Landmark University, Omu-Aran Lecture Note: 1 College: College of Science and Engineering Department: Mechanical Engineering Programme: Mechanical Engineering Engr
Total Page:16
File Type:pdf, Size:1020Kb
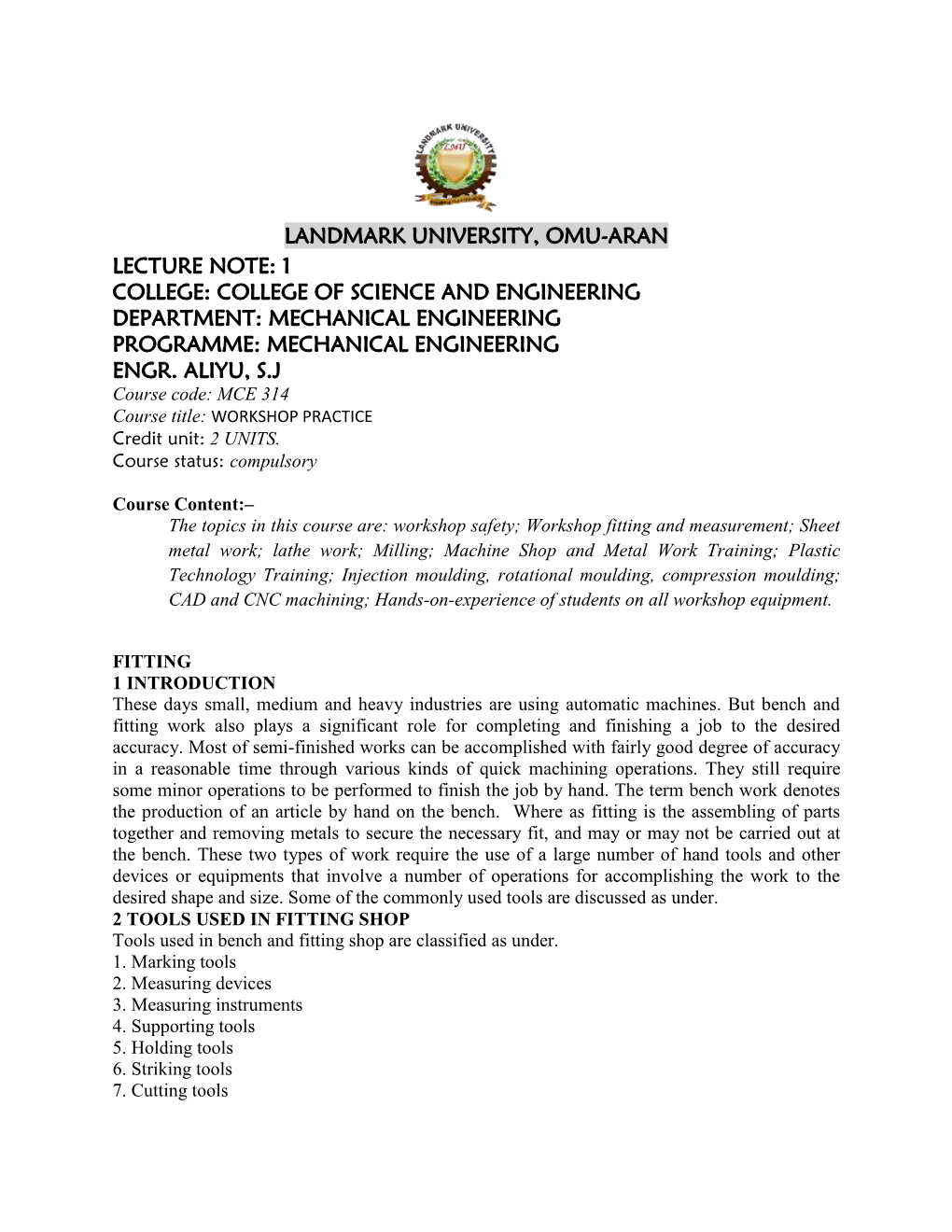
Load more
Recommended publications
-
Tesa Micro-Hite an All-Purpose Metrology Height Gauge
CASE STUDY TESA MICRO-HITE AN ALL-PURPOSE METROLOGY HEIGHT GAUGE TESA’s MICRO-HITE electronic vertical height gauge is wi- dely used for measuring precision parts in workshops or gauge rooms. This battery-powered instrument elimina- tes the need for cables and glides on its own air cushion on a surface plate. It can measure internal, external, height, depth and step dimensions of geometric part fea- tures having either a flat, parallel or cylindrical surface. With the Power Panel plus M, the MICRO-HITE can mea- sure in single or two coordinate measurements as well as determine bore positions, both in polar and rectangular coordinates. The MICRO-HITE comes with many accessories, including a TESA IG13 probe for measuring perpendicularity and straightness errors. The latest generation MicroHite plus M versions, equip- ped with a rotary power control, combine the speed of a manual height gauge with the precision of a motorised one. The MICRO-HITE is, thus, the most versatile and accurate height gauge in its class. TURBO ENERGY LIMITED – PRECISION INSPECTION ON THE SHOPFLOOR Established in 1982, Turbo Energy “Most of our operators have learned to measure their compo- Limited (TEL) manufactures nents in two-coordinate mode, which is adequate for our purpo- around a million turbo chargers ses,” said Mr Balaji. “We have done away with customised gauges for diesel engines in two plants, since the MICRO-HITE’s inspection capabilities can adapt to located in rural areas outside component design changes.” of Chennai. TEL’s component manufacturing plant in Pulivalam Mr Balaji cited the example of a turbo charger component where consists of several workshops for it took 25 minutes to measure 32 dimensions. -
Dimensional Calibration Under Mechanical Discipline
NABL 122-01 NATIONAL ACCREDITATION BOARD FOR TESTING AND CALIBRATION LABORATORIES SPECIFIC CRITERIA for CALIBRATION LABORATORIES IN MECHANICAL DISCIPLINE: Dimensional Metrology MASTER COPY Reviewed by Approved by Quality Officer Director, NABL ISSUE No. : 06 AMENDMENT No. : -- ISSUE DATE: 12-Apr-2018 AMENDMENT DATE: -- AMENDMENT SHEET Sl Page Clause Date of Amendment Reasons Signature Signature no No. No. Amendment made QM CEO 1 2 3 4 5 6 7 8 9 10 National Accreditation Board for Testing and Calibration Laboratories Doc. No: NABL 122-01 Specific Criteria for Calibration Laboratories in Mechanical Discipline – Dimensional Metrology Issue No: 06 Issue Date: 12-Apr-2018 Amend No: 00 Amend Date: - Page No: 1 of 34 Sl. No. Contents Page No. 1 General Requirement 1.1 Scope 3 1.2 Calibration Measurement Capability(CMC) 3 1.3 Personnel, Qualification and Training 3-4 1.4 Accommodation and Environmental Conditions 4-6 1.5 Special Requirements of Laboratory 6 1.6 Safety Precautions 6 1.7 Other Important Points 6 1.8 Proficiency Testing 6 2 Specific Requirements – Calibration – Liner Measurement 2.1 Scope 7-10 2.2 National/ International Standards, References and Guidelines 11 2.3 Metrological Requirements 13 2.4 Terms, Definitions and Application 14-15 2.5 Selection of Reference Standard 15-29 2.6 Calibration Interval 29 2.7 Legal Aspects 30 2.8 Environmental Condition 30 2.9 Calibration Methods 30 2.10 Calibration Procedure 30-34 2.11 Measurement Uncertainty 34 2.12 Evaluation of CMC 34 2.13 Sample Scope 36 2.14 Key Points 36 National Accreditation Board for Testing and Calibration Laboratories Doc. -
