1. in an Open Loop Control System (A) Output Is Independent of Control Input
Total Page:16
File Type:pdf, Size:1020Kb
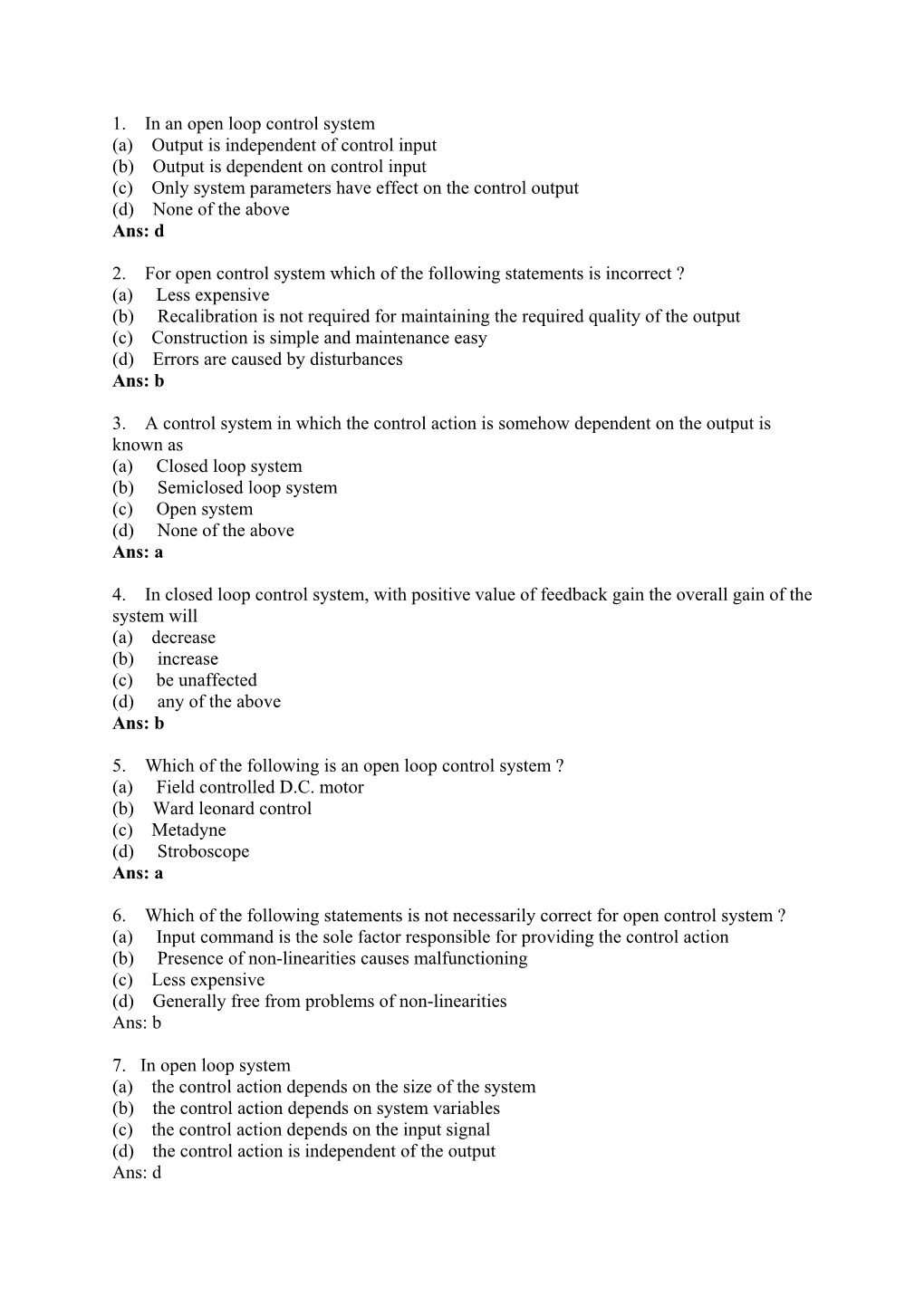
Load more
Recommended publications
-
Ee 6361- Electrical Drives & Control Ii/Iii Mechanical
EE 6361- ELECTRICAL DRIVES & CONTROL II/III MECHANICAL EE A Course Material on EE – 6361 ELECTRICAL DRIVES & CONTROL By Mr. S.SATHYAMOORTHI /R.RAJAGOPAL ASSISTANT PROFESSOR DEPARTMENT OF ELECTRICAL AND ELECTRONICS ENGINEERING SASURIE COLLEGE OF ENGINEERING VIJAYAMANGALAM – 638 056 1 R.RAJAGOPAL, S.SATHYAMOORTHI,AP/EEE 2015-16 EE 6361- ELECTRICAL DRIVES & CONTROL II/III MECHANICAL QUALITY CERTIFICATE This is to certify that the e-course material Subject Code : EE- 6361 Subject : Electrical Drives & Control Class : II Year MECH Being prepared by me and it meets the knowledge requirement of the university curriculum. Signature of the Author Name: R.RAJAGOPAL,S.SATHYAMOORTHI Designation: AP/EEE This is to certify that the course material being prepared by Mr.S.Sathyamoorthi / R.Rajagopal is of adequate quality. He has referred more than five books among them minimum one is from aboard author. Signature of HD Name: Mr. E.R.Sivakumar SEAL 2 R.RAJAGOPAL, S.SATHYAMOORTHI,AP/EEE 2015-16 EE 6361- ELECTRICAL DRIVES & CONTROL II/III MECHANICAL EE6361 ELECTRICAL DRIVES AND CONTROL Unit-I Introduction Basic elements-types of electric drives-factors influencing electric drives-heating and cooling curves- loading conditions and classes of duty-Selection of power rating for drive motors with regard to thermal overloading and load variation factors Unit-II Drive motor characteristics Mechanical characteristics- speed- torque characteristics of various types of load and drive motors - braking of electrical motors-dc motors: shunt, series, compound motors-single -
Control of DC Servomotor
Control of DC Servomotor Report submitted in partial fulfilment of the requirement to the degree of B.SC In Electrical and Electronic Engineering Under the supervision of Dr. Abdarahman Ali Karrar By Mohammed Sami Hassan Elhakim To Department of Electrical and Electronic Engineering University of Khartoum July 2008 Dedication I would like to take this opportunity to write these humble words that are unworthy of expressing my deepest gratitude for all those who made this possible. First of all I would like to thank god for my general existence and everything else around and within me. Second I would like to thank my beloved parents(Sami & Sawsan), my brothers (Tarig & Hassan), and my sister (Latifa), thank you so much for your support, guidance and care, you were always there to make me feel better and encourage me. I would like also to thanks all my friends inside and out Khartoum university, thank you for your patients tolerance and understanding, for your endless love that has stretched so far, for easing my pain and pulling me through. A special thanks to my partner Muzaab Hashiem without his help and advice i won’t be able to do what i did, thank you for being an ideal partner, friend and bother. Last but not the least i would like to thank my supervisor Dr. Karar and all those who helped me throughout this project, thank you for filling my mind with this rich knowledge. Mohammed Sami Hassan Elhakim. I Acknowledgement The first word goes to God the Almighty for bringing me to this world and guiding me as i reached this stage in my life and for making me live and see this work. -
