Uranium Hexafluoride Handling
Total Page:16
File Type:pdf, Size:1020Kb
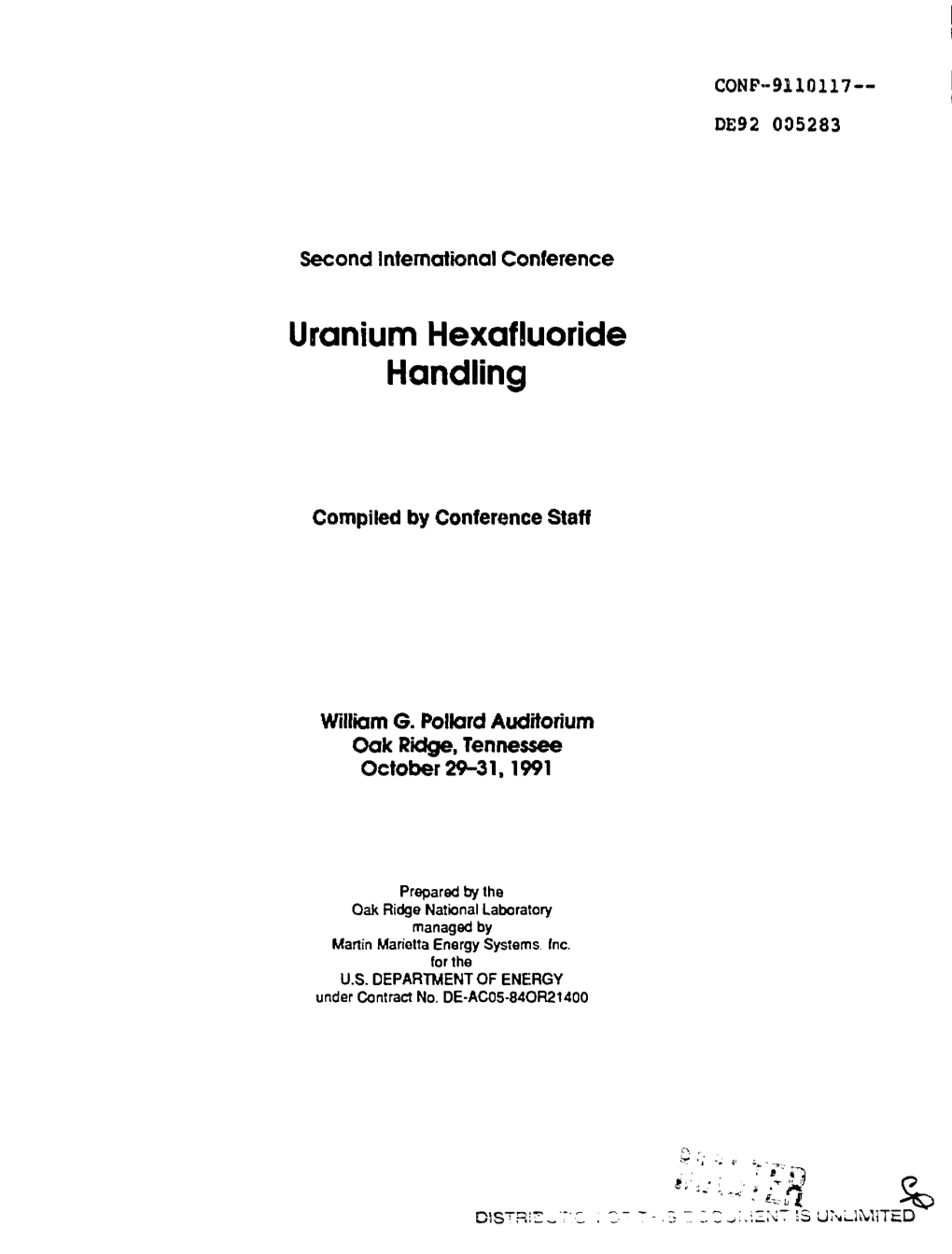
Load more
Recommended publications
-
A Guide to Export Controls
Foreign Affairs, Trade and Affaires étrangères, Commerce et Development Canada Développment Canada A Guide To CANADA’S EXPORT CONTROLS December 2012 Introduction The issuance of export permits is administered by the Export Controls Division (TIE) of Foreign Affairs, Trade and Development Canada (DFATD). TIE provides assistance to exporters in determining if export permits are required. It also publishes brochures and Notices to Exporters that are freely available on request and on our website www.exportcontrols.gc.ca. How to contact us: Export Controls Division (TIE) Foreign Affairs, Trade and Development Canada 111 Sussex Drive Ottawa, Ontario K1A 0G2 Telephone: (613) 996-2387 Facsimile: (613) 996-9933 Email: [email protected] For information on how to apply for an export permit and additional information on export controls please refer to our website. To enquire on the status of an export permit application: Recognized EXCOL users can check the status of an export permit application on-line. Non-recognized users can call (613) 996-2387 or email [email protected] and quote your export permit application identification (ref ID) number. Export Controls Division website: www.exportcontrols.gc.ca This Guide, at time of publication, encompasses the list of items enumerated on the Export Control List (ECL) that are controlled for export in accordance with Canadian foreign policy, including Canada’s participation in multilateral export control regimes and bilateral agreements. Unless otherwise specified, the export controls contained in this Guide apply to all destinations except the United States. Canada’s Export Control List can be found at the Department of Justice website at http://canada.justice.gc.ca/. -
Key Official US and IAEA Statements About Iran's Nuclear Programs
Key Official US and IAEA Statements About Iran’s Nuclear Programs Anthony H. Cordesman There is a great deal of speculation about Iran’s nuclear programs that do not list sources or reflect the views of the US intelligence community. It is worth examining what top US intelligence official have said during the last few years, and the details of the IAEA report published in November 2011 – one that clearly reflected official inputs from the US and a number of European intelligence services. U.S. Official Statements on the Iranian Nuclear and Missile Threat The annual unclassified reports to Congress by the Office of the Director of National Intelligence are a key source of US official view. Although the 2010 report by James R. Clapper has already been partly overtaken by the pace of Iran’s rapidly developing program, it still represents the most detailed unclassified estimate of Iran’s capabilities by a senior US official:1 Nuclear We continue to assess Iran is keeping open the option to develop nuclear weapons though we do not know whether Tehran eventually will decide to produce nuclear weapons. Iran continues to develop a range of capabilities that could be applied to producing nuclear weapons, if a decision is made to do so. During the reporting period, Iran continued to expand its nuclear infrastructure and continued uranium enrichment and activities related to its heavy water research reactor, despite multiple United Nations Security Council Resolutions since late 2006 calling for the suspension of those activities. Although Iran made progress in expanding its nuclear infrastructure during 2001, some obstacles slowed progress during this period. -
