The Effect of the Environment on the Corrosion Products and Corrosion Rates on Gas Transmission Pipelines
Total Page:16
File Type:pdf, Size:1020Kb
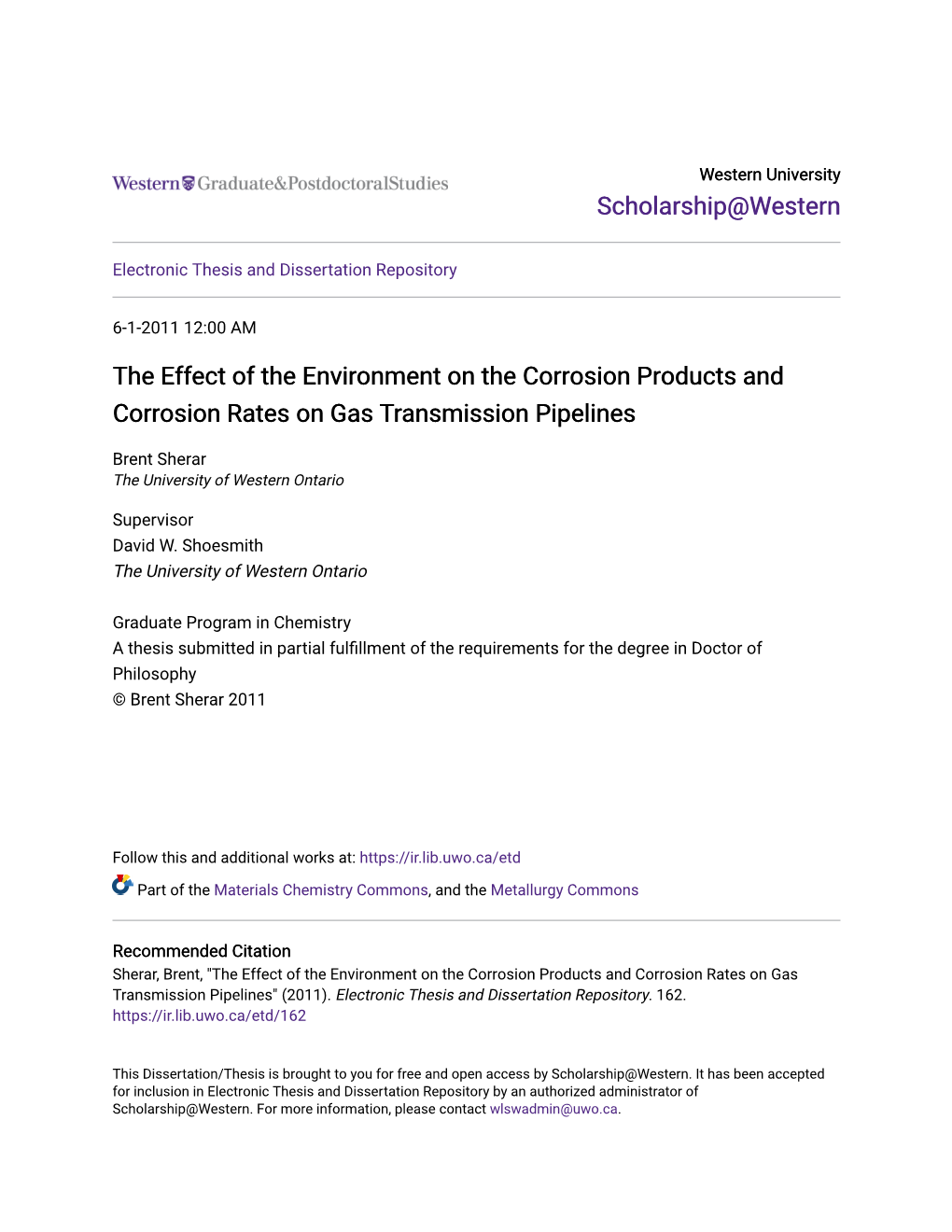
Load more
Recommended publications
-
Annual Report 2015 / Institute for Nuclear Waste Disposal. (KIT
KIT SCIENTIFIC REPOrts 7725 Annual Report 2015 Institute for Nuclear Waste Disposal Institut für Nukleare Entsorgung H. Geckeis, M. Altmaier, S. Fanghänel (eds.) H. Geckeis, M. Altmaier, S. Fanghänel (eds.) Annual Report 2015 Institute for Nuclear Waste Disposal Institut für Nukleare Entsorgung Karlsruhe Institute of Technology KIT SCIENTIFIC REPORTS 7725 Annual Report 2015 Institute for Nuclear Waste Disposal Institut für Nukleare Entsorgung by H. Geckeis, M. Altmaier, S. Fanghänel (eds.) Report-Nr. KIT-SR 7725 The Institute for Nuclear Waste Disposal, INE, (Institut für Nukleare Entsorgung) belongs to the KIT Energy Center. The KIT Energy Center with its 1100 employees is one of the largest energy research centers in Europe. It bundels the energy research activities of the KIT, the merger of the former Forschungszentrum Karlsruhe and Universität Karlsruhe and reknown cooperation partners. By this, it crosses the lines between disciplines and combines fundamental and applied research in all relevant energies for industry, household, service and mobility. The involved institutes and research groups conduct the research work on their own authority. The joining of subjects, the interdisciplinary collaboration of scientists, and the common use of high-end devices and installations, develops a new quality of research and teaching. The KIT Energy Center develops solutions in energy technology from a single source and acts as a highly valuable consultancy institution for politics, business, and society in all questions of energy. (http://www.energy.kit.edu/) Impressum Karlsruher Institut für Technologie (KIT) KIT Scientific Publishing Straße am Forum 2 D-76131 Karlsruhe KIT Scientific Publishing is a registered trademark of Karlsruhe Institute of Technology. -
A Review on Iron Oxide‐Based Nanoarchitectures for Biomedical
DOI: 10.1002/smtd.201800512 Article type: Review A Review on Iron Oxide-Based Nanoarchitectures for Biomedical, Energy Storage, and Environmental Applications Shunsuke Tanaka, Yusuf Valentino Kaneti*, Ni Luh Wulan Septiani, Shi Xue Dou, Yoshio Bando, and Md. Shahriar A. Hossain, Jeonghun Kim, and Yusuke Yamauchi* S. Tanaka, Dr. Y. V. Kaneti, Prof. Y. Bando International Research Center for Materials Nanoarchitectonics (WPI-MANA), National Institute for Materials Science (NIMS), 1-1 Namiki, Tsukuba, Ibaraki 305-0044, Japan E-mail: [email protected] N. L. W. Septiani Department of Engineering Physics and Research Center for Nanoscience and Nanotechnology, Bandung Institute of Technology, 10 Ganesha Street, Bandung 40132, Indonesia S. Tanaka, Prof. S. X. Dou, Prof. Y. Bando Australian Institute of Innovative Materials (AIIM), University of Wollongong, North Wollongong, New South Wales 2500, Australia Dr. M. S. A. Hossain School of Chemical Engineering and School of Mechanical & Mining Engineering, Faculty of Engineering, Architecture and Information Technology (EAIT), The University of Queensland, Brisbane, QLD 4072, Australia Dr. J. Kim, Prof. Y. Yamauchi This is the author manuscript accepted for publication and has undergone full peer review but has not been through the copyediting, typesetting, pagination and proofreading process, which may lead to differences between this version and the Version of Record. Please cite this article as doi: 10.1002/smtd.201800512. This article is protected by copyright. All rights reserved. School of Chemical Engineering and School of Mechanical & Mining Engineering, Faculty of Engineering, Architecture and Information Technology (EAIT), The University of Queensland, Brisbane, QLD 4072, Australia E-mail: [email protected] Prof. -
