Defence Brochure
Total Page:16
File Type:pdf, Size:1020Kb
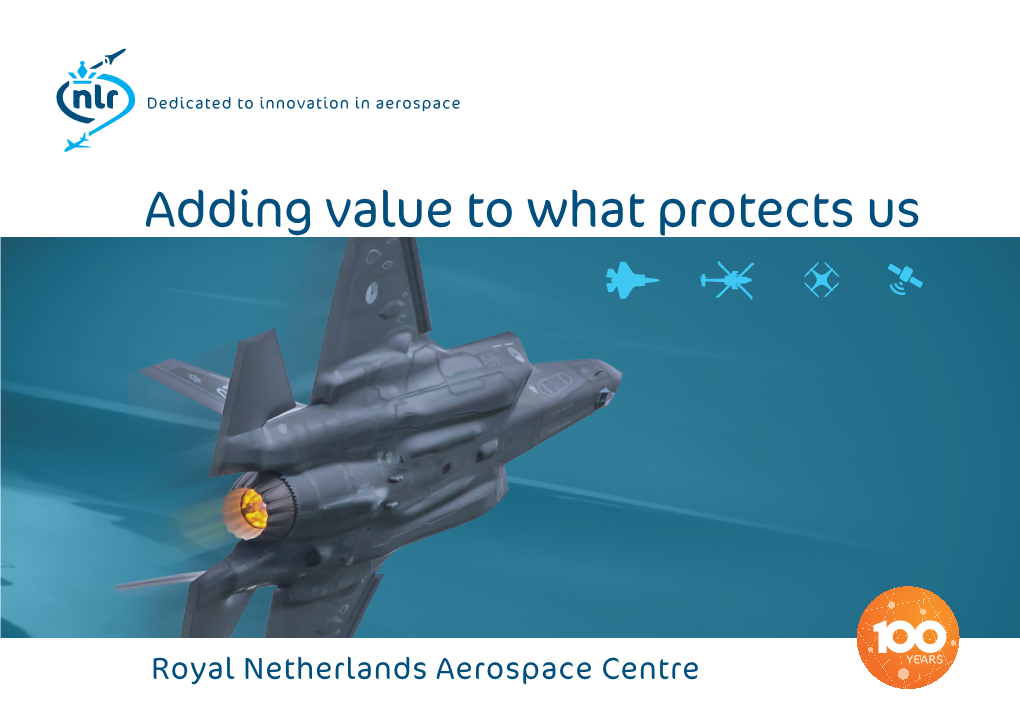
Load more
Recommended publications
-
“I Have the Fokker in Sight!”
“I have the Fokker in sight!” After some delays caused by tropical cyclone “Gita” the first of our two Fokker F27 Friendship aircraft arrived from New Zealand on Monday 27 February. Now registered VH-EWH, the Friendship departed Auckland on Sunday 26 February, stopping to refuel at Norfolk Island before proceeding to Coolangatta to clear customs. The intention was to proceed to Wollongong that same day, but bad weather in the Illawarra dictated an overnight stay at Coolangatta. The second aircraft will be ferried sometime in the next few months. In Australian service the Fokker F27 Friendship was operated from the late 1950’s by many of the domestic and regional airlines. Some of the Australian airlines which operated the type include Trans Australia Airlines, Ansett ANA, East West, Queensland Airlines, Bill Peach’s Aircruising Australia and Airlines of NSW. The type was also operated by the Department of Civil Aviation and CSIRO. The Fokker F27 was developed during the early 1950’s and was intended to compete with or replace piston engine aircraft such as the DC-3. It uses Rolls Royce Dart turboprop engines, is pressurised and, in typical configuration seats around 50 passengers. Our F27s were most recently in service with a company that provided services to New Zealand Post and our Kiwi readers would be well familiar with the sight and unique sounds of the F27s as they made their way around the mail runs. Convair CV-440 progress The return to flight project for our Convair CV-440 made significant progress this month with completion of the new engine installation. -
Fokker Dr.I for X-Plane 10
Aerobask Fokker Dr.I for X-Plane 10 User Manual Aerobask Table of Contents Part I: Historical Background 3 Introduction 4 About the Dr.I 4 The Red Baron 5 The Aerobask Model 6 Final Thoughts 6 Part II: Aircraft Description & Instructions ! Installation and Settings 8 Re uire!ents 8 Installation 8 Settings 8 Aircra"t Di!ensions # Aircra"t S$eci"ications %& '$$er Instru!ents %% (o)er Instru!ents %* +n,Screen Menus %- Starting . Sto$$ing the /ngine %4 Takeo"" . (anding %5 Part III: Air Co#$at in t%e Fokker Dr'I 1( Air 0o!bat in 1,2lane %& %3 4etting and Ar!ing AI Aircra"t %3 Setting u$ Tea!s in 1,2lane %3 Using the Dr.I in Multi$la5er %8 Basic Fighter Tactics %# The Dicta Boelcke %# 0o!!on Maneu6ers *& 2 Part I: Historical Background Historical I: Part )he Red Baron+s Dr'I Baron+s Red )he P%oto: ,ikipedia Aerobask Introduction 0ongratulations on your purchase of the Aerobask Fokker Dr.I for 1,2lane 1&. This aircra"t is 6er5 di"ferent fro! our $re6ious products – usually we o"fer you renditions of very modern *%st century aircra"t8 such as the E$ic 9ictor5: the Fokker Dr.I8 built in earl5 *&th centur58 is the co!$lete o$$osite. And it has a histor5. A$out t%e Dr'I The Dr.I is a tri$lane8 which is a rare thing in itself. The Dr.I is also one of the !ost fa!ous fighter aircra"t. In late ;orld War I it )as an answer to the earlier British So$)ith Tri$lane which had been a real danger to the 4er!ans since No6e!ber 1#%6.% Ant%on4 Fokker- de6eloper of t%e Dr'I The Dr.I )as a successful fighter during the final months of the war8 but it had so!e shortco!ings, such as slo) s$eed8 short range8 unreliable engines and wing failures due to the tri$lane conce$t. -
Read Book Essentials of Statistics 5Th Edition Ebook, Epub
ESSENTIALS OF STATISTICS 5TH EDITION Author: Mario F Triola Number of Pages: --- Published Date: --- Publisher: --- Publication Country: --- Language: --- ISBN: 9780321924599 DOWNLOAD: ESSENTIALS OF STATISTICS 5TH EDITION Essentials of Statistics 5th edition PDF Book The 11 papers in Part 1 are devoted to the theme of information systems and communications and the 10 papers in Part 2 focus on geographical analysis and geometric modeling. From aerobics and yoga - to bowling, tennis, weight training, and more - the Cengage Learning Activities Series goes beyond the basics, showing you how to improve, excel, and get more enjoyment from your activities, whatever your skill level and background.H. Getting a flat, toned