SAE Steel Grades
Total Page:16
File Type:pdf, Size:1020Kb
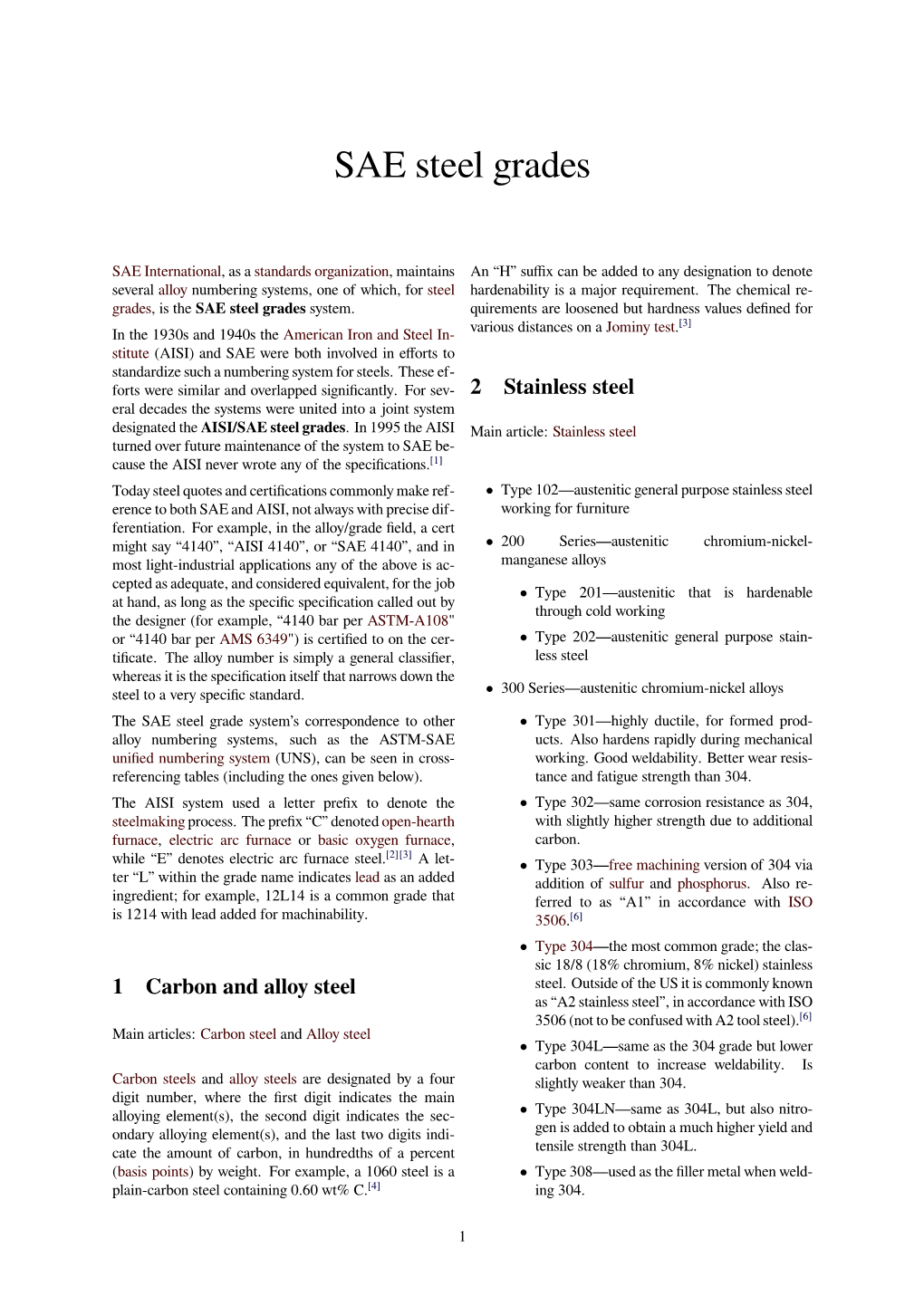
Load more
Recommended publications
-
(12) Patent Application Publication (10) Pub. No.: US 2013/0062568 A1 Miralles (43) Pub
US 2013 OO62568A1 (19) United States (12) Patent Application Publication (10) Pub. No.: US 2013/0062568 A1 Miralles (43) Pub. Date: Mar. 14, 2013 (54) ACID CLEANING AND CORROSION Publication Classification INHIBITING COMPOSITIONS COMPRISING GLUCONCACD (51) Int. Cl. C09K 5/6 (2006.01) (71) Applicant: Ecolab USA Inc., St. Paul, MN (US) (52) U.S. Cl. CPC ...................................... C09K 15/16 (2013.01) (72) Inventor: Altony Miralles, Woodbury, MN (US) USPC .......................................................... 252/392 (73) Assignee: ECOLAB USA INC., St. Paul, MN (US) (57) ABSTRACT (21) Appl. No.: 13/674,539 A biodegradable acid cleaning composition for cleaning stainless steel, and other Surfaces is disclosed. The composi (22) Filed: Nov. 12, 2012 tion comprises urea sulfate in combination with gluconic acid which serves as a corrosion inhibitor. The composition retains Related U.S. Application Data the cleaning and corrosion prevention properties of similar (60) Continuation of application No. 13/344.982, filed on phosphoric acid solutions but is safe for the environment and Jan. 6, 2012, which is a continuation of application No. is less expensive to produce. Applicants have surprisingly 12/887,660, filed on Sep. 22, 2010, now abandoned, found that the traditionally alkaline corrosion inhibitor, glu which is a division of application No. 127751,674, filed conic acid, can work effectively in an acidic cleaning com on Mar. 31, 2010, now Pat. No. 7,828,908. position. US 2013/0062568 A1 Mar. 14, 2013 ACID CLEANING AND CORROSION also are used to improve corrosion resistance and enhance INHIBITING COMPOSITIONS COMPRISING brightness of the base metal surface. GLUCONCACD 0008. One of the problems which arises in the use of steel is its corrosion, either by the atmosphere or by the environ CROSS-REFERENCE TO RELATED ment in which it is used. -
High-Carbon Steels: Fully Pearlitic Microstructures and Applications
© 2005 ASM International. All Rights Reserved. www.asminternational.org Steels: Processing, Structure, and Performance (#05140G) CHAPTER 15 High-Carbon Steels: Fully Pearlitic Microstructures and Applications Introduction THE TRANSFORMATION OF AUSTENITE to pearlite has been de- scribed in Chapter 4, “Pearlite, Ferrite, and Cementite,” and Chapter 13, “Normalizing, Annealing, and Spheroidizing Treatments; Ferrite/Pearlite Microstructures in Medium-Carbon Steels,” which have shown that as microstructure becomes fully pearlitic as steel carbon content approaches the eutectiod composition, around 0.80% carbon, strength increases, but resistance to cleavage fracture decreases. This chapter describes the me- chanical properties and demanding applications for which steels with fully pearlitic microstructures are well suited. With increasing cooling rates in the pearlite continuous cooling trans- formation range, or with isothermal transformation temperatures ap- proaching the pearlite nose of isothermal transformation diagrams, Fig. 4.3 in Chapter 4, the interlamellar spacing of pearlitic ferrite and cementite becomes very fine. As a result, for most ferrite/pearlite microstructures, the interlamellar spacing is too fine to be resolved in the light microscope, and the pearlite appears uniformly dark. Therefore, to resolve the inter- lamellar spacing of pearlite, scanning electron microscopy, and for the finest spacings, transmission electron microscopy (TEM), are necessary to resolve the two-phase structure of pearlite. Figure 15.1 is a TEM mi- crograph showing very fine interlamellar structure in a colony of pearlite from a high-carbon steel rail. This remarkable composite structure of duc- © 2005 ASM International. All Rights Reserved. www.asminternational.org Steels: Processing, Structure, and Performance (#05140G) 282 / Steels: Processing, Structure, and Performance tile ferrite and high-strength cementite is the base microstructure for rail and the starting microstructure for high-strength wire applications. -
