Vehicle Stabilization
Total Page:16
File Type:pdf, Size:1020Kb
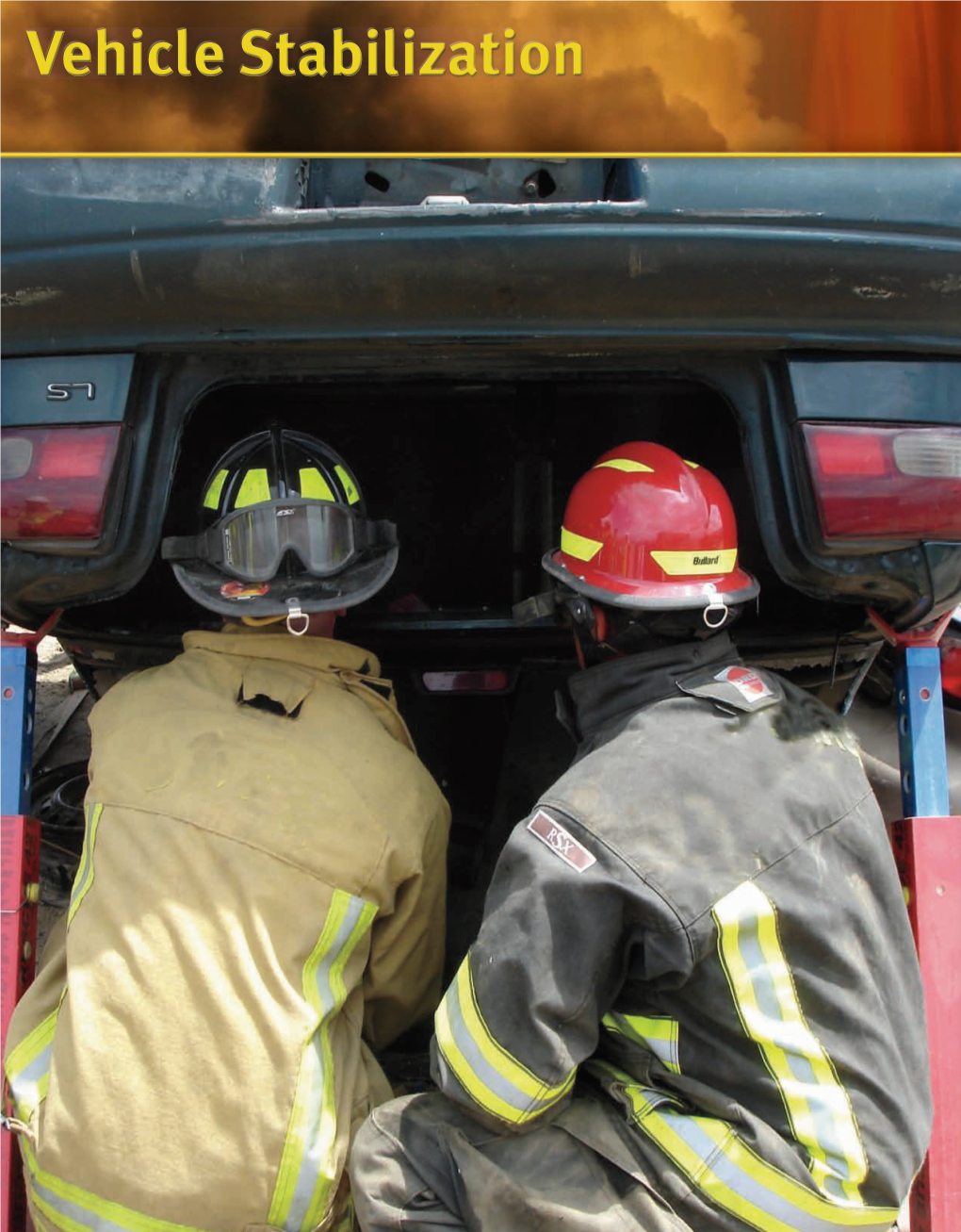
Load more
Recommended publications
-
Get to Know Guide
Review this Quick Reference Guide for an overview of some important features in your Chevrolet Corvette. More detailed information can be found in your Owner Manual. Some optional equipment✦ described in this guide may not be included in your vehicle. For easy reference, keep this guide with your Owner Manual in your glove box. ✦ denotes optional equipment www.chevrolet.com INSTRUMENT PANEL Turn Signal Lever/ Driver Head-Up Display Exterior Lamps Control/ Windshield Information Controls✦ Cruise Control Wipers Lever Center Controls Power Fuel Door Release Bluetooth Tilt Steering Telescopic Audio Steering Start/Stop Folding Top Button/Hatch-Trunk Controls✦ Wheel Steering Wheel Wheel Button Button✦ Release Button Lever Button✦ Controls Symbols Fog Lamps Check Engine Antilock Brake System Warning Lights On Low Tire Pressure Safety Belt Reminder Security Brake System Warning 1 to 4 Shift Airbag Readiness (manual Active Handling/ transmission) Traction Control Off 2 Hazard Warning Audio System/ Automatic Climate Flashers Button Navigation System✦ Controls Active Driver’s Passenger’s Handling Heated Seat Heated Seat System Button Control✦ Control✦ Note: Refer to your Owner Manual to learn about the information being relayed by the lights and gauges of the instrument cluster, as well as what to do to ensure safety and prevent damage to your vehicle. See Instruments and Controls in your Owner Manual. 3 KEYLESS ACCESS SYSTEM The Keyless Access System enables operation of the doors, ignition and hatch/trunk without removing the transmitter from a pocket or purse. The system will recognize the transmitter when it is within 3 feet of the vehicle. Entering the Vehicle • With the transmitter within range of the vehicle, press the pad (A) at the rear edge of each door to unlock and open the door. -
State Laws Impacting Altered-Height Vehicles
State Laws Impacting Altered-Height Vehicles The following document is a collection of available state-specific vehicle height statutes and regulations. A standard system for regulating vehicle and frame height does not exist among the states, so bumper height and/or headlight height specifications are also included. The information has been organized by state and is in alphabetical order starting with Alabama. To quickly navigate through the document, use the 'Find' (Ctrl+F) function. Information contained herein is current as of October 2014, but these state laws and regulations are subject to change. Consult the current statutes and regulations in a particular state before raising or lowering a vehicle to be operated in that state. These materials have been prepared by SEMA to provide guidance on various state laws regarding altered height vehicles and are intended solely as an informational aid. SEMA disclaims responsibility and liability for any damages or claims arising out of the use of or reliance on the content of this informational resource. State Laws Impacting Altered-Height Vehicles Tail Lamps / Tires / Frame / Body State Bumpers Headlights Other Reflectors Wheels Modifications Height of head Height of tail Max. loaded vehicle lamps must be at lamps must be at height not to exceed 13' least 24" but no least 20" but no 6". higher than 54". higher than 60". Alabama Height of reflectors must be at least 24" but no higher than 60". Height of Height of Body floor may not be headlights must taillights must be raised more than 4" be at least 24" at least 20". -
