New Voxel-Based Data Format FAV for Seamless 3D Data Flow to 3D Printers
Total Page:16
File Type:pdf, Size:1020Kb
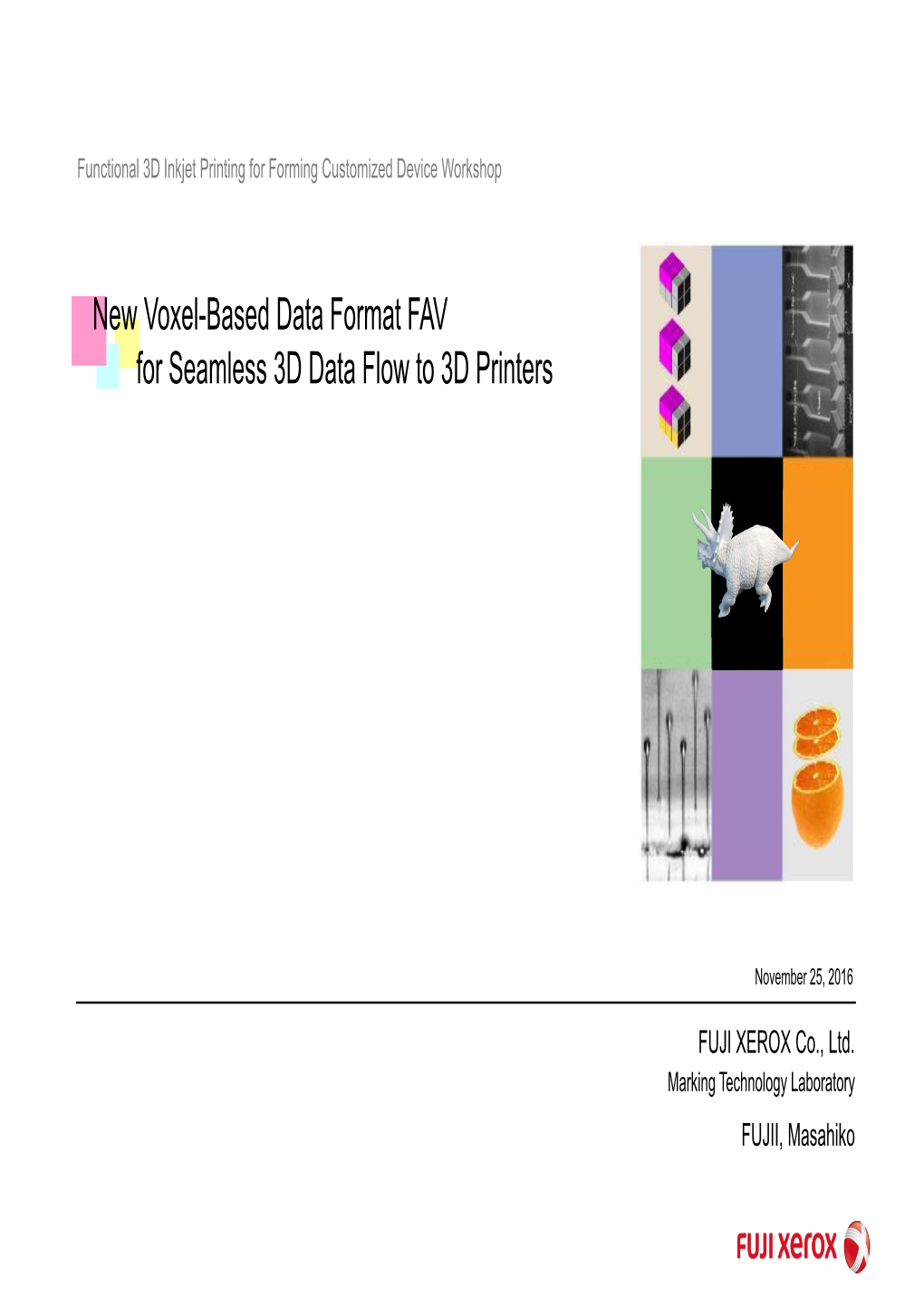
Load more
Recommended publications
-
Projet™ 6000 3D Professional Printer
ProJet™ 6000 3D Professional Printer Facility Requirements Guide Original Instructions Rev. D, P/N 40-D095 1. Table of Contents . 2 1.1 02.0 What is a Facility Requirements Guide . 3 1.2 03.0 Symbols Used in this Guide . 4 1.3 04.0 The ProJet™ 6000 System . 5 1.4 05.0 Facility Guidelines . 6 1.4.1 05.1 Moving Equipment and Access for System Installation . 7 1.4.2 05.2 ProJet™ 6000 Physical Dimensions . 8 1.4.3 05.3 Floor Specifications . 11 1.4.4 05.4 Room Size . 12 1.4.5 05.5 Electrical Requirements . 13 1.4.6 05.6 Client Workstation Requirements to Operate 3DManage . 14 1.4.7 05.7 Network Interface . 15 1.4.8 05.8 Safety Information . 16 1.4.9 05.9 Print Material Handling and Safety . 17 1.5 06.0 Operating Environment . 20 1.5.1 06.1 Air Quality and Temperature . 21 1.5.2 06.2 Humidity . 22 1.5.3 06.3 Lighting . 23 1.5.4 06.4 Vibration and Shock . 24 1.6 07.0 Limitations of Liability . 25 1.7 08.0 Safety Notice . 26 1.8 09.0 Thank You . 27 1.9 10.0 Contacting 3D Systems . 28 1.10 11.0 Ancillary Supplies and Equipment . 30 1.11 12.0 Initial Site Survey Checklist . 31 1.12 13.0 3D Connect Service . 33 1.13 14.0 Pre-Installation Checklist . 34 Table of Contents 02.0 What is a Facility Requirements Guide 03.0 Symbols Used in this Guide 04.0 The ProJet™ 6000 System 05.0 Facility Guidelines 05.1 Moving Equipment and Access for System Installation 05.2 ProJet™ 6000 Physical Dimensions 05.3 Floor Specifications 05.4 Room Size 05.5 Electrical Requirements 05.6 Client Workstation Requirements to Operate 3DManage 05.7 Network Interface 05.8 Safety -
Luna Moth: Supporting Creativity in the Cloud
Pedro Alfaiate Instituto Superior Técnico / Luna Moth INESC-ID Inês Caetano Instituto Superior Técnico / INESC-ID Supporting Creativity in the Cloud António Leitão Instituto Superior Técnico / INESC-ID 1 ABSTRACT Algorithmic design allows architects to design using a programming-based approach. Current algo- 1 Migration from desktop application rithmic design environments are based on existing computer-aided design applications or building to the cloud. information modeling applications, such as AutoCAD, Rhinoceros 3D, or Revit, which, due to their complexity, fail to give architects the immediate feedback they need to explore algorithmic design. In addition, they do not address the current trend of moving applications to the cloud to improve their availability. To address these problems, we propose a software architecture for an algorithmic design inte- grated development environment (IDE), based on web technologies, that is more interactive than competing algorithmic design IDEs. Besides providing an intuitive editing interface which facilitates programming tasks for architects, its performance can be an order of magnitude faster than current aalgorithmic design IDEs, thus supporting real-time feedback with more complex algorithmic design programs. Moreover, our solution also allows architects to export the generated model to their preferred computer-aided design applications. This results in an algorithmic design environment that is accessible from any computer, while offering an interactive editing environment that inte- grates into the architect’s workflow. 72 INTRODUCTION programming languages that also support traceability between Throughout the years, computers have been gaining more ground the program and the model: when the user selects a component in the field of architecture. In the beginning, they were only used in the program, the corresponding 3D model components are for creating technical drawings using computer-aided design highlighted. -
3D Modeling: Surfaces
