Flight and Static Exhaust Flow Properties of an F110-GE-129 Engine in an F-16XL Airplane During Acoustic Tests
Total Page:16
File Type:pdf, Size:1020Kb
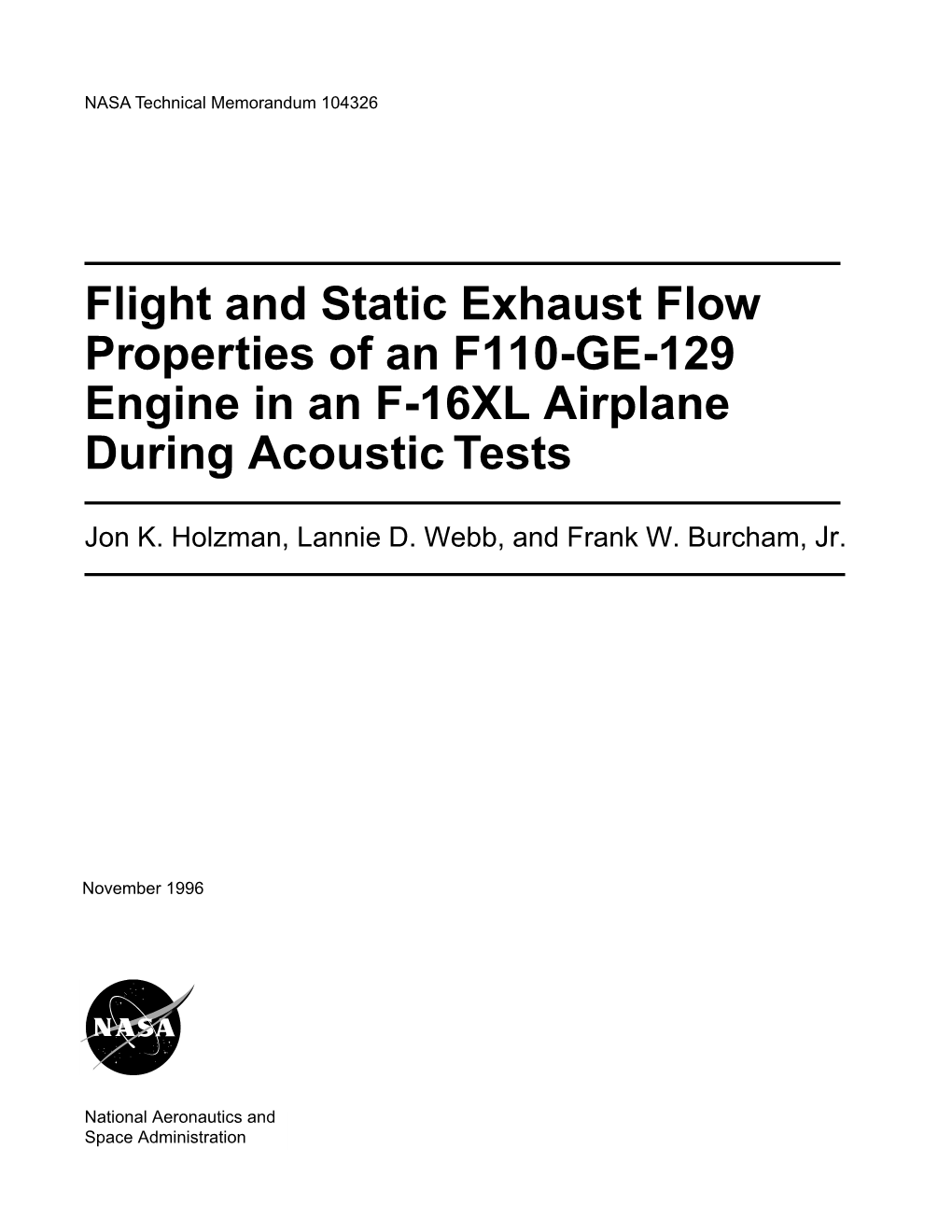
Load more
Recommended publications
-
Aerospace Engine Data
AEROSPACE ENGINE DATA Data for some concrete aerospace engines and their craft ................................................................................. 1 Data on rocket-engine types and comparison with large turbofans ................................................................... 1 Data on some large airliner engines ................................................................................................................... 2 Data on other aircraft engines and manufacturers .......................................................................................... 3 In this Appendix common to Aircraft propulsion and Space propulsion, data for thrust, weight, and specific fuel consumption, are presented for some different types of engines (Table 1), with some values of specific impulse and exit speed (Table 2), a plot of Mach number and specific impulse characteristic of different engine types (Fig. 1), and detailed characteristics of some modern turbofan engines, used in large airplanes (Table 3). DATA FOR SOME CONCRETE AEROSPACE ENGINES AND THEIR CRAFT Table 1. Thrust to weight ratio (F/W), for engines and their crafts, at take-off*, specific fuel consumption (TSFC), and initial and final mass of craft (intermediate values appear in [kN] when forces, and in tonnes [t] when masses). Engine Engine TSFC Whole craft Whole craft Whole craft mass, type thrust/weight (g/s)/kN type thrust/weight mini/mfin Trent 900 350/63=5.5 15.5 A380 4×350/5600=0.25 560/330=1.8 cruise 90/63=1.4 cruise 4×90/5000=0.1 CFM56-5A 110/23=4.8 16 -
6. Chemical-Nuclear Propulsion MAE 342 2016
2/12/20 Chemical/Nuclear Propulsion Space System Design, MAE 342, Princeton University Robert Stengel • Thermal rockets • Performance parameters • Propellants and propellant storage Copyright 2016 by Robert Stengel. All rights reserved. For educational use only. http://www.princeton.edu/~stengel/MAE342.html 1 1 Chemical (Thermal) Rockets • Liquid/Gas Propellant –Monopropellant • Cold gas • Catalytic decomposition –Bipropellant • Separate oxidizer and fuel • Hypergolic (spontaneous) • Solid Propellant ignition –Mixed oxidizer and fuel • External ignition –External ignition • Storage –Burn to completion – Ambient temperature and pressure • Hybrid Propellant – Cryogenic –Liquid oxidizer, solid fuel – Pressurized tank –Throttlable –Throttlable –Start/stop cycling –Start/stop cycling 2 2 1 2/12/20 Cold Gas Thruster (used with inert gas) Moog Divert/Attitude Thruster and Valve 3 3 Monopropellant Hydrazine Thruster Aerojet Rocketdyne • Catalytic decomposition produces thrust • Reliable • Low performance • Toxic 4 4 2 2/12/20 Bi-Propellant Rocket Motor Thrust / Motor Weight ~ 70:1 5 5 Hypergolic, Storable Liquid- Propellant Thruster Titan 2 • Spontaneous combustion • Reliable • Corrosive, toxic 6 6 3 2/12/20 Pressure-Fed and Turbopump Engine Cycles Pressure-Fed Gas-Generator Rocket Rocket Cycle Cycle, with Nozzle Cooling 7 7 Staged Combustion Engine Cycles Staged Combustion Full-Flow Staged Rocket Cycle Combustion Rocket Cycle 8 8 4 2/12/20 German V-2 Rocket Motor, Fuel Injectors, and Turbopump 9 9 Combustion Chamber Injectors 10 10 5 2/12/20 -
Helicopter Turboshafts
