Self-Curing Concrete by Using Super Absorbent Polymer
Total Page:16
File Type:pdf, Size:1020Kb
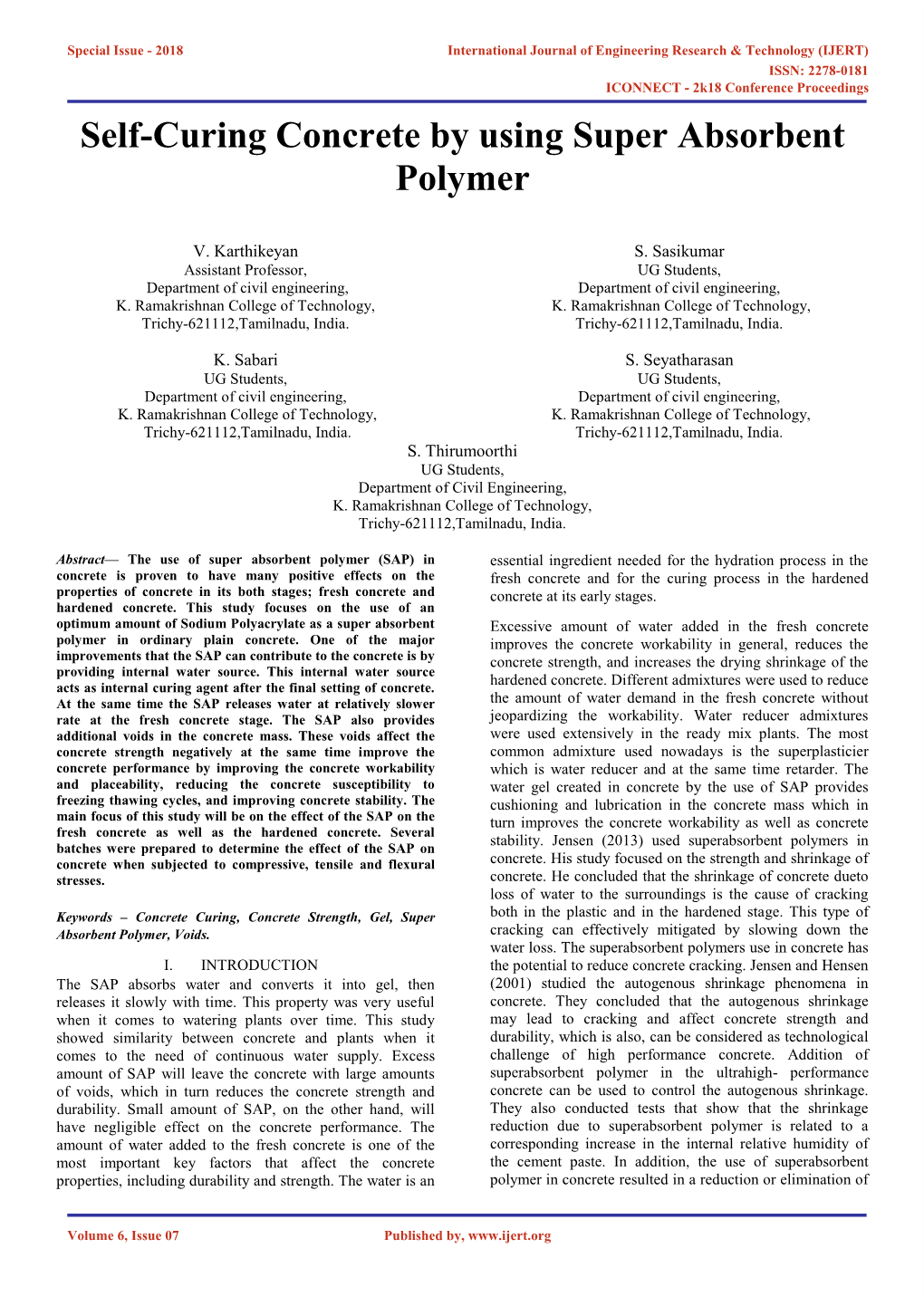
Load more
Recommended publications
-
Study on Water Absorption–Dehydration Characteristics for SAP Composite Soil for Rainwater Harvesting
water Article Study on Water Absorption–Dehydration Characteristics for SAP Composite Soil for Rainwater Harvesting Youwei Qin 1, Tao Yang 1,*, Siyuan Wang 2, Fangling Hou 3, Pengfei Shi 1 and Zhenya Li 1 1 State Key Laboratory of Hydrology-Water Resources and Hydraulic Engineering, Centre for Global Change and Water Cycle, Hohai University, Nanjing 210098, China; [email protected] (Y.Q.); [email protected] (P.S.); [email protected] (Z.L.) 2 Shenzhen Water Planning and Design Institute, Shenzhen 518001, China; [email protected] 3 Nanjing Hydraulic Research Institute, Nanjing 210029, China; fl[email protected] * Correspondence: [email protected] Received: 4 June 2020; Accepted: 21 August 2020; Published: 25 August 2020 Abstract: As a water absorption material, superabsorbent polymer (SAP) has gained its popularity in agriculture and environmental remediations. This study conducted a comparative investigation on saturated water content of cinnamon soil mixed with SAP. Two SAPs, SAP1 and SAP2, with different behaviors were tested, where SAP1 is an organic superabsorbent polymer, and SAP2 is polyacrylic acid sodium salt polymer. The saturated water content of SAP composite cinnamon soil was investigated with the weighing method. The repeated water absorption capacity and dehydration behavior of SAP composite soil under different designed rainfall intensity were investigated with a soil column tester. The results showed that (1) cinnamon soil mixed with SAP increased the saturated soil water content, and SAP1 was more effective than SAP2; (2) SAP held strong water absorption ability and recycling efficiency with eight repeated absorption–dehydration tests; (3) the average dehydration time for SAP composite soil were 626 h and 1214 h under 5-year and 10-year design rainfall intensities. -
Superabsorbent Polymers
www.scifun.org Superabsorbent Polymers Absorbers and super absorbers If you spill a drink, your first impulse is probably to grab one or more paper napkins or paper towels to soak up, or absorb, the liquid. If the spill is large, several paper towels will be needed. Even a “quicker-picker-upper” can absorb only a small amount of liquid, before it is saturated (has absorbed all it can). What makes materials more or less absorbent in the first place? The answer is in their chemistry. We can harness the chemistry of polymers to build a better absorber: a super absorber. The word “polymer” means “many parts” (from the Greek: poly = many, meros = parts). A chemical polymer is a molecule made of many repeating units, monomers (mono = one, meros = parts), linked together through chemical bonds. It is useful to think of polymers as chains – a good analogy is a chain of paperclips (the monomers), Figure 1. Polymers are very versatile. They can form materials that are rigid like plastic water bottles or materials that are flexible, like plastic grocery bags. Note that polymeric materials are often called “plastics”. Figure 1. A chain of paperclips linked end-to-end like the individual molecules (monomers) that are chemically bonded to form a chemical polymer chain. Some polymers occur naturally. The most common polymer on Earth, cellulose, is a polymer of glucose molecules and is made (as a result of photosynthesis) by essentially every green plant. Cellulose forms part of a plant’s rigid structures, the wood in a tree trunk, for example. -
