Ludvika Mines Preliminary Economic Assessment
Total Page:16
File Type:pdf, Size:1020Kb
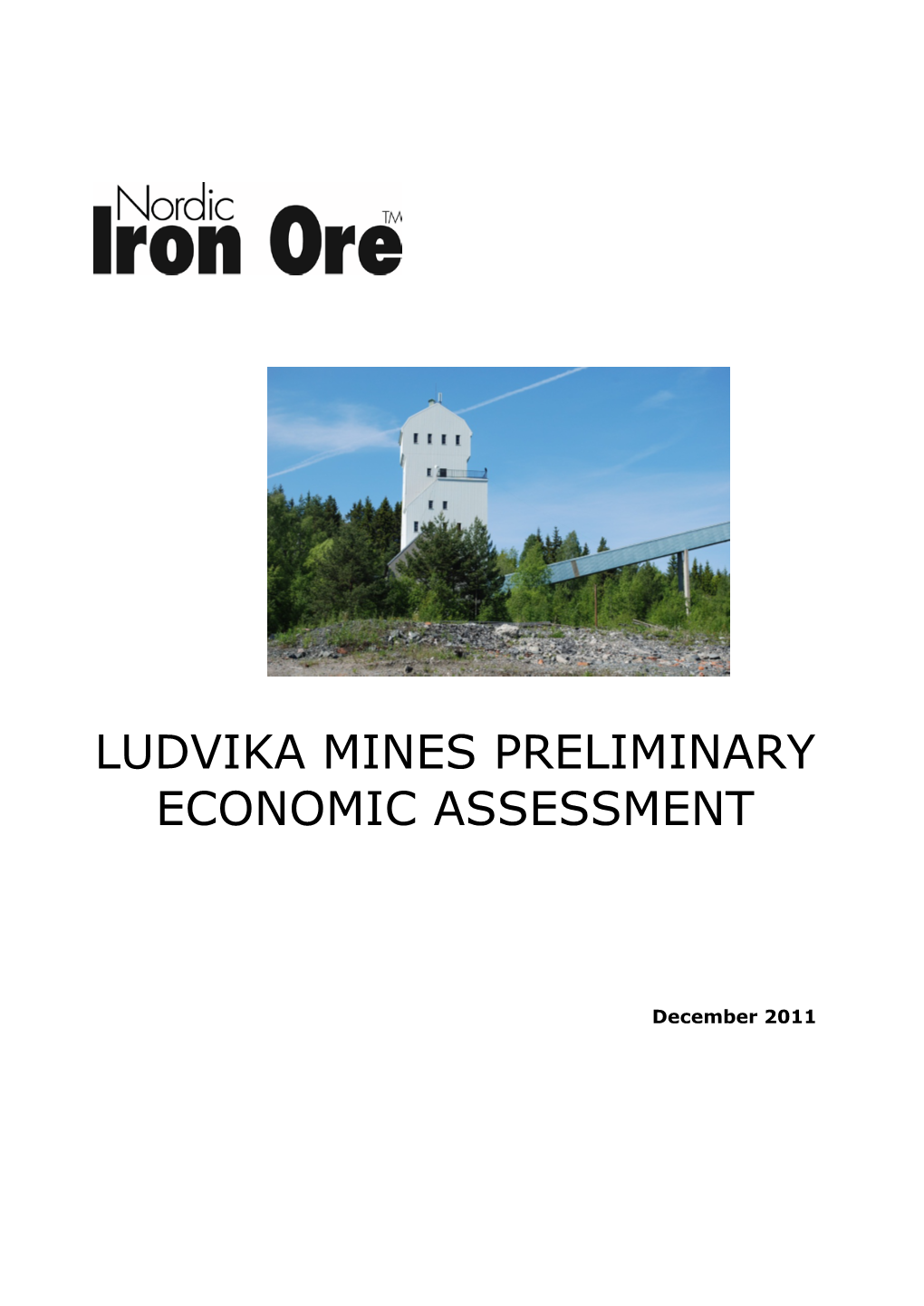
Load more
Recommended publications
-
Geographic Information Systems As a Tool to Support Monitoring and Assessment of Landscape and Regional Sustainability
Geographic Information Systems as a Tool to Support Monitoring and Assessment of Landscape and Regional Sustainability Kjell Andersson Faculty of Forest Sciences School for Forest Management Skinnskatteberg Doctoral Thesis Swedish University of Agricultural Sciences Skinnskatteberg 2011 Acta Universitatis Agriculturae Sueciae 2011:92 Cover: Fragmented ownership and forest landscape © Lantmäteriet Gävle 2011. Permission I 2011/0071-0100 ISSN 1652-6880 ISBN 978-91-576-7636-8 © 2011 Kjell Andersson, Skinnskatteberg Print: SLU Service/Repro, Uppsala 2011 Geographic Information Systems as a Tool to Support Monitoring and Assessment of Landscape and Regional Sustainability Abstract New policies in Sweden about intensive forestry and functional green infrastructure require involvement of different sectors for planning of landscapes and regions. However, Sweden has no territorial land-use planning at these spatial scales. Landowners, municipalities and regional governments work separately to implement policies about sustainability. There is thus a growing need for integrated spatial planning, and thus assessments of sustainability at local to regional levels by comparing monitoring results with norms expressed in policies. The aim of this thesis is to analyse and visualise such data using Geographic Information Systems (GIS) to enhance comprehensive spatial planning approaches for cooperation between different planning sectors. In paper I, habitat functionality was modelled for area-demanding focal species’ requirements in five coarse forest types. Also clear- felling rates within and outside functional habitats for each of four forest owner categories were measured. The differences among landowner categories concerning planning for ecological values were linked to how biodiversity-friendly their policies were. Papers II and III analyses how forest management affects two endangered species, and show that GIS-based proxy variables can be used to predict occurrence of both terrestrial and aquatic focal species. -
Nordic Iron Ore Annual Report 2017 Table of Contents
2OI6 Nordic Iron Ore NIOAnnual Report 2017 2OI7 NIO Nordic Iron Ore Annual Report 2017 Table of contents 1 Summary of 2017 2 Nordic Iron Ore in brief 3 Current permits and mineral resources 4 Statement from the Managing Director 5 Market and products 7 Strategic positioning 8 Where NIO concentrates can be used 9 Project development and planning EU-sponsored research projects 11 Ludvika Mines project Horizon 2020 and ERA-MIN are umbrella 12 Three sub-projects terms for a number of research and innovation 13 Sustainability projects sponsored by the EU. The projects cover many different industries, and Nordic Iron 14 Share Capital and Ownership Ore has been part of the applications for a num- 15 Board of Directors ber of projects oriented on mining exploration, three of which were approved by the EU. The 16 Management first of these approved research projects that 17 Directors’ Report Nordic Iron Ore was part of finished in 2017, and the other two began at year-end 2017. 20 Statement of comprehensive income The Smart Exploration project, led by Uppsa- la University, formally began on 1 December 21 Consolidated balance sheet 2017. Nordic Iron Ore is part of the project, in 22 Consolidated statement of changes in equity partnership with 27 other participants including Ludvika Municipality. In this project, Nordic Iron 23 Consolidated cash flow statement Ore is managing an activity in which advanced 24 Income statement – Parent Company exploration equipment and technology will be demonstrated for the purpose of enhancing the 25 Balance sheet – Parent Company efficiency of exploration. 26 Changes in equity – Parent Company The next project, AMSTEG, begins in May 2018 and is another exploration project in 27 Cash flow statement – Parent Company which alternative equipment will be used. -
