Design and Evaluation of a Recirculating Aquaponic System
Total Page:16
File Type:pdf, Size:1020Kb
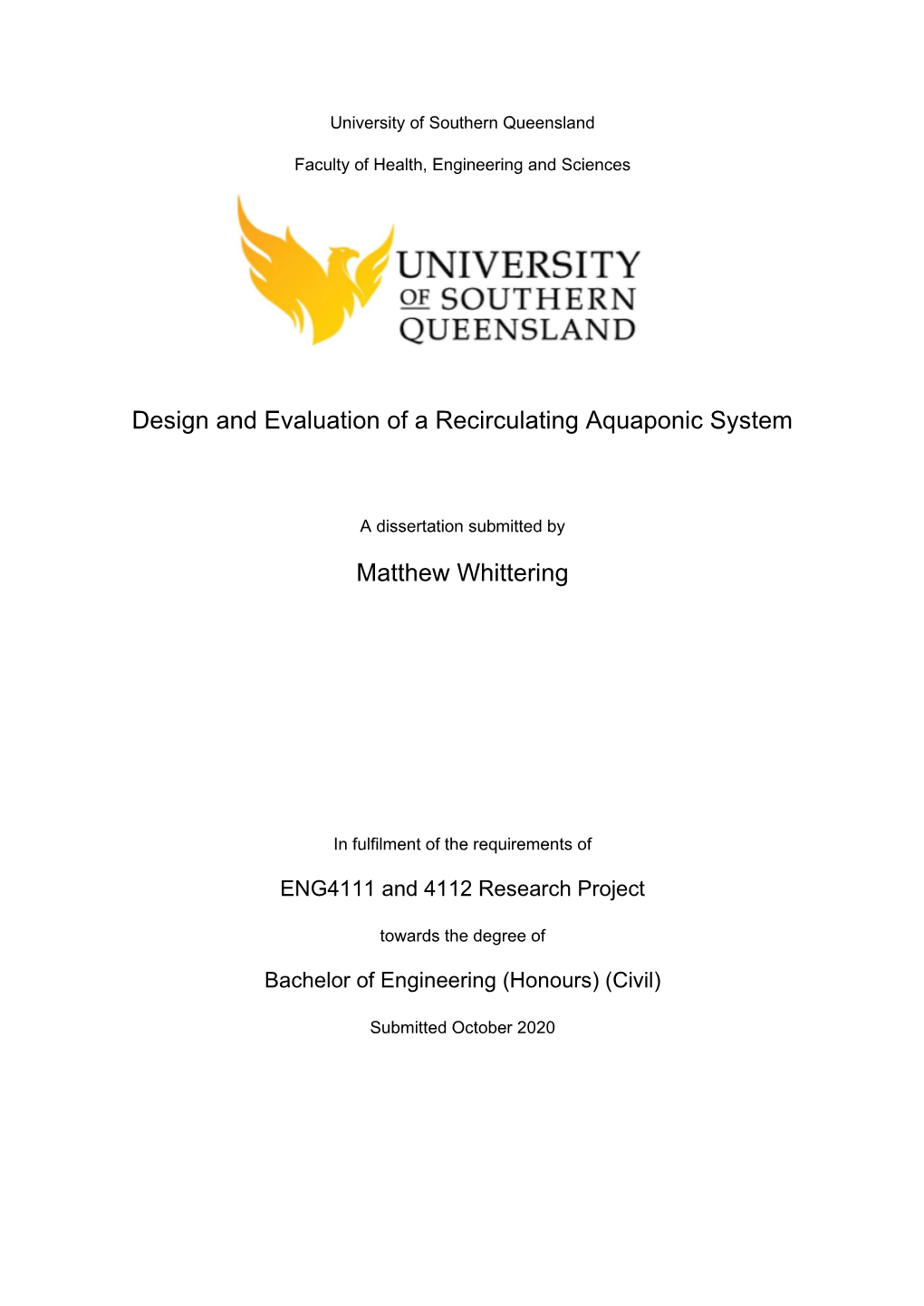
Load more
Recommended publications
-
Advances in Dryland Farming in the Inland Pacific Northwest
This an excerpt of Advances in Dryland Farming in the Inland Pacific Northwest Advances in Dryland Farming in the Inland Pacific Northwest represents a joint effort by a multi-disciplinary group of scientists from across the region over a three-year period. Together they compiled and synthesized recent research advances as well as economic and other practical considerations to support farmers as they make decisions relating to productivity, resilience, and their bottom lines. The effort to produce this book was made possible with the support of the USDA National Institute of Food and Agriculture through the REACCH project. This six-year project aimed to enhance the sustainability of Pacific Northwest cereal systems and contribute to climate change mitigation. The project, led by the University of Idaho, also convened scientists from Washington State University, Oregon State University, the USDA Agricultural Research Service, and Boise State University. To access the entire book, visit the Washington1 State University Extension Learning Library. Chapter 6 Soil Fertility Management Kristy Borrelli, Pennsylvania State University (formerly of University of Idaho) Tai Maaz, Washington State University William Pan, Washington State University Paul Carter, Washington State University Haiying Tao, Washington State University Abstract The inland Pacific Northwest’s (PNW) warm, dry climate and deep soils make it ideal for producing high yields of high-quality wheat. Wheat can grow in some of the region’s driest areas where other crops cannot. However, drastic topography and precipitation gradients result in variable growing conditions that impact crop yield and complicate nutrient management strategies. Interrelated climate, water, and nutrient dynamics drive wheat development, growth, and associated fertility recommendations; understanding these complex relationships will become increasingly important under changing climate conditions. -
Rainwater Harvesting for Dryland Agriculture in the Rift Valley of Ethiopia Birhanu Biazin Temesgen
Rainwater harvesting for dryland agriculture in the Rift Valley of Ethiopia Birhanu Biazin Temesgen Thesis committee Thesis supervisor Prof.dr.ir. L. Stroosnijder Professor of Land Degradation and Development Wageningen University Thesis co-supervisor Dr. G. Sterk Associate professor, Department of Physical Geography Utrecht University Other members Prof. dr. P.C. de Ruiter, Wageningen University Prof. dr. H.H.G. Savenije, Delft University Prof. dr. ir. J.E. Vermaat, Free University Amsterdam Dr. ir. W.B. Hoogmoed, Wageningen University This research was conducted under the auspices of Graduate School: C.T. de Wit Production Ecology and Resource Conservation Rainwater harvesting for dryland agriculture in the Rift Valley of Ethiopia Birhanu Biazin Temesgen Thesis submitted in fulfilment of the requirements for the degree of doctor at Wageningen University by the authority of the Rector Magnificus Prof. dr. M.J. Kropff, in the presence of the Thesis Committee appointed by the Academic Board to be defended in public on Monday 16 April 2012 at 4 p.m. in the Aula. Birhanu Biazin Temesgen Rainwater harvesting for dryland agriculture in the Rift Valley of Ethiopia 162 pages. Thesis, Wageningen University, Wageningen, NL (2012) With references, with summaries in Dutch and English ISBN 978-94-6173-215-6 Financially supported by: Wageningen University (Sandwich Programme) International Foundation for Science (IFS) Sweden International Development Agency (SIDA) Acknowledgement Various individuals and institutions contributed in different forms during the three phases of proposal designing, field data collection and final writing up of my PhD thesis. I am sincerely indebted to my promoter, prof. Leo Stroosnijder for his all-round help. -
