Design, Development and Testing of Shape Shifting Wing Model
Total Page:16
File Type:pdf, Size:1020Kb
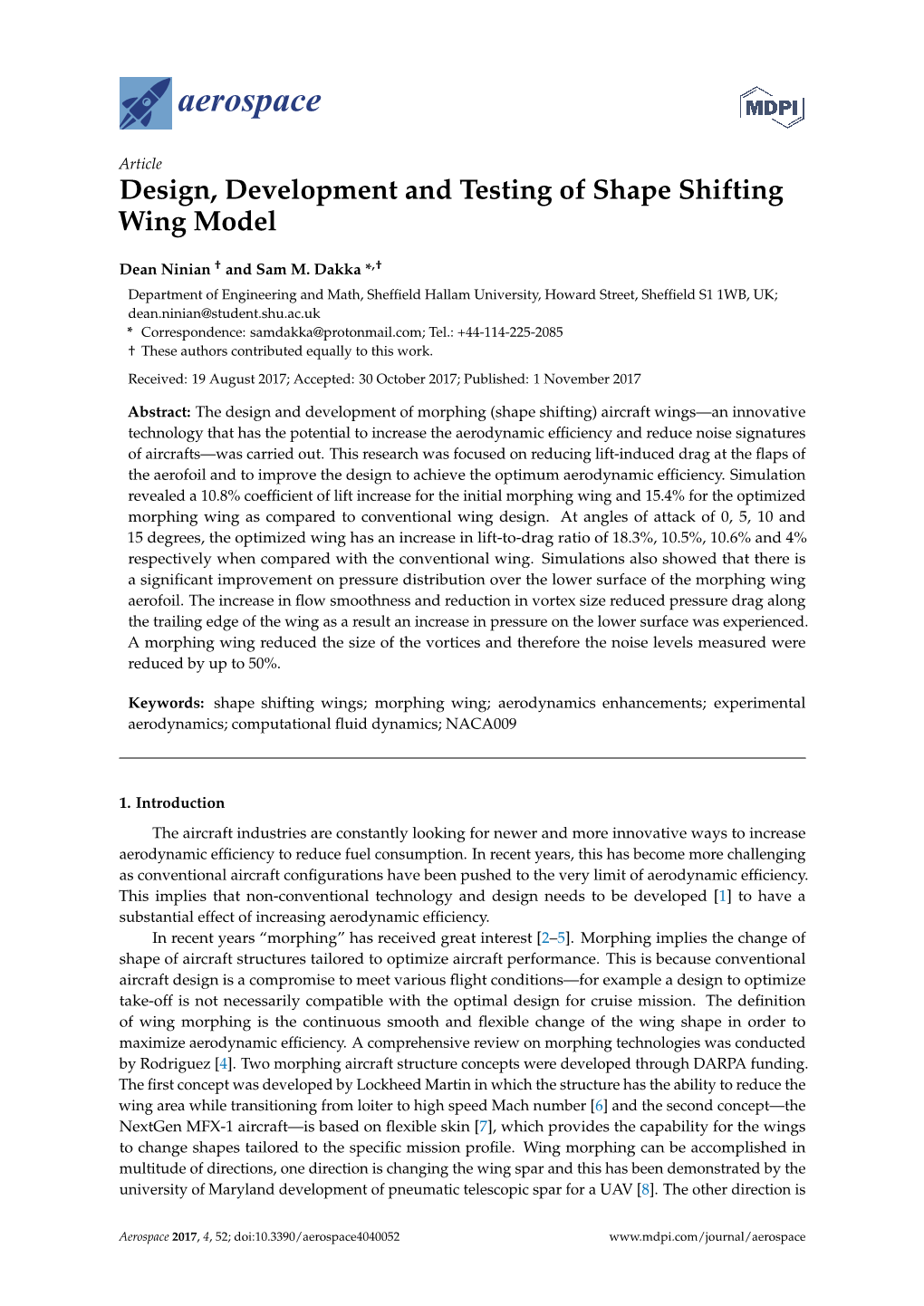
Load more
Recommended publications
-
Flexfloil Shape Adaptive Control Surfaces—Flight Test and Numerical Results
FLEXFLOIL SHAPE ADAPTIVE CONTROL SURFACES—FLIGHT TEST AND NUMERICAL RESULTS Sridhar Kota∗ , Joaquim R. R. A. Martins∗∗ ∗FlexSys Inc. , ∗∗University of Michigan Keywords: FlexFoil, adaptive compliant trailing edge, flight testing, aerostructural optimization Abstract shape-changing control surface technologies has been realized by the ACTE program in which the The U.S Air Force and NASA recently concluded high-lift flaps of the Gulfstream III test aircraft a series of flight tests, including high speed were replaced by a 19-foot spanwise FlexFoilTM (M = 0:85) and acoustic tests of a Gulfstream III variable-geometry control surfaces on each wing, business jet retrofitted with shape adaptive trail- including a 2 ft wide compliant fairings at each ing edge control surfaces under the Adaptive end, developed by FlexSys Inc. The flight tests Compliant Trailing Edge (ACTE) program. The successfully demonstrated the flight-worthiness long-sought goal of practical, seamless, shape- of the variable geometry control surfaces. changing control surface technologies has been Modern aircraft wings and engines have realized by the ACTE program in which the high- reached near-peak levels of efficiency, making lift flaps of the Gulfstream III test aircraft were further improvements exceedingly difficult. The replaced with 23 ft spanwise FlexFoilTM variable next frontier in improving aircraft efficiency is to geometry control surfaces on each wing. The change the shape of the aircraft wing in-flight to flight tests successfully demonstrated the flight- maximize performance under all operating con- worthiness of the variable geometry control sur- ditions. Modern aircraft wing design is a com- faces. We provide an overview of structural and promise between several constraints and flight systems design requirements, test flight envelope conditions with best performance occurring very (including critical design and test points), re- rarely or purely by chance. -
Topology Optimization of Large-Scale 3D Morphing Wing Structures
actuators Article Topology Optimization of Large-Scale 3D Morphing Wing Structures Peter Dørffler Ladegaard Jensen 1,* , Fengwen Wang 1 , Ignazio Dimino 2 and Ole Sigmund 1 1 Department of Mechanical Engineering, Technical University of Denmark, 2800 Kongens Lyngby, Denmark; [email protected] (F.W.); [email protected] (O.S.) 2 Adaptive Structures Technologies, The Italian Aerospace Research Centre, CIRA, Via Maiorise, 81043 Capua, Italy; [email protected] * Correspondence: [email protected] Abstract: This work proposes a systematic topology optimization approach for simultaneously de- signing the morphing functionality and actuation in three-dimensional wing structures. The actuation was modeled by a linear-strain-based expansion in the actuation material. A three-phase material model was employed to represent structural and actuating materials and voids. To ensure both structural stiffness with respect to aerodynamic loading and morphing capabilities, the optimization problem was formulated to minimize structural compliance, while the morphing functionality was enforced by constraining a morphing error between the actual and target wing shape. Moreover, a feature-mapping approach was utilized to constrain and simplify the actuator geometries. A trailing edge wing section was designed to validate the proposed optimization approach. Numerical results demonstrated that three-dimensional optimized wing sections utilize a more advanced structural layout to enhance structural performance while keeping the morphing functionality better than two-dimensional wing ribs. The work presents the first step towards the systematic design of three-dimensional morphing wing sections. Citation: Jensen, P.D.L.; Wang, F.; Dimino, I.; Sigmund, O. Topology Keywords: topology optimization; morphing wing; aerospace design optimization; smart and Optimization of Large-Scale 3D adaptive structures; feature mapping Morphing Wing Structures. -