Monitoring and Indicators of Forest Biodiversity in Europe – from Ideas to Operationality
Monitoring and Indicators of Forest Biodiversity in Europe – From Ideas to Operationality Marco Marchetti (ed.) EFI Proceedings No. 51, 2004 European Forest Institute IUFRO Unit 8.07.01 European Environment Agency IUFRO Unit 4.02.05 IUFRO Unit 4.02.06 Joint Research Centre Ministero della Politiche Accademia Italiana di University of Florence (JRC) Agricole e Forestali – Scienze Forestali Corpo Forestale dello Stato EFI Proceedings No. 51, 2004 Monitoring and Indicators of Forest Biodiversity in Europe – From Ideas to Operationality Marco Marchetti (ed.) Publisher: European Forest Institute Series Editors: Risto Päivinen, Editor-in-Chief Minna Korhonen, Technical Editor Brita Pajari, Conference Manager Editorial Office: European Forest Institute Phone: +358 13 252 020 Torikatu 34 Fax. +358 13 124 393 FIN-80100 Joensuu, Finland Email: [email protected] WWW: http://www.efi.fi/ Cover illustration: Vallombrosa, Augustus J C Hare, 1900 Layout: Kuvaste Oy Printing: Gummerus Printing Saarijärvi, Finland 2005 Disclaimer: The papers in this book comprise the proceedings of the event mentioned on the back cover. They reflect the authors' opinions and do not necessarily correspond to those of the European Forest Institute. © European Forest Institute 2005 ISSN 1237-8801 (printed) ISBN 952-5453-04-9 (printed) ISSN 14587-0610 (online) ISBN 952-5453-05-7 (online) Contents Pinborg, U. Preface – Ideas on Emerging User Needs to Assess Forest Biodiversity ......... 7 Marchetti, M. Introduction ...................................................................................................... 9 Session 1: Emerging User Needs and Pressures on Forest Biodiversity De Heer et al. Biodiversity Trends and Threats in Europe – Can We Apply a Generic Biodiversity Indicator to Forests? ................................................................... 15 Linser, S. The MCPFE’s Work on Biodiversity ............................................................. -
Caverion and Kalmar Municipality Aim for 21 Million in Savings by Improving the Energy Efficiency of Buildings
Caverion and Kalmar municipality aim for 21 million in savings by improving the energy efficiency of buildings Caverion Corporation Investor news 13 September 2013 at 10 a.m. Caverion and Kalmar municipality aim for 21 million in savings by improving the energy efficiency of buildings Kalmar municipality is now carrying out one of Sweden's largest projects to upgrade their properties together with Caverion. The cost of energy will be reduced by 21 million euros over the next 20 years.The project started in 2012 when Caverion analyzed the buildings regarding needs of upgrade, identified energy conservation measures and calculated the cost. Approximately 50-70 people will be employed and the project will be carried out during 2013-2016. The properties, which for the most part were built in the 1960’s and 70’s, will be upgraded in order to meet the energy needs of today. The energy use will be reduced by more than 20 % to meet the environmental requirement of the EU. – We are pleased that Kalmar municipality continues to reduce their energy use. This type of energy saving project enables Caverion to actively take responsibility for a sustainable environment and community, says Ulf Kareliusson, CEO, Caverion Sverige AB. Outdated systems and equipment will be upgraded in 175,000 square metres of schools, preschools and administration buildings with modern and energy efficient equipment. The upgrade will also reduce the cost of maintenance and improve the indoor climate for a better working environment for children and teachers. Future energy savings are going to fund the project. – This project is needed to keep our costs at a sustainable level. -
