3 Reactive Multilayers
Total Page:16
File Type:pdf, Size:1020Kb
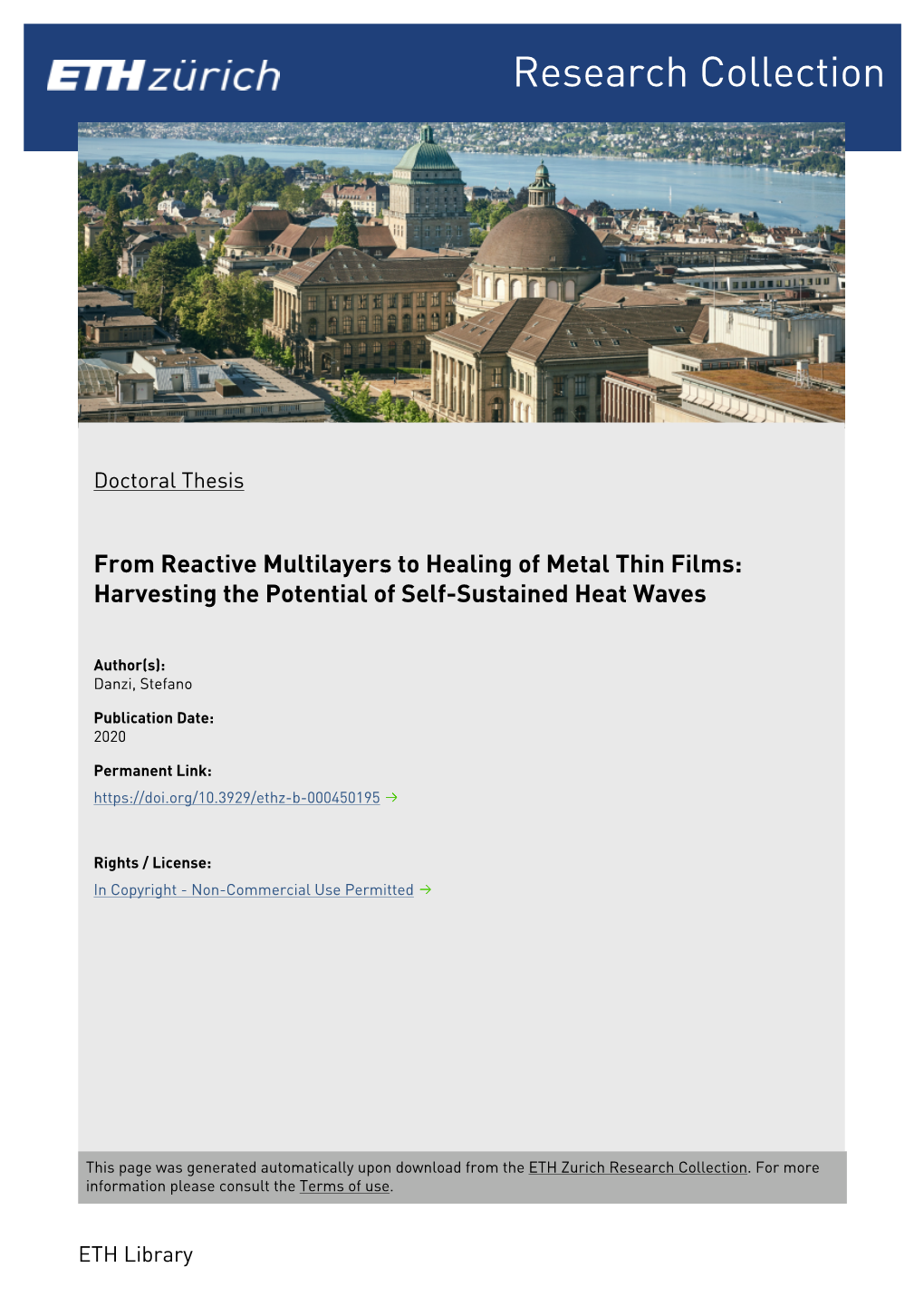
Load more
Recommended publications
-
Characterization of Impact Initiation of Aluminum-Based Intermetallic-Forming Reactive Materials
CHARACTERIZATION OF IMPACT INITIATION OF ALUMINUM-BASED INTERMETALLIC-FORMING REACTIVE MATERIALS A Thesis Presented to The Academic Faculty by Michael D. Tucker In Partial Fulfillment of the Requirements for the Degree Master of Science in Mechanical Engineering in the School of Mechanical Engineering Georgia Institute of Technology December 2011 CHARACTERIZATION OF IMPACT INITIATION OF ALUMINUM-BASED INTERMETALLIC-FORMING REACTIVE MATERIALS Approved by: Dr. Naresh Thadhani, Advisor School of Mechanical Engineering Georgia Institute of Technology Dr. Joe Cochran School of Mechanical Engineering Georgia Institute of Technology Dr. Antonia Antoniou School of Mechanical Engineering Georgia Institute of Technology Dr. Ken Gall School of Mechanical Engineering Georgia Institute of Technology Date Approved: August 2011 To all those who made a sacrifice of time, money, thoughts, prayers, and patience for me, and others like me. May I be a blessing to others as others have been to me and before me for all those after. To my family who I would do anything for, my parents, and to the memory of Uncle Willie and Uncle Lewis whom my family lost this year, and to my great-grandfather and greatest inspiration, Roy Nathaniel Tucker.... Papa, \I ain't dead yet" iii ACKNOWLEDGEMENTS First I would like to give honor to my Lord and Savior Jesus Christ for all the blessings that have been bestowed upon me, including the opportunity to further my education. I want to thank Dr. Thadhani for extending the opportunity to work and learn in his lab. I would like to thank my parents for their constant support of all my endeavors in life and for pushing me to be the man that I am today. -
Development of PVD-Coated and Nanostructured Reactive Multilayer Films
Seema Sen Development of PVD-coated and nanostructured reactive multilayer films Werkstofftechnik Aktuell Schriftenreihe aus dem Fakultätsübergreifenden Institut für Werkstofftechnik (IWT) an der TU Ilmenau Herausgegeben von Univ.-Prof. Dr. rer. nat. Peter Schaaf und Univ.-Prof. Dr.-Ing. Edda Rädlein Band 19 Die vorliegende Schriftenreihe "Werkstofftechnik Aktuell" berich- tet über aktuelle Forschungsergebnisse aus dem Institut für Werk- stofftechnik (IWT) der TU Ilmenau. Die ausgewählten Texte spiegeln die breit gefächerten materialwissenschaftlichen und werk- stofftechnischen Themen, die am IWT bearbeitet werden, wieder. Für weitere Informationen und Rückfragen können Sie sich gerne an das Institut (www.tu-ilmenau.de/wt) wenden oder das Institut persönlich besuchen. Über Ihre Anregungen, konstruktive Kritik und Ihre Kontaktaufnahme würden wir uns sehr freuen. Das IWT steht wissenschaftlichen Zusammenarbeiten stets aufgeschlossen gegenüber. Development of PVD-coated and nanostructured reactive multilayer films Seema Sen Universitätsverlag Ilmenau 2018 Impressum Bibliografische Information der Deutschen Nationalbibliothek Die Deutsche Nationalbibliothek verzeichnet diese Publikation in der Deutschen Nationalbibliografie; detaillierte bibliografische Angaben sind im Internet über http://dnb.d-nb.de abrufbar. Diese Arbeit hat der Fakultät für Elektrotechnik und Informationstechnik der Technischen Universität Ilmenau als Dissertation vorgelegen. Tag der Einreichung: 14. November 2017 1. Gutachter: Univ.-Prof. Dr. rer. nat. habil. Dr h.c. -
Download Author Version (PDF)
