SCS-527 “Sea Duck”
Total Page:16
File Type:pdf, Size:1020Kb
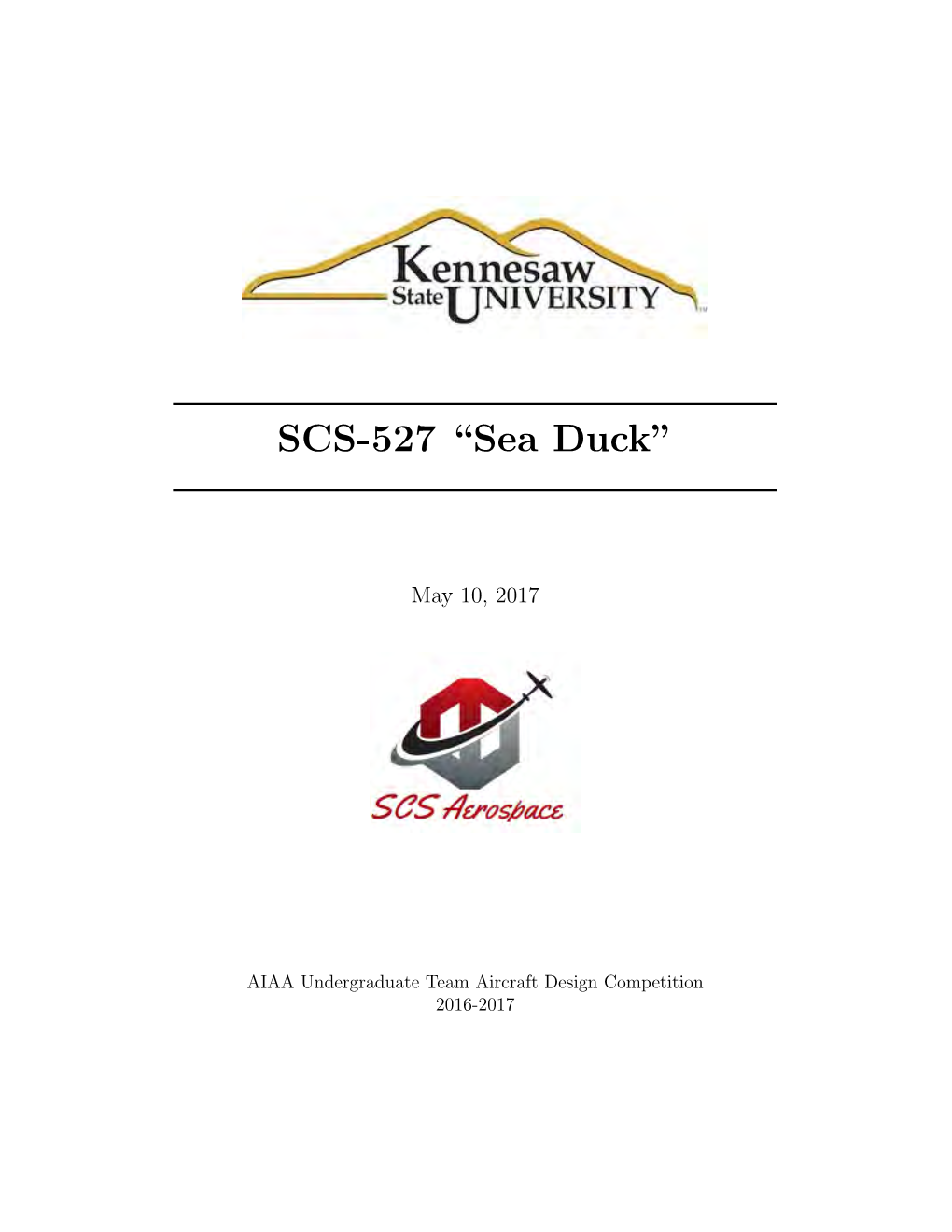
Load more
Recommended publications
-
Development of Next Generation Civilian Aircraft
International Journal of Scientific & Engineering Research Volume 11, Issue 12, December-2020 293 ISSN 2229-5518 Development of Next Generation Civilian Aircraft H Sai Manish Department of Mechanical and Manufacturing Engineering, Manipal Institute of Technology, Manipal, Karnataka, India Abstract Designing a NEXT GENERATION FLYING VEHICLE & its JET ENGINE for commercial air transportation civil aviation Service. Implementation of Innovation in Future Aviation & Aerospace. In the ever-changing dynamics of the world of airspace and technology constant Research and Development is required to adapt to meet the requirement of the passengers. This study aims to develop a subsonic passenger aircraft which is designed in a way to make airline travel economical and affordable to everyone. The design and development of this study aims to i) to reduce the various forces acted on the aircraft thereby reducing the fuel consumption, ii) to utilise proper set of materials and composites to reduce the aircraft weight and iii) proper implementation of Engineering Design techniques. This assessment considers the feasibility of the technology and development efforts, as well as their potential commercial prospects given the anticipated market and current regulatory regime. Keywords Aircraft, Drag reduction, Engine, Fuselage, Manufacture, Weight reduction, Wings Introduction Subsonic airlines have been IJSERthe norm now almost reaching speeds of Mach 0.80, with this into consideration all the commercial passenger airlines have adapted to design and implement aircraft to subsonic speeds. Although high speeds are usually desirable in an aircraft, supersonic flight requires much bigger engines, higher fuel consumption and more advanced materials than subsonic flight. A subsonic type therefore costs far less than the equivalent supersonic design, has greater range and causes less harm to the environment. -
Design of Seaplanes
APPENDIX C3: Design of Seaplanes This appendix is a part of the book General Aviation Aircraft Design: Applied Methods and Procedures by Snorri Gudmundsson, published by Elsevier, Inc. The book is available through various bookstores and online retailers, such as www.elsevier.com, www.amazon.com, and many others. The purpose of the appendices denoted by C1 through C5 is to provide additional information on the design of selected aircraft configurations, beyond what is possible in the main part of Chapter 4, Aircraft Conceptual Layout. Some of the information is intended for the novice engineer, but other is advanced and well beyond what is possible to present in undergraduate design classes. This way, the appendices can serve as a refresher material for the experienced aircraft designer, while introducing new material to the student. Additionally, many helpful design philosophies are presented in the text. Since this appendix is offered online rather than in the actual book, it is possible to revise it regularly and both add to the information and new types of aircraft. The following appendices are offered: C1 – Design of Conventional Aircraft C2 – Design of Canard Aircraft C3 – Design of Seaplanes (this appendix) C4 – Design of Sailplanes C5 – Design of Unusual Configurations Figure C3-1: A Lake LA-250 Renegade, shown here during climb after T-O, is a popular option for amphibious aircraft. The large deflected flap on the horizontal tail is a hydraulically actuated trim tab used for slow speed operations only. It trims out the thrust effect of the highly mounted piston-propeller, improving its handling. -
