Knfc Fuel Service Technology Development
Total Page:16
File Type:pdf, Size:1020Kb
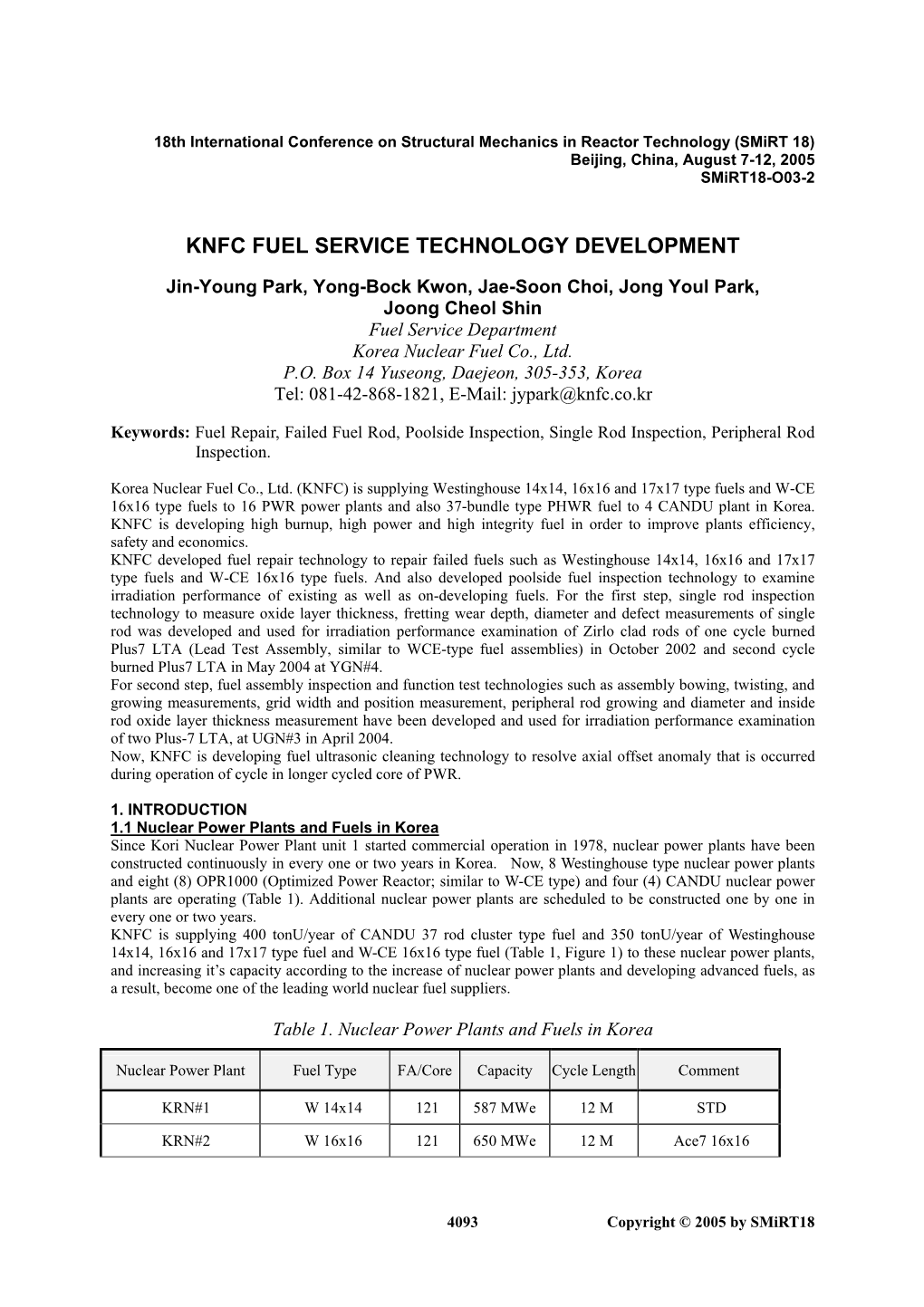
Load more
Recommended publications
-
Radioactive Waste Management Programmes in NEA Member Countries
RADIOACTIVE WASTE MANAGEMENT PROGRAMMES IN OECD/NEA MEMBER COUNTRIES HUNGARY NATIONAL NUCLEAR ENERGY CONTEXT Commercial utilisation of nuclear power in Hungary goes back to several decades. The four VVER 440/213 nuclear units of the Paks Nuclear Power Plant were connected to the electricity grid between 1983 and 1987. In 2015 the NPP generated 15.8 TWh of electricity which accounted for 52.7% of the total electricity generated in that year in Hungary. These data are characteristic for the period of time around 2015. In January 2014 the Government of Hungary and the Government of the Russian Federation concluded an agreement on the cooperation in the field of peaceful use of nuclear energy, which was promulgated in the Act II of 2014. Among others, the Agreement includes the cooperation on the establishment of two VVER-1200 type nuclear power plant units at the Paks site, to be commissioned in 2025, and 2026 respectively. The present country profile of Hungary does not cover the spent fuel and radioactive waste management issues of the new units. Components of Domestic Electricity Production 2015 Source: MAVIR Hungarian Independent Transmission Operator Company Ltd. SOURCES, TYPES AND QUANTITIES OF WASTE Waste classification Most of the radioactive waste in Hungary originates from the operation of the Paks NPP, and much smaller quantities are generated by other (rather institutional, non-NPP) users of radioactive isotopes. The following classification scheme is based on Appendix 2 in the Decree 47/2003 (VIII. 8.) of the Minister of Health on certain issues of interim storage and final disposal of radioactive wastes, and on certain radiohygiene issues of naturally occurring radioactive materials concentrated during industrial activity. -
OECD-IAEA Paks Fuel Project Was Established in 2005 As a Joint Project Between the IAEA and the OECD/NEA
spine: 5.455 mm 81 pages OECD–IAEA Paks Fuel Project Final Report INTERNATIONAL ATOMIC ENERGY AGENCY VIENNA 09-2210-PUB-1389-cover.indd 1 2010-06-29 10:12:33 OECD–IAEA PAKS FUEL PROJECT The following States are Members of the International Atomic Energy Agency: AFGHANISTAN GHANA NIGERIA ALBANIA GREECE NORWAY ALGERIA GUATEMALA OMAN ANGOLA HAITI PAKISTAN ARGENTINA HOLY SEE PALAU ARMENIA HONDURAS PANAMA AUSTRALIA HUNGARY PARAGUAY AUSTRIA ICELAND PERU AZERBAIJAN INDIA PHILIPPINES BAHRAIN INDONESIA POLAND BANGLADESH IRAN, ISLAMIC REPUBLIC OF PORTUGAL BELARUS IRAQ QATAR BELGIUM IRELAND REPUBLIC OF MOLDOVA BELIZE ISRAEL ROMANIA BENIN ITALY RUSSIAN FEDERATION BOLIVIA JAMAICA SAUDI ARABIA BOSNIA AND HERZEGOVINA JAPAN SENEGAL BOTSWANA JORDAN SERBIA BRAZIL KAZAKHSTAN SEYCHELLES BULGARIA KENYA SIERRA LEONE BURKINA FASO KOREA, REPUBLIC OF SINGAPORE BURUNDI KUWAIT SLOVAKIA CAMEROON KYRGYZSTAN SLOVENIA CANADA LATVIA SOUTH AFRICA CENTRAL AFRICAN LEBANON SPAIN REPUBLIC LESOTHO SRI LANKA CHAD LIBERIA SUDAN CHILE LIBYAN ARAB JAMAHIRIYA SWEDEN CHINA LIECHTENSTEIN SWITZERLAND COLOMBIA LITHUANIA SYRIAN ARAB REPUBLIC CONGO LUXEMBOURG TAJIKISTAN COSTA RICA MADAGASCAR THAILAND CÔTE D’IVOIRE MALAWI THE FORMER YUGOSLAV CROATIA MALAYSIA REPUBLIC OF MACEDONIA CUBA MALI TUNISIA CYPRUS MALTA TURKEY CZECH REPUBLIC MARSHALL ISLANDS UGANDA DEMOCRATIC REPUBLIC MAURITANIA UKRAINE OF THE CONGO MAURITIUS UNITED ARAB EMIRATES DENMARK MEXICO UNITED KINGDOM OF DOMINICAN REPUBLIC MONACO GREAT BRITAIN AND ECUADOR MONGOLIA NORTHERN IRELAND EGYPT MONTENEGRO UNITED REPUBLIC EL SALVADOR MOROCCO OF TANZANIA ERITREA MOZAMBIQUE UNITED STATES OF AMERICA ESTONIA MYANMAR URUGUAY ETHIOPIA NAMIBIA UZBEKISTAN FINLAND NEPAL VENEZUELA FRANCE NETHERLANDS VIETNAM GABON NEW ZEALAND YEMEN GEORGIA NICARAGUA ZAMBIA GERMANY NIGER ZIMBABWE The Agency’s Statute was approved on 23 October 1956 by the Conference on the Statute of the IAEA held at United Nations Headquarters, New York; it entered into force on 29 July 1957. -
