Outlook for Tungsten
Total Page:16
File Type:pdf, Size:1020Kb
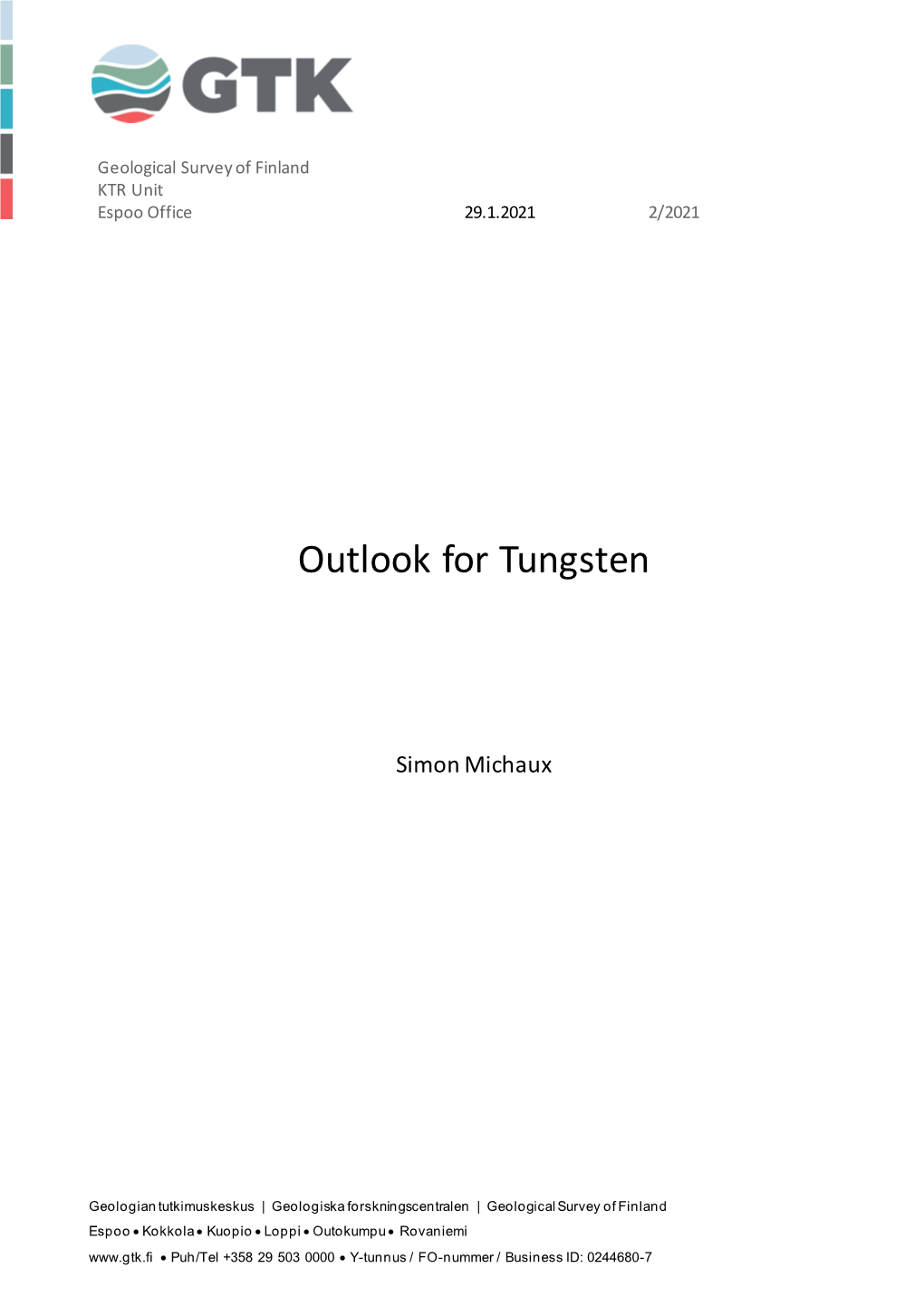
Load more
Recommended publications
-
Current Developments in Uk Mining Projects
CURRENT DEVELOPMENTS IN UK MINING PROJECTS C P Broadbent1) and C A Blackmore1) 1)Wardell Armstrong International Ltd, 46 Chancery Lane, London WC2A 1JE, UK 1 Introduction In October 2017 The Mining Technology Division (MTD) of the IOM3 organised a highly successful conference “Current Developments in the UK Mining Industry”. The aims and objectives of the conference was to define the then current state of the UK Mining Industry1. This conference was a great success and, with the exception of a presentation on Wolf Minerals Ltd, Hemerdon Project, gave the definitive status of most major UK Mining Projects. This paper provides an update of many of these projects. Although the last UK deep pit coal mine, Kellingley Colliery, North Yorkshire closed in December 20152 and was capped off in March 2016. The UK still has large reserves of available fossil fuels and many types of industrial minerals and metals are found in the diverse geology of the UK. Presently there are a number of major initiatives active making 2018, despite events at Hemerdon, one of the most active years in recent times for “new” UK mining ventures. The locations of the projects covered in this paper are shown in Figure 1. 1) 1 Sirius Minerals Plc 2 British Fluorspar Limited 3 West Cumbria Mining 4 Cornish Lithium Limited 5 South Crofty – Strongbow Exploration 8 6 Cornwall Resources Limited – Redmoor Project 7 Dalradian Gold Limited – Curraghinalt Project 8 Scotgold Resources – Cononish Mine 7 3 1 9 Anglesea Mining Plc – Parys Mountain 10 Wolf Minerals Limited - Drakelands Mine 2 Figure 1: Location of the projects c 9 o vered in this paper this paper 10 6 4 5 1 Current Developments – The UK Mining Industry – Presentations at MTD Conference, London 4-5 October 2017 2 Dodgson, L. -
Effects of Metal Contacts and Doping for High
TW-P061 Effects of metal contacts and doping for high-performance field-effect transistor based on tungsten diselenide (WSe2) Seo-Hyeon Jo and Jin-Hong Park School of Electronics and Electrical Engineering, Sungkyunkwan University, Suwon 440-746, Korea Transition metal dichalcogenides (TMDs) with two-dimensional layered structure, such as molybdenum disulfide (MoS2) and tungsten diselenide (WSe2), are considered attractive materials for future semiconductor devices due to its relatively superior electrical, optical, and mechanical properties. Their excellent scalability down to a monolayer based on the van der Waals layered structure without surface dangling bonds makes semiconductor devices based on TMD free from short channel effect. In comparison to the widely studied transistor based on MoS2, researchs focusing on WSe2 transistor are still limited. WSe2 is more resistant to oxidation in humid ambient condition and relatively air-stable than sulphides such as MoS2. These properties of WSe2 provide potential to fabricate high-performance filed-effect transistor if outstanding electronic characteristics can be achieved by suitable metal contacts and doping phenomenon. Here, we demonstrate the effect of two different metal contacts (titanium and platinum) in field-effect transistor based on WSe2, which regulate electronic characteristics of device by controlling the effective barreier height of the metal-semiconductor junction. Electronic properties of WSe2 transistor were systematically investigated through monitoring of threshold voltage shift, carrier concentration difference, on-current ratio, and field-effect mobility ratio with two different metal contacts. Additionally, performance of transistor based on WSe2 is further enhanced through reliable and controllable n-type doping method of WSe2 by triphenylphosphine (PPh3), which activates the doping phenomenon by thermal annealing process and adjust the doping level by controlling the doping concentration of PPh3. -