Investigation of Steel Corrosion in MX80 Bentonite at 120°C
Investigation of steel corrosion in MX80 bentonite at 120°C Hélène Lotz, Charly Carrière, Christian Bataillon, Emmanuel Gardes, Isabelle Monnet, Eddy Foy, Michel Schlegel, James Dynes, Delphine Neff, Florence Mercier-Bion, et al. To cite this version: Hélène Lotz, Charly Carrière, Christian Bataillon, Emmanuel Gardes, Isabelle Monnet, et al.. In- vestigation of steel corrosion in MX80 bentonite at 120°C. Materials and Corrosion / Werkstoffe und Korrosion, Wiley-VCH Verlag, 2021, 71 (1-2), pp.120-130. 10.1002/maco.202011777. cea-02931494 HAL Id: cea-02931494 https://hal-cea.archives-ouvertes.fr/cea-02931494 Submitted on 11 Dec 2020 HAL is a multi-disciplinary open access L’archive ouverte pluridisciplinaire HAL, est archive for the deposit and dissemination of sci- destinée au dépôt et à la diffusion de documents entific research documents, whether they are pub- scientifiques de niveau recherche, publiés ou non, lished or not. The documents may come from émanant des établissements d’enseignement et de teaching and research institutions in France or recherche français ou étrangers, des laboratoires abroad, or from public or private research centers. publics ou privés. Page 1 of 22 1 2 3 Title: Investigation of steel corrosion in MX80 bentonite at 120°C 4 5 6 Running title: Steel corrosion in MX80 bentonite at 120°C 7 8 Hélène Lotz1, Charly Carrière1, Christian Bataillon2, Emmanuel Gardes3, Isabelle Monnet3, 9 1 4 5 1 1 10 Eddy Foy , Michel L. Schlegel , James J. Dynes , Delphine Neff , Florence Mercier , 11 Philippe Dillmann1 12 13 14 1Université -
Surface Charge and Growth of Sulphate and Carbonate Green Rust in Aqueous Media
Available online at www.sciencedirect.com Geochimica et Cosmochimica Acta 108 (2013) 141–153 www.elsevier.com/locate/gca Surface charge and growth of sulphate and carbonate green rust in aqueous media Romain Guilbaud a,⇑,1, Maggie L. White b, Simon W. Poulton a,1 a School of Civil Engineering and Geosciences, Newcastle University, Newcastle Upon Tyne NE1 7RU, UK b School of Chemical Engineering and Advanced Materials, Newcastle University, Newcastle Upon Tyne NE1 7RU, UK Received 16 March 2012; accepted in revised form 16 January 2013; available online 8 February 2013 Abstract We report the first determination of the point of zero charge of sulphated and carbonated green rust particles. Green rust has been recognised as a prevalent mineral in environments such as hydromorphic soils, groundwaters and anoxic Fe(II)-rich water bodies, and the evolution of its net surface charge with pH has direct implications for the uptake of contaminants, met- als and nutrients in such settings. We find that the surface of both sulphated and carbonated green rust is positively charged at pH < 8.3, whereas it is negatively charged at pH > 8.3. Thus, alkaline settings will promote enhanced adsorption of metallic cations. However, the behaviour of ionic species