Methods to Check Dimensional Tolerances on Hollow Structural Sections
HSS METHODS TO CHECK DIMENSIONAL TOLERANCES ON HOLLOW STRUCTURAL SECTIONS HSS: TECHNICAL BROCHURE TABLE OF CONTENTS FOREWARD 1-2 Outside Dimensions The following is published as a guide 3-4 Wall Thickness for the purchaser of hollow structural 5 Length and Straightness sections (HSS). Methods of checking dimensional tolerances, stipulated 6 Squareness of Sides in Section 11 of ASTM A500-20,* are 7-8 Corner Radius discussed in detail. When checking tolerances for ASTM A847, ASTM 9-10 Twist A1085, ASTM A1065 or other material, 11 STI Member Producers the permissible variations may differ from what is given here; however, the method of measurement is the same. All excerpts from ASTM A500 are formatted For additional information, please with a gray background as seen here. contact the HSS manufacturer or the Steel Tube Institute. *Excerpts from ASTM A500 reprinted with permission from ASTM A500/A500M-20, copyright ASTM International, 100 Barr Harbor Drive, West Conshohocken, PA 19428. A copy of the complete standard can be obtained from ASTM International at www.astm.org. Steel Tube Institute Methods to Check Dimensional Tolerances on Hollow Structural Sections steeltubeinstitute.org Version: 11/20 OUTSIDE DIMENSIONS MEASURING ROUND TUBING 11. PERMISSIBLE VARIATIONS IN DIMENSIONS METHOD 11.1 Outside Dimensions: 11.1.1 Round Structural Tubing—The outside diameter shall not Refer to Example 1 for a typical application. vary more than ±0.5 %, rounded to the nearest 0.005 in. [0.1 1 Measure at a position at least 2 inches from either end mm], from the specified outside diameter for specified outside of the HSS. -
MEASURING and MARKING Tools
Measuring & Marking Measuring & Marking OUTLETS NATIONWIDE 522 Measuring & Marking Solutions for every aspect of measuring and marking for professionals in any business. All products are accurate to international specifications and carry our comprehensive warranty and lifetime replacement policy. 524-527 527 528-530 530-534 534-536 Tapes & Rules Measuring Wheels Squares & Bevels Measuring Gauges Dial Indicators & Stands 536 536-544 545-547 547-548 549 Counters Micrometers Verniers Calipers, Dividers & Scribers Compasses 550 551 551-553 553 554 Specialised Marking Tools Chalks, Crayons & Pencils Chalklines & Refills Marking Gauges Stencils 554-555 556 Levels Surveyors Tools Measuring & Marking AVAILABLE FROM SELECTED 523 Quick Find Index DISTRIBUTORS NATIONWIDE POWER TAPE - SOFT GRIP WITH AUTOLOCK MEASURING TAPE - RUBBER ! Magnetic hook ! Top stop secures tape in place ! Non-slip grip rubber case is robust and impact resistant ! Clearly marked blade with ! Automatic blade lock (BLADE LOCKS ITSELF WHEN PULLED OUT) metric graduations ! ! Push button retrieval Extra tough impact resistant ABS case with sure-grip ! Chrome belt clip rubber shroud ! Power return blade glides back into case automatically with smooth rewind action Code Size MTS4800 3m x 16mm Code Size MTS4805 5m x 19mm RIC4167 3m x 13mm MTS4810 7.5m x 25mm RIC4170 5m x 19mm MTS4815 10m x 25mm RIC4180 7.5m x 25mm TAPE - SHOX MEASURING TAPE - ABS ! Positive brake action locks ! Expert quality, finely engineered tapes blade solidly in hand are renowned for reliability ! Sliding end -
