Single-Equipment with Multiple-Application for an Automated Robot-Car Control System
Total Page:16
File Type:pdf, Size:1020Kb
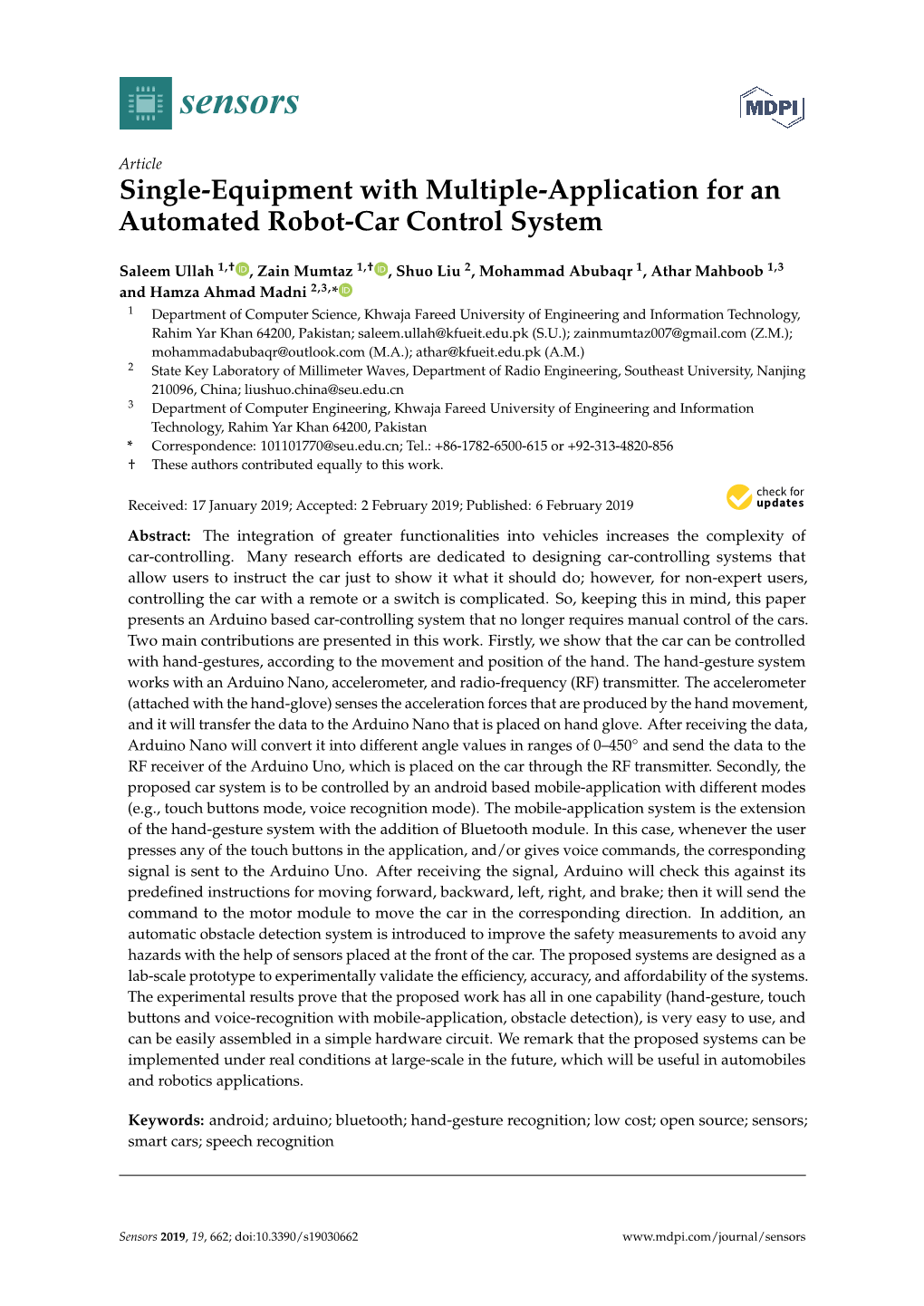
Load more
Recommended publications
-
Arduino Nano
Arduino Nano Arduino Nano Front Arduino Nano Rear Overview The Arduino Nano is a small, complete, and breadboard-friendly board based on the ATmega328 (Arduino Nano 3.0) or ATmega168 (Arduino Nano 2.x). It has more or less the same functionality of the Arduino Duemilanove, but in a different package. It lacks only a DC power jack, and works with a Mini-B USB cable instead of a standard one. The Nano was designed and is being produced by Gravitech. Schematic and Design Arduino Nano 3.0 (ATmega328): schematic, Eagle files. Arduino Nano 2.3 (ATmega168): manual (pdf), Eagle files. Note: since the free version of Eagle does not handle more than 2 layers, and this version of the Nano is 4 layers, it is published here unrouted, so users can open and use it in the free version of Eagle. Specifications: Microcontroller Atmel ATmega168 or ATmega328 Operating Voltage (logic 5 V level) Input Voltage 7-12 V (recommended) Input Voltage (limits) 6-20 V Digital I/O Pins 14 (of which 6 provide PWM output) Analog Input Pins 8 DC Current per I/O Pin 40 mA 16 KB (ATmega168) or 32 KB (ATmega328) of which 2 KB used by Flash Memory bootloader SRAM 1 KB (ATmega168) or 2 KB (ATmega328) EEPROM 512 bytes (ATmega168) or 1 KB (ATmega328) Clock Speed 16 MHz Dimensions 0.73" x 1.70" Power: The Arduino Nano can be powered via the Mini-B USB connection, 6-20V unregulated external power supply (pin 30), or 5V regulated external power supply (pin 27). -
A Frequency Generator with Si5351a Synthesizer Module
A Frequency Generator with Si5351A Synthesizer Module This article describes a simple Frequency Generator that can be used in place of a Variable Frequency Oscillator (VFO) or to replace a Crystal Oscillator. My basic goal was to build a project that could be duplicated easily with components that could be easily sourced through mail order with low cost. The project initially used the AD9850 DDS (Direct Digital Synthesizer) from Analog Devices that outputs both sine and square waves from 1 Hz to 42 MHz. As I wanted a Generator capable of going higher than that in frequency I decided to proceed with Si5351A controlled from an Arduino board or even better from a barebones ATmega328P-PU, as these MCUs are highly popular. After all I had published the detailed construction of a Generator with AD9850 in SV-News early this year (January 2015 issue). The basis of the project is a small readily available board with a mere surface of 3 by 3 centimeters military grade board that incorporates the Si5153A from Silicon Labs, a special 10 ppm 27 MHz crystal, a 3,3 volt regulator (as Si5351A operates in that level) and two mosfet transistors that operate as level converters for the control ports of the ic (SDA and SCL). An on-board jumper selects the desired level for the ports to either 5 or 3,3 volts. The ic which is an SMD type can simultaneously produce up to three different square wave frequencies with a range from 8 Khz to 160 MHz and a 50 ohm output impedance. -
Water Level Tracking System by Using Online Arduino a Thesis Submitted to the Gradute School of Applied Sciences of Near East U