Nanoscale Accepted Manuscript This is an Accepted Manuscript, which has been through the Royal Society of Chemistry peer review process and has been accepted for publication. Accepted Manuscripts are published online shortly after acceptance, before technical editing, formatting and proof reading. Using this free service, authors can make their results available to the community, in citable form, before we publish the edited article. We will replace this Accepted Manuscript with the edited and formatted Advance Article as soon as it is available. You can find more information about Accepted Manuscripts in the Information for Authors. Please note that technical editing may introduce minor changes to the text and/or graphics, which may alter content. The journal’s standard Terms & Conditions and the Ethical guidelines still apply. In no event shall the Royal Society of Chemistry be held responsible for any errors or omissions in this Accepted Manuscript or any consequences arising from the use of any information it contains. www.rsc.org/nanoscale Page 1 of 41 Nanoscale Nanoscale REVIEW High Energetic Compositions Based on Functionalized Carbon Nanomaterials Received 00th November 2015, Qi-Long Yana, Michael Gozin†a, Feng-Qi Zhaob, Adva Cohena, Si-Ping Pangc Accepted 00th January 2016 DOI: 10.1039/x0xx00000x In recent years, research in the field of carbon nanomaterials (CNMs), such as fullerenes, expanded graphite (EG), carbon nanotubes (CNTs), graphene, and graphene oxide (GO), have been widely used in energy storages, electronics, catalysts, www.rsc.org/ biomaterials, as well as medical applications. Regarding energy storage, one of the most important research directions is the development of CNMs as carriers of energetic components by coating or encapsulation, thus forming safer advanced nanostructures with better performances. -
Mechanical Desensitization of an Al/WO3 Nanothermite by Means of Carbonaceous Coatings Derived from Carbohydrates
Journal of C Carbon Research Article Mechanical Desensitization of an Al/WO3 Nanothermite by Means of Carbonaceous Coatings Derived from Carbohydrates Pierre Gibot 1,* , Quentin Miesch 1, Arnaud Bach 1,2, Fabien Schnell 1, Roger Gadiou 2 and Denis Spitzer 1 1 Laboratoire des Nanomatériaux pour desSystèmes Sous Sollicitations Extrêmes (NS3E), CNRS-ISL-UNISTRA UMR 3208, Institut franco-allemand de recherches de Saint-Louis (ISL), 5 rue du Général Cassagnou, BP70034, 68301 Saint-Louis, France 2 Institut de Science des Matériaux de Mulhouse (IS2M), CNRS UMR 7361, Université de Haute Alsace (UHA), 15 rue Jean Starcky, BP2488, 68057 Mulhouse, France * Correspondence: [email protected]; Tel.: +33-(0)3-89-69-58-77 Received: 4 June 2019; Accepted: 26 June 2019; Published: 1 July 2019 Abstract: Nanothermites show great developmental promise in the near future in civilian, military and aerospace applications due to their tuneable reactive properties (ignition delay time, combustion velocity and pressure release). However, the high mechanical sensitivities of some of these energetic nanocomposites can make transportation and handling of them hazardous. Here, a mechanical desensitization (shock and friction) of an Al/WO3 nanothermite is successfully obtained by means of carbon adding through the pyrolysis of naturally occurring molecules (carbohydrates). The combustion behaviour of the carbon-based energetic mixtures were also evaluated and a respectable reactivity has been evidenced. Keywords: nanothermites; saccharides; carbon; desensitization; energetic nanocomposites 1. Introduction The mixtures of metal and oxide powders at the micro-scale, which are known as thermites, are interesting energetic composites for specific applications, such as in the ordnance domain. The reaction between both components is described as an exothermic oxidoreduction chemical reaction leading to a high adiabatic temperature [1]. -