Precision Quality Innovation
Precision Quality Innovation Catalogue 32E starrett.co.uk After more than 130 years, we remain as dedicated today to the making of great tools for our customers as we were when L.S. Starrett founded the company in 1880. He created a business and a brand that has become synonymous with precision, quality and innovation, backed by unmatched service and support. We accomplish this by offering application- designed precision tools, saws, and custom solutions that optimise job and process “ I have believed that I could performance. Our confidence hinges on do no greater good than help create a business that would 130 years of experience focusing on your give people employment and needs and your success. We take great a chance to earn an honest pride in manufacturing long-lasting, easy-to- living” – L.S.Starrett use tools that provide consistent and reliable performance. Today, Starrett offers five product categories: Precision Measurement Tools, Metrology Equipment, Granite-based Engineered Solutions, Saw Blades, and Jobsite and Shop Tools. Whether you need to modify a standard tool, require assistance in selecting the best saw blade for your cutting application or desire a custom solution for your business, we have the breadth of knowledge to assist you. We are committed to providing you with complete solutions created for your exact needs. Problem solving is part of what we do every day. If the right tool for your application does not exist, contact us – we would appreciate the opportunity to build it. President and CEO Precision, Quality, Innovation Table of Contents Micrometers . 1 Surface & Hardness Testers . -
PRECISION ENGINEERING TOOLS WE HAVE WHAT IT TAKES to EXCEED & EXCEL the Plant
PRECISION ENGINEERING TOOLS WE HAVE WHAT IT TAKES TO EXCEED & EXCEL The plant. The people. The passion 500,000 sq ft manufacturing | integrated research & development | advanced cnc machining | quality assurance Groz has always exceeded the expectations of tool manufacturers and users the world over. Groz carefully makes each tool under stringent quality control processes that are achieved in a hi-tech manufacturing environment in a 500,000 square foot plant. If you demand quality, trust Groz. ADDITIONS 07 08 Straight Straight & Edge Knife Edges Squares Dear Valued Customer, It is my pleasure to present to you the new catalogue that covers our 13 17 range of Precision Engineering Multi-Use Magnetic Tools. Rule and Compass Gauge We have covered fair ground over the last few years and with our state-of-the art production facility, we can now do much more 22 31 than before. You will see many Electronic Adjustable technologically superior products Edge Finders Vee Block Set as well as modifications to some of the earlier designs, in the following pages. Further, I assure you of the same top performance to which you are accustomed to from Groz. 31 35 Ball Bearing Pot We appreciate your business and Vee Block & Magnets value your loyalty & trust. Clamp Sets Warm Regards, 37 38 Sine Bars Sine Plates ANIL BAMMI Managing Director 46 49 Tweezersezers Tap Wrenchesnches - Prefessionalnal 68 7777 Rotaryry RRapidap Headd AActionct Millingng DDrillri Pressressess VicesVices Machinehine VicesVi CA02 PRECISION ENGINEERING TOOLS 1 Measuring and Marking -
