Control of Nonmetallic Inclusions in Continuously Cast Steels in View of Macro- Cleanliness, Castability, Precipitation Modification and Grain Refinement
Total Page:16
File Type:pdf, Size:1020Kb
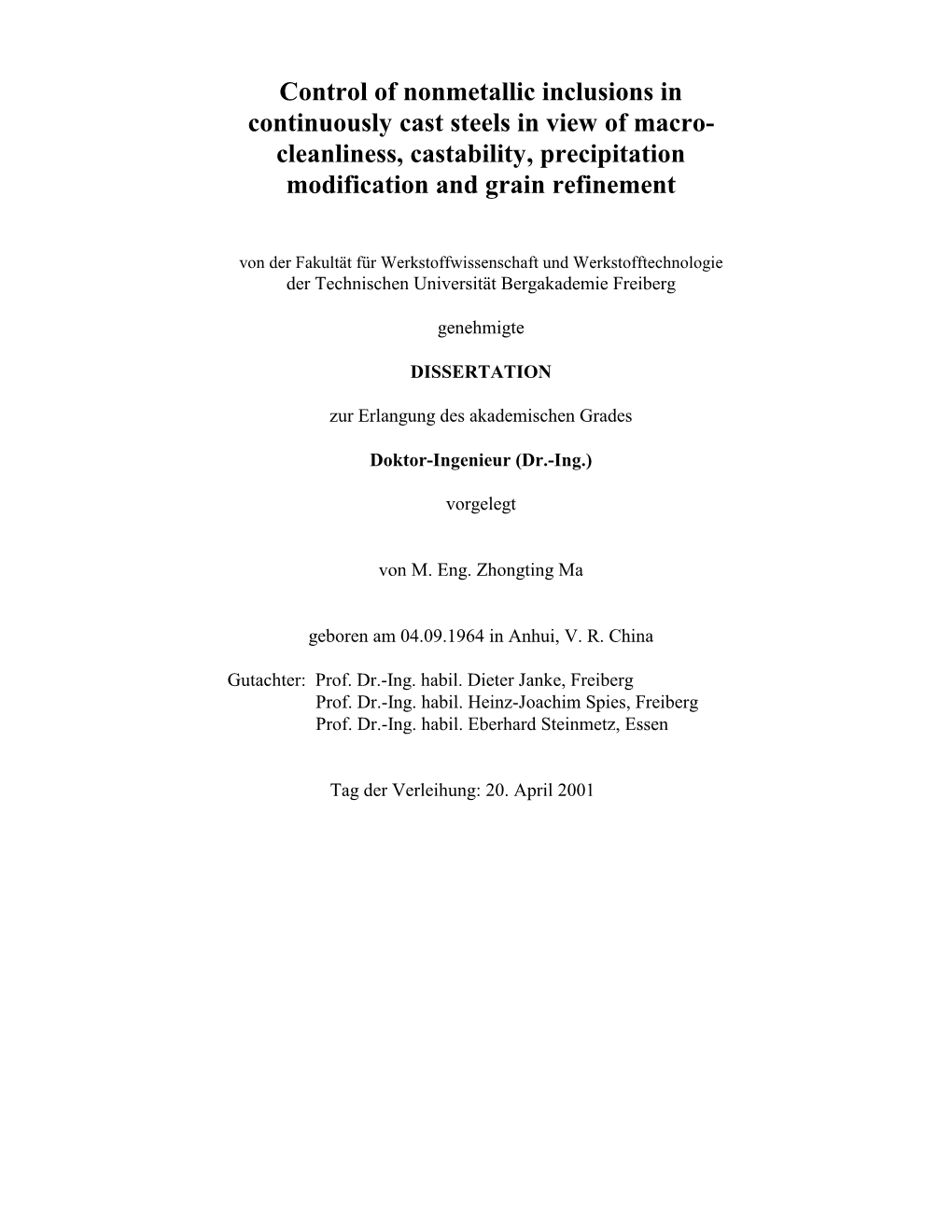
Load more
Recommended publications
-
Thermodynamics of Titanium Oxide in Ladle Slags
ISIJ International, Vol. 41 (2001), No. 12, pp. 1447–1453 Thermodynamics of Titanium Oxide in Ladle Slags Sung-Mo JUNG and R. J. FRUEHAN1) Formerly Postdoctoral research associate, at Department of Materials Science and Engineering, Carnegie Mellon University, now at Graduate School of Iron and Steel Technology, Pohang University of Science and Technology, Pohang 790-784, Korea. 1) Department of Materials Science and Engineering, Carnegie Mellon University, Pittsburgh, PA 15213 USA. (Received on May 17, 2001; accepted in final form on August 27, 2001) It is necessary to have information on the thermodynamic behavior of titanium oxide in ladle type slags in order to control the titanium content in several grades of steel. In the present study, the thermodynamics was determined from the equilibrium between Fe–Csat–Ti and CaO–SiO2-–30%Al2O3–MgO–TiOx slags , in equilibrium with CO and from the equilibrium between Fe–Csat–(16 18)%Cr–Si–Ti and CaO–SiO2– 20%Al2O3–MgO–TiOx slags in equilibrium with CO. From the experiment with Fe–Csat–Ti alloy, the activity coefficients of TiO1.5 and TiO2 vary with basicity from 0.3 to 1.5 and from 0.5 to 2.3, respectively. And from , the experiment with Fe–Csat–(16 18)%Cr–Si–Ti alloy, the activity coefficients of TiO1.5 and TiO2 vary with ba- sicity from 0.4 to 1.4 and from 0.6 to 3.5, respectively. The results obtained from the equilibrium between , Fe–Csat–(16 18)%Cr–Si–Ti and CaO-SiO2–20%Al2O3–MgO–TiOx slags were used to estimate the titanium content of silicon-added stainless steel. -
ARCHIVES of FOUNDRY ENGINEERING Volume 18, Issue 1/2018, 129 - 1 3 4 During Electrolytic Dissolution
ARCHIVES ISSN (2299-2944) Volume 18 of Issue 1/2018 FOUNDRY ENGINEERING 129 – 134 DOI: 10.24425/118825 24/1 Published quarterly as the organ of the Foundry Commission of the Polish Academy of Sciences A Study of Inclusions in Aluminum and Titanium Deoxidized 4130 R.B. Tuttle *, S. Kottala Saginaw Valley State University, 209 Pioneer Hall, 7400 Bay Rd., 48710 University Center, United States * Corresponding author. E-mail address: [email protected] Received 02.10.2017; accepted in revised form 14.11.2017 Abstract In this paper, the authors investigated the size distribution of titanium oxide (TiO2), titanium nitride (TiN) and titanium carbide (TiC) inclusions in a titanium deoxidized 4130 steel and compared it with the 4130 base alloy composition inclusions. TiN and TiC inclusions are of particular interest due to their role as heterogeneous nuclei for various phase reactions in steels. Two types of samples were prepared, a polished sample and a filtered sample. Electrolytic dissolution was employed to make the filter paper samples. The size range of titanium inclusions was found to be more than that of the non-metallic inclusions from 4130 base alloy heat. Titanium inclusions from the filter and polished samples were round in shape. TiC and TiN inclusions were not found in the electrolytic extraction samples. Inclusions and their chemistries were analyzed using scanning electron microscope and energy dispersive spectrometer. The inclusion size range was larger for the titanium deoxidized samples than the base alloy. However, in both steels the majority of inclusions had a size smaller than 10 μm. Keywords: Steel, Sand casting, Inclusions, Electrolytic extraction, Inclusion characterization 1. -
