Methamphetamine?
Total Page:16
File Type:pdf, Size:1020Kb
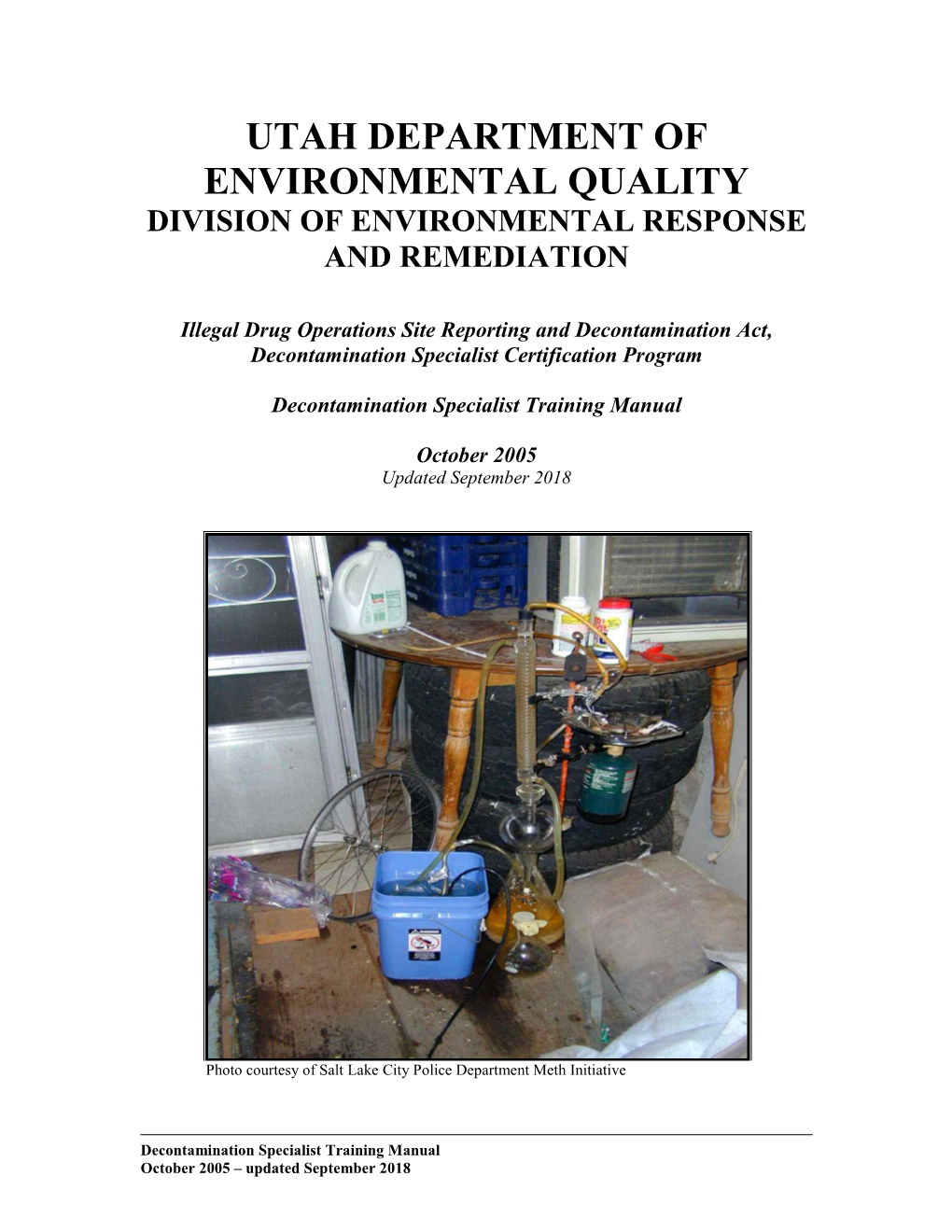
Load more
Recommended publications
-
Dichloroethylene
Development Support Document Final, October 15, 2007 Accessible 2013 1,1-Dichloroethylene CAS Registry Number: 75-35-4 Prepared by Shannon Ethridge, M.S. Toxicology Section Chief Engineer’s Office ___________________________________________________________ TEXAS COMMISSION ON ENVIRONMENTAL QUALITY 1,1 Dichloroethylene Page 2 TABLE OF CONTENTS CHAPTER 1 SUMMARY TABLES ........................................................................................... 4 CHAPTER 2 MAJOR USES OR SOURCES ............................................................................ 6 CHAPTER 3 ACUTE EVALUATION ....................................................................................... 6 3.1 HEALTH-BASED ACUTE REV AND ESL ................................................................................. 6 3.1.1 Physical/Chemical Properties and Key Studies ............................................................. 6 3.1.2 Mode-of-Action (MOA) Analysis ................................................................................. 10 3.1.3 Dose Metric .................................................................................................................. 10 3.1.4 Point of Departure (POD) for the Key Study............................................................... 10 3.1.5 Dosimetric Adjustments ............................................................................................... 11 3.1.6 Critical Effect and Adjustment of PODHEC .................................................................. 11 3.1.7 Health-Based -
Health Effects Support Document for Hexachlorobutadiene Health Effects Support Document for Hexachlorobutadiene
Health Effects Support Document for Hexachlorobutadiene Health Effects Support Document for Hexachlorobutadiene U.S. Environmental Protection Agency Office of Water (4304T) Health and Ecological Criteria Division Washington, DC 20460 www.epa.gov/safewater/ EPA 822-R-03-002 February 2003 Printed on Recycled Paper FOREWORD The Safe Drinking Water Act (SDWA), as amended in 1996, requires the Administrator of the Environmental Protection Agency (EPA) to establish a list of contaminants to aid the agency in regulatory priority setting for the drinking water program. In addition, SDWA requires EPA to make regulatory determinations for no fewer than five contaminants by August 2001. The criteria used to determine whether or not to regulate a chemical on the CCL are the following: The contaminant may have an adverse effect on the health of persons. The contaminant is known to occur or there is a substantial likelihood that the contaminant will occur in public water systems with a frequency and at levels of public health concern. In the sole judgment of the administrator, regulation of such contaminant presents a meaningful opportunity for health risk reduction for persons served by public water systems. The Agency’s findings for the three criteria are used in making a determination to regulate a contaminant. The Agency may determine that there is no need for regulation when a contaminant fails to meet one of the criteria. This document provides the health effects basis for the regulatory determination for hexachlorobutadiene. In arriving at the regulatory determination, data on toxicokinetics, human exposure, acute and chronic toxicity to animals and humans, epidemiology, and mechanisms of toxicity were evaluated. -
