Characterization and Magnetic Augmentation of a Low Voltage Electromagnetic Raelgun
Total Page:16
File Type:pdf, Size:1020Kb
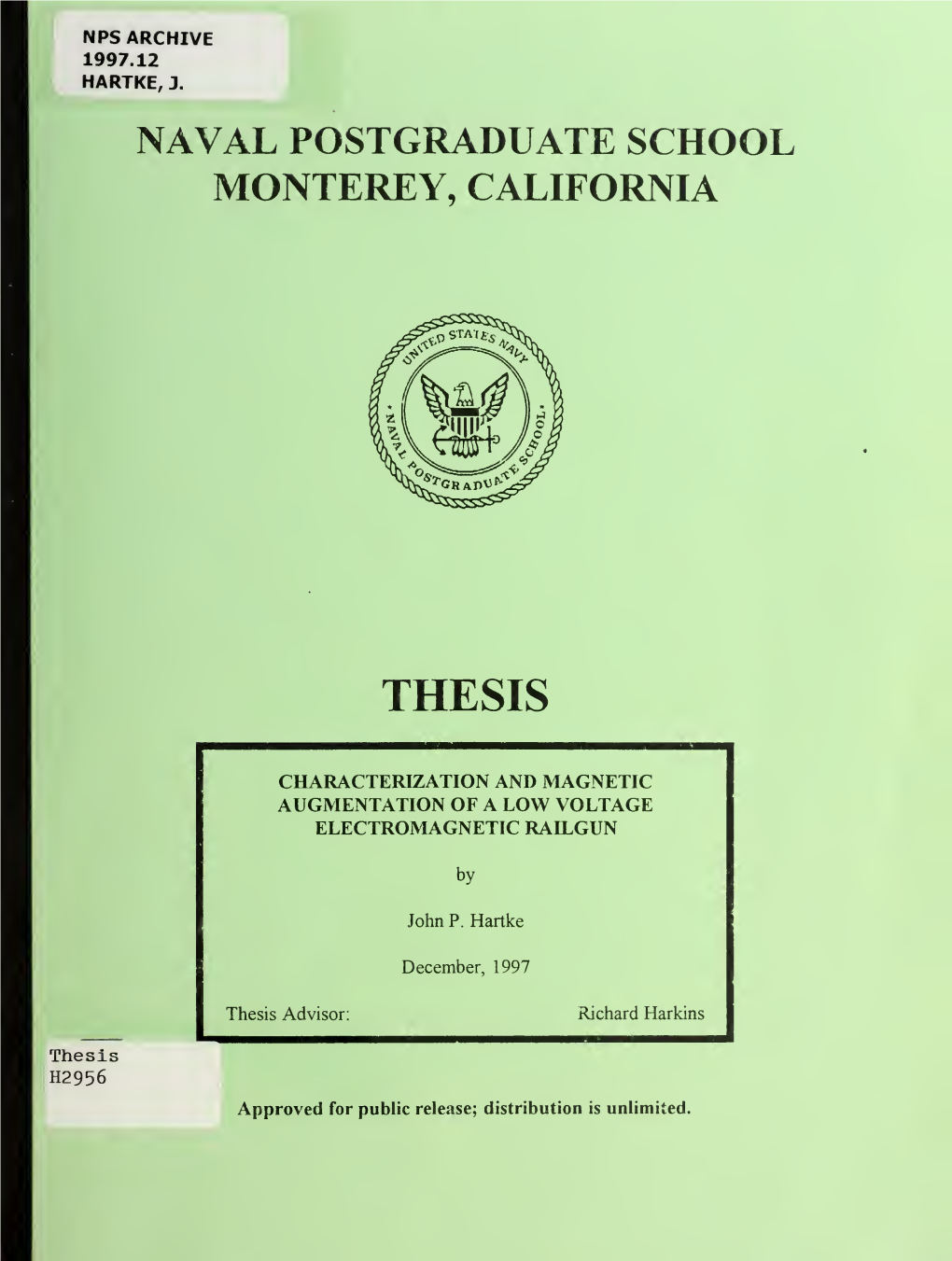
Load more
Recommended publications
-
The University of Texas at Austin
The University of Texas at Austin Institute for Advanced Technology, The University of Texas at Austin - AUSA - February 2006 IAT Talk 1358 Eraser Institute for Advanced Technology, The University of Texas at Austin - AUSA - February 2006 IAT Talk 1358 Transitioning EM Railgun Technology to the Warfighter Dr. Harry D. Fair, Director Institute for Advanced Technology The University of Texas at Austin The Governator is correct! • At the IAT, we are harnessing large quantities of electric energy to enable radically new capabilities for the warfighter. • These new electric weapons are capable of accelerating high energy hypervelocity projectiles Electric guns are real. from electric railguns on land, sea, and air platforms, and are capable of protecting these platforms by electromagnetic protection systems. Institute for Advanced Technology, The University of Texas at Austin - AUSA - February 2006 IAT Talk 1358 Hypervelocity Electromagnetic Railguns What are they? How do they work? Why change to electromagnetic energy? How can we use them? When can we have them? What are the implications for the Army and the Navy? Institute for Advanced Technology, The University of Texas at Austin - AUSA - February 2006 IAT Talk 1358 What is an Electromagnetic Railgun? Converts Electricity to Kinetic Energy The barrel can have any cross section - round, The accelerating Force square, rectangular is provided by Electromagnetic Forces and can accelerate projectiles to very high velocities Force Muzzle view We routinely launch projectiles to hypervelocities -
Pulsed Rotating Machine Power Supplies for Electric Combat Vehicles
Pulsed Rotating Machine Power Supplies for Electric Combat Vehicles W.A. Walls and M. Driga Department of Electrical and Computer Engineering The University of Texas at Austin Austin, Texas 78712 Abstract than not, these test machines were merely modified gener- ators fitted with damper bars to lower impedance suffi- As technology for hybrid-electric propulsion, electric ciently to allow brief high current pulses needed for the weapons and defensive systems are developed for future experiment at hand. The late 1970's brought continuing electric combat vehicles, pulsed rotating electric machine research in fusion power, renewed interest in electromag- technologies can be adapted and evolved to provide the netic guns and other pulsed power users in the high power, maximum benefit to these new systems. A key advantage of intermittent duty regime. Likewise, flywheels have been rotating machines is the ability to design for combined used to store kinetic energy for many applications over the requirements of energy storage and pulsed power. An addi - years. In some cases (like utility generators providing tran- tional advantage is the ease with which these machines can sient fault ride-through capability), the functions of energy be optimized to service multiple loads. storage and power generation have been combined. Continuous duty alternators can be optimized to provide Development of specialized machines that were optimized prime power energy conversion from the vehicle engine. for this type of pulsed duty was needed. In 1977, the laser This paper, however, will focus on pulsed machines that are fusion community began looking for an alternative power best suited for intermittent and pulsed loads requiring source to capacitor banks for driving laser flashlamps. -