Development of Slow Release Nano Composite Fertilizer Using
DEVELOPMENT OF SLOW-RELEASE NANO-COMPOSITE FERTILIZER USING BIODEGRADABLE SUPERABSORBENT POLYMER By Benard Kiplangat Rop I80/50014/2015 Department of Chemistry, University of Nairobi A Thesis Submitted in Fulfillment of the Requirements for the Degree of Doctor of Philosophy in Chemistry of the University of Nairobi November, 2019 1 DECLARATION I declare that this thesis is my original work and has not been submitted elsewhere for examination, award of degree or publication. Where other people’s work or my own has been used, this property has been acknowledged and referenced in accordance with the University of Nairobi’s requirements. Signature____________________ Date__________________________ Benard Kiplangat Rop I80/50014/2015 Department of Chemistry, School of Physical Sciences, University of Nairobi This thesis has been submitted for examination with our approval as research supervisors. 1. Dr. Damaris Mbui Signature________________ Date______________ Department of Chemistry, University of Nairobi 2. Dr. George N. Karuku Signature________________ Date______________ Department of Land Resources & Agricultural Technology, University of Nairobi 3. Dr. Njagi Njomo Signature________________ Date______________ Department of Chemistry, University of Nairobi 4. Dr. Immaculate Michira Signature________________ Date______________ Department of Chemistry, University of Nairobi i DEDICATION My wife Gladys for her constant love, support and encouragement throughout this journey; I couldn’t have done it without you. My sons, Brian, Ian and Allan ii ACKNOWLEDGMENT I would like to sincerely and gratefully thank my supervisors, Dr. Damaris Mbui, Dr. George N. Karuku, Dr. Njagi Njomo and Dr. Immaculate Michira, all from the University of Nairobi for their support, guidance, understanding and friendship during my studies. They gave me an opportunity to work independently with their guidance. -
Sodium Polyacrylate Superabsorbent Polymers SCIENTIFIC
Sodium Polyacrylate Superabsorbent Polymers SCIENTIFIC Introduction Water from one cup is poured into an “empty” cup (actually containing sodium polyacrylate) and the water “disappears!” Concepts • Polymers • Osmosis • Superabsorbents • Industrial chemistry Materials Sodium polyacrylate, 0.5 g Styrofoam® cups or other opaque containers, 2 Distilled or deionized water, 100 mL Safety Precautions Sodium polyacrylate is nontoxic. However, it is irritating to the eyes and also to nasal membranes if inhaled. Wear chemical splash goggles whenever working with chemicals, heat or glassware. Sodium polyacrylate is an obvious choice for student pranks. Be careful students do not have access to sodium polyacrylate outside of chemistry class. Please review current Material Safety