WATER LEVEL TRACKING SYSTEM BY USING ONLINE ARDUINO A THESIS SUBMITTED TO THE GRADUTE SCHOOL OF APPLIED SCIENCES OF NEAR EAST UNIVERSITY By ÇAĞRI ÖZKAN In Partial Fulfillment of the Reguirements for The Degree of Master of Science in Information Systems Engineering NICOSIA, 2017 WATER LEVEL TRACKING SYSTEM BY USING ONLINE ARDUINO A THESIS SUBMITTED TO THE GRADUTE SCHOOL OF APPLIED SCIENCES OF NEAR EAST UNIVERSITY By ÇAĞRI ÖZKAN In Partial Fulfillment of the Reguirements for The Degree of Master of Science in Information Systems Engineering NICOSIA, 2017 I hereby declare that all information in this document has been obtained and presented in accordance with academic rules and ethical conduct. I also declare that, as required by these rules and conduct, I have fully cited and referenced all material and results that are not original to this work. Name, Last name : Çağrı Özkan Signature : Date: ACKNOWLEDGMENTS I would like to express my deepest gratitude to my supervisor Assistant Professor Dr. Boran Sekeroglu for his great support and open-minded mentorship, without whom this study would not have been completed. Special thanks go to Mr. Murat Ozturk, Mr. Süleyman Pasa, Mr. Emrah Bebek, Mr. Abdullah Sarı, Mr. Cengiz Barcın, and Ms. Aria Toprak for their technical assistance on firefighting reservoirs and project itself. I am grateful to Assistant Prof. Dr. Sertan Kaymak, Dr. Perihan Aysal Adun and Ms. Kezban Alpan for their invaluable recommendations. I would like to thank all the chairs in my jury for their scholarly recommendations. I am deeply grateful to my parents for their long-life support. -
Arduino Nano 3.1 Item# ARMB-0022
Arduino Nano 3.1 Item# ARMB‐0022 Overview: Arduino Nano is a surface mount breadboard embedded version with integrated USB. It is a smallest, complete, and breadboard friendly. It has everything that Diecimila/Duemilanove has (electrically) with more analog input pins and onboard +5V AREF jumper. Physically, it is missing power jack. The Nano is automatically sense and switch to the higher potential source of power, there is no need for the power select jumper. Nano’s got the breadboard‐ability of the Boarduino and the Mini+USB with smaller footprint than either, so users have more breadboard space. It’s got a pin layout that works well with the Mini or the Basic Stamp (TX, RX, ATN, GND on one top, power and ground on the other). This new version 3.0 comes with ATMEGA328 which offer more programming and data memory space. It is two layers. That make it easier to hack and more affordable. Electronics Source Co.,Ltd Website : http://www.es.co.th 7/129 Central Pinklao Bldg., 17FL., Unit 1702 Email : [email protected] Baromrachonnee Rd., Bangkok‐noi, Bangkok 10700 Tel : (662) 884‐9210 (6 line) Fax : (662) 884‐9213‐4 Specifications: Microcontroller Atmel ATmega328 Operating Voltage (logic level) 5 V Input Voltage (recommended) 7‐12 V Input Voltage (limits) 6‐20 V Digital I/O Pins 14 (of which 6 provide PWM output) Analog Input Pins 8 DC Current per I/O Pin 40 mA Flash Memory 32 KB (of which 2KB used by bootloader) SRAM 2 KB EEPROM 1 KB Clock Speed 16 MHz Dimensions 0.70” x 1.70” Electronics Source Co.,Ltd Website : http://www.es.co.th 7/129 Central -
Deepedgebench: Benchmarking Deep Neural Networks on Edge Devices*
