PANJAPAKKUL-THESIS-2018.Pdf
Total Page:16
File Type:pdf, Size:1020Kb
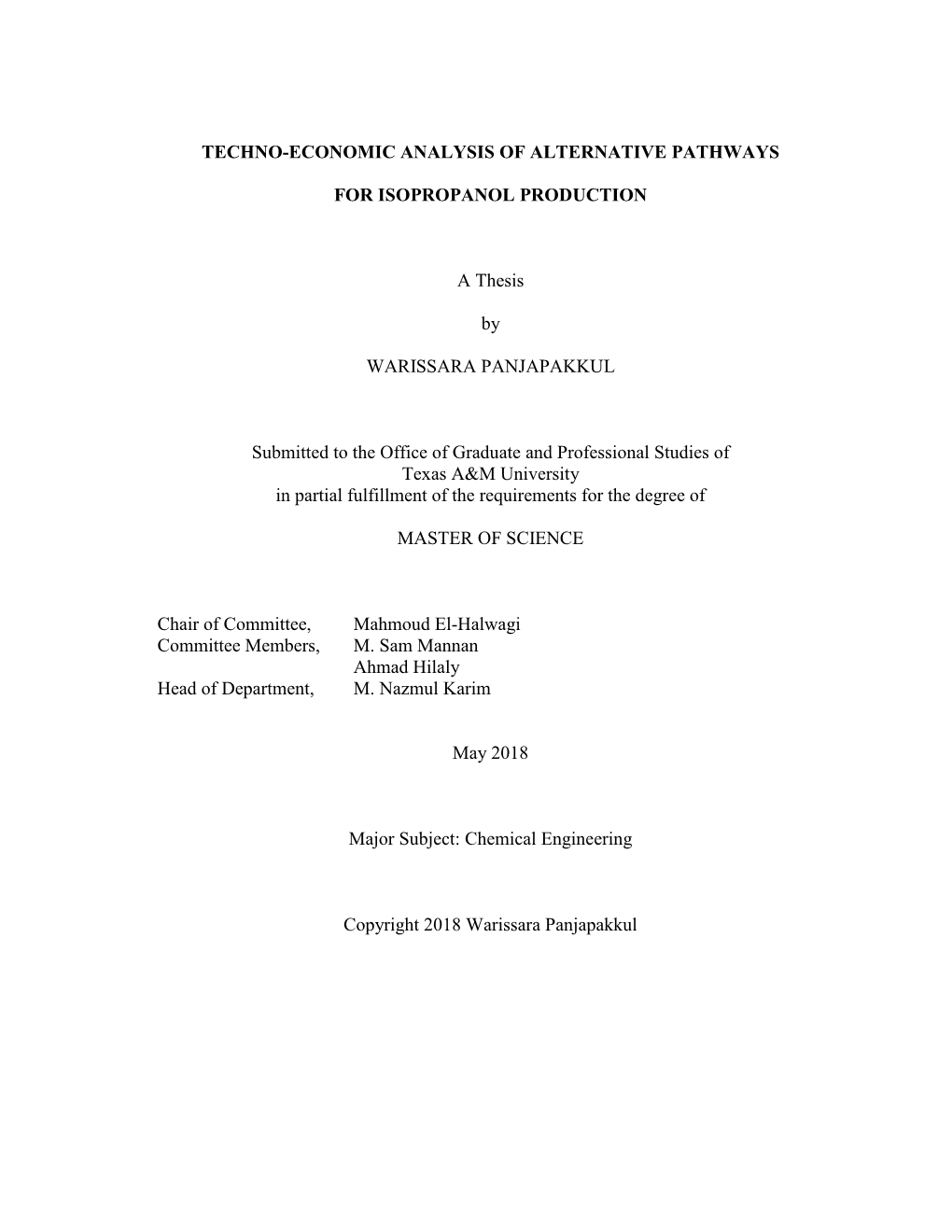
Load more
Recommended publications
-
SAFETY DATA SHEET Nonflammable Gas Mixture: Carbon Dioxide / Carbon Monoxide / Nitric Oxide / Nitrogen / Propane Section 1
SAFETY DATA SHEET Nonflammable Gas Mixture: Carbon Dioxide / Carbon Monoxide / Nitric Oxide / Nitrogen / Propane Section 1. Identification GHS product identifier : Nonflammable Gas Mixture: Carbon Dioxide / Carbon Monoxide / Nitric Oxide / Nitrogen / Propane Other means of : Not available. identification Product type : Gas. Product use : Synthetic/Analytical chemistry. SDS # : 002173 Supplier's details : Airgas USA, LLC and its affiliates 259 North Radnor-Chester Road Suite 100 Radnor, PA 19087-5283 1-610-687-5253 24-hour telephone : 1-866-734-3438 Section 2. Hazards identification OSHA/HCS status : This material is considered hazardous by the OSHA Hazard Communication Standard (29 CFR 1910.1200). Classification of the : GASES UNDER PRESSURE - Compressed gas substance or mixture GHS label elements Hazard pictograms : Signal word : Warning Hazard statements : Contains gas under pressure; may explode if heated. May displace oxygen and cause rapid suffocation. May increase respiration and heart rate. Precautionary statements General : Read and follow all Safety Data Sheets (SDS’S) before use. Read label before use. Keep out of reach of children. If medical advice is needed, have product container or label at hand. Close valve after each use and when empty. Use equipment rated for cylinder pressure. Do not open valve until connected to equipment prepared for use. Use a back flow preventative device in the piping. Use only equipment of compatible materials of construction. Prevention : Not applicable. Response : Not applicable. Storage : Protect from sunlight. Store in a well-ventilated place. Disposal : Not applicable. Hazards not otherwise : In addition to any other important health or physical hazards, this product may displace classified oxygen and cause rapid suffocation. -
Experimental and Analytical Study of Nitric Oxide Formation During Combustion of Propane in a Jet-Stirred Combustor
NASA Technical Paper 1181 I 1 Experimental and Analytical Study of Nitric Oxide Formation During / Combustion of Propane in a Jet-Stirred Combustor , ' N. T. Wakelyn, Casimir J. Jachimowski, and Charles H. Wilson , TECH LIBRARY KAFB, NM 0134538 NASA Technical Paper 1181 Experimental and Analytical Study of Nitric Oxide Formation During Combustion of Propane in a Jet-Stirred Combustor N. T. Wakelyn, Casimir J. Jachimowski, and Charles H. Wilson Langley Research Center Hampton, Virginia National Aeronautics and Space Administration Scientific and Technical Information Otfice 1978 '8' SUMMARY A jet-stirred combustor, constructed of castable zirconia and with an inconel injector, has been used to study nitric oxide formation in propane-air combustion with residence times in the range from 3.2 to 3.3 msec and equiva lence ratios varying from 0.7 to 1.4. The residence time range was character istic of that found in the primary zones of aircraft turbines. Premixed propane-air formulations were subjected to intense and turbulent backmixed combustion within the cavity formed between the injector and the hemispherical inner walls of the zirconia shell. The volume of the combustor cavity was 12.7 cm3 and the mass loading was maintained in the range from 0.053 to 0.055 g/cm3-sec. Measurements were made of combustor operating tem perature and of nitric oxide concentration. Maximum nitric oxide concentrations of the order of 55 ppm were found in the range of equivalence ratio from 1.0 to 1.1. Nitric oxide concentrations were predicted over the range of equivalence ratio by a computer program which employs a perfectly stirred'reactor (PSR) algorithm with finite-rate kinetics. -
