begin to display unexpected and mately, failure. -
Hoffmann Architects, Inc. G000
DRAWINGS G000 COVER SHEET G001 SITE PLAN, ABBREVIATIONS, SYMBOLS, AND NOTES A101 FLOOR PLANS A201 EAST AND SOUTH ELEVATIONS A202 WEST AND NORTH ELEVATIONS FACADE REPAIRS A501 DETAILS 61 DURANT TERRACE MIDDLETOWN, CT CITY OF MIDDLETOWN 245 deKOVEN DRIVE 06457 HOFFMANN ARCHITECTS, INC. 2711 Jefferson Davis Highway, Suite 333 2321 Whitney Avenue, 2 nd Floor 1040 Avenue of the Americas, Suite 14C Arlington, VA Hamden, Connecticut New York, NY SEAL 22202 06518 10018 PROJECT NO. 219068 17 SEPTEMBER 2020 G000 COPYRIGHT HOFFMANN ARCHITECTS, INC. 2020 DURANT TERRACE (ONE WAY) FACADE SIDEWALK SIDEWALK REPAIRS MAIN DRIVEWAY ENTRANCE CANOPY 61 DURANT TERRACE MAIN ENTRANCE MIDDLETOWN, CT NORTH PARKING LOT LAKE STREET EXISTING BUILDING ENTRANCE/ ENTRANCE/ 61 DURANT TERRACE EXIT EXIT BUILDING ADDRESS: SIDEWALK 61 DURANT TERRACE DUMPSTERS SOUTH PARKING LOT MIDDLETOWN, CT 06457 DURANT STREET ENTRANCE/ EXISTING TERRACE EXIT SIDEWALK CLIENT / OWNER: CITY OF MIDDLETOWN EXISTING 245 deKOVEN DRIVE PERGOLA MIDDLETOWN, CT 01109 SITE PLAN EXISTING SCALE: BOCCE COURT BIRDSEY AVENUE (ONE WAY) GENERAL NOTES: DRAFTING SYMBOLS: SIDEWALK 1. THE CONTRACTOR SHALL FIELD VERIFY ALL DIMENSIONS AND CONDITIONS OF THE SITE AND/OR BUILDING. 2. THE CONTRACTOR SHALL, UNLESS OTHERWISE PROVIDED IN THE NORTH ARROW CONTRACT DOCUMENTS, SECURE AND PAY FOR THE REQUIRED CONSTRUCTION PERMIT(S), FEES, LICENSES AND INSPECTIONS NECESSARY FOR THE PROPER EXECUTION OF THE WORK. 3. COORDINATION OF ALL WORK UNDER THIS CONTRACT SHALL BE MAINTAINED TO ENSURE THE QUALITY AND TIMELY COMPLETION OF FLOOR ELEVATION MARK THE WORK/PROJECT. ELEVATION NOTICE: 4. THE CONTRACTOR SHALL PERFORM ALL CUTTING AND PATCHING REQUIRED TO COMPLETE THE WORK OR TO MAKE ITS PARTS FIT DO NOT SCALE DRAWINGS. -
Sustainable Restoration of Yale University's Art + Architecture Building
Sustainable Restoration of Yale University’s Art + Architecture Building RUSSELL M. SANDERS, BENJAMIN SHEPHERD, ELIZABETH SKOWRONEK, AND ALISON HOFFMANN Renovation of a Modernist icon Renovation of Paul Rudolph Hall at by a serious fire in 1969, the structure demanded innovation to restore the Yale University suffered a series of unsympathetic reno- vations, which split and reconfigured its original aesthetic while incorporating When Yale University’s Art + Architec- soaring double-height drafting room and ture Building was completed in 1963, sustainable-design strategies. obstructed light and views. The external New York Times architecture critic Ada facade was scarred and barely recogniz- Louise Huxtable praised it as “a spec- able after Rudolph’s vast fenestrations tacular tour de force.”1 It appeared on were filled in with double-glazed win- the cover of every major architecture dows that were disrespectful of the magazine and has since been described original geometries. Interior volumes as “the Bilbao of its day.”2 Designed by lost their definition not only through Paul Rudolph, then chair of the School unwelcome intrusions and divisions but, of Architecture, the Art + Architecture more importantly, by removal of the Building is considered one of his most ceiling planes and the signature linear important works. The complex of inter- lighting system that defined them. locking spaces and strata catapulted the For the project team in 2006, the designer to fame with its assertive treat- task was imposing: restore a controver- ment of concrete forms (Fig. 1). sial, commanding piece of American By the late 1990s, however, the build- architectural heritage while introducing ing had been so altered that it bore little new infrastructure and sustainability resemblance to its original form. -
Hoffmann Architects, an Architecture and Engineering Firm
NEWS Contact Alison Hoffmann 1.800.239.6665 [email protected] www.hoffarch.com HOFFMANN ARCHITECTS CELEBRATES 40 YEARS IN BUSINESS September 2017 – Hoffmann Architects, an architecture and engineering firm specializing in the rehabilitation of building exteriors, commemorates the founding of the firm 40 years ago, in 1977. Hoffmann Architects’ history began with the mission to address design details that are commonly overlooked. After immigrating to the United States from Hungary in the 1950s, Hoffmann Architects founder and president John J. Hoffmann, FAIA studied architecture at the City College of New York. As a young architect, he observed that the design of construction details was falling less and less to design professionals, and more to vendors and installers. As a result, intersections, terminations, and other details were often executed inadequately, leaving