Evaluating the Impact
Total Page:16
File Type:pdf, Size:1020Kb
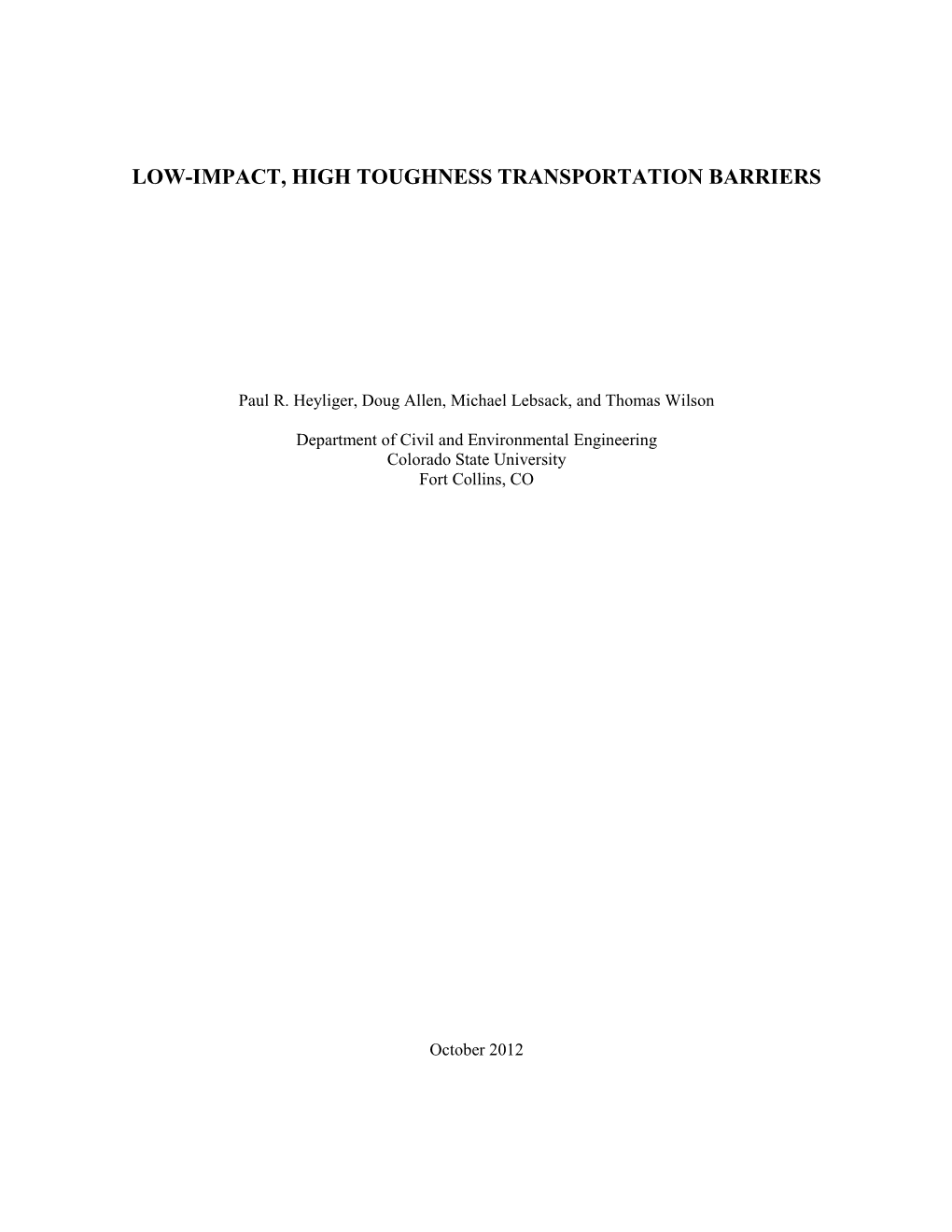
Load more
Recommended publications
-
Manual on Uniform Traffic Control Devices Manual on Uniform Traffic
MManualanual onon UUniformniform TTrafficraffic CControlontrol DDevicesevices forfor StreetsStreets andand HighwaysHighways U.S. Department of Transportation Federal Highway Administration for Streets and Highways Control Devices Manual on Uniform Traffic Dotted line indicates edge of binder spine. MM UU TT CC DD U.S. Department of Transportation Federal Highway Administration MManualanual onon UUniformniform TTrafficraffic CControlontrol DDevicesevices forfor StreetsStreets andand HighwaysHighways U.S. Department of Transportation Federal Highway Administration 2003 Edition Page i The Manual on Uniform Traffic Control Devices (MUTCD) is approved by the Federal Highway Administrator as the National Standard in accordance with Title 23 U.S. Code, Sections 109(d), 114(a), 217, 315, and 402(a), 23 CFR 655, and 49 CFR 1.48(b)(8), 1.48(b)(33), and 1.48(c)(2). Addresses for Publications Referenced in the MUTCD American Association of State Highway and Transportation Officials (AASHTO) 444 North Capitol Street, NW, Suite 249 Washington, DC 20001 www.transportation.org American Railway Engineering and Maintenance-of-Way Association (AREMA) 8201 Corporate Drive, Suite 1125 Landover, MD 20785-2230 www.arema.org Federal Highway Administration Report Center Facsimile number: 301.577.1421 [email protected] Illuminating Engineering Society (IES) 120 Wall Street, Floor 17 New York, NY 10005 www.iesna.org Institute of Makers of Explosives 1120 19th Street, NW, Suite 310 Washington, DC 20036-3605 www.ime.org Institute of Transportation Engineers -
MN MUTCD Chapter 2H
Chapter 2B. REGULATORY SIGNS TABLE OF CONTENTS Chapter 2B. REGULATORY SIGNS 2B.1 Application of Regulatory Signs ..........................................................................................2B-1 2B.2 Design of Regulatory Signs ..................................................................................................2B-1 2B.3 Size of Regulatory Signs ......................................................................................................2B-1 2B.4 Right-of-Way at Intersections ...............................................................................................2B-7 2B.5 STOP Sign (R1-1) and ALL WAY Plaque (R1-3P) ...............................................................2B-8 2B.6 STOP Sign Applications .......................................................................................................2B-9 2B.7 Multi-Way Stop Applications ...............................................................................................2B-9 2B.8 YIELD Sign (R1-2) ..............................................................................................................2B-10 2B.9 YIELD Sign Applications .....................................................................................................2B-10 2B.10 STOP Sign or YIELD Sign Placement .................................................................................2B-10 2B.11 Stop Here For Pedestrians Signs (R1-5 Series) ....................................................................2B-11 2B.12 In-Street and Overhead Pedestrian -
Spill Clean-Up Recommendations for Emergency Escape Ramps (Eers): Western Mountain Dots’ Perspectives