48-51 Characterization Martensitic Stainless Steel Surgica.Pdf
CHARACTERIZATION OF LOCALLY PRODUCED MARTENSITIC STAINLESS STEEL SURGICAL GRADE AISI 420A By Muhammad Kamran, Faraz Hussain, Taqi Zahid Butt, Fahad Riaz* Abstract The Martensitic stainless steel surgical grade AISI 420A is one of the major alloys being used in the production of surgical instruments in Pakistan. Till today, this alloy is being imported from Japan and France. Recently this grade has been developed in Pakistan. In this study this locally produced Martensitic stainless steel surgical grade AISI 420A was investigated. The sheet samples were tested for their composition, heat treated by austenizing at 1000 + 20°C, 0 quenched in N2 gas followed by tempering at 200 C and finally tested for their mechanical properties. It was observed that chemical composition fall within the standard composition with minor changes. It was also observed that hardness and tensile properties are within range. Introduction Pakistan is one of the largest countries producing and supplying surgical instruments all over the world. Tonnages of raw material are required for the production purposes. Surgical industry of Pakistan holds a history of more than 100 years, when some British doctors got their surgical instruments repaired from the skilled workers of Sialkot and that was the foundation of Sialkot surgical industry. [1] Surgical Instruments Manufacturers Association of Pakistan (SIMAP) was established during 1958 with an aim to help solving the problems of surgical community. Surgical association has more than 2300 members till date, who are grossly engaged in manufacturing of surgical instruments to meet their export commitments in the International Market. The value of exports of surgical instruments for the financial year 2007-2008 was US $255 Million. -
UDDEHOLM STAVAX® ESR © UDDEHOLMS AB No Part of This Publication May Be Reproduced Or Transmitted for Commercial Purposes Without Permission of the Copyright Holder
UDDEHOLM STAVAX® ESR © UDDEHOLMS AB No part of this publication may be reproduced or transmitted for commercial purposes without permission of the copyright holder. This information is based on our present state of knowledge and is intended to provide general notes on our products and their uses. It should not therefore be construed as a warranty of specific properties of the products described or a warranty for fitness for a particular purpose. Classified according to EU Directive 1999/45/EC For further information see our “Material Safety Data Sheets”. Edition 11, 05.2013 The latest revised edition of this brochure is the English version, SS-EN ISO 9001 which is always published on our web site www.uddeholm.com SS-EN ISO 14001 UDDEHOLM STAVAX ESR UDDEHOLM STAVAX ESR Uddeholm Stavax ESR is a premium stainless mould steel for small and medium inserts and cores. Uddeholm Stavax ESR combines corrosion and wear resistance with excellent polishability, good machinability and stability in hardening. Mould maintenance requirement is reduced by assuring that core and cavity surfaces retain their original finish over extended operating periods. When compared with non stainless mould steel, Uddeholm Stavax ESR offers lower production costs by maintaining rust free cooling channels, assuring consistent cooling and cycle time. This