Chassis Control
CHASSIS CONTROL MASAHARU SATOU DEPUTY GENERAL MANAGER VEHICLE DYNAMICS ENGINEERING GROUP INFINITI PRODUCT DEVELOPMENT DYNAMIC PERFORMANCE of INFINITI Q50 In control ( Precise handling & Small correction ) . DAS ( Most advanced steering system in the world ) . Stiffer chassis ( Body & Suspension ) . Good aerodynamics Cl ( zero lift ) . Tire improvement . Enhancing good fuel economy . Improved thanks to initial media feedback STIFFER CHASSIS FOR BETTER HANDL ING . 60% Improvement in front end bending stiffness from previous model FR BODY BENDING DASH/COWL TOP STIFFNESS panel Reinforcement G sedan Q50 60% Stiffness G sedan Smooth section to Q50 SILL/FR FLOOR support circular structure Reinforcement FR END Circular structure HIGH TENSIL E STEEL . First use of 1.2G High Elongation and High Tensile Steel . W eight reduction of 13 pounds . Provides lower profile structure and additional headroom . Increases body stiffness Hot Press 1.2GPa 980MPa 1.2G High Tensile Steel 780MPa W orld first for automotive 590MPa NEW MUL TI-L INK REAR SUSPENSION . New geometry & structure . Camber stiffness 8% improve . Reduced road noise AERODYNAMICS . Infiniti Q50 has zero aerodynamic lift at the front and rear Rear lift . Accomplished without front and rear spoilers ★ Competitor A . Early collaboration with design ★ ★ Competitor B and engineering team ★ Competitor C Competitor D ★ Q50 Front ZeroLift Rear Zero Lift Front lift AERODYNAMICS . Drag coefficient is 0.26 Cd . This contributes to improved fuel economy Drag (Cd) Better Infiniti Q50 0.26 BMW3 (11MY) 0.27 BMW3 (12MY) 0.26 Mercedes Benz C 0.27 Audi A4 0.28 L exus IS (12MY) 0.31 OTHER HANDL ING UPGRADES 3rd Gen. run-flat tire Upgraded double- Reduced Good grip wishbone front suspension unsprung weight Low RRC DIRECTOR OF PERFORMANCE INFINITI Q50 CHASSIS BENEFITS . -
§1920. Vehicle Frame Height §1920. Vehicle Frame
MRS Title 29-A, §1920. VEHICLE FRAME HEIGHT §1920. Vehicle frame height 1. Minimum and maximum frame end heights. A motor vehicle may not be operated on a public way or receive a certificate of inspection with a frame end height of less than 10 inches or with the frame end height lower than the vehicle was originally manufactured if originally manufactured to be less than 10 inches. A motor vehicle may not be operated on a public way or receive a certificate of inspection with a maximum frame end height based on the manufacturer's gross vehicle weight rating that is greater than: A. [PL 2005, c. 276, §2 (RP).] B. For a vehicle of 4,500 pounds and less, 24 inches in the front and 26 inches in the rear; [PL 1993, c. 683, Pt. A, §2 (NEW); PL 1993, c. 683, Pt. B, §5 (AFF).] C. For a vehicle of 4,501 pounds to 7,500 pounds, 28 inches in the front and 30 inches in the rear; [PL 2019, c. 335, §2 (AMD).] D. For a vehicle of 7,501 pounds to 10,000 pounds, 30 inches in the front and 32 inches in the rear; [PL 2019, c. 335, §2 (AMD).] E. For a vehicle of 10,001 pounds to 11,500 pounds, 31 inches in the front and 33 inches in the rear; and [PL 2019, c. 335, §3 (AMD).] F. For a vehicle of 11,501 pounds to 13,000 pounds, 32 inches in the front and 34 inches in the rear. [PL 2019, c. -
Effec Tive 7/16/2020
