Chapter 16 MAINTENANCE RESOURCE MANAGEMENT
Total Page:16
File Type:pdf, Size:1020Kb
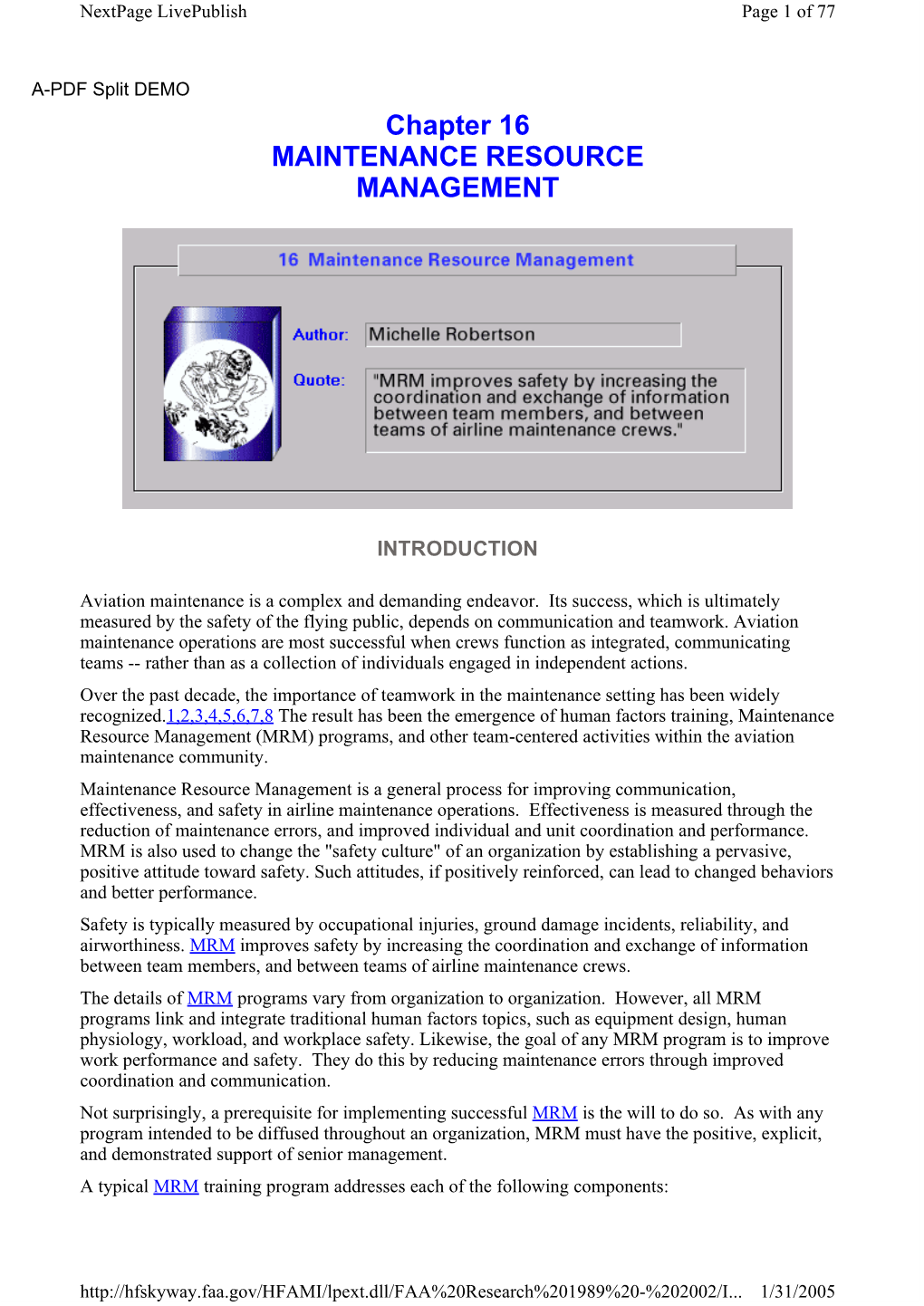
Load more
Recommended publications
-
Printing Office
Chapter 16 MAINTENANCE RESOURCE MANAGEMENT INTRODUCTION Aviation maintenance is a complex and demanding endeavor. Its success, which is ultimately measured by the safety of the flying public, depends on communication and teamwork. Aviation maintenance operations are most successful when crews function as integrated, communicating teams -- rather than as a collection of individuals engaged in independent actions. Over the past decade, the importance of teamwork in the maintenance setting has been widely recognized.1,2,3,4,5,6,7,8 The result has been the emergence of human factors training, Maintenance Resource Management (MRM) programs, and other team-centered activities within the aviation maintenance community. Maintenance Resource Management is a general process for improving communication, effectiveness, and safety in airline maintenance operations. Effectiveness is measured through the reduction of maintenance errors, and improved individual and unit coordination and performance. MRM is also used to change the "safety culture" of an organization by establishing a pervasive, positive attitude toward safety. Such attitudes, if positively reinforced, can lead to changed behaviors and better performance. Safety is typically measured by occupational injuries, ground damage incidents, reliability, and airworthiness. MRM improves safety by increasing the coordination and exchange of information between team members, and between teams of airline maintenance crews. The details of MRM programs vary from organization to organization. However, all MRM programs link and integrate traditional human factors topics, such as equipment design, human physiology, workload, and workplace safety. Likewise, the goal of any MRM program is to improve work performance and safety. They do this by reducing maintenance errors through improved coordination and communication. -
Crew Resource Management in Healthcare
FLYING LESSONS: CREW RESOURCE MANAGEMENT IN HEALTHCARE Authored by: Colin Konschak, FACHE, CEO Blake Smith, Principal www.divurgent.com © Divurgent 2017-2018 INTRODUCTION Patient safety has come under closer scrutiny in recent years and experts agree that human factors are major contributors to adverse events in healthcare. In its1999 landmark report, “To Err is Human: Building a Safer Health Care System,” the Institute of Medicine (IOM) stated that anywhere from 44,000 to 98,000 patients die each year as a result of medical errors at an estimated annual cost of $29 billion.i Medical errors, two-thirds of which are preventable, are the eighth leading cause of death in the U.S. each year.ii As medicine relies on increasingly complex technologies, this problem will only intensify. For example, The New York Times recently conducted a study that found an alarming number of injuries related to radiation therapy. The injuries, which should have been avoidable, were caused by faulty programming, poor safety procedures, software flaws that should have been recognized, and inadequate staffing and training.iii Like medicine, aviation relies on teams of experts working together to carry out complex procedures that, if not executed properly, can have serious consequences. If 98,000 people died in plane crashes each year, it would be the equivalent of a fatal jet crash – 268 passengers – every day. Airlines, however, have taken steps to prevent such catastrophes and health care providers are taking note. FOLLOWING AVIATION’S LEAD In 1977, two Boeing 747s collided on a runway in the Canary Islands, killing 582 people. -
