Macro Stickies Content in Pulp: the “Pick-Up” Method (Five-Year Review of T 277 Pm-99 to Upgrade As an Official Method)
Total Page:16
File Type:pdf, Size:1020Kb
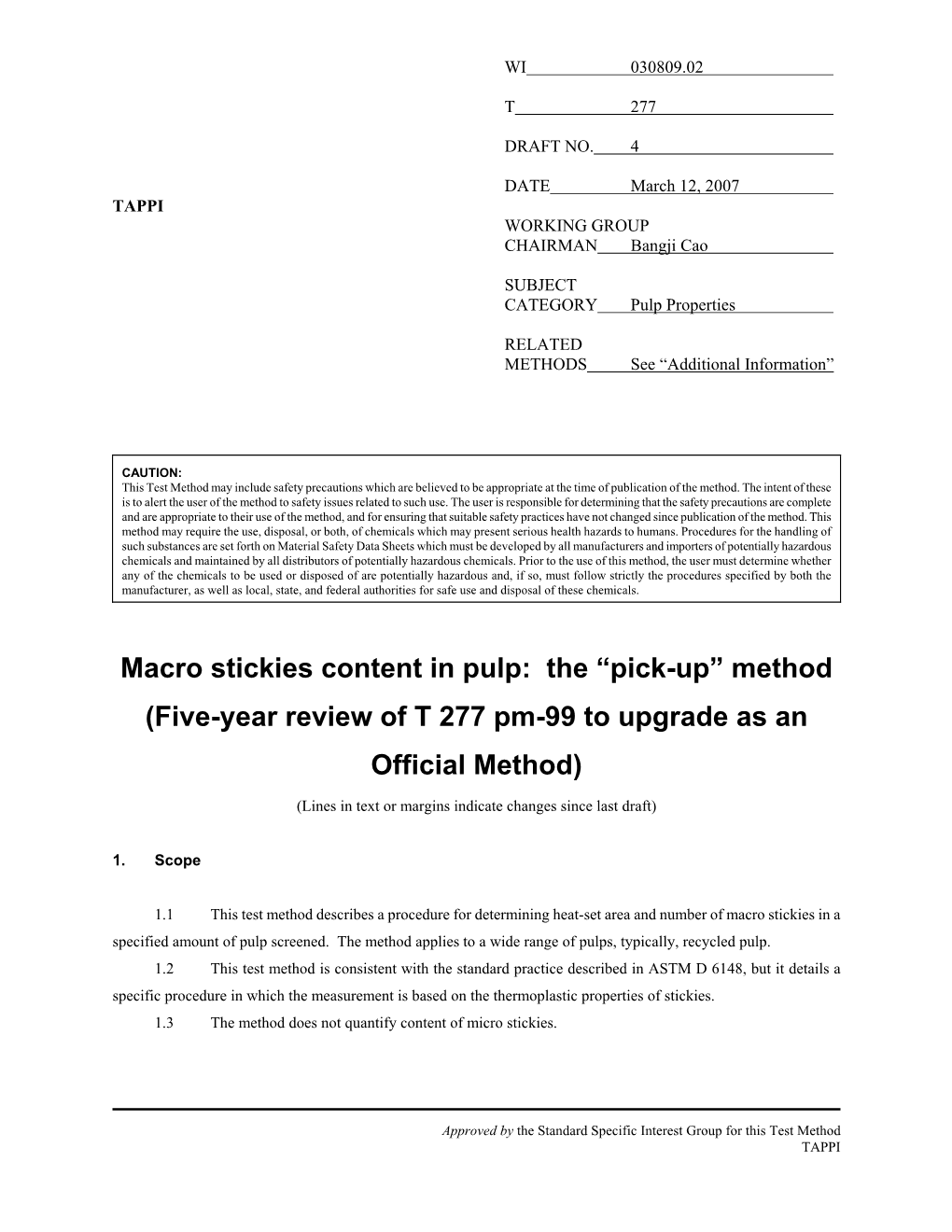
Load more
Recommended publications
-
Production of Sugars, Ethanol and Tannin from Spruce Bark and Recovered Fibres
IENCE SC • VTT SCIENCE • T S E Production of sugars, ethanol and tannin from N C O H I N spruce bark and recovered fibres S O I V Dissertation L • O S G Valorisation of forest industry-related side- and waste streams in a T 76 Y H • R G biorefinery context could help to reduce dependence on fossil I E L S H 76 E G A resources and introduce new value chains and sources of income I R H C for the forest industry. This thesis examined two abundant and H underutilized biomass streams spruce bark and recovered fibres as biorefinery feedstocks for the production of sugars, ethanol and tannin. Hot water extraction of tannins from spruce bark, steam explosion to reduce the recalcitrance of the feedstock towards hydrolytic Production of sugars, ethanol and tannin from spruce... enzymes, enzymatic hydrolysis of bark carbohydrates and fermentation of released sugars to ethanol were demonstrated and the effect of main process parameters studied. Recovered fibres were fractionated from solid recovered fuel, a standardised combustion fuel composed mainly of packaging waste, and the composition and enzymatic digestibility of the material were determined. The effect of pretreatment, solids loading and the use of surfactants on hydrolysis yield was studied. Selected steps for processing spruce bark and recovered fibres were scaled up from laboratory- to small pilot scale.The results of the work carried out in this thesis indicate that the biorefinery concepts presented for spruce bark and recovered fibres have technical potential for industrial application. Production -
What Happens to Cellulosic Fibers During Papermaking and Recycling? a Review
PEER-REVIEWED REVIEW ARTICLE ncsu.edu/bioresources WHAT HAPPENS TO CELLULOSIC FIBERS DURING PAPERMAKING AND RECYCLING? A REVIEW Martin A. Hubbe,* Richard A. Venditti, and Orlando J. Rojas Both reversible and irreversible changes take place as cellulosic fibers are manufactured into paper products one or more times. This review considers both physical and chemical changes. It is proposed that by understanding these changes one can make better use of cellulosic fibers at various stages of their life cycles, achieving a broad range of paper performance characteristics. Some of the changes that occur as a result of recycling are inherent to the fibers themselves. Other changes may result from the presence of various contaminants associated with the fibers as a result of manufacturing processes and uses. The former category includes an expected loss of swelling ability and decreased wet-flexibility, especially after kraft fibers are dried. The latter category includes effects of inks, de-inking agents, stickies, and additives used during previous cycles of papermaking. Keywords: Paper recycling, Drying, Deinking, Hornification, Inter-fiber bonding, Refining, Fines, Fiber length, Conformability Contact information: Department of Forest Biomaterials Science and Engineering, Box 8005, North Carolina State University, Raleigh, NC 27695-8005, USA; *Corresponding author: [email protected] INTRODUCTION Cellulosic fibers can change significantly when formed into a wet web of paper and subsequently subjected to such processes as pressing, drying, printing, storage, repulping, and deinking. Some of the changes can be subtle. Often it is possible to substitute recovered fibers in place of virgin fibers used for the production of paper or paperboard. On the other hand, characteristic differences between recycled fibers and virgin fibers (fresh from pulping wood, not recycled) can be expected; many of these can be attributed to drying. -