EFFEC TIVE 7/16/2020 In addition to the valuable warranty information you will find herein we encourage you to visit the Continental Tire the Americas, LLC (“CTA”) website at www. continentaltire.com (US) and www.continentaltire.ca (Canada) for safety and maintenance information and up-to-date changes, including a Customer Care FAQ tab with downloadable brochures. Please also visit the Rubber Manufacturer Association (RMA) website at www.rma.org for additional safety and maintenance information. THE TOTAL CONFIDENCE PLAN IS NOT A WARRANTY THAT THE TIRE WILL NOT FAIL OR BECOME UNSERVICABLE IF NEGLECTED OR MISTREATED. The purchase of Continental brand tires provides an extra measure of confidence with the support of the Total Confidence Plan. The Total Confidence Plan is a comprehensive package of all available warranties and services including: Limited Warranty, Flat Tire Roadside Assistance, Customer Satisfaction Trial, Mileage Warranty (if applicable) and Road Hazard Coverage. 2 2 1. ELIGIBILITY The Total Confidence Plan applies to the original owner of new Continental brand passenger and light truck (LT) tires that are (a) new replacement market tires bearing the Continental brand name and D.O.T. Tire Identification Number, (b) operated in normal service, (c) used on the same vehicle on which they were originally installed according to the vehicle manufacturer’s recommendations and (d) purchased from an authorized Continental brand tire dealer. Tires used in competition are not eligible for any coverage under this Total Confidence Plan. Additionally, tires used in commercial service including, but not limited to, taxicabs, police cars, emergency vehicles, non- passenger service vehicles are not eligible for the extra coverage set forth in Section 3 of this Total Confidence Plan. -
2013 ANNUAL REPORT CITY of MILTON FIRE DEPARTMENT 2013 ANNUAL REPORT
CITY OF MILTON FIRE DEPARTMENT 2013 ANNUAL REPORT CITY of MILTON FIRE DEPARTMENT 2013 ANNUAL REPORT 2013 was another very active and productive year for the City of Milton Fire Department which afforded great opportunities to implement positive improvements, placing the department in a very stable position for coming years. Overall emergency response activity was slightly below the prior year, allowing members to complete many ongoing projects, while also accomplishing several long-term goals. All of this activity has placed us in an excellent position to accomplish our primary mission of providing emergency services to the citizens of Milton. EMERGENCY ACTIVITY Despite a slight reduction in the overall number of emergency responses, 2013 still presented several challenging incidents requiring more than the response of the initial alarm assignment. The total number of emergency calls decreased by roughly 1.75%, down to 1,463 calls, from 1,489 the previous year. This reduction is attributable to two related issues: a reduction of nearly 5% in the number of medical response calls, and a nearly 16% reduction in the number of vehicle accidents. There is no clear explanation for the cause of these reductions. Otherwise, this year’s activity actually reflects a continued stabilization of annual activity over the past 10 years to roughly 1,500 calls per year. Rescue calls decreased this year, now totaling 1,202 calls, but still constitute the vast majority of our emergency calls, now 82% of our annual emergency activity. Rescue calls include: medical emergencies such as strokes, heart attacks, falls, etc.; all vehicle accidents including those that involve entrapment requiring forcible extrication with specialized hydraulic tools such as the “Jaws of Life”; and rescue calls like a child locked in a vehicle, elderly who have fallen and need help back into bed (lift assist), and even the occasional animal rescue. -