belly is not that hard, if you know which exercises are the right ones and which diet to follow during your abs workout program. Learn The Strategies To Make A Lot Of Money With Day Trading. Professional chefs give step-by-step advice for shopping for the cheapest, tastiest ingredients-and offer recipes that put those ingredients to good use, from homemade Chinese "take-out" to the frugal barbecue. ' - Mental Health OT Communication and Mental Illness is a comprehensive and practical textbook written by a multidisciplinary group of experts in the field of mental health which will be of interest to all those interested in improving their understanding of individuals with mental illness. This book looks at how to provide a helpful environment for children to grow up with a sense of both inner and self confidence. Windows 7 For Dummies Quick Reference covers all the information you need most often: tips on navigating the new desktop, launching programs, working with files and folders, getting online and managing e-mail, using special features, and much more. -
Fokker 70 Information Booklet
Fokker 70 Information Booklet v v Introduction The Fokker 70 is a regional aircraft developed from the Fokker 100. Both aircraft have a large systems commonality and pilots share the same type rating. From 1994 until 1997, 47 aircraft were built by the Fokker Aircraft Company. A sophisticated flight deck and avionics, good performance and low noise and engine emissions continue to make the Fokker 70 a versatile and cost-effective 80-seater. Designed with a life of 90,000 landings, most Fokker 70s are currently in service with ten operators around the world in all types of operational environments. The Fokker 70 is in use as a passenger aircraft and as a VIP aircraft, serving Heads of State. Various operators have indicated to keep their Fokker 70s in service beyond 2030. Comprehensive support for the Fokker 70 is available from Fokker Services and other companies. While various pre-owned Fokker 70s have been traded, it is expected that the Fokker 70 will continue to remain available for sale by their current owners, typically at affordable prices. Fokker Services neither own nor sell any aircraft. Rather, it assists prospective new operators in locating available aircraft on the market as well providing input with respect to aircraft support matters for operator business planning.This booklet provides basic information on the aircraft, its payload and performance, as well as maintenance and general support. For more specific information on the Fokker 70, please contact: [email protected] v v 1 v Great Passenger Comfort The Fokker 70 seats up to 80 passengers mostly at a comfortable 32in (81cm) seat pitch. -
Engine Failure Involving Fokker 100, VH-FWI, 41 Km South East of Geraldton Airport, Western Australia on 9 July 2019
Engine failure involving Fokker 100, VH-FWI 41 km south-east of Geraldton Airport, Western Australia on 9 July 2019 ATSB Transport Safety Report Aviation Occurrence Investigation (Defined) AO-2019-033 Final – 4 February 2021 Cover photo: Copyright ® TommyNg (Planespotters.net) Released in accordance with section 25 of the Transport Safety Investigation Act 2003 Publishing information Published by: Australian Transport Safety Bureau Postal address: PO Box 967, Civic Square ACT 2608 Office: 62 Northbourne Avenue Canberra, ACT 2601 Telephone: 1800 020 616, from overseas +61 2 6257 2463 Accident and incident notification: 1800 011 034 (24 hours) Email: [email protected] Website: www.atsb.gov.au © Commonwealth of Australia 2021 Ownership of intellectual property rights in this publication Unless otherwise noted, copyright (and any other intellectual property rights, if any) in this publication is owned by the Commonwealth of Australia. Creative Commons licence With the exception of the Coat of Arms, ATSB logo, and photos and graphics in which a third party holds copyright, this publication is licensed under a Creative Commons Attribution 3.0 Australia licence. Creative Commons Attribution 3.0 Australia Licence is a standard form licence agreement that allows you to copy, distribute, transmit and adapt this publication provided that you attribute the work. The ATSB’s preference is that you attribute this publication (and any material sourced from it) using the following wording: Source: Australian Transport Safety Bureau Copyright in material obtained from other agencies, private individuals or organisations, belongs to those agencies, individuals or organisations. Where you want to use their material you will need to contact them directly. -