Arxiv:1701.07063V2 [Physics.Ins-Det] 23 Mar 2017 ACCEPTED by IEEE TRANSACTIONS on PLASMA SCIENCE, MARCH 2017 1
This work has been accepted for publication by IEEE Transactions on Plasma Science. The published version of the paper will be available online at http://ieeexplore.ieee.org. It can be accessed by using the following Digital Object Identifier: 10.1109/TPS.2017.2686648. c 2017 IEEE. Personal use of this material is permitted. Permission from IEEE must be obtained for all other uses, including reprinting/republishing this material for advertising or promotional purposes, collecting new collected works for resale or redistribution to servers or lists, or reuse of any copyrighted component of this work in other works. arXiv:1701.07063v2 [physics.ins-det] 23 Mar 2017 ACCEPTED BY IEEE TRANSACTIONS ON PLASMA SCIENCE, MARCH 2017 1 Review of Inductive Pulsed Power Generators for Railguns Oliver Liebfried Abstract—This literature review addresses inductive pulsed the inductor. Therefore, a coil can be regarded as a pressure power generators and their major components. Different induc- vessel with the magnetic field B as a pressurized medium. tive storage designs like solenoids, toroids and force-balanced The corresponding pressure p is related by p = 1 B2 to the coils are briefly presented and their advantages and disadvan- 2µ tages are mentioned. Special emphasis is given to inductive circuit magnetic field B with the permeability µ. The energy density topologies which have been investigated in railgun research such of the inductor is directly linked to the magnetic field and as the XRAM, meat grinder or pulse transformer topologies. One therefore, its maximum depends on the tensile strength of the section deals with opening switches as they are indispensable for windings and the mechanical support. -
Booster Rookie Book Typical Kicker Layout
BOOSTER Table of Contents Foreword .................................................................................................................................... 3 Introduction................................................................................................................................ 4 Booster History and Design........................................................................................................ 5 Injection ..................................................................................................................................... 9 Gradient Magnets and Power Supplies......................................................................................17 Magnets .....................................................................................................................................18 GMPS........................................................................................................................................23 RF..............................................................................................................................................27 High Level.................................................................................................................................31 Low Level/Feedback..................................................................................................................32 Notching and Cogging...............................................................................................................37 -
Design and Optimization of an Electromagnetic Railgun
