Applications of Pulsed Light for Sterilization
Total Page:16
File Type:pdf, Size:1020Kb
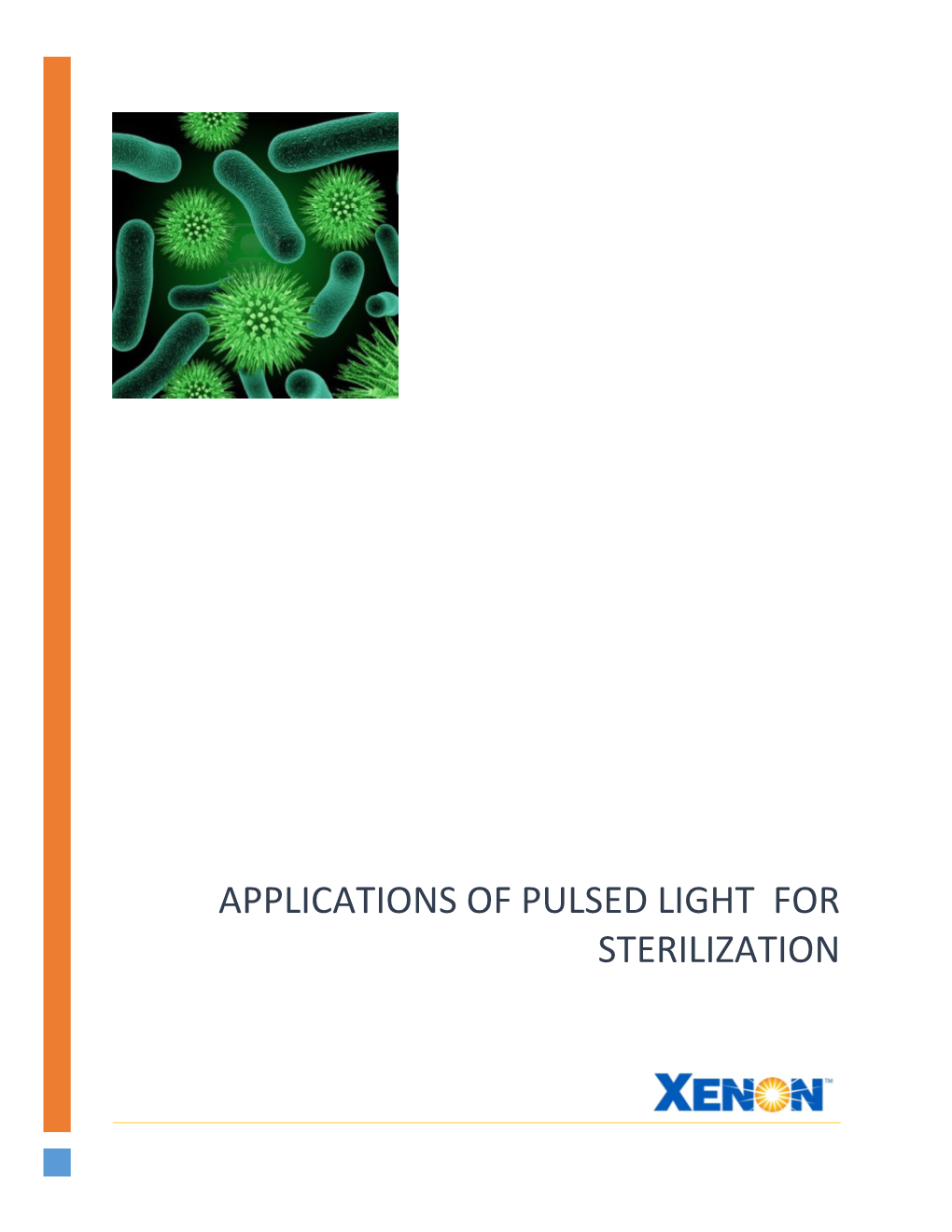
Load more
Recommended publications
-
Industrial Lighting a Primer
Industrial Lighting A Primer All through history people have sought better ways to illuminate their work. Even the cavemen needed torches to allow them to draw on the walls of their underground caverns. Fire brought both light and heat for thousands of years before crude lamps of animal fat gave way to the candle for general indoor illumination used around the world. Roman Grease Lamp An offshoot of the common candlestick became what we now call the Lacemakers Globe. This quite possibly could qualify as the world’s first industrial light source! It was observed that when a candle flame was aligned behind a rounded glass bottle filled with water, a magnifying and focusing effect was produced, in addition to simply lighting up a small area. This was high technology of the first order! No longer did the lacemaker have to pack it in when the sun went down, for soon the new Lacemaker’s Globe became fairly common in European Cottage Industry, enabling the production of lace at a greater rate than ever before. It is also not too much of a stretch to conclude that the repetitive patterns of the lacemaker could be looked upon as a forerunner to the theory of mass production, along with the pin makers who toiled away in the ‘second tier’ of the feeble light pool cast by the globe, hammering heads onto straightened bits of wire in order to make the common pin. This was mighty slim pickings by today’s standards to be sure, but just a few hundred years ago it represented a revolutionary increase in handiwork production after the sun went down, for the very first time in history. -
!History of Lightingv2.Qxd
CONTENTS Introduction 3 The role of lighting in modern society 3 1. The oldest light sources 4 Before the advent of the lamp 4 The oldest lamps 4 Candles and torches 5 Further development of the oil lamp 6 2. Gaslight 9 Introduction 9 Early history 9 Gas production 10 Gaslight burners 10 The gas mantle 11 3. Electric lighting before the incandescent lamp 14 Introduction 14 Principle of the arc lamp 15 Further development of the arc lamp 16 Applications of the arc lamp 17 4. The incandescent lamp 20 The forerunners 20 The birth of the carbon-filament lamp 22 Further development of the carbon-filament lamp 25 Early metal-filament lamps 27 The Nernst lamp 28 The birth of the tungsten-filament lamp 29 Drawn tungsten filaments 30 Coiled filaments 30 The halogen incandescent lamp 31 5. Discharge lamps 32 Introduction 32 The beginning 32 High-voltage lamps 33 Early low-pressure mercury lamps 34 The fluorescent lamp 35 High-pressure mercury lamps 36 Sodium lamps 37 The