Design of a Transonic Wing with an Adaptive Morphing Trailing Edge Via Aerostructural Optimization
Design of a Transonic Wing with an Adaptive Morphing Trailing Edge via Aerostructural Optimization David A. Burdettea, Joaquim R. R. A. Martinsa,∗ a University of Michigan, Department of Aerospace Engineering Abstract Novel aircraft configurations and technologies like adaptive morphing trailing edges offer the potential to improve the fuel efficiency of commercial transport aircraft. To accurately quantify the benefits of morphing wing technology for commercial transport aircraft, high-fidelity design optimization that considers both aerodynamic and structural design with a large number of design vari- ables is required. To address this need, we use high-fidelity aerostructural that enables the detailed optimization of wing shape and sizing using hundreds of de- sign variables. We perform a number of multipoint aerostructural optimizations to demonstrate the performance benefits offered by morphing technology and identify how those benefits are enabled. In a comparison of optimizations con- sidering seven flight conditions, the addition of a morphing trailing edge device along the aft 40% of the wing can reduce cruise fuel burn by more than 5%. A large portion of fuel burn reduction due to morphing trailing edges results from a significant reduction in structural weight, enabled by adaptive maneuver load alleviation. We also show that a smaller morphing device along the aft 30% of the wing produces nearly as much fuel burn reduction as the larger morphing device, and that morphing technology is particularly effective for high aspect ratio wings. Keywords: Morphing, Adaptive compliant trailing edge, Wing design, Aerostructural optimization, Common Research Model ∗Corresponding author Preprint submitted to Elsevier August 8, 2018 1. Introduction Increased awareness of environmental concerns and fluctuations in fuel prices in recent years have led the aircraft manufacturing industry to push for improved aircraft fuel efficiency. -
Mission Adaptive Compliant Wing – Design, Fabrication and Flight Test
UNCLASSIFIED/UNLIMITED Mission Adaptive Compliant Wing – Design, Fabrication and Flight Test Sridhar Kota, Russell Osborn, Gregory Ervin, Dragan Maric FlexSys Inc. 2006 Hogback Rd. ,Suite 7 Ann Arbor, MI, U.S.A [email protected] Peter Flick and Donald Paul Air Force Research Laboratory Dayton, OH, U.S.A ABSTRACT This paper provides an overview of the design, fabrication and testing of a variable camber trailing edge for a high-altitude, long-endurance aircraft. The key enabling technology for the lightweight, low-power adaptive trailing edge is due to utilization of elasticity in the underlying structure through implementation of compliant mechanisms. The paper describes flight testing of the “Mission Adaptive Compliant Wing” (MACW) adaptive structure trailing edge flap used in conjunction with a natural laminar flow airfoil. The MACW technology provides lightweight, low-power, variable geometry re-shaping of the upper and lower flap surface with no seams or discontinuities. In this particular study, the airfoil flap system is optimized to maximize the laminar boundary layer extent over a broad lift coefficient range for endurance aircraft applications. The wing was flight tested at full-scale dynamic pressure, full-scale Mach, and reduced-scale Reynolds Numbers on the Scaled Composites White Knight aircraft. Data from flight testing revealed laminar flow was maintained over approximately 60% of the airfoil chord for much of the lift range. Drag results are provided based on a dynamic pressure scaling factor to account for White Knight fuselage and wing interference effects. The expanded “laminar bucket” capability allows the endurance aircraft to significantly extend its range (15% or more) by continuously optimizing the wing L/D throughout the mission. -