Stickies Detection Methods Macro and Micro Detailed Report
FINAL REPORT January 31, 2003 CONTAINERBOARD GROUP AMERICAN FOREST & PAPER ASSOCIATION Project Title: Evaluation of Various Adhesive Contaminant Analysis Methods for the Use in Old Corrugated Container Recycling Plants Names of Principal Investigators: Richard A. Venditti and Hou-min Chang Institution: North Carolina State University tel. (919) 515-6185 Dept. of Wood and Paper Science fax. (919) 515-6302 Raleigh NC 27695-8005 email: [email protected] TABLE OF CONTENTS Page: Executive Summary 2 Introduction 3 Literature Review 4 Materials and Methods 5 Stickies Test Methods: Macro Stickies Tests 5 Stickies Test Methods: Micro Stickies Tests 8 Materials for Testing 10 Results and Discussion 12 Macro-stickies Results 12 Micro-stickies Results 17 Evaluations of Stream-lined Tests 21 Estimates of Time and Labor Necessary for the Various 22 Stickies Test Methods. Evaluation of Stickies Removal Across a Water Clarifier 24 Overall Stickies Test Methods Recommendations for 25 Various Applications in an OCC Recycle Mill Conclusions 29 Figures 30 1 EXECUTIVE SUMMARY This project involves critically evaluating different test methods for their ability to detect stickies contaminants in old corrugated container (OCC) recycling plants. Tests were broadly classified as either macro or micro stickies test methods based on standard industrial terms. The macro stickies test methods evaluated were a bleaching and dyeing of handsheets, Port Townsend Method 1 (involves dyeing handsheets with black dye followed by image analysis), Port Townsend Method 2 (involves dyeing lab-screened rejects on filter pads with black dye followed by image analysis), Tappi Method 277 (involves pressing lab- screened rejects against a white coated material that transfers to stickies followed by image analysis), and a deposition method in which stickies are deposited onto a sample of a paper machine wire. -
Adhesive Contaminants (Stickies) and Methods for Removal
257 ADHESIVE CONTAMINANTS (STICKIES) AND METHODS FOR REMOVAL JOHN H. KLUNGNESS* AND MAHENDHA R. DOSHI** *USDA Forest Service, Forest Products Laboratory, Madison, WI 53705 **D~shi & Associates Inc.. Marathon Engineers/Architects/Planners, Inc. Appleton, WI ABSTRACT A variety of adhesive contaminants (“stickies”) are encountered in wastepapers. They are broadly classified as hot melts, pressure-sensitive adhesives, and lattices. Their properties and control methods are discussed. Specifically, control methods include furnish selection, improved pulping end deflaking. well-designed screening end cleaning systems, and dispersion end additives to detackify or stabilize stickies, or both. A new technology is also discussed regarding it’s possible application for controlling stickie contaminants. Test methods for measuring stickies are also reviewed. INTRODUCTION Large amounts of wastepaper are generated every day in the United States and interest in its reuse has increased steadily due to environmental concerns and improved economics. In 1990, for example, 28.9 million tons of wastepaper were collected for recycling. By 1995, that amount is expected to increase to almost 40 million tons with a collection rate of almost 40% [1]. To facilitate the use of secondary fibers, sticky contaminants, or "stickies,” must be controlled [2]. CLASSIFICATION AND PROPERTIES OF STICKIES Wastepaper bales usually contain extraneous materials such as sand, glass, staples, nails, inks, coatings, plastic, styrofoam, wax, EVA (ethylene vinyl acetate), SBR (styrene butadiene rubber), etc. A particularly troublesome contaminant in wastepaper is “stickies” which, in their original state, were used as paper adhesives. Inks end coatings can also be a source of stickies. Four primary components of inks include pigment, vehicle, binder, and modifier. -
