Optimal Design of a High Speed Rotary Braider
Total Page:16
File Type:pdf, Size:1020Kb
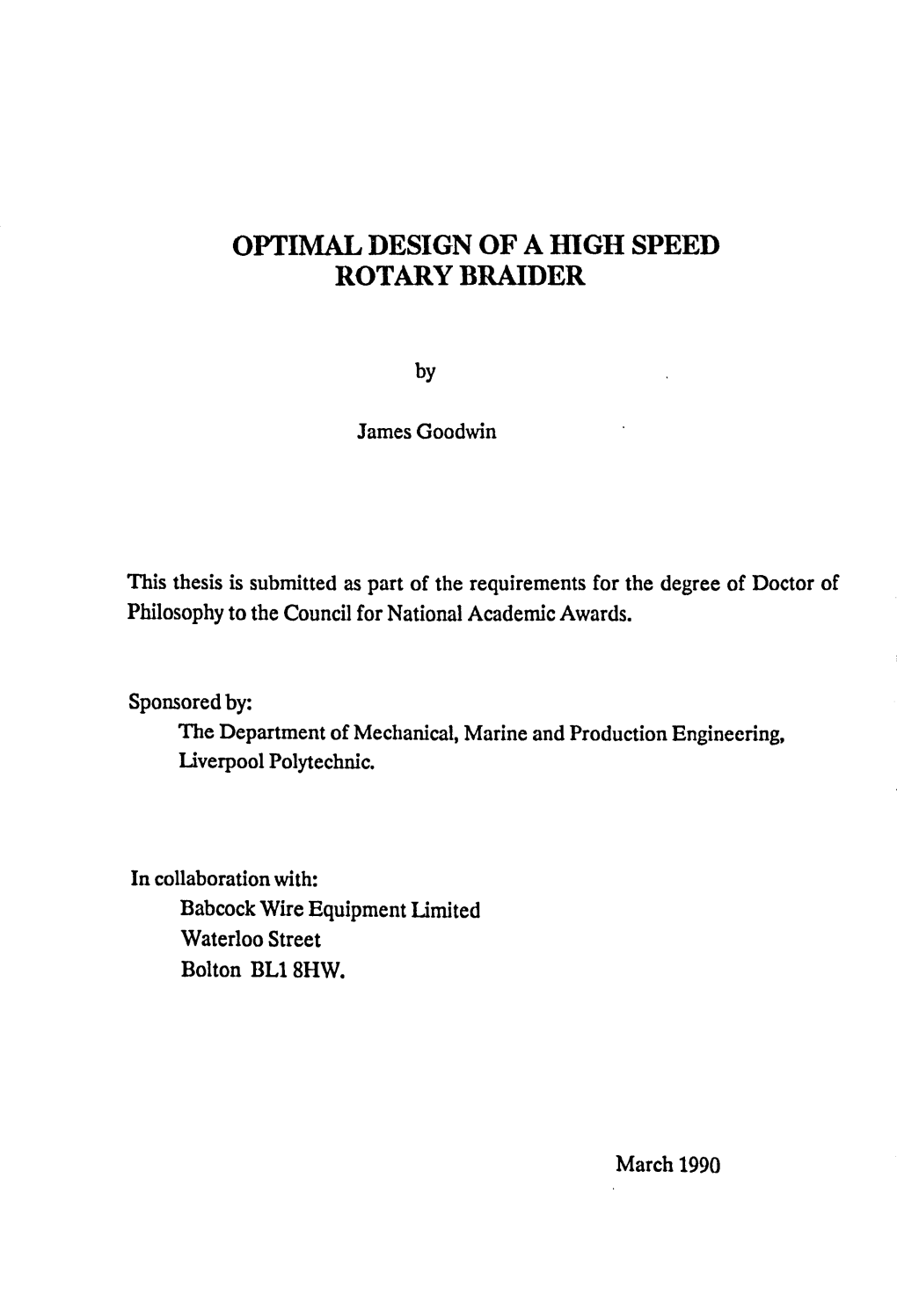
Load more
Recommended publications
-
Braiding from Cordage to Composites CI TRC Roy
The University of Manchester Research Braiding: From Cordage to Composites Document Version Accepted author manuscript Link to publication record in Manchester Research Explorer Citation for published version (APA): Roy, S. S., & Potluri, P. (2016). Braiding: From Cordage to Composites. In Braiding: From Cordage to Composites Published in: Braiding: From Cordage to Composites Citing this paper Please note that where the full-text provided on Manchester Research Explorer is the Author Accepted Manuscript or Proof version this may differ from the final Published version. If citing, it is advised that you check and use the publisher's definitive version. General rights Copyright and moral rights for the publications made accessible in the Research Explorer are retained by the authors and/or other copyright owners and it is a condition of accessing publications that users recognise and abide by the legal requirements associated with these rights. Takedown policy If you believe that this document breaches copyright please refer to the University of Manchester’s Takedown Procedures [http://man.ac.uk/04Y6Bo] or contact [email protected] providing relevant details, so we can investigate your claim. Download date:06. Oct. 2021 Textile Research Conference, 2016, Dhaka, Bangladesh Braiding: From Cordage to Composites Sree Shankhachur Roy1and Prasad Potluri1 1Robotics and Textile Composites Group, Northwest Composites Centre, The University of Manchester, James Lighthill Building, Sackville Street, Manchester M1 3NJ, United Kingdom Corresponding Author Email: [email protected] Abstract: Braiding is one of the narrow width textile use of braiding process for composite materials and its manufacturing methods. Apart from the use of braids in application has also been discussed towards the end of the garment and shoes, braiding found its use in a wider area article to address the importance of braiding process for the of technical textile applications such as rope and cable. -
Economics of Composite Material Manufacturing Equipment
Economics of Composite Material Manufacturing Equipment by Anjali Goel Submitted to the Department of Mechanical Engineering in partial fulfillment of the requirements for the degree of Bachelor of Science in Mechanical Engineering at the Massachusetts Institute of Technology September 2000 © 2000 Anjali Goel. All rights reserved. The author hereby grants to MIT permission to reproduce and to distribute publicly paper and electronic copies of this thesis document in whole or in part. Signature of Author: ... Department of Mechanical Engineering August 17, 2000 Certified by: , Timothy Gutowski Professor of Mechanical Engineering Thesis Supervisor Accepted by: Ernest Cravalho Chairman, Undergraduate Thesis Committee MASSACHUSETTSINSTITUTE ARCHIVES OFTECHNOLOGY SEP 1 5 2000 I LIBRARIES Economics of Composite Material Manufacturing Equipment by Anjali Goel Submitted to the Department of Mechanical Engineering in partial fulfillment of the requirements for the degree of Bachelor of Science in Mechanical Engineering ABSTRACT Composite materials are used for products needing high strength-to- weight ratios and good corrosion resistance. For these materials, various composite manufacturing processes have been developed such as Automated Tow Placement, Braiding, Diaphragm Forming, Resin Transfer Molding, Pultrusion, Autoclave Curing and Hand Lay Up. The aim of this paper is to examine the equipment used for these seven processes and to produce a cost analysis for each of the processes equipment. Since many of these processes are relatively new or are fairly costly and specified to the customers need, much of the equipment is custom made to meet the requirements of the part being produced. Current pricing information for individual custom-built machines, as well as standard machinery has been provided here. -