55th ASC Annual International Conference Proceedings Copyright 2019 by the Associated Schools of Construction Spill Clean-up Recommendations for Emergency Escape Ramps (EERs): Western Mountain DOTs’ Perspectives Deniz Besiktepe, Ph.D. Student¹, Dr. Rodolfo Valdes- Dr. Kelly Strong, Ph.D.² Vasquez, Ph.D.¹, and Dr. Scott Shuler, Ph.D.¹ ¹ Department of Construction Management, ² Department of Construction Management, Colorado State University University of Northern Iowa Fort Collins, Colorado Cedar Falls, Iowa Steep grades and runaway trucks have the potential of severe and fatal crashes. The use of an emergency escape ramp (EER) accommodates the control of runaway trucks by slowing and stopping them. Fuel or hazardous material (hazmat) spills may result from rollover or jack knife after trucks enter the EER. The objective of this research is to understand the clean-up processes and the remediation techniques after trucks enter ramps, and the auditing/verification processes after the clean-up. Additionally, this study presents a set of recommendations to improve spill clean-up processes and remediation techniques after trucks enter EERs. The recommendations are developed by using the combined method of literature review, phone interviews with staff from western state Departments of Transportations (DOTs), emergency responder companies, and hazmat personnel from Colorado DOT unit as well as exploratory analysis. The implementation of the recommendations will benefit DOTs and freight carriers through improved driver safety and freight security, and the general public through less hazmat discharge into the natural environment. Key Words: Emergency escape ramp, Truck escape ramp, Runaway truck ramp, Fuel spills, Clean- up, Maintenance. Introduction Emergency Escape Ramps (EERs) have proven to be an effective method to control and stop runaway vehicles by transferring the vehicles’ energy through gravitational deceleration, rolling resistance or both (Abdelwahab, & Morral, 1997). -
Download Lesson PDF File
STEM Curriculum Planning Guide This instructional design guide serves as the template for the design and development of STEM units of instruction at the Dayton Regional STEM Center in Dayton, Ohio. The guide is anchored to the STEM Education Quality Framework also developed at the Dayton Regional STEM Center. STEM Unit Title Saving Runaway Gramps Economic Cluster Manufacturing, Materials Engineering, Civil Engineering Targeted Grades 6 STEM Disciplines Science, Technology, Engineering, and Mathematics Non-STEM English Language Arts and Fine Arts Disciplines The electronic template is copyrighted to Dayton Regional STEM Center. No permission has been granted for template reproduction. However, lesson contents may be reproduced and attributed to Dayton Regional STEM Center free of charge. Page 1 of 32 Draft: Friday, December 8, 2017 www.daytonregionalstemcenter.org Section I: STEM Unit Overview Unit Overview Students are engaged to consider the challenges faced by people in wheelchairs and develop remedial strategies following engineering design. While modern building designs follow specific regulations to provide safe accessibility to wheelchairs, many older neighborhoods still contain designs inaccessible and dangerous for people in wheelchairs. For example, many ramp designs have slopes too large or lengths too short to safely stop a rolling wheelchair. Therefore, students are challenged to design accessible ramps using common rocks and minerals to modify ramp surfaces that can safely and efficiently stop wheelchairs. In completing the design challenge, students will demonstrate understanding of mathematical relationships between speed and motion and differentiation of potential and kinetic energy. By maintaining an Engineering Log, students will also develop skills in writing quantitative ideas and evidence-based argument. -