Michigan Technological University Digital Commons @ Michigan Tech Dissertations, Master's Theses and Master's Reports 2018 DESIGN AND OPTIMIZATION OF AN ELECTROMAGNETIC RAILGUN Nihar S. Brahmbhatt Michigan Technological University, [email protected] Copyright 2018 Nihar S. Brahmbhatt Recommended Citation Brahmbhatt, Nihar S., "DESIGN AND OPTIMIZATION OF AN ELECTROMAGNETIC RAILGUN", Open Access Master's Report, Michigan Technological University, 2018. https://doi.org/10.37099/mtu.dc.etdr/651 Follow this and additional works at: https://digitalcommons.mtu.edu/etdr Part of the Controls and Control Theory Commons DESIGN AND OPTIMIZATION OF AN ELECTROMAGNETIC RAIL GUN By Nihar S. Brahmbhatt A REPORT Submitted in partial fulfillment of the requirements for the degree of MASTER OF SCIENCE In Electrical Engineering MICHIGAN TECHNOLOGICAL UNIVERSITY 2018 © 2018 Nihar S. Brahmbhatt This report has been approved in partial fulfillment of the requirements for the Degree of MASTER OF SCIENCE in Electrical Engineering. Department of Electrical and Computer Engineering Report Advisor: Dr. Wayne W. Weaver Committee Member: Dr. John Pakkala Committee Member: Dr. Sumit Paudyal Department Chair: Dr. Daniel R. Fuhrmann Table of Contents Abstract ........................................................................................................................... 7 Acknowledgments........................................................................................................... 8 List of Figures ................................................................................................................ -
Permanent Magnet DC Motors Catalog
Catalog DC05EN Permanent Magnet DC Motors Drives DirectPower Series DA-Series DirectPower Plus Series SC-Series PRO Series www.electrocraft.com www.electrocraft.com For over 60 years, ElectroCraft has been helping engineers translate innovative ideas into reality – one reliable motor at a time. As a global specialist in custom motor and motion technology, we provide the engineering capabilities and worldwide resources you need to succeed. This guide has been developed as a quick reference tool for ElectroCraft products. It is not intended to replace technical documentation or proper use of standards and codes in installation of product. Because of the variety of uses for the products described in this publication, those responsible for the application and use of this product must satisfy themselves that all necessary steps have been taken to ensure that each application and use meets all performance and safety requirements, including all applicable laws, regulations, codes and standards. Reproduction of the contents of this copyrighted publication, in whole or in part without written permission of ElectroCraft is prohibited. Designed by stilbruch · www.stilbruch.me ElectroCraft DirectPower™, DirectPower™ Plus, DA-Series, SC-Series & PRO Series Drives 2 Table of Contents Typical Applications . 3 Which PMDC Motor . 5 PMDC Drive Product Matrix . .6 DirectPower Series . 7 DP20 . 7 DP25 . 9 DP DP30 . 11 DirectPower Plus Series . 13 DPP240 . 13 DPP640 . 15 DPP DPP680 . 17 DPP700 . 19 DPP720 . 21 DA-Series. 23 DA43 . 23 DA DA47 . 25 SC-Series . .27 SCA-L . .27 SCA-S . .29 SC SCA-SS . 31 PRO Series . 33 PRO-A04V36 . 35 PRO-A08V48 . 37 PRO PRO-A10V80 . -
Equivalence of Current–Carrying Coils and Magnets; Magnetic Dipoles; - Law of Attraction and Repulsion, Definition of the Ampere
