Properties of Cement Mortar Using Limestone Sludge Powder Modified
Total Page:16
File Type:pdf, Size:1020Kb
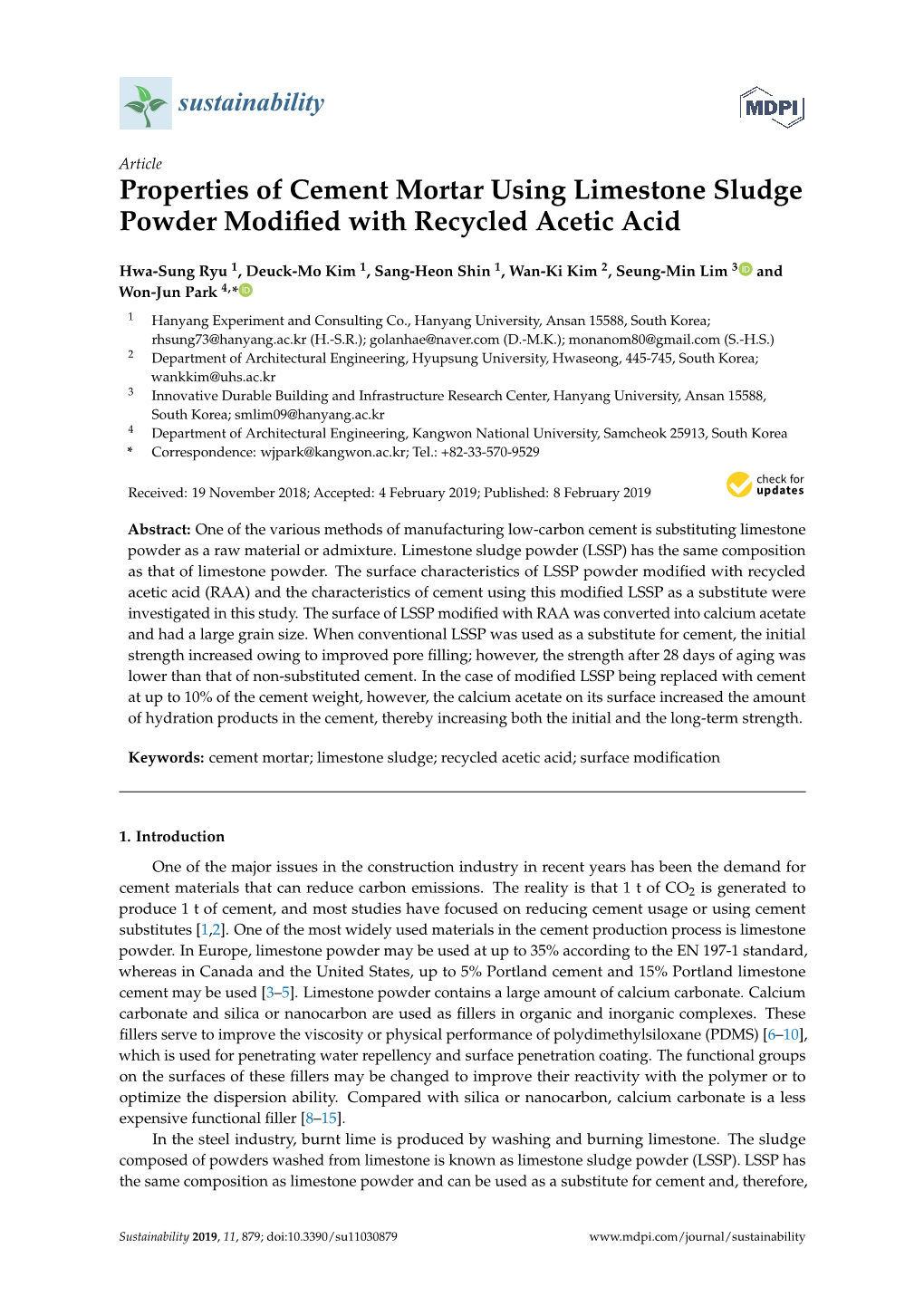
Load more
Recommended publications
-
Bedrock Geology Glossary from the Roadside Geology of Minnesota, Richard W
Minnesota Bedrock Geology Glossary From the Roadside Geology of Minnesota, Richard W. Ojakangas Sedimentary Rock Types in Minnesota Rocks that formed from the consolidation of loose sediment Conglomerate: A coarse-grained sedimentary rock composed of pebbles, cobbles, or boul- ders set in a fine-grained matrix of silt and sand. Dolostone: A sedimentary rock composed of the mineral dolomite, a calcium magnesium car- bonate. Graywacke: A sedimentary rock made primarily of mud and sand, often deposited by turbidi- ty currents. Iron-formation: A thinly bedded sedimentary rock containing more than 15 percent iron. Limestone: A sedimentary rock composed of calcium carbonate. Mudstone: A sedimentary rock composed of mud. Sandstone: A sedimentary rock made primarily of sand. Shale: A deposit of clay, silt, or mud solidified into more or less a solid rock. Siltstone: A sedimentary rock made primarily of sand. Igneous and Volcanic Rock Types in Minnesota Rocks that solidified from cooling of molten magma Basalt: A black or dark grey volcanic rock that consists mainly of microscopic crystals of pla- gioclase feldspar, pyroxene, and perhaps olivine. Diorite: A plutonic igneous rock intermediate in composition between granite and gabbro. Gabbro: A dark igneous rock consisting mainly of plagioclase and pyroxene in crystals large enough to see with a simple magnifier. Gabbro has the same composition as basalt but contains much larger mineral grains because it cooled at depth over a longer period of time. Granite: An igneous rock composed mostly of orthoclase feldspar and quartz in grains large enough to see without using a magnifier. Most granites also contain mica and amphibole Rhyolite: A felsic (light-colored) volcanic rock, the extrusive equivalent of granite. -
Oregon Department of Human Services HEALTH EFFECTS INFORMATION
Oregon Department of Human Services Office of Environmental Public Health (503) 731-4030 Emergency 800 NE Oregon Street #604 (971) 673-0405 Portland, OR 97232-2162 (971) 673-0457 FAX (971) 673-0372 TTY-Nonvoice TECHNICAL BULLETIN HEALTH EFFECTS INFORMATION Prepared by: Department of Human Services ENVIRONMENTAL TOXICOLOGY SECTION Office of Environmental Public Health OCTOBER, 1998 CALCIUM CARBONATE "lime, limewater” For More Information Contact: Environmental Toxicology Section (971) 673-0440 Drinking Water Section (971) 673-0405 Technical Bulletin - Health Effects Information CALCIUM CARBONATE, "lime, limewater@ Page 2 SYNONYMS: Lime, ground limestone, dolomite, sugar lime, oyster shell, coral shell, marble dust, calcite, whiting, marl dust, putty dust CHEMICAL AND PHYSICAL PROPERTIES: - Molecular Formula: CaCO3 - White solid, crystals or powder, may draw moisture from the air and become damp on exposure - Odorless, chalky, flat, sweetish flavor (Do not confuse with "anhydrous lime" which is a special form of calcium hydroxide, an extremely caustic, dangerous product. Direct contact with it is immediately injurious to skin, eyes, intestinal tract and respiratory system.) WHERE DOES CALCIUM CARBONATE COME FROM? Calcium carbonate can be mined from the earth in solid form or it may be extracted from seawater or other brines by industrial processes. Natural shells, bones and chalk are composed predominantly of calcium carbonate. WHAT ARE THE PRINCIPLE USES OF CALCIUM CARBONATE? Calcium carbonate is an important ingredient of many household products. It is used as a whitening agent in paints, soaps, art products, paper, polishes, putty products and cement. It is used as a filler and whitener in many cosmetic products including mouth washes, creams, pastes, powders and lotions. -
