14. Brake Systems
Total Page:16
File Type:pdf, Size:1020Kb
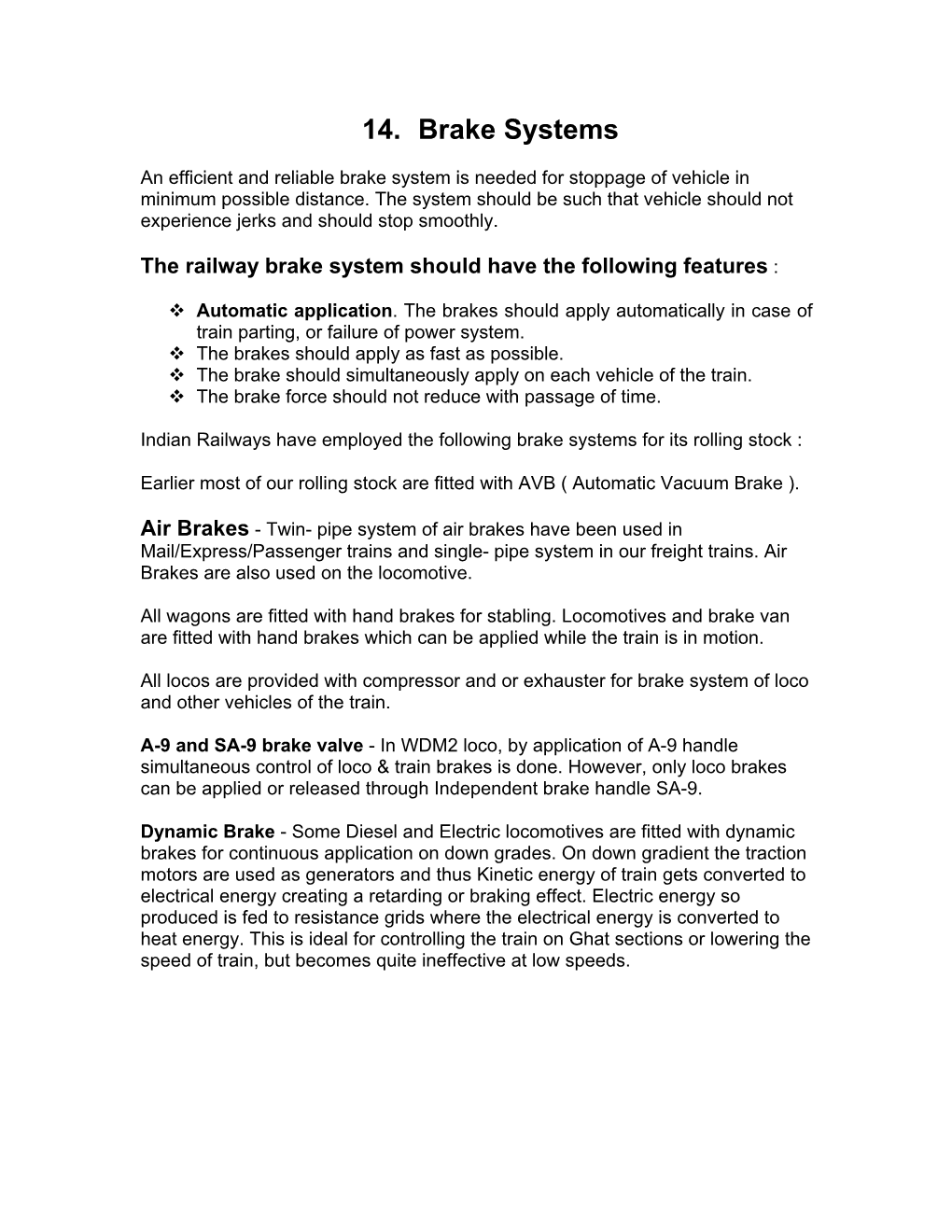
Load more
Recommended publications
-
Determination of Forces in the Elements of the Brake Rigging of Bogies of Freight Cars
E3S Web of Conferences 166, 07004 (2020) https://doi.org/10.1051/e3sconf/202016607004 ICSF 2020 Determination of forces in the elements of the brake rigging of bogies of freight cars İsrail Elyazov1, Vasyl Ravlyuk2,*, Andriy Rybin2, and Vitalii Hrebeniuk2 1Azerbaijan Technical University, Department of Railway Transport Operation, 25 H. Javid Ave., Baku, Az 1073, Azerbaijan 2Ukrainian State University of Railway Transport, Department of Cars, 7 Feuerbach Sq., Kharkov, 61050, Ukraine Abstract. The article presents the results of studies the purpose of which was solving the problem of deceleration of abnormal wear of brake pads in freight cars of Ukrzaliznytsia JSC. In the studies, the design schemes of brake rigging during braking were considered theoretically. Particular attention was paid to the determination of force loads acting in the rods of the rigging and the contact area of the brake pads with the rolling surfaces of the wheels during braking. Design analysis was performed to determine rational solutions from the point of view of determined force load of the rigging elements of the bogies during braking, in particular, taking into account the action of harmful torque caused by the movement of the bogie on inequalities “track joints”. Based on the conducted studies, it was decided to create a 2D generalized model diagram to determine reliable information on the operation of triangle brake rigging. 1 Introduction a basis to propose a generalized mathematical design model for which theoretical studies with corresponding Today, the main task of Ukrzaliznytsya JSC is increasing calculations have been performed. the volume of freight transportation, which requires increasing the weight and the speed of freight trains. -
Dynamic Testing of Innovative Railway Brake System for Freight Wagons
A NNALS of Faculty Engineering Hunedoara – International Journal of Engineering Tome XVII [2019] | Fascicule 1 [February] 1.Gligorche VRTANOSKI, 2.Tasko SMILESKI DYNAMIC TESTING OF INNOVATIVE RAILWAY BRAKE SYSTEM FOR FREIGHT WAGONS 1.Institute of Production Enginering and Management, Faculty of Mechanical Engineering, SS. Cyril and Methodius University in Skopje, Skopje, MACEDONIA 2.Faculty of Mechanical Engineering, SS. Cyril and Methodius University in Skopje, Skopje, MACEDONIA Abstract: In this paper is shown dynamic testing of innovative railway brake system for freight wagons. Brake systems have the essential function of decelerating and stopping of railway rolling stock. Because the brake systems are a subject of large static and dynamic loads in external conditions, lot of tests should be done. In this paper will be shown the way of conducting dynamic testing on the innovative railway brake system. Keywords: railway, dynamic, testing, brake, freight wagon 1. INTRODUCTION The development of rail transport in recent decades goes in direction of increasing the speed and loading performance of the railway vehicles. This directly affects the development of brake technology [11]. The braking system has an essential function of reducing the speed and braking of the vehicle for the minimum possible time. The braking process of rolling stock is of great importance for the safety in the railway traffic. As railway operators focus on the need for greater improvements in efficiency and safety, there is still a significant need to advancements of the railway brake systems [12]. Several types of brake systems are used in the railways. Most commonly are used compressed air brake systems, called pneumatic brake systems [2]. -