Dryland Farming, Drought, and Adaptation in the Golden Triangle, Montana
University of Montana ScholarWorks at University of Montana Graduate Student Theses, Dissertations, & Professional Papers Graduate School 2015 Raising Grain in Next Year Country: Dryland Farming, Drought, and Adaptation in the Golden Triangle, Montana Caroline M. Stephens University of Montana Follow this and additional works at: https://scholarworks.umt.edu/etd Part of the Environmental Studies Commons, Food Security Commons, Nature and Society Relations Commons, Place and Environment Commons, and the United States History Commons Let us know how access to this document benefits ou.y Recommended Citation Stephens, Caroline M., "Raising Grain in Next Year Country: Dryland Farming, Drought, and Adaptation in the Golden Triangle, Montana" (2015). Graduate Student Theses, Dissertations, & Professional Papers. 4513. https://scholarworks.umt.edu/etd/4513 This Thesis is brought to you for free and open access by the Graduate School at ScholarWorks at University of Montana. It has been accepted for inclusion in Graduate Student Theses, Dissertations, & Professional Papers by an authorized administrator of ScholarWorks at University of Montana. For more information, please contact [email protected]. RAISING GRAIN IN NEXT YEAR COUNTRY: DRYLAND FARMING, DROUGHT, AND ADAPTATION IN THE GOLDEN TRIANGLE, MONTANA by CAROLINE MUIR STEPHENS Bachelor of Arts, Centre College, Danville, Kentucky, 2011 THESIS presented in partial fulfillment of the requirements for the degree of Master of Sciences in Environmental Studies The University of Montana, -
Sustainable Small Acreage Farming in Idaho: Finding and Evaluating Land
SUSTAINABLE SMALLsmall ACREAGEacreage FINDING AND FARMING IN IDAHO: EVALUATING LAND IRIS MAYES, ARIEL AGENBROAD, JENNIFER WERLIN, SAMANTHA GRAFF BUL 932 Sustainable Small Acreage Farming in Idaho: Finding and Evaluating Land Iris Mayes UI Extension Educator Ariel Agenbroad UI Extension Area Educator Jennifer Werlin UI Extension Educator Figure 1. Rural Property in Latah County, 2017. Samantha Graff Teacher/FFA Advisor, Mt. Adams School District, Washington Introduction IDAHO HAS A LONG HISTORY of small acreage farming that allows people to produce their own food themselves and Contents also to develop various farm-based business enterprises. 1 Introduction Establishing a small farm (Figure 1) is worthwhile, but it 2 Farm Planning requires time and attention to many details. 2 Finding Land This publication provides an overview of important consider- 2 Natural Resources ations for prospective farmers when selecting land to establish a successful small farm or ranch. Evaluating farm goals, assess- 4 Topography and Slope ing potential markets, and thinking through lifestyle choices, 4 Climate family relationships and partnerships on the farm are among 6 Pest and Problems the central concerns for a profitable and sustainable business. 7 Physical Assets Before purchasing property, it is advisable to learn about the 8 Nearby Industry and Agriculture history of the land. If the soil has been treated with pesticides 8 Marketing Farm Products and fertilizers and/or is depleted, it may need a rest period while you amend the soil with organic matter such as manure 8 Site History or compost, before it can be put back into production. There is Legal and Regulatory 8 much to think about before you acquire land so that you can Considerations grow your farm dream into a successful small farm business. -
Advances in Dryland Farming in the Inland Pacific Northwest