Enzymatic Stickies Control in MOW, OCC, and ONP Furnishes
James W. Fitzhenry Philip M. Hoekstra Dan Glover Senior Development Specialist Development Group Manager Project Manager Buckman Laboratories Buckman Laboratories Buckman Laboratories 1256 N. Mclean Blvd. 1256 N. Mclean Blvd 1256 N. Mclean Blvd Memphis, TN 38108 Memphis, TN 38108 Memphis, TN 38108 . Abstract Stickies remain as one of the major obstacles in the manufacture of quality paper using recycled fiber sources such as OCC, MOW, and ONP. A combination of proper water clarification, effective screening and cleaning practices, and low impact repulping will allow for the mechanical removal of a majority of stickies. However, stickie contaminants often remain in the process even after peak mechanical efficiencies for stickies removal are attained. The chemical control of stickies is the next tool for a papermaker's use. Some new effective tools in this arena are enzymes. Enzymes are gaining wider acceptance in the pulp and paper industry for a variety of applications such as pulp mill and paper machine boilouts, deposit control by dispersion of accumulated slime, pitch control, drainage assistance as well as other uses. A recent area of research involves using enzymes for the control of stickies. This paper describes laboratory work done in the search for an enzyme that will act on stickies. Evidence of action on stickies could be shown if the enzyme reduced either the size or the number of stickies. Laboratory data has provided this evidence. We will discuss work done on a number of different furnishes, and the effect of enzymes in reduction of stickies. Introduction Secondary fiber contaminants are a major issue in most recycled mills throughout the U.S., as the amount of recycled fibers such as mixed office waste (MOW), old corrugated containers (OCC), and old newsprint (ONP) used per ton of paper produced increases across the country (1). -
Size Distribution Analysis of Microstickies Treated by Enzyme Mixtures in Papermaking Whitewater YANAN TANG, BO LI, SHENGFANG GENG, CARL HOUTMAN, and SHUBIN WU
PEER-REVIEWED RECYCLING Size distribution analysis of microstickies treated by enzyme mixtures in papermaking whitewater YANAN TANG, BO LI, SHENGFANG GENG, CARL HOUTMAN, AND SHUBIN WU ABSTRACT: Microstickies present a formidable challenge for papermakers. Many strategies have been explored to control them. Enzyme treatment is a promising technology, but the mechanism of its action has not been deter- mined, thus inhibiting further application of this new technology. This study investigated characteristics and size dis- tributions of microstickies treated by esterase-cellulase mixtures. Determination of particle size and number was accomplished using a modified flow cytometer, which combined streaming capillary flow, laser-based particle size analysis and fluorescent dye tracing. The results showed that treatment of samples with enzyme mixtures induced size reduction of the larger microstickies. This effect was most dramatic for 1:1 ratios of esterase to cellulase. The treated particles were more stable than untreated ones. The smaller microstickies treated with some ratios of ester- ase and cellulase tended to aggregate over time. The behaviors of microstickies treated by enzyme mixtures were only slightly affected by temperature and shearing action. The surface physicochemical characteristics of these par- ticles indicated that changes of these basic properties affected the whole whitewater system and resulted in a new equilibrium among all the particles. Application: This work provides a new method for controlling microstickies and could serve as a valuable refer- ence for the future application of enzymes in papermaking. he annual global production and consumption of and flotation [20,21]. Removal of the smaller stickies (70%– Tpaper and paperboard have recently reached almost 90% of stickies) is challenging [8]. -
