High Performance Micro-Scale Light Emitting Diode Display
Total Page:16
File Type:pdf, Size:1020Kb
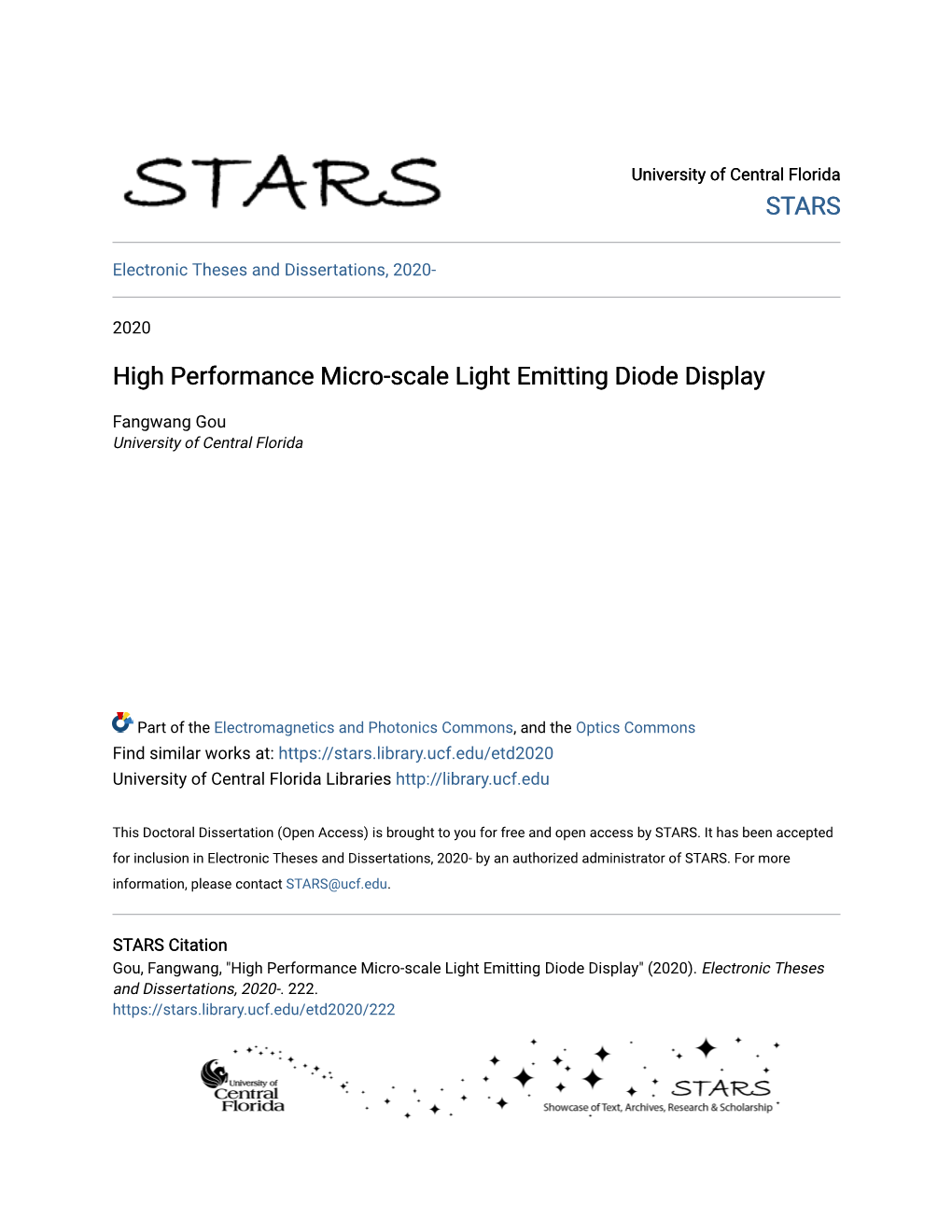
Load more
Recommended publications
-
Idw ’08 the 15Th International Display Workshops
IDW ’08 THE 15TH INTERNATIONAL DISPLAY WORKSHOPS Workshops on • LC Science and Technologies • Active Matrix Displays • FPD Manufacturing, Materials and Components • Plasma Displays • EL Displays and Phosphors • Field Emission Display and CRT • Organic LED Displays • 3D/Hyper-Realistic Displays and Systems • Applied Vision and Human Factors • Projection and Large-Area Displays, and Their Components • Electronic Paper • MEMS for Future Displays and Related Electron Devices • Display Electronic Systems Topical Sessions on • Display Technologies for Professional Use • Flexible Displays • Final Program Toki Messe Niigata Convention Center Niigata, Japan December 3(Wed) – 5(Fri), 2008 CONTENTS Program Highlights............................................................................... 5 General Information.............................................................................. 9 Hotel and Travel Information............................................................... 12 Plenary Sessions Wednesday, December 3 IDW ’08 Opening ............................................................................... 16 IDW ’08 Keynote Addresses.............................................................. 16 IDW ’08 Invited Address.................................................................... 17 Workshop on LC Science and Technologies Wednesday, December 3 Opening............................................................................................... 18 LCT1 Fascinating LC Materials ...................................................... -
Pinhole Microled Array As Point Source Illumination for Miniaturized Lensless Cell Monitoring Systems †
Proceedings Pinhole microLED Array as Point Source Illumination for Miniaturized Lensless Cell Monitoring Systems † Shinta Mariana 1,*, Gregor Scholz 1, Feng Yu 1, Agus Budi Dharmawan 1,2, Iqbal Syamsu 1,3, Joan Daniel Prades 4, Andreas Waag 1 and Hutomo Suryo Wasisto 1,* 1 Institute of Semiconductor Technology (IHT) and Laboratory for Emerging Nanometrology (LENA), Technische Universität Braunschweig, 38106 Braunschweig, Germany; gregor.scholz@tu‐braunschweig.de (G.S.); f.yu@tu‐braunschweig.de (F.Y.); a.dharmawan@tu‐braunschweig.de (A.B.D.); i.syamsu@tu‐braunschweig.de (I.S.); a.waag@tu‐braunschweig.de (A.W.) 2 Faculty of Information Technology, Universitas Tarumanagara, 11440 Jakarta, Indonesia 3 Research Center for Electronics and Telecommunication, Indonesian Institute of Sciences (LIPI), 40135 Bandung, Indonesia 4 MIND, Department of Electronic and Biomedical Engineering, Universitat de Barcelona, 08028 Barcelona, Spain; [email protected] * Correspondence: s.mariana@tu‐braunschweig.de (S.M.); h.wasisto@tu‐braunschweig.de (H.S.W.) † Presented at the Eurosensors 2018 Conference, Graz, Austria, 9–12 September 2018. Published: 21 November 2018 Abstract: Pinhole‐shaped light‐emitting diode (LED) arrays with dimension ranging from 100 μm down to 5 μm have been developed as point illumination sources. The proposed microLED arrays, which are based on gallium nitride (GaN) technology and emitting in the blue spectral region (λ = 465 nm), are integrated into a compact lensless holographic microscope for a non‐invasive, label‐free cell sensing and imaging. From the experimental results using single pinhole LEDs having a diameter of 90 μm, the reconstructed images display better resolution and enhanced image quality compared to those captured using a commercial surface‐mount device (SMD)‐based LED. -