surrounding green rust is more complicated than that predicted by simple pH-dependent adsorption, as our experiments suggest that green rust likely grows via dissolution–reprecipitation during Ost- wald-ripening. This implies that adsorbed species are potentially subject to repetitive steps of release into solution, re-adsorp- tion and co-precipitation during particle growth. The growth rate of green rust particles is highest within the first 50 min of aging, and appears to decrease towards an asymptote after 200 min, suggesting that particle growth controls on the uptake of dissolved species will be most important during the early steps of green rust growth. -
Experiments and Numerical Model Studies on Interfaces Work Package ACED
Deliverable D2.5: Experiments and numerical model studies on interfaces Work Package ACED The project leading to this application has received funding from the European Union’s Horizon 2020 research and innovation programme under grant agreement No 847593. http://www.ejp-eurad.eu/ EURAD Deliverable D2.5 – Experiments and numerical model studies on interfaces Document information Project Acronym EURAD Project Title European Joint Programme on Radioactive Waste Management Project Type European Joint Programme (EJP) EC grant agreement No. 847593 Project starting / end date 1st June 2019 – 30 May 2024 Work Package No. 2 Work Package Title Assessment of Chemical Evolution of ILW and HLW Disposal Cells Work Package Acronym ACED Deliverable No. D2.5 Deliverable Title Experiments and numerical model studies on interfaces Lead Beneficiary FZJ Contractual Delivery Date M5 Actual Delivery Date 12/05/2021 Type Report Dissemination level PU Authors Guido Deissmann (FZJ), Naila Ait Mouheb (FZJ), Christelle Martin (Andra), Maria J. Turrero (CIEMAT), Elena Torres (CIEMAT), Bruno Kursten (SCK CEN), Eef Weetjens (SCK CEN), Diederik Jacques (SCK CEN), Jaime Cuevas (UAM), Javier Samper (UDC), Luis Montenegro (UDC), Markku Leivo (VTT), Mervi Somervuori (VTT), Leena Carpen (VTT) To be cited as: Deissmann G., Ait Mouheb N., Martin C., Turrero, M.J., Torres, E., Kursten, B., Weetjens, E., Jacques, D., Cuevas, J., Samper, J., Montenegro, L., Leivo, M., Somervuori, M., Carpen, L. (2021): Experiments and numerical model studies on interfaces. Final version as of 12.05.2021 of deliverable D2.5 of the HORIZON 2020 project EURAD. EC Grant agreement no: 847593. Disclaimer All information in this document is provided "as is" and no guarantee or warranty is given that the information is fit for any particular purpose. -
Is Copper Immune to Corrosion When in Contact with Water
Author: Digby D. Macdonald Samin Sharifi -Asl George R. Engelhardt Mirna Urquidi-Macdonald Research 2012:11Issues in the corrosion of copper in a Swedish high level nuclear waste repository Report number: 2012:11 ISSN: 2000-0456 Available at www.stralsakerhetsmyndigheten.se SSM perspective Background The KBS-3 repository concept developed by SKB for disposal of spent nuclear fuel is based on a multi barrier principle for isolation of the fuel and to delay any escaping radionuclides. The concept is based on three barriers; copper canister, bentonite buer and granitic bedrock. The copper canister will in this respect work as a corrosion barrier and completely isolate the spent nuclear fuel from the surroundings until failure of the 5 cm thick copper canister by either corrosion or mecha- nical loads occurs. In order to review