Toxicological Profile for 1,1-Dichloroethene Draft for Public Comment December 2019 1,1-DICHLOROETHENE Ii
F Toxicological Profile for 1,1-Dichloroethene Draft for Public Comment December 2019 1,1-DICHLOROETHENE ii DISCLAIMER Use of trade names is for identification only and does not imply endorsement by the Agency for Toxic Substances and Disease Registry, the Public Health Service, or the U.S. Department of Health and Human Services. This information is distributed solely for the purpose of pre dissemination public comment under applicable information quality guidelines. It has not been formally disseminated by the Agency for Toxic Substances and Disease Registry. It does not represent and should not be construed to represent any agency determination or policy. ***DRAFT FOR PUBLIC COMMENT*** 1,1-DICHLOROETHENE iii FOREWORD This toxicological profile is prepared in accordance with guidelines developed by the Agency for Toxic Substances and Disease Registry (ATSDR) and the Environmental Protection Agency (EPA). The original guidelines were published in the Federal Register on April 17, 1987. Each profile will be revised and republished as necessary. The ATSDR toxicological profile succinctly characterizes the toxicologic and adverse health effects information for these toxic substances described therein. Each peer-reviewed profile identifies and reviews the key literature that describes a substance's toxicologic properties. Other pertinent literature is also presented, but is described in less detail than the key studies. The profile is not intended to be an exhaustive document; however, more comprehensive sources of specialty information are referenced. The focus of the profiles is on health and toxicologic information; therefore, each toxicological profile begins with a relevance to public health discussion which would allow a public health professional to make a real-time determination of whether the presence of a particular substance in the environment poses a potential threat to human health. -
1,1-Dichloroethene (Vinylidene Chloride)
This report contains the collective views of an international group of experts and does not necessarily represent the decisions or the stated policy of the United Nations Environment Programme, the International Labour Organization, or the World Health Organization. Concise International Chemical Assessment Document 51 1,1-DICHLOROETHENE (VINYLIDENE CHLORIDE) Please note that the pagination and layout of this web version are not identical to the printed CICAD First draft prepared by Dr Bob Benson, US Environmental Protection Agency, Denver, Colorado, USA Published under the joint sponsorship of the United Nations Environment Programme, the International Labour Organization, and the World Health Organization, and produced within the framework of the Inter-Organization Programme for the Sound Management of Chemicals. World Health Organization Geneva, 2003 The International Programme on Chemical Safety (IPCS), established in 1980, is a joint venture of the United Nations Environment Programme (UNEP), the International Labour Organization (ILO), and the World Health Organization (WHO). The overall objectives of the IPCS are to establish the scientific basis for assessment of the risk to human health and the environment from exposure to chemicals, through international peer review processes, as a prerequisite for the promotion of chemical safety, and to provide technical assistance in strengthening national capacities for the sound management of chemicals. The