classic stainless tool steel is the right choice when rust in production is unacceptable and where requirements for good hygiene are high, as within the medical industry, optical industry and for other high quality transparent parts. Uddeholm Stavax ESR is a part of the Uddeholm Stainless Concept 3 UDDEHOLM STAVAX ESR General Applications Uddeholm Stavax ESR is a premium grade Uddeholm Stavax ESR is recommended for all stainless tool steel with the following proper- types of moulding tools and its special proper- ties: ties make it particularly suitable for moulds •good corrosion resistance with the following demands: •excellent polishability • Corrosion/staining resistance, i.e. -
Carbon Steel
EN380 12-wk Exam Solution Fall 2019 Carbon Steel. 1. [19 pts] Three compositions of plain carbon steel are cooled very slowly in a turned-off furnace from ≈ 830◦C (see phase diagram below). For each composition, the FCC grains of γ−austenite (prior to transformation) are shown in an optical micrograph of the material surface. Sketch and label the phases making up the microstructures present in the right hand micrograph just after the austenite has completed transformation (note: the gray outlines of the prior γ grains may prove helpful). (a) [4 pts] C0 = 0:42% C (by wt). 830◦C 726◦C EN380 12-wk Exam Solution Page 1 Fall 2019 EN380 12-wk Exam Solution Fall 2019 (b) [4 pts] C0 = 0:80% C (by wt). 830◦C 726◦C (c) [4 pts] C0 = 1:05% C (by wt). 830◦C 726◦C (d) [7 pts] For the composition of part (c), C0 = 1:05% C (by wt), calculate the fraction of the solid that is pearlite at 726◦C. CF e3C − C0 6:67% − 1:05% Wpearlite = Wγ at 728◦C = = = 95:74% Pearlite CF e3C − Cγ 6:67% − 0:8% EN380 12-wk Exam Solution Page 2 Fall 2019 EN380 12-wk Exam Solution Fall 2019 2. [11 pts] Write in the correct term for each of the following related to carbon steels[1 pt each] (terms will be used exactly once): This material features carbon content in excess of Cast Iron 2:0% and is known for its excellent hardness, wear resistance, machinability and castability. -
Chromium Martensitic Hot-Work Tool Steels Hot-Work Tool Steels Division for Engineering Sciences, Physics and Mathematics Department of Materials Engineering
Chromium martensitic Sjöström Johnny hot-work tool steels Division for Engineering Sciences, Physics and Mathematics Department of Materials Engineering Chromium martensitic hot-work tool steels martensitic hot-work Chromium Chromium martensitic hot-work tool steel (AISI H13) was developed to endure the severe conditions of high temperature metal forming operations such as die cast- ing, hot rolling, extrusion and hot forging. The mechanical properties are high and strongly connected to the microstructure and have been improved over the years by Johnny Sjöström alloying and heat treatment. Damages still occur and one of the most common failure mechanisms is thermal fatigue. In this thesis the thermal fatigue damage on hot forming tools has been studied. Several types of hot work tools steels have been experimentally tested and the mi- crostructural changes during thermal fatigue have been evaluated. The tool material behaviour has also been simulated to support the integration of die design, tool steel properties and use. Chromium martensitic The general aim of this thesis is to increase the knowledge of the chromium martensitic hot-work tool steel damage, performance and microstructure. hot-work tool steels – damage, performance and microstructure Karlstad University Studies Karlstad University Studies ISSN 1403-8099 2004:52 ISBN 91-85335-21-5 Johnny Sjöström Chromium martensitic hot-work tool steels – damage, performance and microstructure Karlstad University Studies 2004:52 Johnny Sjöström. Chromium martensitic hot-work tool steels -