Synthesis, Characterization and Performance Evaluation of Nano‑Energetic Composite
This document is downloaded from DR‑NTU (https://dr.ntu.edu.sg) Nanyang Technological University, Singapore. Synthesis, characterization and performance evaluation of nano‑energetic composite Tan, Meng Lu 2018 Tan, M. L. (2018). Synthesis, characterization and performance evaluation of nano‑energetic composite. Master's thesis, Nanyang Technological University, Singapore. https://hdl.handle.net/10356/82944 https://doi.org/10.32657/10220/47540 Downloaded on 11 Oct 2021 15:18:25 SGT SYNTHESIS, CHARACTERIZATION AND PERFORMANCE EVALUATION OF NANO-ENERGETIC COMPOSITE TAN MENG LU SCHOOL OF MATERIALS SCIENCE AND ENGINEERING 2019 SYNTHESIS, CHARACTERIZATION AND PERFORMANCE EVALUATION OF NANO-ENERGETIC COMPOSITE TAN MENG LU SCHOOL OF MATERIALS SCIENCE AND ENGINEERING A thesis submitted to the Nanyang Technological University in partial fulfilment of the requirement for the degree of Masters of Engineering 2019 Abstract Abstract Thermites belong to a class of energetic material comprising of a metal as a fuel and a metal oxide as the oxidizer. The research on nano-thermites has significantly emerged in the last two decades and novel ways to harness their energy with improved reactivity, reduced sensitivity and high stability remains highly desirable to date. In this work, Al/NiO nano-thermite system was studied due to their relatively gasless reaction. Gasless thermite reactions could offer potential in applications requiring little flow disturbances and vibrations. A novel self-assembly technique to promote better intermixing of the fuel-oxidizer system through surface functionalization with complimentary functional groups as well as the addition of an energetic polymer binder to reduce the sensitivity were studied. The heat release characteristics and reaction mechanism of Al/NiO nano-thermites were studied. -
Double Click on the Seminar Number to Jump to Th
Papers Published in the Proceedings of the International Pyrotechnics Seminars (double click on the Seminar number to jump to that location) 1 Estes Park, Colorado, USA 1968 2 Snowmass-at-Aspen Colorado, USA 1970 3 Colorado Springs, Colorado, USA 1972 4 Steamboat Village, Colorado, USA 1974 5 Vail, Colorado, USA 1976 6 Estes Park, Colorado, USA 1978 7 Vail, Colorado, USA 1980 8 Steamboat Springs, Colorado, USA 1982 9 Colorado Springs, Colorado, USA 1984 10 Karlsruhe, Germany 1985 11 Vail, Colorado, USA 1986 12 Juan les Pins, France 1987 13 Grand Junction, Colorado, USA 1988 14 Jersey, Channel Islands, UK 1989 15 Boulder, Colorado, USA 1990 16 Jönköping, Sweden 1991 17 Beijing, China 1991 18 Breckenridge, Colorado, USA 1992 19 Christchurch, New Zealand 1994 20 Colorado Springs, Colorado, USA 1994 21 Moscow, Russia 1995 22 Fort Collins, Colorado, USA 1996 23 Tsukuba, Japan 1997 24 Monterey, California, USA 1998 25 Brest, France 1999 26 Nanjing, Jiangsu, P.R.. China 1999 27 Grand Junction, Colorado, USA 2000 28 Adelaide, Australia 2001 29 Westminster, Colorado, USA 2002 30 Saint Malo, France 2003 31 Fort Collins, Colorado, USA 2004 32 Karlsruhe, Germany 2005 33 Fort Collins, Colorado, USA 2006 34 Beaune, France 2007 35 Fort Collins, Colorado, USA 2008 36 Rotterdam, The Netherlands 2009 37 Reims, France 2011 38 Denver, Colorado, USA 2012 39 Valencia, Spain 2013 1st Seminar 1968 index Estes Park, Colorado, USA page 1 Pyro research areas for further exploratory development. Hamrick J T 1 2 Colored smoke signals: castable compositions. Lane G A and Janowiak E 25 M 3 Ignition and output characteristics of pyrotechnics for electro-explosive 39 device applications. -
