D2d3e7a3dc363faa7bea5b478c
Total Page:16
File Type:pdf, Size:1020Kb
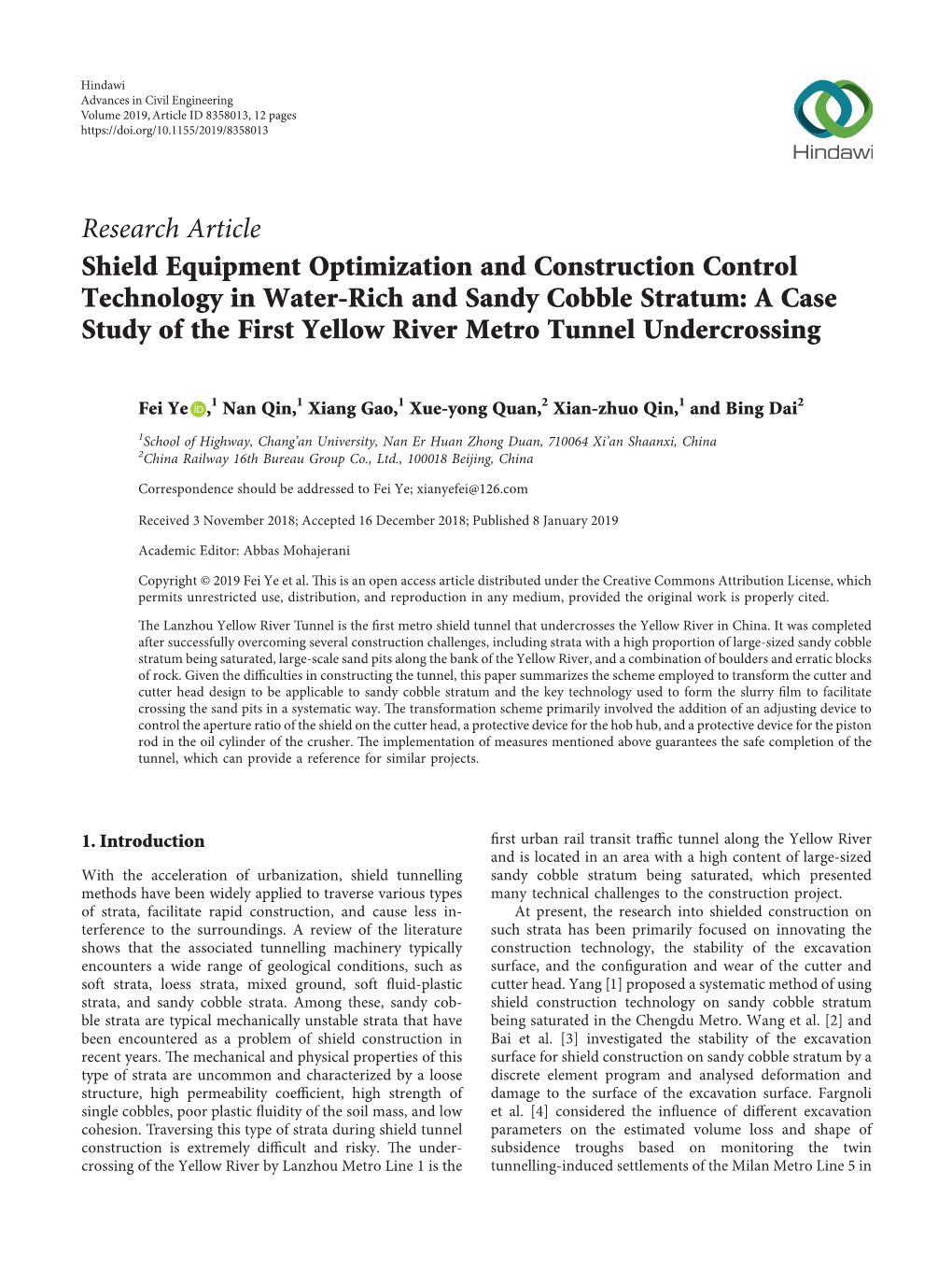
Load more
Recommended publications
-
Unravelling Decision-Making Processes on Location Choices For
Delft University of Technology Unravelling Decision-Making Processes on Location Choices for High-Speed Railway Stations in China A Comparison of Shenzhen, Lanzhou and Jingmen Wang, Biyue; de Jong, Martin; Van Bueren, Ellen; Ersoy, Aksel; Chen, Yawei DOI 10.1080/14649357.2021.1933578 Publication date 2021 Document Version Final published version Published in Planning Theory and Practice Citation (APA) Wang, B., de Jong, M., Van Bueren, E., Ersoy, A., & Chen, Y. (2021). Unravelling Decision-Making Processes on Location Choices for High-Speed Railway Stations in China: A Comparison of Shenzhen, Lanzhou and Jingmen. Planning Theory and Practice. https://doi.org/10.1080/14649357.2021.1933578 Important note To cite this publication, please use the final published version (if applicable). Please check the document version above. Copyright Other than for strictly personal use, it is not permitted to download, forward or distribute the text or part of it, without the consent of the author(s) and/or copyright holder(s), unless the work is under an open content license such as Creative Commons. Takedown policy Please contact us and provide details if you believe this document breaches copyrights. We will remove access to the work immediately and investigate your claim. This work is downloaded from Delft University of Technology. For technical reasons the number of authors shown on this cover page is limited to a maximum of 10. Planning Theory & Practice ISSN: (Print) (Online) Journal homepage: https://www.tandfonline.com/loi/rptp20 Unravelling Decision-Making -
Interim Report 2018 Chinasoft International Limited 2 HIGHLIGHTS
CONTENTS 1 PAGE Highlights ........................................................... 2 Chairman’s Report ..................................................... 3 Recent Business Development ........................................... 6 Management Discussion and Analysis ..................................... 18 Interim Results – Consolidated Statement of Comprehensive Income (Unaudited) .............. 28 – Consolidated Statement of Financial Position (Unaudited) ................... 29 – Consolidated Statement of Changes in Equity (Unaudited) ................... 31 – Consolidated Statement of Cash Flows (Unaudited) ........................ 32 – Notes to the Unaudited Consolidated Financial Statements .................. 33 Other Information ..................................................... 