Experimental Investigation of the Effect of Liquid Viscosity on Slug Flow in Small Diameter Bubble Column
Total Page:16
File Type:pdf, Size:1020Kb
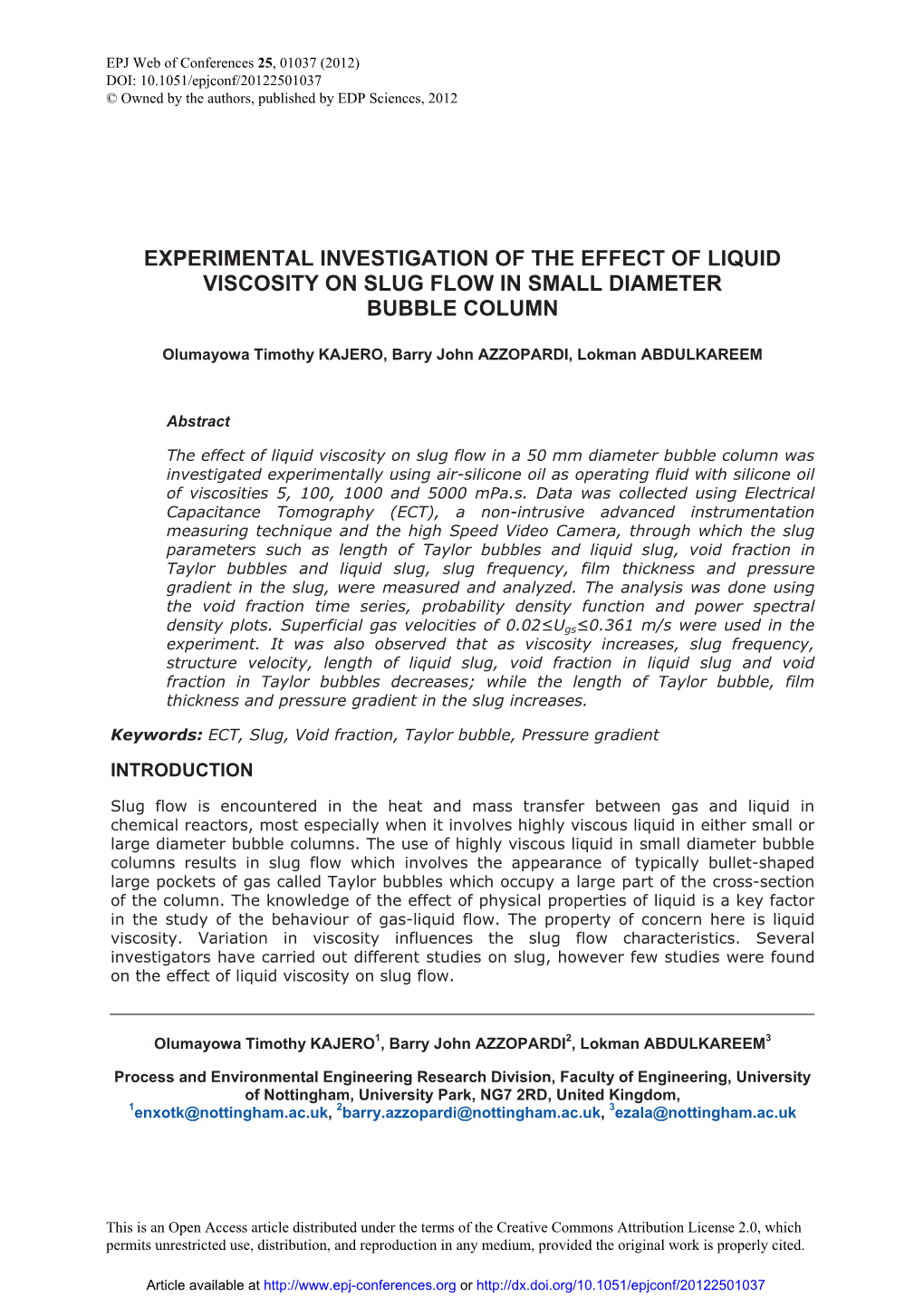
Load more
Recommended publications
-
(2020) Role of All Jet Drops in Mass Transfer from Bursting Bubbles
PHYSICAL REVIEW FLUIDS 5, 033605 (2020) Role of all jet drops in mass transfer from bursting bubbles Alexis Berny,1,2 Luc Deike ,2,3 Thomas Séon,1 and Stéphane Popinet 1 1Sorbonne Université, CNRS, UMR 7190, Institut Jean le Rond ࢚’Alembert, F-75005 Paris, France 2Department of Mechanical and Aerospace Engineering, Princeton University, Princeton, New Jersey 08544, USA 3Princeton Environmental Institute, Princeton University, Princeton, New Jersey 08544, USA (Received 12 September 2019; accepted 13 February 2020; published 10 March 2020) When a bubble bursts at the surface of a liquid, it creates a jet that may break up and produce jet droplets. This phenomenon has motivated numerous studies due to its multiple applications, from bubbles in a glass of champagne to ocean/atmosphere interactions. We simulate the bursting of a single bubble by direct numerical simulations of the axisymmetric two-phase liquid-gas Navier-Stokes equations. We describe the number, size, and velocity of all the ejected droplets, for a wide range of control parameters, defined as nondimensional numbers, the Laplace number which compares capillary and viscous forces and the Bond number which compares gravity and capillarity. The total vertical momentum of the ejected droplets is shown to follow a simple scaling relationship with a primary dependency on the Laplace number. Through a simple evaporation model, coupled with the dynamics obtained numerically, it is shown that all the jet droplets (up to 14) produced by the bursting event must be taken into account as they all contribute to the total amount of evaporated water. A simple scaling relationship is obtained for the total amount of evaporated water as a function of the bubble size and fluid properties. -
Investigation of Drag Coefficient and Virtual Mass Coefficient on Rising Ellipsoidal Bubbles
AN ABSTRACT OF THE THESIS OF Alexander M. Dueñas for the degree of Master of Science in Nuclear Engineering presented on December 5, 2019. Title: Investigation of Drag Coefficient and Virtual Mass Coefficient on Rising Ellipsoidal Bubbles Abstract approved: _____________________________________________________________________ Qiao Wu Wade R. Marcum Accurately describing drag and virtual mass forces in two-phase flows is crucial for high fidelity modeling of nuclear thermal hydraulic safety systems. This study compares existing drag coefficient, CD, correlations commonly used in computational fluid dynamics (CFD) applications for air bubbles to experimental data collected for ellipsoidal air bubbles of varying diameter. This study also measured the virtual mass coefficient on a cylinder rod using a method that considers viscous and wake effects. This experiment used velocity field measurements obtained with particle image velocimetry (PIV). An experimental flow loop has been built to inject air bubbles of varying diameter into an optically clear acrylic test section and had the capability to use a cylinder rod perpendicular to flow. A rigorous uncertainty analysis is presented for measured values which provided insight for improvements for future experimental studies. These experiments resulted in total, form, and skin drag coefficients to be directly measured with the nominal trend of increasing form drag for increasing bubble diameter experimentally confirmed. The virtual mass coefficient analysis demonstrated a method applicable for steady state conditions. This method was capable of retrieving the potential flow solution when the predicted drag work from the wake was removed and identified experimental setups useful for characterizing the influence of wake dynamics on virtual mass. ©Copyright by Alexander M. -