DeepEdgeBench: Benchmarking Deep Neural Networks on Edge Devices* *Note: This the preprint version of the accepted paper at IC2E’21 Stephan Patrick Baller∗, Anshul Jindal∗, Mohak Chadha∗, Michael Gerndt∗ ∗Chair of Computer Architecture and Parallel Systems, Technische Universitat¨ Munchen,¨ Germany Garching (near Munich), Germany Email: fstephan.baller, anshul.jindal, [email protected], [email protected] Abstract—EdgeAI (Edge computing based Artificial Intelli- strict latency requirements that the cloud would have difficulty gence) has been most actively researched for the last few years to meeting since it may be far away from the users [7]. handle variety of massively distributed AI applications to meet The concept of Edge Computing has been recently proposed up the strict latency requirements. Meanwhile, many companies have released edge devices with smaller form factors (low power to complement cloud computing to resolve these problems by consumption and limited resources) like the popular Raspberry performing certain tasks at the edge of the network [8]. The Pi and Nvidia’s Jetson Nano for acting as compute nodes at idea is to distribute parts of processing and communication to the edge computing environments. Although the edge devices are the ”edge” of the network, i.e closer to the location where it is limited in terms of computing power and hardware resources, needed. As a result, the server needs less computing resources, they are powered by accelerators to enhance their performance behavior. Therefore, it is interesting to see how AI-based Deep the network is less strained and latencies is decreased. Neural Networks perform on such devices with limited resources. -
Internet of Things Security Encryption Capacity Comparison for Iot Based on Arduino Devices
Master of Science in Computer Science June 2020 Internet of Things Security Encryption Capacity Comparison for IoT based on Arduino Devices Olaide Jamiu Olalekan Faculty of Computing, Blekinge Institute of Technology, 371 79 Karlskrona, Sweden This thesis is submitted to the Faculty of Computing at Blekinge Institute of Technology in partial fulfilment of the requirements for the degree of Master of Science in Computer Science. The thesis is equivalent to 20 weeks of full time studies. The author declare that he is the sole author of this thesis and that he had not used any sources other than those listed in the bibliography and identified as references. He further declares that he has not submitted this thesis at any other institution to obtain a degree. Contact Information: Author: Jamiu Olalekan Olaide [email protected] University advisor: Anders Carlsson Department of Computer Science and Engineering Faculty of Computing Blekinge Institute of Technology Internet : www.bth.se SE-371 79 Karlskrona, Sweden Phone : +46 455 38 50 00 Fax : +46 455 38 50 57 ABSTRACT Background: IoT is a system of devices with unique identifiers (UIDs) and can transfer data over a network. They are widely used in various sectors such as Health, Commercial, Transport, etc. However, most IoT devices are being exploited, as it is being recorded for the past few years, on how vulnerable users can be if they have any of these devices in their network. Arduino is one of the most commonly used IoT devices, notably products such as Uno and Mega2560 are highly acceptable in the market and the research world. -
Arduino Nano Introduction
