Challenger Shuttle
Total Page:16
File Type:pdf, Size:1020Kb
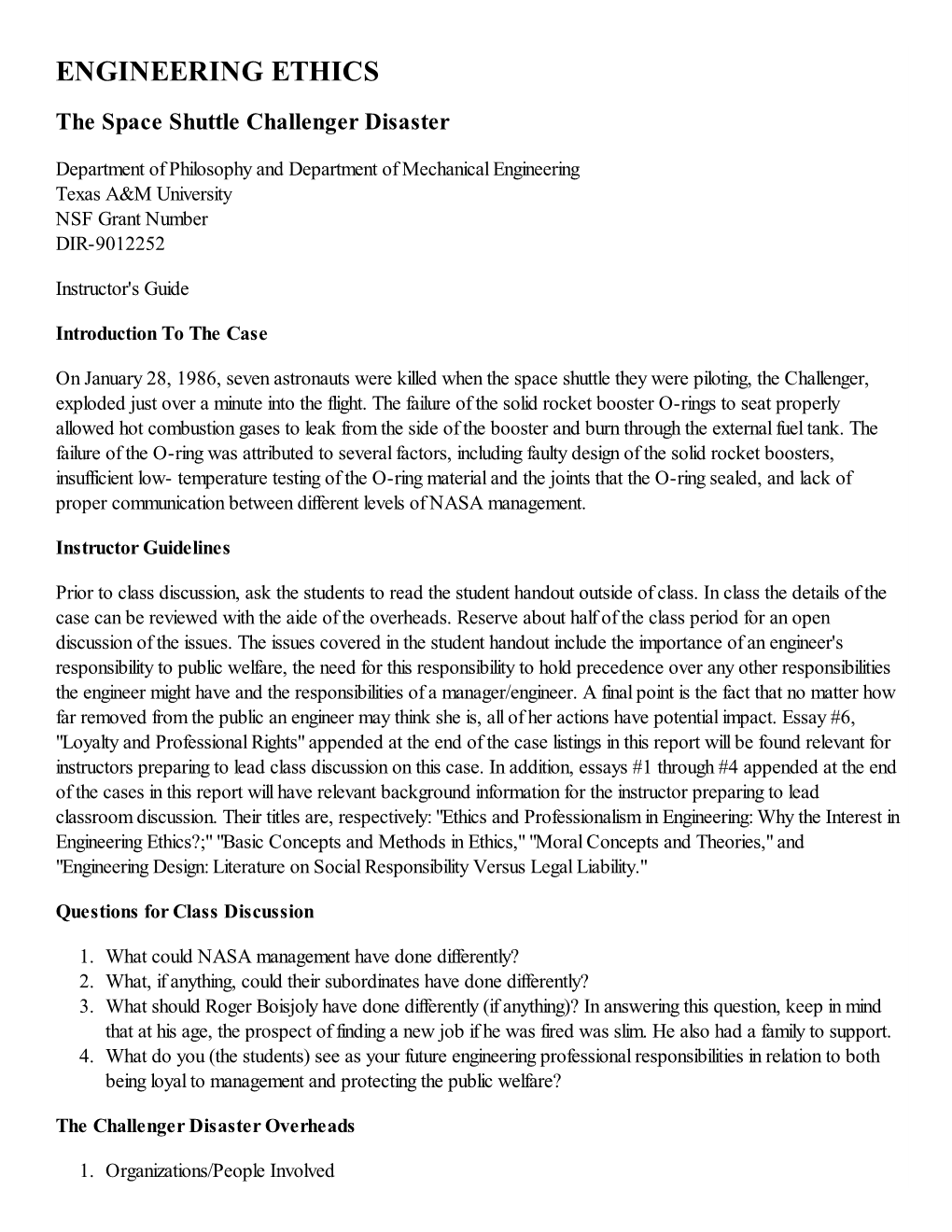
Load more
Recommended publications
-
Space Launch System (Sls) Motors
Propulsion Products Catalog SPACE LAUNCH SYSTEM (SLS) MOTORS For NASA’s Space Launch System (SLS), Northrop Grumman manufactures the five-segment SLS heavy- lift boosters, the booster separation motors (BSM), and the Launch Abort System’s (LAS) launch abort motor and attitude control motor. The SLS five-segment booster is the largest solid rocket motor ever built for flight. The SLS booster shares some design heritage with flight-proven four-segment space shuttle reusable solid rocket motors (RSRM), but generates 20 percent greater average thrust and 24 percent greater total impulse. While space shuttle RSRM production has ended, sustained booster production for SLS helps provide cost savings and access to reliable material sources. Designed to push the spent RSRMs safely away from the space shuttle, Northrop Grumman BSMs were rigorously qualified for human space flight and successfully used on the last fifteen space shuttle missions. These same motors are a critical part of NASA’s SLS. Four BSMs are installed in the forward frustum of each five-segment booster and four are installed in the aft skirt, for a total of 16 BSMs per launch. The launch abort motor is an integral part of NASA’s LAS. The LAS is designed to safely pull the Orion crew module away from the SLS launch vehicle in the event of an emergency on the launch pad or during ascent. Northrop Grumman is on contract to Lockheed Martin to build the abort motor and attitude control motor—Lockheed is the prime contractor for building the Orion Multi-Purpose Crew Vehicle designed for use on NASA’s SLS. -
IAC-17-D2.4.3 Page 1 of 18 IAC-17
68th International Astronautical Congress (IAC), Adelaide, Australia, 25-29 September 2017. Copyright ©2017 by DLR-SART. Published by the IAF, with permission and released to the IAF to publish in all forms. IAC-17- D2.4.3 Evaluation of Future Ariane Reusable VTOL Booster stages Etienne Dumonta*, Sven Stapperta, Tobias Eckerb, Jascha Wilkena, Sebastian Karlb, Sven Krummena, Martin Sippela a Department of Space Launcher Systems Analysis (SART), Institute of Space Systems, German Aerospace Center (DLR), Robert Hooke Straße 7, 28359 Bremen, Germany b Department of Spacecraft, Institute of Aerodynamics and Flow Technology, German Aerospace Center (DLR), Bunsenstraße 10, 37073 Gottingen, Germany *[email protected] Abstract Reusability is anticipated to strongly impact the launch service market if sufficient reliability and low refurbishment costs can be achieved. DLR is performing an extensive study on return methods for a reusable booster stage for a future launch vehicle. The present study focuses on the vertical take-off and vertical landing (VTOL) method. First, a restitution of a flight of Falcon 9 is presented in order to assess the accuracy of the tools used. Then, the preliminary designs of different variants of a future Ariane launch vehicle with a reusable VTOL booster stage are described. The proposed launch vehicle is capable of launching a seven ton satellite into a geostationary transfer orbit (GTO) from the European spaceport in Kourou. Different stagings and propellants (LOx/LH2, LOx/LCH4, LOx/LC3H8, subcooled LOx/LCH4) are considered, evaluated and compared. First sizing of a broad range of launcher versions are based on structural index derived from existing stages. -