44 Interim Report 2018 Chinasoft International Limited 2 HIGHLIGHTS Results for the first half of 2018 For the six months ended 30 June 2018 2017 Income statement highlights (unaudited) (unaudited) % Change RMB’000 RMB’000 Revenue 4,813,853 4,145,060 16.1% Revenue from service 4,770,267 4,047,248 17.9% Profit for the period 355,805 240,445 48.0% Profit attributable to Owners of the Company 358,759 245,470 46.2% Basic EPS (RMB cents) 14.87 10.26 44.9% (unaudited) (audited) Statement of financial 30 June 31 December position highlights 2018 2017 % Change RMB’000 RMB’000 Total assets 8,948,585 8,751,533 2.3% Total liabilities (3,308,763) (3,521,567) (6.0%) Total equity 5,639,822 5,229,966 7.8% • The Directors do not recommend the payment of an interim dividend for the six months ended 30 June 2018. • No closure for the Register of Members of the Company. Chinasoft International Limited Interim Report 2018 CHAIRMAN’S REPORT 3 Dear Investors: During the first half of 2018, I believe that everyone underwent a unique moment of their investment career (some may even say it’s the dark era). -
Annual Report
(於新加坡註冊成立的有限公司) (incorporated in Singapore with limited liability) (Singapore Stock Code: 5EN) (新加坡股份代號:5EN) (Hong Kong Stock Code: 1021) (香港股份代號:1021) MIDAS HOLDINGS LIMITED ANNUAL REPORT 2015 GROWTH AND 增长与 INTEGRATION 整合 ANNUAL REPORT 2015 CORPORATE 公司 STRUCTURE 架構 CORPORATE OFFICE 公司辦事處 Chen Wei Ping, Executive Chairman Chew Hwa Kwang, Patrick, Chief Executive Officer 陳維平,執行主席 Chan Chee Kin, Chief Financial Officer 周華光,行政總裁 JILIN MIDAS ALUMINIUM INDUSTRIES CO., LTD. 陳子堅,首席財務總監 Li Zhenyu, General Manager 吉林麥達斯鋁業有限公司 SHANXI WANSHIDA ENGINEERING PLASTICS CO., LTD. 李鎮宇,總經理 Xu Honghong, General Manager 山西萬士達工程塑料有限公司 LUOYANG MIDAS ALUMINIUM INDUSTRIES CO., LTD. Sun Qixiang, General Manager 許宏宏,總經理 JILIN MIDAS LIGHT ALLOY CO., LTD. 洛陽麥達斯鋁業有限公司 Hou Tiemin, General Manager 孫起祥,總經理 吉林麥達斯輕合金有限公司 侯鐵民,總經理 01 MIDAS HOLDINGS LIMITED ANNUAL REPORT 2015 TABLE OF CONTENTS IFC CORPORATE STRUCTURE 02 CORPORATE PROFILE 06 MESSAGE FROM THE EXECUTIVE CHAIRMAN 08 MESSAGE FROM THE CHIEF EXECUTIVE OFFICER 10 BOARD OF DIRECTORS 12 EXECUTIVE OFFICERS 13 CORPORATE INFORMATION 15 FINANCIAL HIGHLIGHTS 17 FINANCIAL CONTENTS 02 MIDAS HOLDINGS LIMITED ANNUAL REPORT 2015 CORPORATE PROFILE extrusion products for the passenger rail transportation Incorporated on 17 November 2000 as an sector in the PRC and international markets. It is investment holding company, listed on 23 February our principal business division and accounted for 2004 on Singapore Exchange Securities Trading Limited 99.2% of our total revenue for the financial year ended (“SGX-ST”) and on 6 October 2010 on The Stock Exchange 31 December 2015 (“FY2015”). We are also one of of Hong Kong Limited (“SEHK”), Midas Holdings Limited the first and amongst the few in the PRC aluminium alloy (the “Company” or “Midas”, together with its subsidiaries, extrusion industry to possess capabilities for the downstream referred to the “Group”) has grown over the years to gain fabrication of passenger train car body components. -
China Fangda Group Co., Ltd