Ocean Acidification and Oceanic Carbon Cycling 13
Ocean Acidification and Oceanic Carbon Cycling 13 Dieter A. Wolf-Gladrow and Bjo¨rn Rost Contents Atmospheric CO2 ............................................................................... 104 Air-Sea CO2 Exchange and Ocean Carbonate Chemistry ..................................... 104 Rate of Surface Ocean Acidification and Regional Differences .. ........................... 104 The Physical Carbon Pump and Climate Change .............................................. 105 Impact of Ocean Acidification on Marine Organisms and Ecosystems ....................... 106 The Biological Carbon Pump and Climate Change ............................................ 107 Take-Home Message ............................................................................ 108 References ....................................................................................... 109 Abstract The concentration of atmospheric CO2 is increasing due to emissions from burning of fossil fuels and changes in land use. Part of this “anthropogenic CO2” invades the oceans causing a decrease of seawater pH; this process is called “ocean acidification.” The lowered pH, but also the concomitant changes in other properties of the carbonate system, affects marine life and the cycling of carbon in the ocean. Keywords Anthropogenic CO2 • Seawater acidity • Saturation state • Climate change • Physical carbon pump • Global warming • Biological carbon pumps • Phyto- plankton • Primary production • Calcification D.A. Wolf-Gladrow (*) • B. Rost Alfred Wegener Institute, Helmholtz Centre -
Interaction of Calcium Supplementation and Nonsteroidal Anti-Inflammatory Drugs and the Risk of Colorectal Adenomas
2353 Interaction of Calcium Supplementation and Nonsteroidal Anti-inflammatory Drugs and the Risk of Colorectal Adenomas Maria V. Grau,1 John A. Baron,1,2 Elizabeth L. Barry,1 Robert S. Sandler,3 Robert W. Haile,4 Jack S. Mandel,5 and Bernard F. Cole1 Departments of 1Community and Family Medicine and 2Medicine, Dartmouth Medical School, Lebanon, New Hamsphire; 3Department of Medicine, University of North Carolina, Chapel Hill, North Carolina; 4Department of Preventive Medicine, University of Southern California, Los Angeles, California; and 5Department of Epidemiology, Rollins School of Public Health, Emory University, Atlanta, Georgia Abstract Background: Calcium and aspirin have both been found to be Results: In the Calcium Trial, subjects randomized to calcium chemopreventive against colorectal neoplasia. However, the who also were frequent users of NSAIDs had a reduction joint effect of the two agents has not been well investigated. of risk for advanced adenomas of 65% [adjusted risk ratio Methods: To explore the separate and joint effects of calcium (RR), 0.35; 95% confidence interval (95% CI), 0.13-0.96], and and aspirin/nonsteroidal anti-inflammatory drugs (NSAID), there was a highly significant statistical interaction between we used data from two large randomized clinical trials calcium treatment and frequent NSAID use (Pinteraction = among patients with a recent history of colorectal adenomas. 0.01). Similarly, in the Aspirin Trial, 81 mg aspirin and In the Calcium Polyp Prevention Study, 930 eligible subjects calcium supplement use together conferred a risk reduction were randomized to receive placebo or 1,200 mg of elemental of 80% for advanced adenomas (adjusted RR, 0.20; 95% CI, calcium daily for 4 years. -