Data Sheets for additional safety, handling, and disposal information. Pre-Lab Preparation Before the students come into the room, place 0.5 g of sodium polyacrylate in one of the Styrofoam cups. Procedure 1. Add approximately 100 mL of distilled or deionized water to the second Styrofoam cup. 2. Tell the students that the water will “disappear” when poured into the other cup. (You can tip the cup forward some- what to show that it is “empty”; it will be difficult to see the 0.5 g of sodium polyacrylate against the white Styrofoam cup.) 3. Slowly pour the water into the cup containing sodium polyacrylate. Swirl the cup a bit (give the sodium polyacrylate time to absorb the water). 4. Tip the cup downward slightly to show the students that the water has “disappeared”! (Don’t turn the cup upside down, or you may dump the jelly-like mass on the floor!) Disposal Please consult your current Flinn Scientific Catalog/Reference Manual for general guidelines and specific procedures, and review all federal, state and local regulations that may apply, before proceeding. -
SUPER ABSORBENT POLYMERS: a DIMINUTIVE REVIEW Madhuja Manoj Katkar Institute of Chemical Technology, Mumbai, India
Journal of Textile and Clothing Science ISSN: 2581-561X (Online) http://www.jtcsonline.com REVIEW SUPER ABSORBENT POLYMERS: A DIMINUTIVE REVIEW Madhuja Manoj Katkar Institute of Chemical Technology, Mumbai, India A R T I C L E I N F O A B S T R A C T Article history: Super absorbency is superior swelling abilities originate to Received 02 February 2019 absorb and retain large amounts of aqueous solutions. Super- Received in revised form 23 absorbent polymers are cross-linked networks of hydrophilic February 2019 polymer chains. With today’s demand for one-click solution, the Accepted 15 March 2019 development of superabsorbent technology has been largely 28/03/2019-Mar Keywords: directed by the needs of disposable hygiene segment, agriculture Absorbent, Agriculture, industry etc. Over the years, starch-grafted superabsorbent Industrial, Medical, Polymer, polymer turned into cross-linked acrylic homopolymers. This Water paper discusses concept, mechanism and major application areas of superabsorbent. 1. Introduction dissolving in water [2]. water uptake potential A Polymer is a large molecule composed of these materials goes as high as 100,000% of of several repeating units. 3-D crosslinked its own weight in a short period of time [3]. network of polymer molecules forms polymer The maximum volume of superabsorbent gels. Superabsorbent polymer (SAP) is polymers covers the synthetic or chemically or physically cross-linked polymer petrochemical source and mostly acrylic acid gels. When water meets one of these chains, it and its sodium or potassium salts, and is drawn into the molecule by osmosis. Water acrylamide is used in the industrial rapidly migrates into the interior of the production of superabsorbent polymers. -
Preparation and Analysis of Crosslinked