Structural Design and Verification of an Innovative Whole Adaptive Variable Camber Wing
This is a repository copy of Structural design and verification of an innovative whole adaptive variable camber wing. White Rose Research Online URL for this paper: http://eprints.whiterose.ac.uk/155098/ Version: Accepted Version Article: Zhao, A, Zou, H, Jin, H et al. (1 more author) (2019) Structural design and verification of an innovative whole adaptive variable camber wing. Aerospace Science and Technology, 89. pp. 11-18. ISSN 1270-9638 https://doi.org/10.1016/j.ast.2019.02.032 © 2019 Published by Elsevier Masson SAS. This manuscript version is made available under the CC-BY-NC-ND 4.0 license http://creativecommons.org/licenses/by-nc-nd/4.0/. Reuse This article is distributed under the terms of the Creative Commons Attribution-NonCommercial-NoDerivs (CC BY-NC-ND) licence. This licence only allows you to download this work and share it with others as long as you credit the authors, but you can’t change the article in any way or use it commercially. More information and the full terms of the licence here: https://creativecommons.org/licenses/ Takedown If you consider content in White Rose Research Online to be in breach of UK law, please notify us by emailing [email protected] including the URL of the record and the reason for the withdrawal request. [email protected] https://eprints.whiterose.ac.uk/ 1 Structural design and verification of an innovative whole adaptive variable camber wing 2 Anmin Zhaoa,b, Hui Zoua, Haichuan Jina, Dongsheng Wena 3 aNational key Laboratory of Human Machine and Environment Engineering, Beihang 4 University, Beijing, 100191, China 5 bNational key laboratory of Computational Fluid Dynamics, Beihang University, Beijing, 6 100191, China 7 Abstract: A whole adaptive variable camber wing (AVCW) equipped with an innovative 8 double rib sheet (DRS) structure is experimentally and numerically studied in this work. -
In-Flight Wingtip Folding: Inspiration from the XB-70 Valkyrie Gaétan X
International Journal of Aviation, Aeronautics, and Masthead Logo Aerospace Volume 6 | Issue 3 Article 7 2019 In-flight Wingtip Folding: Inspiration from the XB-70 Valkyrie Gaétan X. Dussart Cranfield University, [email protected] Mudassir Lone Cranfield University, [email protected] Ciaran O'Rourke Airbus Ltd, [email protected] Thomas Wilson Airbus Ltd, [email protected] Follow this and additional works at: https://commons.erau.edu/ijaaa Part of the Aeronautical Vehicles Commons, Applied Mechanics Commons, and the Aviation and Space Education Commons Scholarly Commons Citation Dussart, G. X., Lone, M., O'Rourke, C., & Wilson, T. (2019). In-flight Wingtip Folding: Inspiration from the XB-70 Valkyrie. International Journal of Aviation, Aeronautics, and Aerospace, 6(3). Retrieved from https://commons.erau.edu/ijaaa/vol6/iss3/7 This Article is brought to you for free and open access by the Journals at Scholarly Commons. It has been accepted for inclusion in International Journal of Aviation, Aeronautics, and Aerospace by an authorized administrator of Scholarly Commons. For more information, please contact [email protected], [email protected]. Dussart et al.: In-flight Wingtip Folding: Inspiration from the XB-70 Valkyrie Introduction To help develop future aircraft technologies, the authors investigated past developments and applications in the field of folding wingtips for inspiration, focusing on the XB-70 Valkyrie. Arguably the most iconic example of folding wingtip capable vehicle, it included the largest moving lifting surfaces ever flown and provides a good insight on the actuator and systems requirement for wingtip folding. Following a justification for incremental aircraft design changes, the authors introduce past and on-going developments in folding wingtip systems for large civil aircraft. -