Reference List of Customers
Industrial Systems Group, Bangalore An ISO 90001 Unit Reference List of Customers 1 Rolling Mills...........................................................................................................2 2 Process Lines.........................................................................................................11 3 Steel Making.........................................................................................................13 4 Static Excitation Equipment..................................................................................17 5 Aluminium ............................................................................................................19 6 Cement ..................................................................................................................21 7 Paper......................................................................................................................23 8 Rubber ...................................................................................................................24 9 Mining & Material Handling.................................................................................25 10 Reactive Power Compensation..............................................................................28 11 Other Industries .....................................................................................................30 12 Other Industries – Sub_stations.............................................................................33 13 Pumping Station....................................................................................................34 -
Faculty of Degree Engineering - 083 Department of Electrical Engineering -09
Faculty of Degree Engineering - 083 Department of Electrical Engineering -09 Multiple Choice Questions Subject: Control of Electric Drives Branch: Electrical Engineering Subject code: 2160913 Semester: 6th 1. The selection of an electric motor for any application depends on which of the following factors ? (A) Electrical characteristics (B) Mechanical characteristics (C) Size and rating of motors (D) Cost (e) All of the above 2. For a particular application the type of electric-and control gear are determined by which of the following considerations ? (A) Starting torque (B) Conditions of environment (C) Limitation on starting current (D) Speed control range and its nature (e) All of the above 3. Which ofthefollowingmotors is preferred for traction work ? (A) Universal motor (B) D.C. series motor (C) Synchronous motor (D) Three-phase induction motor Dr. Subhash Technical Campus- The Jewel of Junagadh Faculty of Degree Engineering - 083 Department of Electrical Engineering -09 4 Which of the following motors always starts on load ? (A) Conveyor motor (B) Floor mill motor (C) Fan motor (D) All of the above 5 is preferred for automatic drives. (A) Squirrel cage induction motor (B) Synchronous motors (C) Ward-Leonard controlled D.C. motors (D) Any of the above 6. When the load is above a synchronous motor is found to be more economical. (A) 2 kW (B) 20 kW (C) 50 kW (D) 100 kW 7. The load cycle for a motor driving a power press will be (A) variable load (B) continuous (C) continuous but periodical (D) intermittent and variable load 8. Light duty cranes are used in which of the following ? (A) Power houses (B) Pumping stations (C) Automobile workshops (D) All of the above Dr. -