PREPARATION AND ANALYSIS OF CROSSLINKED LIGNOCELLULOSIC FIBERS AND CELLULOSE NANOWHISKERS WITH POLY(METHYL-VINYL ETHER CO MALEIC ACID) – POLYETHYLENE GLYCOL TO CREATE NOVEL WATER ABSORBING MATERIALS A Dissertation Presented to The Academic Faculty by Lee Ann Goetz In Partial Fulfillment of the Requirements for the Degree Doctorate of Philosophy in the School of Chemistry and Biochemistry Georgia Institute of Technology December 2012 Copyright © Lee Ann Goetz 2012 PREPARATION AND ANALYSIS OF CROSSLINKED LIGNOCELLULOSIC FIBERS AND CELLULOSE NANOWHISKERS WITH POLY(METHYL-VINYL ETHER CO MALEIC ACID) – POLYETHYLENE GLYCOL TO CREATE NOVEL WATER ABSORBING MATERIALS Approved by: Dr. Arthur Ragauskas, Advisor Dr. Lawrence A. Bottomley School of Chemistry and Biochemistry School of Chemistry and Biochemistry Georgia Institute of Technology Georgia Institute of Technology Dr. Facundo Fernandez Dr. Yulin Deng School of Chemistry and Biochemistry College of Engineering, Chemical and Georgia Institute of Technology Biomolecular Engineering Georgia Institute of Technology Dr. Preet Singh College of Engineering, Materials Science and Engineering Georgia Institute of Technology Date Approved: December 2012 This is dedicated to my family and friends for their constant love, support, and encouragement of me throughout this journey. I couldn’t have done it without you. ACKNOWLEDGEMENTS I wish to thank everyone who has helped me through the process of completing my doctoral studies. I would also like to thank my advisor, Arthur Ragauskas, the IPST@GT Foundation for my IPST GRA, and my committee members. Thank you to Kristiina Oksman and Aji Mathew for sponsoring me at Lulea University, Skelleftea, Sweden and Kristina Knutson for initially writing and receiving the NSF grant that allowed me to travel and study with them. -
Preparation of a Superabsorbent Polymer and Exploration of Its Properties
Preparation of a superabsorbent polymer and exploration of its properties A Dissertation Submitted in partial fulfillment FOR THE DEGREE OF MASTER OF SCIENCE IN CHEMISTRY Under Academic Autonomy NATIONAL INSTITUTE OF TECHNOLOGY ROURKELA By Amrita Jagdev Under the guidance of Dr R.K.Patel Department of Chemistry NATIONAL INSTITUTE OF TECHNOLOGY ROURKELA-769008(ORISSA) GUIDE CERTIFICATE Dr. R.K.PATEL M.Sc., PhD.FIC (INDIA) Sr. Lecturer of Chemistry Department National Institute Of Technology Rourkela-769008 Orissa This is to certify that the dissertation entitled “PREPARTION OF SUPERABSORBENT POLYMER AND EXPLORATION OF ITS PROPERTIES” submitted by Amrita Jagdev to the department of chemistry, National Institute of Technology, Rourkela for the degree of Master of Science in Chemistry is based on the result obtain in the bonafide project work carried out by her under my Guidance and supervision. I further certify that to the best of my knowledge Amrita Jagdev bears a good moral character. N.I.T, Rourkela Dr. R. K. Patel Date: 2 ACKNOWLEGDEMENTS The respect and gratitude for my guide Dr . R. K. Patel Assistant Professor, Department of Chemistry, National Institute of Technology, Rourkela, cannot be expressed in words. I am grateful to him for devoting time for thought provoking and stimulating discussions in spite of his busy schedule. I thank him for his patience, guidance and regular monitoring of the work and inputs without which this work could have never come to fruition. Indeed, the experience of working under him is one of that I will cherish for ever. I also want to thank M.Islam for his support at every stage of my work. -