xenon lamp 38 6. Electricity production and distribution 39 Introduction 39 Influence machines and batteries 39 Magneto-electric generators 40 Self-exciting generators 41 The oldest public electricity supply systems 41 The battle of systems 42 The advent of modern a.c. networks 43 The History of Light and Lighting While the lighting industry is generally recognized as being born in 1879 with the introduction of Thomas Alva Edison’s incandescent light bulb, the real story of light begins thousands of years earlier. This brochure was developed to provide an extensive look at one of the most important inventions in mankind’s history: artificial lighting. -
Humphry Davy and the Arc Light
REMAKING HISTORY By William Gurstelle Humphry Davy and the Arc Light » Thomas Edison did not invent the first electric BRILLIANT light.* More than 70 years before Edison’s 1879 MISTAKES: Humphry Davy, incandescent lamp patent, the English scientist chemist, inventor, Humphry Davy developed a technique for produc- and philosopher: ing controlled light from electricity. “I have learned Sir Humphry Davy (1778–1829) was one of the more from my failures than from giants of 19th-century science. A fellow of the my successes.” prestigious Royal Society, Davy is credited with discovering, and first isolating, elemental sodium, potassium, calcium, magnesium, boron, barium, and strontium. A pioneer in electrochemistry, he appeared between the electrode tips, Davy had to also developed the first medical use of nitrous oxide separate the carbon electrodes slightly and care- and invented the miner’s safety lamp. The safety fully in order to sustain the continuous, bright arc lamp alone is directly responsible for saving of electricity. Once that was accomplished, he found hundreds, if not thousands, of miners’ lives. the device could sustain the arc for long periods, But it is his invention of the arc lamp for which we even as the carbon rods were consumed in the heat remember him here. Davy’s artificial electric light of the process. consisted of two carbon rods, made from wood Davy’s arc lamp of 1807 was not economically charcoal, connected to the terminals of an enormous practical until the cost of producing a 50V-or-so collection of voltaic cells. (In Davy’s day, thousands power supply became reasonable. -
High Performance Flash and Arc Lamps Catalog
Europe: Saxon Way, Bar Hill, Cambridge, CB3 8SL Tel: +44 (0)1954 782266 Fax: +44 (0)1954 782993 USA: 44370 Christy St., Freemont, CA 94538, USA Tel: (800) 775-OPTO Tel: (510) 979-6500 Fax: (510) 687-1344 USA: 35 Congress Street, Salem, MA 01970, USA Tel: (978) 745-3200 Fax: (978) 745-0894 Asia: 47 Ayer Rajah Cresent, 06-12, Singapore 139947 Tel: +65-775-2022 Fax: +65-775-1008 Japan: 18F, Parale Mitsui Building 