UV Cured Flexible Cholesteric Liquid Crystal Displays
UV Cured Flexible Cholesteric Liquid Crystal Displays Tod Schneider, Erica Montbach, Don Davis, Sean Franklin, Diaz McDaniel, Mark Lightfoot, Nithya Venkataraman, Forrest Nicholson, Asad Khan, and J. William Doane Kent Displays, Inc. Kent, OH, USA Abstract Flexible Cholesteric liquid crystal displays have been rapidly maturing into a strong contender in the flexible display market. Encapsulation of the Cholesteric liquid crystal permits the use of flexible plastic substrates and roll-to-roll production. Recent advances include ultra-thin displays, laser-cut segmented displays of variable geometry, and smart card applications. Exciting technologies such as UV curing, and simultaneous laser-edge sealing/singulation enable high volume production, excellent quality control and non-traditional display geometries and formats. Keywords: UV Cure, Flexible Displays, Roll-to-Roll, Plastic Substrates, Cholesteric Liquid Crystals, Bistable Introduction Nearly every commercial liquid crystal display (LCD) manufactured and sold today is made from a sandwich of liquid crystal (LC) between two precisely spaced glass substrates coated with a transparent conductor. A few challenges remain for LCDs in the consumer market; namely, flexibility, durability, weight and power consumption. The first three issues can be addressed by using thin plastic substrates whereas the last issue can be solved using a bistable display, i.e. a display that is stable (with no power applied) in two states such as reflective or transmissive. Unfortunately, a problem arises when sandwiching liquid crystal between two flexible substrates: the fluid will flow! When the cell is flexed or pressed upon, the gap between the substrates becomes smaller displacing the LC and inducing flow. Cholesteric liquid crystal displays (ChLCDs) are bistable LCDs that have low power consumption and exhibit high reflectance under ambient lighting1. -
Catalog-Web-ONYX-And-STAX.Pdf
1 ABOUT NEXT LED Table of Contents Our Focus Next LED is a leading American manufacturer of 2 About Next LED commercial, billboard, sports, and indoor LED displays. We pour the quality and work ethic of 4 LED 101 the heartland into every sign we engineer and assemble from our headquarters in Wichita, 6 Pitch / Dealer Tools Kansas. As the LED signage industry matures and businesses and organizations around the world realize the benefits of dynamic marketing 8 Commercial Signs through digital signs, it is our sole focus to provide the most reliable products and related services 10 Franchise / Dynamic Data that go beyond the physical components of the display. In a word, every Next LED product comes 12 Billboards loaded with VALUE. 14 Sports Highest Quality Parts While all LED signs aren’t created equal, they are, 16 Operating Software for the most part, created using the same types of components, often supplied by the exact same OEM companies. Next LED uses the highest quality 18 Custom Content LED diodes, lamps, ribbon cables, power supplies, data, and aluminum cabinetry to create a rugged, Questions? Call us at: reliable product for both on and off premise use. 2 888.263.6530 5 Year Parts, Labor, & Brightness Warranty Experience the Best Warranty in the Industry 5 YEARS It’s one thing to say you’ve got a great product; it’s another to stand behind it. Next LED’s industry leading warranty guarantees that you won’t have TM NO PARTS LABOR BRIGHTNESS anything to worry about for up to five years. -
Quantum Dot Displays to Spur Premium Display Market Growth
