Design and Testing of a Cupola Furnace for Michael Okpara University of Agriculture, Umudike
Total Page:16
File Type:pdf, Size:1020Kb
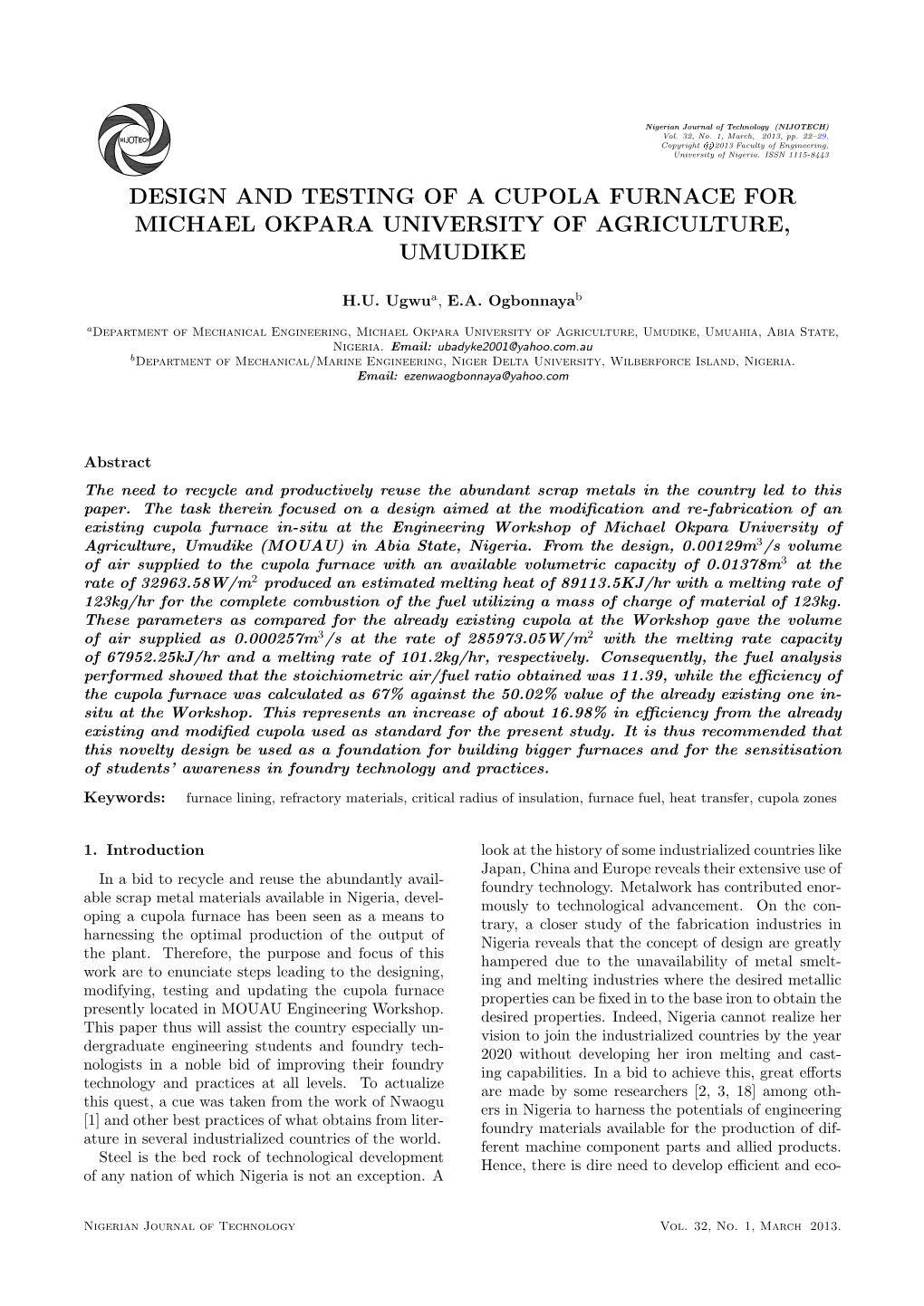
Load more
Recommended publications
-
ITP Metal Casting: Advanced Melting Technologies
Advanced Melting Technologies: Energy Saving Concepts and Opportunities for the Metal Casting Industry November 2005 BCS, Incorporated 5550 Sterrett Place, Suite 306 Columbia, MD 21044 www.bcs-hq.com Advanced Melting Technologies: Energy Saving Concepts and Opportunities for the Metal Casting Industry Prepared for ITP Metal Casting by BCS, Incorporated November 2005 Acknowledgments This study was a collaborative effort by a team of researchers from University of Missouri–Rolla, Case Western Reserve University, and Carnegie Mellon University with BCS, Incorporated as the project coordinator and lead. The research findings for the nonferrous casting industry were contributed by Dr. Jack Wallace and Dr. David Schwam, while the ferrous melting technologies were addressed by Dr. Kent Peaslee and Dr. Richard Fruehan. BCS, Incorporated researched independently to provide an overview of the melting process and the U.S. metal casting industry. The final report was prepared by Robert D. Naranjo, Ji-Yea Kwon, Rajita Majumdar, and William T. Choate of BCS, Incorporated. We also gratefully acknowledge the support of the U.S. Department of Energy and Cast Metal Coalition (CMC) in conducting this study. Disclaimer This report was prepared as an account of work sponsored by an Agency of the United States Government. Neither the United States Government nor any Agency thereof, nor any of their employees, makes any warranty, expressed or implied, or assumes any legal liability or responsibility for the accuracy, completeness, or usefulness of any information, apparatus, product, or process disclosed, or represents that its use would not infringe privately owned rights. Reference herein to any specific commercial product, process, or service by trade name, trademark, manufacturer, or otherwise does not necessarily constitute or imply its endorsement, recommendation, or favoring by the United States Government or any Agency thereof. -