Promoting Social Trust and Sustainability - Preventing Social Risk and Extremism”
A bilateral Swedish/Dutch work-shop November 6-7, 2017 “Promoting Social Trust and Sustainability - Preventing Social Risk and Extremism” Monday November 6 Venue: The world heritage of Falun, Falun Mine conference, room Argentum/ Falu Gruva konferens, lokal Argentum Sessions open for all – in English 08.45 Register & coffee 09.15 Introductory welcome to the day Jonas Stier, Tomas Axelson 09.30 Dealing with social tensions, promoting cohesion in local Lars Walter, Veronika Wegsö, Borlänge community – search for a fruitful approach Municipality, Josefin Bergström/Marcus Hjelm, Knowledge House, Borlänge Municipality 10.10 Break & coffee 10.30 Dealing with social tensions, promoting cohesion in local Sandra van t’Hooge, Municipality of Groningen, community - search for a fruitful approach Netherlands, Anita Nijnuis Municipality of Groningen, Govert Buijs, University of Groningen 11.10 Break 11.20 Evaluating local strategies safeguarding democracy against Tomas Axelson, Dalarna university extremism 11.35 Perspective on strategies on social tensions, safeguarding Lars Korsell, The National Coordinator democracy and against extremism 11.50 Looking at the Future – cooperation partnership – a Jonas Stier, Dalarna University Govert Buijs, perspective University of Groningen. 12.15 Lunch break Hosts: Dalarna University, Falun, Sweden and County Administrative Board of Dalarna, Falun, Sweden 13.40- Free time/special program for our guests from the Netherlands in Falun World Heritage (see falun.se/varldsarvet). 16.00 Sessions for local authorities – in Swedish/ På svenska 13.30 Implementering av erfarenheter och förslag. Social risk – Camilla Sahlander och Ulrika Jutesund social oro. Hur arbeta demokratistärkande, förebyggande Länsstyrelsen Dalarnas län. och förhindrande? [Implementation of experience and approaches – social risk, social anxiety and longterm strengthening of democratic resilience] 13.50 Verktyg för kartläggning av risk för våldsbejakande Lars Korsell, Nationella samordnaren mot extremism på lokal nivå. -
Annual Report | 2018
1 ANNUAL REPORT | 2018 SBB Annual report 2018 2 CONTENTS VISION Samhällsbyggnadsbolaget aims to be the best THIS IS SAMHÄLLSBYGGNADSBOLAGET 3 Nordic property company for social BUSINESS MODEL 5 infrastructure properties and residentials. CEO ILIJA BATLJAN 7 LETTER FROM THE CHAIRMAN 11 OPERATIONS Economy and the property market 14 Earnings capacity 16 Tenants 20 MISSON Value creating property management 21 Samhällsbyggnadsbolaget shall benefit its Property development 23 shareholders and society in general: Regions 27 Transactions 46 • To be a natural and reliable partner to the SUSTAINABILITY public sector in the Nordic region, by long- Sustainability report 51 term ownership, management, renovation MANAGEMENT REPORT and building of social infrastructure The year in brief 59 properties. Properties 64 Financing 66 • To acquire, develop, build and manage The share 70 residentials throughout Sweden. Tax 74 Risk and sensitivity 76 • To work actively as a community builder and Corportate governance 80 long-term partner to municipalities, county Allocation of earnings 88 councils and government agencies in order to FINANCIAL STATEMENTS create building rights for housing. Consolidated Income Statement 90 Consolidated Balance Sheet 91 Cons. Statement of changes in equity 93 Consolidated Cash Flow Statement 94 Notes – Group 95 Income Statement of Parent Company 125 Balance Sheet of Parent Company 126 Statement of changes in Parent Company’s equity 127 Cash Flow Statement of Parent Company 128 Notes – Parent Company 129 Audit Report 142 OTHER Definitions 146 Investor relations 150 SBB Annual report 2018 3 INFORMATION ABOUT THE GROUP SAMHÄLLSBYGGNADSBOLAGET I NORDEN (SBB) Ilija Batljan founded SBB (abbreviated SBB or the Group or the company in the report) in March 2016 with a vision to create the best Nordic property company focused on residentials and social infrastructure properties. -
