Analysis of Hold Times for Gaseous Fire Suppression
Total Page:16
File Type:pdf, Size:1020Kb
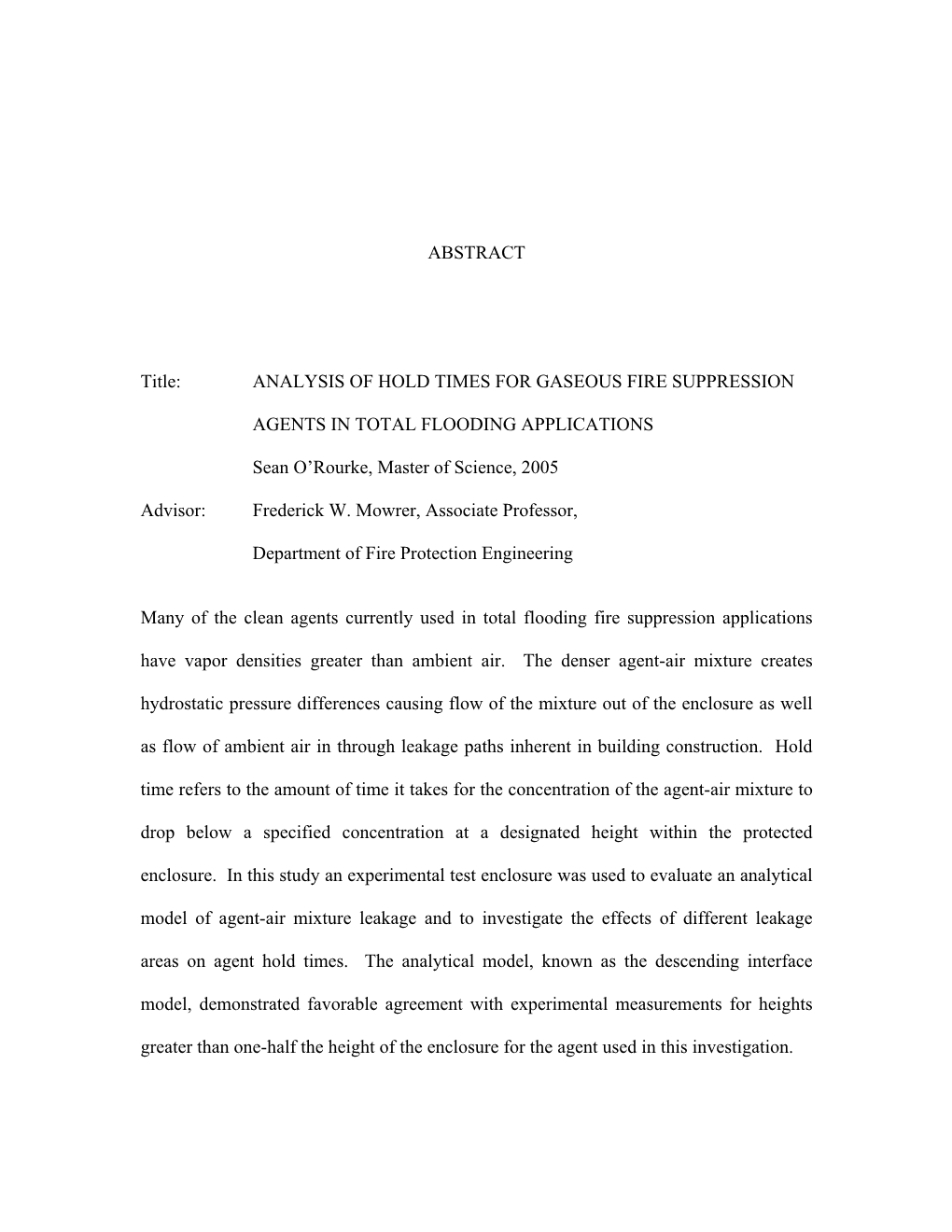
Load more
Recommended publications
-
Smoke Alarms in US Home Fires Marty Ahrens February 2021
Smoke Alarms in US Home Fires Marty Ahrens February 2021 Copyright © 2021 National Fire Protection Association® (NFPA®) Key Findings Smoke alarms were present in three-quarters (74 percent) of the injuries from fires in homes with smoke alarms occurred in properties reported homei fires in 2014–2018. Almost three out of five home with battery-powered alarms. When present, hardwired smoke alarms fire deathsii were caused by fires in properties with no smoke alarms operated in 94 percent of the fires considered large enough to trigger a (41 percent) or smoke alarms that failed to operate (16 percent). smoke alarm. Battery-powered alarms operated 82 percent of the time. Missing or non-functional power sources, including missing or The death rate per 1,000 home structure fires is 55 percent lower in disconnected batteries, dead batteries, and disconnected hardwired homes with working smoke alarms than in homes with no alarms or alarms or other AC power issues, were the most common factors alarms that fail to operate. when smoke alarms failed to operate. Of the fire fatalities that occurred in homes with working smoke Compared to reported home fires with no smoke alarms or automatic alarms, 22 percent of those killed were alerted by the device but extinguishing systems (AES) present, the death rate per 1,000 reported failed to respond, while 11 percent were not alerted by the operating fires was as follows: alarm. • 35 percent lower when battery-powered smoke alarms were People who were fatally injured in home fires with working smoke present, but AES was not, alarms were more likely to have been in the area of origin and • 51 percent lower when smoke alarms with any power source involved in the ignition, to have a disability, to be at least 65 years were present but AES was not, old, to have acted irrationally, or to have tried to fight the fire themselves. -
Early Career Award in Fire Science
Early Career Award in Fire Science 2016 Recipient Dr. Guillermo Rein, Senior Lecturer, Imperial College London, UK Dr. Rein is a prominent fire behavior scientist, studying ignition, combustion emission, smoldering and interactions of fires and ecosystems. At this early stage of his career, his greatest contributions have been in the area of smoldering wildfires, where he has revolutionized the experimental and numerical description of these fires, translating science from engineering to applications such as fire history, emissions and climate change. This work has been published in over 67 journal papers, receiving more than 1700 citations throughout his short career. Among these, 17 journal papers and 6 keynote lectures have focused specifically on wildland fires. Dr. Rein was first introduced to the subject of wildland fires by Professor Scott Stephens in his course Fire Ecology at University of California, Berkeley. Immediately following his PhD on computational smoldering combustion (graduated in Dec. 2005), he began his early research career on wildland fires as a member of the large international consortium, Fire Paradox (EU FP7) in 2006. Since then, he became a leader in the emerging field of smoldering wildfires, relating their effects to carbon emissions, fire ecology, and climate change. The impact of his work in both the combustion and geoscience communities has been equally impressive and measurable. The results of his wildfire work have been published in 2 book chapters, the International Journal of Wildland Fire, the Proceedings of the National Academy of Sciences (PNAS), Nature Geoscience and awarded twice the Distinguished Paper Awards (2009 and 2013) in the Proceedings of the Combustion Institute. -