RECENT DEVELOPMENTS in NUCLEAR SAFETY in HUNGARY April 2019
1 HI LI HUNGARIAN ATOMIC ENERGY AUTHORITY Nuclear Safety Bulletin H-1539 Budapest, P.O. Box 676, Phone: +36 1 4364-800, Fax: +36 1 4364-883, e-mail: [email protected] website: www.haea.gov.hu RECENT DEVELOPMENTS IN NUCLEAR SAFETY IN HUNGARY April 2019 General 2018 annual safety performance assessment of nuclear facilities The HAEA regularly evaluates the safety performance of the operators of nuclear facilities. The main sources of data for the assessment are the regular reports and the event reports of the licensees, the protocols of regulatory inspections including the regular and comprehensive inspections focusing on specific areas, and the reactive inspections. Below we give a short review on the 2018 safety performance assessment. The safety performance data are taken from the quarterly reports of Paks NPP and the semi-annual reports of the other licensees. Paks Nuclear Power Plant Eighteen reportable events occurred in 2018. Eighteen events have been reported by the NPP altogether, all of them were of category „below scale” corresponding to Level-0 on the seven-level International Nuclear Event Scale (INES). 2 There has been no event causing violation of technical operating specification since 2014. On 24 October 2018, the NPP moved to Operating Conditions and Limits (OCL) based on a license by the HAEA. There was no event causing violation of OCL since then. Five automatic reactor protection actuations occurred in 2018. One SCRAM-III and the SCRAM-I actuation were connected to the same event, which was caused by the low water level of steam generators of Unit 3. -
Nuclear Power Reactors in the World
REFERENCE DATA SERIES No. 2 2010 Edition Nuclear Power Reactors in the World INTERNATIONAL ATOMIC ENERGY AGENCY VIENNA ISBN 978-92-0-105610-8 ISSN 1011-2642 @ 10-20781_IAEA-RDS-2-30_cover.indd 1 2010-05-26 08:59:05 REFERENCE DATA SERIES No. 2 NUCLEAR POWER REACTORS IN THE WORLD 2010 Edition INTERNATIONAL ATOMIC ENERGY AGENCY VIENNA, 2010 NUCLEAR POWER REACTORS IN THE WORLD IAEA, VIENNA, 2010 IAEA-RDS-2/30 ISBN 978–92–0–105610–8 ISSN 1011–2642 Printed by the IAEA in Austria July 2010 CONTENTS Introduction . 5 Definitions . 7 Table 1. Reactors in operation, long-term shutdown and under construction, 31 Dec. 2009 . 10 Table 2. Type and net electrical power of reactors connected to the grid, 31 Dec. 2009 . 12 Table 3. Type and net electrical power of reactors under construction, 31 Dec. 2009 . 13 Table 4. Reactor years of experience, up to 31 Dec. 2009 . 14 Table 5. Operating reactors and net electrical power, 1980 to 2009 . 16 Table 6. Nuclear electricity production and share from 1980 to 2009 . 18 Table 7. Annual construction starts and connections to the grid, 1954 to 2009 . 21 Table 8. Number of new reactors connected to the grid and median construction time span . 22 Table 9. Construction starts during 2009 . 24 Table 10. Connections to the grid during 2009 . 25 Table 11. Scheduled connections to the grid during 2009 . 25 Table 12. Reactors planned for construction as known on 31 Dec. 2009 . 26 Table 13. Reactors under construction, 31 Dec. 2009 . 29 Table 14. Reactors in operation, 31 Dec. -
