Electric Motors
Total Page:16
File Type:pdf, Size:1020Kb
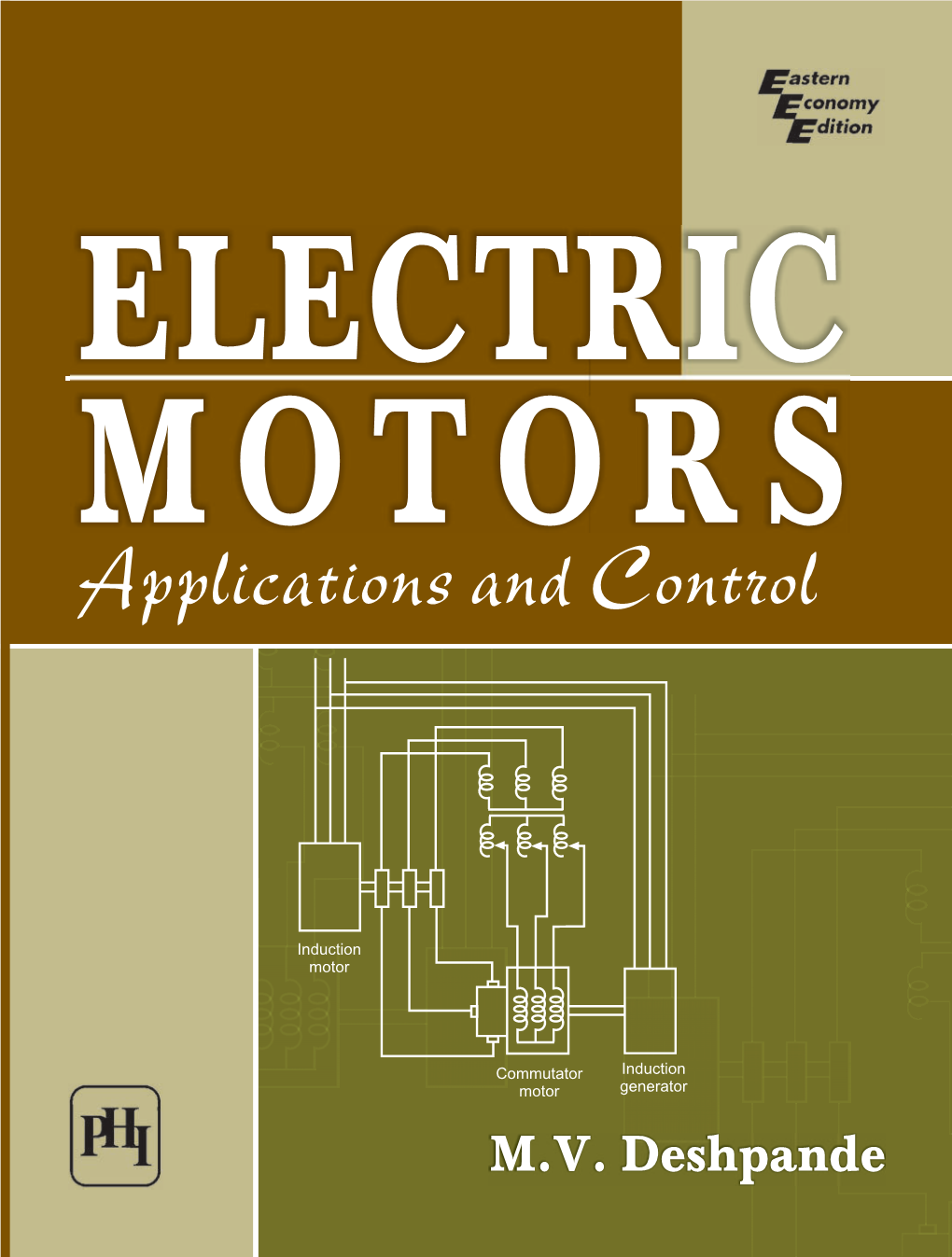
Load more
Recommended publications
-
Ee 6361- Electrical Drives & Control Ii/Iii Mechanical
EE 6361- ELECTRICAL DRIVES & CONTROL II/III MECHANICAL EE A Course Material on EE – 6361 ELECTRICAL DRIVES & CONTROL By Mr. S.SATHYAMOORTHI /R.RAJAGOPAL ASSISTANT PROFESSOR DEPARTMENT OF ELECTRICAL AND ELECTRONICS ENGINEERING SASURIE COLLEGE OF ENGINEERING VIJAYAMANGALAM – 638 056 1 R.RAJAGOPAL, S.SATHYAMOORTHI,AP/EEE 2015-16 EE 6361- ELECTRICAL DRIVES & CONTROL II/III MECHANICAL QUALITY CERTIFICATE This is to certify that the e-course material Subject Code : EE- 6361 Subject : Electrical Drives & Control Class : II Year MECH Being prepared by me and it meets the knowledge requirement of the university curriculum. Signature of the Author Name: R.RAJAGOPAL,S.SATHYAMOORTHI Designation: AP/EEE This is to certify that the course material being prepared by Mr.S.Sathyamoorthi / R.Rajagopal is of adequate quality. He has referred more than five books among them minimum one is from aboard author. Signature of HD Name: Mr. E.R.Sivakumar SEAL 2 R.RAJAGOPAL, S.SATHYAMOORTHI,AP/EEE 2015-16 EE 6361- ELECTRICAL DRIVES & CONTROL II/III MECHANICAL EE6361 ELECTRICAL DRIVES AND CONTROL Unit-I Introduction Basic elements-types of electric drives-factors influencing electric drives-heating and cooling curves- loading conditions and classes of duty-Selection of power rating for drive motors with regard to thermal overloading and load variation factors Unit-II Drive motor characteristics Mechanical characteristics- speed- torque characteristics of various types of load and drive motors - braking of electrical motors-dc motors: shunt, series, compound motors-single -
Reference List of Customers
Industrial Systems Group, Bangalore An ISO 90001 Unit Reference List of Customers 1 Rolling Mills...........................................................................................................2 2 Process Lines.........................................................................................................11 3 Steel Making.........................................................................................................13 4 Static Excitation Equipment..................................................................................17 5 Aluminium ............................................................................................................19 6 Cement ..................................................................................................................21 7 Paper......................................................................................................................23 8 Rubber ...................................................................................................................24 9 Mining & Material Handling.................................................................................25 10 Reactive Power Compensation..............................................................................28 11 Other Industries .....................................................................................................30 12 Other Industries – Sub_stations.............................................................................33 13 Pumping Station....................................................................................................34 -
