Secondary-Electron-Emission Properties of Conducting Surfaces with Application to Multistage Depressed Collectors for Microwave Amplifiers
Total Page:16
File Type:pdf, Size:1020Kb
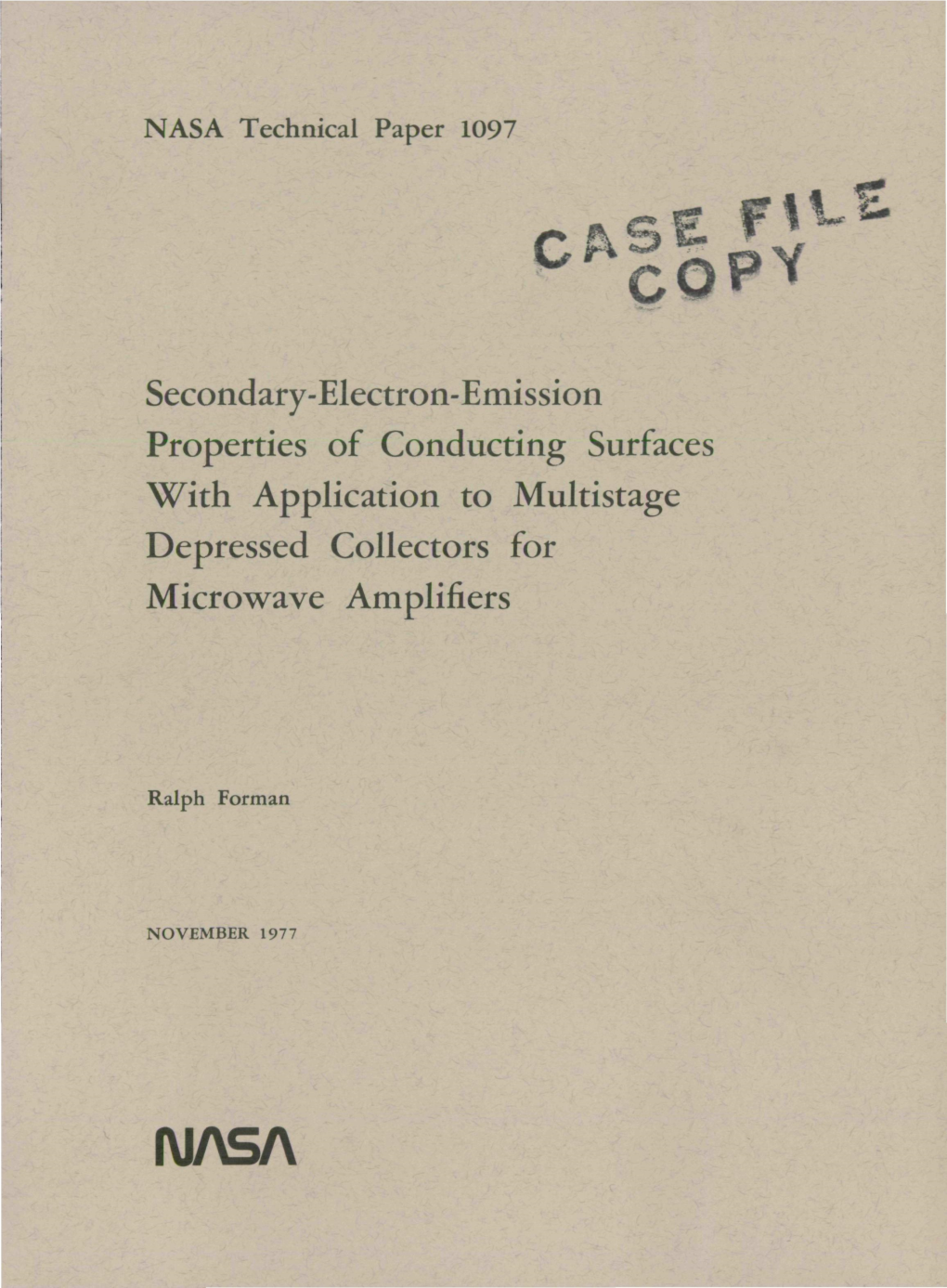
Load more
Recommended publications
-
Measurements and Studies of Secondary Electron Emission of Diamond Amplified Photocathode
BNL-81607-2008-IR C-A/APl#328 October 2008 Measurements and Studies of Secondary Electron Emission of Diamond Amplified Photocathode Qiong Wu Collider-Accelerator Department Brookhaven National Laboratory Upton, NY 11973 Notice: This document bas been authorized by employees of Brookhaven Science Associates, LLC under Contract No. DE-AC02-98CH10886 with the US.Department of Energy. Tbe United States Government retains a non- exclusive, paid-up, irrevocable, world-wide license to publish or reproduce the published form ofthis document, or allow others to do so, for United States Government purposes. MEASUREMENTSAND STUDIES OF SECONDARY ELECTRONEMISSION OF DIAMONDAMPLIFIED PHOTOCATHODE Qiong Wu September, 2008 CONTENTS 1 Introduction .......................................................................................................... 1 1.1 The Diamond Amplified Photocathode (DAF') hoject .................................... 1 1.2 Advantages of diamond for amplified photocathodes ...................................... 4 1.2.1 Wide Band Gq ..... ....................................... 5 1.2.2 Best Rigidiiy ..................... ............ 6 1.2.3 Highest Thermal Conducfivity ................................................................................................ 7 1.2.4 Very high Mobility and Sahrralion Velocity............ ....................... ....8 2 DAP Design ........................................................................................................ 10 2.1 vacuum .......................................................................................................... -
Abstract an Introduction to the Physics and Applications Of
Abstract An Introduction To The Physics And Applications Of Electron Sources Kevin L. Jensen Naval Research Laboratory Models of thermal, field, photo, and secondary emission, as well as space charge limited current flow, have existed since the 1920’s. With the realization that such sources were crucial to Radar and communications, research in harnessing their capabilities greatly accelerated, and now they are key components of cutting edge applications such as High Power Microwave generation and x-ray Free Electron Lasers. Although the processes behind the emission mechanisms (namely, heat, electric field, photoemission effect, and ejection of secondaries due to a high energy primary beam) appear distinct, they can all be understood collectively using simple models from quantum mechanics, condensed matter physics, and electrostatics. A description of the theoretical models and some history behind each mechanism, examples of the kinds of emitters that employ those mechanisms, and the challenges to utilizing the beams generated by various electron source candidates (particularly with respect to beam parameters such as current density, space charge, emittance, and brightness) will be covered. A full description of the canonical emission equations of thermal (Richardson), field (Fowler-Nordheim), photo (Fowler-DuBridge), and secondary (Young) equations is given – but even more interestingly, a demonstration of how the equations are fundamentally related is explored. Processes that affect emission, such as electrostatic shielding, coatings, space charge (Child-Langmuir), and complications due to material properties (metal versus semiconductor) shall be described. Biographical Summary Kevin L. Jensen is a theoretical physicist whose research concerns emission properties of electron sources, particularly cold cathodes and photocathodes, but also thermal and secondary sources, for vacuum nanoelectronics, space-based applications, high power microwave generation, and particle accelerators and Free Electron Lasers. -