Kommun Invest Green Bonds Impact Report, December 2017
Kommun invest Green Bonds Impact Report, December 2017 Report on 146 Swedish local government investment projects financed by Kommun invest Green Bonds as of year-end 2017. CONTENTS About this report This report was written and compiled by: Foreword By the Kommun invest Green Bonds Environmenal Committee ....................4 • Björn Bergstrand, Head of Sustainability/ Senior Investor Relations Manager, Kommun invest i Sverige AB Executive Summary ...........................................................................................................................................................6 • Erik Törnblom, Analyst, Kommun invest i Sverige AB Introduction Any errors, omissions or otherwise are our Paris targets and the role of Swedish local governments ..........................................................9 responsibility. Project impact reporting is based on data col- Kommun invest – a provider of sustainable finance .......................................................................10 lected from financed projects during Q4-2017 Nordic position paper on Green Bonds impact reporting ....................................................... 13 and Q1-2018. The data has been reviewed by Kommun invest however their accuracy has not been verified by neither Kommun invest nor Kommun invest Green Bonds a third party. Climate impact calculations have been made by Kommun invest, and their accu- Green Bonds issuance �����������������������������������������������������������������������������������������������������������������������������������������������16 -
Environmental Compensation
TemaNord 2015:572 TemaNord TemaNord 2015:572 TemaNord Ved Stranden 18 DK-1061 Copenhagen K www.norden.org Environmental compensation Key conditions for increased and cost effective application Environmental compensation Environmental impacts are increasing due to human activities. The overuse of the benefits nature provides us is the direct result of our failure to put a price on these benefits. One way of addressing this is to require environmental compensation. The purpose of the study is to provide Nordic Council of Ministers and national decision-makers with an overview of key conditions for increased, flexible and cost-effective application of compensation. The study shows that for a relatively small cost society can make a significant investment in the provision of biodiversity and ecosystem services by requiring compensation. The study outlines three main recommendations on how to increase the use of environmental compensation: 1. Stimulate supply of, and demand for, compensation 2. Clarify and supplement guidelines and legal framework 3. Strengthen Nordic cooperation on compensation TemaNord 2015:572 ISBN 978-92-893-4335-0 (PRINT) ISBN 978-92-893-4337-4 (PDF) ISBN 978-92-893-4336-7 (EPUB) ISSN 0908-6692 TN2015572 omslag.indd 1 08-09-2015 13:59:16 Environmental compensation Key conditions for increased and cost effective application Anders Enetjärn, Scott Cole, Matleena Kniivilä, Svein Erik Hårklau, Linus Hasselström, Tryggve Sigurdson and Johan Lindberg TemaNord 2015:572 Environmental compensation Key conditions for increased -
For New Arrivals in Ludvika and Smedjebacken As a New Arrival in a Country and a Community, There Is Much That Is Different to What You Are Used To