8, Higashida-cho, Kawasaki-ku, Kawasaki-shi, Kanagawa-ken, 210-0005 Japan Tel: 81 44 200 9150 Fax: 81 44 200 9160 www.perkinelmer.com/opto Optoelectronics Lighting Imaging Telecom High Performance Flash and Arc Lamps Lighting Imaging Teleco m Introduction This publication is divided into two sections: Past, Present and Future Part 1 – Technical Information Solid state laser systems have historically used pulsed and CW (DC) xenon or krypton filled arc lamps as exci- Part 2 – Product Range tation for pump sources. When in 1960, at Hughes Research Labs, the first practical pulsed laser system Part 1 is intended to give the necessary technical infor- was demonstrated by mation to manufacturers, designers and researchers to T. H. Maiman the technology and understanding enable them to select the correct flashlamp for their involved in the manufacture and operation of application and also to give an insight into the design flashlamps was of a very basic nature. Up to procedures necessary for correct flashlamp operation. that time (1960) the major use of flashlamps was pho- Part 2 is a guide to the wide, varied and complex range tography and related applications. -
History of Electric Light
SMITHSONIAN MISCELLANEOUS COLLECTIONS VOLUME 76. NUMBER 2 HISTORY OF ELECTRIC LIGHT BY HENRY SGHROEDER Harrison, New Jersey PER\ ^"^^3^ /ORB (Publication 2717) CITY OF WASHINGTON PUBLISHED BY THE SMITHSONIAN INSTITUTION AUGUST 15, 1923 Zrtie Boxb QSaftitnore (prcee BALTIMORE, MD., U. S. A. CONTENTS PAGE List of Illustrations v Foreword ix Chronology of Electric Light xi Early Records of Electricity and Magnetism i Machines Generating Electricity by Friction 2 The Leyden Jar 3 Electricity Generated by Chemical Means 3 Improvement of Volta's Battery 5 Davy's Discoveries 5 Researches of Oersted, Ampere, Schweigger and Sturgeon 6 Ohm's Law 7 Invention of the Dynamo 7 Daniell's Battery 10 Grove's Battery 11 Grove's Demonstration of Incandescent Lighting 12 Grenet Battery 13 De Moleyns' Incandescent Lamp 13 Early Developments of the Arc Lamp 14 Joule's Law 16 Starr's Incandescent Lamp 17 Other Early Incandescent Lamps 19 Further Arc Lamp Developments 20 Development of the Dynamo, 1840-1860 24 The First Commercial Installation of an Electric Light 25 Further Dynamo Developments 27 Russian Incandescent Lamp Inventors 30 The Jablochkofif " Candle " 31 Commercial Introduction of the Differentially Controlled Arc Lamp ^3 Arc Lighting in the United States 3;^ Other American Arc Light Systems 40 " Sub-Dividing the Electric Light " 42 Edison's Invention of a Practical Incandescent Lamp 43 Edison's Three-Wire System 53 Development of the Alternating Current Constant Potential System 54 Incandescent Lamp Developments, 1884-1894 56 The Edison " Municipal -
Miniature and Low Wattage HID Lamps?