This an excerpt of Advances in Dryland Farming in the Inland Pacific Northwest Advances in Dryland Farming in the Inland Pacific Northwest represents a joint effort by a multi-disciplinary group of scientists from across the region over a three-year period. Together they compiled and synthesized recent research advances as well as economic and other practical considerations to support farmers as they make decisions relating to productivity, resilience, and their bottom lines. The effort to produce this book was made possible with the support of the USDA National Institute of Food and Agriculture through the REACCH project. This six-year project aimed to enhance the sustainability of Pacific Northwest cereal systems and contribute to climate change mitigation. The project, led by the University of Idaho, also convened scientists from Washington State University, Oregon State University, the USDA Agricultural Research Service, and Boise State University. To access the entire book, visit the Washington1 State University Extension Learning Library. Chapter 3 Conservation Tillage Systems Prakriti Bista, Oregon State University Stephen Machado, Oregon State University Rajan Ghimire, New Mexico State University (formerly of Oregon State University) Georgine Yorgey, Washington State University Donald Wysocki, Oregon State University Abstract Conservation tillage may improve the sustainability of winter wheat- based crop rotations in the dryland areas of the inland Pacific Northwest (PNW). Intensive tillage systems often bury most surface crop residues, pulverize soil, and reduce surface roughness. The tilled systems also have the potential to accelerate soil fertility loss and soil erosion, reducing the long-term sustainability of dryland agriculture. This chapter reviews the sustainability challenges posed by conventional tillage, including soil erosion, soil organic matter (SOM) depletion, soil fertility loss, and soil acidification. -
Dryland Husbandry in Ethiopia
, DRYLAND HUSBANDRY IN ETHIOPIA Research Report Edited by Mitiku Haile Diress Tsegaye Tegegne Teka DHP Publications Series No .. 7, December 2001 THE OSSREA Organization for Social Science Research in Eastern and Southern Africa , SCQle :.1: © 200 I Organization for Social Science Research in Eastern and Southern Africa (OSSREA) All Rights Reserved Published 200 I Printed in Ethiopia [SSN 1608-8891 ~ Typesetting: Selamawit Gelachew This publication is the exclusive property of the Organization for Social Science Research in Eastern and Southern Africa (OSSREA). Any use, copy, reproduction, or quotation of any nature must be accompan ied by the prior consent of The R_sional Project Coordinator, DHP/OSSREA. Cover photograph from DHP-Ethiopia Site: Tegegne Teka, Aba'ala, North Afar, Afar Regional State, Ethiopia Organization for Social Science Research in Easte rn and Southern Africa P.O . Box 3197 1, Addis Ababa, Ethiopia Fax : 251 -1-551399 E-mail: [email protected] pu b.o [email protected] http://www.ossrea.org Tegeglle Teka: Editor, DHP Publications Series & Regional Project Co-ordinator Dryland Husbandry Project Regional Advisory Committee of the Dryland Husbandry Project Prof. Abdel Ghaffar M. Ahmed (OSSREA, Ethiopia) Prof. Anders Hjort af Ornii s (EPOS, Li nkoping Uni versity, Sweden) Dr. Kassim O. Farah ( PINEP, University of Nairobi, Kenya) IGAD (OJ ibouti) Dr. Hashim EI Atta (U ni versity of Khartoum , Sudan) Prof. E. N. Sabiiti (Makerere University, Uganda) Dr. Nashon Musimba (Uni versity of Nairobi, Kenya) Dr. Bisral Gebru (U niversity of Asmara, Eritrea) Dr. Mitiku Haile (Mekelle University, Eth iopia) Dr. Tegegne Teka (OSSREA, Ethi opia) Editorial Address: DHP Publications Series OSSREk P.O.Box 31971 Addis Ababa, Ethiopia Tel: 251-1-551163/553281 Fax: 251-1-551399 E-mail:. -
Aohan Dryland Farming System. Proposal for the Globally Important Agricultural Heritage Systems