Effect of Deoxidation Sequence on Carbon Manganese Steel Weld Metal Microstructures
Effect of Deoxidation Sequence on Carbon Manganese Steel Weld Metal Microstructures Deoxidation sequence has a strong influence on nonmetallic inclusions formation and the subsequent weld refinement BY F-C. LIAO AND S. LIU ABSTRACT. During investigation of indi boundary ferrite and Widmanstatten side the molten metal for the purpose of vidual and combined effects of aluminum plate ferrite are often grouped together as deoxidation. Some common deoxidizers and titanium on low-carbon low-alloy primary ferrite (PF). As the weld tempera used in steel making are aluminum, silicon, steel weld metal microstructures, experi ture continues to drop, fine acicular ferrite manganese, and titanium. In arc welding, mental welds were made on 12.7-mm (AF) laths begin to nucleate intragranularly. these same elements are also used for (0.5-in.) thick A516 C70 pressure vessel Finally, the remaining austenite transforms weld pool deoxidation and alloying. They steel plates using ER70S-3 welding wire to a variety of microstructural features, enter the weld pool from the base metal, and a low-oxygen potential commercial which include bainite (B), martensite (M) electrode, or fluxes. In ladle refining of flux. In the aluminum or titanium (individ and pearlite (P). Together with the re steels, the deoxidation reactions occur at ual) addition series welds, the results indi tained austenite, martensite and carbides near isothermal and equilibrium condi cated that the final weld metal microstruc form the microconstituents known as tions quite different from those found in tures are related to the inclusion size dis MAC. The relative proportions of the dif most welding conditions. -
Inclusions Properties at 1673 K and Room Temperature with Ce Addition
www.nature.com/scientificreports OPEN Inclusions properties at 1673 K and room temperature with Ce addition in SS400 steel Received: 13 January 2017 Fei Pan 1,2,3, Hao-Long Chen4, Yen-Hsun Su1, Yen-Hao Su 5 & Weng-Sing Hwang1 Accepted: 13 April 2017 Inclusion species formed in SS400 steel with Ce-addition was predicted by thermodynamic calculation. The Published: xx xx xxxx analysis of the inclusion morphology and size distribution was carried out by applying Scanning Electron Microscopy (SEM) and Transmission Electron Microscope (TEM). Nano-Fe3O4 particles were also found in cerium-deoxidized and -desulfurized steel and their shapes were nearly spherical. The complex Ce2O3 inclusions covering a layer of 218 nm composed by several MnS particles with similar diffraction pattern. Most importantly, the complex Ce2O3 characterized by using TEM diffraction is amorphous in the steel, indicating that Ce2O3 formed in the liquid iron and then MnS segregated cling to it. Nonmetallic inclusions with high melting point in steel could be