Miniature HID Lamps? Page 1 of 4 Miniature and Low Wattage HID Lamps? I know that some of us want a more energy efficient flashlight or a more energy efficient bicycle headlight or the like. And some of us wonder why commercial products to satisfy those desires aren't out there? As for flashing a xenon strobe rapidly with low energy flashes - there is a bit of a problem. Performance of xenon flashtubes largely gets better with higher flash energy and worse with lower flash energy. If the energy is high enough to give satisfactory improvement of energy efficiency over halogen lamps, any economical flashtube including all made of glass as opposed to quartz will not survive such flashing repeated rapidly enough to appear to glow continuously. NOTE - It takes 50-60 flashes per second to avoid flicker! Movies avoid flicker at 24 frames/second by having the "on" fraction of each cycle being about 80 percent of the cycle as opposed to the fraction of 1 percent that a fast xenon strobe would have. (NOTE - someone tells me that movie projectors "blink" twice per frame for 48 "blinks" per second, and this may well be true for just some projectors.) You need the off time to be under 20 or preferably under about 16 milliseconds to make the light appear continuous. Further discussion of this is in a separate file on making xenon glow continuously. Now back to miniature HID lamps: One obstacle is the thermal conduction loss from the arc. This is surprisingly proportional to the overall length of the arc and surprisingly independent of the width of the arc or the gas/vapor pressure or the power. -
What Makes the Powerarc a Better Illuminator
ELEMENTAL ANALYSIS FLUORESCENCE GRATINGS & OEM SPECTROMETERS What makes the PowerArc OPTICAL COMPONENTS CUSTOM SOLUTIONS PARTICLE CHARACTERIZATION a better Illuminator RAMAN / AFM-RAMAN / TERS SPECTROSCOPIC ELLIPSOMETRY SPR IMAGING A 75 Watt Xenon Arc Lamp Illuminator Provides the Same Power Output as a 450 Watt Xenon Arc Lamp in a Vertical Lamp Housing! Users of old style vertical arc lamp housings are throwing Please note that the PowerArc™ series of lamp housings away as much as 90% of the lamps output, due to are designed for lamps from 75 watts to 150 watts. poor collection efficiency. These old style vertical lamp Please also refer to our KiloArc™ light source for ultra high housings have a collection lens in front of the arc lamp and intensity requirements with 1,000 watt arc lamps. sometimes, but not always, a back reflector behind them. The problem with this old design is that only the light that Arc Lamp Housing actually strikes these optical elements is delivered outside At the heart of the PowerArc™ lamp housing is a of the lamp housing. All other photons emitted by the lamp proprietary on-axis ellipsoidal reflector. Our reflectors are wasted, simply heating the inside of the lamp housing. collect up to 70% of the radiant energy from the arc lamp, Conversely the unique PowerArc™ lamp housing has an versus only 12% for typical condenser systems in vertical enveloping ellipsoidal reflector that collects virtually all of lamp housings. The ellipse literally wraps around the arc the light emitted by the lamp arc, delivering those photons lamp, collecting 5 to 6 times more output power than a to a secondary focal point outside of the lamp housing, conventional system. -
Basic Physics of the Incandescent Lamp (Lightbulb) Dan Macisaac, Gary Kanner,Andgraydon Anderson
