Failure Modes and Effects Analysis for Hydrogen Fuel Cell Vehicles – Subtask 1
Total Page:16
File Type:pdf, Size:1020Kb
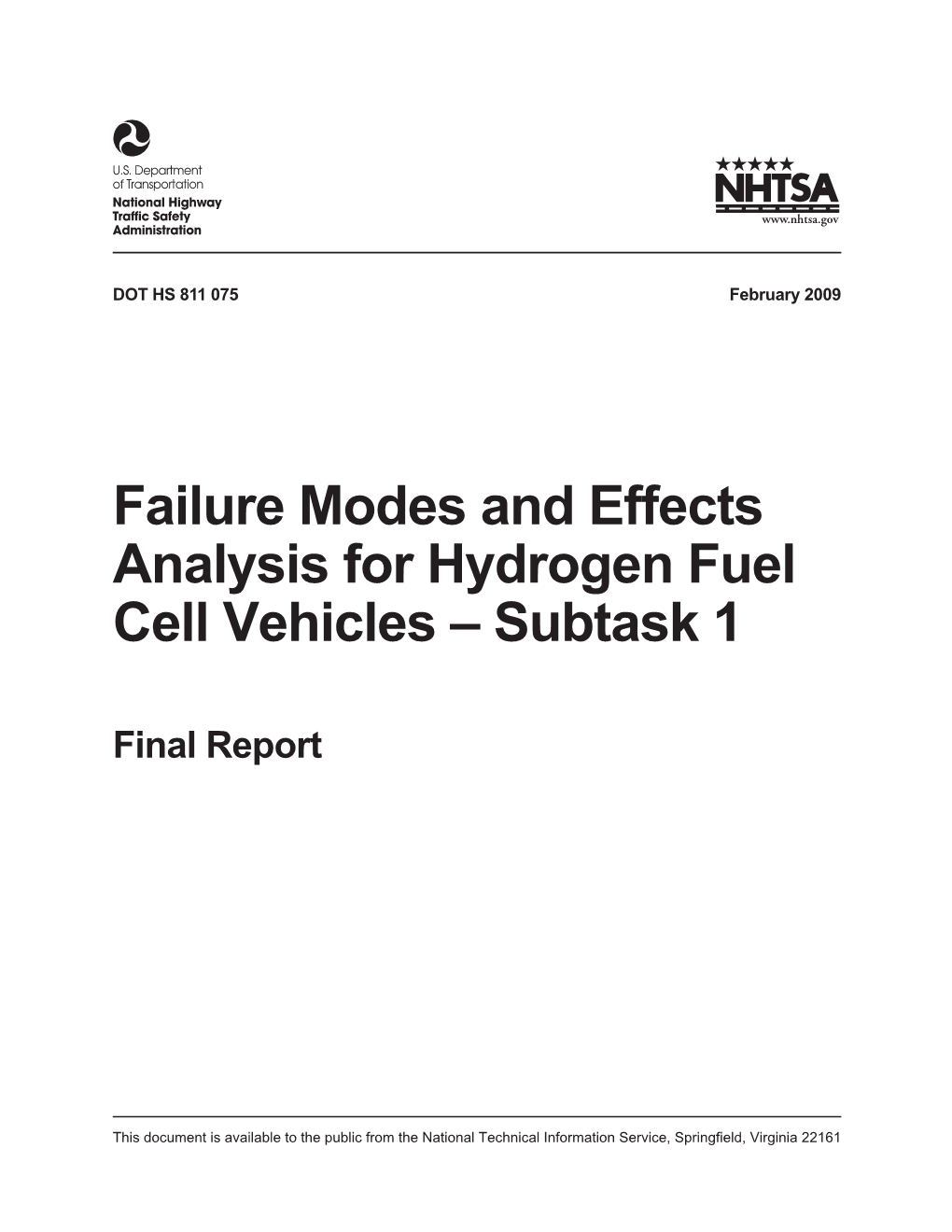
Load more
Recommended publications
-
Fracture Control Plan for Jsc Space-Flight Hardware
JSC 25863C FRACTURE CONTROL PLAN FOR JSC SPACE-FLIGHT HARDWARE JSC Fracture Control Board Public Release Statement: This document has been reviewed for Proprietary, SBU, and Export Control (ITAR/EAR) and has been determined to be nonsensitive. It has been released to the public via the NASA Scientific and Technical Information (STI) Process DAA NF 1676 TN56113. March 2018 National Aeronautics and Space Administration Lyndon B. Johnson Space Center Houston, Texas 77058 Verify correct revision before use at https://qmsmasterlist.jsc.nasa.gov/Home.aspx/Organization/31 -6&)5$&785(&21752/3/$1 )25-6&63$&()/,*+7+$5':$5(5(9,6,21& 0DUFK 'LJLWDOO\VLJQHGE\0RKDPPDG6KRHE DIILOLDWH '1F 86R 86*RYHUQPHQWRX 1$6$RX 3HRSOH 3UHSDUHGE\ 0RKDPPDG6KRHE DIILOLDWH PVKRHEFQ 0RKDPPDG6KRHE DIILOLDWH 'DWH 0RH6KRHE 'DWH -(76)UDFWXUH&RQWURO 'LJLWDOO\VLJQHGE\$GULHQ0DUWLQH] DIILOLDWH 5HYLHZHGE\ '1F 86R 86*RYHUQPHQWRX 1$6$RX 3HRSOH $GULHQ0DUWLQH] DIILOLDWH DPDUWLQHFQ $GULHQ0DUWLQH] DIILOLDWH 'DWH 1LFN0DUWLQH] 'DWH -(76)UDFWXUH&RQWURO/HDG &RQFXUUHGE\ 'LJLWDOO\VLJQHGE\1$7+$1$(/*5((1( 1$7+$1$(/*5((1( 'DWH (61DWKDQDHO*UHHQH 'DWH 3UHVVXUH6\VWHPV)UDFWXUH7HFKQLFDO'LVFLSOLQH/HDG &RQFXUUHGE\ 'LJLWDOO\VLJQHGE\-$0(60&0$+21 -$0(60&0$+21 'DWH (6-DPHV0F0DKRQ 'DWH -6&)UDFWXUH&RQWURO%RDUG&KDLU $SSURYHGE\ Digitally signed by MARY SCHWARTZ MARY SCHWARTZ Date: 2018.04.26 08:14:22 -05'00' ($.HYLQ:LQGRZ 'DWH 'LUHFWRU(QJLQHHULQJ 6HHFRYHUIRUIXOOGLVFORVXUH9HULI\FRUUHFWUHYLVLRQEHIRUHXVHDW KWWSVTPVPDVWHUOLVWMVFQDVDJRY+RPHDVS[2UJDQL]DWLRQ 3DJHRI JSC 25863, FRACTURE CONTROL PLAN FOR JSC SPACE-FLIGHT HARDWARE, REVISION C March 30, 2018 DOCUMENT HISTORY LOG Document Date Originator Approval Description Revision Fracture Control Plan Basic May 1992 for JSC Flight Hardware Fracture Control Plan August A for JSC Flight 1998 Hardware Fracture Control Plan April B for JSC 2009 Space-flight Hardware Moe Shoeb Per EA-CCB- Changes reflect the CR/D-0239 Fracture Control March methodology of latest C 2018 release of NASA-STD 5019A and SSP 52005F. -
Deep Sea Dive Ebook Free Download
DEEP SEA DIVE PDF, EPUB, EBOOK Frank Lampard | 112 pages | 07 Apr 2016 | Hachette Children's Group | 9780349132136 | English | London, United Kingdom Deep Sea Dive PDF Book Zombie Worm. Marrus orthocanna. Deep diving can mean something else in the commercial diving field. They can be found all over the world. Depth at which breathing compressed air exposes the diver to an oxygen partial pressure of 1. Retrieved 31 May Diving medicine. Arthur J. Retrieved 13 March Although commercial and military divers often operate at those depths, or even deeper, they are surface supplied. Minimal visibility is still possible far deeper. The temperature is rising in the ocean and we still don't know what kind of an impact that will have on the many species that exist in the ocean. Guiel Jr. His dive was aborted due to equipment failure. Smithsonian Institution, Washington, DC. Depth limit for a group of 2 to 3 French Level 3 recreational divers, breathing air. Underwater diving to a depth beyond the norm accepted by the associated community. Limpet mine Speargun Hawaiian sling Polespear. Michele Geraci [42]. Diving safety. Retrieved 19 September All of these considerations result in the amount of breathing gas required for deep diving being much greater than for shallow open water diving. King Crab. Atrial septal defect Effects of drugs on fitness to dive Fitness to dive Psychological fitness to dive. The bottom part which has the pilot sphere inside. List of diving environments by type Altitude diving Benign water diving Confined water diving Deep diving Inland diving Inshore diving Muck diving Night diving Open-water diving Black-water diving Blue-water diving Penetration diving Cave diving Ice diving Wreck diving Recreational dive sites Underwater environment. -