buildings open to distress and failure. In 1977, he founded his own practice, Hoffmann Architects, with the intention of providing specialized expertise in building exterior details and construction technology. Since that time, Hoffmann Architects has grown to nearly four dozen employees in three states and has evolved a reputation for excellence in building envelope rehabilitation design. Hoffmann Architects staff with owner John J. Hoffmann, FAIA (center) in the early 1980s. Consistently ranked in the top 100 architecture/engineering firms by Building Design+Construction magazine, Hoffmann Architects has contributed to the preservation and longevity of some of the most significant architectural landmarks in the United States, including the United States Capitol, the Smithsonian Institution, the Chrysler Building, Rockefeller Center, the New York Stock Exchange, the United Nations, Folger Shakespeare Library, the Ford Foundation Building, and Lincoln Center for the Performing Arts. -
Windows: an Integral Part of the Building Envelope
ISSUE 3/2008 V O L U M E 2 5 N U M B E R 3 Journal of architectural technology published by Hoffmann Architects, Inc., specialists in the rehabilitation of building exteriors. Windows: An Integral Part of the Building Envelope Juan Kuriyama, AIA and Bradley Carmichael, EIT With the reports from recent tion options may be limited by any clinical research substantiating the number of factors, from landmark importance of natural lighting and regulations to structural limitations to ventilation in workplace productivity, aesthetic concerns, within these limits it health, and well-being, window design is often possible to improve energy effi- has become about more than building ciency, optimize light transmittance, and aesthetics or even energy efficiency. shape building appearance both inside From the capacity to create dramatic and out. And, because deterioration in gestures in glazing afforded by glass one building component can adversely curtain wall technology, to the im- affect interrelated components, ad- provements in thermal transfer made dressing distress or inefficiency in the possible by chemical advances in the fenestration not only will impact other glazing industry, to the race to develop building systems, but, as new research carbon-neutral strategies like “day- has touted, will shape one critical part lighting” that reduce demand on the of the building dynamic: the occupants. power grid, windows have taken on multi-faceted significance in building A Window Components Primer design. Even from humankind’s earli- est attempts at creating boundaries, Before considering rehabilitation op- we’ve found that our most successful tions for existing windows, it’s impor- efforts establish meaningful connec- tant to know the composition and tions between inside and outside, properties of the existing wall system, which establish our control over the so that an appropriate, compatible delimited structure by contextualizing repair or replacement design can be developed. -
Performance Considerations for Historic Window Replacement and Repair
I S S U E 2/2020 VOLUME 37 NUMBER 2 Journal of architectural technology published by Hoffmann Architects, Inc., specialists in the rehabilitation of building exteriors. Performance Considerations for Historic Window Replacement and Repair Rachel C. Palisin, PE, LEED AP BD+C and Richard W. Off, AIA F rom the stained glass windows Determining a path for historic win- that welcome variegated light into dow treatment that balances aesthet- cathedrals to the steel-framed geo- ics and historic integrity with contem- metric designs of Art Deco and the porary performance standards can be bold leaded glass of the Prairie style, challenging, particularly if the windows windows have served to define the are architecturally significant. character of buildings and spaces since Through thoughtfully designed and ex- the advent of glazed fenestration. Not ecuted repairs, some historic windows only do windows estab- can realize performance gains that ex- lish the aesthetics and tend their lifespan and improve indoor ambiance of a structure, comfort. However, where deteriora- they form an integral part tion is advanced, or where there is a of the building enclosure. More than ornament, compelling need to modernize the as- windows serve a vital role sembly to meet current performance in protecting the building standards, replacement may be war- from the elements and in ranted. In such cases, careful consider- modulating the transfer of ation of materials and window design heat, moisture, and light is critical to respecting historic char- from exterior to interior. acter while meeting project require- ments. Decisions about wood frames As windows age, their versus metal or composite, insulating components become glazing versus single-pane, true divided subject to the ravages of lights versus applied muntins, and time and weather: sealant historical versus modern anchorage, crumbles, wood decays, Meeting performance demands while preserving building among other considerations, require metal corrodes, glass character presents challenges for historic window projects. -