National Register of Historic Places Multiple Property
NFS Form 10-900-b 0MB No. 1024-0018 (Jan. 1987) United States Department of the Interior National Park Service National Register of Historic Places Multipler Propertyr ' Documentation Form NATIONAL This form is for use in documenting multiple property groups relating to one or several historic contexts. See instructions in Guidelines for Completing National Register Forms (National Register Bulletin 16). Complete each item by marking "x" in the appropriate box or by entering the requested information. For additional space use continuation sheets (Form 10-900-a). Type all entries. A. Name of Multiple Property Listing ____Iron and Steel Resources of Pennsylvania, 1716-1945_______________ B. Associated Historic Contexts_____________________________ ~ ___Pennsylvania Iron and Steel Industry. 1716-1945_________________ C. Geographical Data Commonwealth of Pennsylvania continuation sheet D. Certification As the designated authority under the National Historic Preservation Act of 1966, as amended, J hereby certify that this documentation form meets the National Register documentation standards and sets forth requirements for the listing of related properties consistent with the National Register criteria. This submission meets the procedural and professional requiremerytS\set forth iri36JCFR PafrfsBOfcyid the Secretary of the Interior's Standards for Planning and Evaluation. Signature of certifying official Date / Brent D. Glass Pennsylvania Historical & Museum Commission State or Federal agency and bureau I, hereby, certify that this multiple -
Thermal Analysis of a Conventional Cupola Furnace with Effects of Excess Air on the Flue Gases Specific Heat !
