Mars Sample Return Spacecraft Systems Architecture
Total Page:16
File Type:pdf, Size:1020Kb
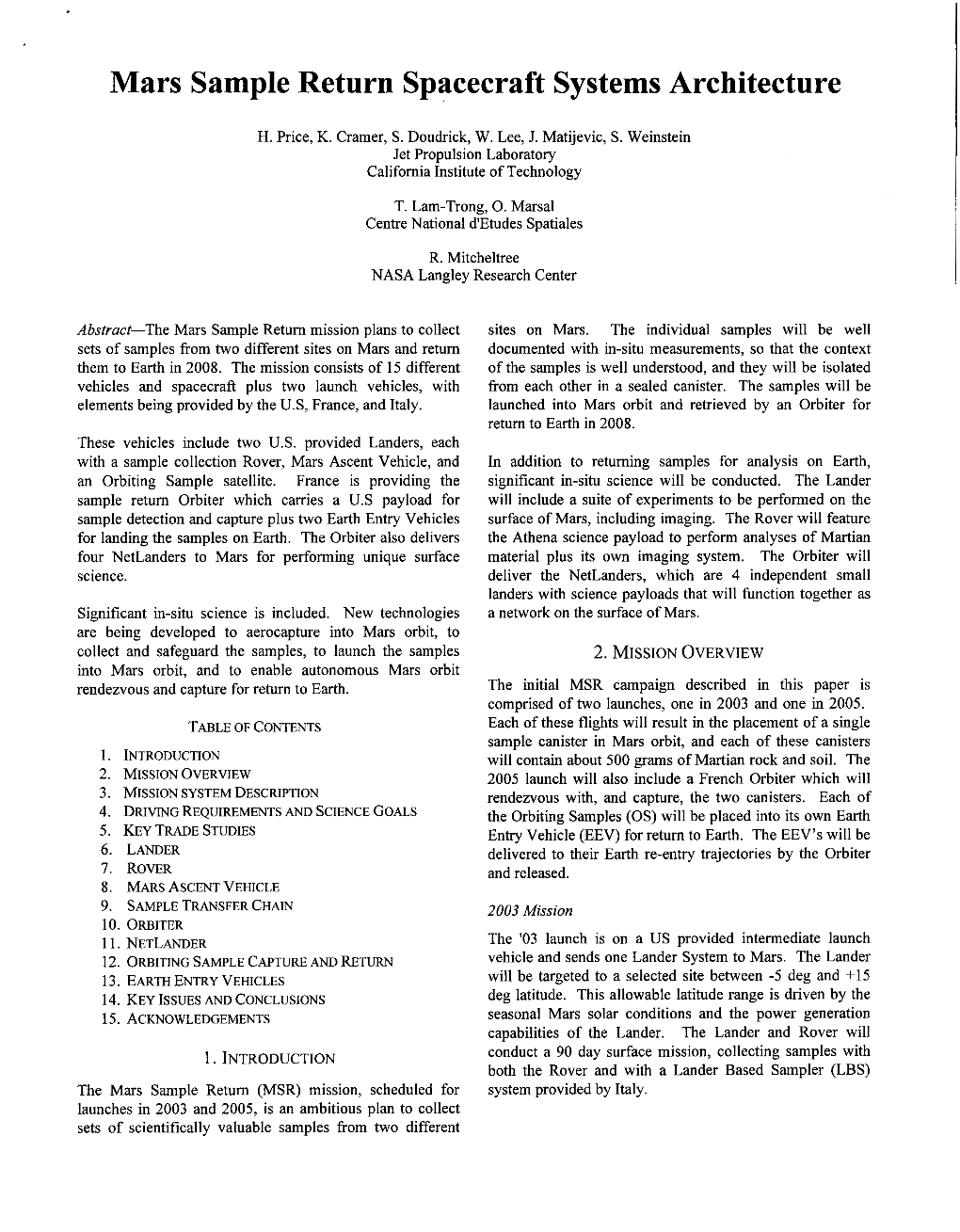
Load more
Recommended publications
-
Lessons from Insight for Future Planetary Seismology
Open Archive Toulouse Archive Ouverte (OATAO ) OATAO is an open access repository that collects the wor of some Toulouse researchers and ma es it freely available over the web where possible. This is a publisher's version published in: https://oatao.univ-toulouse.fr/26931 Official URL : https://doi.org/10.1029/2019JE006353 To cite this version : Panning, M. P. and Pike, W. T. and Lognonné, Philippe,... [et al.]On͈Deck Seismology: Lessons from InSight for Future Planetary Seismology. (2020) Journal of Geophysical Research: Planets, 125 (4). ISSN 2169-9097 Any correspondence concerning this service should be sent to the repository administrator: [email protected] RESEARCH ARTICLE On-Deck Seismology: Lessons from InSight for Future 10.1029/2019JE006353 Planetary Seismology Special Section: 1 2 3 1 4 5 InSightatMars M. P. Panning , W. T. Pike , P. Lognonné , W. B. Banerdt , N. Murdoch , D. Banfield , C. Charalambous2 , S. Kedar1, R. D. Lorenz6 , A. G. Marusiak7 , J. B. McClean2,8 ,C. 1 9 2 10 Key Points: Nunn , S. C. Stähler ,A.E.Stott , and T. Warren • Based on InSight recordings, 1 2 atmospheric noise is amplified for Jet Propulsion Laboratory, California Institute of Technology, Pasadena, CA, USA, Department of Electrical and seismic sensors on deck, consistent Electronic Engineering, Imperial College London, London, UK, 3Planetology and Space Science Team, Université de with Viking observations Paris, Institut de Physique du Globe, CNRS, Paris, France, 4Department of Electronics, Optronics and Signal Processing, • -
The Reference Mission of the NASA Mars Exploration Study Team
NASA Special Publication 6107 Human Exploration of Mars: The Reference Mission of the NASA Mars Exploration Study Team Stephen J. Hoffman, Editor David I. Kaplan, Editor Lyndon B. Johnson Space Center Houston, Texas July 1997 NASA Special Publication 6107 Human Exploration of Mars: The Reference Mission of the NASA Mars Exploration Study Team Stephen J. Hoffman, Editor Science Applications International Corporation Houston, Texas David I. Kaplan, Editor Lyndon B. Johnson Space Center Houston, Texas July 1997 This publication is available from the NASA Center for AeroSpace Information, 800 Elkridge Landing Road, Linthicum Heights, MD 21090-2934 (301) 621-0390. Foreword Mars has long beckoned to humankind interest in this fellow traveler of the solar from its travels high in the night sky. The system, adding impetus for exploration. ancients assumed this rust-red wanderer was Over the past several years studies the god of war and christened it with the have been conducted on various approaches name we still use today. to exploring Earth’s sister planet Mars. Much Early explorers armed with newly has been learned, and each study brings us invented telescopes discovered that this closer to realizing the goal of sending humans planet exhibited seasonal changes in color, to conduct science on the Red Planet and was subjected to dust storms that encircled explore its mysteries. The approach described the globe, and may have even had channels in this publication represents a culmination of that crisscrossed its surface. these efforts but should not be considered the final solution. It is our intent that this Recent explorers, using robotic document serve as a reference from which we surrogates to extend their reach, have can continuously compare and contrast other discovered that Mars is even more complex new innovative approaches to achieve our and fascinating—a planet peppered with long-term goal. -
