View to Its Use in An
Total Page:16
File Type:pdf, Size:1020Kb
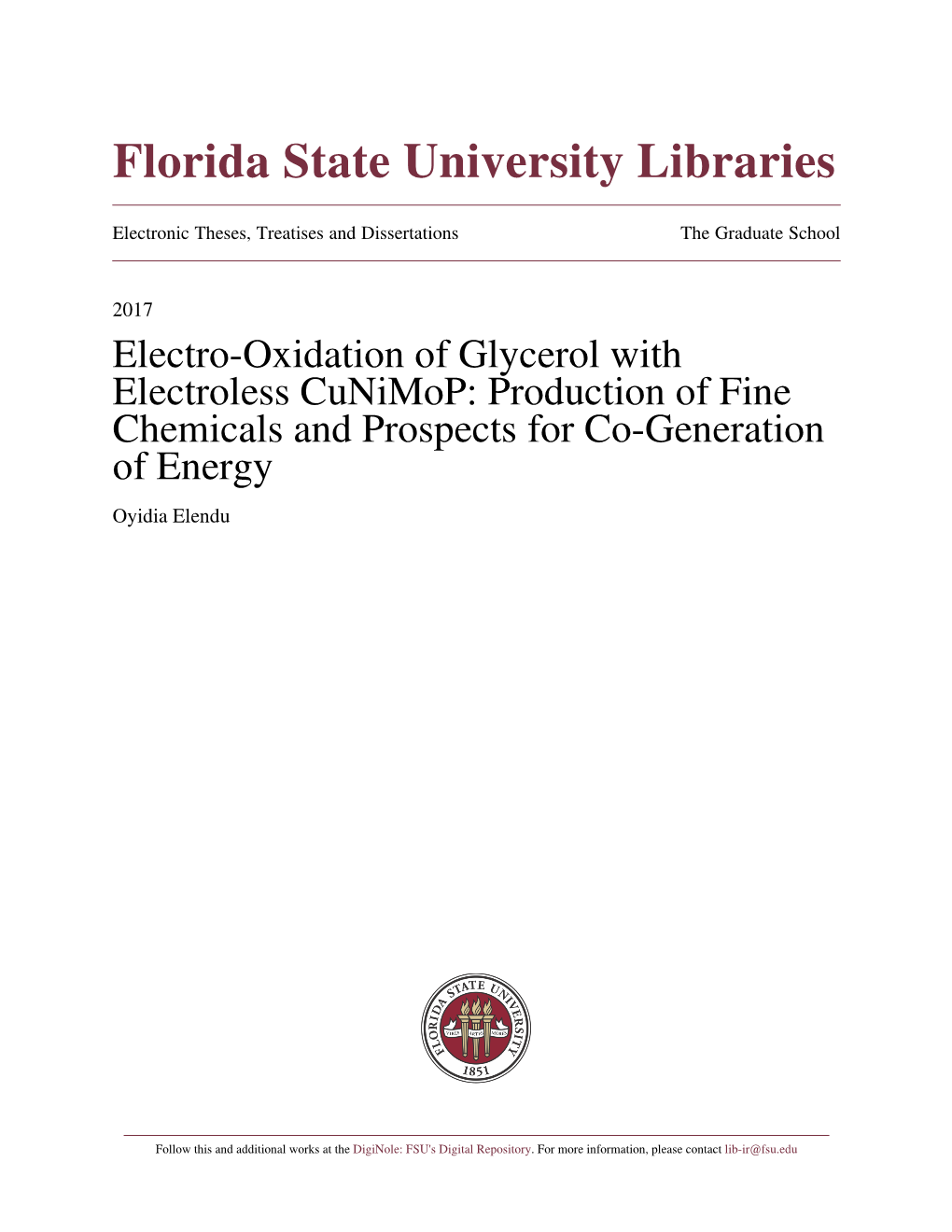
Load more
Recommended publications
-
(12) United States Patent (10) Patent No.: US 9,101,662 B2 Tamarkin Et Al
USOO91 01662B2 (12) United States Patent (10) Patent No.: US 9,101,662 B2 Tamarkin et al. (45) Date of Patent: *Aug. 11, 2015 (54) COMPOSITIONS WITH MODULATING A61K 47/32 (2013.01); A61 K9/0014 (2013.01); AGENTS A61 K9/0031 (2013.01); A61 K9/0034 (2013.01); A61 K9/0043 (2013.01); A61 K (71) Applicant: Foamix Pharmaceuticals Ltd., Rehovot 9/0046 (2013.01); A61 K9/0048 (2013.01); (IL) A61 K9/0056 (2013.01) (72) Inventors: Dov Tamarkin, Macabim (IL); Meir (58) Field of Classification Search Eini, Ness Ziona (IL); Doron Friedman, CPC ........................................................ A61 K9/12 Karmei Yosef (IL); Tal Berman, Rishon See application file for complete search history. le Ziyyon (IL); David Schuz, Gimzu (IL) (56) References Cited (73) Assignee: Foamix Pharmaceuticals Ltd., Rehovot U.S. PATENT DOCUMENTS (IL) 1,159,250 A 11/1915 Moulton (*) Notice: Subject to any disclaimer, the term of this 1,666,684 A 4, 1928 Carstens patent is extended or adjusted under 35 1924,972 A 8, 1933 Beckert 2,085,733. A T. 1937 Bird U.S.C. 154(b) by 0 days. 2,390,921 A 12, 1945 Clark This patent is Subject to a terminal dis 2,524,590 A 10, 1950 Boe claimer. 2,586.287 A 2/1952 Apperson 2,617,754 A 1 1/1952 Neely 2,767,712 A 10, 1956 Waterman (21) Appl. No.: 14/045,528 2.968,628 A 1/1961 Reed 3,004,894 A 10/1961 Johnson et al. (22) Filed: Oct. 3, 2013 3,062,715 A 11/1962 Reese et al. -
Tio2 DARK ACTIVATION and MICROBIAL STIMULATION
DISSERTATION CATALYTIC STRATEGIES FOR ENHANCING ELECTROCHEMICAL OXIDATION OF 1,4-DIOXANE: TiO2 DARK ACTIVATION AND MICROBIAL STIMULATION Submitted by Jeramy R. Jasmann Department of Chemistry In partial fulfillment of the requirements For the Degree of Doctor of Philosophy Colorado State University Fort Collins, Colorado Summer 2016 Doctoral Committee: Advisor: Thomas Borch Co-Advisor: Jens Blotevogel Delphine Farmer William Sanford James Neilson Michael Elliot Copyright by Jeramy Roland Jasmann 2016 All Rights Reserved ABSTRACT CATALYTIC STRATEGIES FOR ENHANCING ELECTROCHEMICAL OXIDATION OF 1,4-DIOXANE: TiO2 DARK ACTIVATION AND MICROBIAL STIMULATION 1,4-dioxane, a probable human carcinogen, is an emerging contaminant currently being reviewed by the U.S. Environmental Protection Agency for possible health-based maximum contaminant level regulations. As both stabilizer in commonly used chlorinated solvents and as a widely used solvent in the production of many pharmaceuticals, personal care products (PPCPs), 1,4-dioxane has been detected in surface water, groundwater and wastewater around the U.S. It is resistant to many of the traditional water treatment technologies such as sorption to activated carbon, air stripping, filtering and anaerobic biodegradation making 1,4-dioxane removal difficult and/or expensive. State-of-the art technologies for the removal of 1,4-dioxane usually apply advanced oxidation processes (AOPs) using strong oxidants in combination with UV-light and sometimes titanium dioxide (TiO2) catalyzed photolysis. These approaches require the use of expensive chemical reagents and are limited to ex situ (i.e. pump and treat) applications. Here, at Colorado State University’s Center for Contaminant Hydrology, innovative flow-through electrolytic reactors have been developed for treating groundwater contaminated with organic pollutants. -