Thermionic Emission
Gas Discharge Fundamentals Fall, 2017 Kyoung-Jae Chung Department of Nuclear Engineering Seoul National University Thermionic emission Theoretically, the current density, , of electrons emitted from a cathode at an absolute temperature, (K), is given by: = / Richardson-Dushman equation 2 − Work function (eV) Schottky effect (field enhanced thermionic emission): For a constant temperature, the current still slowly increases with the applied extraction potential by lowering the surface barrier. = exp 4 2 − − 0 Space charge limited current : When the external electric field is not sufficiently high, the emitted electron current density is limited by space charge. The space charge limited current is determined by the extraction voltage and independent of the cathode current. Emission (source) limited current: When the external electric field is sufficiently high, the saturation emission electron current is determined by the cathode temperature. 2/29 Radiation Source Engineering, Fall 2017 Secondary electron emission (SEE) Electrons, ions or neutral particles cause secondary electron emission through different physical processes. The secondary electron emission is described by the secondary emission coefficient, , which is defined as the number of secondaries produced per an incident primary for normal incidence. = Since depends on the state of the surface, e.g. depending on the surface film, there is an extremely wide variation in the measured values. SEE by ion impact ( ) SEE by electron impact ( ) 3/29 Radiation Source Engineering, Fall 2017 Secondary electron emission (SEE) The coefficient of the secondary emission for a proton incident on a gold-plated tungsten filament with an energy of 1.6-15 keV is given by = (1.06 ± 0.01) / Ep is the proton energy in keV 1 2 The dependence of SEE on the incidence angle is given approximately by a sec law. -
Ultrafast Secondary Emission 2D X-Ray Imaging Detectors
TRNT _^______—J WIS-91/74/Oct.-PH Ultrafast Secondary Emission 2D X-ray Imaging Detectors A. Akkerman,1 A. Breskin, R. Chechik,2 V. Elkind, I. FVumkin3 and I. Gibrekhterman The Weizmann Institute of Science 76100 Rehovot, Israel Presented at the European Workshop on X-ray Detectors for Synchrotron Radiation Sources Aussois, France, September 30-October 4, 1991 Also Soreq Research Center, Yavne, Israel The Hettie H. Heinemann Research Fellow Technion. Haifa, Israel Ultra fast Secondary Emission 2D X-ray Imaging Detectors A. Akkerman,1 A. Breskin, R. Chechik,2 V. Elkind, I. Frumkin3 and I. Gibrekhterman The Weizmann Institute of Science 76100 Rehovot, Israel Abstract We describe a new method for subnanosecond, parallax-tree, high accuracy X-ray imaging at high photon flux. X-rays are ronverted in thin Csl layers. Secondary emitted electrons are amplified in multistage electron multipliers, operating at low gas pressures (10-40 Torr). Introduction Fast and accurate large area X-ray imaging is requested in many applications in basic and applied re search. Examples are particle identification with Transition Radiation, plasma diagnostics, medical or indus trial radiography and X-ray diffraction experiments with high luminosity Synchrotron Radiation Sources. Gaseous wire chambers, traditionally used for X-ray imaging1' over a large area, are often too slow (100 ns typical resolution) and suffer from parallax errors in localization, due to different photon absorption depths in the detection volume. Space charge effects limit the counting rate of traditional gaseous detectors. Re cently developed gaseous ji-strip detectors2* are also based on photon conversion in the gas, and therefore suffer from the same limitations. -
