Mse 257: Indigenous Methods of Materials Processing
Total Page:16
File Type:pdf, Size:1020Kb
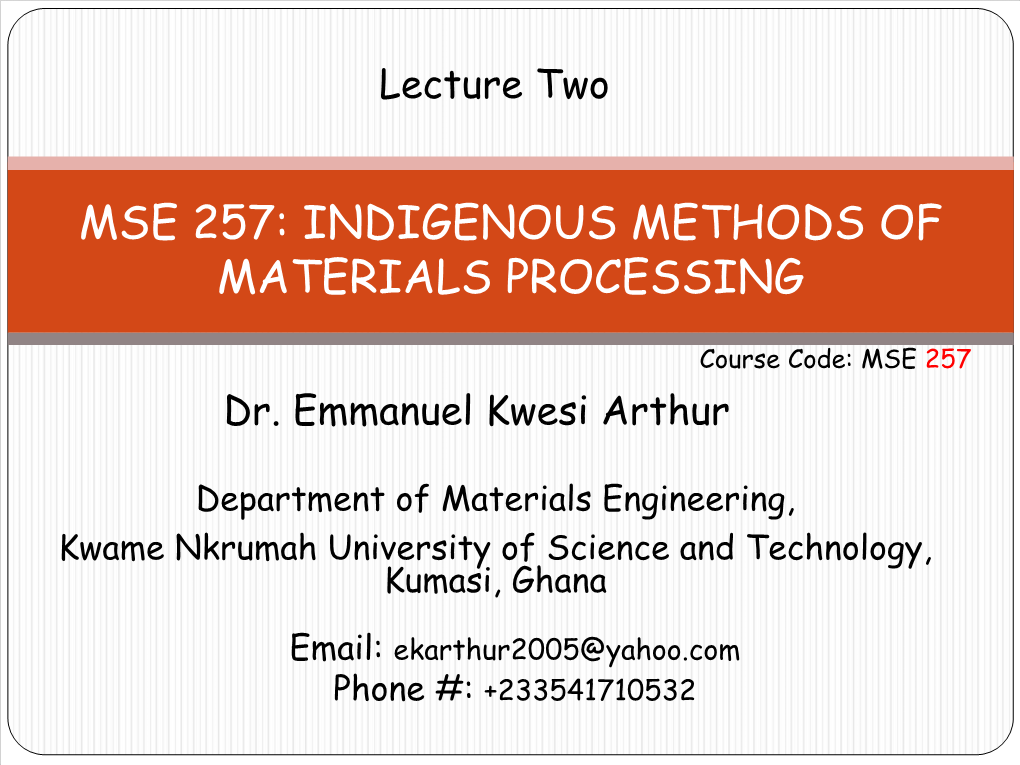
Load more
Recommended publications
-
UAW Ford Agreements Cvr 1Up.Indd 2 11/15/16 7:07 AM SKILLED TRADES AGREEMENTS and LETTERS of UNDERSTANDING
SKILLED TRADES AGREEMENTS AND LETTERS OF UNDERSTANDING between UAW® and the FORD MOTOR COMPANY Agreements Dated November 5, 2015 133 MICHIGAN (Effective November 23, 2015) ♲ printed on recycled paper PRINTED IN U.S.A. 64353-UAW Ford Skilled Trades Cvr 1up.indd 1 10/26/16 8:24 AM National Ford Department Staff 2015 Negotiations Jimmy Settles Vice President and Director UAW Ford, Aerospace, Chaplaincy and Insurance Greg Drudi Roy Escandon Angelique Peterson- Don Godfrey Jeffrey Faber Mayberry Brett Fox Ford Motor Company and the UAW recognize Darryl Nolen Gregory Poet Kenneth Gafa their respective responsibilities under federal Bob Tiseo Reggie Ransom and state laws relating to fair employment Phil Argento Michael Gammella Lorenzo Robinson practices. Tracy Ausen Raenell Glenn Michael Robison Carol Bagdady R. Brian Goff Nick Rutovic The Company and the Union recognize the Matthew Barnett Ruth Golden Angelo Sacino Monica Bass moral principles involved in the area of civil Jane Granger Les Shaw David Berry rights and have reaffirmed in their Collective Andre Green Michael Shoemaker Carlo Bishop Bargaining Agreement their commitment not Joe Gucciardo Casandra Shortridge Shawn Campbell to discriminate because of race, religion, color, Dan Huddleston Larry Shrader Jerry Carson age, sex, sexual orientation, union activity, Michael Joseph Garry Sommerville Alfonzo Cash Thomas Kanitz national origin, or against any employee with Jeffrey Terry Tiffany Coger Brandon Keatts disabilities. Kevin Tolbert Gerard Coiffard Michael Kerr Vaughan Tolliver Sean -
17403 Model Answer Page No: 1/34 Impor
MAHARASHTRA STATE BOARD OF TECHNICAL EDUCATION (Autonomous) (ISO/IEC - 27001 - 2005 Certified) SUMMER 2016 EXAMINATION Subject Code: 17403 Model Answer Page No: 1/34 Important Instructions to examiners: 1) The answers should be examined by key words and not as word-to-word as given in the model answer scheme. 2) The model answer and the answer written by candidate may vary but the examiner may try to assess the understanding level of the candidate. 3) The language errors such as grammatical, spelling errors should not be given more importance. (Not applicable for subject English and Communication Skills). 4) While assessing figures, examiner may give credit for principal components indicated in the figure. The figures drawn by candidate and model answer may vary. The examiner may give credit for any equivalent figure drawn. 5) Credits may be given step wise for numerical problems. In some cases, the assumed constant values may vary and there may be some difference in the candidate’s answers and model answer. 6) In case of some questions credit may be given by judgment on part of examiner of relevant answer based on candidate’s understanding. 7) For programming language papers, credit may be given to any other program based on equivalent concept. ………………………………………………………………………………………………………………… Marks 1. a) Attempt any SIX of the following : 12 i) Name the common materials used for forging. 02 Answer: (Note: Any four - 1/2 mark each) Common materials used for forging: 1. Aluminum alloys 5. Low-alloy steels 9. Titanium alloys 02 2. Magnesium alloys 6. Martensitic stainless steels 10. Tantalum alloys 3. -