Fokker 50 Information Booklet
Fokker 50 Information Booklet v v Introduction The Fokker 50 is a regional turboprop aircraft of which a total of 208 were built until 1997 by the Fokker Aircraft Company. It was the natural successor of the F-27 Friendship. Designed with a life of 90,000 landings, many Fokker 50s are currently in service with close to 30 operators worldwide in all types of operational environments. The versatile Fokker 50 is in use as a 50-seat passenger aircraft and 7-ton freighter, as well as a special mission aircraft with several governments. Various operators have indicated to keep their Fokker 50s in service beyond 2030. Comprehensive support for the Fokker 50 continues to be available from Fokker Services and other companies. While numerous pre-owned Fokker 50s have been traded, it is expected that the Fokker 50 will continue to remain available for sale by their current owners, typically at affordable prices. Fokker Services assists prospective new operators in locating available aircraft on the market as well providing input on aircraft support matters for operator business planning. Fokker Services neither own nor sell any aircraft. This information booklet provides basic details on the aircraft, its payload and performance, as well as maintenance and general support. For more specific information, please email: [email protected] v v 1 v Great Passenger Comfort The Fokker 50 seats 46 to 56 passengers at a comfortable seat pitch. Latest technology slim backrest seats may be installed, decreasing weight and increasing effective seat pitch by up to 2 inches (5 cm). Ample overhead bin and wardrobe space is available. -
F.27-200MAR Maritime - 1983, 3X
F.27-200MAR Maritime - 1983, 3x Philippines Type: Maritime Patrol Aircraft (MPA) Min Speed: 170 kt Max Speed: 330 kt Commissioned: 1983 Length: 23.1 m Wingspan: 29.0 m Height: 8.7 m Crew: 8 Empty Weight: 11204 kg Max Weight: 19773 kg Max Payload: 0 kg Propulsion: 2x Dart RDa.7 Mk.532-7L Sensors / EW: - ELT-263 - ESM, RWR, Radar Warning Receiver, Max range: 222.2 km - CA/APS-504(V)2 - Radar, Radar, Surface Search, Long-Range, Max range: 370.4 km OVERVIEW: The Fokker F27 Friendship is a turboprop airliner designed and built by the defunct Dutch aircraft manufacturer Fokker. DETAILS: VARIANTS: F27-100 - was the first production model; 44 passengers || F27-200 - uses the Dart Mk 532 engine || F27-300 Combiplane - Civil passenger/cargo aircraft || F27-300M Troopship - Military transport version for Royal Netherlands Air Force || F27-400 - "Combi" passenger/cargo aircraft, with two Rolls-Royce Dart 7 turboprop engines and large cargo door || F27-400M - Military version for US Army with designation C-31A Troopship, still in use in 2011 || F27-500 - The -500, had a 1.5 m (4 ft 11 in) longer fuselage, a return to the Dart Mk 528 engine, and accommodation for up to 52 passengers || F27-500M - Military version || F27-500F - A version of the -500 for Australia with smaller front and rear doors || F27-600 - Quick change cargo/passenger version of -200 with large cargo door || F27-700 - A F27-100 with a large cargo door || F27 200-MAR - Unarmed maritime reconnaissance version || F27 Maritime Enforcer - Armed maritime reconnaissance version || F-27 - license-built version manufactured by Fairchild Hiller in the United States || FH-227 - stretched version of the F-27, independently developed and manufactured by Fairchild Hiller in the United States. -
The Fokker S-14 Mach-Trainer for FS9,FSX and Prepar3d