GEOPHYSICS (08/430/0012) THE EARTH'S MAGNETIC FIELD OUTLINE Magnetism Magnetic forces: - equivalence of current–carrying coils and magnets; magnetic dipoles; - law of attraction and repulsion, definition of the ampere. Magnetic fields: - magnetic fields from electrical currents and magnets; magnetic induction B and lines of magnetic induction. The geomagnetic field The magnetic elements: (N, E, V) vector components; declination (azimuth) and inclination (dip). The external field: diurnal variations, ionospheric currents, magnetic storms, sunspot activity. The internal field: the dipole and non–dipole fields, secular variations, the geocentric axial dipole hypothesis, geomagnetic reversals, seabed magnetic anomalies, The dynamo model Reasons against an origin in the crust or mantle and reasons suggesting an origin in the fluid outer core. Magnetohydrodynamic dynamo models: motion and eddy currents in the fluid core, mechanical analogues. Background reading: Fowler §3.1 & 7.9.2, Lowrie §5.2 & 5.4 GEOPHYSICS (08/430/0012) MAGNETIC FORCES Magnetic forces are forces associated with the motion of electric charges, either as electric currents in conductors or, in the case of magnetic materials, as the orbital and spin motions of electrons in atoms. Although the concept of a magnetic pole is sometimes useful, it is diácult to relate precisely to observation; for example, all attempts to find a magnetic monopole have failed, and the model of permanent magnets as magnetic dipoles with north and south poles is not particularly accurate. Consequently moving charges are normally regarded as fundamental in magnetism. Basic observations 1. Permanent magnets A magnet attracts iron and steel, the attraction being most marked close to its ends. -
Permanent Magnet Design Guidelines
NOTE(2019): THIS ORGANIZATION (MMPA) IS OBSOLETE! MAGNET GUIDELINES Basic physics of magnet materials II. Design relationships, figures merit and optimizing techniques Ill. Measuring IV. Magnetizing Stabilizing and handling VI. Specifications, standards and communications VII. Bibliography INTRODUCTION This guide is a supplement to our MMPA Standard No. 0100. It relates the information in the Standard to permanent magnet circuit problems. The guide is a bridge between unit property data and a permanent magnet component having a specific size and geometry in order to establish a magnetic field in a given magnetic circuit environment. The MMPA 0100 defines magnetic, thermal, physical and mechanical properties. The properties given are descriptive in nature and not intended as a basis of acceptance or rejection. Magnetic measure- ments are difficult to make and less accurate than corresponding electrical mea- surements. A considerable amount of detailed information must be exchanged between producer and user if magnetic quantities are to be compared at two locations. MMPA member companies feel that this publication will be helpful in allowing both user and producer to arrive at a realistic and meaningful specifica- tion framework. Acknowledgment The Magnetic Materials Producers Association acknowledges the out- standing contribution of Parker to this and designers and manufacturers of products usingpermanent magnet materials. Parker the Technical Consultant to MMPA compiled and wrote this document. We also wish to thank the Standards and Engineering Com- mittee of MMPA which reviewed and edited this document. December 1987 3M July 1988 5M August 1996 December 1998 1 M CONTENTS The guide is divided into the following sections: Glossary of terms and conversion A very important starting point since the whole basis of communication in the magnetic material industry involves measurement of defined unit properties. -
Improvement of Electromagnetic Railgun Barrel Performance and Lifetime By
