High Temperature Thruster Technology for Spacecraft Propulsion
Total Page:16
File Type:pdf, Size:1020Kb
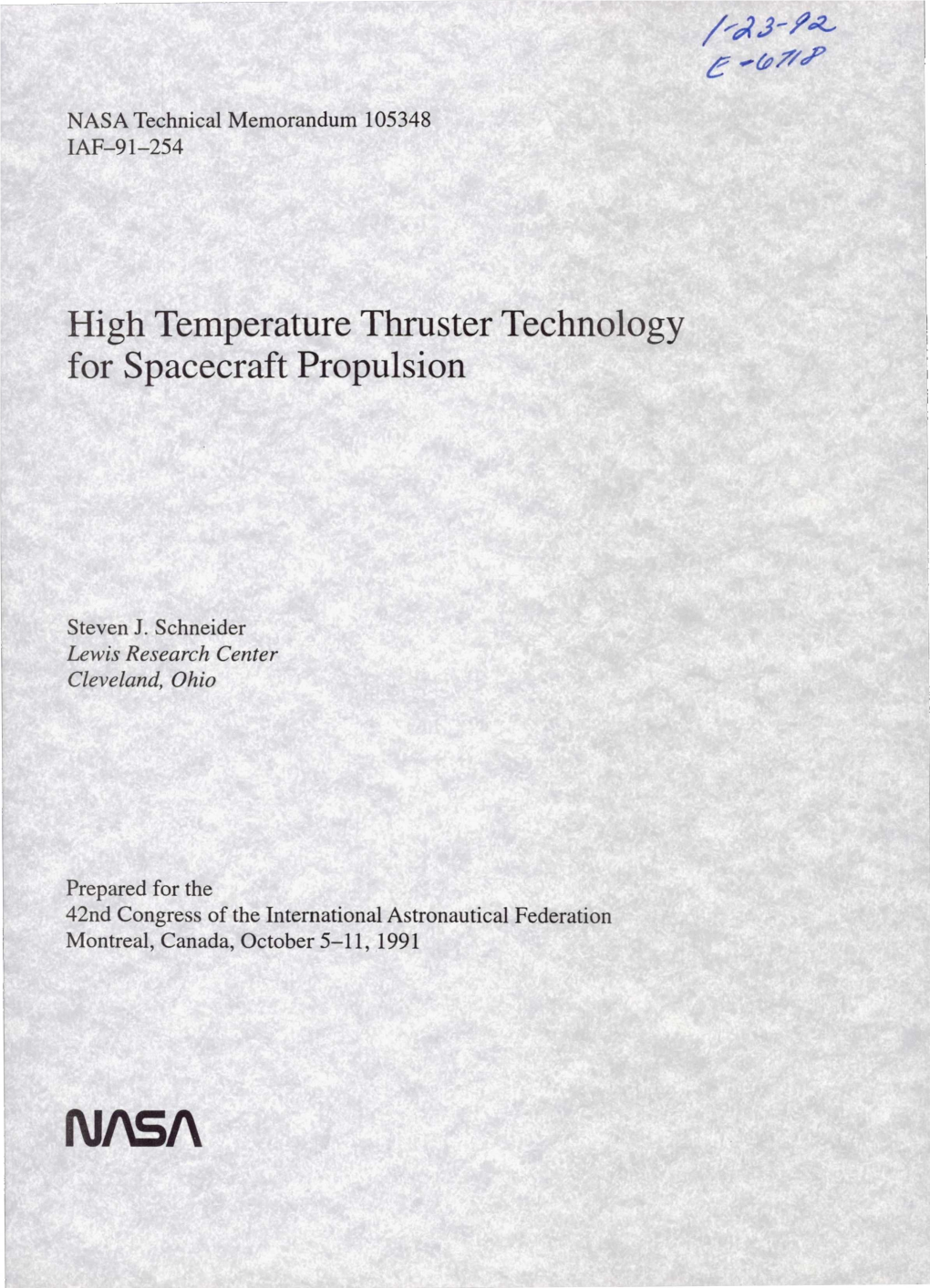
Load more
Recommended publications
-
Microgravity and Macromolecular Crystallography Craig E
CRYSTAL GROWTH & DESIGN 2001 VOL. 1, NO. 1 87-99 Review Microgravity and Macromolecular Crystallography Craig E. Kundrot,* Russell A. Judge, Marc L. Pusey, and Edward H. Snell Mail Code SD48 Biotechnology Science Group, NASA Marshall Space Flight Center, Huntsville, Alabama 35812 Received August 24, 2000 ABSTRACT: Macromolecular crystal growth is seen as an ideal experiment to make use of the reduced acceleration environment provided by an orbiting spacecraft. The experiments are small, are simply operated, and have a high potential scientific and economic impact. In this review we examine the theoretical reasons why microgravity is a beneficial environment for crystal growth and survey the history of experiments on the Space Shuttle Orbiter, on unmanned spacecraft, and on the Mir space station. The results of microgravity crystal growth are considerable when one realizes that the comparisons are always between few microgravity-based experiments and a large number of earth-based experiments. Finally, we outline the direction for optimizing the future use of orbiting platforms. 1. Introduction molecules, including viruses, proteins, DNA, RNA, and complexes of those molecules. In this review, the terms Macromolecular crystallography is a multidisciplinary protein or macromolecule are used to refer to this entire science involving the crystallization of a macromolecule range. or complex of macromolecules, followed by X-ray or The reduced acceleration environment of an orbiting neutron diffraction to determine the three-dimensional spacecraft has been posited as an ideal environment for structure. The structure provides a basis for under- biological crystal growth, since buoyancy-driven convec- standing function and enables the development of new tion and sedimentation are greatly reduced. -
Summary of Liquid Propulsion System Needs in Support of The
· m~-W Summary ofLiquid Propulsion System Needs in Support ofthe Constellation Program Terry Lorier, Program Manager, Space Propulsion Systems Development Pratt & Whitney Rocketdyne Canoga Park, CA Phil Sumrall, AdvancedPlanning Manager, Ares Projects Office NASA Marshall Space Flight Center Huntsville. AL Michael Baine, Ph.D., Orion Propulsion System Manager NASA Johnson Space Center Houston, TX Abstract In January 2004, the President ofthe United States established the Vision for Space Exploration (VSE) to complete the International Space Station, retire the Space Shuttle and develop its replacement, and expand the human presence on the Moon as a stepping stone to human exploration ofMars and worlds beyond. In response, NASA developed the Constellation Program, consisting ofthe components shown in Figure 1. This paper will summarize the manned spaceflight liquid propulsion system needs in support ofthe Constellation Program over the next 10 years. It will address all liquid engine needs to support human exploration from low Earth orbit (LEO) to the lunar surface, including an overview ofengines currently under contract, those baselined but not yet under contract, and those propulsion needs that have yet to be initiated. There may be additional engine needs for early demonstrators, but those will not be addressed as part ofthis paper. Also, other portions ofthe VSE architecture, including the planned Orion abort test boosters and the Lunar Precursor Robotic Program, are not addressed here as they either use solid motors or are focused on unmanned elements ofreturning humans to the Moon. Our Exploration Fleet What will the vehicles look like? Orion Crew Exploration Vehicle Figure 1. Constellation Program components I. -