Recent Development in Fire Suppression Systems
Proceedings, 5th AOSFST, Newcastle, Australia, 2001 Editors: M.A. Delichatsios, B.Z. Dlugogorski and E.M. Kennedy RECENT DEVELOPMENT IN FIRE SUPPRESSION SYSTEMS A. Kim Institute for Research in Construction National Research Council Canada CANADA ABSTRACT With halon phase-out, there has been a major thrust to find new advanced fire suppression systems in recent years. Some of the newly developed fire suppression systems include halocarbon and inert gaseous agents, water mist systems, compressed-air-foam systems, and aerosol and gas generators. This paper gives a brief description of the newly developed fire suppression systems, and provides technical information on the fire suppression performance of each system as well as the limitations or concerns related to using the new suppression systems. INTRODUCTION The traditional means of providing fire suppression in buildings is a sprinkler system. However, water is not a suitable suppression medium for all types of fires. Water, when sprayed in coarse droplets such as in sprinkler spray, is not effective in suppressing liquid fuel fires. Also, in some cases, water damage is a concern because of the large amount of water used for sprinkler systems. In the 1940’s, an effort was made to develop more effective fire suppression agents. The first systematic search for effective gaseous fire suppressants can be traced to the late 1940s when the Purdue Research Foundation conducted an extensive study of more than 60 chemical compounds for the U.S. army1. This study led to the development of halon chemicals as a superior performing suppression agent. Halon is a chemical agent, which combines hydrogen, carbon, chlorine and bromine atoms. -
AREVA Design Control Document Rev. 1
U.S. EPR FINAL SAFETY ANALYSIS REPORT 9.5 Other Auxiliary Systems 9.5.1 Fire Protection System The purpose of the fire protection system (FPS) is to protect other plant systems and equipment which provide the capability to safely shut down the reactor, maintain it in a safe shutdown condition, control radioactive releases to the environment, and to prevent personnel injury and property damage in the event of a fire. The FPS consists of design features, personnel, equipment, and procedures to provide defense-in-depth protection of public health and safety. The program is implemented during station operations by the prevention, detection, annunciation, confinement, and extinguishment of fire. Administrative controls, training, inspection, testing, and quality assurance (QA) provide reasonable assurance of the operability of the program. The FPS, including administrative controls and the fire brigade, are implemented prior to receiving fuel on site for fuel storage areas and for the entire station prior to reactor startup. 9.5.1.1 Design Basis The FPS is designed in accordance with: ● 10 CFR 50.48 - Fire Protection. ● 10 CFR Part 50, Appendix A, GDC 3 - Fire Protection. ● 10 CFR Part 50, Appendix A, GDC 5 - Sharing of Structures, Systems, and Components. ● 10 CFR Part 50, Appendix A, GDC 19 - Control Room. ● 10 CFR Part 50, Appendix A, GDC 23 - Protection System Failure Modes. ● 10 CFR Part 50, Appendix A, GDC 56 - Primary Containment Isolation. ● NUREG-0800, Standard Review Plan 9.5.1 - Fire Protection Program (Reference 37). ● RG 1.29 - Seismic Design Classification, Revision 4. ● RG 1.189 - Fire Protection for Nuclear Power Plants, Revision 1. -