Maintenance and Training Center at Paks Nuclear Power Plant
Visit to the Maintenance and Training Center at Paks NPP VISIT TO THE MAINTENANCE AND TRAINING CENTER AT PAKS NUCLEAR POWER PLANT Gábor Náfrádi Institute of Nuclear Techniques (NTI), Budapest University of Technology and Economics (BME), Budapest, Hungary, [email protected] ABSTRACT The last official program of the Teaching Physics Innovatively (TPI-15) conference was a visit to Paks Nuclear Power Plant (NPP) in particular to the Maintenance and Training Center (MTC), with approximately 30 participants. The scope of MTC is the preservation of staff competence and training for any new activities in a non-radioactive environment. Besides this work, the MTC offers for the public guided tours for the better understanding of the basic nuclear processes and operational techniques of a modern NPP. 1. HISTORY AND IMPORTANCE OF PAKS NPP Paks is a small town located in the middle of Hungary on the shore of the river Danube. Here is the Paks Nuclear Power Plant (NPP) [1] located, which operates 4 nuclear units from the 1980’s. The type of the units is VVER440-213 [2] which denotes a Russian-designed Pressurized Water Reactor (PWR). The first unit produces electricity since 1982 and the youngest unit is in operation since 1987. The nominal electric power of the reactors was 440 MW, however, through the years the reactor powers have risen to 500 MW. The planned operation time of the units was 30 years, but thanks to the operation lifetime extension programs this period will be expanded by another 20 years [3]. The total power of the four units is 2000 MW, which covers approximately 50% [4] of the Hungarian electricity production and approximately 40% of the electricity consumption. -
Vanda Lamm Nuclear Legislation in Hungary 1. General Framework Of
Vanda Lamm Nuclear Legislation in Hungary 1. General framework of nuclear legislation1 The first step of nuclear legislation in Hungary goes back to the 1960s when the Government adopted Decree 10 of 1964 relating to radioactive substances and preparations. The 1964 Decree was in force until a comprehensive act on atomic energy was adopted in 1980 (Act 1. of 1980), which was in effect until 1996 when it was replaced by Act CXVI of 1996. The Atomic Energy Act still in place. The preparation for an act on atomic energy was started at practically the same time as Hungary’s engagement in executing its nuclear program, at the beginning of the 1970s. The agreement with the former USSR concerning the erection of a nuclear power plant in Hungary was concluded on 28 December 1966, and the construction works at Paks started in 1974.2 The four units of Paks Nuclear Power Plant are VVER-440/213, belonging to the second generation of Soviet-designed power stations; they were put into commercial operation between 1983 and 1987.3 The total installed capacity of Paks Nuclear Power Plant is 1889 MWe.4 In Hungary, the nuclear power's share of electricity production is almost 40%. Still, Paks is the only nuclear power plant in Hungary, operates as a shareholders' company under the name of MVM (Magyar Villamosművek Zrt.)Paks Nuclear Power Plant Ltd. It should be noted that in Hungary, there are two research reactors and three facilities used for the short term and long-term storage of radioactive wastes and nuclear fuels.5 1 That paper treats Hungarian legislation -
NEA News Volume No