Proposal for Globally Important Agricultural Heritage Systems (GIAHS) Programme Aohan Dryland Farming System Location: Aohan County, Chifeng City, Inner Mongolia Autonomous Region, P.R. China People’s Government of Aohan County, Inner Mongolia Autonomous Region Center for Natural and Cultural Heritage of Institute of Geographic Sciences and Natural Resources Research, Chinese Academy of Sciences December 12, 2011 1 Summary Information a. Country and Location: Aohan County, Chifeng City, Inner Mongolia Autonomous Region, P.R. China b. Program Title/System Title: Aohan Dryland Farming System c. Total Area: 8294 km2 d. Ethnic Groups: Mongolian (5.34%), Manchu (1.11%), Hui (0.29%), Han (93.21%) e. Application Organization: Aohan County People’s Government, Chifeng City, Inner Mongolia Autonomous Region, P.R. China f. From the National Key Organization (NFPI): Centre for Natural and Cultural Heritage (CNACH) of Institute of Geographic Sciences and Natural Resources Research (IGSNRR), Chinese Academy of Sciences (CAS) g. Governmental and Other Partners • Ministry of Agriculture, P.R. China • China Agricultural University • Department of Agriculture of Inner Mongolia Autonomous Region, P.R. China • Aohan County People’s Government, Inner Mongolia Autonomous Region, P.R. China • Department of Agriculture of Aohan County, Inner Mongolia Autonomous Region, P.R. China • Department of Culture of Aohan County, Inner Mongolia Autonomous Region, P.R. China • Key Laboratory of Dry Farming Agriculture, Inner Mongolia Autonomous Region, P.R. China h. Abstract Aohan County is located in the southeast of Chifeng City, Inner Mongolia Autonomous Region, China. It is the interface between China’s ancient farming culture and grassland culture. From 2001 to 2003, carbonized particles of foxtail and broomcorn millet were discovered by archaeologists in the “First Village of China”, Xinglongwa in Aohan County. -
Freedom Through Dryland Farming – the Story of New Mexico’S First Black Settlement, Blackdom
Freedom through Dryland Farming – The Story of New Mexico’s First Black Settlement, Blackdom Maya L. Allen University of New Mexico Blackdom township farmers (NMSU Archives RG98-103-001) Sunday school class Photos: Historical Society for Southeast New Mexico • All Black farming town in southeastern New Mexico Blackdom • Black people cultivated a safe, empowered space for themselves Land Acknowledgement • Mescalero Apache Land • The Mescalero Apache Reservation was established in 1873 The Homestead Act - 1862 • Resulted in the settlement of 270 million acres Blackdom • Blackdom was incorporated in 1903 16 miles south of Roswell, New Mexico Blackdom Blackdom Land patents of the Blackdom residents Bureau of Land Management Federal land conveyance record database Blackdom Timeline Blackdom pooled their acreage to create the Blackdom Oil company and increase In January Frank Boyer and Daniel their probability of finding oil. Enters Keyes depart from Georgia and arrive in People started to truly settle and build into a contract worth 1 million dollars New Mexico in October the community of Blackdom today. Blackdom Blackdom Oil Journey West Settlement Company 1903 1912 1928 1900 1908 1919 Blackdom Townsite Blackdom Post Blackdom Company Office Abandoned Thirteen Black men form the Blackdom Height of Blackdom where an estimated Residents slowly had been leaving Townsite Company valued at $10,000 300 residents lived in town. Town sported Blackdom for numerous reasons. After a church, store, and office building 1928 Blackdom was no more. 24th Infantry Buffalo Soldier Ella Boyer and their children moved to NM in 1901 Homesteaded near Dexter, NM President Ella Boyer 1909 desert land claim under enlarged homestead act Two of the three board Members in 1911 NMSU Archives RG98-125-001 and 002 Blackdom Founding Frank Boyer and twelve other Black men formed the Blackdom Townsite Company with a putative capitalization of $10,000 on Sept. -
The Return of True Agricultural Localism