Faculty of Degree Engineering - 083 Department of Electrical Engineering -09
Faculty of Degree Engineering - 083 Department of Electrical Engineering -09 Multiple Choice Questions Subject: Control of Electric Drives Branch: Electrical Engineering Subject code: 2160913 Semester: 6th 1. The selection of an electric motor for any application depends on which of the following factors ? (A) Electrical characteristics (B) Mechanical characteristics (C) Size and rating of motors (D) Cost (e) All of the above 2. For a particular application the type of electric-and control gear are determined by which of the following considerations ? (A) Starting torque (B) Conditions of environment (C) Limitation on starting current (D) Speed control range and its nature (e) All of the above 3. Which ofthefollowingmotors is preferred for traction work ? (A) Universal motor (B) D.C. series motor (C) Synchronous motor (D) Three-phase induction motor Dr. Subhash Technical Campus- The Jewel of Junagadh Faculty of Degree Engineering - 083 Department of Electrical Engineering -09 4 Which of the following motors always starts on load ? (A) Conveyor motor (B) Floor mill motor (C) Fan motor (D) All of the above 5 is preferred for automatic drives. (A) Squirrel cage induction motor (B) Synchronous motors (C) Ward-Leonard controlled D.C. motors (D) Any of the above 6. When the load is above a synchronous motor is found to be more economical. (A) 2 kW (B) 20 kW (C) 50 kW (D) 100 kW 7. The load cycle for a motor driving a power press will be (A) variable load (B) continuous (C) continuous but periodical (D) intermittent and variable load 8. Light duty cranes are used in which of the following ? (A) Power houses (B) Pumping stations (C) Automobile workshops (D) All of the above Dr. -
Semester Ii Electrical Drives and Controll 1 Printing Technology-Sde
SEMESTER II ELECTRICAL DRIVES AND CONTROLL EE A Course Material on ELECTRICAL DRIVES & CONTROL v 1 PRINTING TECHNOLOGY-SDE MODE SEMESTER II ELECTRICAL DRIVES AND CONTROLL 2 PRINTING TECHNOLOGY-SDE MODE SEMESTER II ELECTRICAL DRIVES AND CONTROLL EE6361 ELECTRICAL DRIVES AND CONTROL Unit-I Introduction Basic elements-types of electric drives-factors influencing electric drives-heating and cooling curves- loading conditions and classes of duty-Selection of power rating for drive motors with regard to thermal overloading and load variation factors Unit-II Drive motor characteristics Mechanical characteristics- speed- torque characteristics of various types of load and drive motors - braking of electrical motors-dc motors: shunt, series, compound motors-single phase and three phase induction motors Unit-III Starting methods Types of d.c motor starters-typical control circuits for shunt and series motors-three phase squirrel and slip ring induction motors Unit-IV Conventional and solid state speed control of D.C Drives Speed control of DC series and shunt motors-Armature and field control, ward-leonard control system- using controlled rectifiers and DC choppers –applications Unit-V Conventional and solid state speed control of AC drives Speed control of three phase induction motor-Voltage control, voltage/frequency control, slip power recovery scheme-using inverters and AC voltage regulators-applications TEXT BOOKS 1. VEDAM SUBRAMANIAM “Electric drives (concepts and applications)”, Tata McGraw-Hill.2001 2. NAGARATH.I.J & KOTHARI .D.P,”Electrical machines”, Tata McGraw-Hill.1998 REFERENCES 1. PILLAI.S.K “A first course on Electric drives”, Wiley Eastern Limited, 1998 2. M.D. SINGH, K.B.KHANCHANDANI,”Power electronics,” Tata McGraw-Hill.1998 3. -