Full-Scale Dynamometer Test of Composite Railway Brake Shoes – Study on the Effect of the Reinforcing Fibre Type
Piotr Wasilewski DOI 10.2478/ama-2018-0031 Full-Scale Dynamometer Test of Composite Railway Brake Shoes – Study on the Effect of the reinforcing Fibre Type FULL-SCALE DYNAMOMETER TEST OF COMPOSITE RAILWAY BRAKE SHOES – STUDY ON THE EFFECT OF THE REINFORCING FIBRE TYPE Piotr WASILEWSKI* *Faculty of Mechanical Engineering, Department of Mechanics and Applied Computer Science, Bialystok University of Technology, ul. Wiejska 45C, 15-351 Bialystok, Poland; SMiOC Frenoplast Bułhak i Cieślawski S.A., Research and Development Department, Korpele 75 – Strefa, 12-100 Szczytno, Poland [email protected] received 4 June 2018, revised 4 September 2018, accepted 7 September 2018 Abstract: When designing or developing friction materials, it is crucial to predict how the modification of the formulation will affect their properties. Fibres are introduced in the composition of the phenolic-based brake friction materials to improve their mechanical strength. Apart from reinforcing the composite, fibres can also affect its tribological and thermophysical properties. In this study two com- posite friction materials are compared. The difference between the materials was the type of reinforcing fibre used in the formulation – in one case it was glass fibre, in the other steel fibre. Thermal diffusivity of both materials was measured and thermal conductivity was calcu- lated. Frictional characteristics determined by means of full-scale dynamometer tests are analysed and discussed. Substitution of glass fi- bre with steel fibre led to increase in the friction coefficient. Maximum average temperature below wheel surface, observed during the test of the material containing steel fibre, was lower as compared to the test results of the material with glass fibre in its formulation, despite higher heat flux in the course of brake applications. -
Thermal Capacity of Railway Wheels Temperatures, Residual Stresses and Fatigue Damage with Special Focus on Metro Applications
THESIS FOR THE DEGREE OF DOCTOR OF PHILOSOPHY IN SOLID AND STRUCTURAL MECHANICS Thermal Capacity of Railway Wheels Temperatures, residual stresses and fatigue damage with special focus on metro applications SHAHAB TEIMOURIMANESH Department of Applied Mechanics CHALMERS UNIVERSITY OF TECHNOLOGY Gothenburg, Sweden, 2014 Thermal Capacity of Railway Wheels – Temperatures, residual stresses and fatigue damage with special focus on metro applications SHAHAB TEIMOURIMANESH ISBN 978-91-7385-974-5 © SHAHAB TEIMOURIMANESH, 2014 Doktorsavhandlingar vid Chalmers tekniska högskola. Ny serie nr 3655 ISSN 0346-718X Department of Applied Mechanics Chalmers University of Technology SE-412 96 Gothenburg Sweden Telephone +46 (0)31 772 1000 Cover: A metro bogie equipped with a tread brake system (upper), a brake block in contact with a railway wheel (lower right) and view of bogie interior with brake block, wheel and axle (lower left) Photographed by Markus Meinel of Interfleet Technology Chalmers Reproservice Gothenburg, Sweden 2014 Thermal Capacity of Railway Wheels – Temperatures, residual stresses and fatigue damage with special focus on metro applications Thesis for the degree of Doctor of Philosophy in Solid and Structural Mechanics SHAHAB TEIMOURIMANESH Department of Applied Mechanics Chalmers University of Technology ABSTRACT Tread (block) braking is still one of the most common braking systems on railway vehicles. The action is carried out by pressing brake blocks against the tread of a wheel, which is also in rolling contact with the rail. The extensive use of tread brakes in metro and suburban applications has created a need for design guidelines or standards for wheels exposed to repeated stop braking. The thermal capacity of the wheels puts a limit to railway tread braking systems. -