Basic Physics of the Incandescent Lamp (Lightbulb) Dan MacIsaac, Gary Kanner,andGraydon Anderson ntil a little over a century ago, artifi- transferred to electronic excitations within the Ucial lighting was based on the emis- solid. The excited states are relieved by pho- sion of radiation brought about by burning tonic emission. When enough of the radiation fossil fuels—vegetable and animal oils, emitted is in the visible spectrum so that we waxes, and fats, with a wick to control the rate can see an object by its own visible light, we of burning. Light from coal gas and natural say it is incandescing. In a solid, there is a gas was a major development, along with the near-continuum of electron energy levels, realization that the higher the temperature of resulting in a continuous non-discrete spec- the material being burned, the whiter the color trum of radiation. and the greater the light output. But the inven- To emit visible light, a solid must be heat- tion of the incandescent electric lamp in the ed red hot to over 850 K. Compare this with Dan MacIsaac is an 1870s was quite unlike anything that had hap- the 6600 K average temperature of the Sun’s Assistant Professor of pened before. Modern lighting comes almost photosphere, which defines the color mixture Physics and Astronomy at entirely from electric light sources. In the of sunlight and the visible spectrum for our Northern Arizona University. United States, about a quarter of electrical eyes. It is currently impossible to match the He received B.Sc. -
Xenon Arc Lamp
INSTRUMENTAL TECHNIQUE PRESENTATION Xenon arc lamp Madhuri Jash 01/08/2015 What is Xenon arc lamp? Xenon arc lamp is a gas discharge lamp where electric power is converted into light by an arc discharge in a xenon atmosphere at high pressure. Why we use xenon here because xenon has the highest overall conversion efficiency. History of arc lamp Carbon arc lamp was the first electric light invented by Humphry Davy in the early 1800s. This was the first widely-used and commercially successful form of electric lamp. 1875 Pavel Yablochkov had developed the Yablochkov Candle which was the first reliable carbon arc lamp and was used in Paris. 1870s-1890s Elihu Thomson and E.W. Rice Jr improved many parts of the arc light system both in DC and AC power. Then xenon short-arc lamps were invented in the 1940s in Germany and introduced in 1951 by Osram. First launched in the 2 kW size and now it is upto 15 kW. Xenon arc lamp construction .There is a fused quartz envelope with thoriated tungsten electrodes. Fused quartz is the only economically feasible material currently available that can withstand the high pressure. .the tungsten electrodes are welded to strips of pure molybdenum metal or Invar alloy, which are then melted into the quartz to form the envelope seal. .Because of the very high power levels involved, large lamps are water-cooled, An O- ring seals off the tube, so that the naked electrodes do not contact the water. .In order to achieve maximum efficiency, the xenon gas inside short-arc lamps is maintained at an extremely high pressure — up to 30 atmospheres — which poses safety concerns, large xenon short-arc lamps are normally shipped in protective shields. -
Cermax® Xenon Arc Lamps
DATASHEET Lighting Solutions PE300BFA CERMAX® XENON ARC LAMPS Key Features High Intensity illumination 5000 Lumens Power range of 180-320 Watts 1000 hours life Broad spectral range with 5900⁰ Kelvin color temperature Made in the U.S.A. Applications Cermax® Xenon lamps from Excelitas Technologies are ideal for applications that require a high degree of illumination control. Medical and industrial fiber optic illuminators The Cermax® Xenon arc lamp from Excelitas Technologies is an innovative Machine vision lamp design in the specialty lighting industry. Cermax Xenon lamps were Infrared and visible spotlights/beacons first introduced in the early 1980s and are now used in diagnostic and Spectroscopy surgical endoscopes in most major hospitals worldwide, in high-brightness Microscopy projection display systems, and for a wide variety of high-performance UV Curing applications. Video projection Solar simulation The Cermax Xenon lamp, Model PE300BFA, has an integrated parabolic Stage and Studio reflector, enabling high intensity, focused output of visible and infrared Wafer inspection radiation. With their internal reflector and rugged ceramic body construction, Cermax Xenon lamps are the safest and most compact alternative to conventional quartz xenon lamps. This makes them ideal for applications requiring a high degree of illumination control. Current-regulated or power-regulated power supplies with output ripples of less than 5% are recommended. Single shot ignition pulses are advised because radio frequency starters may -