SEPTEMBER/OCTOBER 2020 GROWING A REGIONAL FOOD SYSTEM THE RETURN OF TRUE AGRICULTURAL LOCALISM VOLUME 12 NUMBER 4 GREENFIRETIMES.COM PUBLISHER GREEN EARTH PUBLISHING, LLC EDITOR-IN-CHIEF SETH ROFFMAN / [email protected] PLEASE SUPPORT GREEN FIRE TIMES GUEST ASSOCIATE EDITOR ERIN ORTIGOZA Green Fire Times provides a platform for regional, community-based DESIGN WITCREATIVE voices—useful information for residents, businesspeople, students and COPY EDITOR STEPHEN KLINGER visitors—anyone interested in the history and spirit of New Mexico and the Southwest. One of the unique aspects of GFT is that it offers CONTRIBUTING WRITERS ANITA ADALJA, JAIME CHÁVEZ, JULIANA multicultural perspectives and a link between the green movement and CIANO, VANESSA COLÓN, MARTHA COOKE, ZOE FINK, LUCY GENT FOMA, LISA traditional cultures. B. FRIEDLAND, ROD GESTEN, ISABELL JENNICHES, GILLIAN JOYCE, MELANIE MARGARITA KIRBY, JACK LOEFFLER, FAITH MAXWELL, RACHEL MOORE, KYLE Storytelling is at the heart of community health. GFT shares stories MALONE, MIKE MUSIALOWSKI, SAYRAH NAMASTE, ANDREW NEIGHBOR, CORILIA of hope and is an archive for community action. In each issue, a ORTEGA, ERIN ORTIGOZA, SONORA RODRÍGUEZ, ERNIE RIVERA, SETH ROFFMAN, small, dedicated staff and a multitude of contributors offer articles CHRISTINA M. ROGERS, MICAH ROSEBERRY, MIGUEL SANTISTEVAN, MELYNN documenting projects supporting sustainability—community, culture, SCHUYLER, JAMES SKEET, NINA YOZELL-EPSTEIN, MARK WINNE environment and regional economy. CONTRIBUTING PHOTOGRAPHERS ROSE CARMONA, JAIME CHÁVEZ, Green Fire Times is now operated by an LLC owned by a nonprofit VANESSA COLÓN, CORE VISUAL, BYRON FLESHER, MARY GAUL, GABRIELLA MARKS, educational organization (Est. 1972, swlearningcenters.org). Obviously, it BARBARA MOHON, JIM O’DONNELL, MELANIE MARGARITA KIRBY, ERIN ORTIGOZA, is very challenging to continue to produce a free, quality, independent SETH ROFFMAN, MICAH ROSEBERRY, MIGUEL SANTISTEVAN, JAMES SKEET publication. -
This Project Has Provided Additional Documentation in A
Drylands Natural Resources Centre is a cooperative, community-based organization that trains and coordinates over 400 dryland farming families in managing their natural resources, restoring ecosystems, and generating income through agroforestry. Background Founded and led by Kenyan national, Nicholas Syano, Drylands Natural Resources Centre (DNRC) equips subsistence farmers in drylands to restore their degraded lands and address the challenges of deforestation, falling crop yields, and climate change. As demand for firewood has increased with population pressure and as agricultural productivity has declined due to climate stress, farmers have been forced to over-exploit their farmland and adjacent forests. These lands have historically stabilized regional soil and water features. The result is soil erosion, nutrient depletion, and “My own mother and sisters face diminished water tables—a vicious cycle of environmental great hardship because of the degradation and declining agricultural productivity. extreme firewood shortage and are forced to pay great prices or DNRC aims to flip these climate-based feedback loops travel long distances to obtain it. from negative to positive. DNRC delivers an ambitious The nearby streams have dried up program of long-term community engagement, in which and the frogs I used to listen to families restore their land through the application of have disappeared. It is all agricultural and agroforestry best practices that increase connected. We need to stop this crop yield, improve soil and water resources, and generate destruction of our habitat and our valuable tree products. community” – Nicholas Syano DNRC currently works with 430 families (about 3,000 people), 90% of which are women-led, across 11 village community groups led by an elected chairperson, eight of which are currently women. -
Agronomic Options for Improving Rainfall-Use Efficiency of Crops In