Exploring Optoelectronics Potential of Monolayer Tungsten Diselenide
60 Technical focus: Optoelectronics Exploring optoelectronics potential of monolayer tungsten diselenide Three groups have recently reported on preliminary experiments with photovoltaic and light-emission effects from pn junctions created using split-gate electrostatic doping. Mike Cooke reports. esearchers are beginning to explore the semi- both convert light into current and current into light. conductor potential of monolayer materials The creation of n- and p-type conductivity in these Rbeyond graphene with hopes of developing devices was achieved electrostatically with a split gate robust devices that are flexible and transparent for beneath the WSe2 monolayer. deployment in wearable formats, interactive displays, Vienna University of Technology [Andreas Pospischil and efficient solar cells. et al, Nature Nanotechnology, vol 9 (2014), p257] An interesting class of materials that has recently come began its fabrication by forming a split gate of titanium/ to the fore is that of few-layer group-VIB transition-metal gold with a 460nm gap on a silicon/silicon dioxide dichalcogenides (TMDs) such as molybdenum disulfide wafer (Figure 1). Gate bonding pads were also formed (MoS2), molybdenum diselenide (MoSe2), tungsten with titanium/gold. The split gate was covered with disulfide (WS2), and tungsten diselenide (WSe2). silicon nitride, except for the bonding pads. The crystal structure consists of the metal atoms WSe2 flakes were exfoliated from bulk material sup- encapsulated between two layers of sulfur/selenium plied by Nanosurf onto a stack of polymer layers on a chalcogenide atoms. The bonding within a monolayer sacrificial silicon substrate. Suitable flakes were identi- is strong while the bonding between monolayers is fied under an optical microscope. -
The Drakelands Mine (Formerly Known As Hemerdon) in England Owned by Wolf Minerals Ltd
Newsletter_06_2016_9.5_Layout 1 02.08.16 09:20 Seite 1 ITIA Tungsten Newsletter – June 2016 In Pursuit of Tungsten Concentrate The focus of this issue is the production of concentrate, with the two World Wars of the last century and officially opened introductions to the Nui Phao mine in Vietnam owned by again in 2015. Masan Resources and to the Drakelands mine (formerly known as Hemerdon) in England owned by Wolf Minerals Ltd. The Our warmest thanks are due to the authors of these articles which former, commissioned in 2013, is the world’s largest operating contain extensive information about both projects, absorbing to mine whilst the latter produced small amounts of ore during anyone with an interest in the supply of the raw material. International Tungsten Industry Association 454-458 Chiswick High Road, London W4 5TT, UK Tel: +44 20 8996 2221 Fax: +44 20 8994 8728 Email: [email protected] www.itia.info ‧ ‧ ‧ ‧ Newsletter_06_2016_9.5_Layout 1 02.08.16 09:20 Seite 2 Masan Resources Nui Phao Project Bich Dinh Ngoc, Manager Community Liaison & Economic Restoration, Nui Phao Mining Company Masan Resources Corporation (Masan), listed on Hanoi’s the focus was changed to tungsten and, on further UPCoM exchange (UPCoM:MSR), is the largest producer exploration, the first geological resource estimate was of primary and mid-stream tungsten products outside released in 2003. Continued success of further drilling of China. Its flagship asset, the Nui Phao open-pit poly- programs and metallurgical test work encouraged the metallic mine, located approximately 85 km north-east company to undertake environmental and community of Hanoi in Thai Nguyen Province, was acquired by baseline studies and the procurement of required per- Masan Group in 2010 as a greenfield project. -