the license application for spent nuclear fuel it is im- portant that all corrosion mechanisms that can occur in the repository are understood in detail. The objectives for research by SSM are in this respect to maintain and develop knowledge at SSM and in the research community, in order to conduct a comprehensive and eective review of the license application for a spent nuclear fuel repository submitted by SKB. This report covers research result obtained during 2011 in an ongoing research work planned to continue to end of 2013. Objectives The objective with this research project was to increase knowledge in the area of copper corrosion in the planned repository environment and obtain information on how copper corrosion evolves during the assess- ment period of 100 000 years. -
An Introduction to Corrosion Science and Engineering FOURTH EDITION
CORROSION AND CORROSION CONTROL An Introduction to Corrosion Science and Engineering FOURTH EDITION R. Winston Revie Senior Research Scientist CANMET Materials Technology Laboratory Natural Resources Canada Herbert H. Uhlig Former Professor Emeritus Department of Materials Science and Engineering Massachusetts Institute of Technology A JOHN WILEY & SONS, INC., PUBLICATION CORROSION AND CORROSION CONTROL CORROSION AND CORROSION CONTROL An Introduction to Corrosion Science and Engineering FOURTH EDITION R. Winston Revie Senior Research Scientist CANMET Materials Technology Laboratory Natural Resources Canada Herbert H. Uhlig Former Professor Emeritus Department of Materials Science and Engineering Massachusetts Institute of Technology A JOHN WILEY & SONS, INC., PUBLICATION Copyright © 2008 by John Wiley & Sons, Inc. All right reserved Published by John Wiley & Sons, Inc., Hoboken New Jersey Published simultaneously in Canada No part of this publication may be reproduced, stored in a retrieval system, or transmitted in any form or by any means, electronic, mechanical, photocopying, recording, scanning, or otherwise, except as permitted under Section 107 or 108 of the 1976 United States Copyright Act, without either the prior written permission of the Publisher, or authorization through payment of the appropriate per-copy fee to the Copyright Clearance Center, Inc., 222 Rosewood Drive, Danvers, MA 01923, (978) 750-8400, fax (978)750-4470, or on the web at www.copyright.com. Requests to the Publisher for permission should be addressed to the Permissions Department, John Wiley & Sons, Inc., 111 River Street, Hoboken, NJ 07030, (201) 748-6011, fax (201) 748-6008, or online at http://www.wiley.com/go/permission. Limit of Liability/Disclaimer of Warranty: While the publisher and author have used their best efforts in preparing this book, they make no representations or warranties with respect to the accuracy or completeness of the contents of this book and specifi cally disclaim any implied warranties of merchantability or fi tness for a particular purpose. -
Fate of Nitrogen During Submarine Groundwater Discharge Into Long Island North Shore Embayments a Dissertation Presented by Cait