Development of Hydraulic Friction Brake for Railway Rolling Stock∗ (Part I: Static Behavior of Poppet-Type Brake Pressure Control Valve)
1149 Development of Hydraulic Friction Brake for Railway Rolling Stock∗ (Part I: Static Behavior of Poppet-Type Brake Pressure Control Valve) Thum CHENVISUWAT∗∗, Sung-Hwan PARK∗∗∗ and Ato KITAGAWA∗∗∗∗ In this study, a novel hydraulic brake system is proposed in order to increase the reliabil- ity of railway brake systems. The reason hydraulic brake systems have not been taken up as a practical railway brake system until now is that the brake pressure control valve inherently has internal leakage and this causes insufficient fail-safe function. Accordingly, We focus on the development of a hydraulic brake pressure control valve (BPC valve) in this study. By virtue of adopting poppet elements in the valve, the braking force is maintained without in- ternal leakage even when the electric power supply fails. The developed BPC valve includes a built-in pressure feedback mechanism and it enables the pressure control function to be maintained when the pressure transducer is broken. The operating principle and wear com- pensation methods for poppet elements are also examined in this study. The experimental results verify the linearity of static behavior, the stability, and the performance of the valve in maintaining output pressure. Key Words: Railway, Hydraulic Brake, Pressure Control, Poppet Valve, Servomechanism formance of the dynamic brake system is not influenced 1. Introduction by wear. But, the regenerated power is limited by some Recently, electrical railways have adopted a hybrid factors such as the performance of the substation and the brake system composed of a mechanical brake (friction size of electrical transmission lines. Accordingly, its out- brake) and an electrical brake (dynamic brake). -
Rail Accident Report
Rail Accident Report Signal passed at danger at Stafford 26 April 2012 Report 16/2013 September 2013 This investigation was carried out in accordance with: l the Railway Safety Directive 2004/49/EC; l the Railways and Transport Safety Act 2003; and l the Railways (Accident Investigation and Reporting) Regulations 2005. © Crown copyright 2013 You may re-use this document/publication (not including departmental or agency logos) free of charge in any format or medium. You must re-use it accurately and not in a misleading context. The material must be acknowledged as Crown copyright and you must give the title of the source publication. Where we have identified any third party copyright material you will need to obtain permission from the copyright holders concerned. This document/publication is also available at www.raib.gov.uk. Any enquiries about this publication should be sent to: RAIB Email: [email protected] The Wharf Telephone: 01332 253300 Stores Road Fax: 01332 253301 Derby UK Website: www.raib.gov.uk DE21 4BA This report is published by the Rail Accident Investigation Branch, Department for Transport. (Cover photo courtesy Andrew Edkins) Signal passed at danger at Stafford, 26 April 2012 Contents Summary 5 Introduction 6 Preface 6 Key definitions 6 The incident 7 Summary of the incident 7 Context 7 Events preceding the incident 11 Events during the incident 12 Events following the incident 13 The investigation 14 Sources of evidence 14 Acknowledgements 15 Key facts and analysis 16 Identification of the immediate cause 16 Identification -