Publication date: 09 Dec 2019 Author: Richard Son Principal Analyst, Display Chemical Materials [Display Dynamics] Quantum dot displays to spur premium display market growth Brought to you by Informa Tech [Display Dynamics] Quantum dot displays to 1 spur premium display market growth Table of Figures: michellewhitcombihsmarkitcom_2019_12_9_11_5_32_capturejpg1 ..............................................3 michellewhitcombihsmarkitcom_2019_12_9_11_6_23_capturejpg2 ..............................................3 © 2020 Omdia. All rights reserved. Unauthorized reproduction prohibited. [Display Dynamics] Quantum dot displays to 2 spur premium display market growth Key findings . Resolution, slim and bezel-less designs, and a wide color gamut are barometers of innovation in display technology as well as key marketing points of different display products. After the introduction of organic light-emitting diode (OLED), quantum dot (QD), and microLED display technologies that guarantee high definition and flexibility in design, a wide color gamut is now the key feature that determines the premium value of a display. QD displays, groomed to be the core display technology for Samsung Electronics and Samsung Display, are expected to boost the growth of the premium display market. Market for premium displays with various advanced features set to steadily grow Ever since the start of the digital display era, display size, design, and resolution have been used as barometers of innovation in display technology. Display makers marketed size and design as their distinctive features to lure consumers. To make a display slimmer, light-emitting diode backlight unit liquid-crystal displays (LED BLU LCDs) widely adopted edge BLU and bezel-less designs. Curved and bendable display technologies that enabled the production of super-large sized and flexible display designs also gained consumers’ attentions. -
00098OFC2.Qxp:SID Cover
FLEXIBLE AND LOW-POWER DEVICES February 2010 Official Monthly Publication of the Society for Information Display • www.informationdisplay.org Vol. 26, No. 2 FEBRUARY 2010 Information VOL. 26, NO. 2 COVER: This flexible display module from Plastic Logic was made with plastic electronics and Vizplex display media provided by E Ink Corp. It has a resolution of 1280 × 960 and 150 ppi. Cover image courtesy of Plastic Logic Limited, DISPLAY 2009. 2 Editorial Now More than Ever Before: Flexible and Low-Power Technology Meets A Need Stephen P. Atwood 3 Industry News Prime View International, HYDIS Technologies, and LG Display Announce Comprehensive Cooperation Agreement Jenny Donelan 4 Guest Editorial A New Breed of Display Starts to Flex Its Muscles Robert Zehner 6 President’s Corner Getting Excited about Seattle Paul Drzaic 8 Frontline Technology: Flexible AMOLEDs for Low-Power, Rugged Applications Flexible AMOLEDs equipped with phosphorescent OLEDs are well-positioned for low-power, rugged, full-color video applications. Replacing glass with flexible substrates and thin-film encap- sulation makes displays thinner, lighter, and non-breakable – all attractive features for portable applications. With enhanced flexibility and low power consumption, a range of revolutionary opportunities are being created. CREDIT: Cover design by Acapella Studios, Inc. Ruiqing Ma, Mike Hack, and Julie J. Brown 16 Frontline Technology: Flexible Displays Made with Plastic Electronics Plastic Logic has designed and constructed a full-scale manufacturing facility for flexible display modules fabricated using organic semiconductors (“plastic electronics”). These display modules are lightweight, flexible, and robust and are used in the QUEproReader, an e-reader device for mobile business professionals that was introduced in January 2010. -