Effects of Physical Properties on the Behaviour of Taylor Bubbles
Computational Methods in Multiphase Flow V 355 Effects of physical properties on the behaviour of Taylor bubbles V. Hernández-Pérez, L. A. Abdulkareem & B. J. Azzopardi Department of Chemical and Environmental Engineering, Faculty of Engineering, University of Nottingham, UK Abstract Gas-liquid flow in vertical pipes, which is important in oil/gas wells and the risers from sea bed completions to FPSOs, was investigated to determine the effects of physical properties on the characteristics of the mixture such as void fraction, structure frequency and velocity as well as the shape of 3D structures. These are difficult to visualise using conventional optical techniques because even if the pipe wall is transparent, near-wall bubbles would mask the flow deep in the pipe. Therefore, more sophisticated methods are required. Two advanced wire mesh sensors (WMS) were used and the two-phase mixtures employed were air-water and air-silicone oil. The effect of fluid properties is accounted for in terms of the Morton number. It was found that the flow pattern is affected by the fluid properties as the results revealed that contrary to what is commonly assumed when modelling pipe flow, the flow is not symmetric, with a lot of distortion, which is even higher for the air-silicone oil mixture. Keywords: gas/liquid, vertical, wire mesh sensor, slug flow, void fraction, structure velocity. 1 Introduction One of the most common structures found in gas-liquid flows is the Taylor bubble; it is related directly to the slug flow pattern in upward vertical flow, for instance in oil/gas applications. This bubble occupies the greater part of the pipe cross section. -
On Dimensionless Numbers
chemical engineering research and design 8 6 (2008) 835–868 Contents lists available at ScienceDirect Chemical Engineering Research and Design journal homepage: www.elsevier.com/locate/cherd Review On dimensionless numbers M.C. Ruzicka ∗ Department of Multiphase Reactors, Institute of Chemical Process Fundamentals, Czech Academy of Sciences, Rozvojova 135, 16502 Prague, Czech Republic This contribution is dedicated to Kamil Admiral´ Wichterle, a professor of chemical engineering, who admitted to feel a bit lost in the jungle of the dimensionless numbers, in our seminar at “Za Plıhalovic´ ohradou” abstract The goal is to provide a little review on dimensionless numbers, commonly encountered in chemical engineering. Both their sources are considered: dimensional analysis and scaling of governing equations with boundary con- ditions. The numbers produced by scaling of equation are presented for transport of momentum, heat and mass. Momentum transport is considered in both single-phase and multi-phase flows. The numbers obtained are assigned the physical meaning, and their mutual relations are highlighted. Certain drawbacks of building correlations based on dimensionless numbers are pointed out. © 2008 The Institution of Chemical Engineers. Published by Elsevier B.V. All rights reserved. Keywords: Dimensionless numbers; Dimensional analysis; Scaling of equations; Scaling of boundary conditions; Single-phase flow; Multi-phase flow; Correlations Contents 1. Introduction ................................................................................................................. -
