Ley Hill Solutions Newsletter
Total Page:16
File Type:pdf, Size:1020Kb
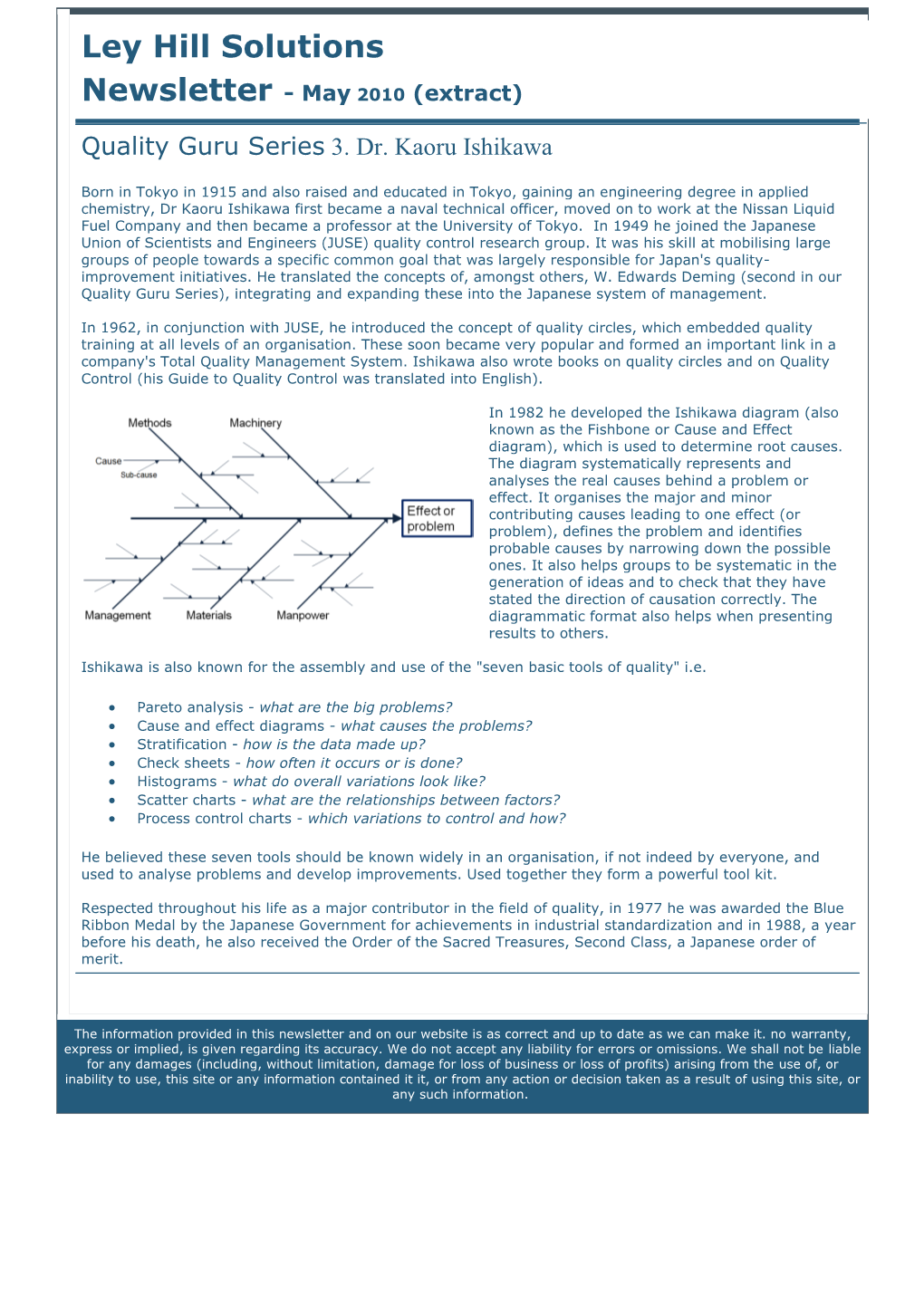
Load more
Recommended publications
-
The 7 Quality Improvement Tools
1 Continuous Quality Improvement for Excellence The 7 Quality Improvement Tools “From my past experience as much as 95% of all problems within a company can be solved by means of these tools” Kaoru Ishikawa Kaoru Ishikawa made many contributions to the field of quality improvement, including a range of tools and techniques. His emphasis was on the human side of quality. The concept of quality improvement as a fundamental responsibility of every member of staff became a key component of the Japanese approach to QI. Ishikawa’s work focuses on the idea of kaizen (a Japanese word that can be roughly translated as ‘continuous management’). This concept developed by Japanese industry in the 1950s and 1960s, is a core principle of quality management today, and holds that it is the responsibility of every staff member to improve what they do. www.nhselect.nhs.uk Helping our members to excel since 2002 2 Continuous Quality Improvement for Excellence Flow Charts / Process Maps What is Process Mapping and How Can it Help? Processes within healthcare have evolved over many years and through many organisational changes; this means there are often many layers to pathways and complicated systems that have built up over time. A good way to review systems and/or pathways to understand where improvements are needed is to work with frontline teams to process map. This is a simple exercise which facilitates a positive and powerful opportunity to create a culture of ownership within the multidisciplinary team to focus on areas for improvement. A process map is a visual way of representing and understanding a step-by-step picture of processes, either one aspect or a whole patient pathway. -
1 the Achievements and Personality of Dr. Kaoru Ishikawa Dr. Noriaki
The Premier Memorial Ishikawa Lecture Dr. Kaoru Ishikawa Birth Centenary Commemoration The Achievements and Personality of Dr. Kaoru Ishikawa Dr. Noriaki KANO Professor Emeritus, Tokyo University of Science Honorary Chairperson, Asian Network for Quality (ANQ) Honorary Member of JSQC, ASQ, and IAQ 1. Quiz for Prof Kaoru Ishikawa (originated by Acn Y. Ando, modified by N. Kano) Q1: How Do You Know Prof. Kaoru Ishikawa? A: Father of TPS B: Father of TPM C: Father of QC Circles Q2: Which country Prof. Ishikawa visited the most? A: U. S. B: Switzerland C: Taiwan Q3: What Prof. Kaoru Ishikawa used to advise his students? A: Be Proficient in English B; Learn to Hold Your Drink C: Be Good with Data 2. English translation of the book: “Kaoru Ishikawa: The Man and Quality Control”, Published by Mrs. Keiko Ishikawa in 1993, to that 172 writers including 144 writers from Japan and 28 writers from 15 other countries contributed. It is translated into English and is uploaded at: “Kaoru Ishikawa: The Man and Quality Control”, http://www.juse.or.jp/english/archives/ 3. My Personal Memory of Professor Ishikawa Why did I Join Professor Ishikawa’s Research Group! : Why did I got selected to his group? No, I did not select his group. It was the only group available because I was considered “unpromising student.” My first option professor declined to accept me and only vacant seat available was in Prof. Ishikawa’s group. I was supervised by Prof Ishikawa for seven and a half years i.e. from the time I was a senior of the undergraduate course until I obtained the Doctorate degree. -
Total Quality Management Course Code: POM-324 Author: Dr
Subject: Total Quality Management Course Code: POM-324 Author: Dr. Vijender Pal Saini Lesson No.: 1 Vetter: Dr. Sanjay Tiwari Concepts of Quality, Total Quality and Total Quality Management Structure 1.0 Objectives 1.1 Introduction 1.2 Concept of Quality 1.3 Dimensions of Quality 1.4 Application / Usage of Quality for General Public / Consumers 1.5 Application of Quality for Producers or Manufacturers 1.6 Factors affecting Quality 1.7 Quality Management 1.8 Total Quality Management 1.9 Characteristics / Nature of TQM 1.10 The TQM Practices Followed by Multinational Companies 1.11 Summary 1.12 Keywords 1.13 Self Assessment