World Cinema Through G G Obal
COSTANZO “A wonderful textbook as well as a scholarly tour-de-force. Costanzo brings new meaning to the concept of global genres and offers up examples that convincingly demonstrate cinematic border crossings and cultural connections amongst far- flung places.” David Desser, University of Illinois at Urbana–Champaign, USA “Costanzo revitalizes both world cinema and genre studies with his stimulating, WORLD insightful cross cultural approach to warrior heroes, wedding films, horror and road WORLD CINEMA movies. It’s a well-written, scholarly work that’s as inventive as it is enjoyable.” Diane Carson, Past President, University Film and Video Association (UFVA) “William Costanzo has cut the clearest path yet through the forest of World CINEMA Cinema. Key genres take us confidently place to place, era to era; while maps, timelines, and surveys of national industries position a rich array of films, many analyzed with real mastery.” Dudley Andrew, Professor of Film and Comparative Literature, Yale University, USA THROUGH World Cinema through Global Genres offers a new response to recent trends in internationalism that shape the increasingly global character of movies. Costanzo is able to render the complex forces of global filmmaking accessible to students; instead of tracing the long histories of cinema country by country, this innovative textbook uses engaging, recent films like Hero (China), Monsoon THROUGH THROUGH G LOBAL Wedding (India), and Central Station (Brazil) as entry points, linking them to comparable American and European films. The book’s cluster-based organization allows students to acquire a progressively sharper understanding of core issues about genre, aesthetics, industry, culture, history, film theory, and representation that apply to all films around the world. -
Aerosafety World November 2009
AeroSafety WORLD DOUSING THE FLAMES FedEx’s automatic system CRM FAILURE Black hole approach UPSET TRAINING Airplane beats simulators IASS REPORT 777 power rollback, more TRAGEDY AS INSPIRATION JAPAN Airlines’ safeTY CENTER THE JOURNAL OF FLIGHT SAFETY FOUNDATION NOVEMBER 2009 “Cessna is committed to providing the latest safety information to our customers, and that’s why we provide each new Citation owner with an FSF Aviation Department Tool Kit.” — Will Dirks, VP Flight Operations, Cessna Aircraft Co. afety tools developed through years of FSF aviation safety audits have been conveniently packaged for your flight crews and operations personnel. These tools should be on your minimum equipment list. The FSF Aviation Department Tool Kit is such a valuable resource that Cessna Aircraft Co. provides each new Citation owner with a copy. One look at the contents tells you why. Templates for flight operations, safety and emergency response manuals formatted for easy adaptation Sto your needs. Safety-management resources, including an SOPs template, CFIT risk assessment checklist and approach-and-landing risk awareness guidelines. Principles and guidelines for duty and rest schedul- ing based on NASA research. Additional bonus CDs include the Approach and Landing Accident Reduction Tool Kit; Waterproof Flight Operations (a guide to survival in water landings); Operator’sMEL Flight Safety Handbook; item Turbofan Engine Malfunction Recognition and Response; and Turboprop Engine Malfunction Recognition and Response. Here’s your all-in-one collection of flight safety tools — unbeatable value for cost. FSF member price: US$750 Nonmember price: US$1,000 Quantity discounts available! For more information, contact: Namratha Apparao, + 1 703 739-6700, ext. -