Optimal Design of Compliant Trailing Edge for Shape Changing
Chinese Journal of Aeronautics Chinese Journal of Aeronautics 21(2008) 187-192 www.elsevier.com/locate/cja Optimal Design of Compliant Trailing Edge for Shape Changing Liu Shili, Ge Wenjie*, Li Shujun School of Mechatronics, Northwestern Polytechnical University, Xi’an 710072, China Received 19 July 2007; accepted 2 January 2008 Abstract Adaptive wings have long used smooth morphing technique of compliant leading and trailing edge to improve their aerodynamic characteristics. This paper introduces a systematic approach to design compliant structures to carry out required shape changes under distributed pressure loads. In order to minimize the deviation of the deformed shape from the target shape, this method uses MATLAB and ANSYS to optimize the distributed compliant mechanisms by way of the ground approach and genetic algorithm (GA) to remove the elements possessive of very low stresses. In the optimization process, many factors should be considered such as airloads, input dis- placements, and geometric nonlinearities. Direct search method is used to locally optimize the dimension and input displacement after the GA optimization. The resultant structure could make its shape change from 0 to 9.3 degrees. The experimental data of the model confirms the feasibility of this approach. Keywords: adaptive wing; compliant mechanism; genetic algorithm; topology optimization; distributed pressure load; geometric nonlin- earity 1 Introduction* changing. Nevertheless, compared to the compliant mechanism, the smart-material-made actuators have As conventional airfoil contours are usually many disadvantages, such as deficient in energy, designed with specific lift coefficients and Mach slow in response, strong in hysteresis, limited by numbers, they could not change in accordance with temperature, and difficult to control too many ac- the environment changing. -
In-Flight Wingtip Folding: Inspiration from the XB-70 Valkyrie
International Journal of Aviation, Aeronautics, and Aerospace Volume 6 Issue 3 Article 7 2019 In-flight Wingtip olding:F Inspiration from the XB-70 Valkyrie Gaétan X. Dussart Cranfield University, [email protected] Mudassir Lone Cranfield University, [email protected] Ciaran O'Rourke Airbus Ltd, [email protected] Thomas Wilson Airbus Ltd, [email protected] Follow this and additional works at: https://commons.erau.edu/ijaaa Part of the Aeronautical Vehicles Commons, Applied Mechanics Commons, and the Aviation and Space Education Commons Scholarly Commons Citation Dussart, G. X., Lone, M., O'Rourke, C., & Wilson, T. (2019). In-flight Wingtip olding:F Inspiration from the XB-70 Valkyrie. International Journal of Aviation, Aeronautics, and Aerospace, 6(3). https://doi.org/ 10.15394/ijaaa.2019.1343 This Article is brought to you for free and open access by the Journals at Scholarly Commons. It has been accepted for inclusion in International Journal of Aviation, Aeronautics, and Aerospace by an authorized administrator of Scholarly Commons. For more information, please contact [email protected]. Dussart et al.: In-flight Wingtip Folding: Inspiration from the XB-70 Valkyrie Introduction To help develop future aircraft technologies, the authors investigated past developments and applications in the field of folding wingtips for inspiration, focusing on the XB-70 Valkyrie. Arguably the most iconic example of folding wingtip capable vehicle, it included the largest moving lifting surfaces ever flown and provides a good insight on the actuator and systems requirement for wingtip folding. Following a justification for incremental aircraft design changes, the authors introduce past and on-going developments in folding wingtip systems for large civil aircraft. -
