Utilisation of Sillimanite Minerals, Their Geology, and Potential Occurrences in Norway – an Overview
Total Page:16
File Type:pdf, Size:1020Kb
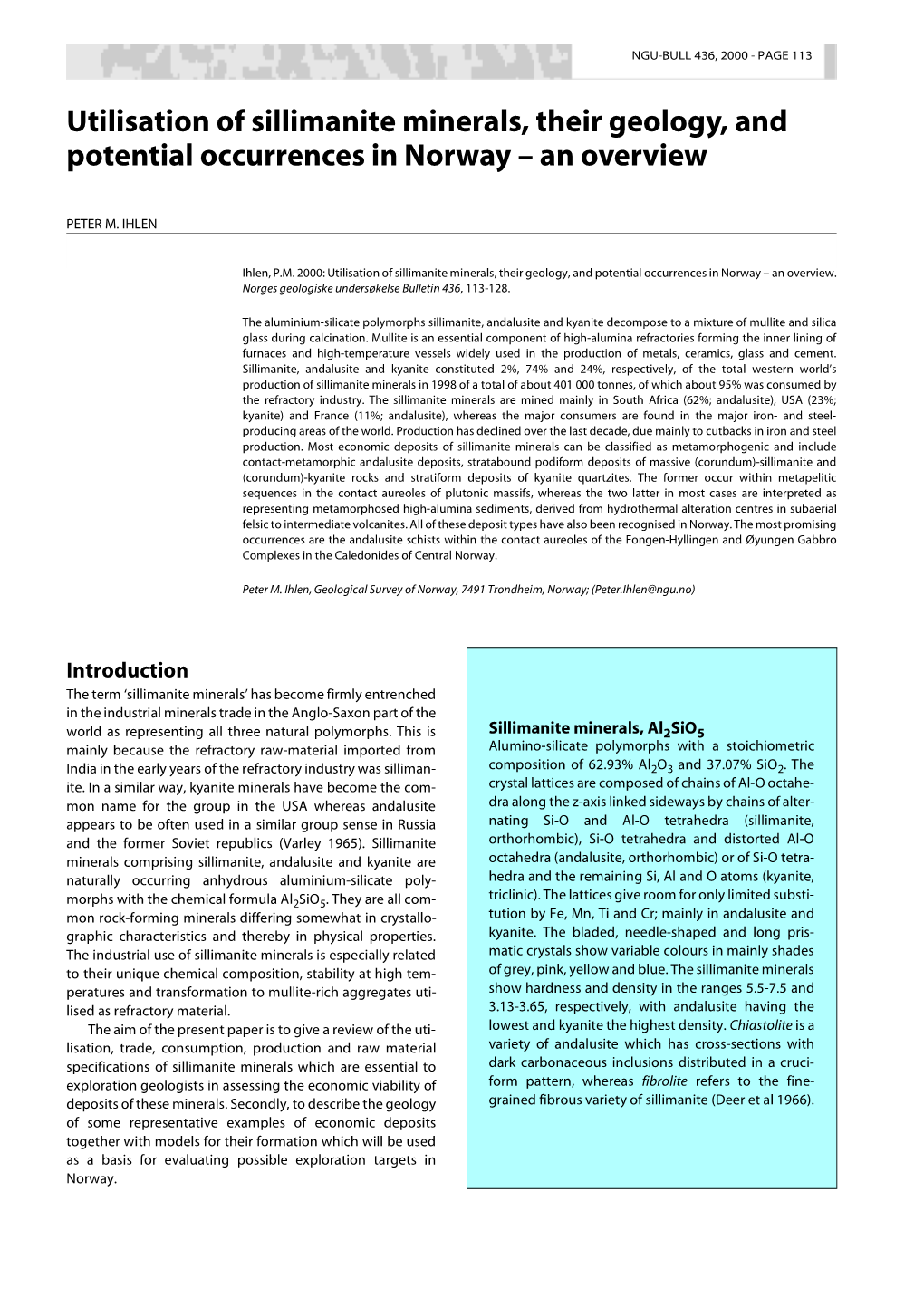
Load more
Recommended publications
-
CORDIERITE-GARNET GNEISS and ASSOCIATED MICRO- CLINE-RICH PEGMATITE at STURBRIDGE, I,{ASSA- CHUSETTS and UNION, CONNECTICUTI Fnor B.Cnrbn, [
THE AMERICAN MINERALOGIST, VOL 47, IVLY AUGUST, 1962 CORDIERITE-GARNET GNEISS AND ASSOCIATED MICRO- CLINE-RICH PEGMATITE AT STURBRIDGE, I,{ASSA- CHUSETTS AND UNION, CONNECTICUTI Fnor B.cnrBn, [/. S. GeologicalSurttey, Washington,D. C. Aesrnacr Gneiss of argillaceous composition at Sturbridge, Massachusetts, and at Union, Connecticut, 10 miles to the south, consists of the assemblagebiotite-cordierite-garnet- magnetite-microcline-quartz-plagioclase-sillimanite. The conclusion is made that this assemblagedoes not violate the phase rule. The cordierite contains 32 mole per cent of Fe- end member, the biotite is aluminous and its ratio MgO: (MgOf I'eO) is 0.54, and the gar- net is alm6e5 pyr26.agro2.espe1.2.Lenses of microcline-quartz pegmatite are intimately as- sociated with the gneissl some are concordant, others cut acrossthe foliation and banding of the gneiss. The pegmatites also contain small amounts of biotite, cordierite, garnet, graphite, plagioclase, and sillimanite; each mineral is similar in optical properties to the corresponding one in the gneiss. It is suggestedthat muscovite was a former constituent of the gneiss at a lower grade of metamorphism, and that it decomposedwith increasing metamorphism, and reacted with quartz to form siliimanite in situ and at lerst part of the microcline of the gneiss and pegmatites These rocks are compared with similar rocks of Fennoscandia and Canada. INtnouucrroN Cordierite-garnet-sillimanitegneisses that contain microcline-quartz pegmatiteare found in Sturbridge,Massachusetts, and Union, Connecti- cut. The locality (Fig. 1) at Sturbridgeis on the south sideof the \{assa- chusettsTurnpike at the overpassof the New Boston Road; this is about 1 mile west of the interchangeof Route 15 with the Turnpike. -
Phase Evolution of Ancient and Historical Ceramics
EMU Notes in Mineralogy, Vol. 20 (2019), Chapter 6, 233–281 The struggle between thermodynamics and kinetics: Phase evolution of ancient and historical ceramics 1 2 ROBERT B. HEIMANN and MARINO MAGGETTI 1Am Stadtpark 2A, D-02826 Go¨rlitz, Germany [email protected] 2University of Fribourg, Department of Geosciences, Earth Sciences, Chemin du Muse´e 6, CH-1700 Fribourg, Switzerland [email protected] This contribution is dedicated to the memory of Professor Ursula Martius Franklin, a true pioneer of archaeometric research, who passed away at her home in Toronto on July 22, 2016, at the age of 94. Making ceramics by firing of clay is essentially a reversal of the natural weathering process of rocks. Millennia ago, potters invented simple pyrotechnologies to recombine the chemical compounds once separated by weathering in order to obtain what is more or less a rock-like product shaped and decorated according to need and preference. Whereas Nature reconsolidates clays by long-term diagenetic or metamorphic transformation processes, potters exploit a ‘short-cut’ of these processes that affects the state of equilibrium of the system being transformed thermally. This ‘short-cut’ is thought to be akin to the development of mineral-reaction textures resulting from disequilibria established during rapidly heated pyrometamorphic events (Grapes, 2006) involving contact aureoles or reactions with xenoliths. In contrast to most naturally consolidated clays, the solidified rock-like ceramic material inherits non-equilibrium and statistical states best described as ‘frozen-in’. The more or less high temperatures applied to clays during ceramic firing result in a distinct state of sintering that is dependent on the firing temperature, the duration of firing, the firing atmosphere, and the composition and grain-size distribution of the clay. -