Low Temperature Environment Operations of Turboengines
0 Qo B n Y n 1c AGARD 2 ADVISORY GROUP FOR AEROSPACE RESEARCH & DEVELOPMENT 3 7 RUE ANCELLE 92200 NEUILLY SUR SEINE FRANCE AGARD CONFERENCE PROCEEDINGS 480 Low Temperature Environment Operations of Turboengines (Design and User's Problems) Fonctionnement des Turborkacteurs en Environnement Basse Tempkrature (Problkmes Pos& aux Concepteurs et aux Utilisateurs) processed I /by 'IMs ..................signed-...............date .............. NOT FOR DESTRUCTION - NORTH ATLANTIC TREATY ORGANIZATION I Distribution and Availability on Back Cover AGARD-CP-480 --I- ADVISORY GROUP FOR AEROSPACE RESEARCH & DEVELOPMENT 7 RUE ANCELLE 92200 NEUILLY SUR SEINE FRANCE AGARD CONFERENCE PROCEEDINGS 480 Low Temperature Environment Operations of Turboengines (Design and User's Problems) Fonctionnement des TurborLacteurs en Environnement Basse Tempkrature (Problkmes PoSes aux Concepteurs et aux Utilisateurs) Papers presented at the Propulsion and Energetics Panel 76th Symposium held in Brussels, Belgium, 8th-12th October 1990. - North Atlantic Treaty Organization --q Organisation du Traite de I'Atlantique Nord I The Mission of AGARD According to its Chartcr, the mission of AGARD is to bring together the leading personalities of the NATO nations in the fields of science and technology relating to aerospace for the following purposes: -Recommending effective ways for the member nations to use their research and development capabilities for the common benefit of the NATO community; - Providing scientific and technical advice and assistance to the Military Committee -
Comparison of Helicopter Turboshaft Engines
Comparison of Helicopter Turboshaft Engines John Schenderlein1, and Tyler Clayton2 University of Colorado, Boulder, CO, 80304 Although they garnish less attention than their flashy jet cousins, turboshaft engines hold a specialized niche in the aviation industry. Built to be compact, efficient, and powerful, turboshafts have made modern helicopters and the feats they accomplish possible. First implemented in the 1950s, turboshaft geometry has gone largely unchanged, but advances in materials and axial flow technology have continued to drive higher power and efficiency from today's turboshafts. Similarly to the turbojet and fan industry, there are only a handful of big players in the market. The usual suspects - Pratt & Whitney, General Electric, and Rolls-Royce - have taken over most of the industry, but lesser known companies like Lycoming and Turbomeca still hold a footing in the Turboshaft world. Nomenclature shp = Shaft Horsepower SFC = Specific Fuel Consumption FPT = Free Power Turbine HPT = High Power Turbine Introduction & Background Turboshaft engines are very similar to a turboprop engine; in fact many turboshaft engines were created by modifying existing turboprop engines to fit the needs of the rotorcraft they propel. The most common use of turboshaft engines is in scenarios where high power and reliability are required within a small envelope of requirements for size and weight. Most helicopter, marine, and auxiliary power units applications take advantage of turboshaft configurations. In fact, the turboshaft plays a workhorse role in the aviation industry as much as it is does for industrial power generation. While conventional turbine jet propulsion is achieved through thrust generated by a hot and fast exhaust stream, turboshaft engines creates shaft power that drives one or more rotors on the vehicle. -
1 Adaptive Wing Technology, Aeroelasticity