October 2016
October 2016 9:00 PM ET/6:00 PM PT 7:20 PM ET/4:20 PM PT 11:15 PM ET/8:15 PM PT 8:00 PM CT/7:00 PM MT 6:20 PM CT/5:20 PM MT 10:15 PM CT/9:15 PM MT Guns of the Magnificent Seven The Forgotten I.Q. 10:35 PM ET/7:35 PM PT 9:00 PM ET/6:00 PM PT SATURDAY, OCTOBER 1 9:35 PM CT/8:35 PM MT 8:00 PM CT/7:00 PM MT SUNDAY, OCTOBER 2 12:20 AM ET/9:20 PM PT The X-Files Great Balls Of Fire 11:20 PM CT/10:20 PM MT 1:05 AM ET/10:05 PM PT 12:05 AM CT/11:05 PM MT 10:50 PM ET/7:50 PM PT 9:50 PM CT/8:50 PM MT Die Hard The Magnificent Seven MONDAY, OCTOBER 3 2:40 AM ET/11:40 PM PT 12:40 AM ET/9:40 PM PT Sixteen Candles 1:40 AM CT/12:40 AM MT 3:15 AM ET/12:15 AM PT 11:40 PM CT/10:40 PM MT 2:15 AM CT/1:15 AM MT The Deer Hunter Guns of the Magnificent Seven The Forgotten TUESDAY, OCTOBER 4 5:50 AM ET/2:50 AM PT 2:15 AM ET/11:15 PM PT 12:25 AM ET/9:25 PM PT 4:50 AM CT/3:50 AM MT 5:05 AM ET/2:05 AM PT 1:15 AM CT/12:15 AM MT 11:25 PM CT/10:25 PM MT 4:05 AM CT/3:05 AM MT The Trailer Show Ravenous The X-Files Great Balls Of Fire 6:00 AM ET/3:00 AM PT 4:25 AM ET/1:25 AM PT 2:15 AM ET/11:15 PM PT 5:00 AM CT/4:00 AM MT 6:50 AM ET/3:50 AM PT 3:25 AM CT/2:25 AM MT 1:15 AM CT/12:15 AM MT 5:50 AM CT/4:50 AM MT Harry and the Hendersons Arthur and the Invisibles 2: The Legend Sixteen Candles 7:55 AM ET/4:55 AM PT 6:00 AM ET/3:00 AM PT 3:50 AM ET/12:50 AM PT 6:55 AM CT/5:55 AM MT Revenge of Maltazard 5:00 AM CT/4:00 AM MT 2:50 AM CT/1:50 AM MT 8:30 AM ET/5:30 AM PT The Magnificent Seven 7:30 AM CT/6:30 AM MT The Legend of Zorro Dazed and Confused 10:10 AM ET/7:10 AM PT 8:15 AM ET/5:15 AM PT 5:35 AM ET/2:35 AM PT 9:10 AM CT/8:10 AM MT The Trailer Show 7:15 AM CT/6:15 AM MT 4:35 AM CT/3:35 AM MT 8:40 AM ET/5:40 AM PT Guns of the Magnificent Seven 7:40 AM CT/6:40 AM MT The Mask of Zorro Robots 12:00 PM ET/9:00 AM PT 10:40 AM ET/7:40 AM PT 7:10 AM ET/4:10 AM PT 11:00 AM CT/10:00 AM MT Reservoir Dogs 9:40 AM CT/8:40 AM MT 6:10 AM CT/5:10 AM MT 10:25 AM ET/7:25 AM PT Harry and the Hendersons 9:25 AM CT/8:25 AM MT E.T. -
The Most Important Aviation System: the Human Team and Decision Making in the Modern Cockpit
University of Tennessee, Knoxville TRACE: Tennessee Research and Creative Exchange Masters Theses Graduate School 8-2004 The Most Important Aviation System: The Human Team and Decision Making in the Modern Cockpit John Cody Allee University of Tennessee - Knoxville Follow this and additional works at: https://trace.tennessee.edu/utk_gradthes Part of the Aerospace Engineering Commons Recommended Citation Allee, John Cody, "The Most Important Aviation System: The Human Team and Decision Making in the Modern Cockpit. " Master's Thesis, University of Tennessee, 2004. https://trace.tennessee.edu/utk_gradthes/1820 This Thesis is brought to you for free and open access by the Graduate School at TRACE: Tennessee Research and Creative Exchange. It has been accepted for inclusion in Masters Theses by an authorized administrator of TRACE: Tennessee Research and Creative Exchange. For more information, please contact [email protected]. To the Graduate Council: I am submitting herewith a thesis written by John Cody Allee entitled "The Most Important Aviation System: The Human Team and Decision Making in the Modern Cockpit." I have examined the final electronic copy of this thesis for form and content and recommend that it be accepted in partial fulfillment of the equirr ements for the degree of Master of Science, with a major in Aviation Systems. Robert B. Richards, Major Professor We have read this thesis and recommend its acceptance: Ralph D. Kimberlin, George W. Garrison Accepted for the Council: Carolyn R. Hodges Vice Provost and Dean of the Graduate School (Original signatures are on file with official studentecor r ds.) To the Graduate Council I am submitting herewith a thesis written by John Cody Allee entitled "The Most Important Aviation System: The Human Team and Decision Making in the Modern Cockpit. -