Failures in Spacecraft Systems: an Analysis from The
FAILURES IN SPACECRAFT SYSTEMS: AN ANALYSIS FROM THE PERSPECTIVE OF DECISION MAKING A Thesis Submitted to the Faculty of Purdue University by Vikranth R. Kattakuri In Partial Fulfillment of the Requirements for the Degree of Master of Science in Mechanical Engineering August 2019 Purdue University West Lafayette, Indiana ii THE PURDUE UNIVERSITY GRADUATE SCHOOL STATEMENT OF THESIS APPROVAL Dr. Jitesh H. Panchal, Chair School of Mechanical Engineering Dr. Ilias Bilionis School of Mechanical Engineering Dr. William Crossley School of Aeronautics and Astronautics Approved by: Dr. Jay P. Gore Associate Head of Graduate Studies iii ACKNOWLEDGMENTS I am extremely grateful to my advisor Prof. Jitesh Panchal for his patient guidance throughout the two years of my studies. I am indebted to him for considering me to be a part of his research group and for providing this opportunity to work in the fields of systems engineering and mechanical design for a period of 2 years. Being a research and teaching assistant under him had been a rewarding experience. Without his valuable insights, this work would not only have been possible, but also inconceivable. I would like to thank my co-advisor Prof. Ilias Bilionis for his valuable inputs, timely guidance and extremely engaging research meetings. I thank my committee member, Prof. William Crossley for his interest in my work. I had a great opportunity to attend all three courses taught by my committee members and they are the best among all the courses I had at Purdue. I would like to thank my mentors Dr. Jagannath Raju of Systemantics India Pri- vate Limited and Prof. -
Study of a Nozzle Vector Control for a Low Cost Mini-Launcher
Study of a nozzle vector control for a low cost mini-launcher Roberto Rodr´ıguez SUPERVISED BY Joshua Tristancho Universitat Politecnica` de Catalunya Master in Aerospace Science & Technology July 2011 Study of a nozzle vector control for a low cost mini-launcher BY Roberto Rodr´ıguez DIPLOMA THESIS FOR DEGREE Master in Aerospace Science and Technology AT Universitat Politecnica` de Catalunya SUPERVISED BY: Joshua Tristancho Applied Physics department ABSTRACT This study is addressed to the control system of a mini-launcher. A reaction control based on purge pressure from a solid propellant engine of a main stage, or using cold gas from a storage tank will be the control method. Pulse modulator system will be the actuation method studied, and simulations about its suitability will be done with Simulink. In this thesis, we try to check if this method is able to be implemented in a low cost way the Wiki-Launcher, a mini-launcher less than 100 kg. At the time we try to check if the control allowed by the reaction control can manage all the phases of the flight. Both possible con- trol configurations are going to be analyzed. Keywords: Nozzle Vector Control, Low cost mini-launcher, Solid propellant Acknowledgements I’m grateful to my parents and my friends for supporting me during this work. I want thank in a special way to Joshua Tristancho for his continuous help and support during this research work and for give me the opportunity to participate within his team in this project. I’m very grateful to all the WikiSat members who helped and supporting me with the re- alization of the thesis, specially Joshua Tristancho, Victor Kravchenco, Esteve Bardolet, Sonia Perez,´ Lara Navarro and Raquel Gonzalez.´ I want to thank the EETAC school for the facilities and tools they have provided to support this work. -
Development of a Fast-Response Variable-Amplitude Programmable Reaction Control System