Revised Group Additivity Values for Enthalpies of Formation (At 298 K) of Carbon– Hydrogen and Carbon–Hydrogen–Oxygen Compounds
Revised Group Additivity Values for Enthalpies of Formation (at 298 K) of Carbon– Hydrogen and Carbon–Hydrogen–Oxygen Compounds Cite as: Journal of Physical and Chemical Reference Data 25, 1411 (1996); https://doi.org/10.1063/1.555988 Submitted: 17 January 1996 . Published Online: 15 October 2009 N. Cohen ARTICLES YOU MAY BE INTERESTED IN Additivity Rules for the Estimation of Molecular Properties. Thermodynamic Properties The Journal of Chemical Physics 29, 546 (1958); https://doi.org/10.1063/1.1744539 Critical Evaluation of Thermochemical Properties of C1–C4 Species: Updated Group- Contributions to Estimate Thermochemical Properties Journal of Physical and Chemical Reference Data 44, 013101 (2015); https:// doi.org/10.1063/1.4902535 Estimation of the Thermodynamic Properties of Hydrocarbons at 298.15 K Journal of Physical and Chemical Reference Data 17, 1637 (1988); https:// doi.org/10.1063/1.555814 Journal of Physical and Chemical Reference Data 25, 1411 (1996); https://doi.org/10.1063/1.555988 25, 1411 © 1996 American Institute of Physics for the National Institute of Standards and Technology. Revised Group Additivity Values for Enthalpies of Formation (at 298 K) of Carbon-Hydrogen and Carbon-Hydrogen-Oxygen Compounds N. Cohen Thermochemical Kinetics Research, 6507 SE 31st Avenue, Portland, Oregon 97202-8627 Received January 17, 1996; revised manuscript received September 4, 1996 A program has been undertaken for the evaluation and revision of group additivity values (GAVs) necessary for predicting, by means of Benson's group additivity method, thermochemical properties of organic molecules. This review reports on the portion of that program dealing with GAVs for enthalpies of formation at 298.15 K (hereinafter abbreviated as 298 K) for carbon-hydrogen and carbon-hydrogen-oxygen compounds. -
Modeling of the Partial Oxidation of Glycerol by Estimation of Its Transfer Function
MATEC Web of Conferences 76, 04033 (2016) DOI: 10.1051/matecconf/20167604033 CSCC 2016 Modeling of the partial oxidation of glycerol by estimation of its transfer function Juan Carlos Beltrán-Prieto1,a, Karel Kolomazník1, Roman Slavík2 1 Department of Automation and Control Engineering, Faculty of Applied Informatics, Tomas Bata University in Zlín, nám. T. G. Masaryka 5555, 760 01 Zlín, Czech Republic 2 Department of Environmental Engineering Protection, Faculty of Technology, Tomas Bata University in Zlín, nám. T. G. Masaryka 275, 762 72 Zlín, Czech Republic Abstract. The reaction pathway for the conversion of glycerol into different products, namely glyceraldehyde, glyceric acid, glycolic acid, mesoxalic acid and tartronic acid was studied by means of electrochemistry. Multiple Pulse Amperometry technique was used to control the potential during the electrooxidation reaction. The estimation of the transfer function was realized on the basis of dynamic models for the oxidation reaction. The equations obtained in the s-domain were expressed in the time domain using Inverse Laplace transformation to describe the variation of glycerol and products concentration. 