Some Drugs Are Excluded from Medicare Part D, but Are Covered by Your Medicaid Benefits Under the Healthpartners® MSHO Plan (HMO)
Some drugs are excluded from Medicare Part D, but are covered by your Medicaid benefits under the HealthPartners® MSHO Plan (HMO). These drugs include some over‐the‐counter (OTC) items, vitamins, and cough and cold medicines. If covered, these drugs will have no copay and will not count toward your total drug cost. For questions, please call Member Services at 952‐967‐7029 or 1‐888‐820‐4285. TTY members should call 952‐883‐6060 or 1‐800‐443‐0156. From October 1 through February 14, we take calls from 8 a.m. to 8 p.m., seven days a week. You’ll speak with a representative. From February 15 to September 30, call us 8 a.m. to 8 p.m. Monday through Friday to speak with a representative. On Saturdays, Sundays and holidays, you can leave a message and we’ll get back to you within one business day. Drug Description Strength 3 DAY VAGINAL 4% 5‐HYDROXYTRYPTOPHAN 50 MG ABSORBASE ACETAMINOPHEN 500 MG ACETAMINOPHEN 120MG ACETAMINOPHEN 325 MG ACETAMINOPHEN 650MG ACETAMINOPHEN 80 MG ACETAMINOPHEN 650 MG ACETAMINOPHEN 160 MG/5ML ACETAMINOPHEN 500 MG/5ML ACETAMINOPHEN 160 MG/5ML ACETAMINOPHEN 500MG/15ML ACETAMINOPHEN 100 MG/ML ACETAMINOPHEN 500 MG ACETAMINOPHEN 325 MG ACETAMINOPHEN 500 MG ACETAMINOPHEN 80 MG ACETAMINOPHEN 100.00% ACETAMINOPHEN 80 MG ACETAMINOPHEN 160 MG ACETAMINOPHEN 80MG/0.8ML ACETAMINOPHEN‐BUTALBITAL 50MG‐325MG ACNE CLEANSING PADS 2% ACNE TREATMENT,EXTRA STRENGTH 10% ACT ANTI‐CAVITY MOUTH RINSE 0.05% Updated 12/01/2012 ACTICAL ACTIDOSE‐AQUA 50G/240ML ACTIDOSE‐AQUA 15G/72ML ACTIDOSE‐AQUA 25G/120ML ACTIVATED CHARCOAL 25 G ADEKS 7.5 MG -
Limestone Resources of Western Washington
State of Washington DANIEL J. EVANS, Governor Department of Conservation H. MA URI CE AHLQUIST, Director DIVISION OF MINES AND GEOLOGY MARSHALL T. HUNTTING, Supervisor Bulletin No. 52 LIMESTONE RESOURCES OF WESTERN WASHINGTON By WILBERT R. DANNER With a section on the UME MOUNTAIN DEPOSIT By GERALD W. THORSEN STATII PRINTING PLANT, OLYMPI A, WASH, 1966 For sale by Department of Conservation, Olympia, Washington. Price, $4,50 FOREWORD Since the early days of Washington's statehood, limestone has been recognized as one of the important mineral resources _of the State. The second annual report of the Washington Geological Survey, published in 1903, gave details on the State's limestone deposits, and in later years five other reports published by the Survey and its successor agencies hove given additional information on this resource. Still other reports by Federal and private agencies hove been published in response to demands for data on limestone here. Although some of the earlier reports included analyses to show the purity of the rocks, very few of the samples for analysis were taken systemati cally in a way that would fairly represent the deposits sampled. Prior to 1900 limestone was produced for use as building stone here, and another important use was for the production of burned Ii me . Portland cement plants soon became leading consumers of Ii mestone, and they con tinue as such to the present time . Limestone is used in large quantities in the pulp industry in the Northwest, and in 1966 there was one commercial lime-burning plant in the State. Recognizing the potential for industrial development in Washington based on more intensive use of our mineral resources, and recognizing the need to up-dote the State's knowledge of raw material resources in order to channel those resources into the State's growing economy, the Industrial Row Materials Advisory Committee of the Deportment of Commerce and Economic Development in 1958 recommended that a comprehensive survey be made of the limestone resources of Washington. -