Code of Practice 32
CODE OF PRACTICE 32 THE SAFE FILLING OF BEVERAGE GAS CYLINDERS REVISION 2: 2014 CODE OF PRACTICE 32 THE SAFE FILLING OF BEVERAGE GAS CYLINDERS Revision 2: 2014 Copyright © 2014 by British Compressed Gases Association. First printed as BCGA Guidance Note 4, 1997. All rights reserved. No part of this publication may be reproduced or transmitted in any form or by any means, electronic or mechanical, including photocopy, without permission from the publisher: BRITISH COMPRESSED GASES ASSOCIATION Registered office: 4a Mallard Way, Pride Park, Derby, UK. DE24 8GX Company Number: 71798, England Website: www.bcga.co.uk ISSN 0260 - 4809 BCGA CP 32 – Revision 2 PREFACE The British Compressed Gases Association (BCGA) was established in l971, formed out of the British Acetylene Association, which existed since l901. BCGA members include gas producers, suppliers of gas handling equipment and users operating in the compressed gas field. The main objectives of the Association are to further technology, to enhance safe practice, and to prioritise environmental protection in the supply and use of industrial gases, and we produce a host of publications to this end. BCGA also provides advice and makes representations on behalf of its Members to regulatory bodies, including the UK Government. Policy is determined by a Council elected from Member Companies, with detailed technical studies being undertaken by a Technical Committee and its specialist Sub-Committees appointed for this purpose. BCGA makes strenuous efforts to ensure the accuracy and current relevance of its publications, which are intended for use by technically competent persons. However this does not remove the need for technical and managerial judgement in practical situations. -
Psdiver Monthly Issue 67 2
Greetings, Recreational agencies teaching and promoting PSDiving are not what we want to see and represent many steps backward for Well, it is official – PADI has entered the PSD training field. those of us who have proclaimed our diving to be beyond They recently announced their program at DEMA. I was out of recreational. We as individuals and some of the ABCs involved the country at that time and was unable to attend DEMA but have proclaimed we are professional divers but considering all have since heard from a number of folks who did attend. that has gotten us, we are shouting into the wind. The concerns about PADI entering the field are many fold. But So for now, I think I am going to join the masses. I am going despite what you might think about it, they only did what every to sit back and watch for a while and see what happens. I have other agency that teaches Public Safety Diving has done. They a pretty good idea of what is coming and expect PADI to have recognized a need and a market and developed a program to an immediate impact on the field starting no later than Spring fill the need. There are some who criticize this but they forget 2010. I think we will probably see either some consolidated that ALL of the agencies make money and ALL of them are for efforts put forth for a PSD Consensus standard by the existing profit entities. PSD training agencies OR a total disregard for that and efforts to protect their own market shares that will likely result in an Without a national standard or an agency consensus standard, even bigger separation in cooperative effort. -