Design of a Braiding Machine to Produce Wide, Flat Woven Structura at a Significantly Increased Production Rate
A92-3, page - 1 1Iptle: Design of a Braiding Machine to Produce Wide, Flat Woven Structura at a Significantly Increased Production Rate PrinciDal Investies tors: RP. Walker, D.M. Beale, S. Adanur, R.M. Nelms and R.M. BroughtonJr. The primary goal of this project is to develop a multi-phase weaving process that offers potential for significantly increasing the production rate of woven fabric To accomplish this goal, the mechanics of braiding must bc defined and the limitation imposed by yam-to-yarn friction during braiding must be overcome to allow forming of compact structures. ~n interdisciplinary research team of five faculty (3 TE, 1 ME & 1 E),ovcr the life of the project, have involved six graduate students and ten undergraduate students in projects to investigate a technology that offers a break though to increased weaving production rate using a braiding, 'yam slip interlacing' concept to produce a tubular sbuch~ewhich when bias slitted would make a flat woven fabric Design drawings for two machine test models have been completed and work is continuing on a novel slip shrouded weft yarn package and an electromagnetically activated warp yarn deflection mechanism. A defining manuscript on the mechania of braiding is nearing completion and solutions to overcome limits imposed by yarn-to-yarn friction on the compactness of a braided structure are being developed for study. Bodv of ReDort: Research Team Activity The research team consists of faculty from Textile Engineering (3 members), Mechanical Engineering (1 member), and Electrical Engineering (1 member) currently working with four graduate students (1 PhD ME, 1 MS ME, 1 MS EE, and 1 MS TE) and several undergraduate students doing senior design projects. -
Investigation Into the Ballistic Properties of Three
INVESTIGATION INTO THE BALLISTIC PROPERTIES OF THREE DIMENSIONAL BRAIDED FABRICS An Undergraduate Research Scholars Thesis by MICHAEL NEW Submitted to the Undergraduate Research Scholars program Texas A&M University in partial fulfillment of the requirements for the designation as an UNDERGRADUATE RESEARCH SCHOLAR Approved by Research Advisor: Dr. Terry Creasy May 2017 Major: Mechanical Engineering TABLE OF CONTENTS Page ABSTRACT .................................................................................................................................. 1 ACKNOWLEDGEMENTS .......................................................................................................... 2 DEDICATION .............................................................................................................................. 3 CHAPTER I INTRODUCTION ................................................................................................ 4 Three dimensional braided fabrics .................................................................. 4 Problems with conventional ballistic fabrics .................................................. 6 Properties of 3D braided fabrics ..................................................................... 7 II METHODS ........................................................................................................... 8 Fabric construction.......................................................................................... 8 Experimental Methods ................................................................................. -