NISTIR 5118 Development of a Fast-Response Variable-Amplitude Programmable Reaction Control System Building and Fire Research Laboratory Gaithersburg, Maryland 20899 NIST United States Department of Commerce Technology Administration QC National Institute of Standards and Technology 100 .056 //5118 1993 /' 'i \ NISTIR 5118 r. Development of a Fast-Response Variable-Amplitude Programmable Reaction Control System William C. Stone January 1993 Building and Fire Research Laboratory National Institute of Standards and Technology Gaithersburg, MD 20899 U.S. Department of Commerce Ronald H. Brown, Secretary National Institute of Standards and Technology John W. Lyons, Director Abstract This report describes a high speed loading system comprised of: a piezoelectric stack and an associated microprocessor-based programmable DC power source; a low-loss mechanical displacement amplifier; a high pressure spring-loaded axial valve; an integral high pressure valve seat; an expansion nozzle; and a high pressure gas supply. A half square wave voltage signal of varying duration and amplitude was used to drive the piezoelectric stack in such a manner as to produce changing displacements which were subsequently amplified by a monolithically milled hinged anvil. The anvil is connected to a valve core which seats upon, and is normally forced closed upon a specially hardened throat of an expansion nozzle by means of a compression spring. The interior side of the thruster nozzle communicates with a high pressure gas supply. The flow of gas through the nozzle is normally prohibited by the spring loaded valve core. As the piezoelectric stack expands under computer control the valve core is lifted off the nozzle throat permitting gas to expand through the nozzle and create thrust that is directly proportional to the control signal from the microprocessor. -
C. Scott Hill (575) 527-4898 (Home) (575) 635-6834 (Cell)
Experience Summary Charles Scott Hill C. Scott Hill (575) 527-4898 (home) (575) 635-6834 (cell) Experience Summary: I have many years of direct experience in hypergolic reaction control rocket Development, Qualification, Production, Failure Investigation, Field repair and Application. Was primary contributor for Apollo Service Module Rocket, Manned Orbiting Laboratory RCS, Shuttle Primary and Vernier Thrusters for RCS. Present: Instructor Mechanical Engineering University of Texas at El Paso Teach courses in Spacecraft Design and Spacecraft Propulsion Jan 2010 to present Position Causal Employee - ARES Corporation, Huntsville, Alabama Time in Position April 2006 - December 2009 Provide mentoring and review of specifications, processes and approaches to Reaction Control Integrated Project Team for the Area I vehicle on the NASA Constellation Program at MSFC. Reported directly to NASA IPT Manager. IPT is developing system for monopropellant thrusters for active roll control and attitude control of the 2nd stage. Made monthly trips and direct support using the Internet. Participate in design reviews. Retired from full time employment - November 1, 2005 Position: Staff Advisor to Program Manager – White Sands Test Facility Time in Position: 3 Years Description and Scope of Current Job: Developed and taught instruction courses for WSTF test personnel in rocket development, Shuttle thruster development and qualification testing, application of rockets to space vehicle. Assisted in failure investigation and provided technical project management consulting. Position: Propulsion Department Manager – White Sands Test Facility Time in Position: 7 Years Number of Personnel DirectlySupervised: 6 direct reports with 115-125 people in Department Description and Scope of Job: Responsible for managing Propulsion Department including overall technical performance, budget control and reporting at the department level; the primary direct customer interface with the Propulsion Office Chief to ensure customer satisfaction and department level strategic planning. -