Haul Truck Audit
Haul Truck Audit Centers for Disease Control and Prevention National Institute for Occupational Safety and Health Haul Truck Audit This audit assesses the administrative issues (i.e. training and policies), haul road and pit conditions, and the job tasks and physical equipment that impact the ergonomics and safety of haul truck drivers. Haul Truck Audit Instructions This audit package contains four documents that are necessary to conduct a haul truck audit. A description and intended use of each document is provided below. 1. Haul Truck Audit Information Page – This page allows the audit user to record pertinent information to be filed with the audit results and recommendations. A separate Haul Truck Audit Information Page should be used for each location and time when conducting an audit of multiple location or at multiple times 2. Haul Truck Audit Answer Sheet – This document can be used to record responses to audit questions, thereby allowing the user to reuse the Haul Truck Audit Questions document multiple times without the need for additional copies of the questions. 3. Haul Truck Audit Questions – This document contains the full set of audit questions and is arranged in a modular format. This should be used to conduct the ergonomics audit. Please note, to complete modules three and eight you will need a tape measure or other means to measure distance. You will also need equipment to measure dust and noise levels to complete module six. 4. Haul Truck Audit Recommendations – This document contains all the recommendations for the audit questions. It includes a checkbox beside each recommendation allowing the user to check the recommendation which corresponds to each of the answers recorded on the answer sheet. -
HPR-280: a Review of Truck Escape Ramps
A REVIEW OF TRUCK ESCAPE RAMPS for HPR-PL-1(31)280 EVALUATION OF ARRESTER BED PERFORMANCE Steven 1. Tritsch, P.E. Senior Research Engineer Arizona Department of Transportation Arizona Transportation Research Center 206 Smth 17th Avenue Mail Drop 075R Phoenix, Arizona 85937 December 1987 INTRODUCTION DESIGN HJSTORICAL EXPERIENCE CURRENT RESEARCH CONCLUSIONS AND RECOMMENDATIONS REFERENCES ANNOTATED BIBLIOGRAPHY . - . .. TRUCK ESCAPE RAMPS INTRODUCTION Truck escape ramps, for the purposes of this review, are designed by highway engineers to safely slow down and stop a runaway vehicle. The typical runaway vehicle may be a loaded tractor trailer unit speeding down a long hill with overheated brakes and no way to stop under its own power. The vehicle ultimately reaches a velocity where curves can no longer be negotiated and crashes - into an ern5ankment, a ravine, or another vehicle. Truck escape ramps have been used in this country for over 30 years. There are currently over 65 escape ramps in use throughout the United States today. Of the three types (gravity ramps, sandpiles, gravel beds) of escape ramps, the gravel bed is the most predominant design used today. The aggregate used in the gravel bed has been referred to as "pea" gravel, which has many connotations, depending on the agency or part of the country one is in. DESIGN The design of escape ramps has evolved from a trial and error process. At the present time, there are no nationally accepted design standards for truck escape ramps. Several states have departmental policies and/or guidelines for designing escape ramps in their jurisdictional boundaries. There are numerous articles and publications on the subject; however, many tack the supporting documentation necessary to justify an overall design methodology for universal use. -