IMPROVEMENT OF ELECTROMAGNETIC RAILGUN BARREL PERFORMANCE AND LIFETIME BY METHOD OF INTERFACES AND AUGMENTED PROJECTILES A Thesis Presented to the Faculty of California Polytechnic State University San Luis Obispo In Partial Fulfillment of the Requirements for the Degree Master of Science in Aerospace Engineering by Aleksey Pavlov June 2013 c 2013 Aleksey Pavlov ALL RIGHTS RESERVED ii COMMITTEE MEMBERSHIP TITLE: Improvement of Electromagnetic Rail- gun Barrel Performance and Lifetime by Method of Interfaces and Augmented Pro- jectiles AUTHOR: Aleksey Pavlov DATE SUBMITTED: June 2013 COMMITTEE CHAIR: Kira Abercromby, Ph.D., Associate Professor, Aerospace Engineering COMMITTEE MEMBER: Eric Mehiel, Ph.D., Associate Professor, Aerospace Engineering COMMITTEE MEMBER: Vladimir Prodanov, Ph.D., Assistant Professor, Electrical Engineering COMMITTEE MEMBER: Thomas Guttierez, Ph.D., Associate Professor, Physics iii Abstract Improvement of Electromagnetic Railgun Barrel Performance and Lifetime by Method of Interfaces and Augmented Projectiles Aleksey Pavlov Several methods of increasing railgun barrel performance and lifetime are investigated. These include two different barrel-projectile interface coatings: a solid graphite coating and a liquid eutectic indium-gallium alloy coating. These coatings are characterized and their usability in a railgun application is evaluated. A new type of projectile, in which the electrical conductivity varies as a function of position in order to condition current flow, is proposed and simulated with FEA software. The graphite coating was found to measurably reduce the forces of friction inside the bore but was so thin that it did not improve contact. The added contact resistance of the graphite was measured and gauged to not be problematic on larger scale railguns. The liquid metal was found to greatly improve contact and not introduce extra resistance but its hazardous nature and tremendous cost detracted from its usability. -
An Inexpensive Hands-On Introduction to Permanent Magnet Direct Current Motors
AC 2011-1082: AN INEXPENSIVE HANDS-ON INTRODUCTION TO PER- MANENT MAGNET DIRECT CURRENT MOTORS Garrett M. Clayton, Villanova University Dr. Garrett M. Clayton received his BSME from Seattle University and his MSME and PhD in Mechanical Engineering from the University of Washington (Seattle). He is an Assistant Professor in Mechanical Engineering at Villanova University. His research interests focus on mechatronics, specifically modeling and control of scanning probe microscopes and unmanned vehicles. Rebecca A Stein, University of Pennsylvania Rebecca Stein is the Associate Director of Research and Educational Outreach in the School of Engi- neering and Applied Science at the University of Pennsylvania. She received her B.S. in Mechanical Engineering and Masters in Technology Management from Villanova University. Her background and work experience is in K-12 engineering education initiatives. Rebecca has spent the past 5 years involved in STEM high school programs at Villanova University and The School District of Philadelphia. Ad- ditionally, she has helped coordinate numerous robotics competitions such as BEST Robotics, FIRST LEGO League and MATE. Page 22.177.1 Page c American Society for Engineering Education, 2011 An Inexpensive Hands-on Introduction to Permanent Magnet Direct Current Motors Abstract Motors are an important curricular component in freshman and sophomore introduction to mechanical engineering (ME) courses as well as in curricula developed for high school science and robotics clubs. In order to facilitate a hands-on introduction to motors, an inexpensive permanent magnet direct current (PMDC) motor experiment has been developed that gives students an opportunity to build a PMDC motor from common office supplies along with a few inexpensive laboratory components. -