Aeroelastic Airworthiness Assessment of the Adaptive Compliant Trailing Edge Flaps
AEROELASTIC AIRWORTHINESS ASSESSMENT OF THE ADAPTIVE COMPLIANT TRAILING EDGE FLAPS Claudia Y. Herrera, Aerospace Engineer, and Natalie D. Spivey, Aerospace Engineer NASA Armstrong Flight Research Center, Edwards Air Force Base, California 93523 Shun-fat Lung, Structures Engineer Jacobs Engineering, NASA Armstrong Flight Research Center, Edwards Air Force Base, California 93523 Gregory Ervin FlexSys Inc., Ann Arbor, Michigan 48105 Peter Flick Air Force Research Laboratory, Air Vehicles Directorate, Wright-Patterson Air Force Base, Ohio, 45433 1. ABSTRACT The Adaptive Compliant Trailing Edge (ACTE) demonstrator is a joint task under the National Aeronautics and Space Administration Environmentally Responsible Aviation Project in partnership with the Air Force Research Laboratory and FlexSys, Inc. (Ann Arbor, Michigan). The project goal is to develop advanced technologies that enable environmentally friendly aircraft, such as adaptive compliant technologies. The ACTE demonstrator flight-test program encompassed replacing the Fowler flaps on the SubsoniC Aircraft Testbed, a modified Gulfstream III (Gulfstream Aerospace, Savannah, Georgia) aircraft, with control surfaces developed by FlexSys. The control surfaces developed by FlexSys are a pair of uniquely-designed unconventional flaps to be used as lifting surfaces during flight-testing to validate their structural effectiveness. The unconventional flaps required a multidisciplinary airworthiness assessment to prove they could withstand the prescribed flight envelope. Several challenges were posed due to the large deflections experienced by the structure, requiring non-linear analysis methods. The aeroelastic assessment necessitated both conventional and extensive testing and analysis methods. A series of ground vibration tests (GVTs) were conducted to provide modal characteristics to validate and update finite element models (FEMs) used for the flutter analyses for a subset of the various flight configurations. -
Multiobjective Optimization for the Aero-Structural Design of Adaptive Compliant Wing Devices
applied sciences Article Multiobjective Optimization for the Aero-Structural Design of Adaptive Compliant Wing Devices Alessandro De Gaspari Department of Aerospace Science and Technology, Politecnico di Milano, Via La Masa 34, 20156 Milano, Italy; [email protected] Received: 14 August 2020; Accepted: 10 September 2020; Published: 13 September 2020 Abstract: The design of morphing structures must combine conflicting structural requirements and multiple load conditions that are related to the aerodynamic shapes aimed at optimizing aircraft performance. This article proposes a multilevel approach for the design of adaptive compliant wing devices. A set of aerodynamic shapes, and associated their loads, is defined by a shape optimization, coupled with a three-dimensional parametric technique, that can identify only feasible shape changes due to the morphing. A topology and sizing multiobjective optimization drives the Pareto-optimal structural design of the compliant structure, which is able to deform itself to match, once actuated, all of the previously defined aerodynamic shapes. Next two design levels produce a more detailed solution which is extended until the definition of the complete device. A 90 pax, twin prop green regional aircraft is used as an innovative aircraft demonstration platform for the design of the morphing droop nose to be installed on the wing. The results show the structural capabilities of this device in terms of the external shape quality and the strain requirements. This work enables the validation of the design method and prove the functionality of compliant structures when accounting for the aeroelastic effects due to the interaction with the wing-box. Keywords: morphing; wing devices; multiobjective optimization; compliant structures; pareto- optimal; aeroelasticity 1. -