Paper Recycling Technology Detailed Part 3
Lecture Refining of Recovered Fibers Several Slides Courtesy of Dr. Med Byrd. What is Refining? Refining is a physical treatment performed on pulp fibers to improve their papermaking characteristics It is essential to the production of strong, smooth, useful paper Several Slides Courtesy of Dr. Med Byrd. Why do we need refining? Increasing bonding area by: Collapsing hollow cell walls into flat ribbons Fraying the fiber surface – “fibrillation” Making the fibers more flexible and conformable, delaminating the wall Cutting some of the longer fibers into smaller lengths to help formation Courtesy of M. Hubbe Refining The effects of refining on freeness, density, tear index, and tensile index in virgin bleached kraft pulps Secondary Fibers, Tappi Fiber Structure Thin primary wall (P), which is delicate and easily removed Secondary wall has three layers S1 – thin and not easily wetted S2 – 70-85% of total mass; easily wetted and swollen S3 - thin, waxy, warty Secondary Fibers, Tappi Fiber Structure Refining damages and removes the Primary and S1 wall layers, exposing the S2 layer Once the S2 layer is exposed and swollen, mechanical action causes the layer to delaminate and collapse Mechanical action also fibrillates the surface, cuts some fibers, and makes them less stiff and more Photomicrograph showing a refined fiber conformable with fibrillation on the surface Refining: Subprocesses The Refining Action The mechanical action required for proper refining is not a simple brushing, cutting, grinding or pounding Rather, -
Chemical Characterization and Enzymatic Control of Stickies in Kraft Paper Production
polymers Article Chemical Characterization and Enzymatic Control of Stickies in Kraft Paper Production Lourdes Ballinas-Casarrubias 1, Guillermo González-Sánchez 2, Salvador Eguiarte-Franco 1, Tania Siqueiros-Cendón 1 , Sergio Flores-Gallardo 2 , Eduardo Duarte Villa 3, Miguel de Dios Hernandez 3, Beatriz Rocha-Gutiérrez 1 and Quintín Rascón-Cruz 1,* 1 Facultad de Ciencias Químicas, Universidad Autónoma de Chihuahua, Circuito Universitario s/n, Campus Universitario No. 2, Chihuahua C.P. 31125, Mexico; [email protected] (L.B.-C.); [email protected] (S.E.-F.); [email protected] (T.S.-C.); [email protected] (B.R.-G.) 2 Centro de Investigación en Materiales Avanzados, S.C. Laboratorio Nacional de Nanotecnología, Miguel de Cervantes No. 120, Chihuahua C.P. 31109, Mexico; [email protected] (G.G.-S.); sergio.fl[email protected] (S.F.-G.) 3 Grupo COPAMEX, Ave. de la Juventud no. 280, San Nicolás de los Garza C.P. 66450, Mexico; [email protected] (E.D.V.); [email protected] (M.d.D.H.) * Correspondence: [email protected] Received: 30 October 2019; Accepted: 12 December 2019; Published: 20 January 2020 Abstract: Paper recycling has increased in recent years. A principal consequence of this process is the problem of addressing some polymeric components known as stickies. A deep characterization of stickies sampled over one year in a recycled paper industry in México was performed. Based on their chemical structure, an enzymatic assay was performed using lipases. Compounds found in stickies by Fourier-transform infrared spectrometry were poly (butyl-acrylate), dioctyl phthalate, poly (vinyl-acetate), and poly (vinyl-acrylate). -