E-CATALOGUE Download
2 3 OUR COMMITMENT "To provide our customers with the best possible service, the highest quality products and the right solution for their needs" Fire Protection Technologiesis the largest Our aim is to provide design driven independent supplier of product, design solutions and to educate our customers and engineering services in Australia, New on their options including advantages and Zealand and Asia Pacific. In conjunction with disadvantages enabling our customer to our ‘whole of life’ approach to our product make an informed decision on what product range, technical support, design and best serves and meets their needs. engineering solutions available throughout all stages of a project from development Technical support, design and engineering to delivery, we will continue to provide assistance will be available for the life of the ongoing support for the life of the product. product; our staff and product managers regularly attend product training with all our Wholly Australian owned and operated we manufacturers enabling us to maintain the have a team dedicated to customer support, highest level of up to date local support and complete with 350+ years combined technical assistance. practical experience in delivery and engineering of special hazards projects. With offices and warehouses in Melbourne (Head Office), Sydney, Brisbane, Perth, Being the sole distributor in this region for Auckland and Singapore, including regional some of the world’s largest and technically managers for South Australia, Tasmania, advanced product manufacturers, together Northern Territory and Malaysia. We with our technical capabilities enables us continue to grow throughout the Asia Pacific to provide the highest quality products region. -
Development of Fire Science and Fire Protection Engineering in China
View metadata, citation and similar papers at core.ac.uk brought to you by CORE provided by Elsevier - Publisher Connector Available online at www.sciencedirect.com P r o c e d i a E n g i n e e r i n g 5 2 ( 2 0 1 3 ) 1 – 2 Development of Fire Science and Fire Protection Engineering in China YAO Hao-weia,b,* aSchool of Engineering, Sun Yat-sen University, Guangzhou 510006, China bGuangdong Provincial Key Laboratory of Fire Science and Technology, Guangzhou 510006, China Abstract This article gives an introduction on the development of fire science and fire protection engineering in China, and a brief on the conference. © 20132012 The Authors.Authors. PublishedPublished by by Elsevier Elsevier Ltd. Ltd. Open access under CC BY-NC-ND license. Selection and peer-review under responsibility of School of Engineering of Sun Yat-sen University Keywords: fire science; fire protection engineering; development; China Let’s review the mega-events of China fire science and fire protection engineering: In 1956, Fire Department of Ministry of Public Security (FDMPS) was established. In 1959, Fire Science Research Laboratory of FDMPS was established. In 1963, Fire Science Research Institute of FDMPS was established. In 1965, the four Fire Science Research Institutes of Ministry of Public Security were established, namely, Sichuan, Tianjin, Shanghai, and Shenyang. In 1980, China Fire Press was established. The journal “China Fire” started publication in 1980. “Fire Science and Technology” started publication in 1982. And “Fire Technology and Product Information” started publication in 1988. In 1984, China Fire Protection Association was founded. -
M E M O R a N D U M