Fate of Nitrogen during Submarine Groundwater Discharge into Long Island North Shore Embayments A Dissertation Presented by Caitlin Young to The Graduate School in Partial Fulfillment of the Requirements for the Degree of Doctor of Philosophy in Geosciences Stony Brook University December 2013 Copyright by Caitlin Young 2013 Stony Brook University The Graduate School Caitlin Young We, the dissertation committee for the above candidate for the Doctor of Philosophy degree, hereby recommend acceptance of this dissertation. Gilbert Hanson Distinguished Professor, Geosciences Michael Sperazza Professor, Geosciences Henry Bokuniewicz Professor, School of Marine and Atmospheric Sciences Robert Aller Professor, School of Marine and Atmospheric Sciences Kevin D. Kroeger Senior Research Scientist US Geological Survey Woods Hole Coastal & Marine Science Center This dissertation is accepted by the Graduate School Charles Taber Dean of the Graduate School ii Abstract of the Dissertation Fate of Nitrogen during Submarine Groundwater Discharge into Long Island North Shore Embayments by Caitlin Young Doctor of Philosophy in Geosciences Stony Brook University 2013 Long Island Sound experiences periods of hypoxia attributed to eutrophication, but the magnitude of nitrogen contributed to surface water via submarine groundwater discharge (SGD) entering Long Island’s north shore embayments is not well characterized. The coastal aquifer, where fresh groundwater mixes with saline coastal water is termed the subterranean estuary (STE). Advective flow combined with sharp salinity and dissolved oxygen gradients make the STE a zone of intense geochemical cycling. However, the fate of nitrogen during transit through Long island embayment STEs is not well understood, particularly how sediment heterogeneity influences nitrogen attenuation in discharge zones. -
Drag Strip 60 Percent Design) Elkhart, Indiana
963063 Revision 3, Addendum 2 Final Design Report Conrail Railyard Superfund Site (Drag Strip 60 Percent Design) Elkhart, Indiana Submission Date: January 30, 2015 Prepared by: AECOM 525 Vine Street, Suite 1800 Cincinnati, OH 45202 On behalf of: Settling Parties: American Premier Underwriters, and Norfolk Southern Railway Company AECOM 513.651.3440 tel 525 Vine Street, Suite 1800 877.660.7727 fax Cincinnati, Ohio 45202 www.aecom.com January 30, 2015 Mr. Timothy Drexler U.S. EPA, HSRL-6J 77 West Jackson Blvd. Chicago, IL 60604-3590 Subject: Revision 3, Addendum 2 Final Design (Drag Strip 60 Percent Design), and Response to EPA Comment Letter dated November 4, 2014 Second Remedial Design / Remedial Action Conrail Railyard Superfund Site Elkhart, Indiana Dear Mr. Drexler: On behalf of the Settling Parties, Norfolk Southern Railway Company (Norfolk Southern) and American Premier Underwriters (APU)1, AECOM2 is providing the referenced submittal, referred to as the Drag Strip 60 Percent Design, to the United States Environmental Protection Agency (EPA). The Drag Strip 60 Percent Design addresses EPA comments dated July 11, 2014. The Settling Parties previously responded to the July 11, 2014 EPA comments and developed a key element of the Drag Strip design in, “Response to EPA July 11, 2014 Comments, and Technical Memorandum: Intermediate Remediation Goal (IRG) Calculation, Conrail Railyard Superfund Site, Elkhart, Indiana,” dated September 19, 2014 (IRG Tech Memo). EPA provided comments dated November 4, 2014 regarding the Settling Parties’ IRG Tech Memo submittal. On December 3, 2014, EPA, Indiana Department of Environmental Management (IDEM), S.S. Papadopulos and Associates (SSPA), the Settling Parties, and AECOM discussed the EPA November 4, 2014 comments letter and the Settling Parties’ initial responses. -
Is Copper Immune to Corrosion When in Contact with Water and Aqueous Solutions?
