The 5.2L V10 FSI Engine Design and Function Self-Study Program
Total Page:16
File Type:pdf, Size:1020Kb
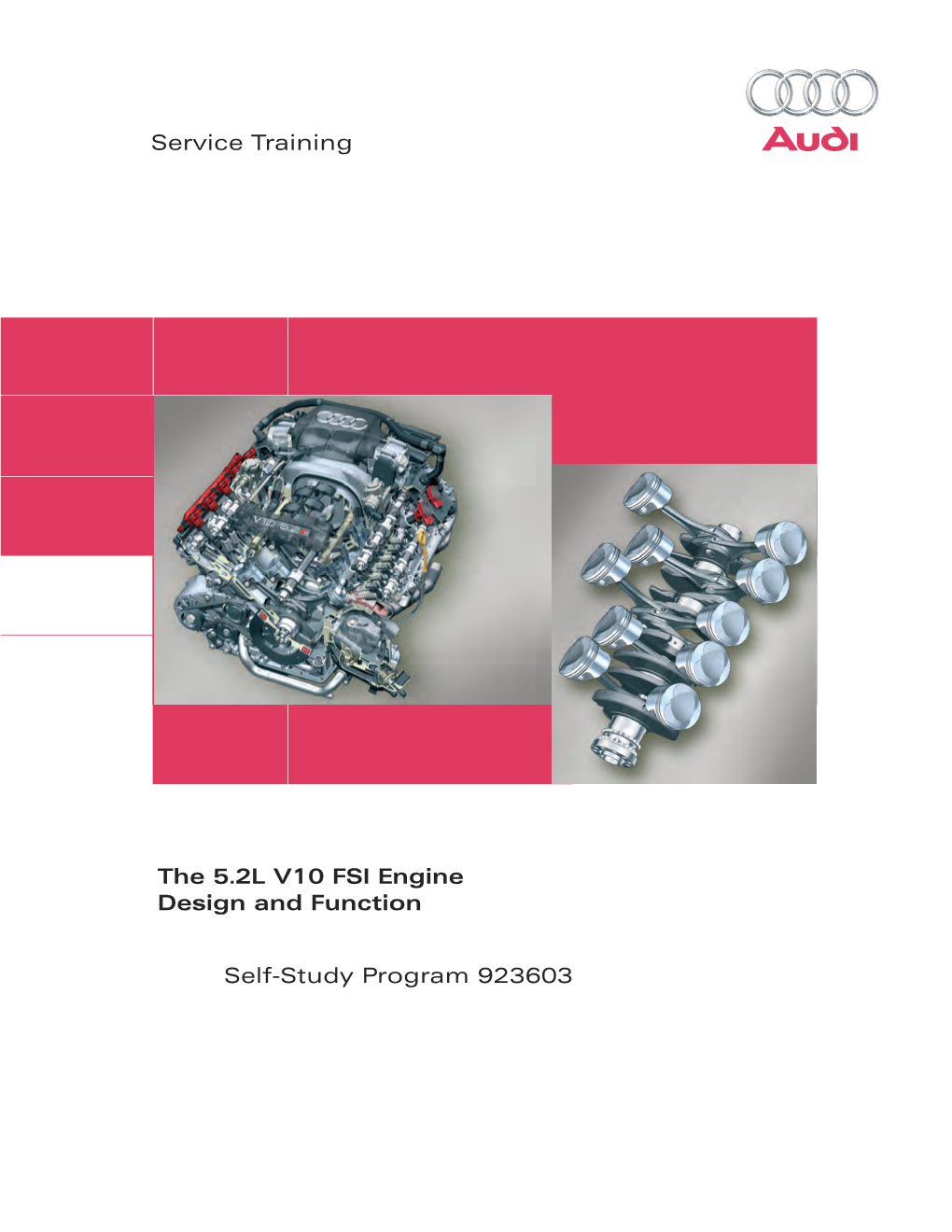
Load more
Recommended publications
-
Optimizing the Cylinder Running Surface / Piston System of Internal
THIS DOCUMENT IS PROTECTED BY U.S. AND INTERNATIONAL COPYRIGHT. It may not be reproduced, stored in a retrieval system, distributed or transmitted, in whole or in part, in any form or by any means. Downloaded from SAE International by Peter Ernst, Saturday, September 15, 2012 04:51:57 PM Optimizing the Cylinder Running Surface / Piston 2012-32-0092 System of Internal Combustion Engines Towards 20129092 Published Lower Emissions 10/23/2012 Peter Ernst Sulzer Metco AG (Switzerland) Bernd Distler Sulzer Metco (US) Inc. Copyright © 2012 SAE International doi:10.4271/2012-32-0092 engine and together with the adjustment of the ring package ABSTRACT and the piston a reduction of 35% in LOC was achieved. This Rising fuel prices and more stringent vehicle emissions engine will go into production in September 2012 with requirements are increasing the pressure on engine limited numbers coated in the Sulzer Metco Wohlen facility manufacturers to utilize technologies to increase efficiency in Switzerland, until an engineered coating system is ready on and reduce emissions. As a result, interest in cylinder surface site to start large series production. More details on the coatings has risen considerably in the past few years. Among engine performance and design changes made to the cast these are SUMEBore® coatings from Sulzer Metco. These aluminium block in order to take full advantage of the coating coatings are applied by a powder-based air plasma spray on the cylinder running surfaces is presented in the paper (APS) process. The APS process is very flexible, and can from Zorn et al. [1]. -
Bishop Rotary Valve Engine
Advanced Engine Technology The Bishop Rotary Valve by Tony Wallis, Bishop Innovation To demonstrate the credibility of Bishop Innovation’s new rotary valve technology it joined forces with Mercedes-Ilmor to develop the technology for use on their V10 Formula One engine only to have its strategy destroyed by a change in engine regulations. 10% power By the early 1990s Bishop Inno- offered by the rotary valve. Fur- ney Australia. Bishop was respon- advantage vation had completed the initial ther, a successful public demon- sible for the cylinder head design, and improved development of its promising new stration of this technology in the development and demonstration durability rotary valve concept for IC en- extreme operating conditions of of the required durability and per- gines and was looking for a way F1 provided a mechanism to ad- formance. By late 2000 back to to further develop the technology. dress the industry’s prejudice. back testing with the poppet valve The automotive industry, having In 1997 Bishop started work- single cylinder engine demon- observed a succession of failed at- ing with Ilmor Engineering (later strated a 10% power advantage tempts spanning the last century, Mercedes-Ilmor) to develop their and improved durability. In 2002 no longer believed the rotary rotary valve technology for F1 the first V10 engines using this valve concept was mechanically engines. The initial development technology were built and tested viable. It chose Formula One (F1), was carried out on 300cc single exhaustively. A completely new as the criteria for success was well cylinder bottom ends supplied by V10 engine was designed and matched to inherent advantages Ilmor at Bishop’s premises in Syd- manufactured in 2003. -
Homage to Ten Years of the V10 Engine: the Audi R8 V10 Decennium