Photomultiplier Tubes 1)-5)
CHAPTER 2 BASIC PRINCIPLES OF PHOTOMULTIPLIER TUBES 1)-5) A photomultiplier tube is a vacuum tube consisting of an input window, a photocathode, focusing electrodes, an electron multiplier and an anode usu- ally sealed into an evacuated glass tube. Figure 2-1 shows the schematic construction of a photomultiplier tube. FOCUSING ELECTRODE SECONDARY ELECTRON LAST DYNODE STEM PIN VACUUM (~10P-4) DIRECTION e- OF LIGHT FACEPLATE STEM ELECTRON MULTIPLIER ANODE (DYNODES) PHOTOCATHODE THBV3_0201EA Figure 2-1: Construction of a photomultiplier tube Light which enters a photomultiplier tube is detected and produces an output signal through the following processes. (1) Light passes through the input window. (2) Light excites the electrons in the photocathode so that photoelec- trons are emitted into the vacuum (external photoelectric effect). (3) Photoelectrons are accelerated and focused by the focusing elec- trode onto the first dynode where they are multiplied by means of secondary electron emission. This secondary emission is repeated at each of the successive dynodes. (4) The multiplied secondary electrons emitted from the last dynode are finally collected by the anode. This chapter describes the principles of photoelectron emission, electron tra- jectory, and the design and function of electron multipliers. The electron multi- pliers used for photomultiplier tubes are classified into two types: normal dis- crete dynodes consisting of multiple stages and continuous dynodes such as mi- crochannel plates. Since both types of dynodes differ considerably in operating principle, photomultiplier tubes using microchannel plates (MCP-PMTs) are separately described in Chapter 10. Furthermore, electron multipliers for vari- ous particle beams and ion detectors are discussed in Chapter 12. -
THE IMPORTANCE of ACCURATE COMPUTATION of SECONDARY ELECTRON EMISSION for MODELING SPACECRAFT CHARGING Abstract
View metadata, citation and similar papers at core.ac.uk brought to you by CORE provided by DigitalCommons@USU THE IMPORTANCE OF ACCURATE COMPUTATION OF SECONDARY ELECTRON EMISSION FOR MODELING SPACECRAFT CHARGING S. Clerc, Alcatel Space, 100 boulevard du Midi, Cannes la Bocca, FRANCE, tel / fax: +33(0) 492 926 052 / 970, [email protected] J.R. Dennison, C.D. Thomson, Physics Department UMC 4415 Utah State University Logan, UT 84322-4415 Office: (435)797-2936 Lab: (435) 797-0925 Abstract Secondary electron emission is a critical contributor to the current balance in spacecraft charging. Spacecraft charging codes use a parameterized expression for the secondary electron yield d(Eo) as a function of incident electron energy Eo. Simple three-step physics models of the electron penetration, transport and emission from a solid are typically expressed in terms of the incident electron penetration depth at normal incidence or range R(Eo ), and the mean free path of the n1 secondary electron, l(E). We recall classical models for the range R(Eo): a power law expression of the form b1Eo , n1 n2 and a more general empirical bi-exponential expression R(Eo) = b1Eo +b2Eo . Expressions are developed that relate the theoretical fitting parameters (l, b1, b2, n1 and n2) to experimental terms (the energy Emax at the maximum secondary electron yield dmax, the first and second crossover energies E1 and E2, and the asymptotic limits for d(Eo ® ¥)). In most models, the yield is the result of an integral along the path length of incident electrons. Special care must be taken when computing this integral. -