Copper Roofing: an Enduring Link Between Past and Future
Volume 15 Number 1 Journal of architectural technology published by Hoffmann Architects, specialists in exterior rehabilitation First Issue 1997 Volume 15 Number 1 Copper Roofing: An Enduring Link Between Past and Future with their standard 20-year warranty. Arthur L. Sanders, AIA Certainly, not all buildings are intended to last more than 30 or 40 years and C ustom-crafted copper roofing, rich may not warrant a copper roof. But in detailing, rich in history, speaks to many are designed for longevity and endurance and long life, its soft blue- merit a roof that will endure equally well. green patina a testament to the passage of time. But as a building material, Without a doubt, copper was and is a copper shouldn’t be relegated to the high initial cost item, typically two or past, despite competition over the past more times the cost of other roofing few decades from lower-cost, pre-formed types, with the exception of slate and metal roofing systems and other roofing tile. This high initial cost was a primary types. If longevity, low maintenance, reason why copper traditionally was and a strong aesthetic statement are a selected only for “important” buildings building owner’s goals, copper remains — public facilities, churches, libraries, the hands-down favorite. and other buildings of long-term value to their owners and their communities. When properly designed, detailed, and That cost came from the high level of installed, a copper roof can easily last craftsmanship required for installation, 50 years or more with relatively little along with the cost of the material itself. -
Avoiding Added Wear and Tęar to Roofing
Hoffmann Architects Second Issue 1992 Volume l0 Number2 Avoiding Added Wear and Têar to Roofing ln these situations, roof damage occurs Richard P. Kadlubowski when: A hnorgh,today's roofing systems r Roofìng equipment is improperly are highly durable and well-designed installed directly on the roofìng for their pri mary weatherproofìng membrane, without adequate function, they are not usually ìntended securement to the supportive or manufactured to support weìght- su bstructure. bearing loads of either equìpment or foot trafiìc, r Routine maintenance and emer- gency repairs require foot tr affìc All too often, however, the roofìng across inadequately protected system is asked to do justthat, These roof surlaces. secondary uses can play a leading role in shortening a roof 's lifespan and I Accessed and terraced roofs have creating unnecessary maintenance and insuffrcient drainage systems and repair problems, But there are ways to wall<way proteclion, avoid the pitlalls and still reap the added benefìts a roofcan offer beyond Here's a closer lool< at each of these simple protection from the elements, potential problem areas and some recommended solutions for avoiding ln many cases, the roof is the most roof damage, convenient locatìon for HVAC equip- ment, water towers, window washing Rooftop Equipment rigs, and other accessories, such as Whether new construction or retrofìt, satellite dishes and communication proper planning of equipment installa- equipment. Rooß are also used for tion is the fìrst step in minimizing the maintenance access or as terraced potential for long-term roof damage, settings fortenant and public use, Before installing or replacing any equipment, the following questìons should be asl<ed: As Prqect Monoger for Hoffmonn Architects, Mr. -
Is That Traffic Coating Necessary? Surface Treatments and Parking Structure Protection