1 Introduction Analysis of reaction products formed during the sustained electrolysis was performed by High The partial oxidation of glycerol via heterogeneous redox Performance Liquid Chromatography (HPLC). Multiple reaction is a process that is carried out under mild pulse amperometry technique was used to control the conditions. This allows the minimization of energy waste potential during the electrooxidation reaction. Proposal of and by-products generation. This process has been a reaction pathway was performed in order to determine intensively studied by several authors [1–7]. In the rate constants, followed by the estimation of the mentioned works, glyceric acid, CO2, hydroxypyruvate, transfer function calculated on the basis of dynamic tartronic acid, mesoxalic acid, glyceraldehyde, or formic models for the anodic oxidation. -
Aerosol Fragmentation Driven by Coupling of Acid–Base and Free
Lawrence Berkeley National Laboratory Recent Work Title Aerosol Fragmentation Driven by Coupling of Acid-Base and Free-Radical Chemistry in the Heterogeneous Oxidation of Aqueous Citric Acid by OH Radicals. Permalink https://escholarship.org/uc/item/2hx5q6wq Journal The journal of physical chemistry. A, 121(31) ISSN 1089-5639 Authors Liu, Matthew J Wiegel, Aaron A Wilson, Kevin R et al. Publication Date 2017-08-01 DOI 10.1021/acs.jpca.7b04892 Peer reviewed eScholarship.org Powered by the California Digital Library University of California 1 Aerosol Fragmentation Driven by Coupling of Acid-Base and Free Radical 2 Chemistry in the Heterogeneous Oxidation of Aqueous Citric Acid by OH 3 Radicals 4 Matthew J. Liu,a,b Aaron A. Wiegel,a Kevin R. Wilson,†a and Frances A. Houle†a 5 aLawrence Berkeley National Laboratory, Chemical Sciences Division, Berkeley, CA, USA 6 94702 7 bUniversity of California, Berkeley, Department of Chemical and Biomolecular Engineering, 8 Berkeley, CA, USA 94720 9† Authors to whom correspondence should be addressed: 10Frances A. Houle ([email protected]) and Kevin R. Wilson ([email protected]) 11 12Abstract 13A key uncertainty in the heterogeneous oxidation of carboxylic acids by hydroxyl radicals (OH) 14in aqueous phase aerosol is how the free radical reaction pathways might be altered by acid-base 15chemistry. In particular, if acid-base reactions occur concurrently with acyloxy radical formation 16and unimolecular decomposition of alkoxy radicals, there is a possibility that differences in 17reaction pathways impact the partitioning of organic carbon between the gas and aqueous phases. 18To examine these questions, a kinetic model is developed for the OH initiated oxidation of citric 19acid aerosol at high relative humidity. -
11 June 2021 Aperto
AperTO - Archivio Istituzionale Open Access dell'Università di Torino Investigation of the degradation of cresols in the treatments with ozone This is the author's manuscript Original Citation: Availability: This version is available http://hdl.handle.net/2318/98980 since 2015-12-29T11:53:12Z Published version: DOI:10.1016/j.watres.2012.02.040 Terms of use: Open Access Anyone can freely access the full text of works made available as "Open Access". Works made available under a Creative Commons license can be used according to the terms and conditions of said license. Use of all other works requires consent of the right holder (author or publisher) if not exempted from copyright protection by the applicable law. (Article begins on next page) 29 September 2021 This is an author version of the contribution published on: Water Reaserch, 46, 8, 2012, DOI: 10.1016/j.watres.2012.02.0408 M.C. Valsania, F. Fasano, S.D. Richardson, M. Vincenti volume 46, Elsevier, 2012, 2795-2804 The definitive