Wo 2009/026223 A2
(12) INTERNATIONAL APPLICATION PUBLISHED UNDER THE PATENT COOPERATION TREATY (PCT) (19) World Intellectual Property Organization International Bureau (43) International Publication Date (10) International Publication Number 26 February 2009 (26.02.2009) PCT WO 2009/026223 A2 (51) International Patent Classification: (81) Designated States (unless otherwise indicated, for every B60R 1/12 (2006.01) H04N 7/18 (2006.01) kind of national protection available): AE, AG, AL, AM, B60R 1/00 (2006.01) AO, AT,AU, AZ, BA, BB, BG, BH, BR, BW, BY, BZ, CA, CH, CN, CO, CR, CU, CZ, DE, DK, DM, DO, DZ, EC, EE, (21) International Application Number: EG, ES, FI, GB, GD, GE, GH, GM, GT, HN, HR, HU, ID, PCT/US2008/073474 IL, IN, IS, JP, KE, KG, KM, KN, KP, KR, KZ, LA, LC, LK, (22) International Filing Date: 18 August 2008 (18.08.2008) LR, LS, LT, LU, LY, MA, MD, ME, MG, MK, MN, MW, MX, MY, MZ, NA, NG, NI, NO, NZ, OM, PG, PH, PL, PT, (25) Filing Language: English RO, RS, RU, SC, SD, SE, SG, SK, SL, SM, ST, SV, SY, TJ, (26) Publication Language: English TM, TN, TR, TT, TZ, UA, UG, US, UZ, VC, VN, ZA, ZM, ZW (30) Priority Data: 60/956,263 16 August 2007 (16.08.2007) US (84) Designated States (unless otherwise indicated, for every kind of regional protection available): ARIPO (BW, GH, (71) Applicant (for all designated States except US): GENTEX GM, KE, LS, MW, MZ, NA, SD, SL, SZ, TZ, UG, ZM, CORPORATION [US/US]; 600 North Centennial Street, ZW), Eurasian (AM, AZ, BY, KG, KZ, MD, RU, TJ, TM), Zeeland, MI 49464 (US). -
Light Engines for XR Smartglasses by Jonathan Waldern, Ph.D
August 28, 2020 Light Engines for XR Smartglasses By Jonathan Waldern, Ph.D. The near-term obstacle to meeting an elegant form factor for Extended Reality1 (XR) glasses is the size of the light engine2 that projects an image into the waveguide, providing a daylight-bright, wide field-of-view mobile display For original equipment manufacturers (OEMs) developing XR smartglasses that employ diffractive wave- guide lenses, there are several light engine architectures contending for the throne. Highly transmissive daylight-bright glasses demanded by early adopting customers translate to a level of display efficiency, 2k-by-2k and up resolution plus high contrast, simply do not exist today in the required less than ~2cc (cubic centimeter) package size. This thought piece examines both Laser and LED contenders. It becomes clear that even if MicroLED (µLED) solutions do actually emerge as forecast in the next five years, fundamentally, diffractive wave- guides are not ideally paired to broadband LED illumination and so only laser based light engines, are the realistic option over the next 5+ years. Bottom Line Up Front • µLED, a new emissive panel technology causing considerable excitement in the XR community, does dispense with some bulky refractive illumination optics and beam splitters, but still re- quires a bulky projection lens. Yet an even greater fundamental problem of µLEDs is that while bright compared with OLED, the technology falls short of the maximum & focused brightness needed for diffractive and holographic waveguides due to the fundamental inefficiencies of LED divergence. • A laser diode (LD) based light engine has a pencil like beam of light which permits higher effi- ciency at a higher F#. -
New Display Technologies (Crts), Displays Have Become Ubiquitous and Have Taken Many Different Forms