Synthesis of Hexacelsian Barium Aluminosilicate by Film Boiling Chemical Vapour Process C
Synthesis of hexacelsian barium aluminosilicate by film boiling chemical vapour process C. Besnard, A. Allemand, P. David, Laurence Maillé To cite this version: C. Besnard, A. Allemand, P. David, Laurence Maillé. Synthesis of hexacelsian barium aluminosilicate by film boiling chemical vapour process. Journal of the European Ceramic Society, Elsevier, In press, 10.1016/j.jeurceramsoc.2020.02.021. hal-02494032 HAL Id: hal-02494032 https://hal.archives-ouvertes.fr/hal-02494032 Submitted on 28 Feb 2020 HAL is a multi-disciplinary open access L’archive ouverte pluridisciplinaire HAL, est archive for the deposit and dissemination of sci- destinée au dépôt et à la diffusion de documents entific research documents, whether they are pub- scientifiques de niveau recherche, publiés ou non, lished or not. The documents may come from émanant des établissements d’enseignement et de teaching and research institutions in France or recherche français ou étrangers, des laboratoires abroad, or from public or private research centers. publics ou privés. Synthesis of hexacelsian barium aluminosilicate by film boiling chemical vapour process C. Besnard1, A. Allemand1-2, P. David2, L. Maillé1* 1University of Bordeaux, CNRS, Safran, CEA, Laboratoire des Composites ThermoStructuraux (LCTS), UMR 5801, F-33600 Pessac 2CEA Le Ripault, F-37260, Monts * Corresponding author, email address: [email protected] Abstract An original oxide/oxide ceramic-matrix composite containing mullite-based fibers and a barium aluminosilicate matrix has been synthesized by the film boiling chemical vapour infiltration process. Alkoxides were used as liquid precursors for aluminum, silicon and barium oxides. The structure and microstructure of the oxide matrix were characterized by Scanning Electron Microscopy, Energy Dispersive Spectroscopy and X-ray diffraction. -
Synthetic Mullite Precursors: Preparation, Structure, and Transformation Behaviour
Synthetic Mullite Precursors: Preparation, Structure, and Transformation Behaviour Habilitationsschrift zur Erlangung der Lehrbefugnis für das Fachgebiet Materialwissenschaften an der Gemeinsamen Fakultät für Bergbau, Hüttenwesen und Maschinenwesen der Technischen Universität Clausthal vorgelegt von: Martin Schmücker Deutsches Zentrum für Luft- und Raumfahrt (DLR) Institut für Werkstoff-Forschung 51147 Köln 2003 2 Vorwort Die vorliegende Habilitationsschrift "Synthetic Mullite Precursors: Preparation, Structure, and Transformation Behaviour" basiert auf meinen Arbeitsschwerpunkten "Struktur nichtkristalliner Aluminiumsilikate" und "Frühstadien der Mullitbildung". Diese Themenbereiche habe ich -neben verschiedenen anderen Aktivitäten- während meiner 10-jährigen Tätigkeit im Institut für Werkstoff-Forschung des DLR konzeptionell entwickelt und kontinuierlich bearbeitet. Die Untersuchungen zur Struktur nichtkristalliner Aluminiumsilikate erfolgten zusammen mit internationalen Kooperationspartnern sowie im Rahmen des DFG-Sonderforschungsbereichs 408 (Anorganische Festkörper ohne Translationssysmmetrie, Univ. Bonn). Während diese Arbeiten überwiegend grundlagenorientiert waren, war der Hintergrund für meine Untersuchungen zur Mullitbildung stärker anwendungsbezogen: Der Einsatz von mullitbasierter Hochleistungskeramik z. B. für thermisch exponierte Bauteile im Bereich von Luftfahrt, Raumfahrt und Antriebstechnik setzt ein tieferes Verständnis der Mullitbildungsmechanismen voraus. Es zeigte sich, daß die Arbeiten zur Mullitbildung und zur Struktur -