THE TEMPERATURE DEPENDENCE of SUSTAINED LOAD CRACKING in Ti-6211 C.L
2557 THE TEMPERATURE DEPENDENCE OF SUSTAINED LOAD CRACKING IN Ti-6211 C.L. Hoffmann, Combustion Engineering, Windsor, CT 06095 USA J.E. Cox, R.W. Judy, Jr., and B.B. Rath, Washington, DC 20375 USA In recent years, the design of structures and components has appropriately e1nphasized fail-safe principles. The basis for these principles includes the recognition that cracks and voids that either are initially in the components or are formed early during the service 1 i fe can continue to grow during service. The durabi 1ity or useful 1ife. of a component is directly related to the rate of degradation of its load-bearing capacity by subcritical crack growth and is, therefore, a function of the material's resistance to subcritical crack growth [1-3]. Sustained load cracking (SLC) due to internal hydrogen in titanium alloys is very complex and depends on alloy composition, microstructure, hydrogen content, and applied stress intensity. One area of interest in investigations of SLC in the near-alpha alloy Ti-6Al-2Cb-1Ta-0.8Mo (Ti-6211) is the temperature dependence of crack growth; this aspect can provide information concerning t herma 1 ly activated rate control 1i ng processes which may determine SLC crack growth rates [4]. In work on the titanium alloy Ti-6Al-6V-2S·n, Moody and- Gerberich [5,6] calculated an activation energy for SLC crack growth in air of approximately 30 kJ/mol. The value was related to the diffusion of nydrogen through the beta phase. Threshold stress intensities for SLC crack growth decreased slightly as temperature was decreased below ambient temperature. -
Monsanto Company Insect Resistant Soybean
RELEASE OF INFORMATION Monsanto is submitting the information in this petition for review by the USDA as part of the regulatory process. By submitting this information, Monsanto does not authorize its release to any third party. In the event the USDA receives a Freedom of Information Act request, pursuant to 5 U.S.C. § 552, and 7 CFR Part 1, covering all or some of this information, Monsanto expects that, in advance of the release of the document(s), USDA will provide Monsanto with a copy of the material proposed to be released and the opportunity to object to the release of any information based on appropriate legal grounds, e.g. responsiveness, confidentiality, and/or competitive concerns. Monsanto expects that no information that has been identified as CBI (confidential business information), will be provided to any third party. Monsanto understands that a CBI- deleted copy of this information may be made available to the public in a reading room and by individual request, as part of a public comment period. Except in accordance with the foregoing, Monsanto does not authorize the release, publication or other distribution of this information (including website posting) without Monsanto's prior notice and consent. 2009 Monsanto Company. All Rights Reserved. This document is protected under copyright law. This document is for use only by the regulatory authority to which this has been submitted by Monsanto Company, and only in support of actions requested by Monsanto Company. Any other use of this material, without prior written consent of Monsanto, is strictly prohibited. By submitting this document, Monsanto does not grant any party or entity any right to license or to use the information or intellectual property described in this document. -
Extensions of Remarks 38799 Extensions of Remarks Tribute to Dr