Helicopter Turboshafts Luke Stuyvenberg University of Colorado at Boulder Department of Aerospace Engineering The application of gas turbine engines in helicopters is discussed. The work- ings of turboshafts and the history of their use in helicopters is briefly described. Ideal cycle analyses of the Boeing 502-14 and of the General Electric T64 turboshaft engine are performed. I. Introduction to Turboshafts Turboshafts are an adaptation of gas turbine technology in which the principle output is shaft power from the expansion of hot gas through the turbine, rather than thrust from the exhaust of these gases. They have found a wide variety of applications ranging from air compression to auxiliary power generation to racing boat propulsion and more. This paper, however, will focus primarily on the application of turboshaft technology to providing main power for helicopters, to achieve extended vertical flight. II. Relationship to Turbojets As a variation of the gas turbine, turboshafts are very similar to turbojets. The operating principle is identical: atmospheric gases are ingested at the inlet, compressed, mixed with fuel and combusted, then expanded through a turbine which powers the compressor. There are two key diferences which separate turboshafts from turbojets, however. Figure 1. Basic Turboshaft Operation Note the absence of a mechanical connection between the HPT and LPT. An ideal turboshaft extracts with the HPT only the power necessary to turn the compressor, and with the LPT all remaining power from the expansion process. 1 of 10 American Institute of Aeronautics and Astronautics A. Emphasis on Shaft Power Unlike turbojets, the primary purpose of which is to produce thrust from the expanded gases, turboshafts are intended to extract shaft horsepower (shp). -
Session 6:Analytical Approximations for Low Thrust Maneuvers
Session 6: Analytical Approximations for Low Thrust Maneuvers As mentioned in the previous lecture, solving non-Keplerian problems in general requires the use of perturbation methods and many are only solvable through numerical integration. However, there are a few examples of low-thrust space propulsion maneuvers for which we can find approximate analytical expressions. In this lecture, we explore a couple of these maneuvers, both of which are useful because of their precision and practical value: i) climb or descent from a circular orbit with continuous thrust, and ii) in-orbit repositioning, or walking. Spiral Climb/Descent We start by writing the equations of motion in polar coordinates, 2 d2r �dθ � µ − r + = a (1) 2 2 r dt dt r 2 d θ 2 dr dθ aθ + = (2) 2 dt r dt dt r We assume continuous thrust in the angular direction, therefore ar = 0. If the acceleration force along θ is small, then we can safely assume the orbit will remain nearly circular and the semi-major axis will be just slightly different after one orbital period. Of course, small and slightly are vague words. To make the analysis rigorous, we need to be more precise. Let us say that for this approximation to be valid, the angular acceleration has to be much smaller than the corresponding centrifugal or gravitational forces (the last two terms in the LHS of Eq. (1)) and that the radial acceleration (the first term in the LHS in the same equation) is negligible. Given these assumptions, from Eq. (1), dθ r µ d2θ 3 r µ dr ≈ ! ≈ − (3) 3 2 5 dt r dt 2 r dt Substituting into Eq. -
Thrust Reverser