Leptonic Secondary Emission in a Hadronic Microquasar Model
A&A 476, 9–15 (2007) Astronomy DOI: 10.1051/0004-6361:20078495 & c ESO 2007 Astrophysics Leptonic secondary emission in a hadronic microquasar model M. Orellana1,2,,P.Bordas3, V. Bosch-Ramon4,G.E.Romero1,2,, and J. M. Paredes3 1 Facultad de Ciencias Astronómicas y Geofísicas, Universidad Nacional de La Plata, Paseo del Bosque, 1900 La Plata, Argentina e-mail: [email protected] 2 Instituto Argentino de Radioastronomía, C.C.5, (1894) Villa Elisa, Buenos Aires, Argentina 3 Departament d’Astronomia i Meteorologia, Universitat de Barcelona, Martí i Franquès 1, 08028 Barcelona, Spain 4 Max Planck Institut für Kernphysik, Saupfercheckweg 1, Heidelberg 69117, Germany Received 16 August 2007 / Accepted 4 September 2007 ABSTRACT Context. It has been proposed that the origin of the very high-energy photons emitted from high-mass X-ray binaries with jet-like features, so-called microquasars (MQs), is related to hadronic interactions between relativistic protons in the jet and cold protons of the stellar wind. Leptonic secondary emission should be calculated in a complete hadronic model that includes the effects of pairs from charged pion decays inside the jets and the emission from pairs generated by gamma-ray absorption in the photosphere of the system. Aims. We aim at predicting the broadband spectrum from a general hadronic microquasar model, taking into account the emission from secondaries created by charged pion decay inside the jet. Methods. The particle energy distribution for secondary leptons injected along the jets is consistently derived taking the energy losses into account. The spectral energy distribution resulting from these leptons is calculated after assuming different values of the magnetic field inside the jets. -
The Challenges of Low-Energy Secondary Electron Emission Measurement
Air Force Institute of Technology AFIT Scholar Theses and Dissertations Student Graduate Works 11-2019 The Challenges of Low-Energy Secondary Electron Emission Measurement Matthew J. Vincie Follow this and additional works at: https://scholar.afit.edu/etd Part of the Electromagnetics and Photonics Commons Recommended Citation Vincie, Matthew J., "The Challenges of Low-Energy Secondary Electron Emission Measurement" (2019). Theses and Dissertations. 3151. https://scholar.afit.edu/etd/3151 This Dissertation is brought to you for free and open access by the Student Graduate Works at AFIT Scholar. It has been accepted for inclusion in Theses and Dissertations by an authorized administrator of AFIT Scholar. For more information, please contact [email protected]. THE CHALLENGES OF LOW-ENERGY SECONDARY ELECTRON EMISSION MEASUREMENT DISSERTATION Matthew J. Vincie, Captain, USAF AFIT-ENG-DS-19-D-007 DEPARTMENT OF THE AIR FORCE AIR UNIVERSITY AIR FORCE INSTITUTE OF TECHNOLOGY Wright-Patterson Air Force Base, Ohio DISTRIBUTION STATEMENT A. APPROVED FOR PUBLIC RELEASE; DISTRIBUTION UNLIMITED. The views expressed in this prospectus are those of the author and do not reflect the official policy or position of the United States Air Force, Department of Defense, or the United States Government. This material is declared a work of the U.S. Government and is not subject to copyright protection in the United States. AFIT-ENG-DS-19-D-007 THE CHALLENGES OF LOW-ENERGY SECONDARY ELECTRON EMISSION MEASUREMENT DISSERTATION Presented to the Faculty Graduate School of Engineering and Management Air Force Institute of Technology Air University Air Education and Training Command In Partial Fulfillment of the Requirements for the Degree of Doctor of Philosophy Matthew J. -
UCLA Electronic Theses and Dissertations