From Truck-Only Lanes
Appendix A. NCHRP Project 03-73 Separation of Vehicles – CMV- Only Lanes Task 7 – Interim Report NCHRP Project 3-73: Separation of Vehicles - CMV-Only Lanes A. NCHRP Project 03-73 Separation of Vehicles – CMV-Only Lanes Task 7 – Interim Report A.1 Introduction This interim report document provides results of the first phase of research on National Cooperative Highway Research Program (NCHRP) Project 03-73 Separation of Vehicles – Commercial Motor Vehicle-Only Lanes project. It presents a review and discussion of a wide range of issues relevant to planning, designing, and evaluating a variety of concepts from CMV-Only Lanes that should be useful to planners and policy makers in the public and private sector. It also presents an evaluation of available data and its suitability to conduct additional analyses in Phase II of the research plan. A.1.1 Project Overview For a number of years, there has been growing interest in commercial motor vehicle (CMV)- only lanes and several notable proposals for CMV-only lane systems/projects have appeared in the planning and traffic engineering literature. To a large extent, this growth in interest has been related to the growth in truck traffic relative to automobile traffic and the contribution of truck traffic to congestion. Heavy trucks have a greater impact on capacity than their sheer volume would suggest, especially when mixed with automobiles. Separation of autos and trucks may be a beneficial way of building more system capacity in certain circumstances. A number of studies also have suggested that CMV-only lanes that are tolled may present a viable means of financing system capacity improvements. -
Chapter #8 Sharing the Road with Other Users
Chapter #8 Sharing the Road with Other Users Chapter #8 Overview Unit 8 will introduce the driver to other roadway users and how to interact with them. The student will learn to interact with pedestrians, bicyclists, motorcyclists, and drivers of large vehicles, emergency vehicles, trains, public transportation and construction vehicles as well as how to drive through work zones. The characteristics of and interaction with these motorized and non-motorized users will be discussed. Risk reducing strategies will be presented for sharing the road with other users. Objectives The students will: 1. Describe the importance of sharing the road with other users. 2. Describe the characteristics of pedestrians and how to share the road with them. 3. Describe the characteristics of bicycles and how to share the road with them. 4. Describe the characteristics of motorcycles, scooters and mopeds and how to share the road with them. 5. Describe the characteristics of large vehicles and how to share the road with them. 6. Describe the characteristics of emergency vehicles and how to share the road with them. 7. Describe the characteristics of trains and public transportation and how to share the road with them. 8. Describe the characteristics of construction vehicles and work zones and how to share the road with them. 9. Define key words associated with the unit objectives. Key Terms Mid-block crosswalk – area located in the middle of a block, which requires you to yield as you would at an intersection. Usually there will be warning signs to alert you of a crosswalk. Move-over laws – require drivers to slow and change lanes when approaching a roadside incident or when approaching an emergency vehicle stopped on the roadway. -