1.0 Introduction Mini Briefing Electronic displays are one of the fastest-growing worldwide technologies. Once reserved for televisions and computers, and composed of large cathode-ray tubes New Display Technologies (CRTs), displays have become ubiquitous and have taken many different forms. Flat-panel displays are overtaking the CRT and are being used in larger quantities for Steve Statham portable computers, a variety of handheld devices, desktop computers and televisions, as well as tiny microdisplays, which are being used in projection televisions, for near-eye applications, where a virtual screen is presented to the viewer. The world of displays is Advances in new display technologies are rapidly changing to meet the evolving needs of the beginning to open up many new possibilities to electronic-device user. consumers and manufacturers. Unfortunately there is always a large time lag between the discoveries made, and the time when practical applications 2.0 Applications finally appear. Even once they have been incorporated into everyday items, they are The electronic-display device industry caters mainly for the sometimes expensive. automation and electronics appliance industries. Characteristic of OEM products, the growth of the display However, major developments are now taking industry is directly linked to the demand trends in end-user place in a variety of display materials with the markets. Display manufacturers, mainly concentrated in potential to enable handheld computers and mobile Japan and East Asian countries, account for over 80% of phones to be more functional and user-friendly, total display production. which could greatly aid in the convergence of functionality and convenience that these products The end-user market (which includes televisions, are intended to deliver. -
Ambient Contrast Ratio of Lcds and OLED Displays
Vol. 25, No. 26 | 25 Dec 2017 | OPTICS EXPRESS 33643 Ambient contrast ratio of LCDs and OLED displays * HAIWEI CHEN, GUANJUN TAN, AND SHIN-TSON WU College of Optics and Photonics, University of Central Florida, Orlando, Florida 32816, USA *[email protected] Abstract: We systematically analyze the ambient contrast ratio (ACR) of liquid crystal displays (LCDs) and organic light-emitting diode (OLED) displays for smartphones, TVs, and public displays. The influencing factors such as display brightness, ambient light illuminance, and surface reflection are investigated in detail. At low ambient light conditions, high static contrast ratio plays a key role for ACR. As the ambient light increases, high brightness gradually takes over. These quantitative results set important guidelines for future display optimization. Meanwhile, to improve an OLED’s ACR at large oblique angles, we propose a new broadband and wide-view circular polarizer consisting of one linear polarizer and two biaxial films. Good performance is realized. © 2017 Optical Society of America under the terms of the OSA Open Access Publishing Agreement OCIS codes: (120.2040) Displays; (230.3720) Liquid-crystal devices; (160.3710) Liquid crystals. References and links 1. D. K. Yang and S. T. Wu, Fundamentals of Liquid Crystal Devices, 2nd ed. (John Wiley & Sons, 2014). 2. H. Seetzen, W. Heidrich, W. Stuerzlinger, G. Ward, L. Whitehead, M. Trentacoste, A. Ghosh, and A. Vorozcovs, “High dynamic range display systems,” ACM Trans. Graph. 23(3), 760–768 (2004). 3. Q. Hong, T. X. Wu, X. Zhu, R. Lu, and S. T. Wu, “Extraordinarily high-contrast and wide-view liquid-crystal displays,” Appl. -
Microdisplays - Market, Industry and Technology Trends 2020 Market and Technology Report 2020