ARDUINO NANO INTRODUCTION Arduino nano differ from other Arduino as it very small so it suitable for small sized projects and it supports breadboards so it can be plugged with other components in only one breadboard. ARDUINO NANO PHYSICAL COMPONENTS Microcontroller In Arduino Nano 2.x version, still used ATmega168 microcontroller while the Arduino Nano 3.x version already used ATmega328 microcontroller. 1 ATmega168 Microcontroller ATmega168 is a low-power CMOS 8-bit microcontroller based on the AVR® enhanced RISC architecture. And its features as follow: High Performance, Low Power Atmel®AVR® 8-Bit Microcontroller Family Advanced RISC Architecture o 131 Powerful Instructions o Most Single Clock Cycle Execution o 32 x 8 General Purpose Working Registers o Fully Static Operation o Up to 20 MIPS Throughput at 20MHz o On-chip 2-cycle Multiplier • High Endurance Non-volatile Memory Segments o 4K/8K/16KBytes of In-System Self-Programmable Flash Program Memory o 256/512/512Bytes EEPROM o 512/1K/1KBytes Internal SRAM o Write/Erase Cycles: 10,000 Flash/100,000 EEPROM o Data Retention: 20 years at 85°C/100 years at 25°C o Optional Boot Code Section with Independent Lock Bits In-System Programming by On-chip Boot Program True Read-While-Write Operation o Programming Lock for Software Security Atmel® QTouch® Library Support o Capacitive Touch Buttons, Sliders and Wheels o QTouch and QMatrix® Acquisition o Up to 64 sense channels Peripheral Features o Two 8-bit Timer/Counters with Separate Prescaler and Compare Mode o One 16-bit Timer/Counter -
Hello, and Welcome to the Presentation of This STM32 Evaluation Boards. It Covers the Main Features of the Evaluation Boards Dedicated to the STM32G4 Series
Hello, and welcome to the presentation of this STM32 evaluation boards. It covers the main features of the evaluation boards dedicated to the STM32G4 series. The demonstration software included with these boards will allow you to become more familiar with this new high- performance microcontroller. 1 The STM32G4 evaluation boards offers everything required for users to get started quickly and develop applications easily. These boards enable a wide diversity of applications taking benefit from security, connectivity and motor control features. The STM32G4 evaluation boards come with the STM32 comprehensive software HAL library together with various packaged software examples. They also embed a debug probe that helps you develop your own applications from the existing examples. 2 The STM32G4 microcontrollers have three sub-families: • STM32G4x4: hi-resolution line • STM32G4x3: performance line • STM32G4x1: access line. Two types of evaluation boards are available: • STM32 Nucleo • Evaluation boards Three discovery kits complement the evaluation boards: digital power, portable oscilloscope and electronic speed controller. Embedded software solutions are available to quickly develop applications based on STM32G4, including a motor control software development kit. 3 The highly affordable STM32 Nucleo boards allow anyone to try out new ideas and to quickly create prototypes with any STM32 MCU. Sharing the same connectors, STM32 Nucleo boards can easily be extended with a large number of specialized application hardware add-ons (Nucleo-64 include Arduino Uno rev3 & ST morpho connectors, Nucleo-32 include Arduino Nano connectors). The STM32 Nucleo boards integrate an ST-Link debugger/programmer, so there is no need for a separate probe. A comprehensive STM32 software HAL library together with various software examples is provided with the STM32 Nucleo boards, and seamlessly works with a wide range of development environments including STM32 CubeIDE, IAR EWARM, Keil MDK-ARM, mbed and GCC/LLVM-based IDEs. -