News NEA2020 – No. 38.1 In this issue: Reducing the construction costs of nuclear power Management and disposal of high-level radioactive waste: Global progress and solutions GNDS: A standard format for nuclear data and more... NEA News Volume No. 38.1 2020 Contents Facts and opinions Reducing the construction costs of nuclear power � � � � � � � � � � � � � � � � � � � � � � � � � � � � � � � � � � � � � � � � � � � � � 4 Management and disposal of high-level radioactive waste: Global progress and solutions � � � � � � � � � � � � � � � � � � � � � � � � � � � � � � � � � � � � � � � � � � � � � � � � � � � � � � � � � � � � � � � � � � � � � � � 8 GNDS: A standard format for nuclear data � � � � � � � � � � � � � � � � � � � � � � � � � � � � � � � � � � � � � � � � � � � � � � � � � � � � � � � 11 NEA updates Workshop on Preparedness for Post-Accident Recovery: Lessons from Experience � � � � � � � � � � � � � � � � � � � � � � � � � � � � � � � � � � � � � � � � � � � � � � � � � � � � � � � � � � � � � � � � � � � � � � � � � � � � 13 Online communications during the COVID-19 pandemic � � � � � � � � � � � � � � � � � � � � � � � � � � � � � � � � � � � � � � 15 News briefs In memoriam: Professor Massimo Salvatores � � � � � � � � � � � � � � � � � � � � � � � � � � � � � � � � � � � � � � � � � � � � � � � � � � � 21 New publications � � � � � � � � � � � � � � � � � � � � � � � � � � � � � � � � � � � � � � � � � � � � � � � � � � � � � � � � � � � � � � � � � � � � � � � � � � 22 OECD Boulogne building. 1 Shutterstock, Peter Varga -
Doing It Right: the Loviisa Way by SIMON RIPPON Impressive Performance at Loviisa in Finland
Doing it right: The Loviisa way BY SIMON RIPPON Impressive performance at Loviisa in Finland OVIISA NUCLEAR POWER station in stems from good management decisions, involvement Finland has one of the best, if not the L best, operating performance records in of plant personnel, efficient outages, and the world. The cumulative capacity factor for Unit 1 since the start of commercial operation reliance on the expertise of many companies. in 1977 is 84 percent, and for the last 19 years, the annual figure has five times been above 90 large-diameter containment was required to From a maintenance point of view, these percent and has never been below 80 percent. accommodate the six-loop VVER-440 plant, unique features of the Loviisa plant have pre- For Unit 2, the cumulative load factor since with its horizontal steam generators. This led sented quite a challenge, both to the plant op- startup in 1980 is 87 percent, with eight of the to the adoption of an ice condenser system to erators and Finnish regulators, and it was for last 16 years above 90 percent and only one provide pressure suppression rather than a full this reason that they decided from the outset that year below 80 percent (at 79.2 percent). pressure containment. they must learn to do things themselves. This Other performance indicators are equally impressive, including the collective radiation doses, which have been at or below 1 person- sievert per year per unit for most of the oper- ating lives of each of the two reactors, and the duration of refueling outages, which have been progressively reduced to a record 15.5 days at Loviisa-1 in 1997. -
1 Notes for the Helsinki Commission Briefing on Hungary, April 9, 2019