Journal(of(Materials(and(( J. Mater. Environ. Sci., 2021, Volume 12, Issue 02, Page 192-204 Environmental(Science( ISSN(:(2028;2508( CODEN(:(JMESCN( http://www.jmaterenvironsci.com! Copyright(©(2021,( University(of(Mohammed(Premier(((((( Oujda(Morocco( Thermal Analysis of a Conventional Cupola Furnace with Effects of Excess Air on the Flue Gases Specific Heat ! Stephen A. Ajah1,2, Donald Idorenyin 1, Uchenna C. Nwokenkwo2, Uzoma S. Nwigwe2, Benjamin O. Ezurike2 1Applied Renewable & Sustainable Energy Research Group, Department of Mechanical Engineering, University of Nigeria, Nsukka, Nigeria 2Department of Mechanical Engineering, Alex Ekwueme Federal University Ndufu-Alike, Ebonyi State, Nigeria *Corresponding author, Email address: [email protected] **Corresponding author, Email address: [email protected] Received 29 Dec 2020, Abstract Revised 16 Feb 2021, A thermal analysis was carried out on a 6.5 m tall and 0.65 m diameter conventional cupola Accepted 17 Feb 2021 furnace at the Nigeria Railway Corporation, Enugu. This study tries to solve metallurgical problem of the furnace wall due to gases dissociation from unbalance excess air and Keywords undefined adiabatic flame temperature used during the operation. A combustion and ! Cupola furnace, thermal analysis of the fuel (coke) used for its operation has been carried out and the ! Thermal analysis, adiabatic combustion temperature of the fuel has been determined to be 2,175.93K. The ! Combustion, stoichiometric and actual air-fuel ratio of the furnace were found to be 10.97 and 12.08 ! Excess air, respectively. The percentage of flue gases difference for wet and dry case were also ! Adiabatic temperature. investigated against the percentage excess air. -
IRON MINING – ARDIS FURNACE and GALENA FURNACE [Compiled and Transcribed by William J
MENOMINEE RANGE HISTORY – IRON MINING – ARDIS FURNACE AND GALENA FURNACE [Compiled and Transcribed by William J. Cummings] Iron Mountain Press, Iron Mountain, Number 33 [Thursday, January 2, 1908], Dickinson County, Michigan, Volume 12, page 1, column 4 Number 31 [Thursday, December 19, 1907], page 1, column 1 Work Commenced. 100 TON FURNACE Work has commenced on the new blast _____ furnace, mention of which was made in The Press two weeks ago. It will be erected on the old waterworks property, near Lake PLANS PREPARING FOR Antoine, and the stone pump-house will be ERECTION IN IRON utilized in the construction. The contract for MOUNTAIN CITY. the steel stack and other machinery has _____ been let to the Prescott Iron Works, of Menominee. The furnace will be of one Work Will Commence on Structure hundred ton capacity and will differ Early in New Year – Meeting of somewhat from furnaces now in operation. Capitalists in New York. The ore for the furnace will be mined in the Randville district. John T. Jones is the leading spirit in the enterprise. The Press can state authoritatively that Iron Mountain is to become a pig iron Iron Mountain Press, Iron Mountain, manufacturing center. Dickinson County, Michigan, Volume 12, Architects are now engaged in making Number 45 [Thursday, March 26, 1908], the plans for a blast furnace to be erected page 1, column 4 here. The furnace is to be erected in the northern part of the city near Lake Antoine. New Blast Furnace. Work on the furnace will commence before the New Year is many weeks old. -
Eco-Friendly Cokeless-Cupola
Eco-friendly cokeless-cupola S. D. SINGH, D. K. BISWAS, K. K. MISHRA and P. RAMACHANDRA RAO National Metallurgical Laboratory, Jamshedpur - 831 007, India Abstract : This paper envisages the developmental work on eco-friendly cokeless cupola at the National Metallurgical Laboratory, Jamshedpur. The normal Cupolas for melting cast-iron in major parts of the World are operating with coke as fuel and the emission from such cupolas have been found to he containing Suspended Particulate Material (SPM) in the range of 700 to 2500 mg/Nm3 with sulphur dioxide content of the order of 400-1000 mg/Nm3. From the pollution point of view, these figures are excessively high. The use of low sulphur gaseous/liquid fuel promises extremely low level of SPM and SOx and does not need any pollution control device and can very