Study on Laser Beam Welding of Copper and Aluminum Joint
IOSR Journal of Mechanical and Civil Engineering (IOSR-JMCE) e-ISSN: 2278-1684,p-ISSN: 2320-334X PP. 65-74 www.iosrjournals.org Study on Laser beam Welding of Copper and Aluminum joint R.S. Chopde 1,2, S.P. Gadewar 1 , M.P. Khond3 , M.J . Rathod4 1(Department of Mechanical Engineering, M.E.S College of Engineering, S.P. Pune university, Pune India, 2(John Deere India Pvt. ltd, Pune India) 3(Department of Mechanical Engineering,College of Engineering, S.P. Pune University, India) 4(Department of Material science and Metallurgy, College of Engineering, Pune, India) Abstract: Aluminum and Copper has more significance in electrical and electronic application such as solar energy collectors or light weight electric motors and actuators. It combines comparably good thermal and electrical properties with attractive price and low material weight. However the main difficulty for widespread use of aluminum is the lack of reliable joining process to connect it with copper. The Intermetallic formation during welding of copper and aluminum are caused by large misalignment in physical properties and even more poor metallurgical affinity of both materials and therefore crack sensitivity and formation of brittle intermetallic phase during fusion welding. Wide range of materials can be welded by laser, especially the alloys that are normally difficult to weld by conventional welding. Since absorption of the laser power is crucial for melting, conductivity and reflectivity are important key factors for achieving better melting. In this effort we have investigated laser welding of aluminum and copper of 2 mm thick with literature studies in past. -
Synthesis and Characterization of Metal-Based Reactive Powders
New Jersey Institute of Technology Digital Commons @ NJIT Dissertations Electronic Theses and Dissertations Summer 8-31-2014 Synthesis and characterization of metal-based reactive powders Yasmine Aly New Jersey Institute of Technology Follow this and additional works at: https://digitalcommons.njit.edu/dissertations Part of the Chemical Engineering Commons Recommended Citation Aly, Yasmine, "Synthesis and characterization of metal-based reactive powders" (2014). Dissertations. 175. https://digitalcommons.njit.edu/dissertations/175 This Dissertation is brought to you for free and open access by the Electronic Theses and Dissertations at Digital Commons @ NJIT. It has been accepted for inclusion in Dissertations by an authorized administrator of Digital Commons @ NJIT. For more information, please contact [email protected]. Copyright Warning & Restrictions The copyright law of the United States (Title 17, United States Code) governs the making of photocopies or other reproductions of copyrighted material. Under certain conditions specified in the law, libraries and archives are authorized to furnish a photocopy or other reproduction. One of these specified conditions is that the photocopy or reproduction is not to be “used for any purpose other than private study, scholarship, or research.” If a, user makes a request for, or later uses, a photocopy or reproduction for purposes in excess of “fair use” that user may be liable for copyright infringement, This institution reserves the right to refuse to accept a copying order if, in its -
Hydrodynamical Analysis of Nanometric Aluminum/Teflon Deflagrations