EDL – Lessons Learned and Recommendations
."#!(*"# 0 1(%"##" !)"#!(*"#* 0 1"!#"("#"#(-$" ."!##("""*#!#$*#( "" !#!#0 1%"#"! /!##"*!###"#" #"#!$#!##!("""-"!"##&!%%!%&# $!!# %"##"*!%#'##(#!"##"#!$$# /25-!&""$!)# %"##!""*&""#!$#$! !$# $##"##%#(# ! "#"-! *#"!,021 ""# !"$!+031 !" )!%+041 #!( !"!# #$!"+051 # #$! !%#-" $##"!#""#$#$! %"##"#!#(- IPPW Enabled International Collaborations in EDL – Lessons Learned and Recommendations: Ethiraj Venkatapathy1, Chief Technologist, Entry Systems and Technology Division, NASA ARC, 2 Ali Gülhan , Department Head, Supersonic and Hypersonic Technologies Department, DLR, Cologne, and Michelle Munk3, Principal Technologist, EDL, Space Technology Mission Directorate, NASA. 1 NASA Ames Research Center, Moffett Field, CA [email protected]. 2 Deutsches Zentrum für Luft- und Raumfahrt e.V. (DLR), German Aerospace Center, [email protected] 3 NASA Langley Research Center, Hampron, VA. [email protected] Abstract of the Proposed Talk: One of the goals of IPPW has been to bring about international collaboration. Establishing collaboration, especially in the area of EDL, can present numerous frustrating challenges. IPPW presents opportunities to present advances in various technology areas. It allows for opportunity for general discussion. Evaluating collaboration potential requires open dialogue as to the needs of the parties and what critical capabilities each party possesses. Understanding opportunities for collaboration as well as the rules and regulations that govern collaboration are essential. The authors of this proposed talk have explored and established collaboration in multiple areas of interest to IPPW community. The authors will present examples that illustrate the motivations for the partnership, our common goals, and the unique capabilities of each party. The first example involves earth entry of a large asteroid and break-up. NASA Ames is leading an effort for the agency to assess and estimate the threat posed by large asteroids under the Asteroid Threat Assessment Project (ATAP). -
High Performance Mars Ascent Vehicles, Earth Return Vehicles and “All-Up” Launch Strategy for Low Cost Sample Return
Concepts and Approaches for Mars Exploration (2012) 4356.pdf HIGH PERFORMANCE MARS ASCENT VEHICLES, EARTH RETURN VEHICLES AND “ALL-UP” LAUNCH STRATEGY FOR LOW COST SAMPLE RETURN. L. G. Lemke1, C. R. Stoker1, B. J. Glass1, J. S. Karcz1, J. V. Bowles1, A. A. Gonzales1, S. Davis2 . 1NASA Ames Research Center, 2SpaceX Company. Introduction: Robotic missions to return carefully straints force a complex architecture to be fractionated selected samples of Mars atmosphere, regolith, and into smaller pieces and implemented over a longer rock have been actively studied and advocated by time than might otherwise be desireable. One conse- NASA for at least the last 15 years and remain a very quence of this mission fractionation is that the DSA high priority objective of both the Science Mission uses a small (≈ 300 kg) Mars Ascent Vehicle (MAV) Directorate (SMD) and the Human Exploration and with a ΔV of ≈ 4 km/s—just enough to attain low Mars Operations Mission Directorate (HEOMD) programs. orbit. This, in turn requires MOR to place the sample As a practical matter, such missions are intrinsically container in a hermetically sealed Earth Return Vehicle among the most complex robotic planetary missions (ERV) before departure toward Earth. The Mars Or- that can be engineered. The current Decadal Survey biter in the DSA is itself a large and highly capable Architecture (DSA) incorporates virtually every tech- spacecraft requiring a dedicated launch and mission nical capability in the robotic spaceflight repertoire— control. atmospheric Entry Descent and Landing (EDL) at A Johnson Space Center (JSC) study con- Mars, Mars surface mobility, subsurface sample acqui- ducted by the then Office of Exploration [1] examined sition, autonomous sample handling for planetary pro- the cost and risk benefits of MSR alternatives not re- tection, Mars surface rendezvous with rovers, launch quiring MOR. -