Brushless DC Electric Motor
Please read: A personal appeal from Wikipedia author Dr. Sengai Podhuvan We now accept ₹ (INR) Brushless DC electric motor From Wikipedia, the free encyclopedia Jump to: navigation, search A microprocessor-controlled BLDC motor powering a micro remote-controlled airplane. This external rotor motor weighs 5 grams, consumes approximately 11 watts (15 millihorsepower) and produces thrust of more than twice the weight of the plane. Contents [hide] 1 Brushless versus Brushed motor 2 Controller implementations 3 Variations in construction 4 AC and DC power supplies 5 KM rating 6 Kv rating 7 Applications o 7.1 Transport o 7.2 Heating and ventilation o 7.3 Industrial Engineering . 7.3.1 Motion Control Systems . 7.3.2 Positioning and Actuation Systems o 7.4 Stepper motor o 7.5 Model engineering 8 See also 9 References 10 External links Brushless DC motors (BLDC motors, BL motors) also known as electronically commutated motors (ECMs, EC motors) are electric motors powered by direct-current (DC) electricity and having electronic commutation systems, rather than mechanical commutators and brushes. The current-to-torque and frequency-to-speed relationships of BLDC motors are linear. BLDC motors may be described as stepper motors, with fixed permanent magnets and possibly more poles on the rotor than the stator, or reluctance motors. The latter may be without permanent magnets, just poles that are induced on the rotor then pulled into alignment by timed stator windings. However, the term stepper motor tends to be used for motors that are designed specifically to be operated in a mode where they are frequently stopped with the rotor in a defined angular position; this page describes more general BLDC motor principles, though there is overlap. -
Electrical Engineering
DEPARTMENT OF ELECTRICAL ENGINEERING Syllabus for M. Tech. Power Electronics & Drives MEE-101 Advance Microprocessors and Applications Max. Marks: 100 (Credit=5) L T P 3 1 2 UNIT I (9 Lecture) Introduction to Microprocessors and Microcontrollers: Review of basics microprocessor,architecture and instruction set of a typical 8-bit microprocessor.Overview of 16 bit and 32 bit microprocessors, arithmetic and I/O coprocessors. Architecture, register details, operation, addressing modes and instruction set of 16 bit 8086 microprocessor, assembly language programming, introduction to multiprocessing, multi-user, multitasking operating system concepts, Pentium-1,2,3 and 4 processors, Motorola 68000 processor.Concepts of micro controller and microcomputer, microcontroller (8051/8751) based design, applications of microcomputer in on line real time control UNIT II (9 Lecture) Input/Output,Memory Interfacing: Parallel and series I/O, Interrupt driven I/O, single and multi-interrupt levels, use of software polling and interrupt controlling for multiplying interrupt levels, programmable interrupt controller, DMA controller, programmable timer/counter, programmable communication and peripheral interface, synchronous and asynchronous data transfer, standard serial interfaces like Rs.232. Types of Memory, RAM and ROM interfacing with timing considerations, DRAM interfacing UNIT III (9 Lecture) Programmable Support Chips: Functional schematic, operating modes, programming and interfacing of 8255, 8251, 8259 and 8253 with microprocessor UNIT IV (9 Lecture) Analog Input & Output: Microprocessor compatible ADC and DAC chips, interfacing of ADC and DAC with microprocessor, user of sample and hold circuit and multiplexer with ADC. Microprocessor Applications: Design methodology, examples of microprocessor applications. Lists of experiments 1. Simple arithmetic operations: Multi precision addition / subtraction / multiplication / division. -