well be installed within any thickly populated municipal area. In view of the above, NML was entrusted by the Technology Information Forecasting and Assessment Coun- cil (TIFAC) of Department of Science & Technology (DST), Govt. of India, to design and develop a suitable eco-friendly cokeless cupola in order to provide indigenous technical know-how to the clusters of foundries located at various places in the Country. Key words : Eco-friendly cokeless cupola, Gaseous fuel, Liquid Fuel, SPM/S0,, Design & development of cokelsss cupola, Technology Evaluations. ' INTRODUCTION There are about 6000 foundries currently operating mostly as cluster in places like Rajkot, Agra, Batala, Coimbatore, Howrah, Belgaum, etc. Almost all of these are coke fired. Coke based foundries are plagued with pollution problems. Normal stack emission from foundries ranges from 700 to 2500 mg/Nm3 of SPM and SOx beyond 400 mg/Nm3. -
Cadmium and Cadmium Compounds
Locating and Estimating Air Emissions From Sources of Cadmium and Cadmium Compounds U. S. Environmental Protection Agency Office of Air and Radiation Office of Air Quality Planning and Standards Locating and Estimating Air Emissions From Sources of Cadmium and Cadmium Compounds Prepared for: Anne Pope Office of Air Quality Planning and Standards Technical Support Division U. S. Environmental Protection Agency Research Triangle Park, N.C. 27711 Prepared by: Midwest Research Institute 401 Harrison Oaks Boulevard, Suite 350 Cary, North Carolina 27513 TABLE OF CONTENTS Section Page 1 PURPOSE OF DOCUMENT ..................1-1 REFERENCES ....................1-4 2 OVERVIEW OF DOCUMENT CONTENTS .............2-1 3 BACKGROUND.......................3-1 NATURE OF POLLUTANT ................3-1 OVERVIEW OF PRODUCTION, USE, AND EMISSIONS ....3-4 Production..................3-4 Use.....................3-6 Emissions ..................3-6 REFERENCES ................... 3-13 4 EMISSIONS FROM CADMIUM PRODUCTION ...........4-1 CADMIUM REFINING AND CADMIUM OXIDE PRODUCTION ...4-1 Process Description .............4-3 Emissions and Controls ............4-6 CADMIUM PIGMENTS PRODUCTION ........... 4-11 Process Description ............ 4-14 Emissions and Controls ........... 4-19 CADMIUM STABILIZERS PRODUCTION ......... 4-20 Process Description ............ 4-22 Emission and Controls ........... 4-24 OTHER CADMIUM COMPOUND PRODUCTION ........ 4-25 Process Descriptions ............ 4-25 Emissions and Controls ........... 4-29 REFERENCES ................... 4-32 5 -
Making ^Anthracite Iron N the Eighteenth Century Charcoal Was the Principal Fuel Used for Smelting Iron
discovery of the ^Process for (^Making ^Anthracite Iron N THE eighteenth century charcoal was the principal fuel used for smelting iron. When in the course of time the demand for I iron increased and the hardwood forests used for making charcoal became smaller, ironmasters looked for other fuels. In Britain and continental Europe they turned to soft coal, which was generally located near deposits of iron ore and from which coke could be made. Anthracite deposits were more scarce. Only a few of the many blast furnaces in Europe—those located near the veins of anthracite—would benefit if a way could be found to use this "stone coal/' as anthracite was then commonly called.1 The situation in the United States was far different, with the development of an entire industry at stake. Deposits of bituminous coal lay for the most part beyond the mountains, far from the centers of population and the extant means of transportation. The iron-rich ridges and valleys of eastern Pennsylvania and New Jersey, however, lay near extensive fields of anthracite. The canals which penetrated into the anthracite regions in the second quarter of the nineteenth century linked cities, towns, and deposits of iron ore, limestone, and anthracite like beads on a chain, 1 The first description of the discovery of the anthracite process appeared in 1841 in the form of a book and may have helped to advertise the process among ironmasters: Walter R. Johnson, Notes on the Use of Anthracite in the Manufacture of Iron with Some Remarks on Its Evaporating Power (Boston, 1841). -
Compacting of Fly Dusts from Cupola and Electric Arc Furnace