Questions 1.14 References / Suggested Readings 1 1.0 Objectives After going through this lesson, you will be able to: Understand the concept of Quality in day-to-day life and business. Differentiate between Quality and Quality Management Elaborate the concept of Total Quality Management 1.1 Introduction Quality is a buzz word in our lives. When the customer is in market, he or she is knowingly or unknowingly very cautious about the quality of product or service. Imagine the last buying of any product or service, e.g., mobile purchased last time. You must have enquired about various features like RAM, Operating System, Processor, Size, Body Colour, Cover, etc. If any of the features is not available, you might have suddenly changed the brand or have decided not to purchase it. Remember, how our mothers buy fruits, vegetables or grocery items. They are buying fresh and look-wise firm fruits, vegetable and groceries. Simultaneously, they are very conscious about the price of the fruits, vegetable and groceries. -
Seven Basic Tools of Quality Control: the Appropriate Techniques for Solving Quality Problems in the Organizations
UC Santa Barbara UC Santa Barbara Previously Published Works Title Seven Basic Tools of Quality Control: The Appropriate Techniques for Solving Quality Problems in the Organizations Permalink https://escholarship.org/uc/item/2kt3x0th Author Neyestani, Behnam Publication Date 2017-01-03 eScholarship.org Powered by the California Digital Library University of California 1 Seven Basic Tools of Quality Control: The Appropriate Techniques for Solving Quality Problems in the Organizations Behnam Neyestani [email protected] Abstract: Dr. Kaoru Ishikawa was first total quality management guru, who has been associated with the development and advocacy of using the seven quality control (QC) tools in the organizations for problem solving and process improvements. Seven old quality control tools are a set of the QC tools that can be used for improving the performance of the production processes, from the first step of producing a product or service to the last stage of production. So, the general purpose of this paper was to introduce these 7 QC tools. This study found that these tools have the significant roles to monitor, obtain, analyze data for detecting and solving the problems of production processes, in order to facilitate the achievement of performance excellence in the organizations. Keywords: Seven QC Tools; Check Sheet; Histogram; Pareto Analysis; Fishbone Diagram; Scatter Diagram; Flowcharts, and Control Charts. INTRODUCTION There are seven basic quality tools, which can assist an organization for problem solving and process improvements. The first guru who proposed seven basic tools was Dr. Kaoru Ishikawa in 1968, by publishing a book entitled “Gemba no QC Shuho” that was concerned managing quality through techniques and practices for Japanese firms. -
A Parallel Chronology of Prof. Kaoru Ishikawa's Life and TQC in Japan
A Parallel Chronology of Prof. Kaoru Ishikawa’s Life and TQC in Japan A Parallel Chronology of Prof. Kaoru Ishikawa’s Life and TQC in Japan Year Prof. Ishikawa’s Life Major Events in the Development of QC 1915 July 13 Born in Nishigahara, Takinogawa Ward, Tokyo City as the first son of Ichiro and Tomiko Ishikawa 1923 Entered Elementary School attached to Shewhart devised the control chart. (Age 8) Tokyo Higher Normal School (1924) 1928 Kinnosuke Ogura suggested the Entered Junior High School attached to possibility of the application of statistical (Age 13) Tokyo Higher Normal School methods to the production process. 1933 (1924) (Age 18) Entered Tokyo High School Fisher’s Statistical Method for Research 1936 Workers was published. (1925) Entered the Department of Applied Yasushi Ishida (Tokyo Electric Chemistry, the Faculty of Engineering, Company) introduced statistical methods (Age 21) Tokyo Imperial University to the production of lightbulbs. (1929) 1937 Dodge and Roming proposed a method During the summer vacation of his of sampling inspection with screening. second year at the university he spent (1929) four weeks in Hokkaido and Karafuto Shewhart’s Economic Control of Quality (present-day Sakhalin) with his of Manufactured Products was published. university friend Takashi Mukaibo (who (1931) later became the President of the Yasushi Ishida devised the control chart, University of Tokyo), visiting pulp mill, which he called “makimono,” and used to coal mine, beet-sugar mill, etc. control the production process of He also visited Manchuria (present-day lightbulbs. (1931) Liaoning Province, China). Kanzo Kiribuchi introduced quality He became a member of the Chemical control as “Hinshitsu Tosei” in his book Society of Japan. -