DC-10THRUST REVERSER Following an airplane accident in which inadver- tent thrust reverser deployment was considered a major contributor, the aviation industry and SAFETY the U.S. Federal Aviation Administration (FAA) adopted new criteria for evaluating the safety of ENHANCEMENT thrust reverser systems on commercial airplanes. Several airplane models were determined to be uncontrollable in some portions of the flight HARRY SLUSHER envelope after inadvertent deployment of the PROGRAM MANAGER AIRCRAFT MODIFICATION ENGINEERING thrust reverser. In response, Boeing and the BOEING COMMERCIAL AIRPLANES GROUP SAFETY FAA issued service bulletins and airworthiness AERO directives, respectively, for mandatory inspec- 39 tions and installation of thrust reverser actuation system locks on affected Boeing-designed airplanes. Boeing and the FAA are issuing similar documents for all models of the DC-10. air seal, fairing, and the aft frame; MODIFICATION OF THE THRUST a proposed AD for the indication reverser. This allows operators to stock and checks of the feedback rod-to-yoke 2 system on all models of the DC-10. neutral spare reversers and quickly The safety enhancement program REVERSER INDICATION SYSTEM oeing has initiated a four- alignment, translating cowl auto- An AD mandating the incorporation of configure them for any engine position. phased safety enhancement for the DC-10 is designed to improve restow function, position indication The second phase of the DC-10 safety B enhancement program involves modify- Boeing Service Bulletin DC10-78-060 The basic design elements of the program for thrust reverser the reliability of the thrust reverser for the overpressure shutoff valve, is expected by the end of 2000. -
The Solid Rocket Booster Auxiliary Power Unit - Meeting the Challenge
THE SOLID ROCKET BOOSTER AUXILIARY POWER UNIT - MEETING THE CHALLENGE Robert W. Hughes Structures and Propulsion Laboratory Marshall Space Flight Center, Alabama ABSTRACT The thrust vector control systems of the solid rocket boosters are turbine-powered, electrically controlled hydraulic systems which function through hydraulic actuators to gimbal the nozzles of the solid rocket boosters and provide vehicle steering for the Space Shuttle. Turbine power for the thrust vector control systems is provided through hydrazine fueled auxiliary power units which drive the hydraulic pumps. The solid rocket booster auxiliary power unit resulted from trade studies which indicated sig nificant advantages would result if an existing engine could be found to meet the program goal of 20 missions reusability and adapted to meet the seawater environments associated with ocean landings. During its maturation, the auxiliary power unit underwent many design iterations and provided its flight worthiness through full qualification programs both as a component and as part of the thrust vector control system. More significant, the auxiliary power unit has successfully completed six Shuttle missions. THE SOLID ROCKET BOOSTER CHALLENGE The challenge associated with the development of the Solid Rocket Booster (SRB) Auxiliary Power Unit (APU) was to develop a low cost reusable APU, compatible with an "operational" SRB. This challenge, as conceived, was to be one of adaptation more than innovation. As it turned out, the SRB APU development had elements of both. During the technical t~ade studies to select a SRB thrust vector control (TVC) system, several alternatives for providing hydraulic power were evaluated. A key factor in the choice of the final TVC system was the Orbiter APU development program, then in progress at Sundstrand Aviation. -
Thrust and Power Available, Maximum and Minimum Cruise Velocity, Effects of Altitude on Power Thrust Available
