Design of Erbium-Doped Tellurium Oxide Optical Amplifiers on a Low-Loss Silicon Nitride Waveguide Platform
Total Page:16
File Type:pdf, Size:1020Kb
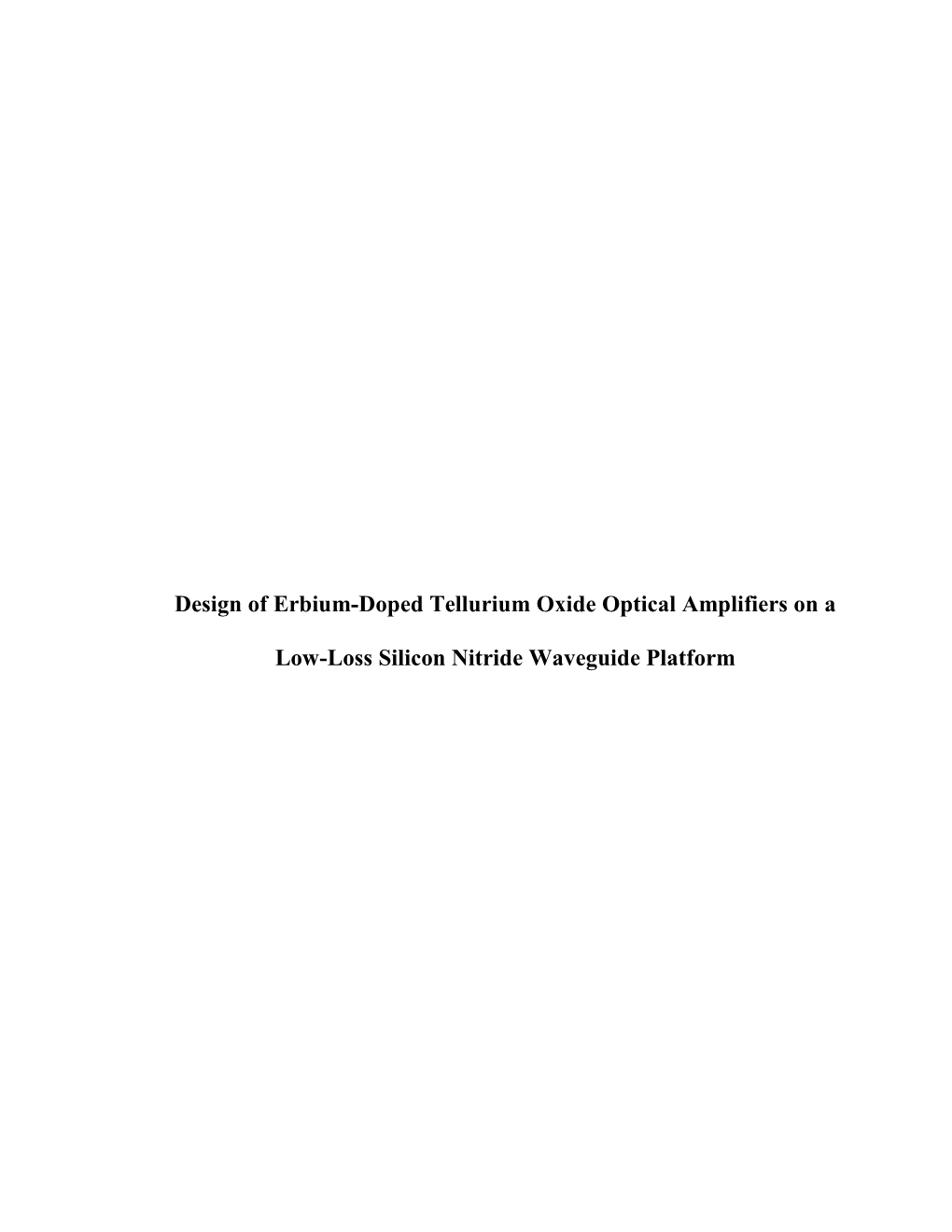
Load more
Recommended publications
-
(VI) and Chromium (V) Oxide Fluorides
Portland State University PDXScholar Dissertations and Theses Dissertations and Theses 1976 The chemistry of chromium (VI) and chromium (V) oxide fluorides Patrick Jay Green Portland State University Follow this and additional works at: https://pdxscholar.library.pdx.edu/open_access_etds Part of the Chemistry Commons Let us know how access to this document benefits ou.y Recommended Citation Green, Patrick Jay, "The chemistry of chromium (VI) and chromium (V) oxide fluorides" (1976). Dissertations and Theses. Paper 4039. https://doi.org/10.15760/etd.5923 This Thesis is brought to you for free and open access. It has been accepted for inclusion in Dissertations and Theses by an authorized administrator of PDXScholar. Please contact us if we can make this document more accessible: [email protected]. All ABSTRACT OF THE TllESIS OF Patrick Jay Green for the Master of Science in Chemistry presented April 16, 1976. Title: Chemistry of Chromium(VI) and Chromium(V) Oxide Fluorides. APPROVEO BY MEMBERS OF THE THESIS CO'"o\l TIEE: y . • Ii . ' I : • • • • • New preparative routes to chromyl fluoride were sought. It was found that chlorine ironofluoride reacts with chromium trioxide and chromyl chlo ride to produce chromyl fluoride. Attempts were ~ade to define a mechan ism for the reaction of ClF and Cr0 in light of by-products observed 3 and previous investigations. Carbonyl fluoride and chromium trioxide react to fom chro·yl fluoride and carbo:i dioxide. A mechanism was also proposed for this react10n. Chromium trioxide 11itl\ l~F6 or WF5 reacts to produce chromyl fluoride and the respective oxide tetrafluoride. 2 Sulfur hexafluoride did not react with Cr03. -
Effect of Gamma Radiation on Electrical and Optical Properties of (Teo2)0·9 (In2o3)0·1 Thin films
Bull. Mater. Sci., Vol. 34, No. 1, February 2011, pp. 61–69. c Indian Academy of Sciences. Effect of gamma radiation on electrical and optical properties of (TeO2)0·9 (In2O3)0·1 thin films S L SHARMA∗ and T K MAITY Department of Physics & Meteorology, Indian Institute of Technology, Kharagpur 721 302, India MS received 13 March 2010 Abstract. We have studied in detail the gamma radiation induced changes in the electrical properties of the (TeO2)0·9 (In2O3)0·1 thin films of different thicknesses, prepared by thermal evaporation in vacuum. The current– voltage characteristics for the as-deposited and exposed thin films were analysed to obtain current versus dose plots at different applied voltages. These plots clearly show that the current increases quite linearly with the radiation dose over a wide range and that the range of doses is higher for the thicker films. Beyond certain dose (a quantity dependent on the film thickness), however, the current has been observed to decrease. In order to understand the dose dependence of the