CS 430/536 Computer Graphics I Overview • 3D model representations 3D Modeling: • Mesh formats Surfaces • Bicubic surfaces • Bezier surfaces Week 8, Lecture 16 • Normals to surfaces David Breen, William Regli and Maxim Peysakhov • Direct surface rendering Geometric and Intelligent Computing Laboratory Department of Computer Science Drexel University 1 2 http://gicl.cs.drexel.edu 1994 Foley/VanDam/Finer/Huges/Phillips ICG 3D Modeling Representing 3D Objects • 3D Representations • Exact • Approximate – Wireframe models – Surface Models – Wireframe – Facet / Mesh – Solid Models – Parametric • Just surfaces – Meshes and Polygon soups – Voxel/Volume models Surface – Voxel – Decomposition-based – Solid Model • Volume info • Octrees, voxels • CSG • Modeling in 3D – Constructive Solid Geometry (CSG), • BRep Breps and feature-based • Implicit Solid Modeling 3 4 Negatives when Representing 3D Objects Representing 3D Objects • Exact • Approximate • Exact • Approximate – Complex data structures – Lossy – Precise model of – A discretization of – Expensive algorithms – Data structure sizes can object topology the 3D object – Wide variety of formats, get HUGE, if you want each with subtle nuances good fidelity – Mathematically – Use simple – Hard to acquire data – Easy to break (i.e. cracks represent all primitives to – Translation required for can appear) rendering – Not good for certain geometry model topology applications • Lots of interpolation and and geometry guess work 5 6 1 Positives when Exact Representations Representing 3D Objects • Exact -
SLS Systems User's Guide
S SLS ™ process user’s guide Thank-you for purchasing 3D Systems® SLS® equipment and DuraForm® materials. Before you start building parts in your SLS™ process facility, please read this guide carefully to enjoy optimum process performance and longer equipment service life. Original Instructions CONTENTS Contents ` About This Guide . 2 ` IRS & IPC. 133 ` Safety . 9 ` SLS System . 180 ` SLS Process . .43 ` BOS . 208 ` Prepare to Build . .55 ` Contacting 3D Systems . 242 ` Build Parts. .73 ` Glossary . 245 ` Break Out Parts . .90 ` Index. 268 ` RCM . .101 L In accordance with laboratory equipment safety standards (EN61010-1, Sect. 5.4.4). If this equipment is used in a manner not specified by the manufacturer, protection provided by the equipment may be impaired. Observe all warning labels, and conform to all safety rules described in this manual. Document 23348-M12-00 Revision B August 2017 Copyright © 2006 by 3D Systems Corporation. All rights reserved. 3D Systems, the 3D logo, Sinterstation, sPro, SLS, and DuraForm are registered trademarks of 3D Systems, Inc. Other trademarks are the property of their respective owners. SLS process user’s guide ABOUT THIS GUIDE This guide describes how to create finished SLS parts made of DuraForm® PA plastic powder laser sintering (LS) material using 3D Systems’ sPro SLS® system and SLS equipment. ` What’s Inside?. .3 ` Instruction Formats . 6 ` Hazard Warnings. .5 ` Other Useful Documents . 7 SLS process 3 ABOUT THIS GUIDE user’s guide what’s inside? What’s Inside? This SLS Process User’s Guide includes the SLS Process Procedures sections summarized below. General safety The instructions in these four sections step you guidelines are presented first. -
DMP Factory 500
DMP Factory 500 Scalable metal additive manufacturing for seamless large parts GF Machining Solutions : all about you When all you need is everything, it’s good to know that there is one company that you can count on to deliver complete solutions and services. From world-class electrical discharge machines (EDM), Laser texturing and Additive Manufacturing through to first-class Milling and Spindles, Tooling, Automation and software systems - all backed by unrivalled customer service and support - we, through our AgieCharmilles, Microlution, Mikron Mill, Liechti, Step-Tec and System 3R technologies, help you raise your game and increase your competitive edge. 3D Systems : Making 3D production real 3D Systems is a global 3D solutions company focused on connecting our customers with the expertise and digital manufacturing workflow required to meet their business, design and engineering needs. From digitalization, design and simulation through manufacturing, inspection and management, our comprehensive portfolio of technologies provides a seamless, customizable workflow designed to optimize products and processes while accelerating outcomes. With advanced hardware, software and materials as well as on demand manufacturing services and a global team of experts, we are on a mission to transform businesses through manufacturing innovation. 2 Market introduction 4 Contents Meet the AM factory 6 Modular concept for scalability 8 Integrating additive manufacturing 9 with traditional technologies The vacuum chamber concept 10 3DXpert™ 11 Build higher -