''Design and Modification of Vacuum Braking System”
Anbalagan . R, Jancirani .J, Venkateshwaran. N / International Journal of Engineering Research and Applications (IJERA) ISSN: 2248-9622 www.ijera.com Vol. 3, Issue 3, May-Jun 2013, pp.907-916 ‘‘Design and Modification of vacuum braking system” Anbalagan . R (*), Jancirani .J(**), Venkateshwaran. N(***) * Department of Automobile Engineering, Rajalakshmi Engineering College, Chennai – 602105. India. ** Madras Institute of Technology, Chennai-600044.India. ***Department of Mechanical Engineering, Rajalakshmi Engineering College, Chennai - 602105. India. Abstract Goto et al [2] developed the optimal braking effect Vacuum brakes are first used in place of and feel for the brake master cylinder for the heavy the air brake in railway locomotives. This vehicles. In this, braking effect was enhanced during braking system uses a vacuum pump for creating a vacuum failure condition by operating the smaller vacuum in the brake pipe. The integral bore. Thus, the vacuum failure detection and the construction of the brake cylinder uses this increase output pressure are performed vacuum reservoir for the application of brakes. mechanically. By this development, it has Nowadays most of the light vehicles are fitted contributed to the design of the optimal brake with vacuum-assisted hydraulic braking system system. where vacuum is created from the engine which Shaffer and Alexander [3] determine reduces the driver effort on foot pedal. whether the performance-based brake testing The vacuum braking system was technologies can improve the safety of the highways modified from above said reasons and the same and roadways through more effective or efficient was tested for implementation in both light and inspections of brakes of the road commercial heavy vehicles. -
Recovering Railroad Diesel-Electric Locomotive Dynamic Brake Energy
RECOVERING RAILROAD DIESEL-ELECTRIC LOCOMOTIVE DYNAMIC BRAKE ENERGY BY TRAVIS D. PAINTER B.S., University of Illinois at Urbana-Champaign, 2004 THESIS Submitted in partial fulfillment for the requirements for the degree of Master of Science in Civil Engineering in the Graduate College of the University of Illinois at Urbana-Champaign, 2006 Urbana, Illinois ii ABSTRACT RECOVERING RAILROAD DIESEL-ELECTRIC LOCOMOTIVE DYNAMIC BRAKE ENERGY Travis D. Painter, M.S. Department of Civil and Environmental Engineering University of Illinois at Urbana-Champaign Christopher P.L. Barkan, Ph.D., Advisor As fuel costs and environmental impacts assume greater importance to railways, so does the importance of options for increased energy efficiency and emissions reduction. A study was conducted on the potential recovery of dynamic brake energy from diesel-electric locomotives in North American freight service. If feasible, such as system could conserve fuel and reduce the environmental impact of railway operations. Using computer simulations (Train Energy Model) and locomotive event recorder data, estimations were made of the energy that could be recovered from dynamic brake use. In addition, the differences between the results of the computer simulations with respect to the actual events recorded were examined in order to evaluate how well the model simulates an engineer's operation of locomotives and provide guidance for future improvements to the simulation model. A case study of the energy recovery potential for a Class 1 railroad operating on an 81-mile route over a major mountain pass in North America was conducted. The route analyzed has two characteristics that make it a good candidate for studying energy recovery potential and possible pollution prevention benefits. -