31295005665780.Pdf
DESIGN AND CONSTRUCTION OF A THREE HUNDRED kA BREECH SIMULATION RAILGUN by BRETT D. SMITH, B.S. in M.E. A THESIS IN -ELECTRICAL ENGINEERING Submitted to the Graduate Faculty of Texas Tech University in Partial Fulfillment of the Requirements for the Degree of MASTER OF SCIENCE IN ELECTRICAL ENGINEERING Jtpproved Accepted December, 1989 ACKNOWLEDGMENTS I would like to thank Dr. Magne Kristiansen for serving as the advisor for my grad uate work as well as serving as chairman of my thesis committee. I am also appreciative of the excellent working environment provided by Dr. Kristiansen at the laboratory. I would also like to thank my other two thesis committee members, Dr. Lynn Hatfield and Dr. Edgar O'Hair, for their advice on this thesis. I would like to thank Greg Engel for his help and advice in the design and construc tion of the experiment. I am grateful to Lonnie Stephenson for his advice and hard work in the construction of the experiment. I would also like to thank Danny Garcia, Mark Crawford, Ellis Loree, Diana Loree, and Dan Reynolds for their help in various aspects of this work. I owe my deepest appreciation to my parents for their constant support and encour agement. The engineering advice obtained from my father proved to be invaluable. 11 CONTENTS .. ACKNOWLEDGMENTS 11 ABSTRACT lV LIST OF FIGURES v CHAPTER I. INTRODUCTION 1 II. THEORY OF RAILGUN OPERATION 4 III. DESIGN AND CONSTRUCTION OF MAX II 27 Railgun System Design 28 Electrical Design and Construction 42 Mechanical Design and Construction 59 Diagnostics Design and Construction 75 IV. -
Recommended Techniques for Effective Maintainability
W..e_: NASA Technical Memorandum 4628 Recommended Techniques for Effective Maintainability A Continuous Improvement Initiative of the NASA Reliability and Maintainability Steering Committee December 1994 = # \ (NASA-TM-4628) RECOMMENOEO N95-31530 TECHNIQUES FOR EFFECTIVE MAINTAINABILITY. A CONTINUOUS IMPROVEMENT INITIATIVE OF THE NASA Unclas RELIABILITY AND MAINTAINABILITY STEERING COMMITTEE (NASA) 105 p H1/38 0060399 | w = J J Ira! J] ii U mmm mini mJ r - w J _J W IL u h_ PREFACE Current and future NASA programs face the challenge of achieving a high degree of mission success with a minimum degree of technical risk. Although technical risk has several . , w elements, such as safety, reliability, and performance, a proven track record of overall system effectiveness ultimately will be the NASA benchmark. This will foster the accomplishment of r mission objectives within cost and schedule expectations without compromising safety or w program risk. A key CharaCteristic of systems effeci_veness is the impiementation of appropriate levels of maintainability throughout the program life cycle. Maintainability is a process for assuring the ease by which a system can be restored to operation following a failure. It is an essential consideration for any program requiring ground n and/or on-orbit maintenance. TheiOffice of S_._ty"and Mission Assurance (OSMA) has undertaken a continuous improvement initiative to develop a technical roadmap that will provide a path toward achieving the desired degree of maintainability while realizing cost and schedule benefits. Although early life cycle costs are a characteristic of any assurance program, operational cost savings and improved system availability almost always result from __° a properlY administered maintainability assurance program.