Depleted Uranium Hexafluoride: Waste Or Resource?
UCRGJC-120397 PREPRINT Depleted Uranium Hexafluoride: Waste or Resource? N. Schwertz J. Zoller R Rosen S. Patton C. Bradley A. Murray This paper was prepared for submittal to the Global ‘95 International Conference on Evaluation of Emerging Nuclear Fuel Cycle Systems Versailles, France September 11-14,1995 July 1995 This isa preprint of apaper intended for publication in a jaurnal orproceedings. Since changes may be made before publication, this preprint is made available with the understanding that it will not be cited or reproduced without the permiasion of the anthor. DISCLAIMER This document was prepared as an account of work sponsored by an agency of the United Stat= Government. Neither theunited States Governmentmor theuniversity of California nor any oftheir employees, makes any warranty, express or implied, or assumesanylegalliabilityorrespomibility forthe accuracy,completeness,orusefuin~ of any information, apparatus, pduct, or process disdosed, or represents that its use wouldnotinfringe privatelyowned rights. Referencehemin to anyspe&c commercial prodocis, proms, or service by trade name, trademark, manufacturer, or otherwise, does not necessarily constituteor imply its endorsement, reconunendation, or favoring by the United States Government or the University of California. The views and opinions of authors expressed herein do not necessady state or reflect those of the United States Government or the University of California, and shall not be used for adveltising or product endorsement purposes. DISCLAIMER Portions of this document may be illegible in electronic image products. Images are produced from the best available original document . DEPLETED URANIUM HEXAFLUORIDE: WASTE OR RESOURCE? N. Schwertz, J. Zoller, R. Rosen, S. Patton LAWRENCE LIVERMORE NATIONAL LABORATORY P. -
Uranium Aerosols at a Nuclear Fuel Fabrication Plant: Characterization Using Scanning Electron Microscopy and Energy Dispersive X-Ray Spectroscopy
Spectrochimica Acta Part B 131 (2017) 130–137 Contents lists available at ScienceDirect Spectrochimica Acta Part B journal homepage: www.elsevier.com/locate/sab Uranium aerosols at a nuclear fuel fabrication plant: Characterization using scanning electron microscopy and energy dispersive X-ray spectroscopy E. Hansson a,b,⁎, H.B.L. Pettersson a, C. Fortin c, M. Eriksson a,d a Department of Medical and Health Sciences, Linköping University, 58185 Linköping, Sweden b Westinghouse Electric Sweden AB, Bränslegatan 1, 72136 Västerås, Sweden c Carl Zeiss SAS, 100 route de Versailles, 78160 Marly-le-Roi, France d Swedish Radiation Safety Authority, 17116 Stockholm, Sweden article info abstract Article history: Detailed aerosol knowledge is essential in numerous applications, including risk assessment in nuclear industry. Received 31 March 2016 Cascade impactor sampling of uranium aerosols in the breathing zone of nuclear operators was carried out at a Received in revised form 28 February 2017 nuclear fuel fabrication plant. Collected aerosols were evaluated using scanning electron microscopy and energy Accepted 3 March 2017 dispersive X-ray spectroscopy. Imaging revealed remarkable variations in aerosol morphology at the different Available online 6 March 2017 workshops, and a presence of very large particles (up to≅100 × 50 μm2) in the operator breathing zone. Charac- teristic X-ray analysis showed varying uranium weight percentages of aerosols and, frequently, traces of nitrogen, Keywords: fl Uranium uorine and iron. The analysis method, in combination with cascade impactor sampling, can be a powerful tool Aerosol for characterization of aerosols. The uranium aerosol source term for risk assessment in nuclear fuel fabrication Impactor appears to be highly complex. -