Hydrodynamical Analysis of Nanometric Aluminum/Teflon Deflagrations BY SHAWN C. STACY, B.S.M.E. A THESIS IN MECHANICAL ENGINEERING Submitted to the Graduate Faculty of Texas Tech University in Partial Fulfillment of the Requirements for the Degree of MASTER OF SCIENCE IN MECHANICAL ENGINEERING Approved Michelle Pantoya Chairperson of the Committee Valery Levitas Brandon Weeks Accepted Fred Hartmeister Dean of the Graduate School May 2008 Texas Tech University, Shawn C. Stacy, May 2008 Acknowledgments I am exceptionally grateful to everyone that has helped me accomplish so much while at Texas Tech University. Specifically, I’m thankful for the opportunities and guidance of Dr. Michelle Pantoya has given me over the last two years. With her help, I have grown much as a researcher and I am more prepared for any challenges ahead of me. I would also like to thank Dr. Mark Grimson at the Texas Tech Imaging Center for helping me with the finer points of electron microscopy. Also, I would like to acknowledge Idaho National Laboratory for technical and financial assistance that was critical to this work. ii Texas Tech University, Shawn C. Stacy, May 2008 Table of Contents ACKNOWLEDGMENTS ................................................................................... II TABLE OF CONTENTS ................................................................................... III ABSTRACT .......................................................................................................... V LIST OF TABLES ............................................................................................. -
Development of a Bonding Concept for MOEMS Packaging: Reactive Nanocomposites
Development of a Bonding Concept for MOEMS Packaging: Reactive Nanocomposites Zur Erlangung des akademischen Grades eines Doktors der Ingenieurwissenschaften (Dr.-Ing.) bei der KIT-Fakultät für Maschinenbau des Karlsruher Instituts für Technologie (KIT) angenommene Dissertation von Dipl.-Ing. Matthias Peter Kremer Hauptreferent: Prof. Dr. Andreas E. Guber Korreferenten: Prof. Dr. Jan G. Korvink, Prof. Dr. Bernhard Wolf Prüfungsvorsitz: Prof. Dr.-Ing. Xu Cheng Tag der mündlichen Prüfung: 19.11.2018 KIT – Universität des Landes Baden-Württemberg und nationales Forschungszentrum in der Helmholtz-Gemeinschaft www.kit.edu This document is licensed under a Creative Commons Attribution- NoDerivatives 4.0 International License (CC BY-ND 4.0): https://creativecommons.org/licenses/by-nd/4.0/deed.en Für Julia und Emilie Die Liebe ist im Grunde die Kraft und die Macht, die allein das Leben lebenswert machen kann. (Konrad Adenauer) Acknowledgements This thesis is the outcome of my work at CTR Carinthian Tech Research AG during the last three years. It was a very nice time and I felt privileged about being able to live in such a wonderful surrounding as Villach, to work with great colleagues and pursuing my academic degree by a very renowned university in Germany. I want to thank a lot of people: First of all, I have to thank Prof. Dr.-Ing. Andreas E. Guber (Karlsruhe Institute of Technology – Institute of Microstructure Technology) for supervision and support- ing this work even from a distance, for helpful discussions and personal advice. I would like to thank Prof. Dr. Jan G. Korvink (Karlsruhe Institute of Technology – Institute of Microstructure Technology) and Prof. -
Combustion Synthesis in Nanostructured Reactive Systems ⇑ ⇑ Alexander S