The Design and Analysis of a Kerosene Turbopump for a South African Commercial Launch Vehicle
The Design and Analysis of a Kerosene Turbopump for a South African Commercial Launch Vehicle. by Jonathan Smyth In fulfilment of the academic requirements for the degree of Master of Science in Mechanical Engineering, College of Agriculture, Engineering and Science, University of KwaZulu-Natal. Supervisor: Mr. Michael Brooks Co-supervisors: Dr. Graham Smith Prof. Jeff Bindon Dr. Glen Snedden (CSIR) DECLARATION 1 - PLAGIARISM I, Jonathan Smyth, declare that 1. The research reported in this thesis, except where otherwise indicated, is my original research. 2. This thesis has not been submitted for any degree or examination at any other university. 3. This thesis does not contain other persons’ data, pictures, graphs or other information, unless specifically acknowledged as being sourced from other persons. 4. This thesis does not contain other persons' writing, unless specifically acknowledged as being sourced from other researchers. Where other written sources have been quoted, then: a. Their words have been re-written but the general information attributed to them has been referenced b. Where their exact words have been used, then their writing has been placed in italics and inside quotation marks, and referenced. 5. This thesis does not contain text, graphics or tables copied and pasted from the Internet, unless specifically acknowledged, and the source being detailed in the thesis and in the References sections. Signed: ……………………………………………………………………………… Mr. Jonathan Smyth As the candidate's supervisor I have approved this dissertation for submission. Signed: ……………………………………………………………………………… Mr. Michael Brooks i DECLARATION 2 - PUBLICATIONS 1. Smyth J.*, Bindon J., Brooks M., Smith G. and Snedden G., "The Design of a Kerosene Turbopump for a South African Commercial Launch Vehicle", 48th AIAA/ASME/SAE/ASEE Joint Propulsion Conference & Exhibit July, Atlanta, Georgia, 2012. -
Space Shuttle- Mission Report
SPACE SHUTTLE- MISSION REPORT (NASA-C9-195740) STS-56 SPACE SHUTTLE t4TSSIDN REPORT (Lockheed Engineering dnd Sciences Co. 52 p Unc 1 as JULY 1993 --- i IT.IIG!H RESEARCH CEIITER LlB!?ll!?Y I!AM IlhT.;?TO:!, VIRGll!lA NASA National Aeronautics and Space Administration Lyndon B. Johnson Space Center Houston, Texas STS-56 SPACE SHUTTLE MISSION REPORT LESC/Flight valuation and Engineering Office Approved by STS-56 Lead Mission Evaluation Room Manager n Manager, Flight ~ngineeringOff ice Manager, 0rbi terwk~Projects / (1 Brewster H: Shaw ~irect';;r, Space Shuttle Operations Prepared by Lockheed Engineering and Sciences Company for Flight Engineering Office NATIONAL AERONAUTICS AND SPACE ADMINISTRATION LYNDON B. JOHNSON SPACE CENTER HOUSTON, TEXAS 77058 July 1993 STS-56 Table of Contents Title Page INTRODUCTION ....................... 1 MISSION SUMMARY ..................... 2 PAYLOADS ......................... ATLAS-2 ........................ Atmos~hericScience ................ Solar Science ............... Shuttle Pointed Autonomous Research Tool for Astronomy-201 ............ Solar Ultraviolet Ex~eriment ........ Hand-~eld. ~arth-0rik fed. Real.Time. Coopera User.Friendly. Location-Targeting and Environmental System Radiation Monitoring Equipment-I11 ........ Cosmic.... Radiation Effects and Activation............ Monitor ... Air..... Force Maui O~tical~ Site ~ ~- .............. Shuttle Amateur Radio Equipment-I1 ........ Commercial Materials Dispersion Apparatus ITA Experiments ................ S~aceTissue Loss Ex~eriment ........... ~h~siolo~icaland -