ANNEX III Restricted Nuclear Goods, Commodities, and Technologies
ANNEX III* Restricted Nuclear Goods, Commodities, and Technologies Pursuant to paragraph 5 (b) of resolution 2087 (2013), the items contained in this document are subject to the provisions of paragraph 8 (a), 8 (b) and 8 (c) of resolution 1718 (2006) under the DPRK sanctions regime; and pursuant to resolution 1929 (2010) under the Iran sanctions regime (corresponding with document INFCIRC/254/Rev.11/Part1‐1) * Annex III to Enrico Carisch and Loraine Rickard-Martin, “United Nations Sanctions on Iran and North Korea: An Implementation Manual,” New York: International Peace Institute. March 2014. UN Sanctions on Iran and North Korea SPECIAL FISSIONABLE MATERIAL INFCIRC/254/Rev.11/Part1 ANNEX B Plutonium-239 For plutonium to reach this state it has to be processed from U-238. Plutonium in this form has gone through a nuclear reactor. Varies based on level of enrichment and portion of Pu-240 inherent in the metal. ~5 kg of very pure Pu- 239 is enough for a strategic nuclear weapon. This metal is extremely heavy per unit of volume. This is a radioactive isotope of plutonium; it generally will be transported in ways to minimize radioactive exposure—lead-lined containers, etc. Uranium-233 Made from thorium-232. It has never been used to generate power or in nuclear weapons, but it has been used in research reactors. Production costs alone have been estimated at 2–4 million per kilogram during the Cold War. This metal is extremely heavy per unit of volume. This is a radioactive isotope of uranium; it generally will be transported in ways to minimize radioactive exposure—lead-lined containers, etc. -
WO 2016/074683 Al 19 May 2016 (19.05.2016) W P O P C T
(12) INTERNATIONAL APPLICATION PUBLISHED UNDER THE PATENT COOPERATION TREATY (PCT) (19) World Intellectual Property Organization International Bureau (10) International Publication Number (43) International Publication Date WO 2016/074683 Al 19 May 2016 (19.05.2016) W P O P C T (51) International Patent Classification: (81) Designated States (unless otherwise indicated, for every C12N 15/10 (2006.01) kind of national protection available): AE, AG, AL, AM, AO, AT, AU, AZ, BA, BB, BG, BH, BN, BR, BW, BY, (21) International Application Number: BZ, CA, CH, CL, CN, CO, CR, CU, CZ, DE, DK, DM, PCT/DK20 15/050343 DO, DZ, EC, EE, EG, ES, FI, GB, GD, GE, GH, GM, GT, (22) International Filing Date: HN, HR, HU, ID, IL, IN, IR, IS, JP, KE, KG, KN, KP, KR, 11 November 2015 ( 11. 1 1.2015) KZ, LA, LC, LK, LR, LS, LU, LY, MA, MD, ME, MG, MK, MN, MW, MX, MY, MZ, NA, NG, NI, NO, NZ, OM, (25) Filing Language: English PA, PE, PG, PH, PL, PT, QA, RO, RS, RU, RW, SA, SC, (26) Publication Language: English SD, SE, SG, SK, SL, SM, ST, SV, SY, TH, TJ, TM, TN, TR, TT, TZ, UA, UG, US, UZ, VC, VN, ZA, ZM, ZW. (30) Priority Data: PA 2014 00655 11 November 2014 ( 11. 1 1.2014) DK (84) Designated States (unless otherwise indicated, for every 62/077,933 11 November 2014 ( 11. 11.2014) US kind of regional protection available): ARIPO (BW, GH, 62/202,3 18 7 August 2015 (07.08.2015) US GM, KE, LR, LS, MW, MZ, NA, RW, SD, SL, ST, SZ, TZ, UG, ZM, ZW), Eurasian (AM, AZ, BY, KG, KZ, RU, (71) Applicant: LUNDORF PEDERSEN MATERIALS APS TJ, TM), European (AL, AT, BE, BG, CH, CY, CZ, DE, [DK/DK]; Nordvej 16 B, Himmelev, DK-4000 Roskilde DK, EE, ES, FI, FR, GB, GR, HR, HU, IE, IS, IT, LT, LU, (DK). -