Sanjay Limaye US Lead-Investigator Ludmila Zasova Russian Lead-Investigator Steering Committee K
Answer to the Call for a Medium-size mission opportunity in ESA’s Science Programme for a launch in 2022 (Cosmic Vision 2015-2025) EuropEan VEnus ExplorEr An in-situ mission to Venus Eric chassEfièrE EVE Principal Investigator IDES, Univ. Paris-Sud Orsay & CNRS Universite Paris-Sud, Orsay colin Wilson Co-Principal Investigator Dept Atm. Ocean. Planet. Phys. Oxford University, Oxford Takeshi imamura Japanese Lead-Investigator sanjay Limaye US Lead-Investigator LudmiLa Zasova Russian Lead-Investigator Steering Committee K. Aplin (UK) S. Lebonnois (France) K. Baines (USA) J. Leitner (Austria) T. Balint (USA) S. Limaye (USA) J. Blamont (France) J. Lopez-Moreno (Spain) E. Chassefière(F rance) B. Marty (France) C. Cochrane (UK) M. Moreira (France) Cs. Ferencz (Hungary) S. Pogrebenko (The Neth.) F. Ferri (Italy) A. Rodin (Russia) M. Gerasimov (Russia) J. Whiteway (Canada) T. Imamura (Japan) C. Wilson (UK) O. Korablev (Russia) L. Zasova (Russia) Sanjay Limaye Ludmilla Zasova Eric Chassefière Takeshi Imamura Colin Wilson University of IKI IDES ISAS/JAXA University of Oxford Wisconsin-Madison Laboratory of Planetary Space Science and Spectroscopy Univ. Paris-Sud Orsay & Engineering Center Space Research Institute CNRS 3-1-1, Yoshinodai, 1225 West Dayton Street Russian Academy of Sciences Universite Paris-Sud, Bat. 504. Sagamihara Dept of Physics Madison, Wisconsin, Profsoyusnaya 84/32 91405 ORSAY Cedex Kanagawa 229-8510 Parks Road 53706, USA Moscow 117997, Russia FRANCE Japan Oxford OX1 3PU Tel +1 608 262 9541 Tel +7-495-333-3466 Tel 33 1 69 15 67 48 Tel +81-42-759-8179 Tel 44 (0)1-865-272-086 Fax +1 608 235 4302 Fax +7-495-333-4455 Fax 33 1 69 15 49 11 Fax +81-42-759-8575 Fax 44 (0)1-865-272-923 [email protected] [email protected] [email protected] [email protected] [email protected] European Venus Explorer – Cosmic Vision 2015 – 2025 List of EVE Co-Investigators NAME AFFILIATION NAME AFFILIATION NAME AFFILIATION AUSTRIA Migliorini, A. -
Mars Earth Return Vehicle (MERV) Propulsion Options
Mars Earth Return Vehicle (MERV) Propulsion Options Steven R. Oleson,1 Melissa L. McGuire,2 Laura Burke,3 James Fincannon,4 Joe Warner,5 Glenn Williams,6 and Thomas Parkey7 NASA Glenn Research Center, Cleveland, Ohio 44135 Tony Colozza,8 Jim Fittje,9 Mike Martini,10 and Tom Packard11 Analex Corporation, Cleveland, Ohio 44135 Joseph Hemminger12 N&R Engineering, Cleveland, Ohio 44135 John Gyekenyesi13 ASRC Engineering, Cleveland, Ohio 44135 The COMPASS Team was tasked with the design of a Mars Sample Return Vehicle. The current Mars sample return mission is a joint National Aeronautics and Space Administration (NASA) and European Space Agency (ESA) mission, with ESA contributing the launch vehicle for the Mars Sample Return Vehicle. The COMPASS Team ran a series of design trades for this Mars sample return vehicle. Four design options were investigated: Chemical Return /solar electric propulsion (SEP) stage outbound, all-SEP, all chemical and chemical with aerobraking. The all-SEP and Chemical with aerobraking were deemed the best choices for comparison. SEP can eliminate both the Earth flyby and the aerobraking maneuver (both considered high risk by the Mars Sample Return Project) required by the chemical propulsion option but also require long low thrust spiral times. However this is offset somewhat by the chemical/aerobrake missions use of an Earth flyby and aerobraking which also take many months. Cost and risk analyses are used to further differentiate the all-SEP and Chemical/Aerobrake options. 1COMPASS Lead, DSB0, 21000 Brookpark Road, and AIAA Senior Member. 2COMPASS Integration Lead, DSB0, 21000 Brookpark Road, non-member. 3Mission Designer, DSB0, 21000 Brookpark Road, and Non-Member. -