For new arrivals in Ludvika and Smedjebacken As a new arrival in a country and a community, there is much that is different to what you are used to. We understand that you have many questions about how things work here. That is why we have tried to gather information which we believe can be of help when you are new in Sweden. In this folder there are short texts about different areas that are important to know about. If you want more detailed information about any of the subjects there are several websites that have information about Swedish society in different languages. You can start by visiting www.informationsverige.se List of fact sheets you will find in this welcome folder • to-do list • Migrationsverket (Swedish Migration Agency) • Skatteverket (Swedish Tax Agency) • Försäkringskassan (Social Insurance Agency) • work • housing • finance • health/medical care • learning Swedish/education • in emergency situations • public transport • social services (socialtjänsten) (the role of the social services, economic support, violence in close relationships) • school and child care • for parents (open pre-school, pre-school/school) (öppna förskolan, förskola/skola) • for young people (youth guidance centre, BRIS, youth recreation centres, Convention on the Rights of the Child, areas of concern) • municipal immigration service (invandrarservice) • library • culture and leisure. To-do list for your initial time in Sweden When you are new in Sweden and have got your residence permit, there are many practical things to consider. We have written a remember-to-do list to make it easier for you. What you need to do is: • notify Skatteverket to register yourself in the population register at your new address in the municipality and get the last 4 digits in your Swedish personal identity number • apply for an ID card • get a bank account • get home insurance with an insurance company. -
Bergslagen-Sweden) Summary Report Workshop/06 (Bergslagen-Sweden) Summary Report
ECOMUSEUMS: WHAT’S NEXT? WORKSHOP/06 (BERGSLAGEN-SWEDEN) SUMMARY REPORT WORKSHOP/06 (BERGSLAGEN-SWEDEN) SUMMARY REPORT Before the Swedish meeting: the Long network project. The general purpose of the Long network project was to create an effective environment for good practices exchange among European ecomuseums. The idea was that ecomuseums could play the role of a bridge, connecting the many sustainable development best practices experienced in Europe, support the growth of local districts based on a strong sense of place, and concur in local leadership building. Therefore, the trail we have followed is based on the networks, both locally and at a larger scale. Networks are not only mere organisational schemes. At a certain scale they produce new opportunities and ideas and make collective knowledge growth and evolve. To be observers in the processes and not merely of the processes is crucial in order to understand this kind of cultural phenomena. The steps: • 2004: harmonisation of our approaches and goals in the Sardagna- Trento workshop/04 • 2004/05: task-forces to try to make ideas circulate (fine tuning of ideas). Learning journeys set up at a national level (in Sweden, Italy, Poland) and internationally, between Italy and Sweden. • 2005: report on 2004/05 activities and making of new working groups in the Argenta workshop/05. Once agreed methods and goals, the new aim is to produce something together (main fields: training, travelling exhibition, communication, evaluation schemes, database). • 2005/06: good job for training and exhibition groups, less for communication and evaluation schemes. A scheme for a database is produced and is presently on a trial period. -
Företagsräkningen 1972. Del 2:3 = the 1972 Census Of