version is available at: http://www.sciencedirect.com/science/article/pii/S0043135412001431 This Accepted Author Manuscript (AAM) is copyrighted and published by Elsevier. It is posted here by agreement between Elsevier and the University of Turin. Changes resulting from the publishing process - such as editing, corrections, structural formatting, and other quality control mechanisms - may not be reflected in this version of the text. You may download, copy and otherwise use the AAM for non-commercial purposes provided that your license is limited by the following restrictions: (1) You may use this AAM for non-commercial purposes only under the terms of the CC-BY-NC-ND license. -
A Comparison Op Phenylhydrazine Oxalate with Mesoxalic Acid Phenyleydrazone
I724 W. I,. EVANS, W. L. MONG AND F. L. SINKS. [CONTRIEUTXON FROM THE CHEMICAL LABORATORYOB THE OHIO STATE UNIVERSITY.] A COMPARISON OP PHENYLHYDRAZINE OXALATE WITH MESOXALIC ACID PHENYLEYDRAZONE. BY W. L. EVANS,W. I,. MONCAND F. L. SINKS. Received May 26, 1917. While making an examination of the products obtained by the oxidation of potassium lactate by means of potassium permanganate in the presence of small quantities of potassium hydroxide, Paul A. Davis and one of us found a white, leafy, mother-of-pearl, crystalline mass after acidifying the filtrate from the oxide of manganese with acetic acid and then adding a solution of phenylhydrazine in diluted acetic acid.l This substance was associated with the pyruvic acid phenylhydrazone from which it could be easily separated, owing to the fact that it was difficultly soluble in alcohol. This compound was found to be identical in every respect with the compound described by Causse as mesoxalic acid phenylhydra- zone, m. p. 163' to 164'.~ Causse obtained this compound from bismuth mesoxalate which he had prepared by the oxidation of glycerol by means of a mixture of bismuth nitrate, potassium nitrate and nitric acid. On the other hand, Fischer3 describes mesoxalic acid phenylhydrazone as a substance which crystallizes from hot water or dilute alcohol in fine yellow needles. According to Elbers4 it has the following composition: CsH6.NH.N = C(COOH)2, and melts between 163' and 164'. Clemms gives the melting point of this compound as 174' if heated quickly. A comparison of the compound obtained by Fischer and that obtained by the repetition of Causse's experiments, showed that they were two entirely different substances. -
Carbon Dioxide Production in the Oxidation of Organic Acids by Cerium(IV) Under Aerobic and Anaerobic Conditions
JCK(Wiley) RIGHT BATCH Carbon Dioxide Production in the Oxidation of Organic Acids by Cerium(IV) under Aerobic and Anaerobic Conditions KARA BUTLER, OLIVER STEINBOCK,* BETTINA STEINBOCK,* NAR S. DALAL Florida State University, Department of Chemistry, Tallahassee, Florida 32306-3006 Received 16 March 1998; accepted 2 June 1998 ABSTRACT: The stoichiometry of CO2 production during the ceric oxidation of various organic acids is measured under conditions with organic acid excess. Measurements utilize a photo- metric methodology. For anaerobic conditions stoichiometries [CO2]produced : [Ce(IV)]reduced of about 0 (malonic acid), 0.5 (e.g., glyoxylic acid), and 1.0 (oxalic acid) are found. Oxalic acid showed an oxygen-induced decrease of CO2 production, while other compounds such as ma- lonic acid increased the amount of produced CO2 or showed no changes (e.g., tartronic acid). In the case of mesoxalic