Torque Characteristics of Various Types of Loads and Drives Motors: Classification of Load Torques: 1
UNIT – 1 CHARACTERISTICS OF ELECTRICAL DRIVES Speed – torque characteristics of various types of loads and drives motors: Classification of load torques: 1. Active Load torques 2. Passive Load torques Active Load Torques: Load torques which have the potential to drive the motor under equilibrium conditions are called active load torques. Load torques usually retain sign when the drive rotation is changed. Passive Torque: Load torques which always oppose the motion and change their sign on the reversal of motion are called passive load torques. Torque due to friction cutting – Passive torque. Components of load torques: 1. Friction Torque (TF) The friction torque (TF) is the equivalent value of various friction torques referred to the motor shaft. 2. Windage Torque (Tw) When a motor runs, the wind generates a torque opposing the motion. This is known as the winding torque. 3. Torque required to do useful mechanical work (Tm) Nature of the torque depends of type of load. It may be constant and independent of speed, some function of speed, may be time invariant or time variant. The nature of the torque may change with the change in the loads mode of operation. Characteristics of different types of load: In electric drives the driving equipment is an electric motor. Selection of particular type of motor driving an m/c is the matching of speed-torque characteristics of the driven unit and that of the motor. · Different types of loads exhibit different speed torque characteristics. · Most of the industrial loads can be classified into the following 4 general categories: 1. Constant torque type load. -
El/ 010 130 08 a CURRICULUM DEVELOPMENT STUDY of the EFFECTIVENESS of UPGRADING the TECHNICAL SKILLS of EDUCATIONALLY DISADVANTAGED UNION MEMBERS
R E P O R T R E S U M E S El/ 010 130 08 A CURRICULUM DEVELOPMENT STUDY OF THE EFFECTIVENESS OF UPGRADING THE TECHNICAL SKILLS OF EDUCATIONALLY DISADVANTAGED UNION MEMBERS. BY.. KOPAS, JOSEPH S. NEGRO AMERICAN LABOR COUNCIL REG. IV, CLEVELAND,OHIO REPORT NUMBER BR -6 -1484 PUB DATE 28 NOV 66 GRANT OEG3-0614840601 EDRS PRICE MF40.18 HC33.28 82P. DESCRIPTORS-.. *EDUCATIONALLY DISADVANTAGED, *UNION MEMBERS, *CURRICULUM DEVELOPMENT, *ELECTROMECHANICAL AIDS;TEACHING MACHINES, TEACHING TECHNIQUES, INDUSTRIALEDUCATION, *SKILL DEVELOPMENT: CLEVELAND, OHIO A SECTION OF A JOB TRAINING PROGRAM CONSISTING OFTHIRTY 10 k.HOUR JOB INSTRf.CTION CURRICULUM MODULESWAS DEVELOPED FOR UPDATING AND UPGRADING THE TECHNICAL SKILLS OFELECTRICAL MAINTENANCE EMPLOYEES. THIS JOB TRAINING PROGRAMWAS TRIED OUT IN C(.ASSES CONSISTING OF MAINTENANCEEMPLOYEES OF THE ELECTRICAL DEPARTMENTS IN A STEEL COMPANY.MEMBERS OF THE CLASSES WERE DIVIDED INTO 2 GROUPS OF 20EACH. HALF OF THE TRAINEES IN EACH GROUP WAS LOANED AN ELECTRONICTUTOR TO USE AT HOME. THE OTHER HALF STUDIED TEXTMATERIAL IN A NORMAL WAY WITHOUT ELECTRONIC TUTORS. A TEST WASPREPARED AND USED AS PRETEST