Tackiness Reducing of the Stickies Surfaces by Inorganic Agents and Organic Polymers
WOOD RESEARCH 63 (6): 2018 1013-1020 TACKINESS REDUCING OF THE STICKIES SURFACES BY INORGANIC AGENTS AND ORGANIC POLYMERS Vladimir Kuna, Jozef Balbercak, Andrej Pazitny, Albert Russ, Stefan Bohacek Pulp and Paper Research Institute Bratislava, Slovak Republic Vladimir Ihnat Slovak Forest Products Research Institute Bratislava, Slovak Republic (Received April 2018) ABSTRACT This paper present the results of application of inorganic minerals and organic polymers for elimination of sticky impurities "macrostickies" in the processing of recovered paper. The impact of individual agents has been monitored on different species of suspensions. On the dark suspension of recycled fibres VL5 with a brightness 53% ISO and an ash content of 17.6%, and the suspension VL1 with a brightness 64% ISO and an ash content of 29.4%. From inorganic minerals, the highest efficiency was achieved in the elimination of macrostickies using bentonite Hydrocol OT. At a dose of 5 kg bentonite.t-1 b.d. recycled fibres efficiency of 65.1% for suspension VL5 and 58.7% for VL1 was achieved. The highest performance of the Acefloc 2550 was achieved from the polymers. When applied to the VL5 suspension, the macrostickies were reduced by 57.1%, and when applied to the VL1 suspension, the macrostickies content dropped by 56.5%. KEYWORDS: Macrostickies, organic polymers, inorganic fillers, average particle size, montmorillonite. INTRODUCTION Increasing the recycling of paper also increases the content of impurities and undesirable substances in the recovered paper (Kuňa et al. 2016), thereby deteriorating its quality. There are various sources and types of impurities in the recovered paper (Holik 2000). These are various microbiological impurities, insoluble impurities such as adhesives, resins, fillers, wet strength agents, and soluble colloidal materials such as coatings, latexes, which combine a variety of sticky impurities called micro and macrostickies. -
Enzymatic Removal of Stickie Contaminants
ENZYMATIC REMOVAL OF STICKIE binders, and high lignin-containing fibers are some sources CONTAMINANTS of stickies that appear during reprocessing wastepapers. Postal stamps, address labels, post-it notes, and self-seal Marguerite S. Sykes John H. Klungness envelopes are among the most common sources of PSAs in Forest Products Technologist Chemical Engineer office papers. The use of PSAs is increasing rapidly; corre- Freya Tan Said Abubakr spondingly, the stickie problem is escalating. Chemical Engineer Supervisory Chemical Engineer USDA Forest Service USDA Forest Service 1 Stickies precipitate on process equipment, redeposit on pulp Forest Products Laboratory Forest Products Laboratory fibers, or pass into process water, only to agglomerate unex- Madison, WI 53705-2398 Madison, WI 53705-2398 pectedly and deposit when least desired or expected. In all cases, stickies contaminate pulp, cause mill shut-downs as a result of fouling of machinery, and cause breaks in the paper ABSTRACT during papermaking or printing. Control of stickies is a costly mill problem (4) that is growing to epidemic propor- tions. Problems associated with stickies are limiting the use Stickie contaminants are a costly problem for both recyclers of recycled fiber now that there is little competitive of market pulp and the papermakers using it. Increased use of economic edge over using virgin fiber. pressure sensitive adhesives (PSAs) has compounded this problem in recycled furnishes. Preliminary laboratory ex- Contaminants, including stickies, are removed most effec- periments using commercially available enzyme preparations tively when they are large enough to be screened out of pulp at the ambient pH of the paper furnish (neutral pH range) slurries, have a density suitable for removal in cleaners, or have resulted in a significant reduction of all residual con- are hydrophobic enough and of the appropriate size to be taminants, including stickies. -