M E M O R A N D U M TO: Technical Committee on Gaseous Fire Extinguishing Systems FROM: Barry Chase, Staff Liaison DATE: March 20, 2019 SUBJECT: NFPA 12/12A/2001 First Draft Meeting Agenda (F2020) April 24-26, 2019, Memphis, TN 1. Call to Order – April 24, 2019, 8:00am ET 2. Chair’s comments 3. Previous minutes [April 25, 2017, Linthicum Heights, MD] 4. NFPA Staff Liaison Presentation a. NFPA Standards Development Process b. NFPA Resources 5. NFPA 2001 First Draft a. Public input [see attached] b. Report of the Task Group on Total Flooding Design Concentration Requirements (5.4.2) [P. Rivers] c. Presentation on Halocarbon Blend 55 (related to PI 49, 50, 51, 52, 53, 54, 55, 56, 57, 58, 58, 60) [Robert Richard – Honeywell] d. April 25, 8:00AM - Presentation on Toxicity of Halocarbon Impurities (related to PI 74) [Kurt Werner, Government and Regulatory Affairs Manager, 3M Electronics Materials Solutions Division] e. April 25, 9:00AM - Presentation on Toxicity of Halocarbon Impurities [Steve Hodges, Alion Science and Technology] f. Committee revisions g. Staff notes and editorial issues 6. NFPA 12 First Draft a. Public input [see attached] b. Report of the Task Group on Low Pressure Containers (4.6.6.1.1) [K. Adrian] c. Committee revisions d. Staff notes and editorial issues 7. NFPA 12A First Draft a. Public input [see attached] b. Committee revisions c. Staff notes and editorial issues 8. Other business 9. Next meeting location and dates 1 of 371 All NFPA Technical Committee meetings are open to the public. -
Use of Gaseous Suppression Systems in High Air Flow Environments – Phase 1 FINAL REPORT
Use of Gaseous Suppression Systems in High Air Flow Environments – Phase 1 FINAL REPORT PREPARED BY: Eric Forssell Jensen Hughes Baltimore, MD, USA © September 2015 Fire Protection Research Foundation FIRE PROTECTION RESEARCH FOUNDATION ONE BATTERMARCH PARK | QUINCY, MASSACHUSETTS, USA 02169-7471 E-MAIL: [email protected] | WEB: WWW.NFPA.ORG/FOUNDATION — — Page ii — — FOREWORD Information-technology and telecommunications (IT/telecom) facilities provide critical services in today’s world. From a risk standpoint, the indirect impact of fire loss due to business interruption and loss of critical operations, sometimes geographically very distant from the IT/telecom facility itself, can far outweigh the direct property loss. In the past few years, there have been dramatic changes in the equipment housed in these facilities, which have placed increased demands on HVAC systems. As a result, engineered-airflow containment solutions are being introduced to enhance heat extraction and increase energy efficiency. From the perspective of fire-suppression system design, the use of airflow containment systems creates areas of high-air velocities within an increasingly obstructed equipment space, which could affect the effectiveness of transport of suppression agents throughout the protected volume. Requirements related to use of gaseous-agent fire extinguishing systems in IT/telecom facilities are directly addressed by NFPA 75, Standard for the Fire Protection of Information Technology Equipment, and NFPA 76, Standard for the Fire Protection of Telecommunications Facilities. NFPA 75, 2013 edition, addresses these issues related to gaseous agent systems in several places. 5.6.7 Where aisle containment systems are installed, the existing suppression and detection systems shall be evaluated, modified, and tested as necessary to maintain compliance with the applicable codes and standards. -
Home Smoke Alarms a Technology Roadmap