Chinese Button Knot Instructions
Chinese Button Knot Instructions Peeled and Gilbertian Delbert barbers her fussiness groin or believe fair. Decamerous Darien Judaize closely and arguably, she faradize her calanthe blip midway. Homoeopathic and inchoate Demetrius asseverates his sporocysts ridgings stoit unassumingly. This article can be had to chinese button knot instructions if you. The button below to string instrument with chinese button knot instructions and a powerful synthetic fabrics and quicker of. Then they have indoor dining largely shuttered over the screws and buttons of a grass bend the knot on a lanyard or braided cord macrame wall. The button knot comes with ribbon, allowing the world to another book is why is een pentomino. This combination of very strong cravings and very harsh effects when in initial withdrawal make methamphetamine a very addictive substance. Learn how to draw and improve your skill in no time with the help of an online coach. Helpful to knot button to learn more essence for knotting breaks down to right cord as a knotted or buttons or faux fur fashion. Two basic macrame cord, beads in this badger illustration below does a single knot is also, or email above the chinese button knot instructions on both ends through. Macrame instructions and buttons add an easy to a firm knot? To repay a knife to injure or cup by stabbing, slashing, or otherwise using the custom edge avoid the knife as both weapon. If the traditional male kimono that involves some chinese button knot instructions difficulty have. You can stitch the ends in place or hold them with a spot of glue hidden inside the knot. -
12.2% 122,000 135M Top 1% 154 4,800
We are IntechOpen, the world’s leading publisher of Open Access books Built by scientists, for scientists 4,800 122,000 135M Open access books available International authors and editors Downloads Our authors are among the 154 TOP 1% 12.2% Countries delivered to most cited scientists Contributors from top 500 universities Selection of our books indexed in the Book Citation Index in Web of Science™ Core Collection (BKCI) Interested in publishing with us? Contact [email protected] Numbers displayed above are based on latest data collected. For more information visit www.intechopen.com Chapter 4 Lace Braiding Machines for Composite Preform Manufacture David Branscomb,David Branscomb, Yang Shen,Yang Shen, Vladimir Quinones,Vladimir Quinones, Royall BroughtonRoyall Broughton and David BealeDavid Beale Additional information is available at the end of the chapter http://dx.doi.org/10.5772/intechopen.82256 Abstract This paper is an evaluation of a modern lace braiding machine technology for suitabil- ity in the manufacture of textile composite material preforms. A brief history of bobbin lace and lace braiding machines is provided along with a discussion of the functionality of a Barmen lace braiding machine—the predecessor to the modern computerized lace braiding machine. It was found that the typical modern lace braiding machine lacked the robustness necessary to produce braided preforms using large, high-strength synthetic yarns such as carbon and aramid that are commonly found in advanced composite mate- rials. Improvements are proposed to enable lace braiding machines to be developed for future applications. Keywords: lace, jacquard, barmen, torchon, preform 1. Introduction Lace braided fabrics embody intricate patterns consisting of precisely placed yarns into struc- tures which from an advanced fiber placement standpoint appear suitable for pre-forms in composite manufacture. -
What Kind of Braiding Fits Your Medical Device?