current, we analysed the optical absorption spectra for the as-deposited and exposed thin films to obtain the dose dependences of the optical bandgap and energy width of band tails of the localized states. The increase of the current with the gamma radiation dose may be attributed partly to the healing effect and partly to the lowering of the optical bandgap. Attempts are on to understand the decrease in the current at higher doses. Employing dose dependence of the current, some real-time gamma radiation dosimeters have been prepared, which have been found to possess sensitivity in the range 5–55 μGy/μA/cm2. -
Luminescent Properties of Cdte Quantum Dots Synthesized Using 3-Mercaptopropionic Acid Reduction of Tellurium Dioxide Directly
Shen et al. Nanoscale Research Letters 2013, 8:253 http://www.nanoscalereslett.com/content/8/1/253 NANO EXPRESS Open Access Luminescent properties of CdTe quantum dots synthesized using 3-mercaptopropionic acid reduction of tellurium dioxide directly Mao Shen1*, Wenping Jia1, Yujing You1, Yan Hu2, Fang Li1,3, Shidong Tian3, Jian Li3, Yanxian Jin1 and Deman Han1 Abstract A facile one-step synthesis of CdTe quantum dots (QDs) in aqueous solution by atmospheric microwave reactor has been developed using 3-mercaptopropionic acid reduction of TeO2 directly. The obtained CdTe QDs were characterized by ultraviolet–visible spectroscopy, fluorescent spectroscopy, X-ray powder diffraction, multifunctional imaging electron spectrometer (XPS), and high-resolution transmission electron microscopy. Green- to red-emitting CdTe QDs with a maximum photoluminescence quantum yield of 56.68% were obtained. Keywords: CdTe quantum dots, 3-mercaptopropionic acid, TeO2, Microwave irradiation, Photoluminescence Background capping ligand for CdTe QDs. Such synthetic approach In recent years, water-soluble CdTe luminescent quantum eliminates the use of NaBH4 and allows facile one-pot dots (QDs) have been used in various medical and bio- synthesis of CdTe QDs. logical imaging applications because their optical proper- ties are considered to be superior to those of organic dyes [1-4]. Up to now, in most of the aqueous approaches, Te Methods Chemicals powder was used as the tellurium source and NaBH4 as the reductant, which needs a pretreatment to synthesize Tellurium dioxide (TeO2,99.99%),cadmiumchlor- the unstable tellurium precursor. The process of preparing ide hemi(pentahydrate) (CdCl2 ·2.5H2O, 99%), and 3-mercaptopropionic acid (MPA, 99%) were pur- CdTe QDs requires N2 as the protective gas at the initial chased from Aldrich Corporation (MO, USA). -
Normal Vibrations of Two Polymorphic Forms of Teo2 Crystals and Assignments of Raman Peaks of Pure Teo2 Glass