F (- Ayaaaaaay Los 44 RW-44 OO U.S
||||IIII USOO5586812A United States Patent (19) 11 Patent Number: 5,586,812 Kanjo et al. 45 Date of Patent: Dec. 24, 1996 54) RAILWAY BRAKING APPARATUS 56 References Cited (75) Inventors: Wajih Kanjo, Lockport, Ill., Eric U.S. PATENT DOCUMENTS Smith, Burlington, Canada, Thomas J. 3,891,277 6/1975 Cope ..................................... 303f68 X Demoise, Export, Pa.; Michael Girotti, 4,746,171 5/1988 Englic .................................... 303189 X Thorold; Thomas McCabe, Dorval, 5,118,165 6/1992 Latvala .................................. 303/71 X both of Canada; Charles B. Fessler, Lancaster, Pa.; Scott Natschke, Primary Examiner Peter M. Poon Kankakee, Ill. Attorney, Agent, or Firm-James Ray & Associates (73) Assignee: Westinghouse Air Brake Company, (57) ABSTRACT Wilmerding, Pa. Apparatus for indicating the condition of hand brakes on railway cars and for applying and releasing railway car (21) Appl. No.: 477,470 parking or hand brakes automatically in response to prede 22 Fed: Jun. 7, 1995 termined conditions including movement of a train, wayside Conditioning apparatus, wayside operating mechanism, a Related U.S. Application Data signal controlled by an operator and performance of prede termined railway operating procedures, such as completion 62 Division of Ser. No. 278,937, Jul 22, 1994. of an air brake test procedure. The apparatus may respond to mechanical, electrical and electronic signals and may oper 51 Int, C. r................. B60T 13/00 ate on pneumatic or electric power provided from the service 52 U.S. Cl. ................................ 303/7; 303/9.76; 303/15; airbrake system of a train or from a source of power outside 303/20, 303/71; 188/170 of such air brake system. -
Modelica Library for the Systems Engineering of Railway Brakes
Modelica library for the systems engineering of railway brakes Marc Ehret Institute of System Dynamics and Control, German Aerospace Center, Germany, [email protected] Abstract content of electronic and software components, systems engineering has become a wide spread and important pro- This work outlines the role of system simulation for the cedure in product development (INCOSE, 2015). development process of railway brakes. The principles of In the context of systems engineering, computer based systems engineering motivate the use of computer based system simulation is a powerful tool since it supports de- simulation in order to enhance the understanding of sys- signers to understand the behavior of systems in design tems and to verify the behavior of systems in early de- stages where an experimental analysis is not feasible. Fur- sign phases. For this reason, the Modelica library "Vir- thermore, it allows engineers to check their own thinking, tual Train Brakes" is presented which enables engineers to to analyze alternatives and capabilities of the system and generate simulation models of railway brakes and to per- to communicate their concept to others (INCOSE, 2015) form system simulations during different phases of the de- (Mittal et al., 2017). Modelica is a well suitable modeling velopment process. By modeling and simulating the brake language to generate models of multi-physical technical systems of a passenger and a freight train, the capability of systems, such as railway brake systems and to study their the library is demonstrated and further investigations are physical behavior. motivated. Keywords: Railway Brakes, Systems Engineering, Multi- The goal of this work is to develop the concept of a Level Models, Variant Models, Generic Models Modelica library which provides an environment for the application of system simulation throughout the entire de- 1 Introduction velopment process of railway brakes. -