Adaptive wing technology, aeroelasticity and flight stability: The lessons from natural flight Dr. Pascual Marqués-Bruna, Faculty of Arts & Sciences, Edge Hill University, St. Helen’s Road, Ormskirk, L39 4QP, United Kingdom. [email protected] Elena Spiridon, School of Natural Sciences and Psychology, Liverpool John Moores University, Tom Reilly Building, Byrom Street, Liverpool, L3 3AF, United Kingdom. [email protected] Abstract This paper reviews adaptive wing morphology and biophysics observed in the natural world and the equivalent adaptive wing technology, aeroelasticity and flight stability principles used in aircraft design. Adaptive wing morphology in birds, including the Harris’ hawk, Common swift, Steppe eagle and Barn swallow, provides excellent examples of aerodynamic and flight control effectiveness that inform the Aeronautical Engineer. The Harris’ hawk and Common swift are gliding birds that change their wing and tail span according to gliding velocity. Inspired by the natural world, effective wing geometry is also modified in aircraft to adjust the aerodynamic load. Bird wings employ an automatic aeroelastic deflection of covert feathers that extend the range of flight configurations and maintain control authority in different flight regimes. Similarly, aircraft structures are not completely rigid and aeroelasticity is important in aircraft. In a Steppe eagle, the alula functions as a high-lift device analogous to the leading edge slats in aircraft wings that allow flight at high angles of attack and low airspeeds without stalling. It has also been suggested that the alula functions as a strake that triggers the development of a leading-edge vortex typical of aircraft delta wings. Sweep-back morphs the hand wing of birds into delta wings that produce lift-generating leading-edge-vortices. -
Analysis of a High-Lift Device by Boundary Layer Blowing System
University Degree in Aerospace Engineering Academic Year 2018-2019 Analysis of a high-lift device by boundary layer blowing system. Bachelor Thesis By Martín López Meijide Tutored and Supervised by Pablo Fajardo Peña July 2019 This work is licensed under Creative Commons Attribution – Non Commercial – Non Derivatives Martín López Meijide Bachelor Thesis Universidad Carlos III de Madrid 2 Martín López Meijide Bachelor Thesis Universidad Carlos III de Madrid Abstract Boundary layer control is a very important subject of investigation in fluid mechanics. The invention of high-lift devices in aircrafts has allowed to increase the capabilities of aerodynamic profiles. This thesis explores one opportunity of taking advantage of boundary layer control in turbulent regimes by means of a blowing system. Carefully CFD simulations have been performed with ANSYS Fluent at different angles of attack for the 2D NACA 4412 airfoil. The boundary conditions are sea level conditions for incompressible flow at Reynold number of 4.8 million, chord of 1m and Mach number of 0.2 for flow velocity. Three modifications of the airfoil geometry have been created at 61%, 50% and 39% of the chord. Each modification includes a slot for the blowing jet of height of 1% of the total chord. The results showed that the blowing system increases the lift coefficient and the aerodynamic efficiency at high angles of attack, which is very useful in take-off and landing configurations. The location of the blowing system at 50% of the chord showed to be the best location for the device. In conclusion, this high-lift device should be implemented and studied further in 3D cases, since it might be an innovative element not only in the aerospace industry, but also other fields of study like wind turbines or nautical ships. -
Design of a Light Business Jet Family David C