harmful in production of high grade wire, spring, and bearing steels1, 2. Inclusions larger than 10 µm are probable to lower the yield strength obviously and also decrease tensile strength3. However, the yield strength and tensile strength would increase remarkably for steels with inclusions less than 0.3 µm3. Adding a or several metal elements into steel has been exploited by steel manufactures in order to form finer grain structures in steel and to improve the performance of the steel4. Titanium5, Aluminium6 and Magnesium7 have been studied a lot as deoxidizers and their functions have also been researched a lot to improve the strength of steel. -
The Effect of Different Non-Metallic Inclusions on the Machinability of Steels
Materials 2015, 8, 751-783; doi:10.3390/ma8020751 OPEN ACCESS materials ISSN 1996-1944 www.mdpi.com/journal/materials Review The Effect of Different Non-Metallic Inclusions on the Machinability of Steels Niclas Ånmark 1,2,*, Andrey Karasev 1 and Pär Göran Jönsson 1 1 Department of Materials Science and Engineering, KTH Royal Institute of Technology, Stockholm SE-100-44, Sweden; E-Mails: [email protected] (A.K.); [email protected] (P.G.J.) 2 Department of Materials and Manufacturing, Swerea KIMAB, Kista SE-164-40, Sweden * Author to whom correspondence should be addressed; E-Mail: [email protected]; Tel.: +46-0-72-508-43-42. Academic Editor: Richard Thackray Received: 19 December 2014 / Accepted: 11 February 2015 / Published: 16 February 2015 Abstract: Considerable research has been conducted over recent decades on the role of non-metallic inclusions and their link to the machinability of different steels. The present work reviews the mechanisms of steel fractures during different mechanical machining operations and the behavior of various non-metallic inclusions in a cutting zone. More specifically, the effects of composition, size, number and morphology of inclusions on machinability factors (such as cutting tool wear, power consumption, etc.) are discussed and summarized. Finally, some methods for modification of non-metallic inclusions in the liquid steel are considered to obtain a desired balance between mechanical properties and machinability of various steel grades. Keywords: inclusions; machinability; steel 1. Introduction Advances in steelmaking during the last six decades have resulted in steel grades with very low level of impurities. In recent years, new “clean and ultra-clean” steels have been developed and commercialized by steel producers around the world, thereby responding to the current and future market demands of steel having significantly improved mechanical properties (e.g., fatigue strength and impact toughness) and an improved corrosion resistance. -
Kinetic Data Paper
Experimental Study of Kinetic Processes During the Steel Treatment at two LMF’s Jörg Peter Kent D. Peaslee David G. C. Robertson University of Missouri-Rolla Department of Materials Science and Engineering 1870 Miner Circle 218 McNutt Hall Rolla, MO 65409-0340 Tel.: 573-341-4714 Fax: 573-341-6934 E-mail: [email protected] or [email protected] Brian G. Thomas University of Illinois at Urbana-Champaign Mechanical and Industrial Engineering Department 1206 West Green Street Urbana, IL 61801 Tel.: 217-333-6919 Fax: 