acid the stoichiometry is increased from about 0.5 to 2.0 due to the presence of molecular oxygen. The results are discussed on the basis of simple reaction mech- anisms demonstrating that useful information on reaction pathways and intermediates can be extracted from these simple measurements. ᭧ 1998 John Wiley & Sons, Inc. Int J Chem Kinet 30: 899±902, 1998 The study of oxidation of relatively low molecular and involve numerous organic acids and radicals as weight carbonic acids by metal ions has been an active intermediates [4,7]. A common characteristic, how- area of kinetics [1]. In particular the oxidation of ma- ever, is that most organic acids are oxidized to carbon lonic acid (CH2(COOH)2) and similar compounds by dioxide. -
G166766A Agilent Fiehn GC/MS Metabolomics RTL Library: List of Compounds
G166766A Agilent Fiehn GC/MS Metabolomics RTL Library: List of Compounds Data Sheet 800 Metabolite library for more compound identification The Agilent Fiehn GC/MS metabolomics RTL Library is the most comprehensive commercially available GC/MS library of metabolite spectra. This expanding library currently contains over 1,400 entries for approximately 800 common metabolites, including spectra corresponding to partial derivatization of metabolites under the recommended conditions. In this list, each entry includes the name, CAS, and PubChem numbers of the native molecule for easier compound recognition and subsequent literature, software, and pathway searching. -
University Microfilms, Inc., Ann Arbor, Michigan ILLUS TRATIONS— (Continued) Figure Page
This dissertation has been 64—6920 microfilmed exactly as received JORDAN, John Maxwell, 1938- STUDIES ON METABOLISM IN PENICILLIUM CHARLESII; SOME RELATIONSHIPS BETWEEN DICARBOXYLIC ACID METABOLISM AND PRO DUCTION OF GALACTOCAROLOSE. The Ohio State University, Ph.D., 1963 Chemistry, biological University Microfilms, Inc., Ann Arbor, Michigan ILLUS TRATIONS— (Continued) Figure Page 12 Variation with time of carbohydrate concentration of systems containing various concentrations of diammonium dihydroxymaleate . ................ 88 13 Atypical behavior of system containing high level of medium n i t r o g e n ......................... 99 14 Changes in hydrogen ion concentration and carbo hydrate concentration of growth medium of the RTg and RT^ series ...•••• ............. 101 15 Changes in hydrogen ion and carbohydrate concen tration of the growth medium for the DHM_ and DHM., series ........... ......... • • 104 16 Changes in hydrogen ion and carbohydrate concen tration of the growth medium for the Funig and Fum^ series .................... ........ 106 17 Changes in hydrogen ion and carbohydrate concen tration of the growth medium for the Mal_ and Mal^ series 110 32 18 Distribution of P -labeled components of a perchloric acid extract of P. charlesii exposed 4.5 days to orthophosphate-P^^ • • • T ..... 126 32 19 Distribution of P -labeled components of a perchloric acid extract of P. charlesii exposed 9 days to orthophosphate-P^............. 129 32 20 Distribution of P -labeled components of a . perchloric acid extract of P. charlesii exposed 13.5 days to orthophosphate-P^ . I I ~ ..... 133 32 21 Distribution of P -labeled components of a perchloric acid extract of P. charlesii exposed l8.0 days to orthophosphate-P^^T • • • • • 136 22 Distribution of P^-labeled and U.V.-light ab sorbing components of perchloric acid extract of P. -
12Th-Chemistry-Interior-Questions.Pdf