Preparation and Mechanical Behavior of Ultra-High Strength Low-Carbon Steel
materials Article Preparation and Mechanical Behavior of Ultra-High Strength Low-Carbon Steel Zhiqing Lv 1,2,*, Lihua Qian 1, Shuai Liu 1, Le Zhan 1 and Siji Qin 1 1 Key Laboratory of Advanced Forging & Stamping Technology and Science, Ministry of Education of China Yanshan University, Qinhuangdao 066004, China; [email protected] (L.Q.); [email protected] (S.L.); [email protected] (L.Z.); [email protected] (S.Q.) 2 State Key Laboratory of Metastable Material Science and Technology, Yanshan University, Qinhuangdao 066004, China * Correspondence: [email protected] Received: 16 December 2019; Accepted: 14 January 2020; Published: 18 January 2020 Abstract: The low-carbon steel (~0.12 wt%) with complete martensite structure, obtained by quenching, was cold rolled to get the high-strength steel sheets. Then, the mechanical properties of the sheets were measured at different angles to the rolling direction, and the microstructural evolution of low-carbon martensite with cold rolling reduction was observed. The results show that the hardness and the strength gradually increase with increasing rolling reduction, while the elongation and impact toughness obviously decrease. The strength of the sheets with the same rolling reduction are different at the angles of 0◦, 45◦, and 90◦ to the rolling direction. The tensile strength (elongation) along the rolling direction is higher than that in the other two directions, but the differences between them are not obvious. When the aging was performed at a low temperature, the strength of the initial martensite and deformed martensite increased with increasing aging time during the early stages of aging, followed by a gradual decrease with further aging. -
Chemical Analyses of Standard Sizes
SECTION P CPHEMICAL ANALYSES OF STANDARD SIZES STANDARD METALS AND DESIGNATION SYSTEMS . 2 EFFECTS OF COMMON ALLOYING ELEMENTS IN STEEL . 3-4 DESIGNATION OF CARBON STEELS . 5-7 DESIGNATION OF ALLOY STEELS .......................... 8-12 STAINLESS AND HEAT RESISTING STEELS .................. 13-17 HIGH TEMPERATURE HIGH STRENGTH ALLOYS . 18 DESIGNATION OF ALLUMINUM ALLOYS . 19-20 OIL TOOL MATERIALS . 21 API SPECIFICATION REQUIREMENTS ....................... 22 Sec. P Page 1 STANDARD METALS AND DESIGNATION SYSTEMS UNS Studies have been made in the metals industry for the purpose of establishing certain “standard” metals and eliminating as much as possible the manufacture of other metals which vary only slightly in composition from the standard metals. These standard metals are selected on the basis of serving the significant metal- lurgical and engineering needs of fabricators and users of metal products. UNIFIED NUMBERING SYSTEM: UNS is a system of designations established in accordance with ASTM E 527 and SAE J1086, Recommended Practice for Numbering Metals and Alloys. Its purpose is to provide a means of correlat- ing systems in use by such organizations as American Iron and Steel Institute (AISI), American Society for Testing Materials (ASTM), and Society of Automotive Engineers (SAE), as well as individual users and producers. UNS designa- tion assignments are processed by the SAE, the ASTM, or other relevant trade associations. Each of these assignors has the responsibility for administering a specific UNS series of designations. Each considers requests for the assignment of new UNS designations, and informs the applicants of the action taken. UNS designation assignors report immediately to the office of the Unified Numbering System for Metals and Alloys the details of each new assignment for inclusion into the system. -
Phase Transformations / Hardenability (Jominy End-Quench)