Annual Report 2019 of China Fangda Group Co., Ltd. China Fangda Group Co., Ltd. 2019 Annual Report April 2020 1 Annual Report 2019 of China Fangda Group Co., Ltd. Chapter 1 Important Statement, Table of Contents and Definitions The members of the Board and the Company guarantee that the announcement is free from any false information, misleading statement or material omission and are jointly and severally liable for the information’s truthfulness, accuracy and integrity. Mr. Xiong Jianming, the Chairman of Board, Mr. Lin Kebin, the Chief Financial Officer, and Mr. Wu Bohua, the manager of accounting department declare: the Financial Report carried in this report is authentic and completed. All the Directors have attended the meeting of the board meeting at which this report was examined. Forward-looking statements involved in this report including future plans do not make any material promise to investors. Investors should pay attention to investment risks. The Company needs to comply with disclosure requirements of the Shenzhen Stock Exchange Industry Information Disclosure Guideline No.6 – Listed Companies Engaged in Decoration Business and disclosure requirements of the Shenzhen Stock Exchange Industry Information Disclosure Guideline No.3 – Listed Companies Engaged in Property Development. The Company has specified market, management and production and operation risks in this report. Please review the potential risks and measures 2 Annual Report 2019 of China Fangda Group Co., Ltd. mentioned in the discussion and analysis of future development in IV. Operation Discussion and Analysis. Based on the total share capital after the market close on the stock registration day when the profit distribution plan is implemented, a cash dividend of RMB 0.50 (tax included) will be distributed to all shareholders for every 10 shares, and no bonus shares will be sent or capital reserves will be transferred to increase capital. -
Leading New ICT Building a Smart Urban Rail
Leading New ICT Building A Smart Urban Rail 2017 HUAWEI TECHNOLOGIES CO., LTD. Bantian, Longgang District Shenzhen518129, P. R. China Tel:+86-755-28780808 Huawei Digital Urban Rail Solution Digital Urban Rail Solution LTE-M Solution 04 Next-Generation DCS Solution 10 Urban Rail Cloud Solution 15 Huawei Digital Urban Rail Solution Huawei Digital Urban Rail Solution Huawei LTE-M Solution for Urban Rail Huawei and Alstom the Completed World’s Huawei Digital Urban Rail LTE-M Solution First CBTC over LTE Live Pilot On June 29th, 2015, Huawei and Alstom, one of the world’s leading energy solutions and transport companies, announced the successful completion of the world’s first live pilot test of 4G LTE multi-services based on Communications- based Train Control (CBTC), a railway signalling system based on wireless ground-to-train CBTC PIS CCTV Dispatching communication. The successful pilot, which CURRENT STATUS IN URBAN RAIL covered the unified multi-service capabilities TV Wall ATS Server Terminal In recent years, public Wi-Fi access points have become a OCC of several systems including CBTC, Passenger popular commodity in urban areas. Due to the explosive growth Information System (PIS), and closed-circuit in use of multimedia devices like smart phones, tablets and NMS LTE CN