Sodium Aluminium Silicate (Tentative)
SODIUM ALUMINIUM SILICATE (TENTATIVE) th Prepared at the 80 JECFA and published in FAO JECFA Monographs 17 (2015), superseding tentative specifications prepared at the 77th JECFA (2013) and published in FAO JECFA Monographs 14 (2013). An ADI 'not specified' for silicon dioxide and certain silicates was established at the 29th JECFA (1985). A PTWI of 2 mg/kg bw for total aluminium was established at the 74th JECFA (2011). The PTWI applies to all aluminium compounds in food, including food additives. Information required: Functional uses other than anticaking agent, if any, and information on the types of products in which it is used and the use levels in these products Data on solubility using the procedure documented in the “Compendium of Food Additives Specifications, Vol. 4, Analytical methods” Data on the impurities soluble in 0.5 M hydrochloric acid, from a minimum of five batches. If a different extraction and determination method is used, provide data along with details of method and QC data. Suitability of the analytical method for the determination of aluminium, silicon and sodium using the proposed “Method of assay” along with data, from a minimum of five batches, using the proposed method. If a different method is used, provide data along with details of the method and QC data. SYNONYMS Sodium silicoaluminate; sodium aluminosilicate; aluminium sodium silicate; silicic acid, aluminium sodium salt; INS No. 554 DEFINITION Sodium aluminium silicate is a series of amorphous hydrated sodium aluminium silicates with varying proportions of Na2O, Al2O3 and SiO2. It is manufactured by, precipitation process, reacting aluminium sulphate and sodium silicate. -
This Dissertation Has Been 62—2136 M Icrofilm Ed Exactly As Received GIELISSE, Peter Jacob M., 1934- INVESTIGATION of PHASE EQ
This dissertation has been 62—2136 microfilmed exactly as received GIELISSE, Peter Jacob M., 1934- INVESTIGATION OF PHASE EQUILIBRIA IN THE SYSTEM ALUMINA-BORON OXIDE-SILICA. The Ohio State University, Ph.D., 1961 M ineralogy University Microfilms, Inc., Ann Arbor, Michigan INVESTIGATION OP PHASE EQUILIBRIA IN THE SYSTEM ALUMINA-BORON OXIDE-SILICA DISSERTATION Presented in Partial Fulfillment of the Requirements for the Degree Doctor of Philosophy in the Graduate School of the Ohio State University By Peter Jacob M. Gielisse, M. S. The Ohio State University 1961 Approved by Adviser Department of Mineralogy ACKNOWLEDGMENTS The writer wishes to extend his sincere thanks to the many people without whose help the preparation of this dissertation would have been impossible. He is indebted in particular to his adviser, Dr. Wilfrid R. Foster, for his invaluable aid, advice and many kindnesses; to the other members of the faculty of the Department of Mineral ogy, Drs. Ernest G. Ehlers, Henry E. Wenden, and Rodney T Tettenhorst; and to his friend and colleague, Thomas J. Rockett. Acknowledgment is also made for financial support re ceived under contract No. AF 33(616)-3189, sponsored by Aeronautical Research Laboratories, Air Force Research Division, Wright Patterson Air Force Base, Ohio; as well as for aid received through a Mershon National Graduate Fellowship awarded to the writer by the Mershon Committee on Education in National Security for 1960-‘61'. It goes without saying that he is also most grate ful to his wife, Anna, for her excellent help and encour agement over the years. TABLE OF CONTENTS Page INTRODUCTION ...................................... -