December 20, 1985 EXTENSIONS OF REMARKS 38799 EXTENSIONS OF REMARKS TRIBUTE TO DR. 0. URCILLE Mr. Hofheimer is currently president of and make a more extensive comment on IFILL, SR. the Richard Bower Co., headquartered in this ill-conceived amendment and on the New York City. Despite the demands of this general problems of putting Federal causes HON. WILLIAM H. GRAY III job, he makes time to participate in a varie of action in all our Nation's laws. OF PENNSYLVANIA ty of community activities. His participa To begin with, I must say that my most IN THE HOUSE OF REPRESENTATIVES tion touches all bases of voluntarism: he serious general objection to the Frank pro actively and unselfishly dedicates his time posal was the lack of evidence of its neces Thursday, December 19, 1985 to the Jewish community, while promoting sity. Indeed, the Superfund 301(e) Study Mr. GRAY of Pennsylvania. Mr. Speaker, better education and health care for his Group, the recent Keystone Conference and I should like today to bring the attention of neighbors. other groups have consistently acknowl my colleagues in the House of Representa As a life trustee of various Jewish philan edged the fact that there is little evidence tives to a most distinguished Philadelphian, thropies and a past president of the Jewish to prove that injured parties are frustrated Dr. 0. Urcille Ifill, Sr. Dr. Ifill has been the Community Center in White Plains, Mr. in recovering for their losses under the ex pastor of the African Methodist Episcopal Hofheimer has proven to be an influential isting tort law regime. -
Operations of the Tenth Cruiser Squadron: a Challenge for the Royal Navy and Its Reserves
OPERATIONS OF THE TENTH CRUISER SQUADRON: A CHALLENGE FOR THE ROYAL NAVY AND ITS RESERVES. TERENCE DAWSON LILLEY B.A.(Hons.), M.A., Master Mariner. A thesis submitted in partial fulfilment of the requirements of the University of Greenwich for the Degree of Doctor of Philosophy © June 2012 i I certify that this work has not been accepted in substance for any degree, and is not concurrently being submitted for any degree other than that of Doctor of Philosophy at the University of Greenwich. I also declare that this work is the result of my own investigations except where otherwise identified by references and that I have not plagiarised the work of others. T.D.Lilley 20th June 2012 ............................... First Supervisor Professor R.J. Knight ............................... Second Supervisor Professor S.R.Palmer ii ACKNOWLEDGEMENTS I wish to acknowledge the careful and continued guidance received from my supervisors, Professor Roger Knight and Professor Sarah Palmer. In addition, Edward Phillips, Senior Law Lecturer and Suzanne Louail also of Greenwich Maritime Institute gave useful help. As ever, academic research depends on support from librarians and archivists and mine is no exception. I am indebted to the staffs of the British Library, Bromley Central Library, Caird Library, Dreadnought Library, London School of Economics, National Archives and the Royal Naval Museum, Portsmouth. Particular help came from Miss J.M.Wraight, Admiralty Librarian and Dr. Alan Scarth of Merseyside Maritime Museum, Liverpool. Finally, I acknowledge the loyal support and patience of my late wife, Margaret and the constant encouragement from my daughter Susan to undertake my research. -
Federal Register / Vol. 71, No. 167 / Tuesday, August 29, 2006 / Rules and Regulations