t Strai sakerhets myndigheten Swedish Radiation Safety Authority Authors: Digby D. Macdonald Samin Sharifi-Asl Research Is Copper Immune to Corrosion When in Contact With Water and Aqueous Solutions? Report number: 2011:09 ISSN: 2000-0456 Available atwww.stralsakerhetsmyndigheten.se SSM perspective Background The KBS-3 concept implies that spent nuclear fuel is placed in copper canisters surrounded by clay and finally placed approximately 500 m down from surface into granitic bedrock, in order to isolate the spent nuclear fuel from humans and environment for very long time scales (i.e. millions of years). The concept is based on the multi-barrier principle, in this respect the barriers are the copper canister, clay material and finally the granitic bedrock. All barriers will work alone and together in order to retard the spent nuclear fuel to enter into the biosphere. In this report it is only degra dation of the first barrier, the copper canister that is considered. The mechanisms of copper corrosion in the planned repository for spent nuclear fuel according to the KBS-3 concept need to be fully understood in order to review the license application in an authoritative way. Copper as a canister material was chosen by SKB already 1978 in the KBS-2 report. The main reasons for selecting copper were 1) copper is thermodynamically immune in the presence of pure anoxic water, and 2) copper has sufficient mechanical strength to resist all plausible mechanical loads present in the repository. Thermodynamically, immunity of copper in pure anoxic water implies that copper will not corrode in the presence of pure anoxic water. -
Nanoscale 9: 12984-12995
Nanoscale View Article Online PAPER View Journal | View Issue Hard templating ultrathin polycrystalline hematite nanosheets: effectofnano-dimensiononCO2 to CO Cite this: Nanoscale, 2017, 9, 12984 conversion via the reverse water-gas shift reaction† Zachary S. Fishman, a Yulian He,a Ke R. Yang,b Amanda W. Lounsbury,a Junqing Zhu,c Thanh Minh Tran,a Julie B. Zimmerman,a Victor S. Batista*b and Lisa D. Pfefferle*a Understanding how nano-dimensionality impacts iron oxide based catalysis is central to a wide range of applications. Here, we focus on hematite nanosheets, nanowires and nanoparticles as applied to catalyze the reverse water gas shift (RWGS) probe reaction. We introduce a novel approach to synthesize ultrathin (4–7 nm) hematite nanosheets using copper oxide nanosheets as a hard template and propose a reaction mechanism based on density functional theory (DFT) calculations. Hematite nanowires and nanoparticles were also synthesized and characterized. H2 temperature programmed reduction (H2-TPR) and RWGS reactions were performed to glean insights into the mechanism of CO2 conversion to CO over the iron Received 17th May 2017, oxide nanomaterials and were compared to H2 binding energy calculations based on density functional Accepted 7th August 2017 theory. While the nanosheets did exhibit high CO2 conversion, 28% at 510 °C, we found that the iron DOI: 10.1039/c7nr03522e oxide nanowires had the highest CO2 conversion, reaching 50% at 750 °C under atmospheric pressure. rsc.li/nanoscale No products besides CO and H2O were detected. Introduction properties ideal for spintronics.10 Still left unstudied, though, is the undoped hematite nanosheet system, and how the pro- Hematite is a nontoxic, stable iron oxide composed of earth perties of the 2D material compares to its 0D and 1D abundant elements with a wide array of applications in water analogues. -
D2.8 First Results on the Thermodynamic Databases and Reactive Transport Models for Steel-Cement Interfaces
Deliverable 2.8: First results on the thermodynamic databases and reactive transport models for steel-cement interfaces at high temperature Work Package 2 The project leading to this application has received funding from the European Union’s Horizon 2020 research and innovation programme under grant agreement No 847593. http://www.ejp-eurad.eu/ EURAD Deliverable D2.8 – Thermodynamic database and model of steel-cement interfaces, 1st results Document information Project Acronym EURAD Project Title European Joint Programme on Radioactive Waste Management Project Type European Joint Programme (EJP) EC grant agreement No. 847593 Project starting / end date 1st June 2019 – 30 May 2024 Work Package No. 2 Work Package Title Assessment of Chemical Evolution of ILW and HLW Disposal Cells Work Package Acronym ACED Deliverable No. D2.8 Deliverable Title First results on the thermodynamic databases and reactive transport models for steel-cement interfaces at high temperature Lead Beneficiary IRSN Contractual Delivery Date August 2020 Actual Delivery Date February 2020 Type Report Dissemination level PU Authors Laurent De Windt (MINES ParisTech), George Dan Miron (PSI), Margit Fabian (MTA), Jules Goethals (Subatech, IMT Atlantique), Charles Wittebroodt (IRSN) To be cited as: De Windt L., Miron G. D., Fabian M., Goethals, J., Wittebroodt C. (2020): First results on the thermodynamic databases and reactive transport models for steel-cement interfaces at high temperature. Final version as of xx.xx.xxxx of deliverable D2.8 of the HORIZON 2020 project EURAD. EC Grant agreement no: 847593. Disclaimer All information in this document is provided "as is" and no guarantee or warranty is given that the information is fit for any particular purpose.