www.Padasalai.Net www.TrbTnpsc.com XII STANDARD CHEMISTRY ONE MARKS [2010 – 2011] 1. The wavelength associated with a particle mass 3.313x10-31 kg moving with velocity of 103 ms 1 is a) 2x10-6m b) 2x10-6cm c) 2x10-7m d) 2x10-7cm 2. Which one of the following particle having same kinetic energy, would have the maximum de – Broglie wave length? a) α – particle b) proton c) - particle d) neutron 3. Which is the most stable molecule? a) N2 b) O2 c) He2 d) Li2 4. The compound formed by SP hybridization is a) NH3 b) CH4 c) BeCl2 d) C2H4 5. Paramagnetic nature can be seen in the molecule having a) a paired electron b) a lone pair of electron c) lone electron d) all of these 6. Bond order can be calculated using the formula a) ½ (Nb-Na) b) ½ (Na-Nb) c) 2 (Na-Nb) d) 2 (Nb-Na) 7. Which is incorrect? a) bond order may be fractional b) if Nb>Na molecule is stable c) greater the bond length stronger the bond d) if Nb=Na molecule is unstable 8. Which is the correct form of Heisenberg’s uncertainity principle? a) X. V = h/4π b) X. p < h/4π c) X. P > h/4π d) X. p > h/2π 9. De – Broglie’s wavelength of a particle is 1x10-10cm then its momentum is a) 6.63x10-24kg ms-1 b) 6.63x10-32kg ms-1 c) 6.63 x10-31kg ms-1 d) 6.63x10-29kg ms -1 10.Which is used by Thomson for his experiment to study the diffraction pattern of electron? a) Gold b) Nickel c) Zinc sulphide d) Silver - 11.The hybridization present in ICl4 is a) sp3 b) dsp3 c) sp3d2 d) sp2 12.The strength of hydrogen bond in decreasing order is www.Padasalai.Neta) H-F>H2O>NH3 b) NH3>H2O>HF c) HF>NH3>H2O -
Catalytic Oxidation of Glycerol to Dihydroxyacetone
CATALYTIC OXIDATION OF GLYCEROL TO DIHYDROXYACETONE Wenbin Hu, Brian Lowry and Arvind Varma * School of Chemical Engineering, Purdue University, West Lafayette, IN 47907, USA Summary Selective oxidation of glycerol to dihydroxyacetone was investigated using Pt-Bi/C bi-metallic catalyst. The catalysts with different metal loadings, supports and synthesis methods were synthesized and tested in a semi-batch reactor. The optimum catalyst was 3wt%Pt, with sequential 0.6wt%Bi impregnation on Norit Darco 20-40 mesh activated carbon, followed by NaBH 4 reduction, for reaction rate and DHA selectivity. With the optimum catalyst, the reaction conditions (temperature, pressure, pH, etc) in the semi-batch reactor were optimized, with which the maximum DHA yield of 46% was obtained at nearly full glycerol conversion. The catalysts were characterized using BET, ICP-OES, TEM, XRD and XPS techniques. Keywords Glycerol; Dihydroxyacetone; Selective Oxidation; Platinum-Bismuth catalyst Introduction Identifying new uses of glycerol, a waste of biodiesel Experimental production from transesterification of vegetable oils, is of Catalyst Synthesis great current interest. Towards this end, many value-added Pt-Bi/C catalysts with different loadings, supports, chemicals, such as propanediol, propylene, impregnation sequences and reduction methods were epichlorohydrin and methanol, have been explored by synthesized. A typical synthesis procedure is described as chemical companies. The use of glycerol to synthesize follows: activated carbon (AC) was submerged in water these chemicals, however, is less attractive due to the with sonication. A predetermined amount of chloroplatinic limited amount of value added. We use glycerol as a acid hydrate was dissolved in 1.2N HCl and added feedstock for its selective oxidation to produce high-value dropwise to the well-stirred AC slurry.