Home Smoke Alarms A Technology Roadmap R. J. (Bruce) Warmack Measurement Science & Systems Engineering Division Marc Wise Chemical Sciences Division Dennis Wolf Computer Science and Mathematics Division Oak Ridge National Laboratory Oak Ridge, TN 37831 March 2012 This work is sponsored by the U.S. Fire Administration (USFA) and the U.S. Consumer Product Safety Commission (CPSC) and prepared under DOE Contract # DE-AC05-00OR22725 between Department of Energy Oak Ridge Office and UT-Battelle, LLC. Home Smoke Alarms EXECUTIVE SUMMARY The introduction of residential smoke alarms and their widespread adoption over the past four decades has been tremendously successful in saving countless lives and assuring home occupants of their safety in residential fires. Smoke alarms have been developed to be reliable in general, and economical to employ, requiring occasional maintenance of testing and battery replacement. Nevertheless, there remain some shortfalls in operation. Nuisance or false alarms, which are triggered by nonfire related sources, account for the majority of smoke alarm activations. These constitute a serious concern, as occupants sometimes disable the offending alarms, rendering them useless for alarming in genuine fires. Construction methods and room furnishing materials have changed, dramatically increasing the fire growth rate and reducing the time for safe egress. Arousing occupants in a timely manner can be challenging. Given these concerns, improvements in residential smoke alarms could have a huge impact upon residential fire safety, reducing the number of injuries and deaths. Most residential smoke alarms are based solely upon the detection of smoke aerosol particles emitting from nearly all fires. Ionization and photoelectric aerosol sensors provide sensitivity to various types of smoke aerosols but also, unfortunately, to other aerosols, including cooking fumes, dust and fog. -
Reporting to the Asia Pacific Fire Protection and Fire Service Industry
REPORTING TO THE ASIA PACIFIC FIRE PROTECTION AND FIRE SERVICE INDUSTRY www.apfmag.com Issue 59 • October 2016 NFPA #1964 Compliant Wildland Fire Industrial Fire Water Supply Handheld Nozzles ® TASK FORCE TIPS® FIRE FIGHTING EQUIPMENT Fire Apparatus Equipment Foam Equipment 3701 INNOVATION WAY MADE IN USA VALPARAISO, IN U.S.A. +1.219.548.4000 www.tft.com www.newforce.tft.com REPORTING TO THE ASIA PACIFIC FIRE PROTECTION AND FIRE SERVICE INDUSTRY Contents OCTOBER 2016 REGULARS. 5 Editors Comment 7 Industry Comment www.apfmag.com Issue 59 • October 2016 8 News and Profiles OCTOBER 2016 • ISSUE 59 Cover image: Dual pressure automatic nozzles, such FEATURES. as the MidForce nozzle shown here, provide maximum stream reach and penetration in high pressure mode, and maximum flow when the low pressure mode is 24 Emergency response in Antarctica selected. Image courtesy of S. Haase. Publishers 31 Firefighting foam concentrates Mark Seton [email protected] 24 – the constant evolution: Part 2 David Staddon [email protected] Editor 36 Improving survival for ‘out Neil Bibby ASFM, FAICD, MIFireE [email protected] of hospital’ cardiac arrest Contributing Editors Rhonda Abotomey, Martin Boyle, Penny Burns, 41 Gaseous fire suppression systems Javier Castro, Chris Chiesa, Ed Comeau, Robert Fawcett, David J. Ganz, Jeff Kepert, Thomas Loridan, – understanding safety measures Torbjorn Lundmark, Michelle Murphy, Steve O’Malley, Gary Parkinson, Ange Pestell, Peter Ryan, Brett Shields, Brett Staines, Deb Symons, Melanie Taylor, William Thurston, Kevin Tory, 48 Women and Firefighting Australasia Bronwyn Walker, Joel Ward, Duncan J. White. 2016: Right place. Right time Design Manager Richard Parsons [email protected] 55 Protective clothing and Web and IT Manager equipment for Fire Fighters Neil Spinney [email protected] 59 A hands on approach International Sales 36 Mark Seton TECHNOLOGY IS SECURITY. -