DC Servo Motor Modeling
MODELING DC SERVOMOTORS CONTROL SYSTEMS TECH NOTE © Dr. Russ Meier, MSOE INTRODUCTION A DC motor is an actuator that converts electrical energy to mechanical rotation using the principles of electromagnetism. The circuit symbol for a DC motor is shown in Figure 1. + Va M - Figure 1: Circuit symbol for a DC servomotor The learning objectives of this technical note are: 1. Draw the equivalent DC servomotor circuit theory model. 2. State the equations of motion used to derive the electromechanical transfer function in the time domain and the s-domain. 3. Draw the DC servomotor signal block diagram. 4. Derive the DC servomotor electromechanical transfer function. CIRCUIT THEORY MODEL The circuit shown in Figure 2 models the DC servomotor. Note that an armature control current is created when the armature control voltage, Va, energizes the motor. The current flow through a series-connected Ra La + + Tm Va Vb R θ m - - Figure 2: DC servomotor circuit theory model armature resistance, an armature inductance, and the rotational component (the rotor) of the motor. The rotor shaft is typically drawn to the right with the torque (Tm) and angular displacement (θm) variables shown. The motor transfer function is the ratio of angular displacement to armature voltage. Figure 3: The DC servomotor transfer function EQUATIONS OF MOTION Three equations of motion are fundamental to the derivation of the transfer function. Relationships between torque and current, voltage and angular displacement, and torque and system inertias are used. Torque is proportional to the armature current. The constant of proportionality is called the torque constant and is given the symbol Kt. -
Direct Drive Dc Torque Servo Motors
DIRECT DRIVE DC TORQUE SERVO MOTORS QT- Series Rare Earth Magnet Motors DIRECT DRIVE DC SERVO MOTORS The Direct Drive DC Torque motor is a servo actuator which can be directly attached to the load it drives. It has a permanent magnet (PM) field and a wound armature which act together to convert electrical power to torque. This torque can then be utilized in positioning or speed control systems. In general, torque motors are deigned for three different types of operation: » High stall torque (“stand-still” operation) for positioning systems » High torque at low speeds for speed control systems » Optimum torque at high speed for positioning, rate, or tensioning systems SUPERIOR QUALITY With the widest range of standard and custom motion solutions, we collaborate with you to deploy rugged, battle-worthy systems engineered and built to meet your singular requirements. Kollmorgen provides direct drive servo motor solutions for the following applications: » Weapons stations and gun turrets » Missile guidance and precision-guided munitions » Radar pedestals and tracking stations » Unmanned ground, aerial and undersea vehicles » Ground vehicles and sea systems » Aircraft and spacecraft systems » Camera gimbals » IR countermeasure platforms » Laser weapon platforms QT- Series D irect Drive DC Servo Motors Advantages of Direct Drive DC Torque Motors Direct drive torque motors are particularly suited for servo system applications where it is desirable to minimize size, weight, power and response time, and to maximize rate and position accuracies. Frameless motors range from 28.7mm (1.13in) OD weighing 1.4 ounces (.0875 lbs) to a 4067 N-m (3000 lb-ft) unit with a 1067mm (42in) OD and a 660.4mm (26in) open bore ID. -