Traffic Operations Guidance Manual REVISION NO.: 15
COMMONWEALTH OF KENTUCKY TRANSPORTATION CABINET FRANKFORT, KY 40622 MANUAL TITLE: Traffic Operations Guidance Manual REVISION NO.: 15 DATE REQUESTED: April 2021 REPRINT: REQUESTED BY: Kim Jasper NEW: NEW & REVISED POLICIES CHAPTER/ EXPLANATION OLD NEW SECTION PAGES PAGES TO BE TO BE DELETED ADDED The purpose of this printing is to include the following new and revised policies and procedures in the Traffic Operations Guidance Manual. This revision also includes one exhibit update and a Table of Contents update. TO-400 One-Way Signing on Bifurcated Highways TO-402-01 Stop Control at Intersections TO-402-01 Passing Regulations TO-402-02 Freeway Prohibition Signs TO-402-02 NO U-TURN Signs TO-402-03 No U-turn Signs TO-402-03 Truck Lane Restrictions TO-402-04 TO-402-04 Speed Regulations TO-402-05 TO-402-05 STOP Signs at Railroad Crossings TO-402-06 TO-402-06 Median Crossover Signs TO-402-07 Anti-Littering Signs TO-402-07 Anti-Littering Signs TO-402-08 KEEP RIGHT EXCEPT TO PASS Signs TO-402-08 Stop Control at Intersections TO-402-09 Weight Limit Signs TO-402-09 KEEP RIGHT EXCEPT TO PASS Signs TO-402-10 NO TURN ON RED Signs TO-402-10 Weight Limit Signs TO-402-11 Yield Here To Pedestrians Signs TO-402-11 NO TURN ON RED Signs TO-402-12 Engine Compression System Signs TO-402-12 Seat Belt Signs TO-402-13 Introduction TO-404-01 TO-404-01 Route Signs TO-404-02 TO-404-02 FORMERLY Signs TO-404-03 TO-404-03 Destination & Distance Signs TO-404-04 TO-404-04 Street Name Signs TO-404-05 TO-404-05 Numbering of Signalized Intersections TO-404-06 TO-404-06 -
Table of Contents Table of Contents
TABLE OF CONTENTS TABLE OF CONTENTS Please read Disclaimer, Acknowledgements, and Copyright info. General Disclaimer In no event will R&R Publishing Inc. (or its directors, officers, or employees) be liable to any party for any direct, indirect, punitive, special, incidental or other consequential damages arising directly or indirectly from any use of our web site, or the electronic or printed versions of Mountain Directory West, Mountain Directory East, or E-Books or software created using the information provided in said books. THE INFORMATION ON OUR WEB SITE, AND IN THE PRINTED AND ELECTRONIC VERSIONS OF THE BOOKS SOLD VIA THIS WEB SITE, ARE PROVIDED “AS IS” AND WITHOUT WARRANTIES TO PERFORMANCE OF, MERCHANTABILITY, OR ANY OTHER WARRANTIES WHETHER EXPRESSED OR IMPLIED. THE USER ASSUMES THE ENTIRE RISK OF USING THE WEB SITE AND THE PRINTED AND ELECTRONIC VERSIONS OF THE BOOKS. While every effort has been made to ensure the accuracy of the maps and text included in the Mountain Directory books, it is nearly impossible to include all necessary detail on such small map pages. We recommend that these maps be used in conjunction with larger, more detailed road maps. The directories do not claim to include every steep grade. In fact, because of the enormous area we have tried to cover, we can guarantee that we have probably missed some passes and steep grades that deserve to be included. We have not attempted to cover unpaved roads since large vehicles usually stay on the main paved roads. Sometimes the percentages quoted are estimates and many times they are based on road signs or information provided by highway departments. -
From Footpaths to Freeways