UCLA UCLA Electronic Theses and Dissertations Title Computational Modeling of Plasma-induced Secondary Electron Emission from Micro- architected Surfaces Permalink https://escholarship.org/uc/item/5n50s2wj Author Chang, Hsing-Yin Publication Date 2019 Peer reviewed|Thesis/dissertation eScholarship.org Powered by the California Digital Library University of California UNIVERSITY OF CALIFORNIA Los Angeles Computational Modeling of Plasma-induced Secondary Electron Emission from Micro-architected Surfaces A dissertation submitted in partial satisfaction of the requirements for the degree Doctor of Philosophy in Materials Science and Engineering by Hsing-Yin Chang 2019 c Copyright by Hsing-Yin Chang 2019 ABSTRACT OF THE DISSERTATION Computational Modeling of Plasma-induced Secondary Electron Emission from Micro-architected Surfaces by Hsing-Yin Chang Doctor of Philosophy in Materials Science and Engineering University of California, Los Angeles, 2019 Professor Jaime Marian, Chair Advances in electrode, chamber, and structural materials will enable breakthroughs in future gen- erations of electric propulsion and pulsed power (EP & PP) technologies. Although wide ranges of EP & PP technologies have witnessed rapid advances during the past few decades, much of the progress was based on empirical development of materials through experimentation and trial-and- error approaches. To enable future technologies and to furnish the foundations for quantum leaps in performance metrics of these systems, a science-based materials development effort is required. The present study aims to develop computational models to simulate, analyze, and predict the sec- ondary electron emission of plasma devices in order to aid the design of materials architectures for EP & PP technologies through an integrated research approach that combines multi-scale modeling of plasma-material interactions, experimental validation, and material characterization. -
Characterization and Optimization of CERN Secondary Emission Monitors (SEM) Used for Beam Diagnostics
CONSEIL EUROPEEN´ POUR LA RECHERCHE NUCLEAIRE´ UNIVERSITAT POLITECNICA` DE CATALUNYA Characterization and optimization of CERN Secondary Emission Monitors (SEM) used for beam diagnostics. BACHELOR DEGREE IN PHYSICS ENGINEERING FINAL DEGREE PROJECT by Araceli Navarro Fern´andez Supervisors: Dr. Federico Roncarolo CERN, Gen`eve Dr. Jordi Llorca UPC, Barcelona May 2017 Abstract The European Organization for Nuclear Research, more commonly known as CERN, is one of the world's most influential particle physics center. The organization is based in a northwest suburb of Geneva, on the Franco-Swiss border and has 22 member states. At CERN, people with different backgrounds from all around the world work together in order to understand, among other things, the fundamental structure of the universe. To do that, particles have to be accelerated up to extremely high energies in a controlled and safe way. This work has been carried out within the BE-BI-PM section, responsible of the beam diagnostics instruments that allow the observation of the transverse profiles of particle beams. Different instruments and techniques are used for this purpose but in the following pages only the monitors based on Secondary Electron Emission (SEE) phenomena will be tackled. After introducing the physics behind Secondary Emission Monitors (SEM), their performance and limitations will be discussed. This will be based on simulations and beam experiments performed during the thesis work, mostly related to the LINAC4 , a new linear accelerator just completed at CERN. The first part of this document contains an introduction to the CERN accelerator chain, with particular emphasis on LINAC4 . Chapter 2 focuses on various aspects of the particles interaction with matter, which are used to define the theory behind SEE, the main process behind the SEM's signal generation. -