Course Description Bachelor of Technology (Electrical Engineering)
COURSE DESCRIPTION BACHELOR OF TECHNOLOGY (ELECTRICAL ENGINEERING) COLLEGE OF TECHNOLOGY AND ENGINEERING MAHARANA PRATAP UNIVERSITY OF AGRICULTURE AND TECHNOLOGY UDAIPUR (RAJASTHAN) SECOND YEAR (SEMESTER-I) BS 211 (All Branches) MATHEMATICS – III Cr. Hrs. 3 (3 + 0) L T P Credit 3 0 0 Hours 3 0 0 COURSE OUTCOME - CO1: Understand the need of numerical method for solving mathematical equations of various engineering problems., CO2: Provide interpolation techniques which are useful in analyzing the data that is in the form of unknown functionCO3: Discuss numerical integration and differentiation and solving problems which cannot be solved by conventional methods.CO4: Discuss the need of Laplace transform to convert systems from time to frequency domains and to understand application and working of Laplace transformations. UNIT-I Interpolation: Finite differences, various difference operators and theirrelationships, factorial notation. Interpolation with equal intervals;Newton’s forward and backward interpolation formulae, Lagrange’sinterpolation formula for unequal intervals. UNIT-II Gauss forward and backward interpolation formulae, Stirling’s andBessel’s central difference interpolation formulae. Numerical Differentiation: Numerical differentiation based on Newton’sforward and backward, Gauss forward and backward interpolation formulae. UNIT-III Numerical Integration: Numerical integration by Trapezoidal, Simpson’s rule. Numerical Solutions of Ordinary Differential Equations: Picard’s method,Taylor’s series method, Euler’s method, modified -
Semester Ii Electrical Drives and Controll 1 Printing Technology-Sde
SEMESTER II ELECTRICAL DRIVES AND CONTROLL EE A Course Material on ELECTRICAL DRIVES & CONTROL v 1 PRINTING TECHNOLOGY-SDE MODE SEMESTER II ELECTRICAL DRIVES AND CONTROLL 2 PRINTING TECHNOLOGY-SDE MODE SEMESTER II ELECTRICAL DRIVES AND CONTROLL EE6361 ELECTRICAL DRIVES AND CONTROL Unit-I Introduction Basic elements-types of electric drives-factors influencing electric drives-heating and cooling curves- loading conditions and classes of duty-Selection of power rating for drive motors with regard to thermal overloading and load variation factors Unit-II Drive motor characteristics Mechanical characteristics- speed- torque characteristics of various types of load and drive motors - braking of electrical motors-dc motors: shunt, series, compound motors-single phase and three phase induction motors Unit-III Starting methods Types of d.c motor starters-typical control circuits for shunt and series motors-three phase squirrel and slip ring induction motors Unit-IV Conventional and solid state speed control of D.C Drives Speed control of DC series and shunt motors-Armature and field control, ward-leonard control system- using controlled rectifiers and DC choppers –applications Unit-V Conventional and solid state speed control of AC drives Speed control of three phase induction motor-Voltage control, voltage/frequency control, slip power recovery scheme-using inverters and AC voltage regulators-applications TEXT BOOKS 1. VEDAM SUBRAMANIAM “Electric drives (concepts and applications)”, Tata McGraw-Hill.2001 2. NAGARATH.I.J & KOTHARI .D.P,”Electrical machines”, Tata McGraw-Hill.1998 REFERENCES 1. PILLAI.S.K “A first course on Electric drives”, Wiley Eastern Limited, 1998 2. M.D. SINGH, K.B.KHANCHANDANI,”Power electronics,” Tata McGraw-Hill.1998 3. -