International Journal of Applied Aviation Studies Federal Aviation Administration
2010 International Journal of Applied Aviation Studies Federal Aviation Administration Volume 10, Number 1 A publication of the FAA Academy International Journal of Applied Aviation Studies A Publication of the FAA Academy Oklahoma City, Oklahoma Volume 10, Number 1 2010 REVIEW PROCESS 1 The Federal Aviation Administration Academy provides traceability and over- sight for each step of the International Journal of Applied Aviation Studies (IJAAS). IJAAS is a peer-reviewed publication, enlisting the support of an international pan- el of consulting editors. Each consulting editor was chosen for his or her expertise in one or more areas of interest in aviation. Using the blind-review process, three or more consulting editors are selected to appraise each article, judging whether or not it meets the requirements of this publication. In addition to an overall appraisal, a Likert scale is used to measure attitudes regarding individual segments of each article. Articles that are accepted are those that were approved by a majority of judges. Articles that do not meet IJAAS requirements for publication are released back to their author or authors. Individuals wishing to obtain a copy of the IJAAS on CD may contact Kay Ch- isholm by email at [email protected], or by telephone at (405) 954-3264, or by writing to the following address: International Journal of Applied Aviation Studies Kay Chisholm AMA-800 PO Box 25082 Oklahoma City, OK 73125 International Journal of Applied Aviation Studies Volume 10, Number 1 ISSN Number: 1546-3214 Copyright © 2010, FAA Academy 1st Printing August, 2010 The International Journal of Applied Aviation Studies 1 POLICY AND DISCLAIMERS Policy Statement: The Federal Aviation Administration (FAA) Academy strongly supports academic freedom and a researcher’s right to publish; therefore, the Fed- eral Aviation Administration Academy as an institution does not endorse the view- point or guarantee the technical correctness of any of the articles in this journal. -
European Journal of American Studies, 12-2 | 2017 “The Old Wild West in the New Middle East”: American Sniper (2014) and the Gl
European journal of American studies 12-2 | 2017 Summer 2017, including Special Issue: Popularizing Politics: The 2016 U.S. Presidential Election “The Old Wild West in the New Middle East”: American Sniper (2014) and the Global Frontiers of the Western Genre Lennart Soberon Electronic version URL: https://journals.openedition.org/ejas/12086 DOI: 10.4000/ejas.12086 ISSN: 1991-9336 Publisher European Association for American Studies Electronic reference Lennart Soberon, ““The Old Wild West in the New Middle East”: American Sniper (2014) and the Global Frontiers of the Western Genre”, European journal of American studies [Online], 12-2 | 2017, document 12, Online since 01 August 2017, connection on 08 July 2021. URL: http://journals.openedition.org/ ejas/12086 ; DOI: https://doi.org/10.4000/ejas.12086 This text was automatically generated on 8 July 2021. Creative Commons License “The Old Wild West in the New Middle East”: American Sniper (2014) and the Gl... 1 “The Old Wild West in the New Middle East”: American Sniper (2014) and the Global Frontiers of the Western Genre Lennart Soberon 1 While recent years have seen no shortage of American action thrillers dealing with the War on Terror—Act of Valor (2012), Zero Dark Thirty (2012), and Lone Survivor (2013) to name just a few examples—no film has been met with such a great controversy as well as commercial success as American Sniper (2014). Directed by Clint Eastwood and based on the autobiography of the most lethal sniper in U.S. military history, American Sniper follows infamous Navy Seal Chris Kyle throughout his four tours of duty to Iraq. -