Nasa X-15 Program
5 24,132 6 9 NASA X-15 PROGRAM By: T.D. Barnes - NASA Contractor - 1960s NASA contractors for the X-15 program were Bendix Field Engineering followed by Unitec, Inc. The NASA High Range Tracking stations were located at Ely and Beatty Nevada with main control being at Dryden/Edwards AFB in California. Personnel at the tracking stations consisted of a Station Manager, a Technical Advisor, and field engineers for the Mod-2 Radar, Data Transmission System, Communications, Telemetry, and Plant Maintenance/Generators. NASA had a site monitor at each tracking station to monitor our contractor operations. Though supporting flights of the X-15 was their main objective, they also participated in flights of the XB-70, the three Lifting Bodies, experimental Lunar Landing vehicles, and an occasional A-12/YF-12/SR-71 Blackbird flight. On mission days a NASA van picked up each member of the crew at their residence for the 4:20 a.m. trip to the tracking station 18 miles North of Beatty on the Tonopah Highway. Upon arrival each performed preflight calibrations and setup of their various systems. The liftoff of the B-52, with the X-15 tucked beneath its wing, seldom occurred after 9:00 a.m. due to the heat effect of the Mojave Desert making it difficult for the planes to acquire altitude. At approximately 0800 hours two pilots from Dryden would proceed uprange to evaluate the condition of the dry lake beds in the event of an emergency landing of the X-15 (always buzzing our station on the way up and back). -
Print Media Portrayal of the Culture of NASA Before and After the Challenger Explosion
University of Tennessee, Knoxville TRACE: Tennessee Research and Creative Exchange Masters Theses Graduate School 12-2002 Print Media Portrayal of the Culture of NASA Before and After the Challenger Explosion Jodi M. Lockaby University of Tennessee - Knoxville Follow this and additional works at: https://trace.tennessee.edu/utk_gradthes Part of the Communication Commons Recommended Citation Lockaby, Jodi M., "Print Media Portrayal of the Culture of NASA Before and After the Challenger Explosion. " Master's Thesis, University of Tennessee, 2002. https://trace.tennessee.edu/utk_gradthes/3540 This Thesis is brought to you for free and open access by the Graduate School at TRACE: Tennessee Research and Creative Exchange. It has been accepted for inclusion in Masters Theses by an authorized administrator of TRACE: Tennessee Research and Creative Exchange. For more information, please contact [email protected]. To the Graduate Council: I am submitting herewith a thesis written by Jodi M. Lockaby entitled "Print Media Portrayal of the Culture of NASA Before and After the Challenger Explosion." I have examined the final electronic copy of this thesis for form and content and recommend that it be accepted in partial fulfillment of the equirr ements for the degree of Master of Science, with a major in Communication. Mark Littmann, Major Professor We have read this thesis and recommend its acceptance: Bonnie Riechert, John Haas Accepted for the Council: Carolyn R. Hodges Vice Provost and Dean of the Graduate School (Original signatures are on file with official studentecor r ds.) To the Graduate Council: I am submitting herewith a thesis written by Jodi M. -
Status of the Space Shuttle Solid Rocket Booster