Notes for the Helsinki Commission Briefing on Hungary, April 9, 2019 Dalibor Rohac, American Enterprise Institute THIS VERSION: April 5, 2019 Since its decisive electoral victory in 2010, Fidesz has embarked on a distinctly authoritarian political project, as articulated in Viktor Orbán’s speech on July 26, 2014 in Romania. There, he singled out Singapore, China, India, Turkey, and Russia as “stars of international analysts”; touted the idea of illiberal democracy; and suggested that Hungary needed to part with Western European “dogmas,” especially with the liberal notion that people “have the right to do anything that does not infringe on the freedom of the other party.”1 Fidesz policies have been consistent with the message of that speech. They have pushed Hungary down the path of kleptocratic authoritarianism along the Turkish and Russian lines: packing of courts, a gradual tightening of restrictions on civil society organizations, mobilization of public opinion against imaginary external enemies, and the concentration of media ownership in few hands close to the ruling party. True, Fidesz relies on strong popular support – yet the party received only 50 percent of the popular vote in the most recent elections of 2018, which translated into a two‐thirds supermajority in parliament thanks to quirks of Hungary’s electoral law. Moreover, even the openly autocratic governments of Turkey and Russia rely on substantial popular support.2 Popular support does not justify crude majority rule, dismantling checks and balances, attacking civil society, distorting markets, and concentrating power in the hands of a narrow political elite. This note focuses on three aspects of Hungary’s development: (1) measurable decline in institutional quality, (2) patterns of politically organized corruption, (3) instances in which Hungary’s government has openly defied the US interests in Central Europe. -
EXTERNAL VECTOR of ROSATOM's DEVELOPMENT: CASE STUDIES of ACTIVITIES in TURKEY, FINLAND and HUNGARY Master's Thesis
MASARYK UNIVERSITY FACULTY OF SOCIAL STUDIES DEPARTMENT OF INTERNATIONAL RELATIONS AND EUROPEAN STUDIES EXTERNAL VECTOR OF ROSATOM’S DEVELOPMENT: CASE STUDIES OF ACTIVITIES IN TURKEY, FINLAND AND HUNGARY Master’s Thesis Author: Nikita Minin UČO: 419802 Supervisor: PhDr. Tomáš Vlček, Ph.D. Study Field: Energy Security Studies Year of Enrollment: 2014 Brno, 2016 2 STATEMENT OF AUTHORSHIP I hereby declare that this thesis I submit for assessment is entirely my own work and has not been taken from the work of others save to the extent that such work has been cited and acknowledged within the text of my work. Date: Nikita Minin ……………………… 3 ACKNOWLEDGEMENTS Sincere words of gratitude go to Tomáš Vlček, who was supervising and guiding me throughout the whole process of making this work happen. Unless for his much appreciated advice, this thesis would not look the way it does, neither it would contribute to my personal and academic growth the way it has done. I would also like to thank the whole department and lecturers for their individual approach towards the issues that were arising in the course of studies and thesis writing. In addition, I’m exceptionally grateful to my parents, who supported me no matter what and believed in me, even when I doubted myself. Moreover, my personal huge thanks go to the European Commission as such that has provided an indispensable financial support for getting the degree at stake through the Erasmus Mundus scheme. With this regard, I’d like to mention Violeta Osouchová, who was supervising my stay and has demonstrated outstanding care and understanding, when dealing with students’ requests, which can be referred to the whole team of the Masaryk University Centre for International Cooperation. -
THE WORLD NUCLEAR WASTE REPORT 2019 Focus Europe. PARTNERS & SPONSORS