PSS Mars Oct 08
Planetary Sciences Subcommittee October 2-3, 2008 Doug McCuistion Director, Mars Exploration Program 2 Memorable Scenes Phoenix Meteorology is Changing from Phoenix Spacecraft thruster expose water-ice in permafrost SSI camera images water- ice particles clouds and Top: Robotic Arm delivers their movement soil+ice dug from trench to the Thermal Evolved Gas Analyzer (TEGA) Bottom: TEGA CELL #0 after receiving ice-bearing sample Phoenix images early morning water- Dust Devil frost. Lasts longer every morning as winter approaches Robotic Arm digs trench and discovers water ice. SSI camera documents H2O SSI camera images multiple sublimation. dust devils TEGA’s mass spectrometer confirms presence of water- ice on Mars. 3 4 Phoenix Meteorology is Changing A White Christmas on Mars? Atmospheric pressure and temperature data have been recorded at the Phoenix landing site every Virga, in the 2 seconds since landing. from of water- snow, has been detected in the atmosphere, getting nearer Dust cloud to the ground approaching daily. Morning wind is up to about 9 mph; enough to rattle the solar arrays but not to damage the spacecraft. 5 6 The End is in Sight Available power (measurement based) WCL Cells Utilized power (modeled) Command Moratorium Command a Conjunction MECA’s Wet Chemistry Lab (WCL) MECA’s Optical Microscope: highest resolution (4 microns/pixel) b discovers perchlorates in soil! optical images delivered from any planetary surface other than earth c AFM Tip Perchlorates: Powerful, but d stable oxidant. Very hydroscopic. Survival heater -
Mars Exploration Study Workshop II: Report of a Workshop Sponsored By
NASA Conference Publication 3243 Mars Exploration Study Workshop II Report of a workshop sponsored by NASA Lyndon B. Johnson Space Center and held at the Ames Research Center May 24-25, 1993 Michael B. Duke and Nancy Ann Budden Lyndon B. Johnson Space Center Houston, Texas National Aeronautics and Space Administration Lyndon B. Johnson Space Center 1993 Preface The Mars Exploration Study Project was undertaken by the Exploration Programs Office (now the Planetary Projects Office) in response to the strategic planning initiatives of the Associate Administrator for Exploration, NASA Headquarters in the summer of 1992. The purpose of the study, as viewed by the Associate Administrator for Exploration, was to establish a vision for the human exploration of Mars which would serve as a mechanism for understanding program and technical requirements that would be placed on a precursor lunar exploration program being developed by the Office of Exploration (The First Lunar Outpost). Emphasis was placed on determining the commonality between the Mars and Moon exploration programs to help ensure that total costs for both programs would be minimized and that the lunar program would not contain dead ends which would be difficult or expensive for the Mars program to correct if both programs are carried out sequentially. The study team chose an approach that emphasized the important aspects of Mars exploration without consideration of the lunar capability. Because Mars exploration is inherently more complex than initial lunar exploration programs, it was considered important to identify the characteristics required for Mars so the evolution of a FLO-like lunar program that would optimize the programmatic interactions could be planned. -