Activity 33. Hydrohalogenation & Hydration of Alkynes
Chem 201, Fall 2010 Activity 33, M Nov 22 Activity 33. Hydrohalogenation & Hydration of Alkynes Alkynes undergo many of the same addition reactions that alkenes do, including additions that require carbocation intermediates. Different energy and geometry changes may be required for additions to an alkyne and an alkene so some surprising outcomes may occur with alkynes. Model 1. Addition of HX Hydrogen halides (HCl, HBr, HI) add to alkynes to make vinyl halides . A carbocation mechanism is followed when the reaction is performed in the dark in a peroxide-free solvent. This addition obeys Markovnikov’s rule. A free-radical-chain mechanism is followed when HBr addition is initiated by organic peroxides. This addition gives an anti-Markonikov product. Critical Thinking Questions 1. Draw the carbocations indicated by the two bouncy curved arrows (below). Based on the observation that the carbocation mechanism yields a Markovnikov product, circle the more stable carbocation. 2. (CI) Draw the free radicals indicated by the two competing pathways (below). Based on the observation that the free-radical mechanism yields an anti-Markovnikov product, circle the more stable free radical. 3. The cations and radicals in CTQ #1 and #2 are called vinyl cations and vinyl radicals , respectively. Based on the regioselectivities reported in Model 1, what effect do alkyl substituents at the charged/radical carbon have on the energies of these species? Is this consistent with, or opposed to, their effect on R 3C+ and R 3C• species? 4. The geometry of a vinyl cation can be anticipated using VSEPR. Count electron domains in the cation below and predict all of the HCC bond angles. -
Alternatives to High Propane Prices Interest Expense and the Cost of Utilities Are the Two Largest “Out of Pocket” Expenses Facing Most Broiler Growers
ThePoultry Engineering, Economics & Management NEWSLETTER Critical Information for Improved Bird Performance Through Better House and Ventilation System Design, Operation and Management Auburn University, in cooperation with the U.S. Poultry & Egg Association Issue No 29, May 2004 Alternatives to High Propane Prices Interest expense and the cost of utilities are the two largest “out of pocket” expenses facing most broiler growers. There is little a grower can do to reduce interest costs, short of major mortgage refinancing. However, costs associated with utilities are another matter. The topics we have addressed in most past issues of this newsletter have all dealt with housing and ventilation factors which can result in improved flock performance and in reduced levels of energy being used, which directly reduces costs to the grower. Electricity rates are typically fixed and are highly regulated. However, the price of heating fuel, specifically propane (liquefied petroleum gas or LPG), has varied widely up and down in most recent years, depending on the time of year and numerous supply and demand conditions. Growers can choose What growers should be aware of is that there are ways to reduce the from several good risk that they will have to buy propane at one of those times when the alternatives to paying price is highest. This newsletter explains several alternative methods consistently high prices growers can use to get lower and more stable propane costs over time. for propane. Understanding the Basics of Propane Pricing The most fundamental factor in propane pricing is that propane is basically a fossil fuel, being derived from raw natural gas during the oil refining process. -