Fishbone Exercise First
Fishbone Kaoru Ishikawa, Organizational Theorist (1915-1989) Cause & Effect Diagram Kaoru Ishikawa • Kaoru Ishikawa (石川 馨 Ishikawa Kaoru, July 13, 1915 – April 16, 1989) was a Japanese organizational theorist, Professor at the Faculty of Engineering at The University of Tokyo, noted for his quality management innovations. • He is considered a key figure in the development of quality initiatives in Japan, particularly the quality circle. • He is best known outside Japan for the Ishikawa or cause and effect diagram (also known as fishbone diagram) often used in the analysis of industrial processes. Outcome: Bad Coffee How and why does the system produce bad coffee? 1. Procedures 2. Equipment 3. Materials 4. People Learning to Improve Learning how to see the system. We want to make visible the actual organizational structures and policies at work. This is an essential context for identifying promising changes and testing specific courses of action. The question we are asking in the first segment this afternoon is this: Why do we get the outcomes that we currently do? When answering this question we tend to see the system through our particular lens. That is why we do this as a group. Individually we only provide a partial view. We want to see the whole system. What are we attempting to improve? • We know that our current system is not inclusive. We aren’t the same as we were in 1950, but we are also not where we want to be in 2020 or 2050. This lack of inclusion is a reproduced reality – socially reproduced outcomes. • At the center of our analysis is the student. -
Top Ten Quality Gurus 1. Dr. Walter Shewhart 2. Dr. W. Edwards
Top Ten Quality Gurus 1. Dr. Walter Shewhart 2. Dr. W. Edwards Deming 3. Dr. Joseph M. Juran 4. Armand V. Feigenbaum 5. Dr. Kaoru Ishikawa 6. Dr. Genichi Taguchi 7. Shigeo Shingo 8. Philip B. Crosby 9. Dr. Eliyahu M. Goldratt 10. Taiichi Ohno 1. Dr. Walter Shewhart Walter Andrew Shewhart (pronounced like "shoe-heart", March 18, 1891 - March 11, 1967) was an American physicist, engineer and statistician, sometimes known as the father of statistical quality control. W. Edwards Deming said of him: As a statistician, he was, like so many of the rest of us, self-taught, on a good background of physics and mathematics. Early life and education Born in New Canton, Illinois to Anton and Esta Barney Shewhart, he attended the University of Illinois before being awarded his doctorate in physics from the University of California, Berkeley in 1917. Work on industrial quality Bell Telephone’s engineers had been working to improve the reliability of their transmission systems. Because amplifiers and other equipment had to be buried underground, there was a business need to reduce the frequency of failures and repairs. When Dr. Shewhart joined the Western Electric Company Inspection Engineering Department at the Hawthorne Works in 1918, industrial quality was limited to inspecting finished products and removing defective items. That all changed on May 16, 1924. Dr. Shewhart's boss, George D. Edwards, recalled: "Dr. Shewhart prepared a little memorandum only about a page in length. About a third of that page was given over to a simple diagram which we would all recognize today as a schematic control chart. -
Six Thought Leaders Who Changed the Quality World Forever Juran by QP Staff