Chemistry of the Noble Gases*
CHEMISTRY OF THE NOBLE GASES* By Professor K. K. GREE~woon , :.\I.Sc., sc.D .. r".lU.C. University of N ewca.stle 1tpon Tyne The inert gases, or noble gases as they are elements were unsuccessful, and for over now more appropriately called, are a remark 60 years they epitomized chemical inertness. able group of elements. The lightest, helium, Indeed, their electron configuration, s2p6, was recognized in the gases of the sun before became known as 'the stable octet,' and this it was isolated on ea.rth as its name (i]A.tos) fotmed the basis of the fit·st electronic theory implies. The first inert gas was isolated in of valency in 1916. Despite this, many 1895 by Ramsay and Rayleigh; it was named people felt that it should be possible to induce argon (apy6s, inert) and occurs to the extent the inert gases to form compounds, and many of 0·93% in the earth's atmosphere. The of the early experiments directed to this end other gases were all isolated before the turn have recently been reviewed.l of the century and were named neon (v€ov, There were several reasons why chemists new), krypton (KpVn'TOV, hidden), xenon believed that the inert gases might form ~€vov, stmnger) and radon (radioactive chemical compounds under the correct con emanation). Though they occur much less ditions. For example, the ionization poten abundantly than argon they cannot strictly tial of xenon is actually lower than those of be called rare gases; this can be illustrated hydrogen, nitrogen, oxygen, fl uorine and by calculating the volumes occupied a.t s.t.p. -
Nuclear Iran a Glossary of Terms
Nuclear Iran A Glossary of Terms Simon Henderson and Olli Heinonen Policy Focus 121 | May 2013 Update HARVARD Kennedy School A COPUBLICATION WITH BELFER CENTER for Science and International Affairs Map: Nuclear installations in Iran. TURKMENISTAN TABRIZ Bonab Lashkar Abad TEHRAN MASHAD Karaj Marivan Parchin Fordow Arak QOM IRAQ Natanz AFGHANISTAN Isfahan Ardakan Saghand Darkhovin Yazd IRAN KUWAIT SHIRAZ Bushehr PAKISTAN Gchine BANDAR ABBAS BAHRAIN SAUDI ARABIA QATAR © 2012 The Washington Institute for Near East Policy UAE OMAN Map: Nuclear installations in Iran. Nuclear Iran A Glossary of Terms Simon Henderson and Olli Heinonen Policy Focus 121 | May 2013 Update HARVARD Kennedy School A COPUBLICATION WITH BELFER CENTER for Science and International Affairs n n n The authors extend special thanks to Mary Kalbach Horan and her editorial team at The Washington Institute. n n n All rights reserved. Printed in the United States of America. No part of this publication may be reproduced or transmitted in any form or by any means, electronic or mechanical, including photocopy, recording, or any information storage and retrieval system, without permission in writing from the publisher. © 2012, 2013 by The Washington Institute for Near East Policy and the Harvard Kennedy School’s Belfer Center for Science and International Affairs Copublished in 2012 and 2013 in the United States of America by The Washington Institute for Near East Policy, 1828 L Street NW, Suite 1050, Washington, DC 20036; and the Harvard Kennedy School’s Belfer Center for Science and International Affairs, 79 JFK St., Cambridge, MA 02138. Cover photo: Iran’s president Mahmoud Ahmadinejad visits the Natanz nuclear enrichment facility. -