Safety Data Sheet
SAFETY DATA SHEET 1. Identification Product number 1000007900 Product identifier AUTO GLASS QUICK RELEASE AGENT Company information Sprayway, Inc. 1005 S. Westgate Drive Addison, IL 60101 United States Company phone General Assistance 1-630-628-3000 Emergency telephone US 1-866-836-8855 Emergency telephone outside 1-952-852-4646 US Version # 01 Recommended use Not available. Recommended restrictions None known. 2. Hazard(s) identification Physical hazards Flammable aerosols Category 1 Health hazards Serious eye damage/eye irritation Category 2A Specific target organ toxicity, single exposure Category 3 narcotic effects Aspiration hazard Category 1 Environmental hazards Not classified. OSHA defined hazards Not classified. Label elements Signal word Danger Hazard statement Extremely flammable aerosol. May be fatal if swallowed and enters airways. Causes serious eye irritation. May cause drowsiness or dizziness. Precautionary statement Prevention Keep away from heat/sparks/open flames/hot surfaces. - No smoking. Do not spray on an open flame or other ignition source. Pressurized container: Do not pierce or burn, even after use. Avoid breathing gas. Wash thoroughly after handling. Use only outdoors or in a well-ventilated area. Wear eye/face protection. Response If swallowed: Immediately call a poison center/doctor. If inhaled: Remove person to fresh air and keep comfortable for breathing. If in eyes: Rinse cautiously with water for several minutes. Remove contact lenses, if present and easy to do. Continue rinsing. Call a poison center/doctor if you feel unwell. Do NOT induce vomiting. If eye irritation persists: Get medical advice/attention. Storage Store in a well-ventilated place. Keep container tightly closed. Store locked up. -
Fuel Properties Comparison
Alternative Fuels Data Center Fuel Properties Comparison Compressed Liquefied Low Sulfur Gasoline/E10 Biodiesel Propane (LPG) Natural Gas Natural Gas Ethanol/E100 Methanol Hydrogen Electricity Diesel (CNG) (LNG) Chemical C4 to C12 and C8 to C25 Methyl esters of C3H8 (majority) CH4 (majority), CH4 same as CNG CH3CH2OH CH3OH H2 N/A Structure [1] Ethanol ≤ to C12 to C22 fatty acids and C4H10 C2H6 and inert with inert gasses 10% (minority) gases <0.5% (a) Fuel Material Crude Oil Crude Oil Fats and oils from A by-product of Underground Underground Corn, grains, or Natural gas, coal, Natural gas, Natural gas, coal, (feedstocks) sources such as petroleum reserves and reserves and agricultural waste or woody biomass methanol, and nuclear, wind, soybeans, waste refining or renewable renewable (cellulose) electrolysis of hydro, solar, and cooking oil, animal natural gas biogas biogas water small percentages fats, and rapeseed processing of geothermal and biomass Gasoline or 1 gal = 1.00 1 gal = 1.12 B100 1 gal = 0.74 GGE 1 lb. = 0.18 GGE 1 lb. = 0.19 GGE 1 gal = 0.67 GGE 1 gal = 0.50 GGE 1 lb. = 0.45 1 kWh = 0.030 Diesel Gallon GGE GGE 1 gal = 1.05 GGE 1 gal = 0.66 DGE 1 lb. = 0.16 DGE 1 lb. = 0.17 DGE 1 gal = 0.59 DGE 1 gal = 0.45 DGE GGE GGE Equivalent 1 gal = 0.88 1 gal = 1.00 1 gal = 0.93 DGE 1 lb. = 0.40 1 kWh = 0.027 (GGE or DGE) DGE DGE B20 DGE DGE 1 gal = 1.11 GGE 1 kg = 1 GGE 1 gal = 0.99 DGE 1 kg = 0.9 DGE Energy 1 gallon of 1 gallon of 1 gallon of B100 1 gallon of 5.66 lb., or 5.37 lb. -
The Influence of Residual Sodium on the Catalytic Oxidation of Propane and Toluene Over Co3o4 Catalysts