Maintenance Resource Management Programs
FLIGHT SAFETY FOUNDATION OCTOBER 2002 FLIGHT SAFETY DIGEST Maintenance Resource Management Programs Provide Tools for Reducing Human Error FLIGHT SAFETY FOUNDATION For Everyone Concerned With the Safety of Flight Flight Safety Digest Officers and Staff Vol. 21 No. 10 October 2002 Hon. Carl W. Vogt Chairman, Board of Governors Stuart Matthews In This Issue President and CEO Robert H. Vandel Maintenance Resource Management Executive Vice President Programs Provide Tools for Reducing 1 James S. Waugh Jr. Human Error Treasurer The programs include a variety of initiatives to identify and ADMINISTRATIVE reduce human error in aviation maintenance. Specialists Ellen Plaugher applaud the goal, but some say that the programs are not Special Events and Products Manager achieving sufficient progress. Linda Crowley Horger Manager, Support Services Data Show 32 Accidents in 2001 Among FINANCIAL 16 Crystal N. Phillips Western-built Large Commercial Jets Director of Finance and Administration Twenty of the accidents were classified as hull-loss accidents. Millicent Wheeler Data show an accident rate in 2001 of 1.75 per 1 million Accountant departures and a hull-loss/fatal accident rate of 1.17 per TECHNICAL 1 million departures. James M. Burin Director of Technical Programs Study Analyzes Differences in Joanne Anderson 23 Technical Programs Specialist Rotating-shift Schedules Louis A. Sorrentino III The report on the study, conducted by the U.S. Federal Managing Director of Internal Evaluation Programs Aviation Administration, said that changing shift rotation for Robert Feeler air traffic controllers probably would not result in improved Q-Star Program Administrator sleep. Robert Dodd, Ph.D. Manager, Data Systems and Analysis B-767 Flap Component Separates Darol V. -
The Magnificent Seven Sculptors
THE MAGNIFICENT SEVEN SCULPTORS STAND CO2 ART CENTRAL HONG KONG 27 MARCH - 1 APRIL 2018 CENTRAL HARBOR FRONT 01 Born in Victoria in 1976, Daniel Agdag is an Australian artist and flmmaker. The son of Armenian immigrants, Agdag studied fne art before turning his hand to flmmaking and receiving his Masters in Film and Television at the Victorian College of the Arts in 2007. He will tell you that he makes things out of cardboard. He’s modest. This declaration in no way illuminates the delicate form and eccentric narrative of his work. To say he pushes the medium to its limits is an understatement. His process is very much akin to freehand drawing. He spends a great deal of time thinking and absorbing objects in the built environment, their peculiar details and functions, which leads him to form narratives. Once this is frmly resolved in his mind, various components of the work begin to slowly emerge, ftting together to compliment the overall idea. This narrative is the blueprint from which he works, it informs every component; it’s place, how each relates to the other, and most importantly, the proportions. The painstaking proportions, the key factor that drives his DANIEL AGDAG aesthetic. Like drawing, he builds the work up piece by ART CENTRAL HONG KONG piece, section by section, always assessing it in relation to the entirety of the parts. 27 MARCH - 1 APRIL The build is entirely intuitive, Agdag describes his process as ‘sketching with cardboard’, as he makes no detailed plans or drawings of the pieces he creates. -