The Fokker S-14 Mach-trainer for FS9,FSX and Prepar3D Fokker S-14 at Twente airforce base History The Fokker S-14 Mach-trainer was the first purpose designed and built side by side jet trainer. First flight was 19 may 1951. The aircraft was always praised for its special performance as a trainer aircraft whereby the side by side seat configuration was a great help to enable optimum communications between instructor and student pilot. Initially the aircraft was equipped with a Rolls Royce Derwent jet engine delivering some 3,600 lbf ( 16.0 kN ) of thrust. To improve the performance even further the engine was replaced with the Rolls Royce Nene Mk3 jet engine delivering some 5,100 lbf ( 22.7 kN ) of thrust. Planned license production in Brasil and with Fairchild in the USA was envisaged however these plans evaporated due to political changes in Brasil while Fairchild abandoned its production plans. During a demonstration flight in 1955 in the United States of America aircraft registration L-4 crashed due to unknown reasons taking the live of the Fokker test pilot Gerben Sonderman. Overtaken by the Lockheed T-33 and the Fouga Magister only 20 aircraft were build and used by the Royal Netherlands Air Force from 1955 till 1967. The aircraft were initially stationed at the Twente Airforce base and operated by the RNLAF Fighter Pilot School. Later they were stationed at the airforce basis of Soesterberg, Ypenburg and Woensdrecht. Fokker S-14 L-11 at Soesterberg airforce base Fokker S-14 Machtrainer Page 1 Today still 3 aircraft exist: The prototype with PH-XIV, formally owned by the National Lucht – en Ruimtevaartlabratorium, now on display at the Aviodrome museum at Lelystad airport in The Netherlands and, RNLAF Registration L-11 at the National Military Museum at the former Soesterberg RNLAF Airforce Base and RNLAF Registration L-17 currently undergoing restoration for static display at the KLu Historical Flight at Gilze-Rijen Airforce base. -
EASA Fokker F28 TC All Marks Data Sheet
TCDS No.: EASA.A.037 Fokker F28 Page 1 of 38 Issue: 06 15 July 2016 European Aviation Safety Agency EASA TYPE-CERTIFICATE DATA SHEET No. EASA.A.037 for FOKKER F28 Type Certificate Holder: Fokker Services B.V. Hoeksteen 40 2132 MS Hoofddorp The Netherlands Airworthiness Category: Large Aeroplanes For models: F28 Mark 1000 F28 Mark 0100 F28 Mark 1000C F28 Mark 0070 F28 Mark 2000 F28 Mark 3000 F28 Mark 3000C F28 Mark 3000R F28 Mark 3000RC F28 Mark 4000 TCDS No.: EASA.A.037 Fokker F28 Page 2 of 38 Issue: 06 15 July 2016 Intentionally left blank TCDS No.: EASA.A.037 Fokker F28 Page 3 of 38 Issue: 06 15 July 2016 TABLE OF CONTENTS SECTION 1 - GENERAL (ALL MODELS) ............................................................................... 4 SECTION 2 – F28 “FELLOWSHIP” SERIES .......................................................................... 5 I. Model F 28 Mark 1000, 1000C......................................................................................... 5 II. Model F28 Mark 2000 ...................................................................................................... 8 III. Model F 28 Mark 3000, 3000C....................................................................................... 10 IV. Model F28 Mark 3000R, 3000RC .................................................................................. 12 V. Model F28 Mark 4000 .................................................................................................... 14 VI. Data Pertinent to Mark 1000, 1000C, 2000, 3000, 3000C, 3000R, 3000RC and 4000 -
Technological Decline in Canadian Aviation Marionne Cronin
Document generated on 09/24/2021 11:39 p.m. Scientia Canadensis Canadian Journal of the History of Science, Technology and Medicine Revue canadienne d'histoire des sciences, des techniques et de la médecine Fading Away: Technological Decline in Canadian Aviation Marionne Cronin Volume 32, Number 2, 2009 Article abstract When Western Canada Airways began flying its pioneering air route down the URI: https://id.erudit.org/iderudit/038158ar Mackenzie Valley in 1929, it did so with a fleet comprised entirely of Fokker DOI: https://doi.org/10.7202/038158ar Super Universal aircraft. By the end of 1933, however, the airline had declared the Super Universals obsolete, replacing them with other aircraft models. In See table of contents only four years, the Fokker Super Universal had gone from state of the art to obsolescent. Exploring Western Canada Airways' decision to replace the Supers, this paper offers insight into the nature of obsolescence, demonstrating