television (CCTV), marks a major step forward in notebooks, the demand on services of these devices in crowded the LTE commercialization of CBTC services. Line/Station Section/Depot Station places such as metro stations has dramatically increased. Huge BBU numbers of Wi-Fi devices on the platforms and in the trains RRU create chances of interference with Wi-Fi networks, which TAU TAU Alstom is the world’s first train manufacturer to integrate LTE 4G into its signalling system solution, the Urbalis Fluence CBTC Train AR IPC PIS AP TCMS solution, which greatly improves the suitability of eLTE, providing a converged ground-to-train wireless communication network Terminal When the CBTC system uses Wi-Fi technology to implement for metro operations. -
Gansu(PDF/181KB)
Mizuho Bank China Business Promotion Division ―Gansu Province Overview Abbreviated Name Gan/Long Provincial Capital Lanzhou Administrative 12 cities, 2 autonomous Divisions prefectures and 69 counties Secretary of the Wang Sanyun; Provincial Party Xinjiang Inner Mongolia Liu Weiping Ningxia Committee; Mayor Gansu Size 454,430 km2 Qinghai Shaanxi Annual Mean 9.1°C Sichuan Temperature Annual Precipitation 474.7 mm Official Government www.gansu.gov.cn URL Note: Personnel information as of September 2014 [Economic Scale] Unit 2012 2013 National Share Ranking (%) Gross Domestic Product (GDP) 100 Million RMB 5,650 6,268 27 1.0 Per Capita GDP RMB 21,978 24,297 30 - Value-added Industrial Output 100 Million RMB 1,931 2,045 N.A. N.A. (enterprises above a designated size) Agriculture, Forestry and Fishery 100 Million RMB 1,358 N.A. N.A. N.A. Output Total Investment in Fixed Assets 100 Million RMB 6,013 6,407 26 1.4 Fiscal Revenue 100 Million RMB 520 606 27 0.5 Fiscal Expenditure 100 Million RMB 2,060 2,308 N.A. N.A. Total Retail Sales of Consumer 100 Million RMB 1,907 2,140 26 0.9 Goods Foreign Currency Revenue from Million USD 22 20 N.A. N.A. Inbound Tourism Export Value Million USD 3,574 4,679 26 0.2 Import Value Million USD 5,326 5,602 26 0.3 Export Surplus Million USD - 1,752 - 923 24 - Total Import and Export Value Million USD 8,899 10,281 27 0.2 Foreign Direct Investment Contracts No. of contracts 20 N.A. -
China Railway Sector
Industrials / China 9 January 2015 Initiation: rail plays to benefit China Railway Sector from urbanisation, overseas push Positive (initiation) • Railway construction and equipment companies stand to benefit Neutral from ongoing investment in HSR and urban rail transit market Negative • Zhuzhou CSR should be key beneficiary of CSR/CNR merger, increasing its market share substantially without paying the price • Our order of preference: Zhuzhou CSR , CSR, CRG, CRCC, CCCC How do we justify our view? urbanisation rate in China, and [3]) has less exposure to railway believe the urban transit market will construction. Local governments’ be a long-term earnings and share- high debt levels and weak land sales price driver for the sector. With could drag down investments in road China’s government’s