Us 2019 / 0177913 A1
US 20190177913A1 ( 19) United States (12 ) Patent Application Publication ( 10) Pub . No. : US 2019 /0177913 A1 Basilio et al. ( 43 ) Pub . Date : Jun . 13 , 2019 ( 54 ) REMOVAL OF STICKIES IN THE 2) U . S . CI. RECYCLING OF PAPER AND PAPERBOARD CPC . .. .. .. .. D21C 5 /022 ( 2013 .01 ) ; D214 1 /00 ( 2013. 01 ); D21H 11/ 14 ( 2013 .01 ) (71 ) Applicant: Thiele Kaolin Company, Sandersville , GA (US ) (72 ) Inventors : Cesar I . Basilio , Milledgeville , GA (57 ) ABSTRACT (US ) ; Steven W . Sheppard , Sandersville , GA (US ) Removal of stickies from waste paper and paperboard is obtained with the use of a modified kaolin -based stickies (21 ) Appl. No. : 15 /834 , 497 removal composition . The modified kaolin - based stickies ( 22) Filed : Dec . 7 , 2017 removal composition is produced by modifying the kaolin clay, separating the modified kaolin clay from the non Publication Classification reactive kaolin clay, and then adding a nonionic surfactant to (51 ) Int. Ci. the modified kaolin -based particles . Removal of stickies is D21C 5 / 02 ( 2006 .01 ) improved by the use of this modified kaolin -based stickies D21H 11/ 14 (2006 . 01) removal composition during the recycling of the waste paper D21 ) 1 / 00 ( 2006 . 01 ) and paperboard . US 2019 /0177913 A1 Jun . 13 , 2019 REMOVAL OF STICKIES IN THE ies control in which stickies are removed from the product RECYCLING OF PAPER AND PAPERBOARD would be a superior solution than those presented in the prior art, because such a method would not involve the use of TECHNICAL FIELD additional chemicals, polymers, dispersants or other addi [ 0001] The present invention relates to the removal of tives , at an additional production cost , and would provide a stickies from waste paper and paperboard . -
TAPPI Standards: Regulations and Style Guidelines
TAPPI Standards: Regulations and Style Guidelines REVISED January 2018 1 Preface This manual contains the TAPPI regulations and style guidelines for TAPPI Standards. The regulations and guidelines are developed and approved by the Quality and Standards Management Committee with the advice and consent of the TAPPI Board of Directors. NOTE: Throughout this manual, “Standards” used alone as a noun refers to ALL categories of Standards. For specific types, the word “Standard” is used as an adjective, e.g., “Standard Test Method,” “Standard Specification,” “Standard Glossary,” or “Standard Guideline.” If you are a Working Group Chairman preparing a Standard or reviewing an existing Standard, you will find the following important information in this manual: • How to write a Standard Test Method using proper terminology and format (Section 7) • How to write TAPPI Standard Specifications, Glossaries, and Guidelines using proper terminology and format (Section 8) • What requirements exist for precision statements in Official and Provisional Test Methods (Sections 4.1.1.1, 4.1.1.2, 6.4.5, 7.4.17). • Use of a checklist to make sure that all required sections have been included in a Standard draft (Appendix 4). • How Working Group Chairman, Working Groups, and Standard-Specific Interest Groups fit into the process of preparing a Standard (Section 6.3, 6.4.1, 6.4.2, 6.4.3, 6.4.4, 6.4.6, 6.4.7). • How the balloting process works (Sections 6.4.6, 6.4.7, 6.4.8, 6.4.9) • How to resolve comments and negative votes (Sections 9.5, 9.6, 9.7) NOTE: This document covers only the regulations for TAPPI Standards, which may include Test Methods or other types of Standards as defined in these regulations.