Superabsorbent Polymer with High Permeability Supersaugfähiges Polymer Mit Hoher Permeabilität Polymere Superabsorbant Presentant Une Permeabilite Elevee
(19) & (11) EP 1 622 655 B1 (12) EUROPEAN PATENT SPECIFICATION (45) Date of publication and mention (51) Int Cl.: of the grant of the patent: A61L 15/60 (2006.01) 24.08.2011 Bulletin 2011/34 (86) International application number: (21) Application number: 04760377.4 PCT/US2004/012707 (22) Date of filing: 23.04.2004 (87) International publication number: WO 2004/096304 (11.11.2004 Gazette 2004/46) (54) SUPERABSORBENT POLYMER WITH HIGH PERMEABILITY SUPERSAUGFÄHIGES POLYMER MIT HOHER PERMEABILITÄT POLYMERE SUPERABSORBANT PRESENTANT UNE PERMEABILITE ELEVEE (84) Designated Contracting States: (74) Representative: Lang, Arne et al AT BE BG CH CY CZ DE DK EE ES FI FR GB GR Evonik Degussa GmbH HU IE IT LI LU MC NL PL PT RO SE SI SK TR DG-IPM-PAT Bau 1042 / PB 15 (30) Priority: 25.04.2003 US 424195 Paul-Baumann-Strasse 1 45764 Marl (DE) (43) Date of publication of application: 08.02.2006 Bulletin 2006/06 (56) References cited: EP-A- 1 153 656 WO-A-00/50096 (73) Proprietor: Evonik Stockhausen, LLC WO-A-01/13841 WO-A-95/11932 Greensboro, NC 27406 (US) US-A- 4 587 308 US-A- 5 032 628 US-A- 5 409 771 US-A- 5 744 564 (72) Inventors: US-A- 6 124 391 US-A1- 2002 161 132 • SMITH, Scott, J. US-B1- 6 388 000 Greensboro, NC 27407 (US) • JOY, Mark, C. • PATENT ABSTRACTS OF JAPAN vol. 2003, no. Greensboro, NC 27410 (US) 02,5 February 2003 (2003-02-05) & JP 2002 302513 • HSU, Whei-Neen A (NIPPON SHOKUBAI CO LTD), 18 October 2002 Greensboro, NC 27410 (US) (2002-10-18) • FRANK, Markus 76532 Baden-Baden (DE) Note: Within nine months of the publication of the mention of the grant of the European patent in the European Patent Bulletin, any person may give notice to the European Patent Office of opposition to that patent, in accordance with the Implementing Regulations. -
Up-Scalable Synthesis of High Porous Superabsorbent Polymer Via Alkaline Hydrolysis of Acrylamide Using Microwave Irradiation: Application in Agriculture
Journal(of(Materials(and(( J. Mater. Environ. Sci, 2018, 9, Issue 3, Page 955-963 Environmental(Sciences( ISSN(:(2028;2508( https://doi.org/10.26872/jmes.2018.9.3.106 CODEN(:(JMESCN( ! Copyright(©(2018,((((((((((((((((((((((((((((( University(of(Mohammed(Premier(((((( http://www.jmaterenvironsci.com / (Oujda(Morocco Up-Scalable Synthesis of High Porous Superabsorbent Polymer via Alkaline Hydrolysis of Acrylamide using Microwave Irradiation: Application in Agriculture Hussam-Aldeen Kalaleh , Yomen Atassi* Laboratory of Materials sciences, Higher Institute for Applied Science and Technology Damascus, Syria Abstract Received 09 Apr 2017, Revised 05 Jul 2017, We present a new one-pot industrial organic synthesis method of poly(acrylate-co- Accepted 10 Jul 2017 acrylamide) superabsorbent polymer via partial alkaline hydrolysis of acrylamide using microwave irradiation. The method allows the hydrolysis, polymerization and gelation Keywords to take place in one pot during a very short reaction time (120 s), and with no need to operate under inert atmosphere. The gel is compact