Design of a Light Business Jet Family David C. Alman Andrew R. M. Hoeft Terry H. Ma AIAA : 498858 AIAA : 494351 AIAA : 820228 Cameron B. McMillan Jagadeesh Movva Christopher L. Rolince AIAA : 486025 AIAA : 738175 AIAA : 808866 I. Acknowledgements We would like to thank Mr. Carl Johnson, Dr. Neil Weston, and the numerous Georgia Tech faculty and students who have assisted in our personal and aerospace education, and this project specifically. In addition, the authors would like to individually thank the following: David C. Alman: My entire family, but in particular LCDR Allen E. Alman, USNR (BSAE Purdue ’49) and father James D. Alman (BSAE Boston University ’87) for instilling in me a love for aircraft, and Karrin B. Alman for being a wonderful mother and reading to me as a child. I’d also like to thank my friends, including brother Mark T. Alman, who have provided advice, laughs, and made life more fun. Also, I am forever indebted to Roe and Penny Stamps and the Stamps President’s Scholarship Program for allowing me to attend Georgia Tech and to the Georgia Tech Research Institute for providing me with incredible opportunities to learn and grow as an engineer. Lastly, I’d like to thank the countless mentors who have believed in me, helped me learn, and Page i provided the advice that has helped form who I am today. Andrew R. M. Hoeft: As with every undertaking in my life, my involvement on this project would not have been possible without the tireless support of my family and friends. -
Drag Reduction with Riblets in Nature and Engineering
Drag reduction with riblets in nature and engineering D.W. Bechert & W. Hage Department of Turbulence Research, German Aerospace Center (DLR), Berlin, Germany. Abstract Reduction of wall friction of turbulent boundary layer flows can be achieved by using surfaces with properties that are related to skin structures occurring in nature. The scales of several species of fast-swimming sharks show a tiny ribbed structure. This ribbed structure hampers the momentum exchange at the surface that is the origin of the turbulent shear stress.The drag-reducing mechanism of ribbed surfaces (or riblets) is explained by using an analytical model that defines the viscous region of the flow, where the riblets are completely immersed in the viscous sublayer of the turbulent boundary layer. Wall shear stress reduction has been investigated experimentally for various riblet surfaces including a replica of sharkskin consisting of 800 plastic model scales with compliant anchoring. The application of these types of structure to long-range commercial aircraft is discussed, including the effect of the drag reductions on the operational costs of the aircraft. 1 Introduction Drag reduction of a moving animal or vehicle can be achieved by a reduction of wall shear stress and, in some situations, by separation control. Here we focus on turbulent wall shear stress reduction. Obviously laminar flow, which has been successfully used on glider wings, offers the lowest attainable wall shear stress. On commercial aircraft, however, the problems associated with the implementation of laminar flow on swept transonic wings are at present not yet completely solved. Even when laminar flow is maintained over a major percentage of the wing, most of the aircraft surface will still have a turbulent boundary layer. -
Institute for Defence Studies and Analyses No.1, Development Enclave, Rao Tula Ram Marg Delhi Cantonment, New Delhi-110010