Nippon Seramikkusu Kyokai GakujutsuRonbunshi 97 [12] 1435-40 (1989) 1435 Normal Vibrations of Two Polymorphic forms of TeO2 Crystals and Assignments of Raman Peaks of Pure TeO2 Glass Takao SEKIYA, Norio MOCHIDA, Atsushi OHTSUKA and Mamoru TONOKAWA† ( Division of Materials Science and Chemical Engineering, Faculty of Engineering, Yokohama National University, 156, Tokiwadai, Hodogaya-ku, Yokohama-shi 240) TeO2結 晶 の 二 つ の 多 形 の 基 準 振 動 の 計 算 とTeO2ガ ラ ス の ラ マ ン ピ ー ク の 帰 属 関 谷 隆 夫 ・持 田 統 雄 ・大 塚 淳 ・殿 川 衛 † (横浜国立 大学工学部物質工学科, 240横 浜市保土 ケ谷区常盤台156) Raman spectra of paratellurite, tellurite and pure TeO2 glass were measured. The normal vibration of paratellurite and tellurite was analyzed. The spectrum of pure TeO2glass were deconvoluted into symmetric Gaussian functions. The normal vibrations of paratellurite are exactly described as combined representations of movement of oxygen atom in Te-eqOax-Te linkage and vibrations of TeO4 trigonal bipyramid (tbp). Compared the resolved Raman peaks of pure TeO2glass with nor mal vibration of paratellurite, all Raman peaks from 420 to 880 cm-1 are assigned to the vibrations of TeO4 tbp and Te-eqOax-Te linkage. The antisymmetric stretching vibrations of Te-qeOax-Te linkage have relatively large intensities to symmetric stretching vibrations of Te-eqOax-Te linkage. In pure TeO2 glass, TeO4 tops are formed by most of tellurium atoms and connected at vertices by the Te-eqOax-Te linkages. [ReceivedMay 18, 1989; AcceptedAugust 22, 1989] Key-words: Normal vibration, Raman spectrum, Paratellurite, Tellurite, Pure TeO2glass 1. -
Chemical Names and CAS Numbers Final
Chemical Abstract Chemical Formula Chemical Name Service (CAS) Number C3H8O 1‐propanol C4H7BrO2 2‐bromobutyric acid 80‐58‐0 GeH3COOH 2‐germaacetic acid C4H10 2‐methylpropane 75‐28‐5 C3H8O 2‐propanol 67‐63‐0 C6H10O3 4‐acetylbutyric acid 448671 C4H7BrO2 4‐bromobutyric acid 2623‐87‐2 CH3CHO acetaldehyde CH3CONH2 acetamide C8H9NO2 acetaminophen 103‐90‐2 − C2H3O2 acetate ion − CH3COO acetate ion C2H4O2 acetic acid 64‐19‐7 CH3COOH acetic acid (CH3)2CO acetone CH3COCl acetyl chloride C2H2 acetylene 74‐86‐2 HCCH acetylene C9H8O4 acetylsalicylic acid 50‐78‐2 H2C(CH)CN acrylonitrile C3H7NO2 Ala C3H7NO2 alanine 56‐41‐7 NaAlSi3O3 albite AlSb aluminium antimonide 25152‐52‐7 AlAs aluminium arsenide 22831‐42‐1 AlBO2 aluminium borate 61279‐70‐7 AlBO aluminium boron oxide 12041‐48‐4 AlBr3 aluminium bromide 7727‐15‐3 AlBr3•6H2O aluminium bromide hexahydrate 2149397 AlCl4Cs aluminium caesium tetrachloride 17992‐03‐9 AlCl3 aluminium chloride (anhydrous) 7446‐70‐0 AlCl3•6H2O aluminium chloride hexahydrate 7784‐13‐6 AlClO aluminium chloride oxide 13596‐11‐7 AlB2 aluminium diboride 12041‐50‐8 AlF2 aluminium difluoride 13569‐23‐8 AlF2O aluminium difluoride oxide 38344‐66‐0 AlB12 aluminium dodecaboride 12041‐54‐2 Al2F6 aluminium fluoride 17949‐86‐9 AlF3 aluminium fluoride 7784‐18‐1 Al(CHO2)3 aluminium formate 7360‐53‐4 1 of 75 Chemical Abstract Chemical Formula Chemical Name Service (CAS) Number Al(OH)3 aluminium hydroxide 21645‐51‐2 Al2I6 aluminium iodide 18898‐35‐6 AlI3 aluminium iodide 7784‐23‐8 AlBr aluminium monobromide 22359‐97‐3 AlCl aluminium monochloride -
Gamma Radiation Dosimetry Using Tellurium Dioxide Thin Film Structures