The Noble Gases
INTERCHAPTER K The Noble Gases When an electric discharge is passed through a noble gas, light is emitted as electronically excited noble-gas atoms decay to lower energy levels. The tubes contain helium, neon, argon, krypton, and xenon. University Science Books, ©2011. All rights reserved. www.uscibooks.com Title General Chemistry - 4th ed Author McQuarrie/Gallogy Artist George Kelvin Figure # fig. K2 (965) Date 09/02/09 Check if revision Approved K. THE NOBLE GASES K1 2 0 Nitrogen and He Air P Mg(ClO ) NaOH 4 4 2 noble gases 4.002602 1s2 O removal H O removal CO removal 10 0 2 2 2 Ne Figure K.1 A schematic illustration of the removal of O2(g), H2O(g), and CO2(g) from air. First the oxygen is removed by allowing the air to pass over phosphorus, P (s) + 5 O (g) → P O (s). 20.1797 4 2 4 10 2s22p6 The residual air is passed through anhydrous magnesium perchlorate to remove the water vapor, Mg(ClO ) (s) + 6 H O(g) → Mg(ClO ) ∙6 H O(s), and then through sodium hydroxide to remove 18 0 4 2 2 4 2 2 the carbon dioxide, NaOH(s) + CO2(g) → NaHCO3(s). The gas that remains is primarily nitrogen Ar with about 1% noble gases. 39.948 3s23p6 36 0 The Group 18 elements—helium, K-1. The Noble Gases Were Kr neon, argon, krypton, xenon, and Not Discovered until 1893 83.798 radon—are called the noble gases 2 6 4s 4p and are noteworthy for their rela- In 1893, the English physicist Lord Rayleigh noticed 54 0 tive lack of chemical reactivity. -
Sorption of Np and Tc in Underground Waters by Uranium Oxides
Sorption of Np and Tc in Underground Waters by Uranium Oxides T.V.Kazakovskaya,a V.I. Shapovalova, N.V. Kushnira , E.V. Zakharovab, S.N.Kalmykovb O.N.Batukb, M.J.Hairec a –Russian Federal Nuclear center –All-Russia Scientific Institute of Experimental Physics; 607190, Sarov, Russia, E-mail: [email protected]; b – Institute of Physical Chemistry and Electrochemistry, Russian Academy of Sciences, Moscow, Russia, c – Oak Ridge National Laboratory, Oak Ridge, Tennessee. Abstract –The production of nuclear fuels results in the accumulation of large quantities of depleted uranium (DU) in the form of uranium hexafluoride (UF6), which is converted to uranium oxides. Depleted uranium dioxide (DUO2) can be used as a component of radiation shielding and as an absorbent for migrating radionuclides (especially 237Np and 99Tc). These may emerge from casks containing spent nuclear fuel (SNF) that are stored for hundreds of thousands of years in high-level wastes (HLW) and SNF repositories (e.g. Yucca Mountain Project). In this case DU oxides serve as an additional engi- neered chemical barrier. This work is a part of the joint Russian –American Program on Beneficial Use of Depleted Uranium. This paper describes the UO2 transformations that take place in contact with various aqueous media (deionized water (DW), J-13 solution that simulates Yucca Mountain ground water, etc.) and sorption of long-lived radionuclides (237Np and 99Тс) from these media by depleted uranium dioxide. Samples of depleted uranium dioxide used in this work originated from the treatment of UF6 in a reducing media to form UO2 (DUO2-1 at 600°C, DUO2-2 at 700°C, and DUO2-3 at 800°C). -
00419717.Pdf