Chapter 2: Introduction
Chapter 2: Introduction 2.1 Multiphase flow. At first glance it may appear that various two or multiphase flow systems and their physical phenomena have very little in common. Because of this, the tendency has been to analyze the problems of a particular system, component or process and develop system specific models and correlations of limited generality and applicability. Consequently, a broad understanding of the thermo-fluid dynamics of two-phase flow has been only slowly developed and, therefore, the predictive capability has not attained the level available for single-phase flow analyses. The design of engineering systems and the ability to predict their performance depend upon both the availability of experimental data and of conceptual mathematical models that can be used to describe the physical processes with a required degree of accuracy. It is essential that the various characteristics and physics of two-phase flow should be modeled and formulated on a rational basis and supported by detailed scientific experiments. It is well established in continuum mechanics that the conceptual model for single-phase flow is formulated in terms of field equations describing the conservation laws of mass, momentum, energy, charge, etc. These field equations are then complemented by appropriate constitutive equations for thermodynamic state, stress, energy transfer, chemical reactions, etc. These constitutive equations specify the thermodynamic, transport and chemical properties of a specific constituent material. It is to be expected, therefore, that the conceptual models for multiphase flow should also be formulated in terms of the appropriate field and constitutive relations. However, the derivation of such equations for multiphase flow is considerably more complicated than for single-phase flow. -
Bibliography
Bibliography L. Prandtl: Selected Bibliography A. Sommerfeld. Zu L. Prandtls 60. Geburtstag am 4. Februar 1935. ZAMM, 15, 1–2, 1935. W. Tollmien. Zu L. Prandtls 70. Geburtstag. ZAMM, 24, 185–188, 1944. W. Tollmien. Seventy-Fifth Anniversary of Ludwig Prandtl. J. Aeronautical Sci., 17, 121–122, 1950. I. Fl¨ugge-Lotz, W. Fl¨ugge. Ludwig Prandtl in the Nineteen-Thirties. Ann. Rev. Fluid Mech., 5, 1–8, 1973. I. Fl¨ugge-Lotz, W. Fl¨ugge. Ged¨achtnisveranstaltung f¨ur Ludwig Prandtl aus Anlass seines 100. Geburtstags. Braunschweig, 1975. H. G¨ortler. Ludwig Prandtl - Pers¨onlichkeit und Wirken. ZFW, 23, 5, 153–162, 1975. H. Schlichting. Ludwig Prandtl und die Aerodynamische Versuchsanstalt (AVA). ZFW, 23, 5, 162–167, 1975. K. Oswatitsch, K. Wieghardt. Ludwig Prandtl and his Kaiser-Wilhelm-Institut. Ann. Rev. Fluid Mech., 19, 1–25, 1987. J. Vogel-Prandtl. Ludwig Prandtl: Ein Lebensbild, Erinnerungen, Dokumente. Uni- versit¨atsverlag G¨ottingen, 2005. L. Prandtl. Uber¨ Fl¨ussigkeitsbewegung bei sehr kleiner Reibung. Verhandlg. III. Intern. Math. Kongr. Heidelberg, 574–584. Teubner, Leipzig, 1905. Neue Untersuchungen ¨uber die str¨omende Bewegung der Gase und D¨ampfe. Physikalische Zeitschrift, 8, 23, 1907. Der Luftwiderstand von Kugeln. Nachrichten von der Gesellschaft der Wis- senschaften zu G¨ottingen, Mathematisch-Physikalische Klasse, 177–190, 1914. Tragfl¨ugeltheorie. Nachrichten von der Gesellschaft der Wissenschaften zu G¨ottingen, Mathematisch-Physikalische Klasse, 451–477, 1918. Experimentelle Pr¨ufung der Umrechnungsformeln. Ergebnisse der AVA zu G¨ottingen, 1, 50–53, 1921. Ergebnisse der Aerodynamischen Versuchsanstalt zu G¨ottingen. R. Oldenbourg, M¨unchen, Berlin, 1923. The Generation of Vortices in Fluids of Small Viscosity. -