Sensors 2002, 2, 347-355 sensors ISSN 1424-8220 © 2002 by MDPI http://www.mdpi.net/sensors Gamma Radiation Dosimetry Using Tellurium Dioxide Thin Film Structures Khalil Arshak* and Olga Korostynska Electronic & Computer Engineering Dept., University of Limerick, Limerick, Ireland. * Author to whom correspondence should be addressed. E-mail: [email protected] Received:3 July 2002 / Accepted:19 July 2002 / Published: 23 August 2002 Abstract: Thin films of Tellurium dioxide (TeO2) were investigated for γ-radiation dosimetry purposes. Samples were fabricated using thin film vapour deposition technique. Thin films of TeO2 were exposed to a 60Co γ-radiation source at a dose rate of 6 Gy/min at room temperature. Absorption spectra for TeO2 films were recorded and the values of the optical band gap and energies of the localized states for as-deposited and γ-irradiated samples were calculated. It was found that the optical band gap values were decreased as the radiation dose was increased. Samples with electrical contacts having a planar structure showed a linear increase in current values with the increase in radiation dose up to a certain dose level. The observed changes in both the optical and the electrical properties suggest that TeO2 thin film may be considered as an effective material for room temperature real time γ-radiation dosimetry. Key words: Gamma Radiation, Dosimetry, Thin Films, Tellurium Dioxide, Optical Band Gap Introduction The ability to detect and perform energy-dispersive spectroscopy of high-energy radiation such as X-rays, γ-rays, and other uncharged and charged particles has improved dramatically in recent years [20]. -
Metals-10-01176.Pdf
metals Article Selective Recovery of Tellurium from the Tellurium-Bearing Sodium Carbonate Slag by Sodium Sulfide Leaching Followed by Cyclone Electrowinning Zhipeng Xu 1,2,3, Zoujiang Li 1,2, Dong Li 1,2, Xueyi Guo 1,2,*, Ying Yang 1,2, Qinghua Tian 1,2,* and Jun Li 1,2 1 School of Metallurgy and Environment, Central South University, Changsha 410083, China; [email protected] (Z.X.); [email protected] (Z.L.); [email protected] (D.L.); [email protected] (Y.Y.); [email protected] (J.L.) 2 National & Regional Joint Engineering Research Center of Nonferrous Metal Resource Recycling, Changsha 410083, China 3 First Materials Co., Ltd., Qingyuan 511517, China * Correspondence: [email protected] (X.G.); [email protected] (Q.T.); Tel.: +86-731-8887-6255 (X.G.); +86-731-8887-7863 (Q.T.) Received: 27 July 2020; Accepted: 19 August 2020; Published: 1 September 2020 Abstract: The rigorous environmental requirements promote the development of new processes with short and clean technical routes for recycling tellurium from tellurium-bearing sodium carbonate slag. In this paper, a novel process for selective recovery of tellurium from the sodium carbonate slag by sodium sulfide leaching, followed by cyclone electrowinning, was proposed. 88% of tellurium was selectively extracted in 40 g/L Na2S solution at 50 ◦C for 60 min with a liquid to solid ratio of 8:1 mL/g, while antimony, lead and bismuth were enriched in the leaching residue. Tellurium in the leach liquor was efficiently electrodeposited by cyclone electrowinning without purification. The effects of current density, temperature and flow rate of the electrolyte on current efficiency, tellurium recovery, cell voltage, energy consumption, surface morphology, and crystallographic orientations were systematically investigated. -