APPROVED FOR PUBLIC RELEASE APPROVED FOR PUBLIC RELEASE APPROVED FOR PUBLIC RELEASE ~ ,—- UNWMFIED — PUBUCLYREI-EMABLF . ,$5 ~ .~16f3 This Document Consists of 18 Pages /“ @ LQS ALAMOS SCIENTIFIC LABORATORY Contribution from Chemistry-MetallurgyDivision E. R. Jette, Division Leader J. F, Lemons, Group Leader Plutonium~‘=Hexaf uor e: Preparation and Properties w A. E. Flor November 9, 1950 — ‘1” Chemistry-Tranwrs.nicElements “-+ - ,- —. 1 Y– -t APPROVED FOR PUBLIC RELEASE — APPROVED FOR PUBLIC RELEASE LA-I.M8 UNCLASSIFIED Los tiSDIOS 1-20 STANDARD DISTRIBUTION Argonne,I?ationslLaboratory 21-30 Atomic Energy Commission, Washington 31-32 Brookhaven National Laboratory 33-36 Carbide and Carbon Cheticals Division (K-25 Plant) 37-38 Carbide and Carbon Chemicsl.sDivision (Y-12 Plant) General.Electric Company, Richland Z-45 Hanford Operations Office 46 Iowa State College 47 Kellex Corporation 4.$ Knolls Atomic Power Laboratory g-;; Mound Laboratory Navel Radiological Defense Laboratory 56- NEPA Project 57 New York Operations Office 58-59 Oak Ridge National Laboratory 60-65 Patent Branch, Washington 66 Technical Information Division, ORE 6741 UCLA Medical Research Laboratory (Warren) University of California Radiatio nLaboratory %85 University of Rochester 86-87 2 APPROVED FOR PUBLIC RELEASE — APPROVED FOR PUBLIC RELEASE Introduction It is the purpose of this paper to present the results of experi- mental investigations on the chemistry of plutonium hernfluoride con- ducted at this laboratory subsequent to the preparation of report LAMS 1118(1). A more satisfactory apparatus for the preparation is des- cribed. More reliable values for the vapor pressure have been obtained and the related physical constants have been calculated. The rate of decomposition of the compound as a result of the associated alpha radiation has been determined and a preliminary observation on the thermal stability is reported. -
DEPLETED URANIUM HEXAFLUORIDE (Current Situation, Safe Handling and Prospects)
DEPLETED URANIUM HEXAFLUORIDE (current situation, safe handling and prospects) 2020 Authors: Alexander Nikitin, Head of Bellona Foundation Oleg Muratov, nuclear physicist, Head of Radiation Technology Dept., TVEL JSC Ksenia Vakhrusheva, Cand. Sci. Econ., Expert, BELLONA International Foundation Editor: Elena Verevkina Design: Alexandra Solokhina This Report was prepared with support and participation of Environmental Board of the Public Council of Rosatom State Atomiс Energy Corporation Publishers: Bellona Foundation Environmental Protection NGO ‘Ecopravo’ Expert and Legal Center TABLE OF CONTENTS Abbreviations ............................................................................................................................. 4 Foreword ..................................................................................................................................... 5 Introduction ................................................................................................................................ 6 Chapter 1. A few words about nuclear physics and radioactivity for non-specialists............... 8 Chapter 2. Uranium hexafluoride and its properties ..................................................................... 11 2.1. Physical properties of uranium hexafluoride .................................................................. 12 2.2. Chemical properties of uranium hexafluoride ................................................................ 13 Chapter 3. What is DUHF ..................................................................................................................