A Thesis Entitled Design, Analysis and Optimization of Rear Sub-Frame Using Finite Element Modeling and Modal Analysis by Gaurav
A Thesis entitled Design, Analysis and Optimization of Rear Sub-frame using Finite Element Modeling and Modal Analysis by Gaurav Kesireddy Submitted to the Graduate Faculty as partial fulfillment of the requirements for the Master of Science Degree in Mechanical Engineering _________________________________________ Dr. Hongyan Zhang, Committee Chair _________________________________________ Dr. Sarit Bhaduri, Committee Member _________________________________________ Dr. Matthew Franchetti, Committee Member _________________________________________ Dr. Amanda Bryant-Friedrich, Dean College of Graduate Studies The University of Toledo May 2017 Copyright 2017, Gaurav Kesireddy This document is copyrighted material. Under copyright law, no parts of this document may be reproduced without the expressed permission of the author. An Abstract of Design, Analysis and Optimization of Rear Sub-frame using Finite Element Modeling and Modal Analysis by Gaurav Kesireddy Submitted to the Graduate Faculty as partial fulfillment of the requirements for the Master of Science Degree in Mechanical Engineering The University of Toledo May 2017 A sub-frame is a structural component of an automobile that carries suspension, exhaust, engine room, etc. The sub-frame is generally bolted to Body in White(BIW). It is sometimes equipped with springs and bushes to dampen vibration. The principal purposes of using a sub-frame are, to spread high chassis loads over a wide area of relatively thin sheet metal of a monocoque body shell, and to isolate vibration and harshness from the rest of the body. As a natural development from a car with a full chassis, separate front and rear sub-frames are used in modern vehicles to reduce the overall weight and cost. In addition, a sub-frame yields benefits to production in that subassemblies can be made which can be introduced to the main body shell when required on an automated line. -
Vehicle Extrication
VEHICLE EXTRICATION Rio Hondo Regional Truck Operations Academy COURSE OBJECTIVES • Review of basic operations and terminology • Review Airbags, SRS, Battery locations and 5-10-20 Rule • Review Hybrid and AFV • Review Stabilization • Review Extrication techniques • Station A Equipment Review • Questions BASIC OPERATIONS • Scene Size Up • Vehicle Assessment “Reading the Wreck” • Patient Assessment • Stabilization • Scan for Airbags/SRS “Peel and Peek” • Gain Access to Patient “5-10-20 Rule” • Extrication Techniques • Patient Removal SIZE UP • Scene Safety and assessment • Victim assessment • Vehicle assessment “Reading the Wreck” • Extrication assessment • Size-up continues until the incident is terminated SCENE ASSESSMENT • Scene Safety • Vehicle traffic • Safe working area • Fuel spills • Down power lines • Environmental considerations • Fires • Alternative Fuel Vehicle leak VEHICLE ASSESSMENT • “Reading the Wreck” Position, Damage and Stability Vehicle construction and type Vehicle and Patient Condition • Vehicle safety systems Air bags/SRS Seat belt Pretensioners Batteries Glass Management READING THE WRECK FULL FRAME CONSTRUCTION Designed to Deflect Energy UNIBODY CONSTUCTION Designed to Absorb/Transfer Energy SPACE FRAME CONSTRUCTION Designed to Absorb/Transfer Energy High Strength Steel VEHICLE ANATOMY One-piece hydroformed body side rings. Door hinges secured by thick through-bolts located in A- and B-pillars. Cast magnesium transverse beam behind the instrument panel. Triple-rolled Pillar/Rail design resists roof collapse. Shock -