Andalusite, 0.5 to 1 Meter ANDALUSITE Across, and This Grades Into a Zone of Andalusite Al2sio5 Crystals in the Slate (Snelgrove Et Al., 1944)
echelon pegmatites passes into a vein of fine- grained (10 to 30 mm) andalusite, 0.5 to 1 meter ANDALUSITE across, and this grades into a zone of andalusite Al2SiO5 crystals in the slate (Snelgrove et al., 1944). 2. Champion mine: As euhedral crystals to 5 cm One of three polymorphs of Al2SiO5 (the other two are kyanite and sillimanite), andalusite is partially altered to muscovite in quartz. On the primarily a constituent of medium-grade 36th level drift, 45 meters east of Number 7 shaft metamorphic rocks derived from shales. Also, it station: A body of massive andalusite in quartzite occurs very much less commonly as a constituent with chalcopyrite and muscovite, adjacent to a of a few rare pegmatites, some quartz veins, and large quartz vein localized along contact between aluminous hydrothermal replacement deposits. It Negaunee Iron Formation and Goodrich Quartzite is often strongly altered to muscovite. Northern (Babcock, 1966a, b). 3. Republic mine: With co- Peninsula. existing sillimanite in rocks adjacent to fayalitic Negaunee Iron Formation (olivine) (Haase and Klein, 1978). Also in a vein with beryl 300 paces east and 75 north of the western ¼ post of section 17, T46N, R29W. FROM: Robinson, G.W., 2004 Mineralogy of Michigan by E.W. Heinrich updated and revised: published by A.E. Seaman Mineral Museum, Houghton, MI, 252p. Figure 35: Andalusite crystals to 3 cm, coated with muscovite in quartz, from the Champion mine, Champion, Marquette County. A. E. Seaman Mineral Museum specimen No. DM 14850, Jeffrey Scovil photograph. Iron County: SW ¼ SE ¼ section 20, T42N, R3W, Lake Mary quadrangle: Found as 1 cm poikiloblasts in the Michigamme Slate with garnet, staurolite, sillimanite, and sericite (Bayley, 1959). -
Metamorphic and Metasomatic Kyanite-Bearing Mineral
Metamorphic and Metasomatic Kyanite-Bearing Mineral Assemblages of Thassos Island (Rhodope, Greece) Alexandre Tarantola, Panagiotis Voudouris, Aurélien Eglinger, Christophe Scheffer, Kimberly Trebus, Marie Bitte, Benjamin Rondeau, Constantinos Mavrogonatos, Ian Graham, Marius Etienne, et al. To cite this version: Alexandre Tarantola, Panagiotis Voudouris, Aurélien Eglinger, Christophe Scheffer, Kimberly Tre- bus, et al.. Metamorphic and Metasomatic Kyanite-Bearing Mineral Assemblages of Thassos Island (Rhodope, Greece). Minerals, MDPI, 2019, 10.3390/min9040252. hal-02932247 HAL Id: hal-02932247 https://hal.archives-ouvertes.fr/hal-02932247 Submitted on 7 Sep 2020 HAL is a multi-disciplinary open access L’archive ouverte pluridisciplinaire HAL, est archive for the deposit and dissemination of sci- destinée au dépôt et à la diffusion de documents entific research documents, whether they are pub- scientifiques de niveau recherche, publiés ou non, lished or not. The documents may come from émanant des établissements d’enseignement et de teaching and research institutions in France or recherche français ou étrangers, des laboratoires abroad, or from public or private research centers. publics ou privés. minerals Article Metamorphic and Metasomatic Kyanite-Bearing Mineral Assemblages of Thassos Island (Rhodope, Greece) Alexandre Tarantola 1,* , Panagiotis Voudouris 2 , Aurélien Eglinger 1, Christophe Scheffer 1,3, Kimberly Trebus 1, Marie Bitte 1, Benjamin Rondeau 4 , Constantinos Mavrogonatos 2 , Ian Graham 5, Marius Etienne 1 and Chantal Peiffert -