Inter-Organization Programme for the Sound Management of Chemicals (IOMC) was established in 1995 by UNEP, ILO, the Food and Agriculture Organization of the United Nations, WHO, the United Nations Industrial Development Organization, the United Nations Institute for Training and Research, and the Organisation for Economic Co-operation and Development (Participating Organizations), following recommendations made by the 1992 UN Conference on Environment and Development to strengthen cooperation and increase coordination in the field of chemical safety. -
High Hazard Chemical Policy
Environmental Health & Safety Policy Manual Issue Date: 2/23/2011 Policy # EHS-200.09 High Hazard Chemical Policy 1.0 PURPOSE: To minimize hazardous exposures to high hazard chemicals which include select carcinogens, reproductive/developmental toxins, chemicals that have a high degree of toxicity. 2.0 SCOPE: The procedures provide guidance to all LSUHSC personnel who work with high hazard chemicals. 3.0 REPONSIBILITIES: 3.1 Environmental Health and Safety (EH&S) shall: • Provide technical assistance with the proper handling and safe disposal of high hazard chemicals. • Maintain a list of high hazard chemicals used at LSUHSC, see Appendix A. • Conduct exposure assessments and evaluate exposure control measures as necessary. Maintain employee exposure records. • Provide emergency response for chemical spills. 3.2 Principle Investigator (PI) /Supervisor shall: • Develop and implement a laboratory specific standard operation plan for high hazard chemical use per OSHA 29CFR 1910.1450 (e)(3)(i); Occupational Exposure to Hazardous Chemicals in Laboratories. • Notify EH&S of the addition of a high hazard chemical not previously used in the laboratory. • Ensure personnel are trained on specific chemical hazards present in the lab. • Maintain Material Safety Data Sheets (MSDS) for all chemicals, either on the computer hard drive or in hard copy. • Coordinate the provision of medical examinations, exposure monitoring and recordkeeping as required. 3.3 Employees: • Complete all necessary training before performing any work. • Observe all safety -
Toxicological Profile for Trichloroethylene
TRICHLOROETHYLENE 23 3. HEALTH EFFECTS 3.1 INTRODUCTION The primary purpose of this chapter is to provide public health officials, physicians, toxicologists, and other interested individuals and groups with an overall perspective on the toxicology of trichloroethylene. It contains descriptions and evaluations of toxicological studies and epidemiological investigations and provides conclusions, where possible, on the relevance of toxicity and toxicokinetic data to public health. A glossary and list of acronyms, abbreviations, and symbols can be found at the end of this profile. 3.2 DISCUSSION OF HEALTH EFFECTS BY ROUTE OF EXPOSURE To help public health professionals and others address the needs of persons living or working near hazardous waste sites, the information in this section is organized first by route of exposure (inhalation, oral, and dermal) and then by health effect (e.g., death, systemic, immunological, neurological, reproductive, developmental, and carcinogenic effects). These data are discussed in terms of three exposure periods: acute (14 days or less), intermediate (15–364 days), and chronic (365 days or more). Levels of significant exposure for each route and duration are presented in tables and illustrated in figures. The points in the figures showing no-observed-adverse-effect levels (NOAELs) or lowest- observed-adverse-effect levels (LOAELs) reflect the actual doses (levels of exposure) used in the studies. LOAELs have been classified into "less serious" or "serious" effects. "Serious" effects are those that evoke failure in a biological system and can lead to morbidity or mortality (e.g., acute respiratory distress or death). "Less serious" effects are those that are not expected to cause significant dysfunction or death, or those whose significance to the organism is not entirely clear. -