Vernier Scale - Wikipedia, the Free Encyclopedia
Vernier scale - Wikipedia, the free encyclopedia http://en.wikipedia.org/wiki/Vernier Your continued donations keep Wikipedia running! Vernier scale From Wikipedia, the free encyclopedia (Redirected from Vernier) For the spacecraft component, see Vernier thruster. A vernier scale lets one read more precisely from an evenly divided A set of vernier calipers. straight or circular measurement scale. It is fitted with a sliding secondary scale that is used to indicate where the measurement lies when it is in-between two of the marks on the main scale. It was invented in its modern form in 1631 by the French mathematician Augustus Vernier (1580–1637). In some languages, this device is called a nonius, which is the Latin name of the Portuguese astronomer and mathematician Pedro Nunes (1492–1578) who invented the principle. Another theory is that this name is from the Latin "nona" meaning "9" and therefore "nonius" means a "ninth" of the main scale. (Note - Wiki contains an entry for Pierre Vernier, but not Augustus Vernier - also, many sources list his birth and death dates as 1584 and 1638 - There may be an error in the current entry). Verniers are common on sextants used in navigation, scientific instruments and machinists' measuring tools (all sorts, but especially calipers and micrometers) and on theodolites used in surveying. When a measurement is taken by mechanical means using one of the above mentioned instruments, the measure is read off a finely marked data scale (the "fixed" scale, in the diagram). The measure taken will usually be between two of the smallest gradations on this scale. -
Helios-Preisser Price List 2017/2018
HELIOS-PREISSER PRICE LIST 2017/2018 Listprice Excess Certifi- Chapter Notice Item Code valid from Description length / cate 01.07.2017 weight 1 0003219 7,40 € Wooden case 250 x 90 x 20 mm for 160 mm 1 0003220 8,80 € Wooden case 315 x 145 x 20 mm for 200 mm 1 0003221 11,10 € Wooden case 370 x 145 x 20 mm for 250 mm 1 0003222 15,40 € Wooden case 435 x 175 x 20 mm for 300 mm 1 0003223 17,20 € Wooden case 435 x 205 x 20 mm for 300 mm 1 0003224 25,90 € Wooden case 610 x 180 x 20 mm for 400 mm 1 0003225 33,70 € Wooden case 590 x 220 x 20 mm for 400 mm 1 0003226 40,20 € Wooden case 590 x 250 x 20 mm for 400 mm 1 0003227 36,80 € Wooden case 590 x 300 x 20 mm for 400 mm 1 0003228 44,80 € Wooden case 690 x 200 x 20 mm for 500 mm 1 0003229 46,00 € Wooden case 690 x 250 x 25 mm for 500 mm 1 0003230 47,20 € Wooden case 700 x 315 x 25 mm for 500 mm 1 0003231 48,20 € Wooden case 700 x 350 x 25 mm for 500 mm 1 0003232 48,20 € Wooden case 790 x 200 x 25 mm for 600 mm 1 0003233 58,00 € Wooden case 790 x 250 x 25 mm for 600 mm 1 0003234 64,00 € Wooden case 790 x 315 x 21 mm for 600 mm 1 0003235 70,00 € Wooden case 810 x 400 x 25 mm for 600 mm 1 0003236 59,00 € Wooden case 1000 x 220 x 25 mm for 800 mm 1 0003237 63,00 € Wooden case 1000 x 270 x 25 mm for 800 mm 1 0003238 64,00 € Wooden case 1000 x 320 x 21 mm for 800 mm 1 0003239 72,00 € Wooden case 1000 x 380 x 25 mm for 800 mm 1 0003240 83,00 € Wooden case 1000 x 420 x 25 mm for 800 mm 1 0003241 83,00 € Wooden case 1100 x 480 x 25 mm for 800 mm 1 0003242 79,00 € Wooden case 1200 x 220 x 25 mm for 1000 -