STRUCUTURE and PHOTOLUMINESCENCE PROPERTIES of Teo2-CORE/Tio2-SHELL NANOWIRES
TH 18 INTERNATIONAL CONFERENCE ON COMPOSITE MATERIALS STRUCUTURE AND PHOTOLUMINESCENCE PROPERTIES OF TeO2-CORE/TiO2-SHELL NANOWIRES H. Kim, C. Jin, S. Park, C. Lee* Department of Materials Science and Engineering, Inha University, 253 Yonghyun-dong, Nam- gu, Incheon 402-751, Republic of Korea * Corresponding author([email protected]) Keywords: TeO2 nanowires, TiO2 coating, Annealing, Photoluminescence, Scanning electron microscopy 1 Introduction Tellurium dioxide (TeO2) is an attractive semiconductor oxide material owing to its unique physical and chemical properties suitable for various technological applications such as deflectors [1], modulators [2], dosimeters [3, 4], optical storage material [5], laser devices [6], and gas sensors [7, 8]. TeO2 thin films have been prepared by various techniques such as reactive sputtering [9], dip- coating [10], and vapor deposition [3]. However, there have been few reports on the synthesis of TeO2 nanostructures. TeO2 nanowires have been synthesized by thermal evaporation of Te powders [11], laser ablation of Te [7], direct thermal oxidation of Te at ambient pressure in a flow of O2 without the presence of any catalyst [12], and hydrolysis of tellurium isopropoxide in the presence of tetra alkyl ammonium bromide solution [13]. In particular, there have been very few reports on the luminescence properties of the TeO2 nanostructures in spite of the wide applications of TeO2 nanostructures in optical and optoelectronic fields. A common technique to control and enhance the properties of nanostructures is to create core-shell coaxial heterostructures [14,15]. For example, the intensity of the light emitted from core-shell nanostructures can be increased significantly or the wavelength of the emission can be controlled by selecting a proper coating material and a proper coating layer thickness [16-18]. -
Study of the Preparation of Telluric Acid and Its Application in Analytical
A STUDY OF THE PRI-PARATION OP TELLURIC ACID A: r US APPLICATION IN ANALYTICAL CHE by . !£N HORNER B« S«, Franklin and Marshall College, 1949 A THESIS submitted in partial fulfillment of the requirements for the degree MAST Department of Chemistry KANSAS STA GB OF AGRICULTU L AND APPLIED SC 1951 &0<LUl~ ii ^1*8 T4 \<V$I Hlol TABLE OP CONTENTS I Oo i INTRODUCTION ft* 1 EXPERIMENTAL 5 Volumetric Determination of Tellurium Dioxide 5 Purification of Tellurium Dioxide . 13 Determination of the Solubility of Telluric Acid and Tellurixim Dioxide in Concentrated Ammonium Hydroxide ..... 13 Preparation of Telluric Acid ... 14 Determination of the Purity of Telluric Acid 20 The Determination of Barium by Homogeneous Precipitation as Barium Tollurate . 