aggressive and port projects to which CCCC has Brian Lam plans for SOEs to strengthen their high exposure. (852) 2532 4341 overseas businesses, we believe both [email protected] railway constructors and equipment ■ Catalysts makers will benefit handsomely by The 13th FYP is expected to be Kelvin Lau increasing their international announced in 3Q15.We estimate total (852) 2848 4467 presence, given their competitive railway FAI for 13th FYP to be greater [email protected] advantage in providing quality than that for 12th FYP. Better-than- products at a low cost. expected 2014 results and railway ■ Investment case FAI target for 2015E could be a near- ■ Recommendation We initiate coverage of the China term catalyst. Railway Construction and Railway We prefer the railway equipment ■ Risks Equipment Sector with a Positive makers over the railway constructors, rating. -
Tunnel-Boring-Machine.Pdf
CONTENTS Ⅰ.Brief Introduction of CRCHI ⅰ.General...................................................................................1 ⅱ.Branches.................................................................................3 ⅲ.Qualified Certificates...............................................................9 Ⅱ. Products ⅰ.Tunnel Boring Machine.........................................................10 A. Earth Pressure Balance Shield (EPB)...............................11 B. Slurry Pressure Balance Shield (SPB)...............................15 C. Hard Rock Shield...............................................................19 D. Special FunctionalTBM.....................................................23 ⅱ. Shotcrete&Diaphragm Wall..............................26 ⅲ. Turnout.................................................................................28 ⅳ. Fastener&Clip&Brake-shoe.........................................33 ⅴ.Railway Electrification Products...........................................37 ⅵ. New Developed Products....................................................39 Ⅲ. Product’s Presentation in Jobsites IV. Technical & Service Backup 1 Add: No.88 Dongqi Road, National Economic & Technical Development Zone, Changsha, China. Zip Code: 410100 Tel: +86 731 84071707 Fax: +86 731 84071767. Ⅰ. China Railway Construction Heavy Industry Co., Ltd ⅰ.General China Railway Construction Heavy Industry Co., Ltd. (hereinafter referred as CRCHI) is affiliated to the China Railway Construction Corporation. The CRCHI is a professional -
View Annual Report
UNITED STATES SECURITIES AND EXCHANGE COMMISSION WASHINGTON, D.C. 20549 FORM 20-F (Mark One) REGISTRATION STATEMENT PURSUANT TO SECTION 12(b) OR (g) OF THE SECURITIES EXCHANGE ACT OF 1934 OR ANNUAL REPORT PURSUANT TO SECTION 13 OR 15(d) OF THE SECURITIES EXCHANGE ACT OF 1934 For the fiscal year ended June 30, 2018 OR TRANSITION REPORT PURSUANT TO SECTION 13 OR 15(d) OF THE SECURITIES EXCHANGE ACT OF 1934 For the transition period from ___________ to ___________. OR SHELL COMPANY REPORT PURSUANT TO SECTION 13 OR 15(d) OF THE