Power Processing, Part 1. Electric Machinery Analysis
DOCONEIT MORE BD 179 391 SE 029 295,. a 'AUTHOR Hamilton, Howard B. :TITLE Power Processing, Part 1.Electic Machinery Analyiis. ) INSTITUTION Pittsburgh Onii., Pa. SPONS AGENCY National Science Foundation, Washingtcn, PUB DATE 70 GRANT NSF-GY-4138 NOTE 4913.; For related documents, see SE 029 296-298 n EDRS PRICE MF01/PC10 PusiPostage. DESCRIPTORS *College Science; Ciirriculum Develoiment; ElectricityrFlectrOmechanical lechnology: Electronics; *Fagineering.Education; Higher Education;,Instructional'Materials; *Science Courses; Science Curiiculum:.*Science Education; *Science Materials; SCientific Concepts ABSTRACT A This publication was developed as aportion of a two-semester sequence commeicing ateither the sixth cr'seventh term of,the undergraduate program inelectrical engineering at the University of Pittsburgh. The materials of thetwo courses, produced by a ional Science Foundation grant, are concernedwith power convrs systems comprising power electronicdevices, electrouthchanical energy converters, and associated,logic Configurations necessary to cause the system to behave in a prescribed fashion. The emphisis in this portionof the two course sequence (Part 1)is on electric machinery analysis. lechnigues app;icable'to electric machines under dynamicconditions are anallzed. This publication consists of sevenchapters which cW-al with: (1) basic principles: (2) elementary concept of torqueand geherated voltage; (3)tile generalized machine;(4i direct current (7) macrimes; (5) cross field machines;(6),synchronous machines; and polyphase -
Permanent Magnet Servomotor and Induction Motor Considerations
Permanent Magnet Servomotor and Induction Motor Considerations Kollmorgen B-104 PM Brushless Servomotor at 0.4 HP Kollmorgen M-828 PM Brushless Rotor Kollmorgen B-802 PM Brushless Servomotor at 15 HP Kollmorgen B-808 PM Brushless Rotor Permanent Magnet Servomotor and Induction Motor Considerations 1 Lee Stephens, Senior Motion Control Engineer Permanent Magnet Servomotor and Induction Motor Considerations Motion long considered a mainstay of induction motors, encroachment in the area of 50 HP and greater have been seen recently for some applications by permanent magnet (PM) servomotors. These applications usually have dynamic considerations that require position-time closed loop and high accelerations. When accelerating large loads, permanent magnet servomotors can work with very high load to inertia ratios and still maintain performance requirements. Having a lower inertia typically will allow for less permanent magnet motor can result in a greater torque energy wasted within the motor. Torque (τ), is the density than an equivalent induction system. If size product of inertia (j) and rotary acceleration (α). If you matters, then perhaps a system should use one require inertia matching, ½ of your energy is wasted technology over another. Speaking of size, the inertia accelerating the motor alone. If the inertia ratio from ratio can be an important figure of merit should motor to load is large, then control schemes must be dynamic needs arise. If you are going to have high dynamic enough to prevent the larger load from driving accelerations and decelerations, the size of the rotor the motor as opposed to the motor controlling the load. will significantly increase the inertia and decrease the Tradeoffs and knowing what can be negotiated. -