An Automated Robot-Car Control System with Hand-Gestures and Mobile Application Using Arduino
Preprints (www.preprints.org) | NOT PEER-REVIEWED | Posted: 3 January 2019 doi:10.20944/preprints201901.0029.v1 Article An Automated Robot-Car Control System with Hand- Gestures and Mobile Application Using Arduino Saleem Ullah1, Zain Mumtaz1, Shuo Liu2, Mohammad Abubaqr1, Athar Mahboob3 and Hamza Ahmad Madni2,3,* 1 Department of Computer Science, Khwaja Fareed University of Engineering and Information Technology, Rahim Yar Khan 64200, Pakistan; [email protected] (S.U.); [email protected] (Z.M.); [email protected] (M.A) 2 State Key Laboratory of Millimeter Waves, Department of Radio Engineering, Southeast University, Nanjing 210096, China; [email protected] (S.L.); [email protected] (H.A.M.) 3 Department of Computer Engineering, Khwaja Fareed University of Engineering and Information Technology, Rahim Yar Khan 64200, Pakistan; [email protected] (A.M.) * Correspondence: [email protected]; Tel.: +86-1782-6500-615 or +92-313-4820-856 Abstract: Gesture recognition has always been a technique to decrease the distance between the physical and the digital world. In this work, we introduce an Arduino based vehicle system which no longer require manual controlling of the cars. The proposed work is achieved by utilizing the Arduino microcontroller, accelerometer, RF sender/receiver, and Bluetooth. Two main contributions are presented in this work. Firstly, we show that the car can be controlled with hand-gestures according to the movement and position of the hand. Secondly, the proposed car system is further extended to be controlled by an android based mobile application having different modes (e.g., touch buttons mode, voice recognition mode). -
Programming Arduino Getting Started with Sketches
Programming Arduino™ Getting Started with Sketches Simon Monk Copyright © 2012 by The McGraw-Hill Companies. All rights reserved. Except as permitted under the United States Copyright Act of 1976, no part of this publication may be reproduced or distributed in any form or by any means, or stored in a database or retrieval system, without the prior written permission of the publisher. ISBN: 978-0-07-178423-8 MHID: 0-07-178423-3 The material in this eBook also appears in the print version of this title: ISBN: 978-0-07- 178422-1, MHID: 0-07-178422-5. All trademarks are trademarks of their respective owners. Rather than put a trademark symbol after every occurrence of a trademarked name, we use names in an editorial fashion only, and to the benefit of the trademark owner, with no intention of infringement of the trademark. Where such designations appear in this book, they have been printed with initial caps. McGraw-Hill eBooks are available at special quantity discounts to use as premiums and sales promotions, or for use in corporate training programs. To contact a representative please e-mail us at [email protected]. All trademarks or copyrights mentioned herein are the possession of their respec-tive owners and McGraw-Hill makes no claim of ownership by the mention of products that contain these marks. “Arduino” is a trademark of the Arduino team. Information has been obtained by McGraw-Hill from sources believed to be reliable. However, because of the possibility of human or mechanical error by our sources, McGraw-Hill, or others, McGraw-Hill does not guarantee the accuracy, adequacy, or completeness of any information and is not responsible for any errors or omissions or the results obtained from the use of such information. -