Evaluation of Current Trends of High Speed Trains Brake System
ADDIS ABABA UNIVERSITY ADDIS ABABA INSTITUTE OF TECHNOLOGY SCHOOL OF MECHANICAL AND INDUSTRIAL ENGINEERING Evaluation of Current Trends of High Speed Trains Brake System A thesis Submitted to The school of Graduate studies Addis Ababa University in partial fulfillment of the requirements for the degree of Masters of Science in Rolling Stock Engineering under mechanical engineering By Oumer Mohammed Advisor Dr. Ing. Demise Alemu Co-Advisor Ato Tsegaye Feleke August, 2014 DECLARATION I, the undersigned, declare that this thesis work is my original work, has not been presented for a degree in this or any other universities, and all sources of materials used for the thesis work have been fully acknowledged. Oumer Mohammed _______________ Name Signature Place: Addis Ababa ____________________ Date of submission This thesis has been submitted for examination with my approval as a university advisor. 1. Dr. Ing. Demise Alemu _______________ Advisor Signature 2. Ato Tsegaye Feleke ________________ Co-advisor Signature ADDIS ABABA UNIVERSITY SCHOOL OF GRADUATE STUDIES Evaluation of Current Trends of High Speed Trains Brake System By Oumer Mohammed Addis Ababa Institute of Technology Approval By Board of Examiners Dr. Birhanu Besha ______________ Head, Railway Center Signature Dr. Ing. Demise Alemu ______________ Advisor Signature Ato Tsegaye Feleke ______________ Co-advisor Signature Ato Fasil G. ______________ Internal Examiner Signature Dr. Daniel Tilahun ______________ External Examiner Evaluation Of Current Trends of High Speed Trains Brake System Acknowledgments First and foremost, I would like to thank my advisor and co-advisor Dr. Ing. Demise Alemu and Ato Tsegaye Feleke for their rich source of ideas, practical insight and support throughout the entire research. -
ON MAGNETIC PULLING FORCE in LINEAR EDDY-CURRENT BRAKE Jacek SKOWRON Rail Vehicle Institute Cracow University of Technology Poland, PL 31-155
PERIODICA POLYTECHNICA SER. TRANSP. ENG. VOL. 21, NO. 3, PP. 273-279 (1993) ON MAGNETIC PULLING FORCE IN LINEAR EDDY-CURRENT BRAKE Jacek SKOWRON Rail Vehicle Institute Cracow University of Technology Poland, PL 31-155 Received Nov. 10, 1992 Abstract In the paper, the mathematical model of the phenomena occurring in the rail eddy-current brake of a passenger train has been worked out. Braking forces between a moving brake shoe and motionless rail are investigated. The analysis is based on the solution to one dimensional vector potential in the inductor, brake air-gap and railway rail (rotor). 1. Introduction The interest in setting up new braking systems for passenger trains results from an increase of travelling speed of trains in which self-acting, friction, air brakes are not efficient enough. Introducing an additional brake be comes inevitable in this situation. The additional brake performs as a service brake within the range of high speed. Afterwards this task is ful filled by the pneumatic brake only when travelling speed is reducer below certain speed value. A rail-type eddy-current brake may serve for this pur pose. The rail-type eddy-current brake is constructed like the rail brake. The brake inductor, parallel to rail brake shoe, does not press on the rail, but it is installed at a short distance from it (several millimeters). In recent works [1 - 5] and [7] on eddy current brakes, only horizontal component of magnetic force acting on brake shoe has been considered, without taking into account vertical magnetic pulling force, treating it as inner force car ried by the wheel sets.