catalysts Article The Influence of Residual Sodium on the Catalytic Oxidation of Propane and Toluene over Co3O4 Catalysts Guangtao Chai 1,2, Weidong Zhang 1, Yanglong Guo 2,* , Jose Luis Valverde 3 and Anne Giroir-Fendler 1,* 1 Université Claude Bernard Lyon 1, Université de Lyon, CNRS, IRCELYON, 2 Avenue Albert Einstein, F-69622 Villeurbanne, France; [email protected] (G.C.); [email protected] (W.Z.) 2 Key Laboratory for Advanced Materials, Research Institute of Industrial Catalysis, School of Chemistry and Molecular Engineering, East China University of Science and Technology, Shanghai 200237, China 3 Department of Chemical Engineering, University of Castilla La Mancha, Avda. Camilo José Cela 12, 13071 Ciudad Real, Spain; [email protected] * Correspondence: [email protected] (Y.G.); [email protected] (A.G.-F.); Tel.: +86-21-64-25-29-23 (Y.G.); +33-472-431-586 (A.G.-F.) Received: 16 July 2020; Accepted: 30 July 2020; Published: 3 August 2020 Abstract: A series of Co3O4 catalysts with different contents of residual sodium were prepared using a precipitation method with sodium carbonate as a precipitant and tested for the catalytic oxidation 1 1 of 1000 ppm propane and toluene at a weight hourly space velocity of 40,000 mL g− h− , respectively. Several techniques were used to characterize the physicochemical properties of the catalysts. Results showed that residual sodium could be partially inserted into the Co3O4 spinel lattice, inducing distortions and helping to increase the specific surface area of the Co3O4 catalysts. Meanwhile, it could negatively affect the reducibility and the oxygen mobility of the catalysts. -
BENZENE Disclaimer
United States Office of Air Quality EPA-454/R-98-011 Environmental Protection Planning And Standards June 1998 Agency Research Triangle Park, NC 27711 AIR EPA LOCATING AND ESTIMATING AIR EMISSIONS FROM SOURCES OF BENZENE Disclaimer This report has been reviewed by the Office of Air Quality Planning and Standards, U.S. Environmental Protection Agency, and has been approved for publication. Mention of trade names and commercial products does not constitute endorsement or recommendation of use. EPA-454/R-98-011 ii TABLE OF CONTENTS Section Page LIST OF TABLES.....................................................x LIST OF FIGURES.................................................. xvi EXECUTIVE SUMMARY.............................................xx 1.0 PURPOSE OF DOCUMENT .......................................... 1-1 2.0 OVERVIEW OF DOCUMENT CONTENTS.............................. 2-1 3.0 BACKGROUND INFORMATION ...................................... 3-1 3.1 NATURE OF POLLUTANT..................................... 3-1 3.2 OVERVIEW OF PRODUCTION AND USE ......................... 3-4 3.3 OVERVIEW OF EMISSIONS.................................... 3-8 4.0 EMISSIONS FROM BENZENE PRODUCTION ........................... 4-1 4.1 CATALYTIC REFORMING/SEPARATION PROCESS................ 4-7 4.1.1 Process Description for Catalytic Reforming/Separation........... 4-7 4.1.2 Benzene Emissions from Catalytic Reforming/Separation .......... 4-9 4.2 TOLUENE DEALKYLATION AND TOLUENE DISPROPORTIONATION PROCESS ............................ 4-11 4.2.1 Toluene Dealkylation -
A Palladium-Catalyzed Approach to Allenic Aromatic Ethers and First Total