SECURITIES EXCHANGE ACT OF 1934 Date of event requiring this shell company report _________________________ Commission file number: 001-33602 HOLLYSYS AUTOMATION TECHNOLOGIES LTD. (Exact name of Registrant as specified in its charter) Not Applicable (Translation of Registrant’s name into English) British Virgin Islands (Jurisdiction of incorporation or organization) No. 2 Disheng Middle Road, Beijing Economic-Technological Development Area, Beijing, P. R. China 100176 (Address of principal executive offices) Arden Xia, Tel: (86 10) 5898 1386, Email: [email protected] Address: No. 2 Disheng Middle Road, Beijing Economic-Technological Development Area, Beijing, P.R. China 100176 (Name, Telephone, E-mail and/or Facsimile number and Address of Company Contact Person) Securities registered or to be registered pursuant to Section 12(b) of the Act. Title of each class Name of each exchange on which registered 1 Ordinary Shares, $0.001 par value per share The NASDAQ Global Select Market Preferred Share Purchase Rights The NASDAQ Global Select Market Securities registered or to be registered pursuant to Section 12(g) of the Act. -
2019年报 广州地铁,载你,载我,载入新时代 Travel Into the New Era
载入新时代 美好生活的理想是引领时代向前的光,一路穿越浩瀚星空,接轨跨越百年的时间意义 全程为你 广州地铁,延伸全程为你的进步之道,向着新时代启程 新时代来得如此迅捷多彩,又让人心潮澎湃!广州地铁,用更宽广的新高度连接起 这个时代有温度的大爱、用更智能的新标准改写着我们惬意出行的畅享里程 不必奔忙弹指间从容有度、不用喧哗却尽情表达, 得到所爱却无需等待 让熟悉的笑容不因空间远离而疏离,谦让的暖意在人际与城际间依然流淌 新时代的广州地铁,用更富远见的新格局和产业聚势的新突破,勾勒出无数城市 “梦想家”的幸福蓝图,载着在乎亲情与挚爱的心灵,从一座城到一群城 再到一整个世界,关乎事业与生活的憧憬从此有了更开阔的承载空间 2019年报 广州地铁,载你,载我,载入新时代 TRAVEL INTO THE NEW ERA ANNUAL REPORT 2019 THE DESIRE FOR A BETTER LIFE IS THE LIGHT GUIDING THE TIMES FORWARD. ACROSS THE VAST SKY, WE CONNECT YOU TO A TIME SPANNING A CENTURY. GUANGZHOU METRO TAKES YOU FORWARD INTO A NEW ERA! THE NEW ERA HAS COME—FAST, COLORFUL AND EXCITING! GUANGZHOU METRO SPREADS LOVE AND TAKES IT TO NEW HEIGHTS IN THIS ERA, AND BRINGS MORE PLEASANT AND SMART SERVICES TO PASSENGERS. THERE’S NO NEED TO RUSH OR JOSTLE, NO NEED TO WAIT TILL YOUR LOVE ARRIVES. FAMILIAR SMILES ARE NOT THAT FAR AWAY. COURTESY AND KINDNESS IS STILL PRESENT AMONG PEOPLE AND IN CITIES. GUANGZHOU METRO, WITH A NEW VISION AND NEW INDUSTRIAL BREAKTHROUGH, HAS DRAWN A BLUEPRINT FOR “DREAMERS” IN NUMEROUS CITIES, CARRYING LOVING SOULS FROM ONE CITY TO ANOTHER, AND ACROSS THE WORLD. A BROADER SPACE PROVIDES YOU A BETTER A CAREER AND LIFE. WITH US ONBOARD, GUANGZHOU METRO TRAVELS INTO THE NEW ERA! 公司概况 Corporation Overview 公司简介 Corporation Profile 01 阳光文化 Sunshine Culture 02 广州地铁线网图 目录 集团董事会成员 Members of the Board of Directors of the Group 03 MAP OF METRO NETWORK OF GUANGZHOU CONTENTS 集团监事会成员 Members of the Board of Supervisors of the Group 03 集团领导班子成员 Members of Leadership Team 04 2019年要事录 Milestones in 2019 05 北 公司荣誉及其他 -
View Annual Report