From Technologies to Markets Microdisplays - Market, Industry and Technology Trends 2020 Market and Technology Report 2020 Sample © 2020 TABLE OF CONTENTS • Glossary and definition • Industry trends 154 • Table of contents o Established technologies players 156 • Report objectives o Emerging technologies players 158 • Report scope o Ecosystem analysis 160 • Report methodology o Noticeable collaborations and partnerships 170 • About the authors o Company profiles 174 • Companies cited in this report • Who should be interested by this report • Yole Group related reports • Technology trends 187 o Competition benchmarking 189 • Executive Summary 009 o Technology description 191 o Technology roadmaps 209 • Context 048 o Examples of products and future launches 225 • Market forecasts 063 • Outlooks 236 o End-systems 088 o AR headsets 104 • About Yole Group of Companies 238 o Automotive HUDs 110 o Others 127 • Market trends 077 o Focus on AR headsets 088 o A word about VR 104 o Focus on Auto HUDs 110 o Focus on 3D Displays 127 o Summary of other small SLM applications 139 Microdisplays - Market, Industry and Technology Trends 2020 | Sample | www.yole.fr | ©2020 2 ACRONYMS AMOLED: Active Matrix OLED HMD: Head mounted Device/Display PPI: Pixel Per Inch AR: Augmented Reality HOE: Holographic Optical Element PWM: Pulse Width Modulation BLU: Back Lighting Unit HRI: High Refractive Index QD: Quantum Dot CF LCOS: Color Filter LCOS HVS: Human Vision System RGB: Red-Green-Blue CG: Computer Generated IMU: Inertial measurement Unit RMLCM: Reactive Monomer -
Liquid-Crystal Displays: Big and Bigger Manufacturers Are Pinning Their Hopes on the Entertainment Market to Use up Increasing Production Capacity
Innovation and LCD TV' Highlight SID 2003 • SID 2003 Review • Show Overview • LCDs • Emissives • Microdisplays • Equipment and Materials • Display Semiconductors and Electronics • Business Conference • Awards Cost reduction, evolution, and innovation could all be seen at SID 2003, which bodes well for the display industry's future. 2 Editorial When Did PCs Get Boring ? Kenneth I. Werner 12 Overview: Finding a Theme Cost reduction, evolution, and innovation could all be seen at SID 2003, which bodes well for the display industry's future. Ken Werner 16 Liquid-Crystal Displays: Big and Bigger Manufacturers are pinning their hopes on the entertainment market to use up increasing production capacity. Alfred Poor 20 Emissive Displays Shine On Greg Pease for SID Light-emitting ·displays are being used in applications from head mounted viewers to stadium displays - and everywhere in between. David Lieberman 26 Microdisplays: LCoS Projects a Bright Future At SID 2003, more companies were showing real LCoS-display products, and with supporting components commercially available, more micro display-based products will reach consumers during the next year. Stephen P. Atwood Next Month in Information Display 30 Manufacturing: Equipment and Materials This year, about one-third of the SID exhibitors were equipment or Large-Area Displays materials suppliers - not counting chip suppliers. • DLP"' Rear Projection Patrick Dunn • Tiled Displays 34 Electronics Is Where You Find It • LCDTV The display-electronics environment is changing so rapidly that it is hard • LCoS Projection to recognize a single trend - except that every conceivable ecological niche is being explored for competitive advantages. Ken Werner 38 Expert Opinion: LCD-TV Technology Gary Feather 39 Expert Opinion: Predicting the Future INFORMATION DISPLAY (ISSN 0362-0972) is published eleven Yoichi Taira times a year for the Society for Information Display by Palisades Convention Management, 4 11 Lafayette Street, 2nd Floor, New 40 The First SID Business Conference York, NY 10003; Leonard H.