The Space Congress® Proceedings 1980 (17th) A New Era In Technology Apr 1st, 8:00 AM Status of The Space Shuttle Solid Rocket Booster William P. Horton Solid Rocket Booster Engineering Office, George C. Marshall Space Flight Center, Follow this and additional works at: https://commons.erau.edu/space-congress-proceedings Scholarly Commons Citation Horton, William P., "Status of The Space Shuttle Solid Rocket Booster" (1980). The Space Congress® Proceedings. 3. https://commons.erau.edu/space-congress-proceedings/proceedings-1980-17th/session-1/3 This Event is brought to you for free and open access by the Conferences at Scholarly Commons. It has been accepted for inclusion in The Space Congress® Proceedings by an authorized administrator of Scholarly Commons. For more information, please contact [email protected]. STATUS OF THE SPACE SHUTTLE SOLID ROCKET BOOSTER William P. Horton, Chief Engineer Solid Rocket Booster Engineering Office George C. Marshall Space Flight Center, AL 35812 ABSTRACT discuss retrieval and refurbishment plans for Booster reuse, and will address Booster status Two Solid Rocket Boosters provide the primary for multimission use. first stage thrust for the Space Shuttle. These Boosters, the largest and most powerful solid rocket vehicles to meet established man- BOOSTER CONFIGURATION rated design criteria, are unique in that they are also designed to be recovered, refurbished, It is appropriate to review the Booster config and reused. uration before describing the mission profile. The Booster is 150 feet long and is 148 inches The first SRB f s have been stacked on the in diameter (Figure 1), The inert weight Mobile Launch Platform at the Kennedy Space is 186,000 pounds and the propellant weight is Center and are ready to be mated with the approximately 1.1 million pounds for each External Tank and Orbiter in preparation for Booster. -
The International Space Station and the Space Shuttle
Order Code RL33568 The International Space Station and the Space Shuttle Updated November 9, 2007 Carl E. Behrens Specialist in Energy Policy Resources, Science, and Industry Division The International Space Station and the Space Shuttle Summary The International Space Station (ISS) program began in 1993, with Russia joining the United States, Europe, Japan, and Canada. Crews have occupied ISS on a 4-6 month rotating basis since November 2000. The U.S. Space Shuttle, which first flew in April 1981, has been the major vehicle taking crews and cargo back and forth to ISS, but the shuttle system has encountered difficulties since the Columbia disaster in 2003. Russian Soyuz spacecraft are also used to take crews to and from ISS, and Russian Progress spacecraft deliver cargo, but cannot return anything to Earth, since they are not designed to survive reentry into the Earth’s atmosphere. A Soyuz is always attached to the station as a lifeboat in case of an emergency. President Bush, prompted in part by the Columbia tragedy, made a major space policy address on January 14, 2004, directing NASA to focus its activities on returning humans to the Moon and someday sending them to Mars. Included in this “Vision for Space Exploration” is a plan to retire the space shuttle in 2010. The President said the United States would fulfill its commitments to its space station partners, but the details of how to accomplish that without the shuttle were not announced. The shuttle Discovery was launched on July 4, 2006, and returned safely to Earth on July 17. -
1 American Institute of Aeronautics and Astronautics from Air Bubbles Cast in the Fuel (Voids) Can Cause Problems During Hot-Fire Operations