Audi MediaInfo Product Communications Audi Sport GmbH Susanne Mellinghoff Phone: +49 152 58811859 Email: [email protected] www.audi-mediacenter.com Homage to ten years of the V10 engine: the Audi R8 V10 Decennium Limited series of 222 units, individually numbered Coupé with exclusive design highlights Edition model coincides with sales launch of the new Audi R8 Neckarsulm, February 28, 2019 – Audi is celebrating the success story of the V10 engine with the Audi R8 V10 Decennium (combined fuel consumption l/100 km: 13,1 [18.0 US mpg]; combined CO2 emissions in g/km: 297 [478 g/mi]*). A 456 kW (620 hp) V10 engine, bronze- colored highlights inside and out, and strictly limited: The edition model with 222 units coincides with the sales launch of the new Audi R8. The name Decennium comes from Latin and means “decade.” It stands for ten years of fascination on the road and success in motorsport. Right from the exterior design, the Audi R8 V10 Decennium makes its character abundantly clear. The special model is available as a coupé and painted in exclusive Daytona Gray, matt effect. The milled 20-inch wheels and the intake manifold of the 5.2 FSI engine are finished in matt bronze. The front spoiler, the side sills and the diffuser are painted in gloss black, supplemented by black Audi rings and badges on the exterior. The side blades and the exterior mirror housings are made from gloss carbon fiber. Alternatively, there is a choice of the exterior colors Daytona Gray, pearl effect; Suzuka Gray, metallic; Floret Silver, metallic; Mythos Black, metallic; Ascari Blue, metallic and Kemora Gray, metallic. -
M Ercedes-ILM O R : 10 Years of Pow Er D Evelopm Ent of the FO 110 V 10-3.0L Form Ula 1 Engine
M e r c e d e s -IL M O R : 1 0 Y e a r s o f P o w e r D e v e lo p m e n t o f th e F O 1 1 0 V 1 0 -3 .0 L F o r m u la 1 E n g in e T h e w o r ld w id e s u c c e s s o f F o r m u la O n e is s tr o n g ly in flu e n c e d b y th e a p p lic a tio n o f h ig h -le v e l te c h n o lo g y a n d h a s b e e n m a d e p o s s ib le b y th e g r e a t c o m m itm e n t a n d d e d ic a tio n o f th e e n g in e m a n u fa c tu r e r s . B e s id e s th e s k ills o f th e d r iv e r s a n d th e o p tim is a tio n o f th e v e h ic le th r o u g h th e u s e o f s o p h is tic a te d a e r o d y n a m ic s , th e p e r s is te n t r e d u c tio n in la p tim e s c a n b e a ttr ib u te d to th e e n o r m o u s d e v e lo p m e n t c o n c e r n in g th e ty r e s a n d th e e v e r m o r e p o w e r fu l e n g in e s . -
The New BMW M6-UK Edition Contents
10/2005 Page 2 The new BMW M6-UK Edition Contents 1. The BMW M6: A new benchmark for BMW and M (short story)..............................................................................................................3 2. The perfect ten: BMW's V10 wins hearts and minds........................................................................14 3. New seven speed transmission: Ultra-fast shifting with Sequential M Gearbox........................................................23 4. Harnessing the power: A chassis providing agility and poise to complement performance........................27 5. Body: Inside and out, the M6 is clearly focused...............................................................32 6. A new beginning for the M coupé: M6 buyers and market ...........................................................................................39 7. The BMW M6 production process: As bespoke as possible .........................................................................................41 8. Standard specifications .........................................................................................43 9. Optional equipment................................................................................................49 10. Technical specifications, external dimensions, torque graphs...............................51 10/2005 Page 3 1. The BMW M6 – short story A new benchmark for BMW and M GmbH They say lightning never strikes twice. But when two 507hp, 205mph, V10- powered M cars are launched in one year, stay indoors when -
SRT VIPER POWERTRAIN Overview