Institute for Defence Studies and Analyses No.1, Development Enclave, Rao Tula Ram Marg Delhi Cantonment, New Delhi-110010 Journal of Defence Studies Publication details, including instructions for authors and subscription information: http://www.idsa.in/journalofdefencestudies Transformation of Indian Naval Aviation Post New Inductions Rikeesh Sharma To cite this article: Rikeesh Sharma (2013): Transformation of Indian Naval Aviation Post New Inductions, Journal of Defence Studies, Vol-7, Issue-1.pp- 31-48 URL: http://www.idsa.in/jds/7_1_2013_TransformationofIndianNavalAviationPostNewInductions_RikeeshSharma Please Scroll down for Article Full terms and conditions of use: http://www.idsa.in/termsofuse This article may be used for research, teaching and private study purposes. Any substantial or systematic reproduction, re- distribution, re-selling, loan or sub-licensing, systematic supply or distribution in any form to anyone is expressly forbidden. Views expressed are those of the author(s) and do not necessarily reflect the views of the IDSA or of the Government of India. Transformation of Indian Naval Aviation Post New Inductions Rikeesh Sharma* The need for credible surveillance over the high seas forms the bedrock and foundation of infallible maritime security, and Maritime Reconnaissance (MR) is the basic input for any successful maritime operation. For the last two decades, Indian naval aviation assets have been dependant on the Ilyushin (IL), the Tuplov (TU) aircraft, the Kamov (KM) 31 and Unmanned Aerial Vehicles (UAVs). The Fleet Air Defence has also received a fillip by the induction of the MIG 29Ks. At the same time, the need for Long Range Maritime Reconnaissance (LRMR) tasking has taken a giant leap forward with the Indian Ocean becoming a common operational ground and a global common for numerous navies. -
The Beriev Be 200 in the USA Tangent Link 2014 the Aircraft
BERIEV Aircraft Company Beriev-200 Amphibious Aircraft This document contains information which is property of BERIEV Aircraft Company and can not be used or published without prior written consent. BERIEV Aircraft Company Beriev Aircraft Company Design bureau Production Flight test facility Gelendzhik test base Hydroaviation training center Airlines This document contains information which is property of BERIEV Aircraft Company and can not be used or published without prior written consent. BERIEV Aircraft Company Product Range Be-114 Be-112 This document contains information which is property of BERIEV Aircraft Company and can not be used or published without prior written consent. BERIEV Aircraft Company Be-200 multirole platform • Fire fighting • Search-and-Rescue • Ecological monitoring and pollution control • Medevac • Freight and passenger This document contains information which is property of BERIEV Aircraft Company and can not be used or published without prior written consent. BERIEV Aircraft Company Deployment Aerodrome B-class (1,800 m paved runway) Hydrodrome fitted 18 m (59 ft) with ramp, minimum water depth 2.6 m Mooring to standard pier up to 48 hours (131 ft3 in) 40 40 m min. (8 (8 ft2 ft) Max. inclination 7 deg 2.5 2.5 m This document contains information which is property of BERIEV Aircraft Company and can not be used or published without prior written consent. BERIEV Aircraft Company Standard Fire Fighting Configuration 4 5 6 7 8 9 10 11 12 13 14 15 16 17 18 Flight crew: two pilots 3 2 1 21 11 20 19 1 – cockpit; 2 – first pilot station; 3 – co-pilot station; 4 – weather radar compartment; 5 – equipment units; 6 – forward maintenance door; 7 – cargo hatch; 8 – blister; 9 – life raft; 10 – liquid retardant tanks; 11 – drain ducts; 12 – aft maintenance door; 13 – forward water tank; 14 – retractable water scoops; 15 – rear water tank; 16 – service compartment; 17 – rear technical compartment; 18 – aft compartment; 19 – lavatory; 20 – aft entrance door; 21 – left emergency door. -