Chemical Science EDGE ARTICLE View Article Online View Journal | View Issue A palladium-catalyzed approach to allenic aromatic ethers and first total synthesis of terricollene A† Cite this: Chem. Sci.,2021,12,9347 a b b b a a a All publication charges for this article Chaofan Huang, Fuchun Shi, Yifan Cui,‡ Can Li,‡ Jie Lin,‡ Qi Liu,‡ Anni Qin,‡ have been paid for by the Royal Society Huanan Wang,‡a Guolin Wu,‡a Penglin Wu,‡a Junzhe Xiao, ‡b Haibo Xu,‡b of Chemistry Yuan Yuan,‡a Yizhan Zhai,‡b Wei-Feng Zheng,‡a Yangguangyan Zheng, ‡a Biao Yu*b and Shengming Ma *ab A palladium-catalyzed C–O bond formation reaction between phenols and allenylic carbonates to give 2,3- allenic aromatic ethers with decent to excellent yields under mild reaction conditions has been described. A Received 7th April 2021 variety of synthetically useful functional groups are tolerated and the synthetic utility of this method has Accepted 4th June 2021 been demonstrated through a series of transformations of the allene moiety. By applying this reaction as DOI: 10.1039/d1sc01896e the key step, the total syntheses of naturally occurring allenic aromatic ethers, eucalyptene and rsc.li/chemical-science terricollene A (first synthesis; 4.5 g gram scale), have been accomplished. Creative Commons Attribution-NonCommercial 3.0 Unported Licence. Introduction Results and discussion Aromatic ethers are prevalent and prominent in a variety of In contrast to the well-established metal-catalyzed coupling natural products, pharmaceuticals, and agrochemicals.1 Tradi- reactions between aryl halides and phenols or aliphatic alcohols tional methods for the preparation of aromatic ethers include (Scheme 1b),9 metal-catalyzed coupling reactions of aryl halides the Williamson ether synthesis,2 direct nucleophilic substitu- tion reactions,3 Mitsunobu reaction,4 Ullman-type couplings of alkoxides with aryl halides,5 etc. -
Detection and Characterization of Subsurface Dissolved Hydrocarbon Plumes by in Situ Mass Spectrometry – a Demonstration in Th
Detection and characterization of subsurface dissolved hydrocarbon plumes by in situ mass spectrometry – A demonstration in the natural laboratory of the Coal Oil Point seep field. Ira Leifer1,2, Tim Short3, Scott Hiller4, Michael Suschikh1 California Oil Spill Prevention and Response Chevron Technology Workshop San Ramon CA, Feb 26-28 2013 Mission Goals 1. Identify dissolved components under surface oil slicks. 2. Identify and characterize dissolved oil component plumes. 3. Use sidescan sonar to characterize plume source. 4. Test conventional fluorometric detection of dissolved and submerged oil (on a shoestring budget) How a MIMS works in situ Membrane Introduction Mass Spectrometer Dissolved gas transfer across a semipermeable membrane from a sample water flow provides sample into the mass spectrometer for analysis Gases breakup into known fragments, which then are used to identify the incoming gases. Key to calibration is reduction of water vapor from the gas stream entering the mass spectrometer Introduction of Analytes from the Water • MIMS is ideal Column – Passive (except for sample pumping and heating, if desired) – Polydimethylsiloxane (PDMS) or Teflon are most common choices (hydrophobic) – Provides sensitive detection of dissolved gases and volatile organic compounds • Need to mechanically support membrane (hydrostatic pressure) – Porous metal or ceramic frit SRI MIMS Adapted for Underwater In Situ Analysis Microcontroller Embedded PC and other electronics MS electronics (Inficon CPM 200) 200 amu linear quadrupole in vacuum housing w/ heating jacket Turbo pump (Varian/Agilent V81-M) MIMS probe Roughing pump (KNF Neuberger) High pressure membrane interface Portable Underwater Mass Spectrometry • Simultaneous in situ quantification of multiple analytes – Dissolved gases – Light hydrocarbons – Volatile organic compounds • High pressure, direct sample introduction – Under development . -