POWER ELECTRONICS TRAINER (Model : XPO-PE) / MICROCONTROLLER BASED PE (Model : XPO-Μc LSPT)
POWER ELECTRONICS TRAINER (Model : XPO-PE) / MICROCONTROLLER BASED PE (Model : XPO-µC LSPT) SALIENT FEATURES u Aesthetically designed injection molded electronic desk. u Master unit carrying useful experiment resources like line Synchronized firing circuits, Power supplies, lamp load, RLC loads, Battery charging supply etc. while the central slot will hold replaceable experiment panels. u Each multi experiment panel is secured in an ABS molded plastic sturdy enclosure, and has colorful screw less overlay showing circuit & Connection through Sturdy 4mm Banana Sockets & Patch Chords. u Set of User Guide provided with each unit. u Order 6 Master units and set of 6 panels (PE 1 x 2 , PE2, PE3, PE6X2nos)+ Power scope, buy more of PE1 and PE6 being major panels. Master Unit Accessories: Built in power supply l 15 pin D connector cable assembly, u DC supply : + 12V, 500mA, l 4mm patchcords : 100mm X 10 Nos & 500mm X 20 Nos. u Unregulated Power supply 17V / 750mA, Optional Power Scope u Regulated 7VDC to 14VDC/3A O/P is provided as 12V Battery charging supply. In absence of battery, same may be used as simulated battery source to run experiments on inverters etc. u Isolated DC supply +12V/ 300mA with isolated common. u On board Inverter transformer of Primary & Secondaries: 12-11-0- 11-12/3A. u On board o/p to Isolated Drive Circuit AC supply u 230V AC line voltage is made available on two banana 4mm Accessory for any Lab CRO for off ground differential measurements sockets as well as 1.5A fuse extender for variac if used. -
Brushless DC Electric Motor
Please read: A personal appeal from Wikipedia author Dr. Sengai Podhuvan We now accept ₹ (INR) Brushless DC electric motor From Wikipedia, the free encyclopedia Jump to: navigation, search A microprocessor-controlled BLDC motor powering a micro remote-controlled airplane. This external rotor motor weighs 5 grams, consumes approximately 11 watts (15 millihorsepower) and produces thrust of more than twice the weight of the plane. Contents [hide] 1 Brushless versus Brushed motor 2 Controller implementations 3 Variations in construction 4 AC and DC power supplies 5 KM rating 6 Kv rating 7 Applications o 7.1 Transport o 7.2 Heating and ventilation o 7.3 Industrial Engineering . 7.3.1 Motion Control Systems . 7.3.2 Positioning and Actuation Systems o 7.4 Stepper motor o 7.5 Model engineering 8 See also 9 References 10 External links Brushless DC motors (BLDC motors, BL motors) also known as electronically commutated motors (ECMs, EC motors) are electric motors powered by direct-current (DC) electricity and having electronic commutation systems, rather than mechanical commutators and brushes. The current-to-torque and frequency-to-speed relationships of BLDC motors are linear. BLDC motors may be described as stepper motors, with fixed permanent magnets and possibly more poles on the rotor than the stator, or reluctance motors. The latter may be without permanent magnets, just poles that are induced on the rotor then pulled into alignment by timed stator windings. However, the term stepper motor tends to be used for motors that are designed specifically to be operated in a mode where they are frequently stopped with the rotor in a defined angular position; this page describes more general BLDC motor principles, though there is overlap.