Spacecraft Propulsion.Pdf
SPACECRAFT PROPULSION Spacecraft propulsion .................................................................................................................................... 1 Rocket technologies .................................................................................................................................. 4 Cold gas rockets .................................................................................................................................... 7 Solid propellant rockets ........................................................................................................................ 7 Liquid propellant rockets .................................................................................................................... 11 Electrothermal rockets ........................................................................................................................ 16 Electrodynamic rockets ....................................................................................................................... 16 Rocket propulsion modelling .................................................................................................................. 19 Tsiolkovsky rocket equation ............................................................................................................... 19 Delta-v budget ..................................................................................................................................... 20 Rocket exit speed ............................................................................................................................... -
Next Generation Spacecraft, Crew Exploration Vehicle
Next Generation Spacecraft, Crew Exploration Vehicle A Special Bibliography From the NASA Scientific and Technical Information Program Includes research on reusable launch vehicles, aerospace planes, shuttle replacement, crew/cargo transfer vehicle, related X-craft, orbital space plane, and next generation launch technology. January 2004 Next Generation Spacecraft, Crew Exploration Vehicle A Special Bibliography from the NASA Scientific and Technical Information Program JANUARY 2004 20040004384 Nebraska Univ., Lincoln, NE, USA Design of Experiments for the Thermal Characterization of Metallic Foam Crittenden, Paul E.; Cole, Kevin D.; Optimal Experiment Design for Thermal Characterization of Functionally Graded Materials; August 18, 2003; In English Contract(s)/Grant(s): NAG1-01087; No Copyright; Avail: CASI; A03, Hardcopy Metallic foams are being investigated for possible use in the thermal protection systems of reusable launch vehicles. As a result, the performance of these materials needs to be characterized over a wide range of temperatures and pressures. In this paper a radiation/conduction model is presented for heat transfer in metallic foams. Candidates for the optimal transient experiment to determine the intrinsic properties of the model are found by two methods. First, an optimality criterion is used to find an experiment to find all of the parameters using one heating event. Second, a pair of heating events is used to determine the parameters in which one heating event is optimal for finding the parameters related to conduction, while the other heating event is optimal for finding the parameters associated with radiation. Simulated data containing random noise was analyzed to determine the parameters using both methods. In all cases the parameter estimates could be improved by analyzing a larger data record than suggested by the optimality criterion. -