and has a water absorbency of 1031 !!superabsorbent g/g. The degree of hydrolysis of the gel is determined by a back titration method. FTIR polymers, spectroscopy is used to confirm the hydrolysis and the formation of sodium acrylate. !!alkaline hydrolysis, Scanning electron microscopy (SEM) reveals that the synthesized hydrogel has a high acrylamide, !! porous structure. The influence of the environmental parameters on water absorbency microwave synthesis, !! such as the pH and the ionic strength is also investigated. The product is tested for !!agriculture. agricultural application as a soil moisture retention agent using onion as example. An ! enhancement in the growth of onion plant is proved in comparison to the growth of the [email protected] onion without the superabsorbent polymer. -
Synthesis and Characterization Superabsorbent Polymers Made of Starch, Acrylic Acid, Acrylamide, Poly(Vinyl Alcohol), 2-Hydroxye
International Journal of Molecular Sciences Article Synthesis and Characterization Superabsorbent Polymers Made of Starch, Acrylic Acid, Acrylamide, Poly(Vinyl Alcohol), 2-Hydroxyethyl Methacrylate, 2-Acrylamido-2-methylpropane Sulfonic Acid Elzbieta˙ Czarnecka 1,2,* and Jacek Nowaczyk 1 1 Faculty of Chemistry, Nicolaus Copernicus University in Toru´n,7 Gagarina Street, 87-100 Toru´n,Poland; [email protected] 2 Plastica Sp. z o.o., Frydrychowo 55, 87-410 Kowalewo Pomorskie, Poland * Correspondence: [email protected] Abstract: Three polymers with excellent absorption properties were synthesized by graft polymeriza- tion: soluble starch-g-poly(acrylic acid-co-2-hydroxyethyl methacrylate), poly(vinyl alcohol)/potato starch-g-poly(acrylic acid-co-acrylamide), poly(vinyl alcohol)/potato starch-g-poly(acrylic acid-co- acrylamide-co-2-acrylamido-2-methylpropane sulfonic acid). Ammonium persulfate and potassium persulfate were used as initiators, while N,N0-methylenebisacrylamide was used as the crosslinking agent. The molecular structure of potato and soluble starch grafted by synthetic polymers was characterized by means of Fourier Transform Infrared Spectroscopy (FTIR). The morphology of the resulting materials was studied using a scanning electron microscope (SEM). Thermal stability was Citation: Czarnecka, E.; Nowaczyk, J. tested by thermogravimetric measurements. The absorption properties of the obtained biopolymers Synthesis and Characterization were tested in deionized water, sodium chroma solutions of various concentrations and in buffer Superabsorbent Polymers Made of solutions of various pH. Starch, Acrylic Acid, Acrylamide, Poly(Vinyl Alcohol), 2-Hydroxyethyl Keywords: semi-interpenetrating network hydrogel; biomaterial; superabsorbent polymer; hydrogel; Methacrylate, 2-Acrylamido-2- graft copolymerization methylpropane Sulfonic Acid. Int. J. Mol. Sci. -
(12) Patent Application Publication (10) Pub. No.: US 2014/0257223 A1 Henn Et Al