GEP-Exomars: a Geophysics And
Lunar and Planetary Science XXXVII (2006) 1982.pdf GEP-ExoMars: a Geophysics and Environment observatory on Mars : Philippe Lognonné1, Tilman Spohn2, David Mimoun1,*, Stephan Ulamec3, Jens Biele3, the ML2SP team and the Aurora Environment team 1IPGP, St. Maur des Fossés, France 2DLR, Institute for Planetary Research, D-12489 Berlin, Germany 3DLR, Institute for Space Simulation, D-51170 Köln, Germany , *E-mail: [email protected] Mass / average Network Instrument Heritage Description Comments kg power, W science Scientific objective: Seismic suite: 2 VBB oblique seismometers Needs soil contact, plus one Short period horizontal MEMS wind and sun SEIS Netlander (Phase B) 1,615 0,28 (Micro-Electro Mechanical System) sensor x protection and The goal of the Long-Lived Geoscience Observatory completing the trihedron. Target sensitivity < decoupling from Meteo suite: wind, temperature, pressure, partly to be replaced humidity, OD, UV spectra, dust impact. by similar Pasteur ATM Beagle-2 (flown) 0,685 0,095 x on Mars, GEP (Geophysics Package) is to initiate the Modes: low/nominal/campaign/dust devil instruments, see rates below Atmospheric electricity probe to measure setup of a permanent network of fixed stations on the electric conductivity, quasi DC electric field AEP Netlander (Phase B) 0,147 0,105 CORE (up to 300 V/m), ELF/VLF radio-electric x emissions (10 Hz to 4 kHz) planet, with the objective to operate for several years. Heat flow and physical properties package. Deployed by a mole up to 5 m deep in Martian regolith: TEM, a thermal These stations will monitor with high resolution the HP3 Beagle-2 (flown) 1,195 0,003 measurement suite (thermal conductivity, heat capacity, thermal gradient [heat flux]); DACTIL, a set of accelerometers (orientation, seismic activity and the rotation of the planet, the depth, so Tri-axial vector magnetic field sensor Champ, Astrid-2 satellites including t and attitude sensors. -
Mars Trajectories Integrated
Trajectory Options for Human Mars Missions Paul D. Wooster * Massachusetts Institute of Technology, Cambridge, Massachusetts, 02139 Robert D. Braun † Georgia Institute of Technology, Atlanta, Georgia, 30332 Jaemyung Ahn ‡ Massachusetts Institute of Technology, Cambridge, Massachusetts, 02139 and Zachary R. Putnam § Georgia Institute of Technology, Atlanta, Georgia, 30332 This paper explores trajectory options for the human exploration of Mars, with an emphasis on conjunction-class missions. Conjunction-class missions are characterized by short in-space durations with long surface stays, as opposed to the long in-space durations and short surface stays characteristic of opposition-class missions. Earth-Mars and Mars- Earth trajectories are presented across a series of mission opportunities and transfer times in order to explore the space of possible crew and cargo transfer trajectories. In the specific instance of crew transfer from Earth to Mars, the potential for aborting the mission without capture into Mars orbit is also of interest. As such two additional classes of trajectories are considered: free-return trajectories, where the trajectory would return the crew to Earth after a fixed period of time; and propulsive-abort trajectories, where the propulsive capability of the transfer vehicle is used to modify the trajectory during a Mars swing-by. The propulsive requirements of a trajectory, due to their associated impact on spacecraft mass, are clearly of interest in assessing trajectories for human Mars missions. Beyond the propulsive requirements, trajectory selection can have a significant impact on the entry velocity and therefore the aeroassist system requirements. The paper suggests potential constraints for entry velocities at Earth and Mars. Based upon Mars entry velocity, the 2- year period free-return abort trajectory is shown to be less desirable than previously considered for many mission opportunities. -