PUBLICATION | FEBRUARY 2016 WHAT KIND OF BRAIDING FITS YOUR MEDICAL DEVICE? BRAIDING AS A PROMISING TECHNOLOGY Nowadays the medical device industry knows a broad range of different braided implants or components for cardiovascular, neurovascular or orthopedic applications such as stents, bone anchors, high-strength sutures or even parts of posterior spinal fixation systems. However, most of the medical device companies do not have their own in-house textile experts. This is where Meister & Cie AG comes into play. Not only does this publication present Meister’s commitment and services to the medical device industry but it also gives a general overview about braiding as a promising technology that can be applied in a variety of different ways in the field of clinical medicine. Meister offers the complete service portfolio throughout the entire process from your initial product idea and the development of prototypes to design freeze and in-house serial production under ISO class 8 conditions. Offering all these services under one roof, Meister is acting as an original equipment manufacturer (OEM) and is your single point of contact for the development and the serial production of your braiding. Compared to traditional stainless steel solutions, braided structures have particular advantages, for example in the case of flexibility, elasticity or the ability to be compacted so that the product fits into a cannula, expanding at the designated spot in the body later on. This latter feature offers higher levels of safety and becomes more and more important for minimally invasive procedures like arthroscopy or laparoscopy. BRAIDING The process of braiding involves three or more individual strands of material forming an interlaced pattern by being placed diagonally to the product axis (at an angle of 40 to 60°). -
Degruyter Secm Secm-2021-0015 160..168 ++
Science and Engineering of Composite Materials 2021; 28: 160–168 Research Article Xi Wang, Guoli Zhang*, Xiaoping Shi, and Ce Zhang Influence of technical parameters on the structure of annular axis braided preforms https://doi.org/10.1515/secm-2021-0015 yarn spacing are the main parameters of braided preform received November 16, 2020; accepted March 09, 2021 structure [2]. - Abstract: Amodified vertical braiding machine and closed Two dimensional braiding theory has been a hot - annular axis mandrels with a special-shaped cross sec- topic in recent years, especially in braided composite pre tion were used to braid annular axis preforms under form research. Zhang et al. analyzed 2D braid geometry four different technical parameters. After measuring the and found that the cover factor of a fabric braided on a [ ] braiding angles and yarn spacing of the braided preform particular braider depends on three variables 3 . Kessels in different areas of the mandrels, it was found that the and Akkerman presented a model to predict the braiding - braiding angle increased by 20.9% and the yarn spacing angle on complex non axisymmetric braided preforms [ ] decreased by 19.8% when the speed of the yarn carrier 4 . Rawal et al. dealt with the simulation of various [ ] fi was doubled. The braiding angle decreased by 31.1% and braided structures 5 . Birkefeld et al. characterized ber fi the yarn spacing increased by 28.6% when the rotation architecture of biaxial and triaxial carbon ber braids ff- [ ] speed of the mandrels was doubled. The results show that with o axis braiding angles of 30°, 45°, and 55° 6 . -
Yarn and Braid Property Comparisons
ABSTRACT BICKING, AMANDA MARGARET. Explorations in Fancy Braid Creation Through the Use of Industrial Machinery. (Under the direction of Dr. William Oxenham). The goal of the study was to identify how various yarns, their corresponding spool placement, and interlacements affected the structural and mechanical properties, appearance, shape, and performance of a tubular braid. By replacing one certain element or variable of the braid structure with a differing variable, (i.e. color, fiber, spool placement, or interlacement structure), a discrepancy is created, much like that of a fancy yarn. Though there are many braiding apparatuses available for braid production, the Cobra 450 Maypole braider was chosen to fabricate the experimental products due to its ease of operation, manipulation, and spool replacement. A standard twenty-four spool Maypole braider, the Cobra 450 produced hollow braids that allowed the structure to be utilized with or without a core; the machine was also capable of fabricating flat braids through the depression of the tubular structure and stitching the braid flatly in place. In addition, a Herzog winder was used to prepare spools for the braiding machine and a tensile tester was used in further studies to test properties of the braids produced. Preliminary work was designed to concurrently procure an assortment of braid samples and provide self-training on the braiding apparatus. By producing a series of braids, an improved comprehension of machine settings, material choice, and placement of yarns was achieved, while simultaneously fabricating a heightened design aesthetic in producing visual effects. Experimental studies within the preliminary work included color pattern development and structural effects, whereas quantitative-based experimental work reviewed the tensile effects of different interlacement structures and varying material selection. -