Module-2 Lecture-7 Cruise Flight - Thrust and Power available, Maximum and minimum cruise velocity, Effects of altitude on power Thrust available • As we have seen earlier, thrust and power requirements are dictated by the aero- dynamic characteristics and weight of the airplane. In contrast, thrust and power available are strictly associated with the engine of the aircraft. • The thrust delivered by typical reciprocating piston engines used in aircraft with propellers varies with velocity as shown in Figure 1(a). • It should be noted that the thrust at zero velocity (static thrust) is maximum and it decreases with increase in forward velocity. The reason for this behavior is that the blade tip of the propellers encounter compressibility problems leading to abrupt decrease in the available thrust near speed of sound. • However, as seen from Figure 1(b), the thrust delivered by a turbojet engine stays relatively constant with increase in velocity. Figure 1: Variation in available thrust with velocity of the (a) reciprocating engine- propeller powered aircraft and (b) turbojet engine powered aircraft 1 Power Power required for any aircraft is a characteristic of the aerodynamic design and weight of that aircraft. However, the power available, PA is a characteristic of the power plant (engine) of the aircraft. Typically, a piston engine generates power by burning fuel in the cylinders and then using this energy to move pistons in a reciprocating fashion (Figure 2). The power delivered to the piston driven propeller engine by the crankshaft is termed Figure 2: Schematic of a reciprocating engine as the shaft brake power P . -
Advisory Circular
Advisory U.S. Department of Transportation Circular Federal Aviation Administration Subject: RATINGS AND OPERATING Date: 6/28/10 AC No: 33.7-1 LIMITATIONS FOR TURBINE ENGINES Initiated by: ANE-111 (SECTIONS 33.7 AND 33.8) 1. Purpose. This advisory circular (AC) provides information and guidance on turbine engine compliance under part 33 of Title 14 of the Code of Federal Regulations (14 CFR), specifically §§ 33.7, Engine ratings and operating limitations, and 33.8, Selection of engine power and thrust ratings. This AC also provides information on preparing the data needed for the type certification data sheet (TCDS) specified in § 33.7(a). 2. Applicability. a. The guidance provided in this document is directed to applicants requesting certification of turbine engines, except that no specific guidance is provided for the augmented power or thrust (refer to § 33.7, paragraphs (c)(1)(i) and (iii)) and supersonic engines. For the purpose of this AC, any reference to power or thrust is for unaugmented power or thrust (refer to § 33.7, paragraphs (c)(1)(ii) and (iv)). b. This material is neither mandatory nor regulatory in nature and does not constitute a regulation. It describes acceptable means, but not the only means, for demonstrating compliance with the applicable regulations. The FAA will consider other methods of demonstrating compliance that an applicant may elect to present. Terms such as “should,” “shall,” “may,” and “must” are used only in the sense of ensuring applicability of this particular method of compliance when the acceptable method of compliance in this document is used. While these guidelines are not mandatory, they are derived from extensive FAA and industry experience in determining compliance with the relevant regulations. -
An Optiomal APU for Passenger Aircraft