SRT VIPER POWERTRAIN Overview 2013 SRT Viper Powertrain OVERVIEW Chrysler Canada: New 2013 SRT® Viper V10 Engine Offers More Power, More Torque, Less Weight • 640 horsepower from 8.4-litre V10 helps provide a Viper-best power-to-weight ratio • 600 lb.-ft. of torque is highest rating for a naturally aspirated automotive engine in the world • With an all-new intake system, new pistons, exhaust valves, camshaft profile boasts lower mass and reduced rotating inertia • New intake system significantly improves air distribution across all 10 cylinders • New lightweight, aluminum flywheel for Viper powertrain for reduced rotating inertia • Revised, close-ratio transmission gearing and new final-drive ratio improves acceleration, provides quicker, smoother shifts with top-speed performance achieved in 6th gear At the heart and soul of the 2013 SRT® Viper is a hand-assembled 8.4-litre all-aluminum, V10 engine. The iconic V10 has been continuously upgraded over the years with improvements in oiling, airflow and an industry-first, single-cam variable-valve timing system. For 2013, the engine features a new ultra- high-flow, composite intake manifold for improved air distribution, new forged pistons, new lightweight, sodium-cooled exhaust valves and an aluminum flywheel. The engine also includes new exhaust catalysts to reduce backpressure. The result is a significant improvement of 40 lb.-ft. of torque and 40 horsepower with weight savings of more than 11 kilograms (25 pounds) for the fully dressed engine. Coupled to the more powerful engine is a Tremec TR6060 six-speed transmission that has been refined with tighter gear ratios and a shifter with reduced throws to maximize driver involvement, while effectively transferring power to the pavement. -
Multidisciplinary Design of Aeronautical Composite Cycle Engines
TECHNISCHE UNIVERSITÄT MÜNCHEN Fakultät für Maschinenwesen Lehrstuhl für Luftfahrtsysteme Multidisciplinary Design of Aeronautical Composite Cycle Engines Sascha Kaiser Vollständiger Abdruck der von der Fakultät für Maschinenwesen der Technischen Universität München zur Erlangung des akademischen Grades eines Doktor-Ingenieurs (Dr.-Ing.) genehmigten Dissertation. Vorsitzender: Prof. Dr.-Ing. Volker Gümmer Prüfer der Dissertation: 1. Prof. Dr.-Ing. Mirko Hornung 2. Adjunct Prof. Dr. Anders Lundbladh Chalmers University of Technology, Gothenburg, Sweden Die Dissertation wurde am 28.02.2019 bei der Technischen Universität München eingereicht und durch die Fakultät für Maschinenwesen am 28.10.2019 angenommen. i Acknowledgement We set out to achieve the lowest sfc in the world, regardless of weight and bulk; so far we’ve achieved the weight and the bulk. – Frank Owner about the Bristol Proteus turboprop engine This thesis is the result of six years of work. It would not have been possible without the support from many people, who cannot be counted or named individually. To some of them I want to convey my gratitude on this page. First, I want to thank my thesis supervisor Prof. Mirko Hornung and my second examiner Prof. Anders Lundbladh for their continuous support throughout the thesis in guiding the research topics into the right direction and asking the right questions at the right time. Most of the work has been conducted at the research institute Bauhaus Luftfahrt e.V., where a motivating and liberal working environment allowed me to explore many different perspectives of my work before converging on the research question. I want to thank my dear colleagues, who held up the good spirit at all times, and fostered a supportive research environment. -
The History and Development of the V8 Engine