Fuel Burn Reduction Through Wing Morphing,” Encyclopedia of Aerospace Engineering, Green Aviation, Wiley, 2016, Pp
Please cite this document as: Martins, Joaquim R. R. A., ”Fuel Burn Reduction Through Wing Morphing,” Encyclopedia of Aerospace Engineering, Green Aviation, Wiley, 2016, pp. 75–79. doi:10.1002/9780470686652.eae1007. This document can be found at: http://mdolab.engin.umich.edu. Fuel Burn Reduction Through Wing Morphing Joaquim R. R. A. Martins1 Abstract Changing the shape of aircraft is beneficial because they operate in a wide range of flight con- ditions with conflicting requirements and the concomitant variations in aircraft performance. This chapter focuses on morphing systems that contribute to reducing fuel burn for commercial transport aircraft. We start with a summary of how morphing can reduce fuel burn from the system-level viewpoint, following which we analyze the three wing-morphing modes: planform, out of plane, and airfoil. For each of these, we review morphing mechanisms that are already in place, such as high-lift systems, and provide an outlook on how more advanced morphing technologies can further reduce fuel burn. The impact of any morph- ing system must be quantified by considering all the disciplines involved, and a clean-sheet design should be done to realize the full potential. The most promising type of morphing for the near future is variable trailing-edge camber, which can tailor the aerodynamic performance and more effectively alleviate maneu- ver load. Research on new materials and morphing mechanisms will make morphing systems lighter, more energy efficient, and more economical. It is just a question of time before we see aircraft wings that exhibit morphing capabilities that seem impossible today. 1 Introduction The word “morphing” originates from the Greek word metamorphosis, which translates to “transformation.” Morphing started being used as a term in computer graphics to mean a smooth transformation from one image into another. -
In-Flight Folding Wingtip System
In-flight folding wingtip system: inspiration from the XB-70 Valkyrie Gaétan Dussart∗ and Mudassir Lone† Cranfield University, Dynamic Simulation and Control Group Cranfield, Bedfordshire, MK43 0AL, United Kingdom Ciaran O’Rourke‡ and Thomas Wilson§ Airbus Operations Ltd Filton, Bristol, BS34 7PA, United Kingdom Wingtip folding can be used to extend aircraft wingspan, allowing designers to take advan- tage of reduced induced drag whilst respecting ground operational limitations. Such devices can also be used in-flight for a variety of other benefits including load alleviation and flight control. The majority of in-flight folding research takes inspiration in past developments made on the XB-70 Valkyrie, which used the folding devices for stability and lift performance benefits. In this paper, the authors investigate the capabilities of the folding wingtip system and potential scaling to large civil aircraft. Manufacturing details are used to size the actuators whilst the aerodynamic loading acting on the wingtip hinges is found from flight test results. Dimensions and aerodynamic loading at cruise of a set of conventional civil aircraft wing are used to evalu- ate the scaling potential of the system for controlled in-flight folding. An estimate of the weight penalty due to the folding device is also given and compared to structural weight savings on the XB-70. The results presented herein help in the evaluation of conventional actuator limits for in-flight folding using arguably the most inspiring military example of wingtip folding so far. I. Project Motivation t is well known that a well designed High Aspect Ratio Wings (HARW) will have better aerodynamic performances Ithan currently used conventional swept wings.