ISSUE 2/2008 V O L U M E 2 5 N U M B E R 2 Journal of architectural technology published by Hoffmann Architects, Inc., specialists in the rehabilitation of building exteriors. Is That Traffic Coating Necessary? Surface Treatments and Parking Structure Protection Lawrence E. Keenan, PE, AIA and Robert A. Marsoli, Jr., EIT Elastomeric traffic-bearing mem- there are locations where no mem- branes are showing up on garages brane performs well, such as those old and new, and their popularity has areas requiring a flexible membrane soared in the past decade. A beautiful that are subject to snow plows. coating that locks out harmful moisture So…what is the best solution? It’s and chlorides must be a reasonable helpful to begin by looking at the rea- long-term investment, right? Not only sons why deck protection is necessary. is this not necessarily true, in some cases, applying such coatings can be a The Problem costly mistake. It is true that parking decks must be cared for to ensure that In northern climates, parking decks are they will be here after we are not, but subjected to extreme corrosive and there is a growing preconception that deteriorating environments. Moisture, installing a traffic-bearing membrane is laden with chlorides from deicing a one-way ticket to the garage equiva- chemicals, tracks into garages or hitch- lent of immortality. While a traffic- es a ride as ice formations behind the bearing membrane may, in fact, be the wheels of vehicles (tenderly referred best solution for many situations, this to as “fenderbergs” by those in the re- is a big-ticket item, and thorough con- pair industry) and ultimately soaks into sideration is necessary to determine the concrete surface. -
Copper Roofing
Hoffmann Architects Journal of architectural technology published by Hoffmann Architects, specìalists in exterior rehabilitation First lssue 1997 Volume l5 Number I Copper Roofing: An Enduring Linl< Between Past and Future with theìr standard 7}-year warranty, Arthur L. Sanders, AIA Certainly, not all buildings are intended to last more than 30 or 40 years and C rrtor-..ufted copper roofìng, rich may not warrant a copper roof But in detailing, rich in history, speal<s to many are designed for longevity and mer- endurance and long life, its soft blue- it a roof that will endure equally well. green patina a testament to the passage of time, But as a building matedal, Without a doubt, copper was and is a copper shouldn't be relegated to the high initial cost item, typically two or past, despite competition overthe past more times the cost of other roolng few decades from lower-cost, pre-formed types, with the exception of slate and metal roofìng systems and other roofìng tile This high initial cost was a primary types. lf longevity, low maintenance, reason why copper traditionally was and a frong aesthetic statement are a selected only for "important" buildings building owner's goals, copper remains - public facilities, churches, libraries, the hands-down favorite. and other buildings of long-term value to their owners and their communities, When properly designed, detailed, and That cost came from the high level of installed, a copper roof can easily last craftsmansh ip required for instal lation, 50 years or more with relatively little along with the cost of the material itself maintenance or care. -
Hoffmann Architects, an Architecture and Engineering Firm Spec
NEWS Contact Alison Hoffmann 1.800.239.6665 [email protected] www.hoffarch.com HOFFMANN ARCHITECTS ANNOUNCES EIGHT STAFF PROMOTIONS May 2017 – Hoffmann Architects, an architecture and engineering firm specializing in the rehabilitation of building exteriors, is pleased to announce the promotion of eight staff members in three offices. Connecticut office: Robert A. Marsoli, Jr., PE has been promoted to Senior Engineer, in appreciation of his loyalty, technical proficiency, and strong client relationships. Celebrating his tenth anniversary with Hoffmann Architects this past February, Marsoli began his career at the firm in 2007 as a Project Coordinator and was promoted in 2010 to Project Manager. After gaining experience and advanced credentials as a Professional Engineer, he earned a promotion to Project Engineer in 2016. In addition to developing designs for challenging structural engineering projects, he has served over the years as a mentor to emerging Robert A. Marsoli, Jr., professionals, and he has shared his growing expertise by publishing articles on topics PE related to the building envelope. With a civil engineering degree from Northeastern University, Marsoli has provided investigation and design services for clients including Aetna, Yale University, the New York State University Construction Fund, the Hospital of Central Connecticut, and Eversource Energy. He lives in North Haven, Connecticut. Rachel A. Mesite earned a promotion to Senior Finance Coordinator, recognizing her outstanding performance and dependability as a key part of the firm’s financial administration. Since joining the firm in 2015 as Finance Coordinator, Mesite has taken on additional responsibilities and has expanded the role of her position to include Rachel A.