Date: 09/22/2017 08:33 AM Toppan Vintage Project: v474603 Form Type: 20-F Client: v474603_Hollysys Automation Technologies, Ltd._20-F Submission Data File General Information Form Type* 20-F Contact Name Kelvin Shiwnath Contact Phone 866-683-5248 Filer Accelerated Status* Large Accelerated Filer Filer File Number Filer CIK* 0001357450 [Hollysys Automation Technologies, Ltd.] (Hollysys Automation Technologies, Ltd.) Filer CCC* ********** Filer is Shell Company* N Filer is Voluntary Filer* N Filer is Well Known Seasoned Issuer* Y Confirming Copy No Notify via Website only No Return Copy No SROS* NASD Period* 06-30-2017 Emerging Growth Company No Elected not to use extended transition period No (End General Information) Document Information File Count* 14 Document Name 1* v474603_20f.htm Document Type 1* 20-F Document Description 1 Form 20-F Document Name 2* v474603_ex8-1.htm Document Type 2* EX-8.1 Document Description 2 Exhibit 8.1 Document Name 3* v474603_ex12-1.htm Document Type 3* EX-12.1 Document Description 3 Exhibit 12.1 Document Name 4* v474603_ex12-2.htm Document Type 4* EX-12.2 Document Description 4 Exhibit 12.2 Document Name 5* v474603_ex13-1.htm Document Type 5* EX-13.1 Document Description 5 Exhibit 13.1 Document Name 6* v474603_ex13-2.htm Document Type 6* EX-13.2 Document Description 6 Exhibit 13.2 Document Name 7* v474603_ex15-1.htm Document Type 7* EX-15.1 Document Description 7 Exhibit 15.1 Document Name 9* holi-20170630.xml Document Type 9* EX-101.INS Document Description 9 XBRL INSTANCE DOCUMENT Document Name 10* holi-20170630.xsd -
产业发展 INDUSTRIAL DEVELOPMENT 产业聚势的新突破 整合业态的运筹之道 New Breakthroughs in Industrial Convergence Strategy to Integrate Business Types
75 76 产业发展 INDUSTRIAL DEVELOPMENT 产业聚势的新突破 整合业态的运筹之道 New Breakthroughs in Industrial Convergence Strategy to Integrate Business Types 中标南昌、重庆和丽江3大线路;新增40多家广州轨道产业联盟会员,推动7家车辆 装备优质企业落户产业园,以产业生态链的平台构建,驱动品牌跃级的发展远见。 Won the bidding of the three major lines of Nanchang, Chongqing and Lijiang; added more than 40 members of Guangzhou Alliance of Metros Industry, promoted 7 enterprises with high-quality vehicle outfitting to settle in the industrial park, and built a platform of industrial ecological chain to drive the leap development of brands. 统筹开展广州及全国城市的 发展广州轨道交通产业 地铁设计工作 联盟会员 Carry out the Design of Subway in Develop members of Guangzhou Guangzhou and other Cities in China Alliance of Rail Transit Industry 多个城市 多家 40 Cities 40 Members 产业发展 产业发展 INDUSTRIAL DEVELOPMENT INDUSTRIAL DEVELOPMENT 产业协同 融合外拓 地铁设计 INDUSTRIAL COLLABORATION INTEGRATION AND EXPANSION METRO DESIGN 2019 年经营收入 Business Revenue in 2019 亿元 16.44 RMB Hundred Million 广州轨道交通产业联盟以“政府引导、市场主导、政产 On the basis of "Government guidance, market orientation, and integration of government, industry, education, and research", Guangzhou 学研相融合”为基础,以“合作、共赢、创新、发展”为原 Alliance of Rail Transit Industry following the principle of "Cooperation, win-win, innovation, and development" and relying on the concept of 则,以“促进科技研发、推进产业升级”为依托,全面落实 "promoting the R&D and industrial upgrading", fully implemented the 市政府关于“2019 年底引进 3-5 家企业落户白云神山轨道 requirements of the Guangzhou Municipal Government on "introducing 3-5 enterprises to settle in Baiyun Shenshan Rail Transit Equipment Industrial 交通装备产业园”的要求,强化产业的引进与集聚,主动摸