History of Additive Manufacturing
Wohlers Report 2015 History of Additive Manufacturing History of additive This 35-page document is a part of Wohlers Report 2015 and was created for its readers. The document chronicles the history of additive manufacturing manufacturing (AM) and 3D printing, beginning with the initial by Terry Wohlers and Tim Gornet commercialization of stereolithography in 1987 to April 2014. Developments from April 2014 through March 2015 are available in the complete 314-page version of the report. An analysis of AM, from the earliest inventions in the 1960s to the 1990s, is included in the final several pages of this document. Additive manufacturing first emerged in 1987 with stereolithography (SL) from 3D Systems, a process that solidifies thin layers of ultraviolet (UV) light-sensitive liquid polymer using a laser. The SLA-1, the first commercially available AM system in the world, was the precursor of the once popular SLA 250 machine. (SLA stands for StereoLithography Apparatus.) The Viper SLA product from 3D Systems replaced the SLA 250 many years ago. In 1988, 3D Systems and Ciba-Geigy partnered in SL materials development and commercialized the first-generation acrylate resins. DuPont’s Somos stereolithography machine and materials were developed the same year. Loctite also entered the SL resin business in the late 1980s, but remained in the industry only until 1993. After 3D Systems commercialized SL in the U.S., Japan’s NTT Data CMET and Sony/D-MEC commercialized versions of stereolithography in 1988 and 1989, respectively. NTT Data CMET (now a part of Teijin Seiki, a subsidiary of Nabtesco) called its system Solid Object Ultraviolet Plotter (SOUP), while Sony/D-MEC (now D-MEC) called its product Solid Creation System (SCS). -
Full Body 3D Scanning
3D Photography: Final Project Report Full Body 3D Scanning Sam Calabrese Abhishek Gandhi Changyin Zhou fsmc2171, asg2160, [email protected] Figure 1: Our model is a dancer. We capture his full-body 3D model by combining image-based methods and range scanner, and then do an animation of dancing. Abstract Compared with most laser scanners, image-based methods using triangulation principles are much faster and able to provide real- In this project, we are going to build a high-resolution full-body time 3D sensing. These methods include depth from motion [Aloi- 3D model of a live person by combining image-based methods and monos and Spetsakis 1989], shape from shading [Zhang et al. laser scanner methods. A Leica 3D range scanner is used to obtain 1999], depth from defocus/focus [Nayar et al. 1996][Watanabe and four accurate range data of the body from four different perspec- Nayar 1998][Schechner and Kiryati 2000][Zhou and Lin 2007], and tives. We hire a professional model and adopt many measures to structure from stereo [Dhond and Aggarwal 1989]. They often re- minimize the movement during the long laser-scanning. The scan quire the object surface to be textured, non-textured, or lambertian. data is then sequently processed by Cyclone, MeshLab, Scanalyze, These requirements often make them impractical in many cases. VRIP, PlyCrunch and 3Ds Max to obtain our final mesh. We take In addition, image-based methods usually cannot give a precision three images of the face from frontal and left/right side views, and depth estimation since they do patch-based analysis. -
Production of Drug Delivery Systems Using Fused Filament Fabrication: a Systematic Review