Advanced Powder Technology xxx (2015) xxx–xxx Contents lists available at ScienceDirect Advanced Powder Technology journal homepage: www.elsevier.com/locate/apt Review paper Combustion synthesis in nanostructured reactive systems ⇑ ⇑ Alexander S. Mukasyan a,b, , Alexander S. Rogachev b,c, Singanahally ThippaReddy Aruna d, a Department of Chemical and Biomolecular Engineering, University of Notre Dame, Notre Dame, IN 46556, USA b Center of Functional Nano-Ceramics, National University of Science and Technology, ‘‘MISIS’’, Moscow 119049, Russia c Institute of Structural Macrokinetics and Materials Science, Russian Academy of Sciences, Chernogolovka 142432, Russia d Surface Engineering Division, Council of Scientific and Industrial Research-National Aerospace Laboratories, Bangalore 560 017, Karnataka, India article info abstract Article history: New classes of reactive systems that are characterized by nano-scale heterogeneity and possess extre- Received 17 September 2014 mely high reactivity, as compared to that for similar reactive systems with micro-scale heterogeneity, Received in revised form 23 March 2015 have attracted a vast attention of many researchers. The recent developments and trends in combustion Accepted 30 March 2015 science toward such ‘‘nano’’ reactive media are presented. These systems include mechanically induced Available online xxxx composite particles, sol–gels, super thermites and multilayer nano-foils. Various combustion-based applications of such nanostructured reactive systems are also discussed. Keywords: Ó 2015 The Society of Powder Technology Japan. Published by Elsevier B.V. and The Society of Powder Combustion synthesis Technology Japan. All rights reserved. Self-propagating high-temperature synthesis Solution combustion Nanomaterials Mechanical activation Super thermites Multilayer reactive nano-foils Contents 1. Introduction . ....................................................................................................... 00 2. Mechanically fabricated reactive microstructures and combustion synthesis . -
Additively Manufactured Thermite-Based Energetics
ADDITIVELY MANUFACTURED THERMITE-BASED ENERGETICS: CHARACTERIZATION AND APPLICATIONS By Kelsay Neely Dissertation Submitted to the Faculty of the Graduate School of Vanderbilt University In partial fulfillment of the requirements For the degree of DOCTOR OF PHILOSOPHY in Mechanical Engineering May 8, 2020 Nashville, Tennessee Approved: Alvin M. Strauss, Ph.D. Kevin C. Galloway, Ph.D. Kelsey B. Hatzell, Ph.D. Kenneth Frampton, Ph.D. Kenneth Pence, Ph.D. ACKNOWLEDGEMENTS This dissertation is the culmination of several years of work. I’d like to thank my advisor Dr. Alvin Strauss for his guidance on my academic career, my professional career, and this project. Similarly, I’d like to thank Dr. Kevin Galloway for all of his feedback and for helping me develop as a researcher and as an academic. I also appreciate the rest of my committee, Dr. Ken Frampton, Dr. Ken Pence, and Dr. Kelsey Hatzell for their advice and feedback on my dissertation. I’d like to thank all of my lab mates, specifically my unwavering safety buddies Adam Jarrell, Connor Strawn, Lucas Wilkins, Ben Snyder, Brayden Terry, and Jake Matthews. Finally, I’d like to thank the Tennessee Space Grant Consortium for funding me as a NASA Space Grant Fellow, and the Naval Sea Systems Command (NAVSEA) for funding me and my work through the Naval Engineering Education Consortium (NEEC). On a personal note, there are a lot more people I need to thank, way too many to mention here but I’ll try. I couldn’t have done this without the unwavering support of my friends. I’d like to thank Darren Tinker, Dylan Shane, Melissa, Tyler, and Bella Keagle, and Chase Mu for keeping me from constantly working all the time.