Flexible, Semi-Transparent Ultrathin Solar Cells 9 March 2014
Flexible, semi-transparent ultrathin solar cells 9 March 2014 At least since the Nobel Prize in physics was awarded in 2010 for creating graphene, the "two dimensional crystals" made of carbon atoms have been regarded as one of the most promising materials in electronics. In 2013, graphene research was chosen by the EU as a flagship- project, with a funding of one billion euros. Graphene can sustain extreme mechanical strain and it has great opto-electronic properties. With graphene as a light detector, optical signals can be transformed into electric pulses on extremely short timescales. For one very similar application, however, graphene is not well suited for building solar cells. "The electronic states in graphene are not very practical for creating photovoltaics", says Thomas This is a microscope photograph of WSe2-samples, Mueller. Therefore, he and his team started to look connected to electrodes. Credit: TU Vienna for other materials, which, similarly to graphene, can arranged in ultrathin layers, but have even better electronic properties. A lot of research has been done on graphene The material of choice was tungsten diselenide: It recently—carbon flakes, consisting of only one layer consists of one layer of tungsten atoms, which are of atoms. As it turns out, there are other materials connected by selenium atoms above and below the too which exhibit remarkable properties if they are tungsten plane. The material absorbs light, much arranged in a single layer. One of them is tungsten like graphene, but in tungsten diselenide, this light diselenide, which could be used for photovoltaics. can be used to create electrical power. -
Variation of (I) Cond
PTE/16/59 Development Management Committee 23 November 2016 County Matter: Minerals South Hams District: Variation of (i) condition 3 of planning permission 9/42/49/0542/85/3 to allow the continued extraction of tungsten and tin, processing and disposal of mineral wastes until 5 June 2036 and (ii) removal of condition 13 of planning permission 9/42/49/0542/85/3 to remove the restriction on the operating hours of the primary crusher Location: Drakelands Mine, Drakelands, Nr Plymouth Applicant: Wolf Minerals (UK) Ltd Application No: 9/42/49/0542/85/3 Date application received by Devon County Council: 9 December 2015 Report of the Head of Planning, Transportation and Environment Please note that the following recommendations are subject to consideration and determination by the Committee before taking effect. Recommendation: It is recommended that: (a) The application to vary Condition 3 (to extend the life of the site from June 2021 to June 2036) and to remove Condition 13 (restriction of hours of operation of the primary crusher) of the existing permission be granted and; (b) The remaining conditions be amended as set out in Appendix II. (c) That Committee notes the terms of the Unilateral Undertaking attached at Appendix III. (d) That Committee notes the Habitats Regulations Assessment attached at Appendix IV. 1. Summary 1.1 This application is to extend the permitted life of the Drakelands (previously Hemerdon) Tungsten Mine until 2036 and to remove a condition relating to restrictions on the primary crusher. The application was accompanied -