G. FEDORKO, A. PRIBULOVÁ, P. FUTÁŠ, D. BARICOVÁ, P. DEMETER ISSN 0543-5846 METABK 51(1) 63-66 (2012) UDC – UDK 669.187:669.041:628:515:622.81=111 COMPACTING OF FLY DUSTS FROM CUPOLA AND ELECTRIC ARC FURNACE Received - Prispjelo: 2010-09-15 Accepted - Prihvaćeno: 2011-02-10 Preliminary Note – Prethodno priopćenje Recycling and utilization of dust waste is important not only from the point of view of its usage as an alternative source of raw materials, but regarding the environmental problems also. Dust emissions arise from thermal and chemical or physical processes and mechanical actions. Two kinds of fl y dusts from cupola furnaces (hot and cold blast cupola furnace) and fl y dust from electric arc furnace were used by experiments. They were pelletized only with addition of water and briquetted with diff erent addition of water glass, bentonite and cement. Quality of bri- quettes was tested by compression – strength test and by break down test in green state, after drying and after storing (1 month). Key words: electric arc furnace, cupola furnace, fl y dust, briquettes, pellets. Kompaktiranje lebdeće prašine iz kupolne i elektrolučne peći. Recikliranje i iskorištavanje otpadne prašine važno je zbog aspekta njezine uporabe kao alternativnog izvora sirovina, ali također i s obzirom na ekološke probleme. Emis- ija prašina nastaje iz termičkih, kemijskih ili fi zikalnih procesa te mehaničkih aktivnosti. U eksperimentalnom dijelu korištene su dvije vrste lebdeće prašine iz kupolne peći (s predgrijanim i hladnim zrakom) te elektrolučne peći. Prašina je peletizirana samo uz dodatak vode i briketirana s različitim dodatkom vodenog stakla, bentonita i cementa. -
A. Fundamentals
A. Fundamentals 1. Introduction 1.1 Principle mechanism Shaft kilns and cupola furnaces are used for the mass conversion and melting of granular and coarse materials. The material is transported through the vertical shaft by gravity. The hot gas flows in a counter current to the material. Typical processes are summarized in Table 1-1. For calcination processes mainly the name shaft kiln is used and for melting processes mainly the name cupola furnace. For the reduction of iron ore the name blast furnace is common. In the following for the general description the designation shaft kiln is used. Calcination of calcite CaCO3 CaO + CO2’ Calcination of magnesite MgCO3 MgO + CO2 Calcination of dolomite CaCO3 MgCO3 CaO MgO + 2 CO2 Calcination of iron ore FeCO3 FeO + CO2 Reduction of iron ore FeO + CO Fe +CO2 Reduction of lead ore Sintering of fireclay Melting of cast iron scrap Melting of copper scrap and anodes Melting of zinc scrap and ingots Melting of lead scrap Melting of aluminium scrap and ingots Melting of rock for mineral wood Melting of solid waste Table 1-1: Typical processes in shaft kilns Table 1-2 summarizes typical characteristic values of cupola furnaces and blast furnaces and Table 1-3 presents those values of common shaft kilns. From the two tables it can be seen that blast furnaces are the biggest one in size and max. outflow. However, the outflow in relation to cross section is only a little bit larger than that of normal shaft kilns. Pure melting furnaces have the highest output flux. Here, the material has only to heat up and to supply with the melting enthalpy. -
Department of Metallurgical Engineering
OBJECTIVE QUESTION BANK Er. SUBRAT KUMAR BEHERA Lecturer in Metallurgy Department of Metallurgical Engineering ORISSA SCHOOL OF MINING ENGINEERING, KEONJHAR A Government of Odisha institution with National Repute Established in the Year 1956 (Approved by AICTE, New Delhi & Affiliated to SCTE&VT, Odisha,BBSR) Iron & Steel Making 1. Which is closest to the purest form of the iron? Cast Iron Wrought Iron Pig Iron Steel 2. The product of a commercial direct reduction process is: Liquid 1ron Pig iron Sponge iron Iron saturated with carbon. 