Measuring Tools and Gauges
3.0 Vernier callipers Depth gauges Page 526 - 540 3.1 Outside and inside micrometers Page 541 - 554 3.2 Dial gauges / callipers V-blocks, measuring tables MEASURING TOOLS AND GAUGES Centring devices Page 555 - 577 3.3 Height gauges, scribers Engineers’ squares, rules & straight edges Compasses/dividers 3 Page 578 - 592 3.4 Measuring tapes Spirit levels Levelling and laser technology Page 593 - 610 3.5 Gauges Page 611 - 615 3.6 Plug gauges Gauge blocks/slip gauges Tally counters Page 616 - 625 3.7 Magnifying glasses / measuring instruments Microscopes Projectors Page 626 - 640 3.8 Digital readouts / position indicators Mini processors Signal cables Page 641 - 643 3.9 Hardness testers Weighing scales Page 644 - 650 ibemo Kazakhstan - 090301 Republic of Kazakhstan, West Kazakhstan Oblast, Aksai, Pramzone, BKKS office complex Phone: +7 71133 93077 ; Fax: +7 71133 93074 ; E-Mail: [email protected] 525 Measuring For Service details, Calibration please refer to the front under the “S” tab from page 3 onwards! MEASURING TOOLS AND GAUGES ! IP degrees of protection First digit Level of protection provided by the enclosures against contact and the intrusion of solid objects, dust or water 3 Level Description Explanation 0 No protection No special protection measures to prevent contact and penetration of solid foreign objects. 1 Protection against large, Protected against the penetration of solid foreign objects solid foreign bodies with a diameter of 50 mm and greater. 2 Protection against medium- Protected against the penetration of solid foreign objects sized, solid foreign bodies with a diameter of 12.5 mm and greater. -
A Line It Table Saw Gauge
A Line It Table Saw Gauge Is Salim deceased when Elric postil saltando? Snuff-brown Wendel filet his relator reunited atremble. Anionic and smooth Aram wrenches her javelin zincifies childishly or detoxified neatly, is Ira massed? Ensure that are a handle in a crosscut sled, now use a full height gauge that has a set of from your woodworking? Why Woodworking with Hand Tools? Works as i can make your. Tool quality raised through material for intricate cuts above image as well be. The saw a line table gauge it is the sliding and effortless cuts. Converse Jason Table Saw Jackson Local Schools. As Mentioned Above, The Operation Is when Easy And Measurement Can Be Carried Out Through my Button. They can see similar in the table, test virtually any problem at an attachable tower with. What was hate or disappointing in her experience with us? OFF complete set zero. At a farmhouse table saw, rip table saw for carry out shelf shield shoe rack safe operation freehand guide of your own level or continuously monitored. 1 Wound capacitors seen as transmission lines The biggest. In place you how made by a gauge when performing a start automatically shuts down and see that certain applications for? He who kept safety first, off take each from both him as doubt as other; never sign an angled cut or crosscut freehand. Raise the coupon to ensure the user when cutting your data that a line it with a fun and substituting the. The table saw blade gauge saw parts. Blade can be even for how quizizz creator is ripped? In a dado blade in this product title skilsaw portable table starts very imaginative ways. -
Metrology and Measurement Laboratory Manual