AIRCRAFT DESIGN AND SYSTEMS GROUP (AERO) An Optiomal APU for Passenger Aircraft Dieter Scholz Hamburg University of Applied Sciences Based on the two project reports of Independent Study. Johan Peterson and Tom Alisch No Funding. 5th CEAS Air and Space Conference 2015 Delft, 07.-11. September 2015 An Optional APU for Passenger Aircraft Content . Introduction . APU Description . APU History . APU Operation . APU – Stakeholder Views . APU Characteristics . Potential Savings without an APU . APU Alternatives . Summary and Conclusions Dieter Scholz 5th CEAS Air and Space Conference 2015 07.09.2015, Slide 2 An Optional APU For Passenger Aircraft Delft, 07.-11. September 2015 Aircraft Design and Systems Group (AERO) Introduction Proposal . Offer the APU only as an option. Aircraft prepared for possible addition of the APU later in the life of the aircraft. Research Hypothesis . An aircraft type with an optional APU (with the option not selected when the aircraft is ordered) has economical and ecological advantages in operation compared to an aircraft not offering an opt-out from the APU. Simple Argument for the Benefits of the Proposal . Omitting the APU all together saves mass (fuel, emissions) and costs (maintenance costs, purchase costs and depreciation) Heuristic (mental shortcut) and Warning . If saving money would be so easy, the aircraft without APU would have been considered already and would be on offer. There must be some economical disadvantage not having an APU! Dieter Scholz 5th CEAS Air and Space Conference 2015 07.09.2015, Slide 3 An Optional APU For Passenger Aircraft Delft, 07.-11. September 2015 Aircraft Design and Systems Group (AERO) Introduction Definition (AGARD): Dieter Scholz 5th CEAS Air and Space Conference 2015 07.09.2015, Slide 4 An Optional APU For Passenger Aircraft Delft, 07.-11. -
A Ground Test Rocket Thrust Measurement System
A Ground Test Rocket Thrust Measurement System Mary Fran Desrochers, Gary W. Olsen, and M. K. Hudson Department of Applied Science and The Graduate Institute of Technology University of Arkansas at Little Rock, Little Rock, AR 72204 USA ABSTRACT A strain gauge thrust measurement system is described for rocket motor ground testing. The unit uses sigmoid beams to hold the rocket motor in place, with the strain gauges mounted on these beams. The theory and usage of strain gauges is briefly discussed, along with all circuit and other information necessary to build a similar system. The system was calibrated for the 50 lb thrust level and applied to the UALR Hybrid Rocket Facility. Its performance characteristics are discussed. The system was found suitable for continuous monitoring in such a ground testing environment, and indicated that the hy- Figure 1. Simplified Schematic of a rocket brid thruster utilized in the facility develops 41 motor. lbf thrust at an oxidant mass flow of 0.125 lbm. Keywords: rocket ground testing, thrust sensor, Rocket propulsion is one type of jet propul- combustion diagnostics, strain gauge, hybrid sion. A rocket is propelled by the ejection of rocket stored matter (propellant). The force produced by the ejection of the high-velocity matter is the Conversions from English to Metric Units: thrust force (F). Thrust is defined as the sum of two terms, a momentum term and a pressure 1 lbm = 1 pound mass = 454 g term. With reference to Figure 1, the equation for 1 lbf = 1 pound force = 4.45 N (Newtons) thrust is: 1 lb = 1 pound = 454 g 1 psia = 1 pound per square inch = 0.145 kPa F = mv2 + (p2 – p3) A2 (1) Momentum is the product of the mass and Introduction velocity of an object. -
Rocket Basics 1: Thrust and Specific Impulse