British Aircraft in Russia Bombers and Boats
SPRING 2004 - Volume 51, Number 1 British Aircraft in Russia Viktor Kulikov 4 Bombers and Boats: SB-17 and SB-29 Combat Operations in Korea Forrest L. Marion 16 Were There Strategic Oil Targets in Japan in 1945? Emanuel Horowitz 26 General Bernard A. Schriever: Technological Visionary Jacob Neufeld 36 Touch and Go in Uniforms of the Past JackWaid 44 Book Reviews 48 Fleet Operations in a Mobile War: September 1950 – June 1951 by Joseph H. Alexander Reviewed by William A. Nardo 48 B–24 Liberator by Martin Bowman Reviewed by John S. Chilstrom 48 Bombers over Berlin: The RAF Offensive, November 1943-March 1944 by Alan W. Cooper Reviewed by John S. Chilstrom 48 The Politics of Coercion: Toward A Theory of Coercive Airpower for Post-Cold War Conflict by Lt. Col. Ellwood P. “Skip” Hinman IV Reviewed by William A. Nardo 49 Ending the Vietnam War: A History of America’s Involvement and Extrication from the Vietnam War by Henry Kissinger Reviewed by Lawrence R. Benson 50 The Dynamics of Military Revolution, 1300-2050 by MacGregor Knox and Williamson Murray, eds. Reviewed by James R. FitzSimonds 50 To Reach the High Frontier: A History of U.S. Launch Vehicles by Roger D. Launius and Dennis R. Jenkins, eds. Reviewed by David F. Crosby 51 History of Rocketry and Astronautics: Proceedings of the Thirtieth History Symposium of the International Academy of Astronautics, Beijing, China, 1996 by Hervé Moulin and Donald C. Elder, eds. Reviewed by Rick W. Sturdevant 52 Secret Empire: Eisenhower, the CIA, and the Hidden Story of America’s Space Espionage by Philip Taubman Reviewed by Lawrence R. -
An Analysis of Coast Guard HH-65 Engine Reliability: a Comparison of Malfunctions to Component Removals
Air Force Institute of Technology AFIT Scholar Theses and Dissertations Student Graduate Works 3-2004 An Analysis of Coast Guard HH-65 Engine Reliability: A Comparison of Malfunctions to Component Removals Donna L. Cottrell Follow this and additional works at: https://scholar.afit.edu/etd Part of the Applied Mathematics Commons, Aviation Commons, and the Systems Engineering Commons Recommended Citation Cottrell, Donna L., "An Analysis of Coast Guard HH-65 Engine Reliability: A Comparison of Malfunctions to Component Removals" (2004). Theses and Dissertations. 4082. https://scholar.afit.edu/etd/4082 This Thesis is brought to you for free and open access by the Student Graduate Works at AFIT Scholar. It has been accepted for inclusion in Theses and Dissertations by an authorized administrator of AFIT Scholar. For more information, please contact [email protected]. AN ANALYSIS OF COAST GUARD HH-65 ENGINE RELIABILITY: A COMPARISON OF MALFUNCTIONS TO COMPONENT REMOVALS THESIS Donna L. Cottrell, Commander, USCG AFIT/GIR/ENC/04-01 DEPARTMENT OF THE AIR FORCE AIR UNIVERSITY AIR FORCE INSTITUTE OF TECHNOLOGY Wright-Patterson Air Force Base, Ohio APPROVED FOR PUBLIC RELEASE; DISTRIBUTION UNLIMITED The views expressed in this thesis are those of the author and do not reflect the official policy or position of the United States Air Force, United States Coast Guard, Department of Defense, Department of Homeland Security, or the United States Government. AFIT/GIR/ENC/04-01 AN ANALYSIS OF COAST GUARD HH-65 ENGINE RELIABILITY: A COMPARISON OF MALFUNCTIONS TO COMPONENT REMOVALS THESIS Presented to the Faculty Department of Mathematics and Statistics Graduate School of Engineering and Management Air Force Institute of Technology Air University Air Education and Training Command In Partial Fulfillment of the Requirements for the Degree of Master of Science in Information Resource Management Donna L.