Journal of Milk Technology
'-/· .> Ί ' JOURNAL OF MILK TECHNOLOGY Volu 14 Number 2 MARCH-APRIL, 1941 Official Publication of International Association of Milk Sanitarians (Association Organized 1911) Alto designated publication of California Association of Dairy and Milk Inspectors Central States Milk Sanitarians Chicago Dairy Technology Society Connecticut Association of Dairy and Milk Inspectors Indianapolis Dairy Technology Club Massachusetts Milk Inspectors’ Association Metropolitan Dairy Technology Society Michigan Association of Dairy and Milk Inspectors Missouri Association of Milk Sanitarians New York State Association of Dairy and Milk Inspectors Pacific Northwest Association of Dairy and Milk Inspectors Pennsylvania Association of Dairy Sanitarians Philadelphia Dairy Technology Society Texas Association of Milk Sanitarians West Virginia Association of Milk Sanitarians II A dvertisements PERHAPS as a boy you took many a drink from it without a thought about how insanitary it might be. N ot so today. The patient work of sanitation and pub YOUR DAIRY CUSTOMERS can actually lic health officers has taught you to say see the safe protection of the Welded “nix” to the public drinking cup. And Wire Hood —and seeing is believing. their science, too, has solved many They recognize that you are safeguard problems of dairy sanitation—including ing their health when they see how you how to protect the pouring lip of your protect that pouring lip from contami sterilized milk and cream bottles. nation. Vet, even though the Hood is locked on with welded wire, it comes off HEALTH OFFICERS themselves say that quickly, without effort. they prefer the complete protection of the Welded Wire Hood Seal. It covers FREE INFORMATION-W rite for details the entire pouring lip and top against on Hood Capping and our interesting insanitary dust and filth. -
Abana Controlled Hand Forging Study Guide As Paginated by the Guild of Metalsmiths - Abana Chapter - Jan 2020 Index
ABANA CONTROLLED HAND FORGING STUDY GUIDE AS PAGINATED BY THE GUILD OF METALSMITHS - ABANA CHAPTER - JAN 2020 INDEX Lesson Number Number Description of Pages Credits (click on box) L 1.01 Drawing Out: Draw a sharp point on a 1/2" square bar 3 Peter Ross and Doug Wilson L 2.01 Hot Punching: Create holes or recesses in bars or plate by driving 2 By Doug Wilson Illustrations by Tom Latané punches into or through hot material. L 3.01 Drawing Out a Round Taper 3 By Jay Close Illustrations by Tom Latané L 4.01 Bending Bar Stock 5 By Jay Close Illustrations by Tom Latané L 5.01 Twisting a Square Bar 4 By Bob Fredell Illustrations by Tom Latané L 6.01 Drawing , Punching, and Bending 4 By Peter Ross Illustrations by Tom Latané L 7.01 Upsetting a Square Bar 3 By Peter Ross Illustrations by Tom Latané L 8.01 Slitting and Drifting Two Mortises or Slots in a Square Sectioned Bar 5 By Jay Close llustrations by Doug Wilson, photos by Jay Close L 9.01 Mortise and Tenon Joinery 3 Text and Illustrations by Doug Wilson L 10.01 Forge Welding 6 By Dan Nauman Illustrations by Tom Latané Photos by Dan Nauman L 11.01 Drawing Down - Part One 6 by Jay Close Illustrations by Tom Latané, photos by Jay Close and Jane Gulden L 11.07 Drawing Down - Part Two 6 by Jay Close Illustrations by Tom Latané, photos by Jay Close and Jane Gulden L 12.01 Forging a Shoulder 4 by Bob Fredell Illustrations by Tom Latané L 13.01 Cutting a Bar 2 by Dan Nauman Illustrations by Doug Wilson L 14.01 Forging a 90-degree Corner 3 Text and Photos by Dan Nauman L 15.01 Forge an Eye on the -