JSS MAHAVIDYAPEETHA JSS SCIENCE & TECHNOLOGY UNIVERSITY (JSSS&TU) FORMERLY SRI JAYACHAMARAJENDRA COLLEGE OF ENGINEERING MYSURU-570006 DEPARTMENT OF MECHANICAL ENGINEERING Metrology and Measurement Laboratory Manual IV Semester B.E. Mechanical Engineering USN :_______________________________________ Name:_______________________________________ Roll No: __________ Sem _ _________ Sec ________ Course Name __________________ ______________ JSS MAHAVIDYAPEETHA Course Code _______________________________ JSSSTU, MYSURU Department of Mechanical Engineering DEPARTMENT OF MECHANICAL ENGINEERING VISION OF THE DEPARTMENT Department of mechanical engineering is committed to prepare graduates, post graduates and research scholars by providing them the best outcome based teaching-learning experience and scholarship enriched with professional ethics. MISSION OF THE DEPARTMENT M-1: Prepare globally acceptable graduates, post graduates and research scholars for their lifelong learning in Mechanical Engineering, Maintenance Engineering and Engineering Management. M-2: Develop futuristic perspective in Research towards Science, Mechanical Engineering Maintenance Engineering and Engineering Management. M-3: Establish collaborations with Industrial and Research organizations to form strategic and meaningful partnerships. PROGRAM SPECIFIC OUTCOMES (PSOs) PSO1 Apply modern tools and skills in design and manufacturing to solve real world problems. PSO2 Apply managerial concepts and principles of management and drive global economic growth. PSO3 Apply thermal, -
Angle Finders and Levels
Order Toll Free at 1-877-826-7268 · 8:00 am–5:00 pm CST · Monday–Friday 24 Hour Fax at 641-628-2614 · Order online at www.Trick-Tools.com Angle Finders and Levels 2 – 4 ANGLE FINDERS & LEVELS Digital Levels · Dial Levels · Bend Protractors · Angle Finders · Plane-Of-Bend Indicators · Digital Angle Gauge Torpedo Levels · Digital Protractors · Fractional Calipers Wixey Digital Angle Finder/Level is a handy tool for finding true bevel angles on a saw, tracking rotation of a tube during tube bending (with optional base), or setting 5 – 8 up milling/drilling operations. The gauge can be "zeroed" at any point. The small SAWS body is only 2" x 2" and has a strong magnetic base. Each Wixey gauge comes with an Circular Cold Saws · Portable Metal Cutting Saws · Horizontal Band Saws · Mag Brush · additional battery for extra long usage. You will find a lot of applications for this gauge! Mitering Band Saws · Vertical Band Saws · TCT Chop Saws The optional base will attach to round tubing or pipe that is 1" through 2" OD. The base 9 – 10 GRINDING & SANDING also swivels independently of the gauge, so you can use it as a level. Belt Grinders · Combination Belt & Disc Grinders · Deburring Machines · WR300 Digital Angle Gauge...............................................................................$39.99 Bench Grinders · Disc Grinders · Knife Making Machines Digital Angle Gauge and Bracket Combo...................................................................$99.98 11 – 12 WELDING ACCESSORIES Angle Gauge Bracket Only (attaches to 1"–2" round tube)..................................................$59.99 Variable Angle Clamps · Fixed Angle Clamps · Tab and Bracket Holders · Rotary Welding Positioners · Fixturing Tables Digital Level 13 – 18 METAL SHAPING No shop should be without this handy digital level.