AND POST -TEST TO MEASURETHE MASTERY OF THE SUBJECT MATTER COVERED IN THE 30 CURRICULUMUNITS. THE CONCLUSIONS INDICATED THAT TRAINEES WHO HAD ELECTRONICTUTORS ACHIEVED HIGHER ON ALL MEASURES. CRS) -lc/ U. S. DEPARTMENT OF HEALTH,EDUCATION AND Office of Education WELFAR' This documenthas been reproducen person or organa:glon exactly as receivedfrom originating it. Pointsof view Or stated do notnecessarily represent op nio position or policy. official Office ofEducatit.. A Curriculum DevelopmeeStudy of the Effectiveness of Upgrading the Technical Skills of Educationally Disadvantaged Union Members. -
Dc Motor Power Control.Pdf
Chapter 1 Introduction 1.1 Introduction Design and implementation of a motor speed controller is a necessary device in our daily life. From the very beginning and till now a lot of methods for motor speed control have been introduced. That is a basic fact that in today’s world costs of all forms of energy are increasing. Therefore in our project and thesis, we have tried to construct a system design to run a motor with economically, efficiently and also power saving. The device presented here makes the motor to control its speed smoothly. Moreover it will allow the motor to run in accordance to the necessary speed. That is let in the summer the temperature is high, then the motor will run with high speed and that will fall with falling in the temperature. Additionally we can also switch the motor ON and OFF from whatever the distance is. 1.2 Historical background The basic principles of electromagnetic induction were discovered in the early 1800's by Oersted, Gauss, and Faraday. In 1819, Hans Christian Oersted and Andie Marie Ampere discovered that an electric current produces a magnetic field. The next 15 years saw a flurry of cross-Atlantic experimentation and innovation. Finally using the principles developed by Michael Faraday and Joseph Henry, he built the first electric motor in 1834. However the first modern DC motor was invented in 1873. Five years later; these motors got microprocessor improvements that were mainly used in car dispatch and motor drive controllers. The induction motor was first realized by Galileo Ferraris in 1885 in Italy. -
Ahmedabad Center
Seat No.: ________ Enrolment No.___________ GUJARAT TECHNOLOGICAL UNIVERSITY BE - SEMESTER–VI (NEW) EXAMINATION – WINTER 2017 Subject Code: 2162404 Date: 03/11/2017 Subject Name:Industrial Drives & Control-I Time:02:30 PM TO 05:00PM Total Marks: 70 Instructions: 1. Attempt all questions. 2. Make suitable assumptions wherever necessary. 3. Figures to the right indicate full marks. Q.1 (a) Is Ward Leonard Control technic existing? Where? 03 (b) Discuss Ward Leonard Control technic. 04 (c) Discuss types of motor duty and selection of motor rating. 07 Q.2 (a) Draw and explain basic block diagram of DC Drive. 03 (b) Enumerate the benefits of Power Electronics Drive over old conventional DC Motor 04 control strategy. (c) Derive the formula of speed and torque for DC Series motor for single phase semi- 07 converter and full converter operation. Also draw the speed -torque characteristics. OR (c) Explain the operation of single phase semi-converter circuit for DC Series Motor 07 with discontinuous armature current condition at α = 30o. Draw various wave-forms. Q.3 (a) Explain steady state & transient stability of electric drive. 03 (b) Discuss transfer function of field controlled dc motor. 04 (c) Explain the operation of 1-phase full converter with conventional current condition 07 having high speed and high inductive load for separately excited DC motor at α = 45o. Also draw various wave-forms. OR Q.3 (a) Explain braking of separately excited dc Motor using chopper circuit. 03 (b) Draw various waveforms of separately excited dc Motor braking using chopper 04 circuit. (c) Derive the equation of speed and torque for single phase full converter separately 07 excited DC shunt motor. -