Blacksmith and Essential Skills
Literacy and Essential Skills in Industrial Arts BLACKSMITH COURSE Student Notes A project of Literacy Ontario Central South This project is funded by the Government of Canada’s Office of Literacy and Essential Skills ACKNOWLEDGEMENTS LOCS would like to gratefully acknowledge the Office of Literacy and Essential Skills, Human Resources Development Canada for funding this project. The Literacy and Essential Skills Project Team Lesley Hamilton – Project Manager David Haw – Project Coordinator Shelley McCarrell – Project Assistant Elise Noriega – Project Assistant Carrie Wakeford – Project Writer Brigid Hayes – Project Evaluator Advisory Committee Andrew Rothfischer – Ministry of Natural Resources Doug Noyes – Literacy Link Eastern Ontario Kathy Neill – John Howard Society of Peterborough Sheila Cowan – LOCS Board of Directors Walter Johnstone – Youth Emergency Shelter LOCS would like to extend a heartfelt thanks to David Haw, the Project Coordinator without whom this project would not have been successful. The vision that David brought to this project was the driver that made everything happen. LOCS would like to thank the blacksmith artists Tracy Greene and Daryl Sanders who worked with us to create course material. Not only did they work with the writer but they delivered a pilot course of the material created. © 2010 Literacy Ontario Central South Literacy and Essential Skills in Industrial Arts – Blacksmith The following participants took part in the piloting of the material: Ruby Albert Tyerne Clark Jamie Sanderson Melanie Stephen Steven Sykes This was extremely successful with these students and they deserve a big thank you for the time and effort for assisting us with this. LOCS would like to acknowledge Carrie Wakeford for the tremendous job of writing this material. -
Commodity Master List
Commodity Master List 005 ABRASIVES 010 ACOUSTICAL TILE, INSULATING MATERIALS, AND SUPPLIES 015 ADDRESSING, COPYING, MIMEOGRAPH, AND SPIRIT DUPLICATING MACHINE SUPPLIES: CHEMICALS, INKS, PAPER, ETC. 019 AGRICULTURAL CROPS AND GRAINS INCLUDING FRUITS, MELONS, NUTS, AND VEGETABLES 020 AGRICULTURAL EQUIPMENT, IMPLEMENTS, AND ACCESSORIES (SEE CLASS 022 FOR PARTS) 022 AGRICULTURAL IMPLEMENT AND ACCESSORY PARTS 025 AIR COMPRESSORS AND ACCESSORIES 031 AIR CONDITIONING, HEATING, AND VENTILATING: EQUIPMENT, PARTS AND ACCESSORIES (SEE RELATED ITEMS IN CLASS 740) 035 AIRCRAFT AND AIRPORT, EQUIPMENT, PARTS, AND SUPPLIES 037 AMUSEMENT, DECORATIONS, ENTERTAINMENT, TOYS, ETC. 040 ANIMALS, BIRDS, MARINE LIFE, AND POULTRY, INCLUDING ACCESSORY ITEMS (LIVE) 045 APPLIANCES AND EQUIPMENT, HOUSEHOLD TYPE 050 ART EQUIPMENT AND SUPPLIES 052 ART OBJECTS 055 AUTOMOTIVE ACCESSORIES FOR AUTOMOBILES, BUSES, TRUCKS, ETC. 060 AUTOMOTIVE MAINTENANCE ITEMS AND REPAIR/REPLACEMENT PARTS 065 AUTOMOTIVE