Kinetics and Products Distribution of Selective Catalytic Hydration of Ethylene and Propylene Oxides in Concentrated Aqueous Solutions
Organic Process Research & Development 2002, 6, 660-664 Kinetics and Products Distribution of Selective Catalytic Hydration of Ethylene and Propylene Oxides in Concentrated Aqueous Solutions I. A. Kozlovsky, R. A. Kozlovsky,* A. V. Koustov, M. G. Makarov, J. P. Suchkov, and V. F. Shvets D.I.Mendeleev University of Chemical Technology of Russia, Chair of Basic Organic and Petrochemical Synthesis, 9 Miusskaya Square, Moscow 125047, Russia Abstract: and metalate anions.I" The kinetics and reaction mechanism The kinetics of selective hydration of ethylene- and propylene of the hydration of a-oxides using homogeneous catalysis oxides in concentrated aqueous solutions is studied during by salts have been explicitly studied.3,IO,1l The kinetic data homogeneous catalysis by sodium bicarbonate. The mathemati obtained have shown that at a concentration of some salts cal model of the process with determined parameters adequately of about 0.5 molJL the distribution factor b = klko is reduced describing the rate of the reaction and products distribution is lO-fold more (to 0.1-0.2). This enables the production of developed. monoglycol with high selectivity at water/oxide molar ratios close to 1. We have used hereinafter homogeneous nucleo philic catalysts with the above-mentioned properties for the Introduction creation of industrial heterogeneous catalysts of a selective The reaction of ethylene- and propylene oxides hydration hydration of ethylene- and propylene oxides by means of is an industrial way of obtaining of glycols, in particular an immobilization of anions of salts on heterogeneous ethylene glycol-one of the most-produced large-scale carriers. 12-17 The largest ethylene glycol producers Shell, 18-24 products of industrial organic synthesis, with the world (4) Masuda, T. -
Vapor Phase Hydration of Ethylene Catalyzed by Solid Acids*
47 Vapor Phase Hydration of Ethylene Catalyzed by Solid Acids* by Kozo Tanabe** and Masahiro Nitta** Summary: The hydration of ethyleneover various solid acids such as metal sulfates, phos- phates, oxides, solid phosphoricacid and cation exchangedzeolites was investigatedin a closed circulation system at 160~300℃. Ferric and aluminum sulfates and zeolites Y showed high catalytic activity in comparison with solid phosphoricacid, SiO2-Al2O3,zeolites A and all other catalysts. The selectivityfor ethanolformation was extremelyhigh in metal sulfates and zeolites A, but low in SiO2-Al2O3 and zeolites Y. The order of activities of metal sulfates was Fe2(SO4)3>Al2(SO4)3>Ni- SO4> Cr2(SO4)3>CuSO4>MnSO4>CaSO4. The catalysts those acid strength in their dried state was as strong as -8.2<Ho≦-3 were found to be active and selective for ethanol for- mation. The activitiesof cation exchangedzeolites A which varied in order of Mg-A>Cd-A> Zn-A>Ca-A>Ag-A>Sr-A>La-A~Ce-A were shown to correlate with the electronegativities of exchangedcations and the adsorptionheats of ethylene. The rate of ethanolformation increasedas the mole ratio of H2O/C2H4 decreased. The experimenton the reaction of ethylenewith heavy water showed that deuterium did not transfer into ethyleneat all. It was concludedby analyzing the kinetic data that theformation of an ad- sorbedethyl carbonium ion from an adsorbedethylene and a proton on acid sites was the rate-deter- miningstep of the hydration. 1 Introduction 2 Experimental The direct synthesis of alcohol from ethylene 2.1 Catalysts