The Drakelands Project Will Be the UK's First New Mine for More Than 40
MATERIALS WORLD FIrst, teLL me A LIttLE BIT ABOUT THE prOjeCT. The Drakelands project will be the Hemerdon is the third-largest tungsten and tin resource in the world and the Drakelands Mine project, based there, will provide a secure supply of tungsten and UK’s first new mine for more than valuable export revenue for the UK. The project will create more than 200 jobs and 40 years, and it will use ZEISS’s pump hundreds of millions of pounds into the Plymouth, Devon and UK economies Mineralogic Mining automated over the next decade. Its estimated production of 5,000 tonnes per annum of tungsten concentrate and 1,000 tonnes of tin concentrate will mean the £123 million mineralogy system. Rhiannon mine will contribute around 3% of global tungsten supply. Garth Jones speaks to Dr Benjamin Tordoff, Segment Manager for WHAT HAS beeN THE TImefrAme FOR THIS prOjeCT? Mining and Minerals at ZEISS, about Tungsten was discovered at Hemerdon in 1867 and the deposit was identified as the mine and the technology. being a large tungsten-tin vein complex in 1916, during exploration for metal resources to contribute to the war effort – it was subsequently used by government agencies in both world wars. In 1986, after an extensive drilling programme and public enquiry, Amax Exploration UK and Hemerdon Mining and Smelting UK Ltd obtained planning permission to open the mine as an opencast operation working to a depth of 200m. At that time, increased tungsten production by China brought about a considerable reduction in the commodity price and, as a result, the Hemerdon project was placed into care-and-maintenance. -
ACS Division of Analytical Chemistry
ANYL DIVISION OF ANALYTICAL CHEMISTRY P. Bohn and M. Bush, Program Chairs SUNDAY MORNING Section A Placeholder Low-Cost & Open-Source Analytical Chemistry J. P. Grinias, Organizer, Presiding 8:00 . Enabling Real-Time Processing of High-Volume Electrochemical Measurements via Open Source Software. N. Arroyo 8:20 . Open-Source Data Acquisition Devices for Chromatographic Instrumentation. S.W. Foster, E.W. Constans, J.P. Grinias 8:40 . Silicon photomultiplier as a low-cost fluorescence detector for capillary electrophoresis. B. Petersen, N.L. Allbritton 9:00 . Sensitive, selective, and quantitative copper sensor using click-chemistry with gold nanoparticles.. R.M. Cary, I. Monroe, j. holbrook, O. Hess, S. Unser, L. Sagle 9:20 . Glucose Responding Fluorescent Microneedle for An Affordable Continuous Glucose Monitoring. J. Kim, H. YIm, J. Park, H. Choi, B. Lee, S. Lee, M. Lee 9:40 Intermission. 10:00 . Low cost paper-based immunoassays for infectious disease diagnostics. K. Hamad- Schifferli 10:20 . Strength in numbers: A library of chemical color tests improves presumptive identification of illicit drugs and cutting agents.. T. Lockwood, B. Ray, G. Scott, M. Lieberman 10:40 . Chemical fingerprinting of carboxylate anions on low-cost paper supports. Y. Xu, M. Bonizzoni 11:00 . An Analysis of the Quality of Beta-Lactam Antibiotics collected in Nepal. W. Lewis, M. Benjamin 11:20 . Open-access resources for the teaching of analytical chemistry. D.T. Harvey 11:40 . Open-source analytical chemistry in the laboratory and the classroom. J.P. Grinias, J.A. Naese, J. Emig Section B Placeholder Active Learning in the Undergraduate Analytical Chemistry Curriculum (Invited) M. -