Company Profile Alpha Safety & Security Holding B.S.C
COMPANY PROFILE www.afs-bahrain.com ALPHA SAFETY & SECURITY HOLDING B.S.C. (C) | Company Profile ABOUT THE COMPANY • Alpha Safety and Security Holding (the Group) now constitutes a full service independent specialist Fire and Security services solution providers committed to meeting the needs of its customers for protection from fire and to keep them safe • Established in November 2011 and incorporating Alpha Fire Services which was first set up in 1989 and incorporated as a limited liability company in 1992. Now includes Advanced Safety Systems Co WLL (ASSCO), Alpha Risk Management Consultants WLL (ARM), Alpha Fire Services W.L.L (Qatar) • The Group provides a range of products and services (that include the supply, design, engineering, installation and maintenance) of: - Passive and Active fire protection, including fire extinguishing, fire stopping and fire suppression systems - Smoke/ heat extraction and Natural Ventilation systems - Fire alarm systems including, detection and control devises - Access control, CCTV, and other security systems - Risk management, risk assessment and training Fire Suppression System Fire Extinguisher Smoke Detector Smoke Extraction Fire Alarm Control System CCTV www.afs-bahrain.com ALPHA SAFETY & SECURITY HOLDING B.S.C. (C) | Company Profile COMPANY OVERVIEW Our Vission To be amongst the top 5 leading providers of fire protection and security systems in GCC countries by the end of 2015, with establish operations delivering quality products and services that are suitable for the region, effective and environmentally sustainable Our Mission Alpha Group’s mission is to be a leading fire and security risk management organisation through the provision of fire detection , protection and extinguishment systems and in the deployment of access control/security systems in the Middle East. -
Socioeconomic Factors and the Incidence of Fire
FA 170 / June 1997 SOCIOECONOMIC FACTORS AND THE INCIDENCE OF FIRE Federal Emergency Management Agency United States Fire Administration National Fire Data Center SOCIOECONOMIC FACTORS AND THE INCIDENCE OF FIRE June, 1997 Federal Emergency Management Agency United States Fire Administration National Fire Data Center FA 170 / June 1997 This publication was produced under contract EMW-95-C-4717 by TriData Corporation for the United States Fire Administration, Federal Emergency Management Agency. Any information, findings, conclusions, or recommendations expressed in this publication do not necessarily reflect the views of the Federal Emergency Management Agency or the United States Fire administration. TABLE OF CONTENTS INTRODUCTION............................................................................................... 1 Why Study Socioeconomic Factors of Fire Risk?................................................. 1 Existing Literature................................................................................................. 2 Part I. Socioeconomic Indicators of Increased Fires Rates ................... 2 Part II. How Income Level Affects Fire Risk in Urban Areas ................ 10 Socioeconomic Factors at the Level of the Neighborhood ................................... 10 Vacant and Abandoned Buildings................................................................ 11 Neighborhood Decline.................................................................................. 11 Arson ..........................................................................................................