51122 Federal Register / Vol. 71, No. 167 / Tuesday, August 29, 2006 / Rules and Regulations DEPARTMENT OF TRANSPORTATION of SLC are not yet fully understood, it and use of DOT specification cylinders. appears the cracks primarily originate On May 8, 2003, we issued a subsequent Pipeline and Hazardous Materials from the bottom of the neck of the final rule (68 FR 24653) making further Safety Administration cylinder, at or below the lowest thread revisions in response to appeals. In position in the interior of the cylinder. these final rules, we added the 49 CFR Parts 173 and 180 The cracking was first brought to following amendments pertaining to [Docket No. PHMSA–03–14405 (HM–220F)] PHMSA’s attention by persons retesting DOT specification cylinders made with cylinders under the periodic retest aluminum alloy 6351–T6: RIN 2137–AD78 procedures of § 180.209 of the • Removed the authorization for the Hazardous Materials Regulations (HMR; manufacture of DOT specification Hazardous Materials: Aluminum 49 CFR parts 171–180). The majority of cylinders made with aluminum alloy Cylinders Manufactured of Aluminum SLC-related ruptures have occurred in 6351–T6 because cylinders Alloy 6351–T6 Used in SCUBA, SCBA, self-contained underwater breathing manufactured with this aluminum alloy and Oxygen Services—Revised apparatus (SCUBA), self-contained have a greater risk of failure than other Requalification and Use Criteria breathing apparatus (SCBA), and oxygen aluminum cylinders. • AGENCY: Pipeline and Hazardous services. Since 1994, the Pipeline and Prohibited the use of cylinders Materials Safety Administration Hazardous Materials Safety made with aluminum alloy 6351–T6 for (PHMSA), DOT. Administration (PHMSA, we) has been the transportation of materials notified of thirteen suspected SLC poisonous by inhalation in Hazard Zone ACTION: Final rule. -
Long Night of the Tankers: Hitler's War Against Caribbean
University of Calgary PRISM: University of Calgary's Digital Repository University of Calgary Press University of Calgary Press Open Access Books 2014 Long Night of the Tankers: Hitler’s War Against Caribbean Oil Bercuson, David J.; Herwig, Holger H. University of Calgary Press Bercuson, D. J. & Herwig, H. H. "Long Night of the Tankers: Hitler’s War Against Caribbean Oil". Beyond Boundaries: Canadian Defence and Strategic Studies Series; 4. University of Calgary Press, Calgary, Alberta, 2014. http://hdl.handle.net/1880/49998 book http://creativecommons.org/licenses/by-nc-nd/4.0/ Attribution Non-Commercial No Derivatives 4.0 International Downloaded from PRISM: https://prism.ucalgary.ca University of Calgary Press www.uofcpress.com LONG NIGHT OF THE TANKERS: HITLER’S WAR AGAINST CARIBBEAN OIL David J. Bercuson and Holger H. Herwig ISBN 978-1-55238-760-3 THIS BOOK IS AN OPEN ACCESS E-BOOK. It is an electronic version of a book that can be purchased in physical form through any bookseller or on-line retailer, or from our distributors. Please support this open access publication by requesting that your university purchase a print copy of this book, or by purchasing a copy yourself. If you have any questions, please contact us at [email protected] Cover Art: The artwork on the cover of this book is not open access and falls under traditional copyright provisions; it cannot be reproduced in any way without written permission of the artists and their agents. The cover can be displayed as a complete cover image for the purposes of publicizing this work, but the artwork cannot be extracted from the context of the cover of this specific work without breaching the artist’s copyright. -
Integrated Modeling for Optimized Regional Transportation with Compressed Natural Gas Fuel