21 DISCUSSION 25 SUMMARY 27 ACK 29 LITERATURE CITED 30 INTRODUCTION The studies reported upon In this paper were directed towards (1) The preparation of telluric acid, and (2) the homogeneous precipitation of barium and similar Ions as tellurates. A review of the literature shows that there have been several methods of preparing telluric acid. Meyer and Franke (4) oxidized the elementary tellurium with a mixture of barium chlorate and sulfuric acid. Krepelka and Kubik (2) oxidized the elementary tellurium with 30 percent hydrogen peroxide, but their method necessitated using a 10-15 fold excess of the oxidizing agent. Staundenmaier (9) reacted a mixture of nitric and chromic acids with tellurium dioxide to effect oxidation to telluric acid. The procedure as developed by Mathers et al. (3) is the most widely used. Crude tellurium dioxide is purified and then oxidized by a slight excess of permanganate in a hot solution of about five molar nitric acid. -
Validation of a New Design of Tellurium Dioxide-Irradiated Target
View metadata, citation and similar papers at core.ac.uk brought to you by CORE provided by Elsevier - Publisher Connector Nuclear Engineering and Technology 48 (2016) 1273e1279 Available online at ScienceDirect Nuclear Engineering and Technology journal homepage: www.elsevier.com/locate/net Technical Note Validation of a New Design of Tellurium Dioxide-Irradiated Target * Aziz Fllaoui a, , Younes Ghamad a, Brahim Zoubir a, Zinel Abidine Ayaz a, Aissam El Morabiti b, Hafid Amayoud c, and El Mahjoub Chakir d a Radiopharmaceutical Production Unit, Life Sciences and Applications Department, Centre National de l'Energie des Sciences et des Techniques Nucleaires, PO Box 1382 R.P. 10001, Rabat, Morocco b Safety Audit Unit, Safety Security Pole, Centre National de l'Energie des Sciences et des Techniques Nucleaires, PO Box 1382 R.P. 10001, Rabat, Morocco c Maintenance and Technical Unit, Technical and Logistic Division, Centre National de l'Energie des Sciences et des Techniques Nucleaires, PO Box 1382 R.P.10001, Rabat, Morocco d Nuclear Physics Department, University Ibn Toufail, BP 242, Kenitra, Morocco article info abstract Article history: Production of iodine-131 by neutron activation of tellurium in tellurium dioxide (TeO2) Received 26 December 2015 material requires a target that meets the safety requirements. In a radiopharmaceutical Received in revised form production unit, a new lid for a can was designed, which permits tight sealing of the target by 16 March 2016 using tungsten inert gas welding. The leakage rate of all prepared targets was assessed using a À Accepted 7 May 2016 helium mass spectrometer. The accepted leakage rate is 10 4 mbr.L/s, according to the Available online 29 May 2016 approved safety report related to iodine-131 production in the TRIGA Mark II research reactor (TRIGA: Training, Research, Isotopes, General Atomics). -
Exploring the Surface Properties of the Liquid Metals