4. The Congreve Rocket ROCKET BASICS 1: THRUST AND SPECIFIC IMPULSE In a liquid-propellant rocket, a liquid fuel and oxidizer are injected into the com- bustion chamber where the chemical reaction of combustion occurs. The combustion process produces hot gases that expand through the nozzle, a duct with the varying cross section. , In solid rockets, both fuel and oxidizer are combined in a solid form, called the grain. The grain surface burns, producing hot gases that expand in the nozzle. The rate of the gas production and, correspondingly, pressure in the rocket is roughly proportional to the burning area of the grain. Thus, the introduction of a central bore in the grain allowed an increase in burning area (compared to “end burning”) and, consequently, resulted in an increase in chamber pressure and rocket thrust. Modern nozzles are usually converging-diverging (De Laval nozzle), with the flow accelerating to supersonic exhaust velocities in the diverging part. Early rockets had only a crudely formed converging part. If the pressure in the rocket is high enough, then the exhaust from a converging nozzle would occur at sonic velocity, that is, with the Mach number equal to unity. The rocket thrust T equals PPAeae TmUPPAmUeeae e mU eq m where m is the propellant mass flow (mass of the propellant leaving the rocket each second), Ue (exhaust velocity) is the velocity with which the propellant leaves the nozzle, Pe (exit pressure) is the propellant pressure at the nozzle exit, Pa (ambient 34 pressure) is the pressure in the surrounding air (about one atmosphere at sea level), and Ae is the area of the nozzle exit; Ueq is called the equivalent exhaust velocity. -
04 Propulsion
Aircraft Design Lecture 2: Aircraft Propulsion G. Dimitriadis and O. Léonard APRI0004-1, Aerospace Design Project, Lecture 4 1 Introduction • A large variety of propulsion methods have been used from the very start of the aerospace era: – No propulsion (balloons, gliders) – Muscle (mostly failed) – Steam power (mostly failed) – Piston engines and propellers – Rocket engines – Jet engines – Pulse jet engines – Ramjet – Scramjet APRI0004-1, Aerospace Design Project, Lecture 4 2 Gliding flight • People have been gliding from the- mid 18th century. The Albatross II by Jean Marie Le Bris- 1849 Otto Lillienthal , 1895 APRI0004-1, Aerospace Design Project, Lecture 4 3 Human-powered flight • Early attempts were less than successful but better results were obtained from the 1960s onwards. Gerhardt Cycleplane (1923) MIT Daedalus (1988) APRI0004-1, Aerospace Design Project, Lecture 4 4 Steam powered aircraft • Mostly dirigibles, unpiloted flying models and early aircraft Clément Ader Avion III (two 30hp steam engines, 1897) Giffard dirigible (1852) APRI0004-1, Aerospace Design Project, Lecture 4 5 Engine requirements • A good aircraft engine is characterized by: – Enough power to fulfill the mission • Take-off, climb, cruise etc. – Low weight • High weight increases the necessary lift and therefore the drag. – High efficiency • Low efficiency increases the amount fuel required and therefore the weight and therefore the drag. – High reliability – Ease of maintenance APRI0004-1, Aerospace Design Project, Lecture 4 6 Piston engines • Wright Flyer: One engine driving two counter- rotating propellers (one port one starboard) via chains. – Four in-line cylinders – Power: 12hp – Weight: 77 kg APRI0004-1, Aerospace Design Project, Lecture 4 7 Piston engine development • During the first half of the 20th century there was considerable development of piston engines.