Potassium Hydroxide Pellets
SAFETY DATA SHEET Preparation Date: 3/13/2015 Revision Date: 3/13/2015 Revision Number: G1 Product identifier Product code: P1315 Product Name: POTASSIUM HYDROXIDE, PELLETS, REAGENT, ACS Other means of identification Synonyms: Caustic Potash CAS #: 1310-58-3 RTECS # TT2100000 CI#: Not available Recommended use of the chemical and restrictions on use Recommended use: Electroplating; photoengraving & lithography; printing inks; in analytical chemistry & in organic synthesis; manfufacturing of liquid soap; pharmaceutical aid (as alkalizing agent); mordant for woods; absorbing carbon dioxide; mercerizing cotton; paint & varnish removers. Principle uses of KOH include chemicals, particularly the production of potassium carbonate and potassium permaganate; pesticides, fertilizers, and other agricultural products; soaps and detergents; scrubbing and cleaning operations, e.g., industrial gases; dyes and colorants; and rubber chemicals. Uses advised against No information available Supplier: Spectrum Chemicals and Laboratory Products, Inc. 14422 South San Pedro St. Gardena, CA 90248 (310) 516-8000 Order Online At: https://www.spectrumchemical.com Emergency telephone number Chemtrec 1-800-424-9300 Contact Person: Martin LaBenz (West Coast) Contact Person: Ibad Tirmiz (East Coast) 2. HAZARDS IDENTIFICATION Classification This chemical is considered hazardous by the 2012 OSHA Hazard Communication Standard (29 CFR 1910.1200) Acute toxicity - Oral Category 3 Skin corrosion/irritation Category 1 Serious eye damage/eye irritation Category 1 Corrosive -
1 Draft Chemicals (Management and Safety)
Draft Chemicals (Management and Safety) Rules, 20xx In exercise of the powers conferred by Sections 3, 6 and 25 of the Environment (Protection) Act, 1986 (29 of 1986), and in supersession of the Manufacture, Storage and Import of Hazardous Chemical Rules, 1989 and the Chemical Accidents (Emergency Planning. Preparedness and Response) Rules, 1996, except things done or omitted to be done before such supersession, the Central Government hereby makes the following Rules relating to the management and safety of chemicals, namely: 1. Short Title and Commencement (1) These Rules may be called the Chemicals (Management and Safety) Rules, 20xx. (2) These Rules shall come into force on the date of their publication in the Official Gazette. Chapter I Definitions, Objectives and Scope 2. Definitions (1) In these Rules, unless the context otherwise requires (a) “Act” means the Environment (Protection) Act, 1986 (29 of 1986) as amended from time to time; (b) “Article” means any object whose function is determined by its shape, surface or design to a greater degree than its chemical composition; (c) “Authorised Representative” means a natural or juristic person in India who is authorised by a foreign Manufacturer under Rule 6(2); (d) “Chemical Accident” means an accident involving a sudden or unintended occurrence while handling any Hazardous Chemical, resulting in exposure (continuous, intermittent or repeated) to the Hazardous Chemical causing death or injury to any person or damage to any property, but does not include an accident by reason only -