Bubble Formation and Dynamics in a Quiescent High&
Bubble Formation and Dynamics in a Quiescent High-Density Liquid Indrajit Chakraborty and Gautam Biswas Dept. of Mechanical Engineering, Indian Institute of Technology, Kanpur 208016, India Dept. of Mechanical Engineering, Indian Institute of Technology, Guwahati 781039, India Satyamurthy Polepalle ADS Target Development Section, Bhabha Atomic Research Centre, Mumbai 400085, India Partha S. Ghoshdastidar Dept. of Mechanical Engineering, Indian Institute of Technology, Kanpur 208016, India DOI 10.1002/aic.14896 Published online June 18, 2015 in Wiley Online Library (wileyonlinelibrary.com) Gas bubble formation from a submerged orifice under constant-flow conditions in a quiescent high-density liquid metal, lead–bismuth eutectic (LBE), at high Reynolds numbers was investigated numerically. The numerical simulation was carried out using a coupled level-set and volume-of-fluid method governed by axisymmetric Navier–Stokes equations. The ratio of liquid density to gas density for the system of interest was about 15,261. The bubble formation regimes var- ied from quasi-static to inertia-dominated and the different bubbling regimes such as period-1 and period-2 with pairing and coalescence were described. The volume of the detached bubble was evaluated for various Weber numbers, We, at a given Bond number, Bo, with Reynolds number Re 1. It was found that at high values of the Weber number, the computed detached bubble volumes approached a 3/5 power law. The different bubbling regimes were identified quanti- tatively from the time evolution of the growing bubble volume at the orifice. It was shown that the growing volume of two consecutive bubbles in the period-2 bubbling regime was not the same whereas it was the same for the period-1 bubbling regime. -
Dynamics of an Initially Spherical Bubble Rising in Quiescent Liquid
ARTICLE Received 23 Sep 2014 | Accepted 12 Jan 2015 | Published 17 Feb 2015 DOI: 10.1038/ncomms7268 Dynamics of an initially spherical bubble rising in quiescent liquid Manoj Kumar Tripathi1, Kirti Chandra Sahu1 & Rama Govindarajan2 The beauty and complexity of the shapes and dynamics of bubbles rising in liquid have fascinated scientists for centuries. Here we perform simulations on an initially spherical bubble starting from rest. We report that the dynamics is fully three-dimensional, and provide a broad canvas of behaviour patterns. Our phase plot in the Galilei–Eo¨tvo¨s plane shows five distinct regimes with sharply defined boundaries. Two symmetry-loss regimes are found: one with minor asymmetry restricted to a flapping skirt; and another with marked shape evolution. A perfect correlation between large shape asymmetry and path instability is established. In regimes corresponding to peripheral breakup and toroid formation, the dynamics is unsteady. A new kind of breakup, into a bulb-shaped bubble and a few satellite drops is found at low Morton numbers. The findings are of fundamental and practical relevance. It is hoped that experimenters will be motivated to check our predictions. 1 Department of Chemical Engineering, Indian Institute of Technology Hyderabad, Yeddumailaram 502 205, India. 2 TIFR Centre for Interdisciplinary Sciences, Tata Institute of Fundamental Research, Narsingi, Hyderabad 500075, India. Correspondence and requests for materials should be addressed to K.C.S. (email: [email protected]). NATURE COMMUNICATIONS | 6:6268 | DOI: 10.1038/ncomms7268 | www.nature.com/naturecommunications 1 & 2015 Macmillan Publishers Limited. All rights reserved. ARTICLE NATURE COMMUNICATIONS | DOI: 10.1038/ncomms7268 he motion of a gas bubble rising due to gravity in a liquid measured experimentally. -