217-244-6534 Keywords: ladle refining, mass transfer rate constant, kinetics, industrial trials ABSTRACT The mass transfer rate during ladle refining was quantified by taking sequential steel and slag samples during the treatment of 20 heats. Each heat was stirred with a different argon flow rate, ranging between 0 and 63 scfm. Heats were treated at two different plants. Al-killed steel was produced at an LMF in 151-t ladles. Si-deoxidized steel was produced at an LMF in 123-t ladles. Mass transfer rate constants were determined for each heat by using process simulation (Metsim) and thermodynamic (FactSage) models. Relationships between mass transfer rate constants and stirring powers as well as ladle geometries were compared between the two plants and published literature. It was found that the reaction kinetics during ladle refining depend on the bulk transport of the steel to the slag/steel interface and on the thermodynamic equilibrium at the slag/steel interface. The necessary refining time decreases if the newly-defined specific steel transport rate is maximized and the slag has a low basicity and FeO concentration before the start of de-S. -
Aluminum-Free Steelmaking: Desulfurization and Nonmetallic Inclusion Evolution of Si-Killed Steel in Contact with Cao-Sio2-Caf2-Mgo Slag
processes Article Aluminum-Free Steelmaking: Desulfurization and Nonmetallic Inclusion Evolution of Si-Killed Steel in Contact with CaO-SiO2-CaF2-MgO Slag Stephano P. T. Piva and Petrus Christiaan Pistorius * Department of Materials Science and Engineering, Carnegie Mellon University, Pittsburgh, PA 15213, USA; [email protected] * Correspondence: [email protected] Abstract: In some applications, deep desulfurization and deoxidation of steels without the use of aluminum are required, using Si as a deoxidant instead, with double-saturated slags in the CaO-SiO2-CaF2-MgO system. This work studied the desulfurization and nonmetallic inclusion evolution for the system using an induction furnace and compared the results with FactSage kinetic simulations. Steel samples were taken from the steel melt and analyzed with ICP-MS and combustion analysis for chemistry, and SEM/EDS for nonmetallic inclusion quantity, size, and composition. The results indicate that the steel was deeply desulfurized, with a final sulfur partition coefficient of 580; MgO was reduced from the slag, yielding dissolved [Mg] that transformed liquid Mn–silicate inclusions into forsterite and MgO. Intentional reoxidation of the melt with oxidized electrolytic iron demonstrated a significant concentration of dissolved [Mg] in the steel, by the formation of additional forsterite and MgO upon reoxidation. Citation: Piva, S.P.T.; Pistorius, P.C. Keywords: Aluminum-Free Steelmaking: steelmaking; slag; kinetics; clean steel; nonmetallic inclusions; ladle treatment Desulfurization and Nonmetallic Inclusion Evolution of Si-Killed Steel in Contact with CaO-SiO2-CaF2-MgO Slag. Processes 2021, 9, 1258. 1. Introduction https://doi.org/10.3390/pr9081258 For certain steel products, alumina-containing nonmetallic inclusions are undesirable, whether because of their effect on steel castability (the tendency of solid alumina and spinel Academic Editors: Chenn Q. -
Welding & Metalworking Products Promotion!