Genetic Algorithm Optimization of a Cost Competitive Hybrid Rocket Booster George Story1 NASA MSFC Huntsville, Al Performance, reliability and cost have always been drivers in the rocket business. Hybrid rockets have been late entries into the launch business due to substantial early development work on liquid rockets and solid rockets. Slowly the technology readiness level of hybrids has been increasing due to various large scale testing and flight tests of hybrid rockets. One remaining issue is the cost of hybrids vs the existing launch propulsion systems. This paper will review the known state-of-the-art hybrid development work to date and incorporate it into a genetic algorithm to optimize the configuration based on various parameters. A cost module will be incorporated to the code based on the weights of the components. The design will be optimized on meeting the performance requirements at the lowest cost. I. Introduction Hybrids, considered part solid and part liquid propulsion system, have been caught in the middle of development goals of the various NASA and military programs. Solid rocket motor technology has matured due to the design simplicity, on-demand operational characteristics and low cost. The reliability of solids, given minimal maintenance requirements, made them the ideal system for military applications. On the other hand, liquid rocket engine technology has matured due to their higher specific impulse (ISP) over solids and variable control thrust capability. Hybrid Rockets have been used in only one flight-production application (Teledyne Ryan AQM-81A ‘Firebolt Supersonic Aerial Target) and one series of recent manned flight demonstrations (Burt Rutan’s SpaceshipOne), suggesting that advantages have been overlooked in some potential applications. -
2015 Year in Review
National Aeronautics and Space Administration Volume 12 Issue 1 January 2016 2015 Year in Review www.nasa.gov GoddardView Trending – 2 Celebrating Hubble’s 25 Years of Endless Discoveries – 3 Journey to Mars Is More Than Just Fiction – 4 On Earth Day, Rock Stars and Earth Science Share Center Stage – 5 Goddard’s 2015 Milestones NASA Observes Annual at a Glance – 6 Day of Remembrance The Day of Remembrance honors Open Houses Provide a Closer Look members of the NASA family who gave Into NASA’s Work – 8 their lives in the name of exploration. A Scientifically Enlightening Year This year marks the 30th anniversary of in Heliophysics – 10 the Challenger disaster, which claimed Half a Century Later, Rick Obenschain the lives of all seven crew members. Completes His Final NASA Mission – 11 Goddard Honors Sen. Mikulski and Her U.S. Senator From Florida Astronomical Contributions – 12 Tours Goddard’s Facilities Sen. Bill Nelson toured the center’s facilities on Jan. 16. In 1986, as a On the cover: Select Goddard milestones member of the U.S. House of Rep- and accomplishments from 2015. resentatives, Nelson served as a payload specialist during a mission Cover credit: NASA/Goddard/John W. aboard the space shuttle Columbia. Jones NP-2016-1-385-GSFC 2015 Is Warmest Year on Record Independent analyses by the Goddard Institute for Space Studies and the Na- Info tional Oceanic and Atmospheric Admin- istration concluded that Earth’s globally Goddard View is an official publication of averaged surface temperatures in 2015 NASA’s Goddard Space Flight Center in were the warmest since modern record- Greenbelt, Maryland. -