STM32 NUCLEO BOARDS Unified Scalable Offering
STM32 NUCLEO BOARDS Unified scalable offering Open STM32 development platform for flexible prototyping The highly affordable STM32 Nucleo boards allow anyone to try out new ideas and to quickly create KEY FEATURES prototypes with any STM32 MCU. • Includes one STM32 microcontroller in a 32-pin, 64-pin STM32 Nucleo boards can easily be extended or 144-pin package with a large number of specialized application • On-board ST-LINK debugger/programmer: hardware add‑ons thanks to Arduino Uno Rev3 • Virtual COM port and ST morpho connectors on Nucleo‑144 and • Mass storage Nucleo‑64, ST Zio connectors on Nucleo‑144, and • Wide extension capabilities with specialized shields: Arduino Nano connectors on Nucleo‑32. • Arduino Uno rev3 connectors on Nucleo-64 and Nucleo-144 • Access to a wider range of peripherals through Zio Moreover, Nucleo boards integrate an ST‑Link connectors on Nucleo-144 debugger/programmer, so there is no need for • Access to all MCU pins through ST morpho connectors on a separate probe. A comprehensive STM32 Nucleo-64 and Nucleo-144 software HAL library together with various • Arduino Nano connectors on Nucleo-32 software examples are provided with STM32 • Direct access to Mbed online resources for most boards Nucleo boards, and work smoothly with a wide • Supported by STM32CubeIDE, IAR, Arm Keil, Arm® range of development environments, allowing Mbed™ online, and more IDEs to build a complete application in only a few minutes. www.st.com/stm32nucleo STM32 NUCLEO BOARDS | UNIFIED SCALABLE OFFERING STM32 Nucleo development STM32 Nucleo expansion boards boards STM32 Nucleo development boards can easily be expanded through a variety of add‑on boards. -
Arduino Nano Is a Small, Complete, and Breadboard-Friendly Board Based on the Atmega328 (Arduino Nano 3.0) Or Atmega168 (Arduino Nano 2.X)
The Arduino Nano is a small, complete, and breadboard-friendly board based on the ATmega328 (Arduino Nano 3.0) or ATmega168 (Arduino Nano 2.x). It has more or less the same functionality of the Arduino Duemilanove, but in a different package. It lacks only a DC power jack, and works with a Mini-B USB cable instead of a standard one. The Nano was designed and is being produced by Gravitech. Arduino Nano 3.0 (ATmega328): schematic, Eagle files. Arduino Nano 2.3 (ATmega168): manual (pdf), Eagle files. Note: since the free version of Eagle does not handle more than 2 layers, and this version of the Nano is 4 layers, it is published here unrouted, so users can open and use it in the free version of Eagle. Microcontroller Atmel ATmega168 or ATmega328 Operating Voltage (logic 5 V level) Input Voltage 7-12 V (recommended) Input Voltage (limits) 6-20 V Digital I/O Pins 14 (of which 6 provide PWM output) Analog Input Pins 8 DC Current per I/O Pin 40 mA 16 KB (ATmega168) or 32 KB (ATmega328) of which 2 KB used by Flash Memory bootloader SRAM 1 KB (ATmega168) or 2 KB (ATmega328) EEPROM 512 bytes (ATmega168) or 1 KB (ATmega328) Clock Speed 16 MHz Dimensions 0.73" x 1.70" The Arduino Nano can be powered via the Mini-B USB connection, 6-20V unregulated external power supply (pin 30), or 5V regulated external power supply (pin 27). The power source is automatically selected to the highest voltage source. The FTDI FT232RL chip on the Nano is only powered if the board is being powered over USB.