AQA GCSE Unit 1: Listening to and Appraising Music – Preparation and Practice
KSKS45 AQA GCSE Unit 1: Listening to and Appraising Music – preparation and practice Alan Charlton is an by Alan Charlton author, composer and examiner and has written numerous books and articles on music education. He INTRODUCTION taught for a number of years at Bedford This article is designed to support students taking the AQA GCSE Music Unit 1 examination paper, Listening to School, initially as a composer- and Appraising Music (42701). It will look at the different types of questions that are typically set, and suggest in-residence, ways in which they can be prepared for and approached. Practice questions, based on extracts on Spotify, are and has a PhD in provided to practise and refine students’ knowledge and aural skills. composition from the University of Bristol. GENERAL FEATURES OF THE PAPER The Listening to and Appraising Music paper examines how effectively students can identify musical elements through listening skills. As well as aural perception skills, they need to display a good understanding of the terminology for the five AQA Areas of Study (the elements of music). The paper lasts an hour, and candidates answer a question paper based on recorded excerpts played on a CD. A typical example of how the questions were distributed can be seen in the 2012 paper, in which there were 18 recorded extracts, each of which was played between two and four times, depending on the difficulty of the questions asked. These were divided into 12 questions (each worth between five and nine marks), further divided into between three and seven shorter questions generally worth one or two marks each. -
People and Place: a Journey Through Film, Tourism, and Heritage
University of Denver Digital Commons @ DU Electronic Theses and Dissertations Graduate Studies 2020 People and Place: A Journey Through Film, Tourism, and Heritage Sarah Beals University of Denver Follow this and additional works at: https://digitalcommons.du.edu/etd Part of the Museum Studies Commons, Other Film and Media Studies Commons, and the Social and Cultural Anthropology Commons Recommended Citation Beals, Sarah, "People and Place: A Journey Through Film, Tourism, and Heritage" (2020). Electronic Theses and Dissertations. 1725. https://digitalcommons.du.edu/etd/1725 This Thesis is brought to you for free and open access by the Graduate Studies at Digital Commons @ DU. It has been accepted for inclusion in Electronic Theses and Dissertations by an authorized administrator of Digital Commons @ DU. For more information, please contact [email protected],[email protected]. People and Place: A Journey Through Film, Tourism, and Heritage ______________ A Thesis Presented to the Faculty of the College of Arts, Humanities and Social Sciences University of Denver ____________ In Partial Fulfillment of the Requirements for the Degree Master of Arts ____________ by Sarah Beals August 2020 Advisor: Dr. Esteban Gomez ©Copyright by Sarah Beals 2020 All Rights Reserved Author: Sarah Beals Title: People and Place: A Journey Through Film, Tourism, and Heritage Advisor: Dr. Esteban Gomez Degree Date: August 2020 Abstract Old Tucson Studios is a theme park where film, tourism, and heritage all converge through the American Western genre. During national social change, Westerns increase in number to reflect national values and identity. Westerns that ally with landscapes and people are potentially the most powerful storytelling tool in mainstream media.