INLEDNING TILL Företagsräkningen 1972 / Statistiska centralbyrån. – Stockholm : Statistiska centralbyrån, 1975. – (Sveriges officiella statistik). Täckningsår: 1972. Engelsk parallelltitel: The 1972 census of enterprises. Företagsräkningen 1972 består av flera delar, delarnas undertitlar: Del 1. Basdata för företag och myndigheter fördelade efter näringsgren, storlek, samhälssektor, ägarkategori och juridisk form. Part 1. Basic data for enterprises and government departments distributed by major division, institutional sector, type of ownership and legal organization. Del 2 (tre band) Basdata för företag och myndigheters verksamhetsställen fördelade efter näringsgren, storlek, region och ägarkategori. 2:1 Verksamhetsställen totalt och fördelade på riksområden, län och A-regioner. 2:2 Verksamhetsställen fördelade på kommuner; A–M-län 2:3 Verksamhetsställen fördelade på kommuner; N–BD-län Part 2. Basic data for local units of enterprises and government agencises, disstributed by industry (SNI, 1, 2, 3-digit level), size, region and type of ownership. Del 3 Sysselsättnings-, resultat- och kapitaldata för företag inom den affärsdrivande sektorn fördelade efter näringsgren, storlek, ägarkategori och juridisk form. Part 3. Data on employees, profits and capital for enterprises in the business sector distribute by industri, size, type of ownership and legal organization. Del 4 Sysselsättnings- och omsättningsdata för verksamhetsställen inom den affärsdrivande sektorn fördelade eftter näringsgren, storlek och region. Part 4. Data of employees and turnover for local units of enterprises in the business sector distributed by industry, size and region. Appendix Lagstiftning, Klassificeringsstandard, Insamlade data, Blankettförteckning, Blankettexempel. Appendix Föregångare: 1951 års företagsräkning / Kommerskollegium. – Stockholm : Statistiska centralbyrån, 1955. – (Sveriges officiella statistik). Täckningsår: 1951. Engelsk parallelltitel: The 1951 census of production, distribution and services. 1931 års företagsräkning / verkställd av Kommerskollegium, Stockholm 1935. -
Guideline for Procurement of Solar Energy
Guideline for Procurement of solar energy EFFECT4buildings Toolbox: Prosumerism; Annex 3 1 The project “Effective Financing Tools for implementing Energy Efficiency in Buildings” (EFFECT4buildings) develops in collaboration with public building managers a comprehensive decision-making support toolbox with a set of financial instruments: Financial calculation tools; Bundling; Funding; Convincing decision makers; Energy Performance Contract; Multi Service Contract; Green Lease Contract; Prosumerism. The tools and instruments chosen by the project has the biggest potential to help building managers to overcome financial barriers, based on nearly 40 interviews with the target group. The project improves these tools through different real cases. To make sure building managers invest in the best available solutions, more knowledge on different possibil ities is needed as well as confirmation from colleagues that the solutions performs well. EFFECT4buildings mapped technological solutions for energy efficiency in buildings with the aim to share knowledge and experiences of energy efficiency solutions among building managers in the Baltic Sea Region. This document is made as manual for procurement of PV and it includes technical description guidelines. Partners EFFECT4buildings project is implemented with the support from the EU funding Programme Interreg Baltic Sea Region (European Regional Development Fund) and Norwegian national funding. The aim of the project is to improve the capacity of public building managers in the Baltic Sea Region by providing them a comprehensive 2 decision-making support toolbox with a set of financial instruments to unlock the investments and lower the risks of implementing energy efficiency measures in buildings owned by public stakeholders. More information: http://www.effect4buildings.se/ EFECT4building project develop a toolbox with a set of financial instruments for building managers to implement more energy efficiency measures.