Columbia Accident Investigation Board (Caib)/ National Aeronautics and Space Administration (Nasa) Accident Investigation Team (Nait)
COLUMBIA ACCIDENT INVESTIGATION BOARD (CAIB)/ NATIONAL AERONAUTICS AND SPACE ADMINISTRATION (NASA) ACCIDENT INVESTIGATION TEAM (NAIT) WORKING SCENARIO FINAL VERSION: JULY 8, 2003 PREFACE This Working Scenario report was written to document the collection of known facts, events, timelines, and historical information of particular interest to the final flight of Columbia. The report was written with the understanding that it could be published, either in part or in its entirety, as part of the official Columbia Accident Investigation Board (CAIB) report. The report includes information and results from numerous analyses, tests, and simulations related to the Columbia investigation that have been completed, or were ongoing at the time that this report was completed. It is anticipated that additional analytical and test results will emerge from ongoing work, as well as from future activities associated with the Columbia investigation and efforts related to the Return-To-Flight work. This Working Scenario includes information and results as they existed up to and including July 8, 2003. CONTENTS Section Page 1.0 INTRODUCTION ........................................................................................ 1-1 1.1 SCOPE....................................................................................... 1-1 1.2 MISSION BACKGROUND.......................................................... 1-2 2.0 LAUNCH COUNTDOWN............................................................................ 2-1 3.0 LAUNCH.................................................................................................... -
E-10948 Spine & Cover Layout
About the cover: Left: Mars Pathfinder Sojourner rover showing Lewis’ Wheel Abrasion Experiment (p. 31) on a special section of the center wheel. This experiment measured abrasion to analyze the consistency of the Martian soil. Two other Lewis experiments were conducted on the Sojourner rover: electrostatic charging experi- ments (p. 32), which measured the accumulation of static charge, and the Materials Adherence Experi- ment, which measured dust accumulation (p. 34) to assess its potential interference on solar panels. In addition, Lewis helped test the air-bag landing system for the Mars Pathfinder, modeled solar energy on Mars to determine solar panel requirements, and provided tungsten points for removing potentially damaging electrostatic charge from the rover. Visit Lewis on the World Wide Web to find out more about our involvement in the Mars Pathfinder mission (http://www.lerc.nasa.gov/WWW/PAO/html/ marspath.htm). Top right: Joint Strike Fighter model installed in Lewis’ 8- by 6-Foot Supersonic Wind Tunnel (p. 87). Bottom right: Astronaut crew training performed onboard Lewis’ DC–9 aircraft (p. 134) in preparation for the Microgravity Science Laboratory missions flown on the Space Shuttle Columbia in April and July of 1997. Research & Technology 1997 National Aeronautics and Space Administration Lewis Research Center Cleveland, Ohio 44135 NASA/TM—1998-206312 Trade names or manufacturers' names are used in this report for identification only. This usage does not constitute an official endorsement, either expressed or implied, by the National Aeronautics and Space Administration. Available from NASA Center for Aerospace Information National Technical Information Service Parkway Center 5287 Port Royal Road 7121 Standard Drive Springfield, VA 22100 Hanover, MD 21076-1320 Price Code: A08 Introduction NASA Lewis Research Center is responsible for developing and transferring critical technologies that address national priorities in aeropropulsion and space applications in part- nership with U.S.