The Historical Record in the Scaglia Limestone at Gubbio: Magnetic Reversals and the Cretaceous-Tertiary Mass Extinction
Sedimentology (2009) 56, 137Ð148 doi: 10.1111/j.1365-3091.2008.01010.x The historical record in the Scaglia limestone at Gubbio: magnetic reversals and the Cretaceous-Tertiary mass extinction WALTER ALVAREZ Department of Earth and Planetary Science, University of California, Berkeley, CA 94720-4767, USA (E-mail: [email protected]) ABSTRACT The Scaglia limestone in the Umbria-Marche Apennines, well-exposed in the Gubbio area, offered an unusual opportunity to stratigraphers. It is a deep- water limestone carrying an unparalleled historical record of the Late Cretaceous and Palaeogene, undisturbed by erosional gaps. The Scaglia is a pelagic sediment largely composed of calcareous plankton (calcareous nannofossils and planktonic foraminifera), the best available tool for dating and long-distance correlation. In the 1970s it was recognized that these pelagic limestones carry a record of the reversals of the magnetic field. Abundant planktonic foraminifera made it possible to date the reversals from 80 to 50 Ma, and subsequent studies of related pelagic limestones allowed the micropalaeontological calibration of more than 100 Myr of geomagnetic polarity stratigraphy, from ca 137 to ca 23 Ma. Some parts of the section also contain datable volcanic ash layers, allowing numerical age calibration of the reversal and micropalaeontological time scales. The reversal sequence determined from the Italian pelagic limestones was used to date the marine magnetic anomaly sequence, thus putting ages on the reconstructed maps of continental positions since the breakup of Pangaea. The Gubbio Scaglia also contains an apparently continuous record across the CretaceousÐTertiary boundary, which was thought in the 1970s to be marked everywhere in the world by a hiatus. -
Reefs and Reef Limestones in Earth History
2 Reefs and Reef Limestones in Earth History Pamela Hallock One can live in the shadow of an idea without grasping it. – Elizabeth Bowen The history of reefs and reef limestones is like a never-ending mystery series, complete with paradoxes to unravel and mass “murders” to solve given only partial texts and enigmatic clues. Limestones play a critical role in recording events in the history of life on Earth, as their production and preservation is intimately related to cycles of carbon, nitrogen and phosporus in the lithosphere, hydrosphere and atmosphere. These biogeochemical cycles, which have been evolving for more than 4,000 million years, are being profoundly disrupted by human activities such as mining and burning of fossil fuels. As a result, the records preserved in limestones provide researchers and policy makers with critical insights into possible consequences of human activities for the future not only of reefs, but of the diversity of ecosystems on Earth and even the future of human civilizations. Limestones have long been of economic interest because many ancient reef provinces are major oil and gas reservoirs today, while others are essential aquifers. As a result, the literature on ancient reefs and lesser carbonate buildups is vast. A few of the multitude of useful compilations include Milliman (1974), Wilson (1975), Bathurst (1976), Toomey (1981), Scholle et al. (1983), Fagerstrom (1987), Crevello et al. (1989), Riding (1991), James and Clarke (1997), Camoin and Davies (1998), Wood (1999), Stanley (2001), and Kiessling et al. (2002). This chapter cannot provide the details available in these books. Instead it summarizes the significance of biogenic reefs and limestones within the context of Earth history. -