'Mind the Gap' Between Atomically Thin Materials 24 December 2014, by Walt Mills
'Mind the gap' between atomically thin materials 24 December 2014, by Walt Mills layer down to the graphene layer, they encountered a surprising amount of resistance. About half of the resistance was caused by the gap, which introduced a large barrier, about 1 electron volt, to the electrons trying to move between layers. This energy barrier could prove useful in designing next generation electronic devices, such as vertical tunneling field effect transistors, said Robinson. The interest in this type of material arose with the discovery of methods to make single layer graphite. Colorized TEM image of tungsten disulfide triangles The Penn State researchers use a more scalable (black) growing on graphene substrate (green). Credit: method than early graphene makers—chemical UT Dallas/Penn State vapor deposition—to deposit a single layer of crystalline tungsten diselenide on top of a few layers of graphene grown from silicon carbide. When it comes to engineering single-layer atomic Although graphene research exploded in the last structures, "minding the gap" will help researchers decade, many similar solids exist that can combine create artificial electronic materials one atomic to create entirely new artificial materials with layer at a time, according to a team of materials unimaginable properties. scientists. The researchers discovered that the tungsten The gap is a miniscule vacuum that researchers in diselenide layer grew in perfectly aligned triangular Penn State's Center for 2-Dimensional and islands 1 to 3 microns in size that slowly coalesced Layered Materials believe is an energy barrier into a single crystal up to 1 centimeter square. They keeping electrons from easily crossing from one reported their results in Nano Letters. -
International Roadmap for Devices and Systems
INTERNATIONAL ROADMAP FOR DEVICES AND SYSTEMS 2020 EDITION BEYOND CMOS THE IRDS IS DEVISED AND INTENDED FOR TECHNOLOGY ASSESSMENT ONLY AND IS WITHOUT REGARD TO ANY COMMERCIAL CONSIDERATIONS PERTAINING TO INDIVIDUAL PRODUCTS OR EQUIPMENT. ii © 2020 IEEE. Personal use of this material is permitted. Permission from IEEE must be obtained for all other uses, in any current or future media, including reprinting/republishing this material for advertising or promotional purposes, creating new collective works, for resale or redistribution to servers or lists, or reuse of any copyrighted component of this work in other works. THE INTERNATIONAL ROADMAP FOR DEVICES AND SYSTEMS: 2020 COPYRIGHT © 2020 IEEE. ALL RIGHTS RESERVED. iii Table of Contents Acknowledgments .............................................................................................................................. vi 1. Introduction .................................................................................................................................. 1 1.1. Scope of Beyond-CMOS Focus Team .............................................................................................. 1 1.2. Difficult Challenges ............................................................................................................................ 2 1.3. Nano-information Processing Taxonomy........................................................................................... 4 2. Emerging Memory Devices .......................................................................................................... -
Wolf Minerals Limited (The Company)