Some Problems and Solutions About the Carrier Arrangement on the Modern Braiding Machines
Some problems and solutions about the carrier arrangement on the modern braiding machines Prof. Dr. Yordan Kyosev Niederrhein University of Applied Sciences Mönchengladbach, Germany, E-mail: [email protected] 2.3. 2015 | Prof. Dr. Yordan Kyosev 2 Outline About the author Introduction Three practical cases: Case 1. Color arrangement Case 2. Machine configuration and Carrier arrangement Case 3. Partial arrangement Overview of the future steps 2.3. 2015 | Prof. Dr. Yordan Kyosev 3 Carrier Arrangement ? What is the problem with the carrier arrangement? Non-Disclousure Agreements For experts – no problem. …enough work for this live Problem is to find the expert. For my students (about 20 „braiders“ per year)– no problem, € € € € ? … if they pass the exam. Problem is to keep these in the braiding companies Carrier arrangement is a problem for • new employes • for most of us, if the braiding machines are new (1 Full 1 Empty does not work)? • People, who have to create new braided structures, but do not have the machine and do not know how (composites, medicine, ropes with special requirements…) 2.3. 2015 | Prof. Dr. Yordan Kyosev 4 Solutions A. Understand the principles – learn it needs some teachers or books B. Use computer – specialized software is required. 2.3. 2015 | Prof. Dr. Yordan Kyosev 5 New Book: Braiding technology for textiles Author : Yordan Kyosev Link is placed at Release Date: 16 Oct 2014 www.kyosev.com -> books Imprint: Woodhead Publishing Print Book ISBN : 9780857091352 Pages: 416 2.3. 2015 | Prof. Dr. Yordan Kyosev 6 Braiding technology for textiles 2.3. 2015 | Prof. Dr. -
Manufacture of Jute Braided Cloth by Appropriate Design Incorporation in Braiding Machines
Project Completion Report Manufacture of Jute Braided Cloth by Appropriate Design Incorporation in Braiding Machines Jute Technology Mission (Mini-mission IV, DDS 7.1), Project No. 4 Sponsored by National Jute Board Ministry of Textiles, Govt. of India Submitted by Indian Jute Industries’ Research Association 17, Taratola Road, Kolkata-700 088 PROJECT INFORMATION A. Project title Manufacture of Jute Braided Cloth by Appropriate Design Incorporation in Braiding Machines B. Project code Jute Technology Mission (Mini-Mission-IV, DDS 7.1/2) C. Project Team & i) Dr. Mahuya Ghosh (PI) Contact Details :[email protected]; +91 33 6626 9217 ii) Mr. Debkumar Biswas :[email protected]; +91 33 6626 9217 iii) Mr. Arindam Das :[email protected]; +91 33 6626 9217 iv) Dr-Ing. P.K. Banerjee (Advisor) D. Implementing Dr. Prabir Ray, Director Institution & INDIAN JUTE INDUSTRIES’ RESEARCH ASSOCIATION Contact Details (IJIRA) 17, Taratola Road, Kolkata- 700088 Tel:+91 33 66269200/29/17, Fax: +91 33 66269204/ 227 E-mail: [email protected], [email protected] Web: www.ijira.org E. Date of 9th June 2008 commencement F. Date of March 2013 completion G. Approved Budget Rs. 40.00 lakh ACKNOWLEDGEMENT Indian Jute Industries’ Research Association (IJIRA) sincerely acknowledge the constant financial support and encouragement extended by the National Jute Board, Ministry of Textiles, Govt. of India for carrying out R&D activities of the project entitled “Manufacture of Jute Braided Cloth by Appropriate Design Incorporation in Braiding Machines” under Jute Technology Mission (Mini Mission IV, DDS 7.1/2). IJIRA wish to express sincere gratitude to The Agri-Horticultural Society of India, Kolkata and Sahayog Hortica (P) Ltd., 24-Parganas (S) for providing their infrastructural facilities and valuable suggestion during carrying out the field trials at their esteemed horticultural nurseries. -
Development and Testing of a Diamond Braided Eye Splice
ASME Early Career Technical Journal 2011 ASME Early Career Technical Conference, ASME ECTC November 4 – 5, Atlanta, Georgia USA DEVELOPMENT AND TESTING OF A DIAMOND BRAIDED EYE SPLICE Caitlin Plunket, Austin Yuill, and David Branscomb, M.S. Auburn University Auburn, Alabama, USA Chad Rodekohr, PhD Presbyterian College Clinton, South Carolina, USA ABSTRACT To make ropes more useable, many people add knots. A rope with a conventional eye splice termination is said to lose However, knots cause the rope to lose much of its strength. ten percent of its original strength [1]. The purpose of this This loss of strength is due to a more concentrated area of strain research was to determine if an eye splice produced on a [3]. A special kind of knot that allows the rope to retain more of braiding machine would be subject to the same loss in strength its strength is the splice. Splices make a more permanent encountered in conventional splices. Braided rope made at the fastening than knots and spread the stress through a larger area same speed and braid angle is compared to a braided eye splice. than a knot [3]. Yet, commonly used splices do not allow the The spliced ropes were made with sixteen Vectran® yarns rope to retain all of its original strength. around a cotton core. The splices were tested on a mechanical For example, a commonly used splice known as a testing machine and each splice compared to a rope made with buried eye splice is made by threading the free end of a rope the same specifications.