The History and Development of the V8 Engine Abstract First developed in 1876 by Nicolaus Otto, the internal combustion engine has revolutionised personal transport since it was first fitted to a threewheeled automobile ten years later. Obviously it has changed dramatically since then in terms on the technology applied in design and construction, but the basic principles of operation remain the same. Originally a single cylinder design, the number of cylinders has increased in attempts to increase smoothness and power. Several engine layout configurations have been developed, one of which is the V style engine. So why look at the V8 in particular? First produced in 1914, the V8 engine is a fairly compact layout for large engine sizes (which were needed in order to move heavy vehicles at sufficient speed) and proved to be the most popular engine layout (in terms of sales) in America since it was introduced and has become famous worldwide. One major reason for this is the noise. Although there have been many great sounding engines over the decades, from various cylinder layouts, almost all V8s sound special and are loved by car enthusiasts. This, along with a wide range of capacities (from under 2 litres to over 8 litres in mass produced form), has earned them places in a wide variety of vehicles initially just in large saloons but later in sports cars, off road vehicles, powerboats, the occasional aeroplane and even a motorbike. The passion towards the V8 design ensures that it will endure. Introduction The idea of an internal combustion engine was first designed in 1680 (although never built) by a Dutch physicist named Christian Huygens. -
Thefrench Connection
RCNMag.com WINTER 2019 BMW V10-Powered SL-C Wide-Body Beck 904 709 hp Craft Small-Block THE FRENCH CONNECTION How a Gallic designer of exotic cars in Dubai hooked up with a Kentucky Cobra builder Page 44 Boss-powered 1969 Alan Mann Open Sports Ford Page 10 PUBLISHING INC PUBLISHING COLE PAID U.S. POSTAGE U.S. PRSTD STD PRSTD COLE PUBLISHING INC., PO BOX 220, THREE LAKES WI 54562 54562 WI LAKES THREE 220, BOX PO INC., PUBLISHING COLE ELECTRONIC SERVICE REQUESTED SERVICE ELECTRONIC $59,995 base price of each car outfitted with nearly $20,000 in options including parking brake, front and rear lift assist, V8 Graziano, and more. Invoices available to show all options. Brand new Michelin Pilot Sport tires ($1,750). MSRP $82,000 not including tires or shipping. Two to choose from - white gel with silver powder coated wheels or grey gel with black powder coated wheels. Ready for your engine and final assembly. $79,900 Winter Sale Price $75,900 Available now! Call or text 715-493-7911 Contents 44 OMING NEXT MONTH C On the Cover A.J. Foyt Indy Car The Jannarelly Design-1 mirrors the Lotus Seven in concept, as a stripped down, Superformance Future GT Forty bare-bones driver. This example was finished at the Dream Car Co. in Kentucky, and The Case For Coilovers is the first Jannarelly on the road in the United States. Photo by Juan Lopez-Bonilla. Smyth Charger Conversion THROTTLE STEERING READER’S RIDE 6 Featuring Your Project Car 34 Racy Story By Steve Temple, Editor Revealing the birth of the wide-body Beck 904 GTS. -
Development of Valvetrain for Formula One Engine
Development of Valvetrain for Formula One Engine Shuichi HAYAKAWA* Kazushi OGIYAMA* Masanori TATE* ABSTRACT From 2000, the development teams involved in Honda’s Formula One engine development program worked as one in development efforts focused on the achievement of increased power through increased engine speed. As part of these efforts, the configuration of the valvetrain was reexamined from the bottom up, and new mechanisms were developed. To enable the realization of high speed and high lift in the valvetrain, a finger follower system was employed as the valve drive method in place of a bucket tappet system. In addition, the application of a measurement method applying Bezier curves to the acceleration of the valve lift curves and the optimization of the gear train reduced fluctuations in the angular velocity of the camshafts and enhanced valve motion. Furthermore, it was necessary to reduce the excessive friction due to increased engine speed. In response to this, the pneumatic valve return system was advanced by reexamining the configuration of the cylinder heads. The development of electronically-controlled regulator system also contributed to reducing friction. 1. Introduction In response to this trend, a jet-type air control system (J-valve mechanism) was newly developed to modify the Competition in technological development is pneumatic valve return system (PVRS). This system particularly intense in Formula One, the pinnacle of the enabled oil agitation resistance in the PVRS cylinder to world’s auto races. Merely maintaining -