CONCEPTS and APPROACHES for MARS EXPLORATION Lunar and Planetary Institute, Houston, TX July 18–20, 2000 Using the Handtool Of
CONCEPTS AND APPROACHES FOR MARS EXPLORATION Lunar and Planetary Institute, Houston, TX July 18–20, 2000 Using the handtool of the Reader, click on the title to view a particular abstract that you’re interested in. (Abstracts are listed alphabetically by first author. Abstract numbers are listed in brackets and bold at the end of each title.) Phoning Home from Mars in 2025 [6212] J. Adams Proposed Science Requirements and Acquisition Priorities for the First Mars Sample Return [6237] C. B. Agee, D. D. Bogard, D. S. Draper, J. H. Jones, C. Meyer Jr., and D. W. Mittlefehldt Clean and Cold Sample Curation [6197] C. C. Allen, C. B. Agee, R. Beer, and B. L. Cooper IPSE: Italian Package for Scientific Experiments [6084] F. Angrilli, E. Flamini, and S. Espinasse Vision 2020: A Proposed Program of Mars Exploration [6019] R. E. Arvidson FIDO Field Trials in Preparation for Mars Rover Exploration and Discovery and Sample Return Missions [6018] R. E. Arvidson, E. T. Baumgartner, P. Schenker, and S. W. Squyres MOD: An Instrument for the 2005 Mars Explorer Program HEDS Payload [6050] J. L. Bada, D. L. Blaney, F. J. Grunthaner, G. D. McDonald, C. R. Webster, M. Duke, R. A. Mathies, C. P. McKay, D. A. Paige, S. K. Ride, and M. Wadhwa A Network Mission: Completing the Scientific Foundation for the Exploration of Mars [6087] W. B. Banerdt “Following the Water” on Mars: Where Is It, How Much Is There, and How Can We Access It? [6013] N. G. Barlow Strategic Planning for Exploration of the Martian Subsurface [6233] D. -
Detection and Characterization of Martian Volatile-Rich Reservoirs: the Netlander Approach
Concepts and Approaches for Mars Exploration 6125.pdf DETECTION AND CHARACTERIZATION OF MARTIAN VOLATILE-RICH RESERVOIRS: THE NETLANDER APPROACH. F. Costard1, J.J. Berthelier2, and the GPR team, G. Musmann3, M. Menvielle2, and the MAGNET team, P. Lognonné4, D. Giardini5, B. Banerdt6, and the NL-SEIS team, A-M Harri7, F. Forget8, and the ATMIS team. 1UMR 8616, CNRS, Orsay, France, [email protected], 2C.E.T.P., UMR 8639, Saint-Maur, France, 3TUBS-IMG, Braunschweig, Germany, 4IPGP, Saint Maur, France, 5ETH, Zurich, Switzerland, 6JPL, Pasadena, USA, 7FMI, Helsinki, Finland, 8 LMD, Paris 6, Jussieu, France, Introduction: Geological and theoretical modeling do them has its own advantages and limitations and the choice indicate that, most probably, a significant part of the vola- is mostly guided by the range of depths to be explored, the tiles present in the past is presently stocked within the needed spatial resolution and the horizontal extent to be Martian subsurface as ground ice, and as clay minerals covered. We therefore propose to fly on each of the 4 (water constitution). The detection of liquid water is of landers of the NETLANDER mission a set of geophysical in- prime interest and should have deep implications in the struments to explore the first few kilometers of the subsur- understanding of the Martian hydrological cycle and also in face with, as major objectives, the detection of possible exobiology. In the frame of the 2005 joint CNES-NASA water rich layers and the characterization of the main fea- mission to Mars, a set of 4 NETLANDERs developed by an tures of the geological structures of the superficial planetary European consortium is expected to be launched between crust.