Gallery of USAF Weapons Note: Inventory Numbers Are Total Active Inventory Figures As of Sept
Gallery of USAF Weapons Note: Inventory numbers are total active inventory figures as of Sept. 30, 2011. ■ 2012 USAF Almanac Bombers B-1 Lancer Brief: A long-range, air refuelable multirole bomber capable of flying intercontinental missions and penetrating enemy defenses with the largest payload of guided and unguided weapons in the Air Force inventory. Function: Long-range conventional bomber. Operator: ACC, AFMC. First Flight: Dec. 23, 1974 (B-1A); Oct. 18, 1984 (B-1B). Delivered: June 1985-May 1988. IOC: Oct. 1, 1986, Dyess AFB, Tex. (B-1B). Production: 104. Inventory: 66. Aircraft Location: Dyess AFB, Tex.; Edwards AFB, Calif.; Eglin AFB, Fla.; Ellsworth AFB, S.D. Contractor: Boeing, AIL Systems, General Electric. Power Plant: four General Electric F101-GE-102 turbofans, each 30,780 lb thrust. Accommodation: pilot, copilot, and two WSOs (offensive and defensive), on zero/zero ACES II ejection seats. Dimensions: span 137 ft (spread forward) to 79 ft (swept aft), length 146 ft, height 34 ft. B-1B Lancer (SSgt. Brian Ferguson) Weight: max T-O 477,000 lb. Ceiling: more than 30,000 ft. carriage, improved onboard computers, improved B-2 Spirit Performance: speed 900+ mph at S-L, range communications. Sniper targeting pod added in Brief: Stealthy, long-range multirole bomber that intercontinental. mid-2008. Receiving Fully Integrated Data Link can deliver nuclear and conventional munitions Armament: three internal weapons bays capable of (FIDL) upgrade to include Link 16 and Joint Range anywhere on the globe. accommodating a wide range of weapons incl up to Extension data link, enabling permanent LOS and Function: Long-range heavy bomber. -
Clark, Carl Proceedings Sub 2.Pmd
2015 HAWAII UNIVERSITY INTERNATIONAL CONFERENCES ARTS, HUMANITIES, SOCIAL SCIENCES & EDUCATION JANUARY 03 - 06, 2015 ALA MOANA HOTEL, HONOLULU, HAWAII THE TELL TALE TELLING: AN ANALYSIS OF THE FILM THE CHALLENGER DISASTER TO THE OFFICIAL FINDINGS AND PERSONAL ACCOUNT OF COMMISSION MEMBER DR. FEYNMAN CLARK, CARL WESTLY TEXAS STATE UNIVERSITY COLLEGE MASS COMMUNICATION Mr. Carl Westly Clark Mass Communication Texas State University College. The Tell Tale Telling: An Analysis of the Film The Challenger Disaster to the Official Findings and Personal Account of Commission Member Dr. Feynman A qualitative comparison of the book What do You Care What Other People Think (Feynman and Leighton 1988) and the film The Challenger Disaster (Discovery Science Channel 2013) . Using the cultivation analysis theory to understand the differences in the two narratives and their possible effects on viewer's opinions. The Tell Tale Telling: An analysis of the film The Challenger Disaster to the official findings and personal account of commission member Dr. Feynman By Carl Clark 2014 “Science teaches us what the rules of evidence are. We mess with that at our peril.” William Hurt as Dr. Richard Feynman “For a successful technology, reality must take precedence over public relations, for nature cannot be fooled” Appendix F by Dr. Richard Feynman Abstract The film The Challenger Disaster (Discovery Science Channel 2013) based off of the book by Dr. Richard Feynman What do You Care What Other People Think (Feynman and Leighton 1988) portrays the investigation into the loss of the space shuttle Challenger. The film’s narrative centers on one man against the corruption and special interests of NASA and Washington D.C. -