Transition from Staurolite to Sillimanite Zone, Rangeley Quadrangle, Maine
CHARLES V. GUIDOTTI Department of Geology and Geophysics, University of Wisconsin, Madison, Wisconsin 53706 Transition from Staurolite to Sillimanite Zone, Rangeley Quadrangle, Maine ABSTRACT GENERAL GEOLOGICAL SETTING Ordovician and Silurian to Devonian pelitic schist, conglomerate, quartzite, calc-silicate Study of pelitic schists in the Rangeley Figure 1 shows the location of the area granulite, and biotite schist. Post-tectonic, area, Maine, by means of petrographic, and a generalized geologic map of the shallow-dipping, adamellite sheets intrude x-ray, and electron-microprobe techniques southwestern third of the Rangeley quad- the metamorphosed strata. As illustrated in enables definition of the isogradic reaction rangle based upon Moench (1966, 1969, Figure 1, the isograds have a clear spacial relating the staurolite and lower sillimanite 1970a, 1970b, 1971). The rocks in this area relation to the distribution of the adamel- zones. The reaction is a discontinuous one consist of tightly folded, northeast-trending lites; but in a few cases, the adamellite and can be shown on an AFM projection as the tie line change from staurolite + chlorite to sillimanite 4- biotite. This topology change, in conjunction with the min- eralogical data provides the equation: Staur + Mg-Chte + Na-Musc + (Gam?) Sill + Bio + K-richer Muse + Ab + Qtz + H20. This reaction should result in a sharp isograd in the field but in fact is found to be spread out over a zone which is called the transition zone. It is proposed that this zene results from buffering of fH20 by means of the equation above. Buffering of fH.,o by continuous reactions also appears to be taking place in the lower sillimanite zone. -
Kyanite and Related Minerals
KYANITE AND RELATED MINERALS (Data in metric tons unless otherwise noted) Domestic Production and Use: In Virginia, one firm with integrated mining and processing operations produced an estimated 85,000 tons of kyanite worth $30 million from two hard-rock open pit mines and synthetic mullite by calcining kyanite. Two other companies, one in Alabama and another in Georgia, produced synthetic mullite from materials mined from four sites; each company sourced materials from one site in Alabama and one site in Georgia. Synthetic mullite production data are withheld to avoid disclosing company proprietary data. Commercially produced synthetic mullite is made by sintering or fusing such feedstock materials as kyanite, kaolin, bauxite, or bauxitic kaolin. Natural mullite occurrences typically are rare and not economical to mine. Of the kyanite-mullite output, 90% was estimated to have been used in refractories and 10% in other uses, including abrasive products, such as motor vehicle brake shoes and pads and grinding and cutting wheels; ceramic products, such as electrical insulating porcelains, sanitaryware, and whiteware; foundry products and precision casting molds; and other products. An estimated 60% to 70% of the refractory use was by the iron and steel industries, and the remainder was by industries that manufacture cement, chemicals, glass, nonferrous metals, and other materials. Andalusite was commercially mined from an andalusite-pyrophyllite-sericite deposit in North Carolina and processed as a blend of primarily andalusite for use -
Geologic Map of the Southern Ivrea-Verbano Zone, Northwestern Italy