Simulations of Cavitation – from the Large Vapour Structures to the Small Bubble Dynamics
Simulations of cavitation – from the large vapour structures to the small bubble dynamics Aurélia Vallier June 2013 . Thesis for the degree of Doctor of Philosophy in Engineering. ISSN 0282-1990 ISRN LUTMDN/TMHP-13/1092-SE ISBN 978-91-7473-517-8 (print) ISBN 978-91-7473-518-5 (pdf) c Aurélia Vallier, June 2013 Division of Fluid Mechanics Department of Energy Sciences Faculty of Engineering Lund University Box18 S-221 00 LUND Sweden A Typeset in LTEX Printed by MediaTryck, Lund, May 2013. i Populärvetenskaplig sammanfattning Mycket få människor omkring oss vet innebörden av ordet kavitation, förutom de som såg filmen "The Hunt for Red October" och kan relatera kavitation till Sean Connery i en ubåt. Kavitation motsvarar bildandet av bubblor, som kan likna kokande vatten i en kastrull. Men den uppstår inte på grund av en hög temperatur utan på grund av ett lågt tryck. Den finns i de flesta tekniska anläggningar som innehåller vätska i rörelse. Problemet med kavitation är dess negativa konsekvenser. Till exempel orsakar den oljud vilket inte är onskvärt för en ubåt. Den kan också leda till förstörelse av ytor, vilket inte är onskvärt i en vattenturbin. Kavitation i vattenturbiner orsakar förändringar och instabilitet i strömningen, och im- plosion av bubblor. Detta resulterar i en minskning i effektivitet, vibrationer och erosion (skador på ytor). Kavitation kan undvikas om turbinen ställts tillräckligt låg, så att det statiska trycket är tillräckligt högt för att förhindra att vatten övergår till gasform. Men byggkostnaderna för en sådan låg inställning är mycket höga. Därför måste man hitta en kompromiss mellan motstridiga krav på en låg installationskostnad och undvikande av neg- ativa effekter från kavitation. -
Two-Phase Flow
Chapter 11 Two-Phase Flow M.M. Awad Additional information is available at the end of the chapter http://dx.doi.org/10.5772/76201 1. Introduction A phase is defined as one of the states of the matter. It can be a solid, a liquid, or a gas. Multiphase flow is the simultaneous flow of several phases. The study of multiphase flow is very important in energy-related industries and applications. The simplest case of multiphase flow is two-phase flow. Two-phase flow can be solid-liquid flow, liquid-liquid flow, gas-solid flow, and gas-liquid flow. Examples of solid-liquid flow include flow of corpuscles in the plasma, flow of mud, flow of liquid with suspended solids such as slurries, motion of liquid in aquifers. The flow of two immiscible liquids like oil and water, which is very important in oil recovery processes, is an example of liquid-liquid flow. The injection of water into the oil flowing in the pipeline reduces the resistance to flow and the pressure gradient. Thus, there is no need for large pumping units. Immiscible liquid-liquid flow has other industrial applications such as dispersive flows, liquid extraction processes, and co- extrusion flows. In dispersive flows, liquids can be dispersed into droplets by injecting a liquid through an orifice or a nozzle into another continuous liquid. The injected liquid may drip or may form a long jet at the nozzle depending upon the flow rate ratio of the injected liquid and the continuous liquid. If the flow rate ratio is small, the injected liquid may drip continuously at the nozzle outlet. -