LITERATURE REVIEW on STABILIZING HIGH SPEED VALVE- and DRIVETRAIN CONCEPTS for RACING APPLICATIONS Internship at the Engine Development Department of Audi Sport
LITERATURE REVIEW ON STABILIZING HIGH SPEED VALVE- AND DRIVETRAIN CONCEPTS FOR RACING APPLICATIONS Internship at the engine development department of Audi Sport Prof. Dr. Ir. A. de Boer Dipl. -Ing. S. Wohlgemuth Thomas Roodink s1501623 [email protected] Introductory remarks In the summer season of 2016 I was allowed to do a six month internship within the research department of Audi Sport in Neckarsulm Germany. A dream came true after Le Mans 2015 when I offered my curriculum vitae to Mr. Baretzky, head of the engine department of Audi Sport. I want to thank him deeply for giving me the opportunity to be part of his team. Moreover, I want to thank Prof. Dr. Ir. A. de Boer of the University of Twente for the great support during the internship and for his flexibility before the start of the internship. A very special thanks goes to Dipl. -Ing. S. Wohlgemuth of the engine research department of Audi Sport for sharing his great knowledge, passion and support. “There is no such thing as cam design, there is only valve lift profile design which requires the creation of a cam and follower mechanism to reliably provide this designed valve lift profile.” G. Blair, 2006 Contents 1. Introduction .................................................................................................................... 4 2. Spring actuated valve train concepts .............................................................................. 5 2.1 Overhead valve (OHV) ........................................................................................... -
Fuel Economy in Focus: Advances in Development of Energy-Efficient Lubricants and Low-Friction Coatings for Automotive Applications
102 Lube 22/3/11 17:04 Page 23 Lube-Tech No.75 page 1 PUBLISHED BY LUBE: THE EUROPEAN LUBRICANTS INDUSTRY MAGAZINE Fuel economy in focus: advances in development of energy-efficient lubricants and low-friction coatings for automotive applications Boris Zhmud, Ph.D., Assoc.Prof. Chief Technology Manager Applied Nano Surfaces AB, Uppsala, Sweden Meeting the challenge • On the coating side - by improving the cylinder just before ignition. This New fuel economy standards for tribological behavior of existing allows for higher compression ratios automobiles erected by governments in materials by means of surface without knocking, and leaner air/fuel the G20 major economies and change coatings; mixtures than in conventional Otto-cycle in customer preferences driven by high • On the lubricant side - by developing internal combustion engines. By fuel prices put increased pressure on lubricants to obtain desired regulating injection pressure and valve car makers. Thus, the U.S. tribological behavior for a given timing and lift, constant electronically- Environmental Protection Agency is material. aided engine efficiency tuning is possible preparing to look at standards for 2017 Development costs, material costs and based on the actual load, fuel type, and beyond - setting at the top of its production costs are always important exhaust parameters, and ambient potential range a standard of 62 mpg factors when market potential of one or conditions. by 2025. In one or another way, those another approach is to be assessed. political and economical incentives An alternative to FSI is homogeneous intensify research and development Smarter engines, lighter cars charge compression ignition (HCCI) efforts taken by major OEMs in order to Engineering advancements in car technology which can be viewed as a achieve new ambitious fuel economy construction over the past decades did hybrid of homogeneous charge spark targets.