BODIES, ACCESSORIES, AND PARTS 070 AUTOMOTIVE VEHICLES AND RELATED TRANSPORTATION EQUIPMENT 075 AUTOMOTIVE SHOP EQUIPMENT AND SUPPLIES 080 BADGES, EMBLEMS, NAME TAGS AND PLATES, JEWELRY, ETC. 085 BAGS, BAGGING, TIES, AND EROSION CONTROL EQUIPMENT 090 BAKERY EQUIPMENT, COMMERCIAL 095 BARBER AND BEAUTY SHOP EQUIPMENT AND SUPPLIES 100 BARRELS, DRUMS, KEGS, AND CONTAINERS 105 BEARINGS (EXCEPT WHEEL BEARINGS AND SEALS -SEE CLASS 060) 110 BELTS AND BELTING: AUTOMOTIVE AND INDUSTRIAL 115 BIOCHEMICALS, RESEARCH 120 BOATS, MOTORS, AND MARINE AND WILDLIFE SUPPLIES 125 BOOKBINDING SUPPLIES -
Blacksmith Metalsmith Knifemaker Farrier •
Pieh Tool Company Pieh Tool Product Catalog Blacksmith Metalsmith Knifemaker Farrier • www.piehtoolco.com www.piehtoolco.com 888.743.4866 928.554.0700 $7 Pieh Tool Company is located in Arizona’s pristine Yavapai County, just minutes from captivating Sedona. We are in a country that is rich with metalsmiths, sculptors, artists and horse enthusiasts! We stock a variety of machinery, vises, power tools, saws, anvils, forges, fluxes, finishes, hammers, tongs, horseshoes, feed, nails, rivets, lag bolts, videos & hundreds of book titles. We serve blacksmiths, fabricators, knifemakers, jewelers, farriers, horseowners and hobbyists. The Pieh Legacy Collection™ demonstrates our commitment to quality blacksmith tools. Be sure to check out the Billy™ tongs, our new Ergonomic Hammer line, and other Pieh Tool products. We’re sure you will be Pieh Tool Company Distribution Center in Camp Verde, Arizona extremely satisfied! EDUCATION The "Bill Pieh Resource for Metalwork" offers educational opportunities to the metal working trades in the United States. Classes are held monthly. Reservations are required. SEMINARS Semi-annual demonstrations offer you an opportunity to learn from the masters in your craft. Be sure to visit the Calendar on our website for our schedule of events. CONVENIENCE Secure online shopping is available to you at www.piehtoolco.com. We ship worldwide. The following trademarks are owned by their respective companies; Pieh Tool Company: Pieh Legacy Collection, the Billy, the Bonnie; Radians: Radians AV; Rad Band, Thoro’Bred: Thoro’Bred, Queens Plate, Easy Care: Easy Boot Glove, Hoof Suspension; Equine Innovations: Hoofjack; Gene Ovnicek: Natural Balance; JET, WILTON, Powermatic: Milwaukee, Sawzall, Hackzall, Thunderbolt, M12, M18, Shockwave. -
Manufacturing Processes by H.N. Gupta.Pdf
This page intentionally left blank MANUFACTURING PROCESSES (SECOND EDITION) H.N. Gupta B.Sc., G.I. Mech.E (London), FIE Visiting Professor Department of Mechanical Engineering I.E.T., Lucknow, U.P. Technical University R.C. Gupta B.Sc., B.E., M.Tech., Ph.D. Professor and Head Department of Mechanical Engineering I.E.T., Lucknow, U.P. Technical University Arun Mittal Senior Faculty Department of Mechanical Engineering I.E.T., Lucknow, U.P. Technical University Copyright © 2009, New Age International (P) Ltd., Publishers Published by New Age International (P) Ltd., Publishers All rights reserved. No part of this ebook may be reproduced in any form, by photostat, microfilm, xerography, or any other means, or incorporated into any information retrieval system, electronic or mechanical, without the written permission of the publisher. All inquiries