B.Tech Chemical Engineering
SRI VENKATESWARA COLLEGE OF ENGINEERING (An Autonomous Institution, Affiliated to Anna University, Chennai) SRIPERUMBUDUR TK.- 602 117 REGULATION – 2016 B.TECH. CHEMICAL ENGINEERING CURRICULUM AND SYLLABUS (I- VIII Semesters) SEMESTER I SL. COURSE COURSE TITLE L T P C No CODE 1 HS16151 Technical English – I 3 1 0 4 2 MA16151 Mathematics – I 3 1 0 4 3 PH16151 Engineering Physics – I 3 0 0 3 4 CY16151 Engineering Chemistry – I 3 0 0 3 5 GE16151 Computer Programming 3 0 0 3 6 GE16152 Engineering Graphics 2 0 3 4 PRACTICALS 7 GE16161 Computer Practices Laboratory 0 0 3 2 8 GE16162 Engineering Practices Laboratory 0 0 3 2 9 GE16163 Physics and Chemistry Laboratory - I 0 0 2 1 TOTAL 17 2 11 26 SEMESTER II SL. COURSE COURSE TITLE L T P C No CODE 1 HS16251 Technical English – II 3 1 0 4 2 MA16251 Mathematics – II 3 1 0 4 3 PH16251 Engineering Physics – II 3 0 0 3 4 CY16251 Engineering Chemistry – II 3 0 0 3 5. GE16251 Basic Electrical and Electronics Engineering 4 0 0 4 6. ME16251 Engineering Mechanics 3 1 0 4 PRACTICALS 7. GE16262 Physics and Chemistry Laboratory - II 0 0 2 1 8. GE16263 Computer Programming Laboratory 0 1 2 2 9. GE16264 Basic Electrical and Electronics Laboratory 0 0 3 2 TOTAL 19 4 7 27 SEMESTER III SL. COURSE COURSE TITLE L T P C No CODE 1 MA16351 Mathematics - III (Common to all branches) 3 1 0 4 2 EE16351 Electrical Drives and Controls (Common to ME and 3 0 0 3 3 CH16301 Organic Chemistry 3 0 0 3 4 CH16302 Mechanics of Solids for Chemical Engineering 3 0 0 3 5. -
Turning Gear Trainee Notes Circuit Diagrams
This document was generated by me, Colin Hinson, from a Crown copyright document held at R.A.F. Henlow Signals Museum. It is presented here (for free) under the Open Government Licence (O.G.L.) and this version of the document is my copyright (along with the Crown Copyright) in much the same way as a photograph would be. The document should have been downloaded from my website https://blunham.com/Radar, if you downloaded it from elsewhere, please let me know (particularly if you were charged for it). You can contact me via my Genuki email page: https://www.genuki.org.uk/big/eng/YKS/various?recipient=colin You may not copy the file for onward transmission of the data nor attempt to make monetary gain by the use of these files. If you want someone else to have a copy of the file, point them at the website. It should be noted that most of the pages are identifiable as having been processed my me. _______________________________________ I put a lot of time into producing these files which is why you are met with the above when you open the file. In order to generate this file, I need to: 1. Scan the pages (Epson 15000 A3 scanner) 2. Split the photographs out from the text only pages 3. Run my own software to split double pages and remove any edge marks such as punch holes 4. Run my own software to clean up the pages 5. Run my own software to set the pages to a given size and align the text correctly.