Phase Transformations / Hardenability (Jominy End-Quench) Presentation Fall '15 (2151) Experiment #7 Phase Transformations & Hardenability of Steels (Jominy End-Quench Test) Jominy End Quench Test ASTM Standard A255 Concept Non-equilibrium phase transformations Continuous cooling transformation diagram & Critical cooling rates Concept of Hardenability Effect of %C & alloying on Hardenability Objective Compare hardenability of 1045 & 4340 steels (very similar wt% C) 2 Review: Eutectoid Reaction in Steels γ (Austenite , FCC) → α (Ferrite , BCC) + Fe 3C (Cementite , FC Orthorhombic) No time element; temperature change assumed slow enough for quasi-equilibrium at all points γ (Austenite) → α (Ferrite) + Fe 3C (Cementite) 0.76 %C → 0.022 %C + 6.70 %C Schematic representations of the microstructures for an iron-carbon alloy of eutectoid composition (0.76 wt% C) above and below the eutectoid temperature. 3 Fig. 9.26 from Callister & Rethwisch, Materials Science & Engineering, An Introduction, 8 th ed., J. Wiley & Sons, 2010 MECE-306 Materials Science Apps Lab 1 Phase Transformations / Hardenability (Jominy End-Quench) Presentation Fall '15 (2151) Isothermal Transformations of Eutectoid Steel – Pearlite Isothermal transformation diagram for a eutctoid Austenite (unstable) iron-carbon alloy, with superimposed isothermal heat treatment curve (ABCD ). Microstructures before, during, and after the austenite-to-pearlite transformation are shown. Notice fast transformation creates “fine” pearlite and slow transform. This figure is nicknamed the “T-T-T” plot (for creates time-temperature-transformation) “coarse” pearlite! 4 Fig. 10.14 from Callister & Rethwisch, Materials Science & Engineering, An Introduction, 8 th ed., J. Wiley & Sons, 2010 Isothermal Transformations of Hyper-Eutectoid Carbon Steel Isothermal transformation diagram for a 1.13 wt% C iron-carbon alloy: A, austenite; C, proeutectoid cementite; P, pearlite. -
The Effect of Austenitizing Conditions on the Mechanical Properties and on Hardenability of Hardened Carbon Steel*
52 The Effect of Austenitizing Conditions on the Mechanical Properties and on Hardenability of Hardened Carbon Steel* By Kazuaki Iijima** The present study was performed to determine the effect of austenitizing conditions on the mechanical properties and hardenability of hardened eutectおid carbon steel, and ascertained tbe relation between those properties and the auste- nitic grain size. The mechanical properties were obtained from as-hardened 0.80% C steel by a torsion test, and the hardenability fr om 0.85% C steel by a Jominy test. The austenitizing conditions were affected by austenitizing temperatures and periods, and austenitizing temperatures in the prior heat treatment. The results obtained were as follows: (i) With the increase of the austenitizing temperature, the toughne8s of hardened steel decreased, the hardenability increased, and the austenitic grain size became coarser; (ii) prokmgation of thle austenitizing time gives the same effbct on tllose properties as does the increase of austenitizing temperature, but in some cases, an abrupt change in toughness and hardenability regardless of the austenitic grain size was observed; (iii) even when tho austenitizing temperature fbr fi nal hardening was held constant (800℃), the toughness and the hardenability were found to be remarkably affected by the austenitizing temperature fbr such prior heat treatment as annealing, hardening or hardening followed by annealing; with the increasing austenitizing temperature, the toughness decreased and the hardenability increased. But in all cases, the austenitic grain size was scarcely affected by the prior heat treatment; (iv) the above results suggest that the decrease in toughness and the ihcrease in hlardenability due to over-heating may be attributed not only to the austenic grain coarsening but algo to some changes in the austenite caused by the overheating process itself. -