crosby Deming Guru Feigenbaum Guide ishikawa Six thought leaders who changed the quality world forever juran by QP Staff shewhart Basic Quality Change doesn’t just happen out of the blue. It happens because someone comes along who challenges the status quo and gets people thinking differently. The quality world certainly has its game- changers, and as part of its annual quality basics issue, QP is highlighting six individuals who indelibly altered the course of quality. Whether you’re reading about these men for the first time or simply refreshing your knowledge, it should be said that this is by no means a comprehensive list. It takes a great many minds to revolutionize an entire field, and any attempt to include each and every person who had an impact on the quality world would take eight magazines rather than eight pages. But don’t let that stop the discussion. If there’s someone whose contributions you feel should be brought to light, visit www.qualityprogress.com and use the comment tool on this article’s webpage to let us know who’s on your list of history’s greatest quality thinkers and why. November 2010 • QP 15 Philip B. Crosby 1926-2001 Philip B. Crosby’s initial foray into the quality field was in able to expect people to be 1952, close on the heels of his military service in Korea. perfect? … Probably not. Published In the nearly five decades that followed, he became widely However, ZD has nothing works renowned in business circles as a guru of quality manage- to do with being perfect. -
Seven Quality Concepts 1
Running head: SEVEN QUALITY CONCEPTS 1 Seven Quality Concepts Benjamin Srock Embry-Riddle Aeronautical University Worldwide Campus Planning, Directing, and Controlling Projects PMGT-614 Jimmie Flores, Ph.D. July 2, 2017 Table of Contents History............................................................................................................................................. 3 Cause and Effect Diagrams ......................................................................................................... 3 Check Sheet ................................................................................................................................. 4 Control Charts.............................................................................................................................. 5 Histograms ................................................................................................................................... 6 Pareto Charts................................................................................................................................ 7 Scatter Plots ................................................................................................................................. 8 Flow Charts................................................................................................................................ 10 References ..................................................................................................................................... 12 SEVEN QUALITY CONCEPTS 3 -
Quality Circle: an Effective Tool for Improvement Employees Performance
ISSN 2349-7807 International Journal of Recent Research in Commerce Economics and Management (IJRRCEM) Vol. 2, Issue 3, pp: (82-85), Month: July 2015 - September 2015, Available at: www.paperpublications.org Quality Circle: An Effective Tool for Improvement Employees Performance NIDA SHIREEN Ph.D Research scholar, Guest faculty of UCCMS, Department of Banking and Business Economics Mohan lal Sukhadia University, Udaipur, India Abstract: Quality circle is a tool for increase employees performance and linking workers to the process of decision making. It consists of small group of workers from all levels of the organizational structure. The main purpose of circle is that every worker desires to take participate in making the environment of organizational a better place to work .The present study focus on quality circle and its seven basic tools . Keywords: Quality circle, Employees, Tools. 1. CONCEPT AND DEFINITION OF QUALITY CIRCLE The concept of quality circle is encouraging employee participation, attitude, develop team work in spirit and motivate employees to give contribution towards through group process. “ Quality circle is a small group of employees from the same work area who voluntarily meet on a regular basis to identify ,examine and solve work related problem ”.This concept was first established in Japan 1962 by Prof . Kaoru Ishikawa. Normally seven to twelve volunteers from the same organization make up a circle. The members of circle take knowledge through a training programme, problem solving session and group discussion. 2. SEVEN BASIC TOOLS The seven tools were developed by Prof. Kaoru Ishikawa these tools are the basic fundamental means of achieving quality improvement and fundamental instrument to improve product quality these tools are basic to monitoring and improvement activities at the process level these are used in analyze data for variation. -