Exploring the surface properties of the liquid metals A thesis submitted in fulfilment of the requirements for the degree of Doctor of Philosophy Ali Zavabeti Bachelor of Telecommunications Engineering (with Honours), Monash University Master of Engineering Science (Research), Monash University School of Engineering College of Science, Engineering and Health RMIT University October, 2018 Abstract of Thesis Gallium based liquid metal alloys feature unique properties that set promising pathways for developing future technologies. In contrast to mercury, gallium is considered a non-hazardous option as a liquid metal. A variety of metals can be alloyed into gallium in order to create mixtures with exciting physical and chemical properties. Galinstan is a eutectic liquid metal alloy, consisting 68.5 wt% gallium, 21.5 wt% indium, and 10 wt% tin which possesses a lower (below 0 ºC) freezing point and higher surface tension than that of gallium liquid metal. Surface tension manipulations of liquid metals in electrolyte environments play an important role in the development of their emerging applications in electrochemical systems and microfluidics. However, the effects of electrolytes on the surface tension of liquid metals were not fully explored and an opportunity existed for a comprehensive study of such liquids. Due to significant potential outcomes, exploring the effects of different electrolyte types and concentrations on gallium based liquid metal dynamics was chosen as one of the main foci of this research. In this PhD thesis, the author establishes a new framework to study the effects of different acidic and basic electrolytes on dynamics of galinstan droplets. The droplet is placed in a recess between two microfluidic channels. -
The Radiochemistry of Tellurium
. (L22&QJv?k) National Academy ‘ v of Sciences 1“National Research Council m NUCLEAR SCIENCE SERIES The Radiochemistry of Tellurium i COMMITTEE ON NUCLEAR SCIENCE L. F. C URTISS,Chaiwzan ROBLEY D. EVANS, Vice Chairman NationalBureauofStandards MassachusettsInstituteofTechnology J.A. DeJUREN, Secrefa~y WestinghouseElectricCorporation C. J.BORKOWSKI J.W. IRVINE,JR. Oak RidgeNationalLaboratory MassachusettsInstituteofTechnology ROBERT G. COCHRAN E. D. KLEMA TexasAgriculturaland Mechanical NorthwesternUniversity College W. WAYNE MEINKE SAMUEL EPSTEIN UniversityofMichigan CaliforniaInstituteofTechnology J.J.NICKSON U. FANO MemorialHospital,New York NationalBureauofStandards ROBERT L. PLATZMAN Laboratoirede ChimiePhysique HERBERT GOLDSTEIN NuclearDevelopmentCorporationof D. M. VAN PATTER America BartolResearchFoundation LIAISON MEMBERS PAUL C. AEBERSOLD CHARLES K. REED Atomic EnergyCommission U. S.Air Force J.HOWARD McMILLEN WILLIAM E. WRIGHT NationalScienceFoundation OfficeofNavalResearch SUBCOMMITTEE ON RADIOCHEMISTRY W. WAYNE ME INKE, Chairman HAROLD KIRBY UniversityofMichigan Mound Laboratory GREGORY R. CHOPPIN GEORGE LEDDICOTTE FloridaStateUniversity Oak RidgeNationalLaboratory GEORGE A. COWAN JULIAN NIELSEN Los Alamos ScientificLaboratory HanfordLaboratories ARTHUR W. FAIRHALL ELLIS P. STEINBERG universityofWashington ArgonneNationalLaboratory JEROME HUDIS PETER C. STEVENSON BrookhavenNationalLaboratory UniversityofCalifornia(Livermore) EARL HYDE LEO YAFFE UniversityofCalifornia(Berkeley) McGillUniversity CONSLJLTANTS NATHAN BALLOU JAMES