Sydney Mining Club Presentation 5th November 2015 Russell Clark, Managing Director ASX:WLF|AIM:WLFE www.wolfminerals.com.au Disclaimer The information contained in this document has been prepared based upon information supplied by Wolf Minerals Limited (the Company). This Document does not constitute an offer or invitation to any person to subscribe for or apply for any securities in the Company. While the information contained in this Document has been prepared in good faith, neither the Company nor any of its shareholders, directors, officers, agents, employees or advisers give any representations or warranties (express or implied) as to the accuracy, reliability or completeness of the information in this Document, or of any other written or oral information made or to be made available to any interested party or its advisers (all such information being referred to as Information) and liability therefore is expressly disclaimed. Accordingly, to the full extent permitted by law, neither the Company nor any of its shareholders, directors, officers, agents, employees or advisers take any responsibility for, or will accept any liability whether direct or indirect, express or implied, contractual, tortious, statutory or otherwise, in respect of, the accuracy or completeness of the Information or for any of the opinions contained in this Document or for any errors, omissions or misstatements or for any loss, howsoever arising, from the use of this Document. Neither the issue of this Document nor any part of its contents is to be taken as any form of commitment on the part of the Company to proceed with any transaction and the right is reserved to terminate any discussions or negotiations with any person. -
Electrical Properties of Wse2, WS2, Mose2, Mos2, and Their Use As Photoanodes in a Semiconductor Liquid Junction Solar Cell Kam-Keung Kam Iowa State University
Iowa State University Capstones, Theses and Retrospective Theses and Dissertations Dissertations 1982 Electrical properties of WSe2, WS2, MoSe2, MoS2, and their use as photoanodes in a semiconductor liquid junction solar cell Kam-Keung Kam Iowa State University Follow this and additional works at: https://lib.dr.iastate.edu/rtd Part of the Condensed Matter Physics Commons Recommended Citation Kam, Kam-Keung, "Electrical properties of WSe2, WS2, MoSe2, MoS2, and their use as photoanodes in a semiconductor liquid junction solar cell " (1982). Retrospective Theses and Dissertations. 8356. https://lib.dr.iastate.edu/rtd/8356 This Dissertation is brought to you for free and open access by the Iowa State University Capstones, Theses and Dissertations at Iowa State University Digital Repository. It has been accepted for inclusion in Retrospective Theses and Dissertations by an authorized administrator of Iowa State University Digital Repository. For more information, please contact [email protected]. INFORMATION TO USERS This reproduction was made from a copy of a document sent to us for microfilming. While the most advanced technology has been used to photograph and reproduce this document, the quality of the reproduction is heavily dependent upon the quality of the material submitted. The following explanation of techniques is provided to help clarify markings or notations which may appear on this reproduction. 1.The sign or "target" for pages apparently lacking from the document photographed is "Missing Page(s)". If it was possible to obtain the missing page(s) or section, they are spliced into the film along with adjacent pages. This may have necessitated cutting through an image and duplicating adjacent pages to assure complete continuity.