WELDING & METALWORKING PRODUCTS PROMOTION! AIRMAX PAPR CLASSIC STYLE PORT-A-TORCH® OUTFIT • Offers affordable protection from harmful contaminants while you weld • Components are industrial-grade for professional use • Features a W40 series variable A D F, • Cutting attachments feature solid forged heads, adjustable shade 9-13 with light shade 4 triangular stainless steel tubes, solid brass • Flame resistant face seal and breathing hose protect against sparks forged levers and a lock ring • Lightweight blower unit mounts on an adjustable belt • Stored in a heav y-dut y, weather-proof • Audible alarm signals when battery and flame-retardant tool bag charge or new filter is required • Includes: Welding tip (23A90-3), • NIOSH approved HE filtration fuel gas regulator (601-15-200), from particulate contaminants oxygen regulator (601-80-540), torch handle (85), cutting attachment (72-3), mixer (D-85), cutting tip (6290-1AC), 3/16" x 12' hose, 20 cu. ft. oxygen cylinder, 10 cu. ft. "MC" acetylene cylinder, cylinder wrench, goggles, striker and instruction manual Model MFG Promo Model MFG Promo No. No. Price No. No. Price SED529 12993 599.95 TTU624 4403211 595.00 AIR-ACETYLENE FEATHER AIR-ACETYLENE TARGET TORCHTM KITS FLAME® TORCH KIT • Hot turbine flame • Interchangeable snap-in tips • Feather brush flame • For professional soldering • Interchangeable screw-in tip and brazing applications • Includes: Heavy-duty torch, • Includes: Heavy-duty torch, UL listed brass regulator, UL listed brass regulator, handle, lighter, wrench, quick-disconnect handle, tip and 12' hose tips and 12' hose 330-1777 330-1663 Model MFG Tip Reg. Promo Model MFG Tip Reg. Promo No. -
An Experimental Study of Non-Metallic Inclusions Precipitation and Its Effect on Impact Toughness Variations in Low Alloy Steel Subjected to Complex Deoxidation
University of Northern Iowa UNI ScholarWorks Dissertations and Theses @ UNI Student Work 2017 An experimental study of non-metallic inclusions precipitation and its effect on impact toughness variations in low alloy steel subjected to complex deoxidation Pavel Bizyukov University of Northern Iowa Let us know how access to this document benefits ouy Copyright ©2017 Pavel Bizyukov Follow this and additional works at: https://scholarworks.uni.edu/etd Part of the Metallurgy Commons Recommended Citation Bizyukov, Pavel, "An experimental study of non-metallic inclusions precipitation and its effect on impact toughness variations in low alloy steel subjected to complex deoxidation" (2017). Dissertations and Theses @ UNI. 368. https://scholarworks.uni.edu/etd/368 This Open Access Dissertation is brought to you for free and open access by the Student Work at UNI ScholarWorks. It has been accepted for inclusion in Dissertations and Theses @ UNI by an authorized administrator of UNI ScholarWorks. For more information, please contact [email protected]. AN EXPERIMENTAL STUDY OF NON-METALLIC INCLUSIONS PRECIPITATION AND ITS EFFECT ON IMPACT TOUGHNESS VARIATIONS IN LOW ALLOY STEEL SUBJECTED TO COMPLEX DEOXIDATION An Abstract of a Dissertation Submitted in Partial Fulfillment of the Requirements for the Degree Doctor of Industrial Technology Approved: _________________________________ Dr. Scott R. Giese, Committee Chair _________________________________ Dr. Kavita Dhanwada Dean of the Graduate College Pavel Bizyukov University of Northern Iowa May 2017 ABSTRACT A low level of non-metallic inclusions in steel is the key requirement in the concept of clean steel. Although the concept has received its name quite recently, it has been implemented at the large-scale steel mills for more than 40 years. -
Metallurgy for the Non-Metallurgist, Second Edition Copyright © 2011, ASM International® A.C
Edited by Arthur C. Reardon ASM International® Materials Park, Ohio 44073-0002 www.asminternational.org Copyright © 2011 by ASM International® All rights reserved No part of this book may be reproduced, stored in a retrieval system, or transmitted, in any form or by any means, electronic, mechanical, photocopying, recording, or otherwise, without the written permission of the copyright owner. First printing, October 2011 Great care is taken in the compilation and production of this book, but it should be made clear that NO WARRANTIES, EXPRESS OR IMPLIED, INCLUDING, WITHOUT LIMITATION, WARRANTIES OF MERCHANTABILITY OR FITNESS FOR A PARTICULAR PURPOSE, ARE GIVEN IN CONNECTION WITH THIS PUBLICATION. Although