High-Strength Low-Alloy Steels
metals Editorial High-Strength Low-Alloy Steels Ricardo Branco 1,* and Filippo Berto 2 1 CEMMPRE, Department of Mechanical Engineering, University of Coimbra, 3030-78 Coimbra, Portugal 2 Department of Mechanical and Industrial Engineering, Norwegian University of Science and Technology, 7491 Trondheim, Norway; fi[email protected] * Correspondence: [email protected] 1. Introduction Modern industry, driven by the recent environmental policies, faces an urgent need for the production of lighter and more environmentally friendly components. High-strength low-alloy steels are key materials in this challenging scenario because they provide a balanced combination of properties, such as strength, toughness, formability, weldability, and corrosion resistance. These features make them ideal for a myriad of engineering applications which experience complex loading conditions and aggressive media, such as aeronautical and automotive components, railway parts, offshore structures, oil and gas pipelines, power transmission towers, construction machinery, among others. The goal of this Special Issue is to foster the dissemination of the latest research devoted to high- strength low-alloy (HSLA) steels from different perspectives. 2. Contributions The understanding of the microstructure features and their dependence on the me- chanical behaviour is of essential importance for the development of safe and durable components as well as to extend the scope of application of the high-strength low-alloy steels. This may justify the intense research conducted on the triangular relationship be- tween the microstructure, the processing techniques, and the final mechanical properties. Citation: Branco, R.; Berto, F. Solis-Bravo et al. [1] addressed the relationship between the precipitate morphology and High-Strength Low-Alloy Steels. -
Surface Vehicle Standard
REV. SURFACE JUN2006 ® J20 VEHICLE Issued 1944-01 STANDARD Revised 2006-06 Superseding J20 MAY2004 Coolant System Hoses 1. Scope This SAE Standard covers reinforced and flexible hoses intended for use in water and ethylene glycol-based engine-coolant system applications. 1.1 Rationale Shelf life was added at the request of the USA department of Defense. 2. References 2.1 Applicable Publications The following publications form a part of the specification to the extent specified herein. Unless otherwise indicated, the latest revision of SAE publications shall apply. 2.1.1 SAE PUBLICATIONS Available from SAE, 400 Commonwealth Drive, Warrendale, PA 15096-0001, Tel: 877-606-7323 (inside USA and Canada) or 724-776-4970 (outside USA), www.sae.org. SAE J1231—Formed Tube Ends for Hose Connections and Hose Fittings SAE J1508—Hose Clamp Specification SAE J1610—Test Method for Evaluating the Sealing Capability of Hose Connections with a PVT Test Facility SAE J1638—Compression Set of Hoses or Solid Discs SAE J1684—Test Method for Evaluating the Electrochemical Resistance of Coolant System Hoses and Materials SAE J2370—Geometric Dimensions and Tolerancing for Curved Hose SAE J2387—Dimensions and Tolerances for Coolant System Hoses SAE J2605—Non-Contact Hose Measurement Study 1 SAE Technical Standards Board Rules provide that: “This report is published by SAE to advance the state of technical and engineering sciences. The use of this report is entirely voluntary, and its applicability and suitability for any particular use, including any patent infringement arising therefrom, is the sole responsibility of the user.” SAE reviews each technical report at least every five years at which time it may be reaffirmed, revised, or cancelled.