Chapter 10 Father of the QC Circle: Prof. Kaoru Ishikawa
Chapter 10 Father of the QC Circle: Prof. Kaoru Ishikawa Prof. Kaoru Ishikawa advocated forming “QC Circle” in order to educate and promote Quality Control for front-line workers in the workplace, on the way to realize Total Quality Control, and strived to promote it by establishing the QC Circle Headquarters, within JUSE, in 1962 for systemization. QC Circle is small groups consisting of people from the same workplace that operate quality control activities autonomously. These small groups promote self-and mutual-development as a part of Total Quality Control activities, utilizing quality control tools and methods for management of the workplace and improvement continuously, with total participation. QC Circle activities aim to bring out and develop members’ potential capabilities. This activity was extensively developed due to the dedicated effort of Prof. Kaoru Ishikawa and, today, there are 9 regional chapters covering entire Japan. The accumulated number of registered circles at the QC Circle Headquarters, from its foundation in 1962 to the present, amounted to 340,000 circles with 2,630,000 members (As of the end of December, 1991). Generally speaking, there still seems to be a significant number of unregistered circles. On the contrary, this figure includes the number of circles once registered a long time ago, however, which have disappeared at present, due to operation shutdown, organizational reform etc. Under the initiative of Prof. Ishikawa, the actual status of QC Circle, regardless of registration status, required investigation, which was conducted by sampling, targeting workplace with 30 employees or over. The result shows estimates as follows: Dissemination rate of QC Circle at workplace (nationwide): 26% Investigation conducted: Approx. -
Chapter 2 Lamenting the Death of Prof. Kaoru Ishikawa Everyone’S Opinion
Chapter 2 Lamenting the Death of Prof. Kaoru Ishikawa: Articles of Condolence in Magazines, Convention Memorandums, and Newspapers, etc. Hinshitsu Kanri (Statistical Quality Control) Memorial Edition for Prof. Kaoru Ishikawa Tatsuo Sugimoto I would now like to give a farewell address for Professor Kaoru Ishikawa. You were an extraordinary person. A pioneer, leader and promoter of quality control in both academia and the industrial world, not only in Japan but also overseas. Your achievements were outstanding and indisputable, and this has been recognized and validated with the numerous awards you have received. These include the Grant Medal given by the American Society for Quality Control in May 1972, and the Second Class Order of the Sacred Treasure in November 1988, which is the highest honor given to quality control specialists. You used to tell us that we needed to improve the quality of companies and promote the development of new products through the implementation of TQC, CWQC and GWQC in order to survive through difficult times. You explained that Japanese companies had to commit to transformation, as there were a number of negative factors to contend with. These include international trade conflicts, appreciation of the yen, and the rapid pace of catch-up by newly industrializing economies (NIES), due to some Japanese products being too strong. Also, as you stated, we have promoted our Japanese concept and practice of quality control in Western developed countries and offered support for revitalization of their economies. In addition to this, we have offered support to developing countries to become stronger. Through the implementation of the QC, each country will be able to compete internationally in product quality through the implementation of QC.