Product Safety Summary
Product Safety Summary Calcium Carbonate CAS No. 497-34-1 This Product Safety Summary is intended to provide a general overview of the chemical substance. The information on the summary is basic information and is not intended to provide emergency response information, medical information or treatment information. The summary should not be used to provide in-depth safety and health information. In-depth safety and health information can be found on the Safety Data Sheet (SDS) for the chemical substance. Names Calcium carbonate Chalk Product Overview Solvay Fluorides, LLC does not sell calcium carbonate directly to consumers. Consumers may be exposed to calcium carbonate in many consumer product applications where the calcium carbonate is not transformed or reacted and is present in powder or granule form. Calcium carbonate is a white, granular or powdered solid. It is used primarily in construction, to make glass, production of polymer compounds as well as for acid gas treatment and pH adjustment. It is also used in the manufacture of other chemicals and pharmaceuticals. Exposure to calcium carbonate, especially powder, can cause irritation to the skin, eyes, and respiratory tract. Manufacture of Product Solvay Fluorides, LLC imports the calcium carbonate it sells from a Solvay affiliate in Europe. Solvay manufactures calcium carbonate by calcining (removing carbon dioxide) quarried marble to form lime (calcium oxide). Water is added to make calcium hydroxide and carbon dioxide (CO2) is passed through the solution to reform a purified calcium carbonate, which is then precipitated (crystallized) into its final form. Page 1 of 4 Copyright 2011-2013, Solvay America, Inc. -
The Investigation of Acetylsalicylic Acid, Sodium Bicarbonate, and Calcium Carbonate
CALIFORNIA STATE SCIENCE FAIR 2010 PROJECT SUMMARY Name(s) Project Number Irfan S. Habib J2113 Project Title The Investigation of Acetylsalicylic Acid, Sodium Bicarbonate, and Calcium Carbonate Abstract Objectives/Goals Does the amount of acetylsalicylic acid in various brands of aspirin tablets depend on the price of the aspirin tablet? Are CaCO3 (calcium carbonate) antacids or NaHCO3 (sodium bicarbonate) antacids more efficient in neutralizing stomach acidity? Does the strength of the base within an antacid depend on the price of the antacid? Methods/Materials A: Titration of Ammonia and Vinegar to obtain basic understanding of titration. B: Titration of aspirin and ammonia was performed to determine the normality (which is the concentration of H+ per 1 L of solution) of each aspirin brand. C: Titration of antacid tablets and vinegar was performed to determine the normality (which is the concentration of OH- per 1L of solution) of each antacid brand. D: Added antacid to 0.5M HCl 1g at a time and recorded pH after each gram was added in order to determine which antacid brand increased the pH of solution at a faster rate. Results A: Normality of Ammonia= 1.06 Normality of Vinegar = 0.83 B: St. Joseph#s was the most expensive aspirin and the Rite Aid brand was the least expensive; however, Ecotrin was the 3rd most expensive and it had the greatest H+ content. The Rite Aid brand had the least amount of H+ content. C: Alka-seltzer was most expensive antacid and Equaline was the least expensive. The Alka-seltzer and Rite Aid brand of antacids had greatest amount of OH- content (both had NaHCO3)and the Equaline (contained CaCO3)had least amount of OH-. -
Calcium Carbonate Dissolution and Precipitation in Water: Factors Affecting the Carbonate Saturometer Method