•usGsscience for a changing world Geologic Map of the Southern Ivrea-Verbano Zone, Northwestern Italy By James E. Quick,1 Silvano Sinigoi,2 Arthur W. Snoke,3 Thomas J. Kalakay,3 Adriano Mayer,2 and Gabriella Peressini2·4 Pamphlet to accompany Geologic Investigations Series Map I- 2776 1U. S. Geological Survey, Reston, VA 20192- 0002. 2Uni versita di Trieste, via Weiss 8, 341 27 Trieste, ltalia. 3Uni versity of Wyoming, Larami e, WY 8207 1- 3006. 4Max-Planck-lnstitut ft.ir Chemi e, J.J. Becherweg 27, 55 128 Mainz, Germany. 2003 U.S. Department of the Interi or U.S. Geological Survey COVER: View of the Ponte della Gula, an ancient bridge spanning the Torrente Mastellone approximately 2 kilometers north of the village of Varallo. Diorite of Valsesia crops out beneath the bridge. Photograph by ADstudia, Silvana Ferraris, photographer, Pizza Calderini, 3-13019 Varallo Sesia ([email protected]) INTRODUCTION REGIONAL SETTING The intrusion of mantle-derived magma into the deep conti The Ivrea-Verbano Zone (fig. 1) is a tectonically bounded sliver nental crust, a process commonly referred to as magmatic of plutonic and high-temperature, high-pressure metamorphic underplating, is thought to be important in shaping crustal com rocks in the southern Alps of northwestern Italy (Mehnert, position and structure. However, most evidence for this process 1975; Fountain, 1976). To the northwest, it is faulted against is indirect. High P-wave velocities and seismic-reflection profiles the basement of the Austro-Alpine Domain by the lnsubric Line, reveal that much of the deep continental crust is dense and a major suture zone that separates the European and Apulian strongly layered, consistent with the presence of layered mafic plates (Schmid and others, 1987; Nicolas and others, 1990). -
Control of Material Transport and Reaction Mechanisms by Metastable Mineral Assemblages: an Example Involving Kyanite, Sillimanite, Muscovite and Quartz
Fluid-Mineral Interactions: A Tribute to H. P. Eugster © The Geochemical Society, Special Publication No.2, 1990 Editors: R. J. Spencer and I-Ming Chou Control of material transport and reaction mechanisms by metastable mineral assemblages: An example involving kyanite, sillimanite, muscovite and quartz C. T. FOSTER,JR. Geology Department, University ofIowa, Iowa City, Iowa 52242, U.S.A. Abstract-Metastable mineral assemblages strongly influence reaction mechanisms and material transport when a new mineral grows in a metamorphic rock. The effects exerted by the metastable assemblages on the reactions that take place when sillimanite grows in a kyanite-bearing rock are examined using metastable elements of activity diagrams and irreversible thermodynamic principles. The results show that a commonly inferred reaction mechanism, where muscovite assists in the growth of sillimanite at the expense of kyanite, is a consequence of material transport constraints imposed by a metastable mineral assemblage in the matrix that separates growing sillimanite from dissolving kyanite. INTRODucnON pressures and temperatures represented by points I, II, and III (Fig. la) is shown in Fig. lb. ONEOFTHEPRIMARYcontrols on mineral textures Sillimanite nuclei first form in sites in the rock that develop during metamorphism is the distri- with the lowest activation energy for nucleation of bution of minerals in a rock at the time when a sillimanite. Under many metamorphic conditions, new mineral nucleates. The distribution of the new the low energy sites for sillimanite nucleation in mineral is strongly influenced by the abundance pelites appear to be in micas, because this is where and location of other minerals with favorable nu- sillimanite is commonly first observed with in- cleation sites for it.