should be emailed to [email protected] ISBN (13) : 978-81-224-2844-5 PUBLISHING FOR ONE WORLD NEW AGE INTERNATIONAL (P) LIMITED, PUBLISHERS 4835/24, Ansari Road, Daryaganj, New Delhi - 110002 Visit us at www.newagepublishers.com Preface to the Second Edition The authors of the book ‘‘Manufacturing Processes’’ are thrilled at the speed with which the first edition of the book has been snapped up and exhausted within four months of its publication necessitating a reprint. This proves that the book has been found useful both by teachers and the students. This is extremely gratifying. It has been felt that to make the text of the book even more useful, certain changes have been made. Therefore the text of the Unit I and Unit IV has been completely rewritten in the second edition of the book. -
Haywood's Historic Farmers Market 2016 Heritage Craft
HAYWOOD’S HISTORIC FARMERS MARKET 2016 HERITAGE CRAFT GUIDELINES Haywood’s Historic Farmers Market is dedicated to assisting local artisans in advancing their craft endeavors. One facet of this obligation is through the Jury process that provides critique and distinction for artisan work judged to be of the highest level of quality indicative of the Western North Carolina region and Appalachia’s fine heritage of creativity and workmanship. HERITAGE CRAFTS DEFINED: (as to inclusion in Haywood’s Historic Farmers Market) Crafts representative of the Appalachian heritage handmade and created within our local communities in a traditional manner, made predominately from materials that originate in the Western North Carolina region. PURPOSE: The purpose of Haywood’s Historic Farmers Market crafts initiative is to preserve and promote the history of Appalachian crafts, emphasizing the techniques and tools that mountain people used in everyday life. The market provides a venue where rural artists can sell culturally significant and quality heritage crafts that define the artistry and heritage of the region. CATEGORIES: BASKETRY: basket weaving, chair caning, brooms FIBER / TEXTILES: quilting, weaving, rug making (rag rugs), wall hangings (all from natural fibers), wearable fiber; dyes, spinning & looms GLASS: hand blown glassware and bowls LEATHER: cobblers, saddlers, and harness makers METALWORKING: blacksmith, bladesmith, tinsmith (copper), silversmith, goldsmith, rifle making MUSICAL INSTRUMENTS: dulcimers, drums, flutes, banjoes, fiddles ORGANIC MEDIA: gourds, dried floral, herbal wreaths, cornhusk crafts (toys, hats, purses, baskets, wreaths) POTTERY, CERAMICS and STONE: plates, containers, sculptural objects, sharpening stones WOOD and BAMBOO: turning, whittling, bending, carving, constructed wood, cabinetry, walking sticks ELIGIBILITY: In keeping with the above Purpose, all jury submissions must be produced by artisans residing in Haywood County, or counties contiguous to Haywood County within the State of North Carolina. -
Basic Blacksmithing