Review Production of Drug Delivery Systems Using Fused Filament Fabrication: A Systematic Review Bahaa Shaqour 1,2,*, Aseel Samaro 3, Bart Verleije 1, Koen Beyers 1, Chris Vervaet 3, and Paul Cos 2 1 Voxdale bv, Bijkhoevelaan 32C, 2110 Wijnegem, Belgium; [email protected] (B.V.); [email protected] (K.B.) 2 Laboratory for Microbiology, Parasitology and Hygiene (LMPH), Faculty of Pharmaceutical, Biomedical and Veterinary Sciences, University of Antwerp, Universiteitsplein 1 S.7, 2610 Antwerp, Belgium; [email protected] 3 Laboratory of Pharmaceutical Technology, Department of Pharmaceutics, Ghent University, Ottergemsesteenweg 460, 9000 Ghent, Belgium; [email protected] (A.S.); [email protected] (C.V.) * Correspondence: [email protected] Received: 4 May 2020; Accepted: 3 June 2020; Published: 5 June 2020 Abstract: Fused filament fabrication (FFF) 3D printing technology is widely used in many fields. For almost a decade, medical researchers have been exploring the potential use of this technology for improving the healthcare sector. Advances in personalized medicine have been more achievable due to the applicability of producing drug delivery devices, which are explicitly designed based on patients’ needs. For the production of these devices, a filament—which is the feedstock for the FFF 3D printer—consists of a carrier polymer (or polymers) and a loaded active pharmaceutical ingredient (API). This systematic review of the literature investigates the most widely used approaches for producing drug‐loaded filaments. It also focusses on several factors, such as the polymeric carrier and the drug, loading capacity and homogeneity, processing conditions, and the intended applications. This review concludes that the filament preparation method has a significant effect on both the drug homogeneity within the polymeric carrier and drug loading efficiency. -
Bonus Ch. 2 More Modeling Techniques
Bonus Ch. 2 More Modeling Techniques When it comes to modeling in modo, the sky is the limit. This book is designed to show you all of the techniques available to you, through written word and visual examples on the DVD. This chapter will take you into another project, in which you’ll model a landscape. From there, you’ll texture it, and later you’ll add the environment. You’ll see how modo’s micro polygon displacement works and how powerful it is. From there, you’ll create a cool toy gun. The techniques used in this project will show you how to create small details that make the model come to life. Then, you’ll learn to texture the toy gun to look like real plastic. Building a Landscape Landscapes traditionally have been a chore for 3D artists. This is because to prop- erly create them, you need a lot of geometry. A lot of geometry means a lot of polygons, and a lot of polygons means a lot of render time. But the team at Luxology has introduced micro polygon displacement in modo 201/202, allow- ing you to create and work with simple objects, but render with millions of poly- gons. How is this possible? The micro polygon displacement feature generates additional polygons at render time. The goal is that finer details can be achieved without physically modeling them into the base object. You can then add to the details achieved through micro poly displacements with modo’s bump map capabilities and generate some terrific-looking models. -
Guide to Selective Laser Sintering (SLS) 3D Printing
WHITE PAPER Guide to Selective Laser Sintering (SLS) 3D Printing Selective laser sintering (SLS) 3D printing is trusted by engineers and manufacturers across different industries for its ability to produce strong, functional parts. In this white paper, we’ll cover the selective laser sintering process, the different systems and materials available on the market, the workflow for using SLS printers, the various applications, and when to consider using SLS 3D printing over other additive and traditional manufacturing methods. January 2021 | formlabs.com Contents What is Selective Laser Sintering 3D Printing? . 3 How SLS 3D Printing Works . 4 A Brief History of SLS 3D Printing . 7 Types of SLS 3D Printers . 7 Traditional Industrial SLS 3D Printers .............................7 Fuse 1: The First Benchtop Industrial SLS 3D Printer ................8 Comparison of SLS 3D Printers ..................................9 SLS 3D Printing Materials . 10 SLS Nylon 12 Material Properties ................................ 10 The SLS 3D Printing Workflow . 11 1. Design and Prepare the File ...................................11 2. Prepare the Printer ..........................................11 3. Print ...................................................... 12 4. Part Recovery and Post-Processing ........................... 13 5. Additional Post-Processing .................................. 14 Why Choose SLS 3D Printing? . 15 Design Freedom ............................................. 15 High Productivity and Throughput .............................. 16 -