Publisher(s) that the aircraft did not achieve this status because of technical changes or dramatic technical breakthroughs in the design of other aircraft. Instead, the CSTHA/AHSTC Super Universal became obsolete because of changes in its use-context. The rise of the Great Bear Lake mineral rush, the introduction of new sorts of ISSN aircraft into the region, increased competition, and changing passenger expectations all encouraged Western Canada Airways' management to 0829-2507 (print) re-evaluate their definition of what constituted a superior technology within 1918-7750 (digital) the context of the Mackenzie Valley. While conditions in 1929 made the Super Universal the best possible choice, by the end of 1933 those circumstances had Explore this journal changed such that the Super was now obsolete. -
Technical Report A-002/2003
TECHNICAL REPORT A-002/2003 Accident of aircraft FOKKER 50, registration PH-FZE, at Melilla Airport (Spain), on 17 January 2003 Technical report A-003/2003 Accident of aircraft FOKKER 50, registration PH-FZE, at Melilla Airport (Spain), on 17 January 2003 SECRETARÍA GENERAL DE TRANSPORTES MINISTERIO DE FOMENTO COMISIÓN DE INVESTIGACIÓN DE ACCIDENTES E INCIDENTES DE AVIACIÓN CIVIL Edita: Centro de Publicaciones Secretaría General Técnica Ministerio de Fomento © NIPO: 161-03-011-0 Depósito legal: M. 23.129-2003 Imprime: Centro de Publicaciones Diseño cubierta: Carmen G. Ayala COMISIÓN DE INVESTIGACIÓN DE ACCIDENTES E INCIDENTES DE AVIACIÓN CIVIL Tel.: +34 91 597 89 63 E-mail: [email protected] C/ Fruela, 6 Fax: +34 91 463 55 35 http://www.fomento.es/ciaiac 28011 Madrid (España) Foreword This report is a technical document that reflects the point of view of the Civil Aviation Accident and Incident Investigation Commission (CIAIAC) regarding the circumstances of the accident and its causes and consequences. In accordance with the provisions of Law 21/2003 and Annex 13 to the Con- vention on International Civil Aviation, the investigation has exclusively a technical nature, without having been targeted at the declaration or assign- ment of blame or liability. The investigation has been carried out without having necessarily used legal evidence procedures and with no other basic aim than preventing future accidents. Consequently, any use of this report for purposes other than that of preven- ting future accidents may lead to erroneous conclusions or interpretations. This report has originally been issued in Spanish language. This English trans- lation is provided for information purposes only. -
Safety Aspects of Aircraft Operation in a Crosswind
View metadata, citation and similar papers at core.ac.uk brought to you by CORE provided by NLR Reports Repository NLR-TP-2001-217 Safety aspectsaspects of aircraft operations iinn crosswind G.W.H. van Es, P.J. van der Geest and T. M.H. Nieuwpoort Nationaal Lucht- en Ruimtevaartlaboratorium National Aerospace Laboratory NLR NLR-TP-2001-217 Safety aspects of aircraft operations in crosswind G.W.H. van Es, P.J. van der Geest and T. M.H. Nieuwpoort This report is based on a presentation held at the Flight Safety Foundation FSF, 11th Annual European Aviation Safety Seminar, Amsterdam on March 8-10, 1999. The presented study was conducted for the Dutch Ministry of Transportation, Public Works and Water Management. The contents of this report may be cited on condition that full credit is given to NLR and the authors. Division: Air Transport Issued: May 2001 Classification of title: Unclassified -3- NLR-TP-2001-217 Summary In the next decades, airline operations will continue to grow. It is expected that the number of departures will almost double by 2016. This increase in departures requires an increase of the capacity of many airports worldwide. An important aspect, which affects the potential growth of airport capacity, as well as the optimal layout of new airports, is the crosswind limit imposed on runway availability. In order to assess the safety margins inherent to current operational crosswind limitations, and to get an impression of the impact on safety margins, if crosswind limitations would be relaxed, this reports gives a broad overview of all safety aspects related to operations in crosswind conditions.