Program Benefits a Short Description of All Program Benefits “A Truly Great Product Is Ultimately Defined by the Customer Experience.”
Program Benefits A Short Description of All Program Benefits “A truly great product is ultimately defined by the customer experience.” True Coverage Coverage for exclusions that commonly create problems. Use this comparison chart to see how RoadVantage coverages stack up against other providers. Your Coverage RoadVantage Provider:________________________________ Tire & Wheel 1 Cosmetic Coverage: Alloy, Chrome/Clad Wheels x or Tire & Wheel 2 Cosmetic Coverage: Wheel Covers (Hubcaps) x or Tire & Wheel 2 Cosmetic Damage - Wheel Replaced if not Repairable x or Tire & Wheel Construction Zones x or Tire & Wheel Tire Pressure Monitor Sensors x or Tire & Wheel Snow Tires x or Tire & Wheel Car Wash x or Tire & Wheel Aftermarket Wheels Meeting 2 Manufacturer’s Specs or with no surcharge x Dent & Ding 2 Hail Damage Benefit x or Dent & Ding Horizontal and Vertical Panels x or Dent & Ding Up to 4 inches vs. 2 inches x or Key Replacement Per Occurrence vs. Aggregate x or Key Replacement Additional Keys Replaced x or 7-Year Terms x or All Programs No Limits x or 1 Included in Plus programs. 2 Included in Preferred programs. PreferredPlus Bundles Compared Coverage Options PreferredPlus Bundles PreferredPlus PreferredPlus Care Tire & Wheel Repair/Replacement w/TPMS Cosmetic Wheel Repair/Replacement Dent & Ding Repair w/Hail Windshield Repair 24-Hour Roadside Assistance Key Replacement Wheel Covers Aftermarket Wheels Curb Damage Interior/Exterior Repair Chrome & Chrome Clad Wheels Program availability varies by state. Please contact your Regional Vice President for details. PreferredPlus & PreferredPlus Care F&I PRODUCTS AND SOLUTIONS Protection Programs Drive Higher Profits on Retail Sales and Leases. -
The Basics of Electricity and Vehicle Lighting the Basics of Electricity and Lighting
$200.00 USD Series of Self-Study Guides from Grote Industries The Basics of Electricity and Vehicle Lighting The Basics of Electricity and Lighting How To Use This Book This self-study guide is divided into six sec- down to expose the first line of the second tions that cover topics from basic theory of question. The answer to the first question is electricity to choosing the right equipment. shown at the far right. Compare your answer It presents the information in text form sup- to the answer key. ported by illustrations, diagrams charts and Choose an answer to the second question. other graphics that highlight and explain key Slide the cover sheet down to expose the first points. Each section also includes a short quiz line of the third question and compare your to give the you a measure of your comprehen- answer to the answer key. sion. At the end of the guide is a final test that In the same manner, answer the balance of is designed to measure the learner’s overall the quiz questions. comprehension of the material. The final exam at the end of this guide To get the most value from this study guide, presents a second test of your knowledge of carefully read the text and study the illustra- the material. Be certain to use the quizzes and tions in each section. In some cases, you may final exam. In the case of the final exam, fold want to underline or highlight key information the answer sheet as directed, and mail to the for easier review and study later. -