Digital Sculpting with Zbrush
DIGITAL SCULPTING WITH ZBRUSH Vincent Wang ENGL 2089 Discourse Analysis 2 ZBrush Analysis Table of Contents Context ........................................................................................................................... 3 Process ........................................................................................................................... 5 Analysis ........................................................................................................................ 13 Application .................................................................................................................. 27 Activity .......................................................................................................................... 32 Works Cited .................................................................................................................. 35 3 Context ZBrush was created by the Pixologic Inc., which was founded by Ofer Alon and Jack Rimokh (Graphics). It was first presented in 1999 at SIGGRAPH (Graphics). Version 1.5 was unveiled at the MacWorld Expo 2002 in New York and SIGGRAPH 2002 in San Antonio (Graphics). Pixologic, the company describes the 3D modeling software as a “digital sculpting and painting program that has revolutionized the 3D industry…” (Pixologic). It utilizes familiar real-world tools in a digital environment, getting rid of steep learning curves and allowing the user to be freely creative instead of figuring out all the technical details. 3D models that are created in -
Modeling of Filament Deposition Rapid Prototyping Process with a Closed Form Solution Steven Leon Devlin Iowa State University
Iowa State University Capstones, Theses and Graduate Theses and Dissertations Dissertations 2017 Modeling of filament deposition rapid prototyping process with a closed form solution Steven Leon Devlin Iowa State University Follow this and additional works at: https://lib.dr.iastate.edu/etd Part of the Other Education Commons Recommended Citation Devlin, Steven Leon, "Modeling of filament deposition rapid prototyping process with a closed form solution" (2017). Graduate Theses and Dissertations. 16121. https://lib.dr.iastate.edu/etd/16121 This Dissertation is brought to you for free and open access by the Iowa State University Capstones, Theses and Dissertations at Iowa State University Digital Repository. It has been accepted for inclusion in Graduate Theses and Dissertations by an authorized administrator of Iowa State University Digital Repository. For more information, please contact [email protected]. Modeling of filament deposition rapid prototyping process with a closed form solution by Steven Leon Devlin A dissertation submitted to the graduate faculty in partial fulfillment of the requirements for the degree of DOCTOR OF PHILOSOPHY Major: Industrial and Agricultural Technology Program of Study Committee: David Grewell, Major Professor Matthew Charles Frank Steven A. Freeman Gretchen Ann Mosher W. Robert Stephenson The student author, whose presentation of the scholarship herein was approved by the program of study committee, is solely responsible for the content of this dissertation. The Graduate College will ensure this dissertation is globally accessible and will not permit alterations after a degree is conferred. Iowa State University Ames, Iowa 2017 Copyright © Steven Leon Devlin, 2017. All rights reserved. ii DEDICATION This dissertation is dedicated to my parents, the late Judith L.