Toxicological Review (PDF)
EPA/635/R02/002 TOXICOLOGICAL REVIEW OF 1,1-DICHLOROETHYLENE (CAS No. 75-35-4) In Support of Summary Information on the Integrated Risk Information System (IRIS) June 2002 U.S. Environmental Protection Agency Washington, DC DISCLAIMER This document has been reviewed in accordance with U.S. Environmental Protection Agency policy and approved for publication. Mention of trade names or commercial products does not constitute endorsement or recommendation for use. Note: This document may undergo revisions in the future. The most up-to-date version will be made available electronically via the IRIS Home Page at http://www.epa.gov/iris. ii CONTENTS —TOXICOLOGICAL REVIEW FOR 1,1-DICHLOROETHYLENE (CAS No. 75-35-4) FOREWORD.................................................................v AUTHORS, CONTRIBUTORS, AND REVIEWERS ................................ vi 1. INTRODUCTION ..........................................................1 2. CHEMICAL AND PHYSICAL INFORMATION RELEVANT TO ASSESSMENTS ....2 3. TOXICOKINETICS RELEVANT TO ASSESSMENTS ............................3 4. HAZARD IDENTIFICATION ................................................6 4.1. STUDIES IN HUMANS—EPIDEMIOLOGY ...............................6 4.2. PRECHRONIC AND CHRONIC STUDIES AND CANCER BIOASSAYS IN ANIMALS—ORAL AND INHALATION ..................................7 4.2.1. Acute Exposure ..................................................7 4.2.2. Longer-Term Exposure ...........................................11 4.2.3. Chronic Studies and Cancer Bioassays ...............................14 -
Trichloroethylene Environmental Hazard
ENVIRONMENTAL CONTAMINANTS ENCYCLOPEDIA TRICHLOROETHYLENE ENTRY July 1, 1997 COMPILERS/EDITORS: ROY J. IRWIN, NATIONAL PARK SERVICE WITH ASSISTANCE FROM COLORADO STATE UNIVERSITY STUDENT ASSISTANT CONTAMINANTS SPECIALISTS: MARK VAN MOUWERIK LYNETTE STEVENS MARION DUBLER SEESE WENDY BASHAM NATIONAL PARK SERVICE WATER RESOURCES DIVISIONS, WATER OPERATIONS BRANCH 1201 Oakridge Drive, Suite 250 FORT COLLINS, COLORADO 80525 WARNING/DISCLAIMERS: Where specific products, books, or laboratories are mentioned, no official U.S. government endorsement is intended or implied. Digital format users: No software was independently developed for this project. Technical questions related to software should be directed to the manufacturer of whatever software is being used to read the files. Adobe Acrobat PDF files are supplied to allow use of this product with a wide variety of software, hardware, and operating systems (DOS, Windows, MAC, and UNIX). This document was put together by human beings, mostly by compiling or summarizing what other human beings have written. Therefore, it most likely contains some mistakes and/or potential misinterpretations and should be used primarily as a way to search quickly for basic information and information sources. It should not be viewed as an exhaustive, "last-word" source for critical applications (such as those requiring legally defensible information). For critical applications (such as litigation applications), it is best to use this document to find sources, and then to obtain the original documents and/or talk to the authors before depending too heavily on a particular piece of information. Like a library or many large databases (such as EPA's national STORET water quality database), this document contains information of variable quality from very diverse sources. -