this information is believed to be accurate by ASM, ASM cannot guarantee that favorable results will be obtained from the use of this publication alone. This publication is intended for use by persons having technical skill, at their sole discretion and risk. Since the conditions of product or material use are outside of ASM’s control, ASM assumes no liability or obligation in connection with any use of this information. No claim of any kind, whether as to products or information in this publication, and whether or not based on negligence, shall be greater in amount than the purchase price of this product or publication in respect of which damages are claimed. THE REMEDY HEREBY PROVIDED SHALL BE THE EXCLUSIVE AND SOLE REMEDY OF BUYER, AND IN NO EVENT SHALL EITHER PARTY BE LIABLE FOR SPECIAL, INDIRECT OR CONSEQUENTIAL DAMAGES WHETHER OR NOT CAUSED BY OR RESULTING FROM THE NEGLIGENCE OF SUCH PARTY. -
Inclusion Evolution Behavior of Ti-Mg Oxide Metallurgy Steel and Its Effect on a High Heat Input Welding HAZ
metals Article Inclusion Evolution Behavior of Ti-Mg Oxide Metallurgy Steel and Its Effect on a High Heat Input Welding HAZ Hao-Nan Lou 1, Chao Wang 1, Bing-Xing Wang 1,*, Zhao-Dong Wang 1, Yu-Qian Li 2 and Zi-Gang Chen 2 1 State Key Laboratory of Rolling and Automation, Northeastern University, NO. 3-11, Wenhua Road, Heping District, Shenyang 110819, Liaoning, China; [email protected] (H.-N.L.); [email protected] (C.W.); [email protected] (Z.-D.W.) 2 Handan Iron & Steel Group Co., Ltd., No. 232, Fuxing Road, Fuxing Distirct, Handan 056015, Hebei, China; [email protected] (Y.-Q.L.); [email protected] (Z.-G.C.) * Correspondence: [email protected]; Tel.: +86-024-8368-1190 Received: 6 June 2018; Accepted: 9 July 2018; Published: 11 July 2018 Abstract: We have studied here the evolution of inclusions in ladle furnace (LF), Ruhrstahl & Heraeus furnace (RH), and simulated welded samples during Ti-Mg oxide metallurgy treatment and the mechanical properties of the heat-affected zone (HAZ) after high heat input welding. The study indicated that inclusions in an LF furnace station are silicomanganate and MnS of size range ~0.8–1.0 µm. After Mg addition, fine Ti-Ca-Mg-O-MnS complex oxides were obtained, which were conducive to the nucleation of acicular ferrite (AF). The corresponding microstructure changed from ferrite side plate (FSP) and polygonal ferrite (PF) to AF, PF, and grain boundary ferrite (GBF). After a simulated welding thermal cycle of 200 kJ/cm, disordered arrangements of acicular ferrite plates, fine size cleavage facets, small inclusions, and dimples all promoted high impact toughness. -
Three-Dimensional Investigations of Different Sulfides in Steels by Using Electrolytic Extraction
DEGREE PROJECT IN MATERIALS SCIENCE AND ENGINEERING, SECOND CYCLE, 30 CREDITS STOCKHOLM, SWEDEN 2016 Three-dimensional Investigations of Different Sulfides in Steels by Using Electrolytic Extraction PANG KIT JERRY LAM KTH ROYAL INSTITUTE OF TECHNOLOGY SCHOOL OF INDUSTRIAL ENGINEERING AND MANAGEMENT ~ 1 ~ www.kth.se ~ 2 ~ Three-dimensional Investigations of Different Sulfides in Steels by Using Electrolytic Extraction Abstract The emphasis of this study is focusing on three-dimensional (3D) investigations of the manganese sulfide (MnS) inclusions characteristics in steels by using electrolytic extraction (EE). Two steel grades, 42CrMo4 and 157C, heat treated (HT) at 900 oC were investigated. 42CrMo4 steel samples were heat treated for 5, 10, 15 and 30 minutes while 157C steel samples were heat treated for 5 minutes. Samples of 42CrMo4 were taken from middle zone of an as-cast steel bar while that for grade 157C were taken from 3 different zones (centre, middle and surface). Inclusions were collected on film filters and analyzed by SEM for classification and determination of their characteristics including the size, number density, morphology and composition. The aspect ratio (AR) as well as particle size distribution (PSD) were also compared for steel samples conducted at various HT times. The result showed that EE is a reliable method of investigation inclusion characteristics. The inclusions were classified into 3 types according to their morphology and composition. Type I was elongated rod-like MnS, type II was coarsened sheet-like MnS and type III was spherical MnS inclusions. In addition, HT significantly reduced the Nv and fairly reduced AR but no significant reduction in size observed.