Three for One Road Hazard Protection Vehicle Service Contract
Three For One Road Hazard Protection Vehicle Service Contract Peace of mind for the road ahead. What does Three For One do for you? You can’t always tell what the road ahead might bring. Sometimes, even the most casual trip can put your car at risk of potholes, windshield chips and parking lot dings. Getting protection Even a rountine against each of these risks can be costly if purchased separately. trip can That’s why there’s Three For One Road Hazard Protection. become costly. Three For One Road Hazard Protection bundles the coverages you need to keep your car in safe condition and looking new. This comprehensive program covers repairs to your tires, wheels and windshield, and paintless dent repair — a revolutionary process that makes dings virtually disappear. By combining three coverages into one program, you get more benefits for less cost. You’ve made a significant investment in your new vehicle. Keep it in great shape for the miles ahead with Three For One Road Hazard Protection. Protection Plans Tire and Wheel y Repair or, if nonrepairable, the replacement of a damaged tire(s) and/or wheel(s) caused by potholes or other road hazards y Cosmetic wheel repair for damage such as nicks, scratches and scrapes up to $150 per occurrence ($600 maximum for Service Contract term) y No limit on number of occurrences y Covers mounting, balancing, new valve stem and sales tax y No deductible y No mileage limitations Windshield y Repairs chips and cracks up to 6 inches on your front windshield caused by propelled rocks or other road hazards -
Vin Clarke Pdf Free Download
VIN CLARKE PDF, EPUB, EBOOK Larrie Benton Zacharie | 72 pages | 25 Oct 2011 | Verpublishing | 9786137815380 | English | United States Vin Clarke PDF Book More From Reference. With a little help from your trusty VIN decoder, you should be feeling confident about your purchase in no time at all. Shine the flashlight on the engine to illuminate small parts. Give them specific details about the truck. For instance, the 6 signifies a model year. Jonathan Lamas is a seasoned automotive journalist. You can identify attributes like the model, engine type and body style from these symbols. Click on "Decode," then scroll down on the next screen to read your vehicle's features. This includes all the extra details, such as the style or trim of a vehicle, that a VIN record will not. A vehicle identification number VIN can tell you everything you need to know about a car. Jonathan Lamas. Contacting a dealership Sometimes specific vehicle information cannot be sought using a VIN decoder. The VIN system was first developed in the mids, but it didn't take on its modern format until The records obtained through a VIN on that site search may contain incorrect information. If you don't see the VIN, check this area on all four wheel frames. You have a Social Security number. The first step to decoding a VIN is to locate the full digit code. When you consider vanity plates too that represent the owner rather than the car, you can see that license plates are not an accurate way of identifying cars. Some states require insurance firms to provide the Department of Motor Vehicles DMV with your VIN along with the insurance policy number so they can police uninsured vehicles.