BASIC BLACKSMITHING An introduction to toolmaking with locally available materials DAVID HARRIES and BERNHARD HEER INTERMEDIATE TECHNOLOGY PUBLICATIONS 1993 Intermediate Technology Publications Ltd, 103-105 Southampton Row, London WClB 4HH, UK © Intermediate Technology Publications 1993 A CIP record for this book is available from the British Library ISBN 1 85339 195 6 Typeset by J&L Composition Ltd, Filey, North Yorkshire Printed in Great Britain by SRP Exeter CONTENTS GLOSSARY VI INTRODUCTION VII 1. Tools and equipment 1 A range of blacksmithing tools and equipment and their uses 2. Raw materials 5 The uses of a range of raw materials commonly used by blacksmiths in rural areas 3. Blacksmithing techniques 7 The basic techniques used by the blacksmith and information about forging temperatures and heat treatment 4. Making your own tools 23 Step-by-step instructions on how to make the following tools: o Round punch 23 o Hot chisel 25 0 Cold chisel 27 o Hot and cold sets 31 c Tongs 41 o Fullers 47 o Hammers 48 5. Products 75 Step-by-step instructions on the following: o Axe-making 75 o Hoe-making 82 o Knife-making 91 o The sickle 95 6. Setting up a workshop 101 Hints for those who wish to set up their own workshop, including how to make bellows, hearths and anvils APPENDIX: Forged tools for the carpenter 111 Step-by-step instructions for making chisels, plane irons and a carpenter's brace and bit QUESTIONNAIRE 127 GLOSSARY Anti-roll bar Carbon steel bar linking together the left and right front suspension units on some cars and vans. -
Direct Match Title File, 2018
U.S. Bureau of Labor Statistics On behalf of the Office of Management and Budget (OMB) and the Standard Occupational Classification Policy Committee (SOCPC) November 2017 (Updated April 15, 2020) ***Questions should be emailed to soc@bls. -
Understanding Alloy Design Principles and Cast Metal Technology in Hot Molds for Medieval Bengal
Indian Journal of History of Science, 45.1 (2010) 101-140 UNDERSTANDING ALLOY DESIGN PRINCIPLES AND CAST METAL TECHNOLOGY IN HOT MOLDS FOR MEDIEVAL BENGAL BARNALI MANDAL*, PRANAB K. CHATTOPADHYAY**, DIPTEN MISRA+ AND PRASANTA K. DATTA++ (Received 9 September 2009; revised 17 November 2009) Two beautiful bronze images of medieval period unearthed in South Bengal have been investigated. After laser cleaning, material characterization was undertaken to reconstruct the technology as well as the knowledge base of metal workers. The bronze items were found to be cast product whose chemistry belongs to copper – zinc – lead system with small addition of tin. The use of copper-zinc alloy in place of copper-tin with addition of lead becomes quite significant in this respect and points towards developing a working knowledge for copper-alloy design. The analysis of microstructures signifies towards a casting technology, where, hot molds were used. For confirmation of the molds, some tribal metal casting operations were also investigated. The technology was then reconstructed in the laboratory and some casting as the facts were produced. Microstructures of all three types look almost similar leading to the conclusion that coppersmiths used hot clay molds for bronze production. Key words: Alloy-design, Bronze casting, Hot molds, Laser cleaning INTRODUCTION East Indian subcontinent has got a long history of using different metals from ancient time and a number of archaeological sites have been * Research Scholar: Department of Metallurgical & Material Engineering, Jadavpur University, Kolkata- 700 032. India, [email protected]. ** Centre for Archaeological Studies & Training, Eastern India, 4 Camac Street, Kolkata- 700 016.