From Footpaths to Freeways A Survey of Roads and Highways in Minnesota By Joel Katz, P.E., PTOE Minnesota Department of Transportation DEDICATION This book is dedicated to the thousands of Minnesotans — past and present — who have been involved in the planning, design, construction, maintenance, and operation of the roads, streets, and highways of Minnesota, , as well as those who have played essential roles in such areas as financing, administration, research, education, and communications. These are the people who have been employed by the federal, state, and local governments; contractors; consultant firms; and educational institutions who have applied their professional and trade experience in developing a transportation system on which our way of life and economic viability has become so greatly dependent. Some of these employees lost their lives while performing construction, maintenance, and enforcement activities. All have worked diligently, loyally, and professionally — especially in emergency situations. Prepared by Center for Transportation Studies, University of Minnesota Editor: Nancy Baldrica Designer: Jennifer Wreisner CTS Coordinators: Pam Snopl, Gina Baas, and Shawn Haag Center for Transportation Studies University of Minnesota 200 Transportation & Safety Building 511 Washington Ave SE Minneapolis, MN 55455 Copyright ©2009 Mn/DOT. Minnesota Department of Transportation 395 John Ireland Boulevard • St. Paul, MN 55155-1899 Phone: 800/657-3774 • 800/627-3529 The Minnesota Department of Transportation is an equal opportunity employer. The University of Minnesota is an equal opportunity educator and employer. This report represents the results of research conducted by the author and does not necessarily represent the views or policies of the Minnesota Department of Transportation and/or the Center for Transportation Studies. -
New Jersey Statewide Transportation Improvement Program
New Jersey Statewide Transportation Improvement Program Fiscal Years 2007 - 2010 Governor Jon Corzine Commissioner Kris Kolluri, Esq. October 1, 2006 Table of Contents Section IA Introduction Section IB Financial Tables Section II NJDOT Project Descriptions Section III NJ TRANSIT Project Descriptions Section IV Authorities, Project Descriptions Section V Transition Projects Section VI Glossary Appendix A FY 2006 Major Project Status Appendix B FY 2007-08 Study & Development Program SECTION IA INTRODUCTION Introduction a. Overview This document is the Statewide Transportation Improvement Program for the state of New Jersey for federal fiscal years 2007 (beginning October 1, 2006) through 2010. The Statewide Transportation Improvement Program (STIP) serves two purposes. First, it presents a comprehensive, one-volume guide to major transportation improvements planned in the state of New Jersey therefore providing a valuable reference for implementing agencies (such as the New Jersey Department of Transportation and the New Jersey Transit Corporation) and all those interested in transportation issues in this state. Second, it serves as the reference document required under federal regulations (23 CFR 450.216) for use by the Federal Highway Administration and the Federal Transit Administration in approving the expenditure of federal funds for transportation projects in New Jersey. Federal legislation requires that each state develop one multimodal Statewide Transportation Improvement Program (STIP) for all areas of the state. In New Jersey, the STIP consists of a listing of statewide line items and programs, as well as the regional Transportation Improvement Program (TIP) projects, all of which were developed by the three Metropolitan Planning Organizations (MPOs). The TIPs contain local and state highway projects, statewide line items and programs, as well as public transit projects.