Journal of Experimental Botany, Vol. 55, No. 407, Water-Saving Agriculture Special Issue, pp. 2413–2425, November 2004 doi:10.1093/jxb/erh154 Advance Access publication 10 September, 2004 Agronomic options for improving rainfall-use efficiency of crops in dryland farming systems Neil C. Turner* CSIRO Plant Industry, Private Bag No. 5, Wembley, WA 6913 and Centre for Legumes in Mediterranean Agriculture, University of Western Australia, 35 Stirling Highway, Crawley, WA 6009, Australia Downloaded from https://academic.oup.com/jxb/article/55/407/2413/496026 by guest on 27 September 2021 Received 18 December 2003; Accepted 27 February 2004 Abstract increasing water scarcity in this century (Seckler et al.,1999; Turner, 2001), particularly for agriculture, and the already Yields of dryland (rainfed) wheat in Australia have scarce availability of new land for agriculture will see less increased steadily over the past century despite rainfall irrigated land available for crop production than in the past. being unchanged, indicating that the rainfall-use effi- While supplemental irrigation can benefit yields and water- ciency has increased. Analyses suggest that at least use efficiency in water-limited environments (Oweis et al., half of the increase in rainfall-use efficiency can be 2000; Turner, 2004), the potential for even limited supple- attributed to improved agronomic management. Vari- mental irrigation is decreasing, with competition for water for ous methods of analysing the factors influencing dry- urban and industrial uses and in order to maintain environ- land yields and rainfall-use efficiency, such as simple mental flows. Thus, agriculture will become increasingly rules and more complex models, are presented and the dependent on rainfall as its sole source of water, and agronomic factors influencing water use, water-use maximizing the efficiency of its use to produce a crop will efficiency, and harvest index of crops are discussed. -
Improving the Sustainability of Dryland Farming Systems: a Global Perspective J.E Parr, B.A
Improving the Sustainability of Dryland Farming Systems: A Global Perspective J.E Parr, B.A. Stewart, S.B. Hornick, and R.P. Singh I. Introduction ................................................ I 11. The Concept of Sustainability ................................. 2 1lI. Dynamics of Soil Productivity .................................. 4 IV. Opportunities and Limitations ................................. 5 V. Perspectives and Strategies ................................... 7 References .................................................... 7 I. Introduction Arid and semiarid regions comprise almost 40% of the world's land area and are inhabited by some 700 million people. Approximately 60%of these drylands are in developing countries. Low rainfall areas constitute from 75-100% of the land area in more than 20 countries in the Near East, Africa, and Asia. Farmers in these regions produce more than 50% of the groundnuts, 80% of the pearl millet, 90% of the chickpeas, and 95% of the pigeon peas. These dryland areas will con tinue to produce most of the world's food grains for expanding populations in the years ahead. However, yields are extremely low compared with those of the humid and subhumid regions. In some countries of sub-Saharan Africa and the Near East food grain production per capita has declined significantly during the past decade. Although part of this decline can be attributed to high rates of popu lation growth, periodic drought, and unfavorable agricultural production and marketing policies of the national governments, much of it results from the steady and continuing degradation of aglicultural lands from soil erosion and nutrient depletion and the subsequent loss of soil productivity (FAO, 1986; Dregne, 1989). Many of these dryland areas are typified by a highly fragile natural resource base.