US 20140257223A1 (19) United States (12) Patent Application Publication (10) Pub. No.: US 2014/0257223 A1 Henn et al. (43) Pub. Date: Sep. 11, 2014 (54) SUPER-ABSORBNG POLYMERS WITH Publication Classification RAPIDABSORPTION PROPERTIES AND METHOD FOR PRODUCING THE SAME (51) Int. Cl. A6IL I5/24 (2006.01) (71) Applicant: EVONIK DEGUSSA GMBH, Essen A6IL 5/42 (2006.01) (DE) A6IL 5/60 (2006.01) (52) U.S. Cl. (72) Inventors: Markus Henn, Gelsenkirchen (DE); CPC ................. A61L 15/24 (2013.01); A61L 15/60 Laurent Wattebled, Dusseldorf (DE): (2013.01); A61L 15/425 (2013.01) Peter Herbe, Kevelaer (DE); Jorg USPC .............. 604/370; 604/372:521/149; 156/60 Harren, Baesweiler (DE); Christoph Loick, Tonisvorst (DE) (57) ABSTRACT The present invention relates to a particulate absorbent poly mer material having: (73) Assignee: EVONIK DEGUSSA GMBH, Essen i) a maximum APCo values 1.6) for at least one number (DE) iselected from the group of integers from 2 to 12 (=APC (21) Appl. No.: 14/352,171 ii) a values 12 for the sum total of all APC values for all numbers i from the group of integers from 2 to 12 (=APC (22) PCT Fled: Nov. 12, 2012 sum); (86) PCT NO.: PCT/EP2012/072360 wherein the APCo value is: S371 (c)(1), APC-10s.-QI. Io evalue'xPI, lose-value (2), (4) Date: Apr. 16, 2014 where the QIo value is the Swell index and ix10 seconds after (30) Foreign Application Priority Data adding the 0.9% by weight NaCl solution, and the PI.ix1O see value is the permeability index and ix10 sec Nov. -
Preparation of Surface-Reinforced Superabsorbent Polymer Hydrogel Microspheres Via Incorporation of in Situ Synthesized Silver Nanoparticles
polymers Article Preparation of Surface-Reinforced Superabsorbent Polymer Hydrogel Microspheres via Incorporation of In Situ Synthesized Silver Nanoparticles Semin Kim , Minsu Kim and Won-Gun Koh * Department of Chemical and Biomolecular Engineering, Yonsei University, Seoul 03722, Korea; [email protected] (S.K.); [email protected] (M.K.) * Correspondence: [email protected] Abstract: Superabsorbent polymer (SAP) particles are primarily applied for absorbing and storing liquids. Here, poly (acrylic acid) (PAA)-based SAP microspheres incorporated with silver nanoparti- cles (AgNPs) are prepared as an effort to maintain microsphere shape during swelling and minimize gel blocking. PAA-based SAP spheres are synthesized via inverse suspension polymerization. Ag- NPs are formed within SAP spheres through in situ reduction of silver nitrate (AgNO3), using polyvinylpyrrolidone as the reducing agent. The formation of AgNPs within SAP was observed via techniques such as scanning electron microscopy, ultraviolet-visible spectroscopy, thermogravimetric analysis, X-ray photoelectron spectroscopy and transmission electron microscopy. Energy dispersive spectroscopy analyses reveal that thin and dense layers of AgNPs are formed on the outer regions of the SAP spheres at higher concentrations of AgNO3. The water absorbency capacity decreases on increasing the amount of incorporated silver nanoparticles; however, it is comparable with that of Citation: Kim, S.; Kim, M.; Koh, W.-G. Preparation of commercially available surface-crosslinked SAP particles. Finally, micro-computerized tomography Surface-Reinforced Superabsorbent (micro-CT) study revealed that AgNP-incorporated SAP spheres maintained their shapes during Polymer Hydrogel Microspheres via swelling and exhibit higher void fractions in the packed gel bed, minimizing gel blocking and Incorporation of In Situ Synthesized improving fluid permeability.