History and Significance of the Morton Number in Hydraulic Engineering
Forum History and Significance of the Morton Number in Hydraulic Engineering Michael Pfister Investigations on Bubble Rise Velocity Research and Teaching Associate, Laboratory of Hydraulic Constructions (LCH), Ecole Polytechnique Fédérale de Lausanne (EPFL), Station 18, Dimensional Analysis CH-1015 Lausanne, Switzerland (corresponding author). E-mail: [email protected] The motion of gas bubbles in boiling water was of particular rel- evance in the early 19th century, as it affects the water circulation Willi H. Hager, F.ASCE in boilers of steamboats, steam engines, and pumps. Mechanical engineers focused on the latter to optimize their efficiency. Using Professor, Laboratory of Hydraulics, Hydrology and Glaciology (VAW), simplified approaches with stagnant water intended to allow for ETH Zurich, Wolfgang-Pauli-Str. 27, CH-8093 Zürich, Switzerland. analytical approaches, which were not successful according to E-mail: [email protected] Schmidt (1934a), however. He conducted a dimensional analysis of the bubble motion in stagnant fluids, finding that the related Forum papers are thought-provoking opinion pieces or essays processes may be described with the following dimensionless founded in fact, sometimes containing speculation, on a civil en- numbers gineering topic of general interest and relevance to the readership of the journal. The views expressed in this Forum article do not ¼ VbD ð1Þ necessarily reflect the views of ASCE or the Editorial Board of Rb ν the journal. V DOI: 10.1061/(ASCE)HY.1943-7900.0000870 F ¼ pffiffiffiffiffiffib ð2Þ b gD Introduction ρ 2 ¼ VbD ð3Þ Two-phase air-water flows occur frequently in hydraulic engineer- Wb σ ing. Their characteristics, particularly the depth-averaged air con- centrations, are of relevance for design. -
Problems and Answers
Problems and Answers Part I Problem I.1 Two parallel flat plates are immersed vertically in water. The clearance between the two plates is b. Calculate the elevation of the liquid due to capillary force. The surface tension, σ, and the density of water are 0.0725 N/m and 3 997 kg/m , respectively. The contact angle, θc,is5, and b ¼ 0.5 mm. Problem I.2 Calculate the absolute pressure on the bottom of the sea. The depth of 3 the sea, H, is 250 m, the density of seawater, ρsw, is 1,030 kg/m , and the atmospheric pressure, p0, is 1,013.3 h Pa. Problem I.3 Mercury is used as the working fluid for measuring the pressure of water by a U-shaped manometer. The water pressure at one entrance of the manometer, p1, is 300 k Pa, and pressure at the other entrance, p2, is 230 k Pa. Calculate the mercury column height, H. The densities of the mercury and water are 13,600 kg/m3 and 1,000 kg/m3, respectively. Answer to Problem I.1 Let the width of each plate be W. The following force balance holds: bWp0 þ ρgbWH ¼ bWp0 þ 2Wσ cos θc (PI.1) The height, H, is expressed by H ¼ 2σ cos θc=ðρgbÞ (PI.2) H ¼ 2 Â 0:0725 Â cos 5=ð997 Â 9:80 Â 0:5 Â 10À3Þ (PI.3) ¼ 0:0296 m ¼ 29:6mm M. Iguchi and O.J. Ilegbusi, Basic Transport Phenomena in Materials Engineering, 227 DOI 10.1007/978-4-431-54020-5, © Springer Japan 2014 228 Problems and Answers Answer to Problem I.2 p ¼ p0 þ ρ gH ¼ 1; 013:3 hPa þ 1; 030 Â 9:8 Â 250 Pa sw (PI.4) ¼ 101:33 kPa þ 2523:5 kPa ¼ 2:62 MPa Answer to Problem I.3 The mercury column height is calculated from Eqs.