Alexandria Engineering Journal (2015) xxx, xxx–xxx HOSTED BY Alexandria University Alexandria Engineering Journal www.elsevier.com/locate/aej www.sciencedirect.com ORIGINAL ARTICLE Integrated modeling for optimized regional transportation with compressed natural gas fuel Hossam A. Gabbar a,*, Raymond Bedard a, Nasser Ayoub b a Faculty of Energy Systems and Nuclear Science, University of Ontario Institute of Technology, 2000 Simcoe St. N., Oshawa, L1H 7K4 ON, Canada b Faculty of Industrial Education, Helwan University, Cairo, Egypt Received 31 March 2014; revised 18 November 2014; accepted 28 October 2015 KEYWORDS Abstract Transportation represents major energy consumption where fuel is considered as a pri- Compressed Natural Gas mary energy source. Recent development in the vehicle technology revealed possible economical (CNG); improvements when using natural gas as a fuel source instead of traditional gasoline. There are sev- Alternative fuels; eral fuel alternatives such as electricity, which showed potential for future long-term transportation. Green transportation; However, the move from current situation where gasoline vehicle is dominating shows high cost Hybrid transportation; compared to compressed natural gas vehicle. This paper presents modeling and simulation method- Refueling infrastructure; ology to optimize performance of transportation based on quantitative study of the risk-based Plug-in hybrid electric performance of regional transportation. Emission estimation method is demonstrated and used vehicles (PHEVs) to optimize transportation strategies based on life cycle costing. Different fuel supply scenarios are synthesized and evaluated, which showed strategic use of natural gas as a fuel supply. Ó 2015 Faculty of Engineering, Alexandria University. Production and hosting by Elsevier B.V. This is an open access article under the CC BY-NC-ND license (http://creativecommons.org/licenses/by-nc-nd/4.0/). -
Hydrogen Embrittlement in Titanium Steam Surface Condenser Tubing Truths, Myths & Misnomers
Hydrogen Embrittlement In Titanium Steam Surface Condenser Tubing Truths, Myths & Misnomers Dennis J. Schumerth Titanium Tubular Consultants 4811 E. La Palma Ave Anaheim, CA 92886 USA E-mail [email protected] [email protected] Thomas Demers System Specialist, NB Power Point Lepreau Generating Station 122 County Line Road Maces Bay, New Brunswick Canada E5J1W1 [email protected] ABSTRACT With more than 600 million feet of Grade 2 passivated by circulating water, (CIRH20) and titanium steam surface condenser tubing in the operating temperatures remain relatively service around the world operating without a low, the solubility limit of hydrogen is rarely single reported corrosion event since 1972, threatened. Indeed, the mere existence of few if any competing materials can make such hydrogen embrittlement in a surface condenser a dramatic claim. However, without proper environment has been infrequent reportedly design, operation and maintenance of the occurring only several times over the past 40+ cathodic system envelope, embrittlement or years of powerplant condenser tube service. hydriding of titanium surface condenser tubing Conversely, industries such as the CPI can occur when solubility limits of nascent (chemical process industry), which can expose hydrogen are exceeded. The results of such the heat exchanger to elevated temperatures, an excursion can, in the case of titanium and pH extremes and high levels of hydrogen other materials, induce the formation of brittle charging without the benefit of passivation hydrides. This corrosion event can ultimately have reported hydrogen embrittlement lead to a loss of structural integrity of the damage. material. Notwithstanding the infrequency of this form of Additional contributing factors may include corrosion in powerplant condenser service, elevated temperature, pH extremes and other recently identified activity has surfaced that parameter anomalies.