Utah State University DigitalCommons@USU All Graduate Theses and Dissertations Graduate Studies 5-1971 Calcium Carbonate Dissolution and Precipitation in Water: Factors Affecting the Carbonate Saturometer Method Lyle M. Dabb Utah State University Follow this and additional works at: https://digitalcommons.usu.edu/etd Part of the Chemistry Commons, and the Soil Science Commons Recommended Citation Dabb, Lyle M., "Calcium Carbonate Dissolution and Precipitation in Water: Factors Affecting the Carbonate Saturometer Method" (1971). All Graduate Theses and Dissertations. 2991. https://digitalcommons.usu.edu/etd/2991 This Thesis is brought to you for free and open access by the Graduate Studies at DigitalCommons@USU. It has been accepted for inclusion in All Graduate Theses and Dissertations by an authorized administrator of DigitalCommons@USU. For more information, please contact [email protected]. ACKNOWLEDGMENTS I would like to thank Dr. Jerome J . Jurinak for his patience and guidance during my classwork and lab experiments. I would also like t o thank Dr . R. L . Smith and Dr. H. B. Petersen for serving as committee members. I thank Robert A. Griffin and Dr. Sung-Ho Lai for their friendship, help, and encouragement. I thank Dr. John J. Hassett for his help when I started this research. Pa rtial support of this study by the Federal Water Quality Admin- istration is gr atefully acknowledged. I thank my wife, Sandy, for keeping our horne affairs running so smoothly and for her understanding and patience. ¥ m fJJt- Lyle M. Dabb TABLE OF CONTENTS Page INTRODUCTION 1 REVIEW OF LITERATURE 3 METHODS AND MATERIALS RESULTS AND DISCUSSION 10 EIGHT NATURAL WATERS FROM VERNAL, UTAH 31 SUMMARY AND CONCLUSIONS . -
Amorphous Calcium–Magnesium Carbonate (ACMC)
Amorphous Calcium–Magnesium Carbonate (ACMC) Accelerates Dolomitization at Room Temperature under Abiotic Conditions German Montes-Hernandez, François Renard, Anne-Line Auzende, Nathaniel Findling To cite this version: German Montes-Hernandez, François Renard, Anne-Line Auzende, Nathaniel Findling. Amorphous Calcium–Magnesium Carbonate (ACMC) Accelerates Dolomitization at Room Temperature under Abiotic Conditions. Crystal Growth & Design, American Chemical Society, 2020, 20 (3), pp.1434- 1441. 10.1021/acs.cgd.9b01005. hal-02896885 HAL Id: hal-02896885 https://hal.archives-ouvertes.fr/hal-02896885 Submitted on 5 Nov 2020 HAL is a multi-disciplinary open access L’archive ouverte pluridisciplinaire HAL, est archive for the deposit and dissemination of sci- destinée au dépôt et à la diffusion de documents entific research documents, whether they are pub- scientifiques de niveau recherche, publiés ou non, lished or not. The documents may come from émanant des établissements d’enseignement et de teaching and research institutions in France or recherche français ou étrangers, des laboratoires abroad, or from public or private research centers. publics ou privés. 1 Amorphous calcium-magnesium carbonate (ACMC) accelerates 2 dolomitization at room temperature under abiotic conditions 3 4 German Montes-Hernandeza *, François Renarda, b, Anne-Line Auzendea, Nathaniel Findlinga 5 6 a Univ. Grenoble Alpes, Univ. Savoie Mont Blanc, CNRS, IRD, IFSTTAR, ISTerre, 38000 7 Grenoble, France 8 b The Njord Centre, Department of Geosciences, University of Oslo, box 1048 Blindern, 0316 Oslo, 9 Norway 10 11 12 13 *Corresponding author: Dr. German Montes-Hernandez 14 E-mail address: [email protected] 15 1 16 Abstract 17 The challenge to produce dolomite CaMg(CO3)2 at low temperature (20-35°C) over laboratory time 18 scales remains so far unsuccessful, which has led to long-lasting scientific debates in the last two 19 centuries.