Toxicological Profile for Trichloroethylene (TCE)
TOXICOLOGICAL PROFILE FOR TRICHLOROETHYLENE U.S. DEPARTMENT OF HEALTH AND HUMAN SERVICES Public Health Service Agency for Toxic Substances and Disease Registry September 1997 TRICHLOROETHYLENE ii DISCLAIMER The use of company or product name(s) is for identification only and does not imply endorsement by the Agency for Toxic Substances and Disease Registry. TRICHLOROETHYLENE iii UPDATE STATEMENT An update Toxicological Profile for Trichloroethylene was released in April 1993. This edition supersedes any previously released draft or final profile. Toxicological profiles are revised and republished as necessary, but no less than once every three years. For information regarding the update status of previously released profiles, contact ATSDR at: Agency for Toxic Substances and Disease Registry Division of Toxicology/Toxicology Information Branch 1600 Clifton Road NE, E-29 Atlanta, Georgia 30333 *Legislative Background vi The toxicological profiles are developed in response to the Super-fund Amendments and Reauthorization Act (SARA) of 1986 (Public Law 99-499) which amended the Comprehensive Environmental Response, Compensation, and Liability Act of 1980 (CERCLA or Superfund). This public law directed ATSDR to prepare toxicological profiles for hazardous substances most commonly found at facilities on the CERCLA National Priorities List and that pose the most significant potential threat to human health, as determined by ATSDR and the EPA. The availability of the revised priority list of 275 hazardous substances was announced in the Federal Register on April 29, 1996 (61 FR 18744). For prior versions of the list of substances, see Federal Register notices dated April 17, 1987 (52 FR 12866); October 20, 1988 (53 FR 41280); October 26, 1989 (54 FR 43619); October 17,1990 (55 FR 42067); October 17, 1991 (56 FR 52166); October 28, 1992 (57 FR 48801); and February 28, 1994 (59 FR 9486). -
UPS Chemical Table ‐ ICAO/IATA Version (U.S
UPS Chemical Table ‐ ICAO/IATA Version (U.S. Air Packages) HAZARD CLASS HAZARDOUS MATERIALS DESCRIPTIONS OR DIVISION LTD QTY PASSENGER AIR CARGO AIR AND PROPER SHIPPING NAMES (Subsidiary if PACKING LABEL(S) REQUIRED OR EXEMPTION, PACKING LTD QTY PACKING PASSENGER AIR PACKING CARGO SPECIAL UNID (ALSO MARK ON PACKAGE) applicable) GROUP SPECIAL PERMIT OR EXCEPTION INSTRUCTION MAX INSTRUCTION MAX ** INSTRUCTION AIR MAX *** PROVISIONS (1) (2) (3) (4) (5) (6) (7) (8) (9) (10) (11) (12) Accellerene - see p-Nitrosodimethylaniline (UN 1369) Accumulators, electric - see Batteries etc. (UN 2794, UN 2795, UN 2800, UN 3028, UN 3292) Accumulators, pressurized, hydraulic/pneumatic (containing non-flammable gas) - see Articles, pressurized, etc. (UN 3164) UN1088 Acetal 3 II FLAMMABLE LIQUID Y341 1 L 353 5 L UN1089 Acetaldehyde Forbidden I UN1841 Acetaldehyde ammonia 9 III MISCELLANEOUS 956 30 kg 956 30 kg A48 UN2332 Acetaldehyde oxime 3 III FLAMMABLE LIQUID Y344 10 L 355 25 L CORROSIVE & UN2789 Acetic acid, glacial 8 (3) II FLAMMABLE LIQUID Y840 0.5 L 851 1 L CORROSIVE & UN2789 Acetic acid solution with > 80% acid, by mass 8 (3) II FLAMMABLE LIQUID Y840 0.5 L 851 1 L Acetic acid solution with >= 50% and <= 80% acid, by UN2790 mass 8 II CORROSIVE Y840 0.5 L 851 1 L Acetic acid solution with > 10% and < 50% acid, by UN2790 mass 8 III CORROSIVE Y841 1 L 852 5 L CORROSIVE & UN1715 Acetic anhydride 8 (3) II FLAMMABLE LIQUID Y840 0.5 L 851 1 L Acetoin - see Acetyl methyl carbinol (UN 2621) UN1090 Acetone 3 II FLAMMABLE LIQUID Y341 1 L 353 5 L UN1541 Acetone