Dynamic Secondary Electron Emission in Dielectric/Conductor Mixed Coatings
Utah State University DigitalCommons@USU Conference Proceedings Materials Physics 2017 Dynamic Secondary Electron Emission in Dielectric/Conductor Mixed Coatings Leandro Olano Instituto de Ciencia de Materiales de Madrid Maria E. Davila Instituto de Ciencia de Materiales de Madrid A. Jacas Instituto de Ciencia de Materiales de Madrid M A. Rodriguez Instituto de Ceramica y Vidrio JR Dennison Utah State Univesity Follow this and additional works at: https://digitalcommons.usu.edu/mp_conf Part of the Condensed Matter Physics Commons Recommended Citation Olano, Leandro; Davila, Maria E.; Jacas, A.; Rodriguez, M A.; and Dennison, JR, "Dynamic Secondary Electron Emission in Dielectric/Conductor Mixed Coatings" (2017). Mulcopim. Conference Proceedings. Paper 42. https://digitalcommons.usu.edu/mp_conf/42 This Conference Paper is brought to you for free and open access by the Materials Physics at DigitalCommons@USU. It has been accepted for inclusion in Conference Proceedings by an authorized administrator of DigitalCommons@USU. For more information, please contact [email protected]. DYNAMIC SECONDARY ELECTRON EMISSION IN DIELECTRIC/CONDUCTOR MIXED COATINGS L. Olano1, I. Montero1, M. E. Dávila1, A. Jacas1, M. A. Rodriguez2, J.R. Dennison3. (1) Instituto de Ciencia de Materiales de Madrid, CSIC, Sor Juana Inés de la Cruz, 3, Cantoblanco, 28049 Madrid, Spain. [email protected] (2) Instituto de Cerámica y Vidrio, CSIC, Kelsen, 5, Cantoblanco, 28049 Madrid, Spain. (3) Utah State University Dept. of Physics, 4415 Old Main Hill, Logan, UT 84322-4415 USA. INTRODUCTION Secondary Emission Yield (SEY) of dielectric materials is of great importance for prediction and testing of the Multipaction discharge in RF components for space applications. -
SECONDARY ELECTRON EMISSION COEFFICIENT from LEXAN: the LOW ENERGY CROSSOVER by ELISE RENE BOERWINKLE ADAMSON, B.S.E.P., M.S
SECONDARY ELECTRON EMISSION COEFFICIENT FROM LEXAN: THE LOW ENERGY CROSSOVER by ELISE RENE BOERWINKLE ADAMSON, B.S.E.P., M.S. A DISSERTATION IN PHYSICS Submitted to the Graduate Faculty of Texas Tech University in Partial Fulfillment of the Requirements for the Degree of DOCTOR OF PHILOSOPHY Approved May, 1993 \^>•V^tZ ar.c %^^i-y ®1993, Elise Adamson ACKNOWLEDGEMENTS I would like to express my thanks to Dr. Lynn Hatfield for his guidance and support throughout the course of this research. I would also like to thank the other members of my committee: Dr. Magne Kristiansen, Dr. Hermann Krompholz, Dr. Thomas Gibson and Dr. Roger Lichti. Many of my co workers and fellow graduate students provided assistance on this project; I would specifically like to thank Michael Angier, Deneen Bennett and Daniel James III for extra help. I would like to acknowledge all of the shop and technical staff for their assistance. And I would like to thank my family, especially my husband David Adamson and my son Brian Adamson, for their help and encouragement. I am grateful to Los Alamos National Laboratory, and the SDIO through the management of DNA, for financial support during this project. 11 TABLE OF CONTENTS ACKNOWLEDGEMENTS ii ABSTRACT i V LIST OF TABLES V LIST OF FIGURES vi CHAPTER I. INTRODUCTION 1 II. THEORETICAL AND EXPERIMENTAL WORK 7 III. METHOD 24 IV. EXPERIMENTAL SETUP 39 V. RESULTS 52 VI. CONCLUSIONS AND FUTURE WORK 65 REFERENCES 69 111 ABSTRACT The energy location of the first crossover point of the secondary electron emission curve of the polymer insulator Lexan (polycarbonate) has been experimentally investigated.