Energy Efficiency – HID Lighting
PDHonline Course E423 (5 PDH) Energy Efficiency High Intensity Discharge Lighting Instructor: Lee Layton, P.E 2014 PDH Online | PDH Center 5272 Meadow Estates Drive Fairfax, VA 22030-6658 Phone & Fax: 703-988-0088 www.PDHonline.org www.PDHcenter.com An Approved Continuing Education Provider www.PDHcenter.com PDHonline Course E423 www.PDHonline.org Energy Efficiency High Intensity Discharge Lighting Lee Layton, P.E Table of Contents Section Page Introduction ………………………………….….. 3 Chapter 1, Lighting Market ………………….….. 5 Chapter 2, Fundamentals of Lighting ………….... 16 Chapter 3, Characteristics of HID Lighting……... 28 Chapter 4, Types of HID Lighting……………..... 37 Summary ……………………………………..…. 66 © Lee Layton. Page 2 of 66 www.PDHcenter.com PDHonline Course E423 www.PDHonline.org Introduction Gas-discharge lamps are light sources that generate light by sending an electrical discharge through an ionized gas. The character of the gas discharge depends on the pressure of the gas as well as the frequency of the current. High-intensity discharge (HID) lighting provides the highest efficacy and longest service life of any lighting type. It can save 75%-90% of lighting energy when it replaces incandescent lighting. Figure 1 shows a typical high-intensity discharge lamp. In a high-intensity discharge lamp, electricity arcs between two electrodes, creating an intensely bright light. Usually a gas of mercury, sodium, or metal halide acts as the conductor. HID lamps use an electric arc to produce intense light. Like fluorescent lamps, they require ballasts. They also take up to 10 minutes to produce light when first turned on because the ballast needs time to establish the electric arc. -
Laser-Free Super-Resolution Microscopy
bioRxiv preprint doi: https://doi.org/10.1101/121061; this version posted January 22, 2021. The copyright holder for this preprint (which was not certified by peer review) is the author/funder, who has granted bioRxiv a license to display the preprint in perpetuity. It is made available under aCC-BY-NC 4.0 International license. Laser-free super-resolution microscopy Kirti Prakasha,b,c,* aNational Physical Laboratory, TW11 0LW Teddington, UK; bDepartment of Embryology, Carnegie Institution for Science, Baltimore, MD 21218, USA; cDepartment of Chemistry, University of Cambridge, Lensfield Road, Cambridge, CB2 1EW, United Kingdom; *Correspondence: [email protected]. We report that high-density single-molecule super-resolution microscopy can be achieved with a conventional epifluores- cence microscope setup and a Mercury arc lamp. The configuration termed as laser-free super-resolution microscopy (LFSM), is an extension of single molecule localisation microscopy (SMLM) techniques and allows single molecules to be switched on and off (a phenomenon termed as "blinking"), detected and localised. The use of a short burst of deep blue excitation (350-380 nm) can be further used to reactivate the blinking, once the blinking process has slowed or stopped. A resolution of 90 nm is achieved on test specimens (mouse and amphibian meiotic chromosomes). Finally, we demonstrate that STED and LFSM can be performed on the same biological sample using a simple commercial mounting medium. It is hoped that this type of correlative imaging will provide a basis for a further enhanced resolution. superresolution microscopy | single molecule localization microscopy | non-coherent illumination source | STED | UV activation Introduction superresolution techniques a minimum power (∼0.1 kW/cm2) is required to switch the fluorophores between dark and bright The resolution of images generated by light microscopy is state (Dickson et al., 1997; Betzig et al., 2006).