3. Abrasion resistance of coke is measured by the M10 M40 Shatter test none 4. Which one of the following is not the irregularitie of the blast furnace? Hanging Slip Tapping Breakout 5. Which one of the following is not function of coke in the blast furnace ? Fuel Carburizer Reducing agent Oxidizing agent 6. Which one of the following is not the zone of the blast furnace? Granular zone Adhesive zone Cohesive zone Tuyere zone 7. Sulphide ore of iron is Magnetite Hematite Pyrites Limonite 8. Which one of the following furnace can be used to produce Alloy steels L D process open hearth furnace Electric Arc furnace Acid Bessemer process 9. Which one of the following is receptacle to collect the liquid slag and metal Bosh Stack Hearth Tuyere 10. Which one of the following process is Direct smelting Blast Furnace LD vacuum Arc Degassing (VAD) COREX 11. The important factors for producing low silicon pig iron in a blast furnace are Higher temperature and higher basicity Lower temperature and lower basicity Lower temperature and higher basicity Higher temperature and lower basicity 12. -
ITP Metal Casting: Theoretical/Best Practice Energy Use In
Theoretical/Best Practice Energy Use In Metalcasting Operations J. F. Schifo J.T. Radia KERAMIDA Environmental, Inc. Indianapolis, IN May 2004 Prepared under Contract to Advanced Technology Institute North Charleston, SC for the U.S. Department of Energy Industrial Technologies Program Washington, DC Industrial Technologies Program Boosting the productivity and competitiveness of U.S. industry through improvements in energy and environmental performance Errata Sheet This is a listing of the corrections that were made since the original posting of the Theoretical/Best Practice Energy Use In Metalcasting Operations in April 2004. Text Errors • Cover, in the title Metal Casting was two words and changed to one word “Metalcasting”. • Page 9, the following sentence was inserted. “This study, therefore, utilized actual metalcasting energy usage by facility type to calculate the total energy used by alloy, rather than summaries of energy consumption data by NAICS codes.” • Page 9, the following sentence was removed: “It is estimated that the industry consumes 466 trillion Btu tacit energy annually.” • Page 10, Table 9, the total 2003 row was deleted. • Page 52, Table 31, removed total row and re-labled header on second column to “2003 Benchmark Tacit Energy.” • Page 52, Table 32 removed total row and re-labled second column to “2003 Benchmark Tacit Energy.” • Page 62, Table 37 was removed and tables 38 through 56 where renumbered accordingly. 1 TABLE OF CONTENTS EXECUTIVE SUMMARY .......................................................................................................... -
Richard S Allen Collection Catalogue Inventory
Inventory of the Richard Sanders Allen Collection Box 1. Hand labeled: Iron Industry General Tahawus & “Mixed Iron.” (Published books and booklets are listed in bibliographic style; pamphlets are not described; organized research materials are listed separately.) Cohen, Linda, Sarah Cohen and Peg Masters. Old Forge: Gateway to the Adirondacks. Postcard History Series. Charleston, SC: Arcadia Publishing, 2003. Cottrell, Alden, T. The Story of Ringwood Manor. 6th ed. Trenton, NJ: Trenton Printing Co., Inc., 1954. Donald, WJA. The Canadian Iron and Steel Industry: A Study in the Economic History of a Protected Industry. Boston: Houghton Mifflin Co., 1915. DuFresne, Jim. Michigan State Parks: A Complete Recreation Guide. 2nd ed. Seattle: The Mountaineers, 1998. Eisenhuth, Chester F. Maltby’s Furnace and One Man’s Memories. NP: The North East Historical Society, 1996. Fennessy, Lana. The History of Newcomb. Newcomb, NY: By the Author, 1996. Ghee, Joyce C. and Joan Spence. Poughkeepsie: Halfway Up the Hudson. Images of America. Charleston, SC: Arcadia Publishing, 1997; reprint 1998. Glenn, Morris F. The Story of Three Towns: Westport, Essex and Willsboro, New York. Alexandria, VA: By the Author, 1805 Sword Lane, Alexandria, Va.: 1977. Gordon, Robert B. A Landscape Transformed: The Ironmaking District of Salisbury, Connecticut. New York: Oxford University Press, 2001. (Two copies) Greer, Edward. Big Steel: Black Politics and Corporate Power in Gary, Indiana. New York: Monthly Review Press, 1979. Hawke, David Freeman. John D.: The Founding Father of the Rockefellers. New York: Harper and Row, Publishers, 1980. Isleib, Charles R and Jack Chard. The West Point Foundry and the Parrott Gun: A Short History.