THE WORLD NUCLEAR WASTE REPORT 2019 Focus Europe. PARTNERS & SPONSORS Bürgerinitiative Umweltschutz Lüchow-Dannenberg This report would have not been possible without the generous support of a diverse group of friends and partners, in particular – listed in alphabetical order – the Altner-Combecher Stiftung, Bäuerliche Notgemeinschaft Trebel, Bund für Umwelt und Naturschutz (BUND), Bürgerinitiative Umweltschutz Lüchow-Dannenberg e.V., Climate Core and Green/EFA MEPs Group in the European Parliament, Heinrich-Böll-Stiftung (HBS) and its offices in Berlin, Brussels, Paris, Prague, and Washington DC, KLAR! Schweiz, Annette und Wolf Römmig, and the Swiss Energy Foundation. Thank you all for making this possible! THE WORLD NUCLEAR WASTE REPORT — 2019 3 FOREWORD More than 40 years ago in my home region, the forest near the village of Gorleben was chosen as the location for the German National Nuclear Waste Disposal Center. The site, which is now at the country’s center but at the time was located directly on the border between East and West Germany, was meant to host all facilities for reprocessing, treatment, storage, and a deep geological repository. The company responsible (which has long since closed) intended to open the repository for spent fuel in the salt dome named Gorleben-Rambow in 1999. After Fukushima, the German government decided to phase out nuclear energy for the second time. The experience of the nuclear catastrophe in Japan in 2011 also set in motion the review of the plans for the repository at Gorleben. After around 40 years of debating and fighting over Gorleben, the German government and parliament decided in favor of a new participatory site selection process for the repos- itory for high-level nuclear waste. -
Multipurpose Utilisation of a Medium Flux Research Reactor – Benefit for the Society
A12 MULTIPURPOSE UTILISATION OF A MEDIUM FLUX RESEARCH REACTOR – BENEFIT FOR THE SOCIETY L. ROSTA Research Institute for Solid State Physics and Optics, Budapest, Hungary Abstract The Budapest Research Reactor (BRR) was restarted after a major refurbishment and increase in power to 10 MW in 1992. Basically, the experience gained with the utilization of this multipurpose facility during the past 20 years is described here. The utilization aims for 3 major activities: i) Research and development base for the energy sector: scientific and safety support for the Paks NPP; research in energy saving and production. ii) A complex source of irradiations for materials testing and modification, diagnostics in nanotechnologies, engineering, healthcare etc. iii) Neutron beams from the horizontal channels of the reactor serve for exploratory as well as for applied research in a very wide range of disciplines. Graduate and professional training is also in the scope of our activity. The reactor went critical first in 1959. It served nearly 3 decades as a home base for learning nuclear sciences and technologies, to development nuclear energetics, which resulted in launching four power plant blocks in the eighties, as well as to establish neutron beam research in our country. Nearly 20 years passed now that the decision was made — after the falling of the “Iron Curtain” — the practically brand new 10 megawatt reactor should be commissioned and opened for the international user community. The reactor reached its nominal power in May 1993 and neutron beam experiments were available on 4 instruments at that time. Thanks to a continuous development the number of experimental stations now is 15, the research staffs has grown from 10 to nearly 50 scientists and research facilities have been improved considerably.