Columbia and Challenger: Organizational Failure at NASA
ARTICLE IN PRESS Space Policy 19 (2003) 239–247 Columbia and Challenger: organizational failure at NASA Joseph Lorenzo Hall* Astronomy Department/School of Information Management and Systems, Astronomy Department, University of California at Berkeley, 601 Campbell Hall, Berkeley, CA 94720-3411, USA Abstract The National Aeronautics and Space Administration (NASA)—as the global leader in all areas of spaceflight and space science— is a unique organization in terms of size, mission, constraints, complexity and motivations. NASA’s flagship endeavor—human spaceflight—is extremely risky and one of the most complicated tasks undertaken by man. It is well accepted that the tragic destruction of the Space Shuttle Challenger on 28 January 1986 was the result of organizational failure. The surprising disintegration of the Space Shuttle Columbia in February 2003—nearly 17 years to the day after Challenger—was a shocking reminder of how seemingly innocuous details play important roles in risky systems and organizations. NASA as an organization has changed considerably over the 42 years of its existence. If it is serious about minimizing failure and promoting its mission, perhaps the most intense period of organizational change lies in its immediate future. This paper outlines some of the critical features of NASA’s organization and organizational change, namely path dependence and ‘‘normalization of deviance’’. Subsequently, it reviews the rationale behind calling the Challenger tragedy an organizational failure. Finally, it argues that the recent Columbia accident displays characteristics of organizational failure and proposes recommendations for the future. r 2003 Elsevier Ltd. All rights reserved. 1. Introduction in 1967 are examples of failure at NASA that cost a total of 17 astronaut lives. -
Economic Benefits of Reusable Launch Vehicles for Space Debris Removal
68th International Astronautical Congress (IAC), Adelaide, Australia, 25-29 September 2017. Copyright ©2017 by the International Astronautical Federation (IAF). All rights reserved. IAC-17-A6.8.5 Economic Benefits of Reusable Launch Vehicles for Space Debris Removal Matthew P. Richardsona*, Dominic W.F. Hardyb a Department of Aeronautics and Astronautics, University of Tokyo, 7-3-1 Hongo, Bunkyo-ku, Tokyo, Japan 113- 8656, [email protected] b Nova Systems, 53 Ellenborough Street, Ipswich, Queensland, Australia 4305, [email protected] * Corresponding Author Abstract An analysis of cost savings which could be realized on active debris removal missions through the use of reusable launch vehicles has been performed. Launch vehicle price estimates were established for three levels of reusable launch vehicle development, based on varying levels of technological development and market competition. An expendable launch vehicle price estimate was also established as a point of comparison. These price estimates were used to form two separate debris removal mission cost estimates, based on previously-proposed debris removal mission concepts. The results of this analysis indicate that reusable launch vehicles could reduce launch prices to levels between 19.6% and 92.8% cheaper than expendable launch vehicles, depending on the level of RLV maturity. It was also determined that a reusable launch vehicle could be used to realize total active debris removal mission cost savings of between 2.8% (for a partially reusable launch